
книги / Обогащение полезных ископаемых
..pdf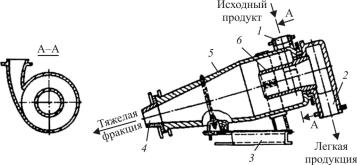
Тяжелосредный гидроциклон – аппарат для обогащения в тяжелой среде под влиянием центробежных сил.
Принцип работы двухпродуктового тяжелосредного гидроциклона (рис. 38) заключается в следующем. Исходный продукт поступает в аппарат в смеси с тяжелой суспензией через загрузочный патрубок 1 по касательной во внутреннюю полость цилиндрической части корпуса. Тангенциальный ввод разделительной среды под давлением формирует внутри аппарата вихревой поток с воздушным столбом вдоль оси. Благодаря центробежным силам, во много раз превосходящим силы тяжести, тяжелый продукт перемещается к стенкам конической части корпуса 5, скользит по ним и разгружается совместно с частью суспензии через разгрузочную насадку 4. Легкий продукт проходит через сливную трубу 6 в разгрузочную камеру 2. Гидроциклон устанавливают вертикально или чаще на раме 3 под определенным углом наклона к горизонту.
Рис. 38. Схема двухпродуктового тяжелосредного гидроциклона
Преимущества тяжелосредных гидроциклонов перед аппаратами, в которых разделение происходит только под действием сил тяжести, заключается в наличии центробежного поля, обеспечивающего повышение эффективности и скорости разделительных процессов.
В технологии обогащения суспензионный процесс может выполнять функции как вспомогательных, так и основных процессов с выдачей готовой продукции. В качестве вспомогательного суспен-
121
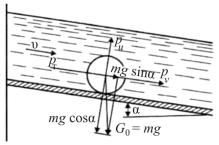
зионный процесс находит широкое применение для предконцентрации полиметаллических руд и позволяет выделить до 35 % породы
вначале технологической схемы.
Вкачестве основного суспензионный процесс применяют на углеобогатительных, хромовых, марганцевых, железорудных и других фабриках в комбинации с другими процессами.
3.1.4. Обогащение на концентрационных столах
Минеральные частицы, транспортируемые потоком воды по наклонной плоскости, имеют сложную траекторию движения. Они скользят и перекатываются по наклонной плоскости, подхватываются вихревыми потоками и перемещаются вместе с водным потоком, затем опускаются вниз и т.д.
Рис. 39. Диаграмма сил, действующих на частицу минерала
На минеральную частицу массой т, которая находится в потоке воды, текущей по наклонной плоскости, действуют следующие силы (рис. 39): сила тяжести частицы в воде G0 = mg, направленная вертикально вниз; динамическое давление струи воды pv в направлении движения частицы; сила динамического воздействия вертикальной составляющей скорости pи, возникающей при турбулентных режимах и направленной вверх; сила трения pт, направленная в сторону, противоположную движению частицы. В результате воздействия этих сил мелкие и легкие зерна будут перемещаться водной струей по наклонной плоскости с большей скоростью, чем крупные и тяжелые.
122
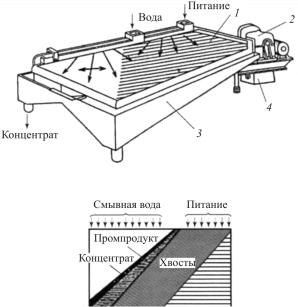
Разделение частиц в потоках жидкости малой толщины осуществляют на концентрационных столах, шлюзах, в желобах и винтовых сепараторах. Наибольшее распространение имеет обогащение полезных ископаемых на концентрационных столах.
Концентрация на столе – процесс разделения минеральных частиц на основе различий в их плотности и крупности в тонком слое воды, текущей по наклонной плоскости.
