
книги / Обогащение полезных ископаемых
..pdf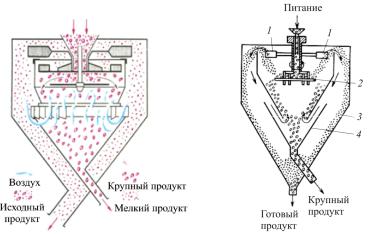
пуса, пульпа получает вращательное движение. Наиболее тяжелые и крупные частицы под действием центробежной силы отбрасываются к стенкам аппарата и нисходящим спиральным потоком движутся вниз к разгрузочной насадке для песков. Мелкие же частицы вместе с водой образуют внутренний поток, который поднимается вверх и выносится через сливной патрубок.
Производительность гидроциклонов и эффективность разделения материала зависят от многих факторов, главные из которых: давление пульпы на входе в гидроциклон; внутренние размеры сечений питающего патрубка, сливной и песковой насадок; диаметр цилиндрической части и угол конусности гидроциклона; плотность пульпы, подаваемой в гидроциклон; характеристика разделяемого материала. С увеличением диаметра гидроциклона увеличивается его объемная производительность. Однако следует учитывать, что чем меньше крупность питания, тем меньше должен быть диаметр гидроциклона.
а |
б |
Рис. 13. Центробежный воздушный сепаратор: а – с внутренней циркуляцией воздуха (вращающимися тарелками); б – с вращающимся диском; 1 – вращающийся диск; 2 – лопасти вентилятора; 3 – наружный конус; 4 – внутренний конус
61
На практике четкость разделения при классификации нарушается циркуляционным движением потока, перемешиванием частиц его турбулентными вихрями и другими технологическими причинами. Поэтому в песках всегда присутствуют мелкие частицы, а в сливе – часть крупных частиц.
Аналогичным образом происходит классификация частиц в потоке воздуха (рис. 13).
2.3.Дробление
2.3.1.Теоретические основы дробления
Дробление и измельчение – процессы разрушения полезных ископаемых под действием внешних сил до заданной крупности, требуемого гранулометрического состава или необходимой степени вскрытия минералов. При дроблении и измельчении не следует допускать переизмельчения материала, так как это ухудшает результаты обогащения (тонкие частицы крупностью менее 10 мкм обогащаются неудовлетворительно) и удорожает процесс. Необходимо соблюдать принцип «не дробить ничего лишнего».
Процессы дробления и измельчения могут быть подготовительными операциями (например, на обогатительных фабриках перед обогащением полезного ископаемого) или иметь самостоятельное значение (дробильно-сортировочные фабрики, дробление и измельчение угля перед коксованием, перед пылевидным его сжиганием и т.д.).
Процессы дробления и измельчения принципиально не различаются между собой. Раскрытие минералов при дроблении и измельчении происходит вследствие разрушения кусков горных пород под действием внешних нагрузок. Для разрушения кусков руды необходимо преодолеть силы сцепления между отдельными кристаллами и внутри кристаллов. Эти силы определяют прочность горных пород, которая зависит от дефектов внутренней структуры, например, наличия внутренних ослабленных зон (трещин, включений). Условно принято считать дроблением такой процесс разрушения,
62

в результате которого получаются продукты крупностью более 5 мм, измельчением – менее 5 мм. Первый вид разрушения осуществляется в дробилках, второй – в мельницах.
При дроблении и измельчении применяют следующие способы разрушения: раздавливание, раскалывание, излом, срез, истирание и удар.
