
книги / Обогащение полезных ископаемых
..pdfприводной механизм машины; способ разгрузки дробленого материала и способ возбуждения дробящего усилия.
В дробилке крупного дробления (рис. 17, а, б) крутой подвижный конус 1 приводится в движение вокруг неподвижной оси. В дробилке среднего и мелкого дробления (рис. 17, в) пологий подвижный конус 1, закрепленный на вращающемся с помощью эксцентрикового стакана валу, расположен внутри неподвижного конуса 2 (обращенного большим основанием вниз). В момент максимального сближения дробящего конуса с чашей такой дробилки создается «параллельная зона», ширина которой определяет размер кусков дробленого продукта.
Процесс дробления в конусных дробилках происходит непрерывно при последовательном перемещении зоны дробления по окружности конусов. Дробленый материал под действием собственной тяжести разгружается через разгрузочное отверстие, имеющее в разомкнутом положении ширину b. При смыкании дробящих органов отверстие уменьшается до размера b0, причем b0 = b – s, где s – ход конуса (двойная амплитуда) в нижней точке.
Крупность дробленого продукта и производительность дробилки данного типоразмера зависят главным образом от ширины разгрузочного отверстия b.
Попадание в дробилки среднего и мелкого дробления вместе с рудой металлических предметов может вызвать поломку дробилок. Современная схема улавливания металлических предметов из руды, подаваемой конвейером в дробилку, включает установку по ходу конвейера двух металлоискателей и мощного подвесного электромагнита между ними.
Конусные дробилки получили широкое распространение в горнорудной промышленности благодаря высокой производительности, сравнительно низкому удельному расходу электроэнергии и способности выдавать достаточно равномерный по крупности дробленый продукт. Недостатками конусных дробилок (в сопоставлении со щековыми) являются: более сложная и дорогая конструкция, большая высота, более сложное обслуживание.
71
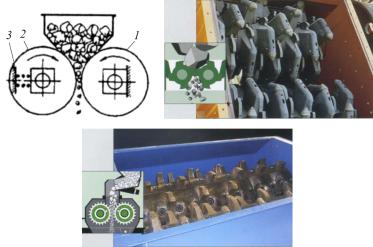
2.3.5.Принцип действия и устройство валковых дробилок
Ввалковых дробилках материал дробится между двумя валками, вращающимися навстречу друг другу (рис. 18). Один из них вращается в неподвижно закрепленных подшипниках 1, другой –
вподвижных 2, удерживаемых в направляющих спиральными амортизирующими пружинами 3, предохраняющими дробилку от поломки при попадании в нее недробимых предметов. При гладкой поверхности валков дробление материала осуществляется раздавливанием и частично истиранием, при зубчатой и рифленой поверхности – раскалыванием, разламыванием и раздавливанием. Дробимый материал поступает в пространство между валками сверху, затягивается ими и дробится. Дробленый продукт выпадает из дробилки под действием силы тяжести.
Рис. 18. Принцип действия валковых дробилок
Валки изготавливаются из чугуна и футеруются по внешней поверхности бандажами из углеродистой или износостойкой марганцовистой стали. Окружная скорость валков составляет от 2 до 7 м/с. В зависимости от конструктивных особенностей и назначения применяют валковые дробилки следующих типов: одновалковые –
72
для агломерата и угля; двухвалковые (с гладкими и рифлеными валками) – для горных пород и руд; двухвалковые с зубчатыми валками – для угля и мягких пород; четырехвалковые с гладкими валками – для кокса и известняка (на аглофабриках). Валковые дробилки высокого давления (ВДВД) отличаются тем, что исходный материал
вкамеру дробления подается через питающую трубу высотой до 3 м, что обеспечивает «объемное» сжатие кусков руды и получение более равномерного по крупности дробленого продукта.
