
книги / Расчёт и проектирование систем обеспечения безопасности.-1
.pdf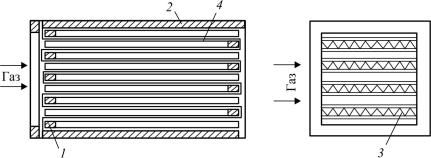
Устройство и области применения кассетных и рамочных фильтров. Устройство и области применения рулонных и масляных фильтров. Зернистые фильтры. Жесткие пористые фильтры. Кассетные и рамочные фильтры
Кассетные фильтры чаще всего используют для очистки от пыли воздуха в системах приточной вентиляции, иногда аспирационного воздуха в системах вытяжной вентиляции.
Кассетой называют отдельную ячейку, заполненную фильтровальным материалом. Поскольку фильтрующая способность одной кассеты невелика, при необходимости очистки большого количества воздуха их собирают на раме.
Раму можно устанавливать на пути движения воздуха вертикально, наклонно или горизонтально. Кассеты по мере запыления вынимают для удаления пыли из фильтровального материала или для его замены.
Фильтровальный материал выбирают в зависимости от назначения фильтра, характеристик газа и пыли. Иногда для повышения эффективности работы фильтровальный материал смачивают маслами или водой.
В рамочных фильтрах фильтровальный материал размещают между П-образными рамками (рис. 5.6). Между соседними слоями материала устанавливают гофрированные разделители, чтобы не было примыкания материала друг к другу. Рамки и корпус фильтра могут быть изготовлены из фанеры, винипласта, алюминия и нержавеющей стали.
Рис. 5.6. Рамочный фильтр: 1 – П-образная рамка; 2 – боковая стенка; 3 – разделители; 4 – фильтрующий материал
111
Рулонные фильтры. Самоочищающиеся масляные фильтры
Рулонные фильтры дают возможность упростить обслуживание и эксплуатацию устройств по очистке воздуха от пыли.
Рулонный автоматический фильтр представляет собой корпус, в верхней части которого размещена катушка с намотанным на нее чистым фильтровальным материалом, который перемещается через проем для воздуха со скоростью 50 см/мин и по мере забивания пылью наматывается на нижнюю катушку. Запыленный материал не регенерируется, а заменяется новым. Использованный материал сжигают – подвергают переработке или захоранивают. В качестве материала используют стекловолокно или синтетические волокна, рыхлый картон, фетр.
Гидравлическое сопротивление рулонных фильтров 100–150 Па. Срок непрерывной службы – до 1 года.
Самоочищающиеся масляные фильтры дают возможность непрерывно очищать большие массы воздуха в системах приточной вентиляции и кондиционирования при концентрации пыли до 10 мг/м3.
В конструкции фильтра предусмотрена автоматическая регенерация фильтрующего слоя, который может быть выполнен в виде шторок или ленточной сетки. Воздух, поступающий в фильтр, последовательно проходит через смоченные в масле сетки, а в ванне с маслом оседает пыль, которую время от времени удаляют.
Зернистые фильтры. Жесткие пористые фильтры
В зернистых фильтрах в качестве фильтрующего слоя используют насыпные материалы, в которых отдельные элементы не связаны между собой. К ним относятся крупнозернистый песок, гравий, шлак, кокс, кусковая резина, пластмасса, керамические кольца и седла и т.д.
Насыпной слой может быть неподвижным, двигаться или находиться в псевдоожиженном состоянии.
При пропускании газа через зернистые материалы твердые и жидкие частицы задерживаются и остаются в фильтрующем слое.
Зернистые фильтры могут применяться при работе в условиях высоких температур, агрессивной среды и при больших механических нагрузках и перепадах давления. Однако они склонны к забиванию пылью, и их регенерация часто затруднена. Поэтому, если пыль с фильтрующего слоя удалить нельзя, его полностью заменяют. Поскольку ско-
112
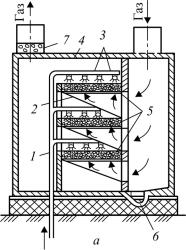
рость фильтрации газа через зернистый материал мала, то такие фильтры требуют больших площадей для их установки.