Концентрационный стол – сепаратор для гравитационного обогащения (рис. 40, а), представляет собой плоскую поверхность трапециевидной формы – деку с узкими рифлями. Деки изготавливают из дерева или алюминия и покрывают линолеумом (полиуретаном) или другими материалами. Деку устанавливают под углом 1–10° в поперечном направлении, и под действием привода она совершает возвратно-поступательное движение в продольном направлении.
а
б
Рис. 40. Концентрационный стол (а): 1 – дека; 2 – приводной механизм; 3 – опорное устройство; 4 – механизм регулирования наклона дек; схема процесса концентрации на столе (б)
123
Впоперечном направлении по всей площади деки идет тонкий поток воды. Питание в виде пульпы подают в верхний угол стола через загрузочный лоток (рис. 40, б).
Поступающие на деку стола частицы минералов подвергаются воздействию двух основных сил: силы воздействия смывного потока воды, направленной поперек деки, и силы инерции частиц, возникающей при возвратно-поступательном движении деки и направленной вдоль деки.
Скорость движения частицы в поперечном направлении деки под воздействием потока воды определяется соотношением тем выше, чем меньше плотность и размер частицы. Следовательно, мелкие
илегкие частицы будут перемещаться в поперечном направлении деки стола с большей скоростью, чем крупные и тяжелые.
Скорость движения частицы минерала в продольном направлении деки стола определяется соотношением силы инерции и силы трения. Следовательно, тяжелые частицы будут перемещаться в продольном направлениидекистоласбольшей скоростью, чемлегкие.
Результирующие скорости легкой и тяжелой частиц обеспечивают движение их по различным траекториям и схождение с деки стола в различных точках.
Врезультате всех явлений на деке стола образуется «веер продуктов» (см. рис. 40, б). В передней части деки концентрируются частицы наиболее тяжелых минералов, в конце деки (у привода) – частицы наиболее легких минералов, а между ними концентрируются частицы промежуточной плотности (сростки).
Процесс разделения зернистого материала на концентрационном столе отличается высокой эффективностью, которая зависит от плотности, крупности, формы частиц, гидродинамики потока воды, параметров движения деки, явлений сегрегации и др.
3.1.5. Обогащение на шлюзах
Обогащение на шлюзах – процесс гравитационного обогащения, в котором разделение частиц производится в слое жидкости, движущейся по наклонному желобу, дно которого имеет шероховатое или гладкое покрытие.
124
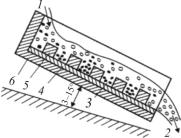
Шлюз – это сепаратор для гравитационного обогащения, в котором разделение частиц осуществляется в слое жидкости, движущейся по наклонному желобу с параллельными бортами, на дно которого укладываются трафареты или покрытия из шероховатого материала (войлок, грубошерстное сукно, рифленая резина и др.) (рис. 41).
На шлюзах обогащают руды россыпных месторождений золота, вольфрама, олова и редких металлов.
Пульпа при разжижении Ж : Т не менее (5–6) : 1 подается в головную верхнюю часть подготовленного к работе шлюза.
При движении пульпы по шлюзу происходит разделение минеральной смеси по плотности и крупности зерен. Вначале на дно шлюза оседают зерна тя-
желых минералов, которые концентрируются между трафаретами или задерживаются шероховатой поверхностью покрытия, а более крупная галька и валуны уносятся потоком и катятся по дну шлюза. Вместе с ними уносятся зерна легких минералов и шламы.
Работа концентрационных шлюзов с улавливающим покрытием характеризуется периодичностью.
По мере накопления тяжелых минералов промежутки между трафаретами полностью ими заполняются и подачу питания на шлюз прекращают. Затем осадок снимают сполоском шлюза. Сполоск ворсистой ткани выполняют путем ее снятия и промывки в специальном баке. Операция по снятию осадка является весьма трудоемкой и в шлюзах новых конструкций процесс сполоска автоматизирован. После снятия концентрата шлюз снова армируют и включают в работу.
Выход концентрата составляет десятые и сотые доли процента. Применительно к обогащению бедных россыпных материалов шлюз характеризуется высокой степенью концентрации.