Валковые дробилки компактны и надежны в работе; вследствие однократного сжатия материал в них не переизмельчается и содержит мало мелочи. Материал перед дроблением, как правило, подвергается грохочению и в дробилку направляется только надрешетный продукт грохота. Материал на грохот обычно подается ленточным конвейером. При загрузке материала в дробилку необходимо обеспечить поступление его по всей длине валков с тем, чтобы работала вся их поверхность. Дробленый продукт, как правило, направляется
вследующую операцию конвейером или самотеком по желобу. Наиболее быстро изнашивающимися частями этих дробилок являются зубчатые сегменты и вкладыши подшипников. Сегменты изготавливают из марганцовистой стали, а зубья по режущим кромкам наплавляют твердым сплавом.
2.3.6. Принцип действия и устройство молотковых и роторных дробилок
В дробилках ударного действия разрушение дробимого материала происходит за счет кинетической энергии движущихся тел. К ним относятся три типа дробилок: молотковые, роторные и стержневые (дезинтеграторы). Молотковые и роторные дробилки (рис. 19) с вращающимся ударным ротором подразделяют на два типа: молотковые с шарнирно подвешенными молотками и роторные с жестко закрепленными лопатками (билами) и предназначаются для дробления материалов малой крепости.
Молотковые и роторные дробилки отличаются большим конструктивным разнообразием. Они изготавливаются одно- и двухро-
73
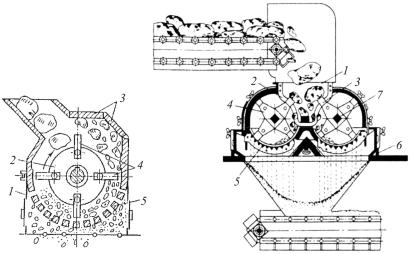
торные, с разгрузкой дробленого продукта через колосниковую решетку и со свободной разгрузкой, с жесткой и самоочищающейся решеткой, реверсивные и нереверсивные, горизонтальные и вертикальные.
|
а |
|
|
|
|
|
б |
|
Рис. |
19. Молотковая однороторная (а) и |
двухроторная (б) дробилка |
||||||
с параллельным |
расположением |
|
роторов: |
1 |
– |
загрузочная |
воронка; |
|
2 – |
фигурные |
колосники; 3 |
– |
молотки; |
4 |
– |
держатели |
молотков; |
5 |
– колосниковые решетки; 6 – |
корпус дробилки; 7 – роторные валы |
Молотковая дробилка с решеткой состоит из сварного корпуса
иротора. Для защиты от износа торцовые стенки корпуса облицованы футеровочными плитами. Исходный материал попадает на быстро вращающийся ротор со свободно подвешенными молотками
иотбрасывается на отбойные плиты. Дробление производится ударами молотков по материалу и ударами кусков об отбойные плиты. Дробленый материал разгружают через решетку, здесь же на решетке происходит додрабливание крупных кусков.
Вроторной дробилке дробление осуществляют жестко установленными на барабане билами. Материал додрабливается при его ударе о неподвижную и подвижную плиты.
74
Молотковые и роторные дробилки применяют для крупного, среднего и мелкого дробления различных полезных ископаемых – хрупких, мягких и средней крепости. Основными преимуществами этих дробилок являются простота конструкции, большая производительность, низкая металлоемкость, высокая степень дробления (до 30) и удобство обслуживания. Основной недостаток роторных дробилок – быстрый износ молотков, бил и решеток, вследствие чего долговечность дробилок снижается. Для молотковых дробилок применяют молотки различной массы (от 3 до 180 кг) и формы в зависимости от крупности и твердости дробимого материала. Молотки изготавливают из стали с наплавкой твердыми сплавами.
Самоочищающиеся молотковые дробилки применяют для дробления липкого материала. Они отличаются тем, что дробящая плита находится в непрерывном движении, а задняя стенка станины тоже защищена постоянно движущимся полотном очистного устройства.
Перед дробилками устанавливают уловители для удаления из загружаемого материала посторонних недробимых металлических предметов.
2.4. Измельчение
Измельчение – это процесс разрушения кусков полезного ископаемого под воздействием внешних сил в замкнутом объеме с целью достижения требуемой крупности (менее 5 мм) или степени раскрытия минералов. Как правило, на измельчение поступает материал после дробления крупностью менее 10–25 мм.
В результате измельчения получают продукт, пригодный по крупности для последующего обогащения и содержащий полезные минералы в виде частиц, максимально освобожденных от пустой породы (рис. 20).