На рис. 5.7 представлена схема
орошаемого гравийного |
фильтра, |
который применяют для |
очистки |
вентиляционного воздуха |
от влаж- |
ной и взрывоопасной пыли или паров. Кроме гравия могут использоваться кокс, шлак и другие кусковые материалы размером 20–30 мм при толщине слоя 150–200 мм.
Расход воды для орошения составляет 0,4–0,75 л/м3, но не менее 1500 л на 1 кг поступающей в фильтр пыли. Для улавливания капель воды на выходе из фильтра устанавливают сепаратор. В некоторых зернистых фильтрах регенерация фильт-
рующего слоя производится в результате его вибрации и обратной продувки атмосферным воздухом.
Существуют конструкции зернистых фильтров с движущимся в вертикальном направлении фильтрующим слоем. В этом случае загрязненный слой непрерывно выводится и заменяется новым.
Если при очистке технологических газов в черной металлургии использовать в качестве фильтрующего материала чугунную дробь, железорудный концентрат, дробленую стружку, то фильтрующий слой после запыления можно не регенерировать, а направлять на переплавку.
Существуют конструкции зернистых магнитных фильтров, в которых фильтрующий слой состоит из ферромагнитных частиц. Из-за возникновения магнитного поля в фильтрующем слое эффективность пылеулавливания увеличивается при меньшей толщине слоя по сравнению с обычными зернистыми фильтрами. Кроме того, в магнитном зернистом фильтре можно очищать газ с температурой ниже той, при которой улавливаемая пыль иличастицыфильтрующегослоятеряютмагнитныесвойства.
Для очистки газов с высокой температурой широко используются керамические, металлокерамические и другие жесткие пористые фильт-
113
ры. Они обладают антикоррозионной устойчивостью и выдерживают большие механические нагрузки. Эти фильтры более эффективны, чем зернистые, компактны и просты в установке. Однако они имеют большое гидравлическое сопротивление проходу газа, плохо регенерируются и дорого стоят.
Жесткие керамические пористые фильтрующие материалы делают
ввиде цилиндрических труб, плиток или тонких листов, которые состоят из зерен, прочно связанных между собой путем спекания, прессования, склеивания или применения связующих веществ.
Регенерацию фильтрующего слоя таких фильтров осуществляют путем обратной продувки их сжатым воздухом или газом, пропускания через них растворов, горячего пара, вибрации или простукивания.
Вметаллокерамических фильтрах, которые по принципу действия напоминают рукавные, фильтрующий слой изготавливают в виде труб диаметром 100 мм и длиной до 2 м из порошков различных металлов
исплавов методом прессования или прокатки с последующим спеканием. Эти фильтры могут полностью очищать газы от частиц пыли размером менее 1 мкм при температуре 600 ° С и выше. Скорость фильтрации
вних 0,2–10 м/мин, гидравлическое сопротивление от 100 до 6000 Па.
Вопросы для самоконтроля
1.Механизмы процесса фильтрования.
2.По каким конструктивным признакам классифицируют промышленные фильтры?
3.Как устроены и работают тканевые фильтры?
4.Какие фильтровальные материалы применяют в тканевых фильтрах?
5.Какие требования предъявляют к фильтровальным тканям?
6.Какиеспособырегенерациитканиприменяютвтканевыхфильтрах?
7.Какопределяютгидравлическоесопротивлениетканевогофильтра?
8.Зернистые фильтры, их преимущества и недостатки, области применения.
9.Кассетные и рамочные фильтры, их преимущества и недостатки, области применения.
10.Рулонные фильтры, их преимущества и недостатки, области применения.
11.Масляные фильтры, их преимущества и недостатки, области применения.