125
Различают шлюзы глубокого наполнения для обработки материала крупнее 20 мм и шлюзы мелкого наполнения для обогащения материала мельче 20 мм.
Шлюзы глубокого наполнения представляют собой желоба прямоугольного сечения, изготовленные из досок толщиной 40–50 мм. Длина шлюзов достигает 150–180 м, ширина изменяется от 0,9 до 1,8 м, а высота (глубина) – от 0,75 до 0,9 м. Угол наклона шлюза составляет 2–3°. На дно шлюза укладывают трафареты. Часто для улавливания мелких тяжелых минералов, оседающих между трафаретами, по всему дну шлюза под трафаретами укладывают ворсистую ткань.
Шлюзы с малым наполнением используются для обогащения тонкозернистого материала. Дно таких шлюзов устилается ворсистыми, шероховатыми покрытиями – войлоком, грубошерстным сукном, рифленой резиной, кордероем, вельветом.
В настоящее время для обогащения тонкозернистого материала применяются шлюзы с ворсистым покрытием следующих типов: стационарные с опрокидывающейся декой, подвижные ленточные, автоматические многодечные и винтовые.
Стационарные шлюзы эксплуатируются на фабриках небольшой производительности. Они изготавливаются в виде слабонаклонной деревянной плоскости с невысокими бортами, покрытой линолеумом или листовым металлом, и закрепляются на стойке. Шлюзы бывают с закрепленным и съемным ворсистым покрытием. В первом случае сполоск шлюза производится сильной струей воды, во втором – ворсистое покрытие снимают и промывают в специальной емкости.
Опрокидывающиеся шлюзы с закрепленным покрытием при сполоске поворачиваются на 45–60° и концентрат смывается струей воды, т.е. операция снятия концентрата частично механизирована.
Ленточные шлюзы применяются для обогащения шламистых продуктов, содержащих золото, платину и олово. Ленточный шлюз состоит из движущейся бесконечной прорезиненной ленты. Лента движется навстречу течению пульпы. Снятие концентрата на них полностью механизировано.
126
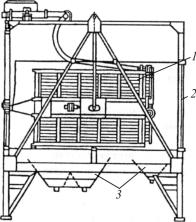
Автоматические многодечные шлюзы являются по конст-
рукции наиболее совершенными аппаратами.
На рис. 42 представлен 40-дечный автоматический шлюз «Бартлез-Мозли», деки которого сгруппированы в два пакета по 20 дек. В промежутке между пакетами размещен привод шлюза.
Рис. 42. Орбитальный шлюз «Бартлез-Мозли»: 1 – деки; 2 – рама; 3 – приемник продуктов обогащения
Деки размером 1,3×1,5 м изготовлены из стекловолокна и расположены в виде двух стеллажей, свободно подвешенных под углом 1–3°. В период шлюзования деки совершают орбитальное движение. Амплитуда качания дек равна 4,8–6,4 мм.
Пульпа равномерно распределяется по всем 40 декам. Продолжительность подачи питания и шлюзования составляет около 35 мин. В конце загрузки деки наклоняются до 45° и осуществляется промывка их водой. После промывки шлюз автоматически возвращается в исходное положение и цикл его работы повторяется.
3.1.6.Обогащение на струйных концентраторах
Вструйных аппаратах обогащение происходит в наклонном потоке под действием силы тяжести. К таким аппаратам относятся:
127
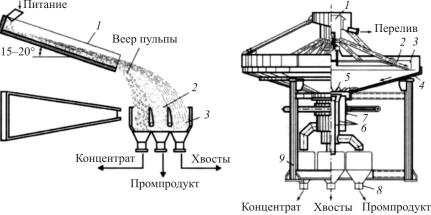
струйные желоба (суживающиеся) и различные установки их на общей раме (струйные концентраторы) (рис. 43, а);
конусные сепараторы, которые состоят из одного или нескольких конусов, установленных основанием вверх и представляющих собой как бы единый круговой суживающийся желоб
(рис. 43, б).