Крупность частиц измельченного продукта обычно не превышает 1 мм, а часто с целью полного раскрытия сростков руду измельчают до крупности частиц менее 0,1 мм.
75
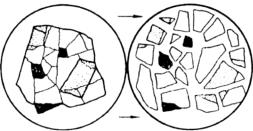
Степень измельчения определяется отношением максимального размера зерен исходного продукта к максимальному размеру зерен измельченного. Степень измельчения может составлять до 250.
аб
Рис. 20. Схема разрушения куска руды при измельчении: а – до измельчения; б – после измельчения
Достижение такой степени измельчения за один прием затруднительно, поэтому измельчение, как и дробление, чаще всего осуществляется в несколько приемов (стадий).
По виду реализации методов разрушения различают механическое измельчение с мелющими телами, пневматическое и аэродинамическое без мелющих тел.
2.4.1. Принцип действия и устройство механических и аэродинамических мельниц
Все измельчительные машины по принципу действия можно разделить на две основные группы: механические мельницы (с мелющими телами) и аэродинамические мельницы (струйные размольные аппараты без мелющих тел).
В свою очередь механические мельницы в зависимости от геометрической формы рабочего корпуса разделяются на барабанные, кольцевые, чашевые и дисковые (рис. 21).
Рабочий корпус барабанных мельниц – футерованный изнутри барабан 1. Мелющими телами 2 служат стальные шары, стержни, галька или крупные куски руды (рис. 21, а).
76
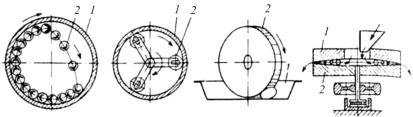
Кольцевые мельницы (рис. 21, б) иногда применяются для сухого измельчения легкоизмельчаемых материалов – угля, фосфоритов и др. Рабочей поверхностью здесь служит внутренняя футеровка кольца 1, а измельчающими телами являются ролики 2 цилиндрической или другой формы, обкатывающие внутреннюю поверхность кольца.
а |
б |
в |
г |
Рис. 21. Механические мельницы
Вчашевой мельнице (рис. 21, в) рабочий корпус – чаша 1, а мелющие тела – бегуны 2, перекатывающиеся по днищу чаши.
Вдисковой мельнице (рис. 21, г) основные рабочие органы неподвижный 1 и подвижный 2 диски.
Аэродинамические (струйные) мельницы в горнорудной про-
мышленности применяются сравнительно редко и исключительно для тонкого и сверхтонкого измельчения материала.
Принцип их действия заключается в том, что частицы материала разгоняются встречными струями сжатого воздуха, перегретого газа и измельчаются в результате соударения друг с другом.
Принципиальная схема струйной мельницы, основанной на разрушении частиц ударом их об отбойную плиту, приведена на рис. 22. Исходный материал, подаваемый через патрубок 9, подхватывается в разгонной трубке 3 потоком газа (поступающим из газопровода 1 через инжектор 2), разгоняется до необходимой скорости и ударяется о размольную плиту 6. Измельченный материал, проходя с газовым потоком через лопасти 5, разделяется в сепараторе под действием центробежных сил на тонкую фракцию, удаляе-
77
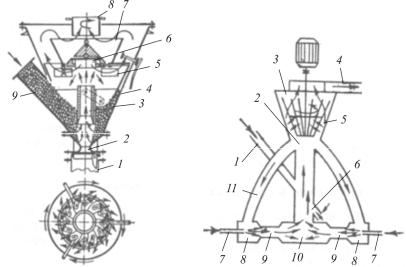
мую через вытеснитель 7 и патрубок 8, и крупную фракцию зерен, которые опускаются по стенкам корпуса 4 и попадают снова в зону измельчения.
Струйная мельница, основанная на разрушении частиц в пересекающихся потоках, показана на рис. 23. Крупная фракция измельчаемого материала через трубы возврата 11, а пар через сопла 7 поступают в смесительные камеры двух эжекторов 5, направленных друг против друга. Проходя через разгонные трубы 9, частицы приобретают скорость 50–100 м/с и, сталкиваясь друг с другом в камере 10, измельчаются. Измельченный материал вместе с исходным материалом, подаваемым через трубу 1, подхватывается газовым потоком и по стояку 2, оснащенным патрубком 6 для подсоса воздуха, подается в сепаратор 3, из которого тонкая фракция удаляется через патрубок 4, а крупная – возвращается по трубам возврата 11 в смесительные камеры эжекторов 8.