114
Классификация аппаратов мокрой очистки газов. Оросительные устройства. Полые скрубберы. Классификация полых скрубберов. Принцип работы и области применения
В мокрых пылеуловителях (ПУ) очистка газа осуществляется при контакте газа с жидкостью. Взвешенные в газе частицы пыли смачиваются, утяжеляются и выводятся из газового потока под действием гравитационных сил или сил инерции, либо захватываются жидкостью и удаляются в виде шлама. Одновременно происходит и охлаждение газа. Поскольку при смачивании масса частиц становится больше, в мокрых ПУ эффективность очистки лучше, чем воднотипных сухих.
Мокрые ПУ применяют в тех случаях, когда
1)уловленная пыль далее не используется;
2)пыль может быть использована в мокром виде или после обезвоживания;
3)необходимо охладить газ независимо от его очистки.
Кдостоинствам мокрых ПУ можно отнести:
–сравнительно небольшую стоимость изготовления;
–высокую эффективность улавливания частиц пыли;
–возможность их использования при высокой температуре и повышенной влажности газов, а также в случае опасности самовозгорания или взрыва очищаемых газов или улавливаемой пыли;
–возможность одновременного осуществления очистки газов от взвешенных частиц (т.е. пылеулавливание), извлечения газообразных примесей (абсорбция) и охлаждения газов (т.е. контактный теплообмен).
Однако мокрые способы улавливания имеют и недостатки: улавливаемый продукт выделяется в виде шлама, что связано с не-
обходимостью обработки сточных вод, а следовательно, с удорожанием процесса очистки;
в случае очистки агрессивных сред аппаратуру и коммуникации необходимо изготавливать из антикоррозионных материалов или применять антикоррозионные покрытия.
В качестве орошающей жидкости чаще всего применяют воду. Для уменьшения количества отработанной жидкости используют замкнутую систему орошения.
Мокрые ПУ классифицируют следующим образом.
По способу действия их делят:
–на оросительные устройства;
–полые (форсуночные) скрубберы;
115
–насадочные скрубберы;
–тарельчатые скрубберы (пенные аппараты);
–скрубберы с подвижной насадкой;
–скрубберы ударно-инерционного действия (ротоклоны);
–центробежные скрубберы;
–механические (динамические) скрубберы;
–скоростные скрубберы (скрубберы Вентури);
–эжекторные скрубберы.
По затратам энергии мокрые ПУ делят на три группы:
1)низконапорные – гидравлическое сопротивление не более 1500 Па (книмотносятся форсуночные, насадочные ицентробежные скрубберы);
2)средненапорные – гидравлическое сопротивление от 1500 до 3000 Па (динамические, эжекторные скрубберы, скрубберы ударноинерционного действия);
3)высоконапорные – гидравлическое сопротивление более 3000 Па (скрубберы Вентури).
Еще одной особенностью работы мокрых ПУ является вынос брызг орошающей жидкости из аппаратов. Чтобы его предотвратить, необходимо соблюдать оптимальный режим работы аппаратов и предусматривать специальные брызго- и каплеуловители.
Мелкие частицы пыли в мокрых ПУ улавливаются плохо, так как на их поверхности образуется пленка газа, которая препятствует их смачиванию. Для улучшения смачиваемости частиц необходимо создать условия для разрушения газовой пленки, что достигается либо организацией движения газового потока в условиях высокой турбулентности, либо вводом в орошающую жидкость специальных поверхност- но-активных веществ.
Рассмотрим основные мокрые пылеуловители.
Оросительные устройства. Промывные камеры
К оросительным устройствам относят брызгала, которые устанавливают в газоходах. В них запыленный газ пропускают через завесу распыляемой жидкости со скоростью не более 3 м/с, чтобы не было уноса брызг. Расход воды зависит от температуры очищаемых газов и степени их охлаждения и составляет 0,1–0,3 л/м3.