Струйный желоб представляет собой короткий (до 1000–1200 мм) клиновидный желоб с плоским и гладким днищем. Устанавливается он под углом 15–20° к горизонту, узкой частью вниз.
а |
б |
Рис. 43. Суживающийся желоб (а) и конусный сепаратор (б): 1 – приемный резервуар; 2 – распределительное конусное кольцо; 3 – стабилизирующая перегородка; 4 – конус; 5 – суживающиеся клинья; 6 – трубы для разгрузки продуктов; 7 – штурвал; 8 – приемный желоб; 9 – рама
Благодаря сужению желоба высота потока увеличивается от 1,5–2 мм у загрузочного конца до 7–12 мм у разгрузочного. В нижних слоях потока сосредоточиваются мелкие частицы большей плотности, а в верхних – крупные меньшей плотности. Расслоенные продукты направляются в отдельные приемники. В струйных аппаратах концентрат выделяется непрерывно.
128
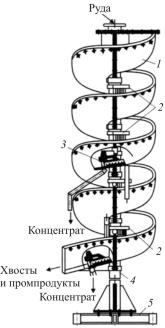
3.1.7. Обогащение в криволинейных и центробежных потоках воды
Обогащение на винтовых сепараторах и шлюзах. Винтовой сепаратор – это сепаратор для гравитационного обогащения, в котором разделение частиц производится в жидкости, движущейся по винтовому желобу с вертикальной осью (рис. 44). Пульпа подается в верхнюю часть желоба и под действием силы тяжести стекает по нему вниз в виде тонкого (6–15 мм) слоя.
При движении по желобу винтового сепаратора частицы распределяются по глубине потока в соответствии с их гидравлической крупностью. Одновременно под влиянием циркулирующих потоков воды, центробежных и гравитационных сил происходит перемещение частиц в поперечном направлении: находящиеся в верхних слоях частицы меньшей гидравлической крупности (преимущественно зерна легких минералов) относятся к внешнему борту, а находящиеся в нижних слоях (частицы тяжелых минералов и крупные – легких) – к внутреннему.
В результате поперечного перераспределения зерен формируются отдельные слои потока (концентрат, промпродукт, хвосты),
которые приобретают установившееся движение.
Основное перераспределение зерен заканчивается после прохождения примерно двух или трех витков, после чего зерна движутся на постоянных расстояниях от оси сепаратора.
129
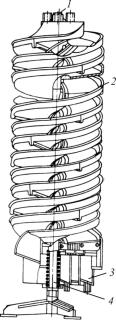
Вывод продуктов обогащения осуществляется отсекателями, установленными на сепараторах отечественной конструкции в конце последнего витка, а на зарубежных – на каждом витке желоба (до трех отсекателей на каждом витке).
Диаметр винтового желоба определяет размер сепаратора. Выбор диаметра сепаратора зависит от заданной производительности, крупности и плотности разделяемого материала. Применяемые в практике винтовые сепараторы имеют желоба
диаметром600–2000 мм.
Число витков желоба зависит от физических свойств разделяемого материала. Оно увеличивается с уменьшением разницы в плотностях разделяемых минералов и их крупности. Число витков желоба в промышленных сепараторах составляет 4–6.
Шаг винтового желоба при постоянном диаметре определяет угол наклона желоба к горизонтальной плоскости. С уменьшением относительного шага винтового желоба (отношение шага к диаметру) показатели обогащения для материала крупностью –2+0,2 мм ухудшаются, а для материала крупностью менее 0,2 мм – улучшаются. Относительный шаг принимается для промышленных винтовых сепараторов равным 0,4–0,6, для винтовых шлюзов – 0,5.
Разновидностью винтовых сепараторов являются винтовые шлюзы (рис. 45), отличающиеся от первых более широким желобом с малым наклоном его днища. Они предназначены для обогащения тонкозернистых материалов крупностью менее 0,5(0,2) мм при малых скоростях движения потока в желобе.
130