Рис. 22. Струйная мельница, |
Рис. 23. Струйная мельница, |
основанная на разрушении частиц |
основанная на разрушении частиц |
ударом их об отбойную плиту |
в пересекающихся потоках |
78 |
|
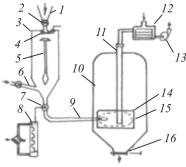
Для измельчения руд, минеральные компоненты которых отличаются по своим упругим свойствам, или для раскрытия пористых, волокнистых, а также пластичных (вязких) руд и материалов, для которых механические методы дробления и измельчения вообще малопригодны, эффективно взрывоструйное измельчение. Процесс взрывоструйного измельчения (процесс Снайдера) основан на распаде кусков руды под действием внутренних сил растяжения при мгновенном снятии с них внешнего давления (рис. 24). Исходный материал из воронки 1 с помощью клапана 2 подается через затвор 4 в камеру 3, оснащенную механизмом 5 для предотвращения зависания в ней материала. После заполнения 0,6–0,8 объема камеры 3,
затвор 4 плотно закрывается и по |
|
трубе 6 подается в течение 5–10 с |
|
пар или газ для создания в камере |
|
давления около 60 кг/см2 (16 МПа). |
|
Затем автоматическим устройст- |
|
вом 8 открывается быстродейст- |
|
вующий (со временем срабаты- |
|
вания 15 · 10–6 с) клапан 7, и ма- |
|
териал из камеры почти со |
|
скоростью звука выбрасывается |
|
по трубопроводу 9 в камеру низ- |
Рис. 24. Принцип действия |
кого давления 10, объем которой |
аппарата для взрывоструйного |
примерно в 50 раз больше, чем |
измельчения |
у камеры 3, а разрежение (около |
|
0,6 кг/см2) создается эксгаустером 13. При выходе из сопла в зону пониженного давления 15 частицы оказываются в состоянии взрыва под действием внутренних сил, что позволяет разделить минералы. Разрушению частиц способствуют также ударные волны, возникающие при столкновении их с отражательной плитой 14. Измельченный материал разгружается через затвор 16, отработанный пар удаляется по выхлопной трубе 11 в конденсатор 12 и затем в эксгаустер 13.
79
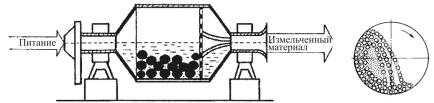
2.4.2. Принцип действия и устройство барабанных мельниц
На обогатительных фабриках и в рудоподготовительных отделениях металлургических предприятий применяются главным образом вращающиеся барабанные мельницы.
Применяемые для измельчения различных материалов барабанные мельницы различаются по форме барабана, характеру среды и измельчающих тел, по способу разгрузки измельченного продукта и по принципу действия.
В зависимости от формы барабана различают мельницы цилиндрические и цилиндроконические. Первые, в свою очередь, классифицируются на три типа: короткие, длинные и трубные. У коротких мельниц длина барабана меньше или равна его диаметру. У длинных длина барабана больше одного, но меньше трех его диаметров. У трубных мельниц длина барабана больше трех диаметров.
Барабанная мельница (рис. 25) представляет собой цилиндрический, иногда цилиндроконический барабан, опирающийся пустотелыми цапфами на подшипники и заполненный до определенного уровня измельчающими телами: стальными шарами, стержнями. При вращении барабана материал вместе с измельчающими телами поднимается на некоторую высоту, а затем скатывается или падает вниз, подвергаясь измельчению за счет ударов и трения в слоях измельчающей среды.
Рис. 25. Принципиальная схема барабанной мельницы
Процесс измельчения материала происходит непрерывно при его движении вдоль барабана от загрузки через пустотелую цапфу до выгрузки из цапфы. Выгрузку продуктов измельчения можно
80