Рис. 14. Способы дробления полезных ископаемых
Способы дробления и измельчения отличаются видом основной необратимой деформации:
раздавливание (рис. 14, а) – разрушение в результате сжатия куска между двумя дробящими поверхностями, наступающее после перехода напряжений за предел прочности на сжатие;
раскалывание (рис. 14, б) – разрушение в результате расклинивания куска между остриями дробящих поверхностей и последующего его разрыва;
излом (рис. 14, в) – разрушение куска в результате его изгиба при ребристой форме дробящих поверхностей;
срез (рис. 14, г) – разрушение, при котором материал подвергается деформации сдвига;
истирание (рис. 14, д) – разрушение кусков скользящей рабочей поверхностью машины, при котором внешние слои куска под-
63
вергаются деформации сдвига и постепенно срезаются вследствие перехода касательных напряжений за пределы прочности;
удар (рис. 14, е) – разрушение куска в результате воздействия динамических кратковременных нагрузок. Дробление ударом приводит к разрушению прежде всего по трещинам и поверхностям соприкосновения зерен отдельных компонентов.
В зависимости от свойств горных пород (прочность, хрупкость, вязкость и др.) выбирается наиболее эффективный способ внешнего силового воздействия на куски породы с целью их дробления. Например, для прочных и не хрупких пород наилучшим способом разрушения может быть раздавливание или удар. При наличии в хрупкой породе большого числа трещин предпочтительнее разрушение ударом, однако при большой вязкости пород эффективность действия удара резко снижается.
На выбор способа дробления влияют также ценность полезного ископаемого и требования к качеству дробленого продукта. Если, например, руда содержит хрупкие и ценные полезные минералы, то при ее дроблении необходимо максимально исключить эффект истирания, приводящий к переизмельчению руды и образованию труднообогатимых шламов.
По технологическому назначению различают три вида процес-
сов дробления:
1)самостоятельное – продукты дробления являются конечными (товарными) и не подвергаются дальнейшей обработке. Например, дробление углей, горных пород для получения щебня и др.;
2)подготовительное – продукты дробления получают заданной крупности и подвергают последующей переработке. Например, дробление руд для последующего обогащения;
3)избирательное – один из компонентов материала отличается незначительной прочностью и разрушается эффективнее другого,
сих последующим разделением по крупности.
Степень дробления (или измельчения) показывает степень сокращения крупности в процессе разрушения кускового материала. Она характеризуется отношением размеров максимальных кусков
64
в дробимом и дробленом материале или, что более точно, отношением средних диаметров до и после дробления. Различают следующие стадии дробления в зависимости от исходной и конечной крупности дробимого материала: крупное (100–200 мм), среднее (25– 80 мм), мелкое (до 3–25 мм).
Классификация процессов и дробильно-измельчительных ма-
шин осуществляется по способу разрушения материала, который определяется видом используемой для разрушения энергии. Различают следующие способы:
механический, осуществляемый за счет использования механических сил;
пневматический (взрывной) – использование энергии пара или сжатого воздуха;
электрогидравлический, электроимпульсный, электротермический – использование электроэнергии;
аэродинамический (струйный) – использование энергии струи газа, разгоняющей куски материала перед их столкновением;
ультразвуковой, осуществляемый за счет использования энергии ультразвука, вызывающей резонансные колебания в кусках материала и их разрушение.
На обогатительных фабриках для дробления различных полезных ископаемых применяют почти исключительно механические дробилки раздавливающего и раскалывающего (щековые, конусные, валковые),
атакжеударного (молотковые, роторные, дезинтегральные) действия.
2.3.2. Классификация дробильных машин
За основу классификации дробильно-измельчительных машин и устройств принимают принцип их действия, т.е. способ разрушения, который определяется видом энергии, непосредственно используемой для разрушения материала.
Дробилки по принципу действия делятся на следующие типы
(рис. 15):
1. Дробилки преобладающего статического действия: щековые – с простым и со сложным движением щеки; конусные – с под-
65
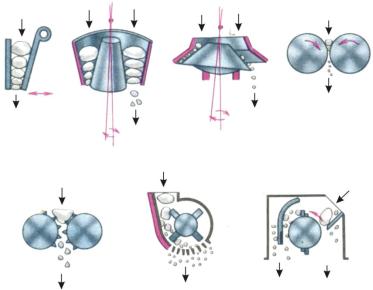
весным валом (ККД, КРД), с консольным валом (КСД, КМД); валковые – двухвалковые с гладкими валками, двух- и четырехвалковые с зубчатыми валками и одновалковые с зубчатым или с желобчатым валком.