Эти устройства используют для очистки газа от пыли, размер частиц которой больше 20 мкм, а также в том случае, если к очистке не предъявляют высоких требований.
116
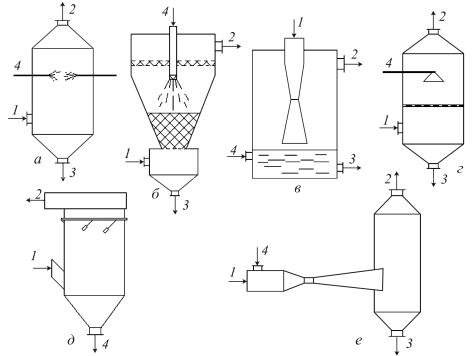
После оросительных устройств в большинстве случаев необходимо устанавливать каплеуловители.
Промывная камера – это усовершенствованное оросительное устройство (рис. 5.8).
Рис. 5.8. Аппараты для мокрой очистки газовых выбросов (газопромыватели): а – полые; б – насадочные; в – ударно-инерционного действия;
г – тарельчатые; д – центробежные; е – скруббер Вентури
Их устанавливают в кондиционерах и в приточных вентиляционных установках для обработки воздуха.
В зависимости от количества рядов форсунок камеры бывают двух- и трехрядные. В начале и в конце камеры устанавливают сепара-
торы для отделения капель жидкости. |
|
Скорость движения газа составляет 1,5–2,5 м/с, |
расход воды – |
0,2–1 л/м3 газа, давление воды перед форсунками – |
0,35–0,5 МПа, |
гидравлическое сопротивление камер – 300–500 Па.
Воду из поддона камеры отводят насосом, очищают в фильтре и снова подают в форсунки.
117
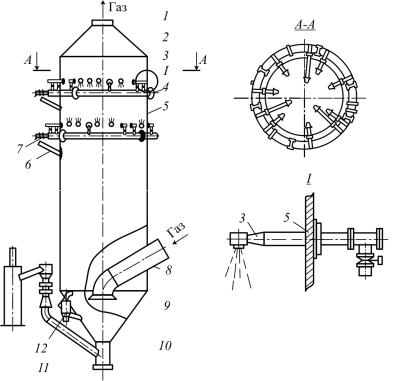
Полые скрубберы
Полый скруббер (рис. 5.9) – это пустотелая цилиндрическая или прямоугольная башня, выполненная из металла или кирпича, железобетона и других материалов. В случае необходимости внутреннюю поверхность футеруют или покрывают антикоррозионными составами.
Рис. 5.9. Полый скруббер: 1 – патрубок для выхода газа; 2 – конфузор; 3 – форсунка; 4 – коллектор орошения; 5 – корпус скруббера; 6 – продувочный
патрубок; 7 – клапан для продувки коллектора орошения; 8 – патрубок для входа газа; 9 – бункер; 10 – патрубок для удаления шлама;
11 – гидравлический затвор; 12 – поплавковая камера
В верхней части форсунки устанавливают таким образом, чтобы все поперечное сечение было перекрыто факелами орошающей жидкости. Наклонный патрубок внизу аппарата способствует более равномерному вводу газа и распределению его по сечению скруббера.
Скрубберы, в которых газ и жидкость двигаются навстречу друг другу, называют противоточными, если газ и жидкость подаются в аппарат сверху, то их называют прямоточными.
118
Однако лучший тепло- и массообмен между газом и жидкостью наблюдается в противоточных скрубберах.
При большом расходе орошающей жидкости форсунки устанавливают в 2 яруса и более.
При однорядном расположении форсунок факел распыления обычно направлен вертикально, сверху вниз или под некоторым углом. При нескольких ярусах форсунок: у верхнего яруса факел направлен вниз, против движения газа, а остальные – вверх, по ходу движения газа.
Взависимости от количества воды, подаваемой на орошение, по-
лые скрубберы делят на охладительные и испарительные.