2. Дробилки динамического действия: ударные – молотковые, роторные и стержневые; с безударным ротором – центробежные однодисковые и центробежные многодисковые.
а |
б |
в |
г |
д |
е |
ж |
Рис. 15. Принципиальные схемы дробилок: а – щековая; б – конусная крупного дробления; в – конусная среднего и мелкого дробления; г – валковая; д – валковая зубчатая; е – молотковая; ж – роторная
На обогатительных фабриках большой производительности для крупного, среднего и мелкого дробления руд наиболее широко применяются конусные дробилки, отличающиеся высокой производительностью и действующие в основном по принципу раздавливания, частично – по принципу истирания и изгиба. На фабриках средней производительности вместо конусных применяются щековые дро-
66
билки, отличающиеся более низкой производительностью. Когда требуется высокая степень дробления при невысокой производительности, применяются валковые дробилки с гладкими валками. Для мягких руд при необходимости получения как можно более низкого выхода мелочи применяют валковые зубчатые дробилки. Все более широкое распространение для дробления самых различных по крепости полезных ископаемых приобретают дробилки ударного действия, обеспечивающие наиболее высокую степень дробления.
При выборе дробилки учитывают крупность исходного материала, требуемый гранулометрический состав продукта дробления и необходимую производительность.
Схемы дробления. Дробимость является обобщающим параметром многих механических свойств горных пород (упругих, прочностных, пластических и др.) и выражает энергоемкость процесса дробления породы.
Операции дробления применяются, как правило, для подготовки полезного ископаемого к измельчению и лишь в отдельных случаях, когда полезное ископаемое характеризуется крупной вкрапленностью ценных минералов, – непосредственно к операциям обогащения. На дробильно-сортировочных фабриках дробление имеет самостоятельное значение.
Дробление является весьма энергоемким процессом, на который расходуется около половины энергозатрат. В материалах, подлежащих дроблению, всегда имеются куски (зерна) мельче того размера, до которого идет дробление в данной стадии. Такие куски целесообразно выделить из исходного материала перед дробильными машинами на грохотах.
Дробилки могут работать в открытом и замкнутом циклах с грохотами. Открытый цикл дробления – это дробление материала без последующего грохочения или без возвращения крупного продукта в дробильное оборудование. Замкнутый цикл дробления – это дробление материала, осуществляемое с последующим грохочением, после чего крупный продукт непрерывно возвращается обратно в дробильное оборудование.
67
При открытом цикле материал проходит через дробилку один раз, и в дробленом продукте всегда присутствует некоторое количество кусков избыточного размера. При замкнутом цикле материал неоднократно проходит через дробилку. Дробленый продукт поступает на грохот, выделяющий из него куски избыточного размера, которые возвращаются для додрабливания в ту же дробилку.
Если грохочение предшествует дроблению, то оно называется
предварительным, а если после дробления, то поверочным (кон-
трольным). При возвращении продукта дробления на предшествующую операцию грохочения последнюю называют совмещенной операцией предварительного и поверочного грохочения.
2.3.3. Принцип действия и устройство щековых дробилок
Щековые дробилки используют в основном для крупного и среднего дробления. В щековой дробилке (см. рис. 15, а) материал разрушается путем раздавливания в сочетании с раскалыванием и изгибом между неподвижной и подвижной щеками. Подвижная щека приближается (при рабочем ходе) или отходит (при холостом ходе) от неподвижной щеки при вращении эксцентрикового вала. Во время рабочего хода происходит дробление, а во время холостого – выгрузка дробленого материала вниз под действием собственного веса. Ширина выпускного отверстия и, следовательно, степень дробления регулируются путем взаимного перемещения клиньев.
В зависимости от расположения оси подвижной щеки различают щековые дробилки с верхним и нижним подвесом этой щеки.
На рис. 16 представлен принцип действия и общий вид щековой дробилки с верхним подвесом подвижной щеки 2. Дробилки этого типа наиболее широко распространены в промышленности. Корпус 1 дробилки, передняя стенка которого является неподвижной щекой, выполняется обычно из стального литья, а щеки 2 футеруются стальными плитами с рифленой рабочей поверхностью. Эти плиты наиболее сильно изнашиваются, вследствие чего они выполняются съемными и изготавливаются из износостойкого материала (литой марганцовистой или хромистой стали).
68
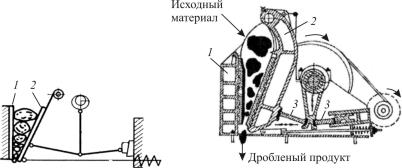
а |
б |
Рис. 16. Принцип действия (а) и общий вид щековой дробилки (б): 1 – неподвижная щека; 2 – подвижная щека; 3 – распорные плиты
Дробящее усилие в дробилке передается через распорные плиты 3. Поэтому вкладыши, в которые входят концы плит, делаются сменными из материала большой твердости. Задняя распорная плита используется для предохранения дробилки от поломок при попадании в рабочее пространство недробимых предметов. Эта плита изготавливается с пониженной прочностью и ломается при попадании
вдробилку случайных металлических предметов.
Взависимости от кинематической схемы привода дробилки с верхним и нижним подвесом щеки могут быть двух типов: с простым и сложным движением щеки.
Степень дробления материала в щековых дробилках обычно составляет от 3 до 4. Ее можно регулировать изменением ширины разгрузочного отверстия.
2.3.4. Принцип действия и устройство конусных дробилок
Конусные дробилки предназначают для крупного (ККД), среднего (КСД) и мелкого (КМД) дробления. Дробление материала в конусных дробилках осуществляется в кольцевом пространстве между неподвижным корпусом 2 и расположенным внутри его подвижным (дробящим) конусом 1 (рис. 17). Ось вращения подвижного конуса незначительно наклонена к оси неподвижного конуса, что обеспечи-
69
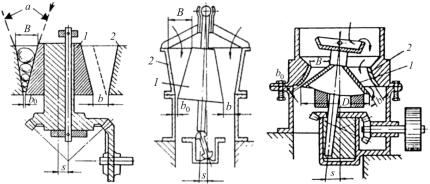
вает определенное значение эксцентриситета. Поэтому при движении по эксцентриситету подвижный конус совершает гирационное движение внутри неподвижного конуса, приближаясь или удаляясь на каждые пол-оборота к той или иной расположенной напротив стороне неподвижного конуса. Подвижный конус, как бы обкатывая внутреннюю поверхность неподвижного конуса, производит дробление крупных кусков в результате их раздавливания, а также частично истирания и разламывания вследствие криволинейной формы дробящих поверхностей. Исходный материал загружается сверху в пространство между подвижным 1 и неподвижным 2 конусами, а разгрузка дробленого продукта осуществляется вниз под дробилку через отверстие, образующееся во время отхода подвижного конуса от неподвижного.
а |
б |
в |
Рис. 17. Принцип действия общий вид конусной дробилки: а – конусная дробилка с неподвижной осью (ККД); б – то же, с подвесным валом (ККД «гирационная»); в – то же, с консольным валом, опирающимся на шаровой подпятник (КСД и КМД); 1 – подвижный конус; 2 – неподвижный конус (корпус); В – ширина приемного отверстия; b – ширина разгрузочного
отверстия; а – угол захвата
Главными различиями конусных дробилок для крупного, среднего и мелкого дробления являются: профиль их рабочего пространства; кинематика движения рабочего конуса и способ его опирания;
70