Вохладительные скрубберы подают большое количество воды, которая в процессе охлаждения газа не успевает испариться, а только нагревается.
Виспарительные скрубберы воду подают в небольшом количестве, которая частично или полностью испаряется. Температура конечного газа в таких устройствах значительно выше, чем в охладительных скрубберах.
Одновременно с охлаждением газов в аппаратах происходит, и очи-
стка от пыли размером более 10 мкм. Мелкие частицы не смачиваются и выносятся газами из скруббера.
Степень очистки обычно составляет 60–70 %, однако ее можно увеличить, повышая: высоту скруббера; скорость газа в нем; удельный расход воды, а следовательно, и количество капель жидкости.
Полые скрубберы используют в основном для охлаждения и увлажнения газов, а также для грубой их очистки.
Оптимальная скорость газового потока в аппарате составляет 0,7–1,5 м/с. Если превысить эти значения, происходит унос капель жидкости, что крайне нежелательно. Чтобы уменьшить данное явление, применяют форсунки грубого распыления воды. В этом случае капли имеют размер около 0,8 мм или более и при оптимальных скоростях газа не выносятся из скруббера. Однако чем крупнее капли, тем меньшее их количество образуется и тем хуже контакт газа с водой.
Если после полого скруббера установлен каплеуловитель, то скорость газа можно увеличить до 2–2,3 м/с. В этом случае повышается турбулентность движения газового потока, столкновение капель с пылью наиболее интенсивно и наблюдается лучший тепло- и массообмен между газом и водой.
Процесс тепло- и массообмена в скруббере происходит следующим образом. При входе в скруббер газ обычно не насыщен полностью
119
влагой. Если газ имеет высокую температуру, вода в скруббере испаряется, и влагосодержание газа увеличивается. Этот процесс сопровождается охлаждением газа при постоянной энтальпии, так как образующийся из воды пар возвращает газу тепло, которое было затрачено на испарение воды, в виде теплосодержания, т.е. энтальпии водяного пара. Температура воды в процессе охлаждения газа в этот период остается постоянной и равной температуре мокрого термометра, так как тепло, передаваемое газом воде, полностью расходуется на парообразование воды. При достижении газом состояния полного насыщения водяным паром парообразование воды прекращается.
В этот период газ из нижней части скруббера успевает пройти в его верхнюю часть. С момента полного насыщения газа водяным паром дальнейшее охлаждение газа вызывает конденсацию части водяных паров. Тепло, выделяющееся приконденсации, идет на нагрев воды. Нагрев вновь продолжается до достижения водой температуры мокрого термометра. Приэтомэнтальпия исодержаниев газе водяного пара уменьшаются.
Таким образом, в нижней части скруббера происходит испарительное охлаждение газа, а в верхней – процесс конденсационного охлаждения.
Расход воды зависит от начальной и конечной температуры газа, начального влагосодержания газа и температуры воды. В среднем он составляет 0,5–0,7 л/м3 газа. Если одновременно с охлаждением газа идет, и его очистка, расход воды увеличивают до 3–10 л/м3 газа.
Гидравлическое сопротивление полого скруббера при отсутствии каплеуловителя составляет около 250 Па.
Скрубберы с насадкой. Типы насадок, пенные аппараты. Конструкция и области применения. Центробежные скрубберы и циклоны. Скрубберы с насадкой
Для улучшения контакта газа с жидкостью применяют смачиваемую насадку, которую вставляют в полый скруббер (рис. 5.10).
Насадку помещают на колосниковую решетку, насыпая ее навалом или укладывая рядами, а тип насадки выбирают в зависимости от условий работы скруббера (рис. 5.11).
Проходя через насадку, газ многократно изменяет направление своего движения, в результате чего содержащаяся в газе пыль или капельные компоненты по инерции попадают на смоченную поверхность насадки и смываются стекающей жидкостью. Поэтому в насадочных скрубберах пыль улавливается более эффективно, чем в полых. Однако
120