
книги / Сварка и свариваемые материалы. Свариваемость материалов
.pdfм
ю
Марка
стали
25ХГСА
ЗОХГСА
25ХГСА
ЗОХГСА
12Х2НВФА
23Х2НВФА
ЗОХГСНА
ЗОХГНСА
ЗОХГСНА
ПРИСАДОЧНЫЕ МАТЕРИАЛЫ ПРИ СВАРКЕ ПОД ФЛЮСОМ И МЕХАНИЧЕСКИЕ СВОЙСТВА СВАРНЫХ СОЕДИНЕНИЙ
|
|
|
Электродная проволока |
|
с в МПа |
| кси, |
|
Термическая обработка |
|
Марка |
|
Дж/см2 |
|||
|
флюса |
|
|
||||
|
|
|
Марка |
ГОСТ или ТУ |
|
не менее |
|
Закалка |
и |
отпуск |
после Св-18ХГС, Св-18ХМА |
2246—70 |
АН-15 |
0,9 ав основно |
50 |
сварки |
на |
а в |
1200 ± |
|
АН-15М |
го металла |
|
±100 МПа
То же, |
до сварки |
Св-08Х21Н10Г6, |
2246—70 |
АН-22 |
600 |
90 |
|
|
|
|
Св-08Х20Н9Г7Т, |
|
АН-22М |
|
|
|
|
|
Св-ЮХ I6H25AM6 |
|
|
|
|
Сварка |
в упрочненном со |
Св-18ХМА |
2246—70 |
АН-15 |
0,9 ав основ |
60 |
|
стоянии при а в^ 1 150 МПа |
|
|
|
ного металла |
|
||
без |
последующей термиче |
|
|
|
|
|
|
ской |
обработки |
|
|
|
|
|
|
Закалка и отпуск на ав = |
0Х4МА |
ЧМТУ |
АН-15 |
1200 |
40 |
||
= 1600-^-1800 МПа после |
|
ЦНИИЧМ |
АН-15М |
1355 |
65 |
||
сварки |
|
|
1033—63 |
|
|
|
|
То же |
|
Св-18ХМА |
2246—70 |
АН-15 |
900 |
60 |
|
То же, до сварки |
Св-08Х21Н10Г6, |
2246—70 |
АН-22 |
600 |
90 |
||
|
|
|
Св-08Х20Н9Г7Т, |
|
АН-22М |
|
|
|
|
|
Св-10Х16Н25АМ6 |
|
|
|
|
Подкладные кольца и замковые соединения для сталей, на пример ЗОХГСНА, не рекомендуются, так как они снижают на дежность изделия в эксплуатации. Вместо подкладных колец первые слои целесообразно выполнять аргонодуговой сваркой на весу. Электродную проволоку и флюс для сварки конструк ционных сталей выбирают согласно табл. 11.9. Для предотвра щения пористости и наводораживания швов флюсы перед сваркой необходимо прокаливать, чтобы их влажность не пре вышала 0,1% для стекловидных флюсов и 0,05% для пемзо видных. Это достигается нагревом стекловидных флюсов до
Спорость сварки, м/ч
Рис. 11.11. Влияние скорости сварки на ширину зоны закалки (а), долю участия ос
новного металла в |
шве (б), глубину проплавления (в): / — однодуговая сварка; 2 — |
|
двудуговая сварка; |
3 — двудуговая сварка |
форсированный режим; 4 — однодуговая |
|
сварка с подогретой присадкой |
|
350—-400 °С, а |
пемзовидных до |
400—500 °С с выдержкой 2— |
3 ч. Максимальная температура |
нагрева под прокалку приме |
няемых флюсов (табл. 11.9 )не должна превышать 650—700 °С во избежание окисления компонентов флюса и его спекания.
В случае сварки |
жестких узлов ферритными |
проволоками, |
а также соединений |
сталей ЗОХГСА, ЗОХГСНА, |
40ХГСНЗМА |
и др. большой толщины применяют подогрев 150—300 °С. Не посредственно после сварки ферритными проволоками во всех
случаях |
необходим общий |
или местный отпуск при 600— |
650 °С |
для предупреждения |
образования холодных трещин. |
Сварку аустенитными материалами производят без предвари тельного подогрева и последующей термообработки соединений.
Узлы в виде толстостенных труб различного диаметра из сталей ЗОХГСНА и 40ХГСНЗМА, предназначенные для ответ ственных силовых конструкций, изготавливают многослойной сваркой под флюсом АН-15 и АН-15М проволокой Св-20Х4ГМА диаметром 2,5—3 мм.
Дальнейшее существенное увеличение производительности возможно при сварке с применением двух и более проволок.
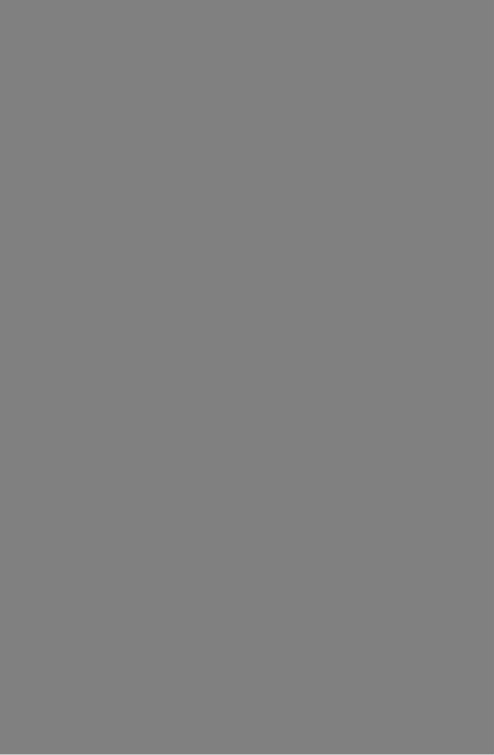
12.1.2, Химический состав, термообработка и структура
В соответствии с условиями длительной работы под напряжением при вы соких температурах стали должны обладать сопротивлением ползучести, длительной прочностью, стабильностью свойств во времени и жаростой костью, Перечисленные свойства с учетом необходимости обеспечения тех нологичности сталей при выплавке, отливке, ковке, прокатке, термической
обработке |
и сварке достигаются введением в их |
состав |
0,5—2,0 % |
Сг, |
0,2— 1,0 % |
Мо, 0,1—0,3% V, а также в некоторых |
случаях |
небольших |
до |
бавок редкоземельных элементов и В.
Легирование Сг повышает жаростойкость сталей, т. е. сопротивление их окислению, а также предотвращает графитизацию в процессе эксплуатации при температуре выше 450 °С. Сг в пределах 1,0— 1,5 % при введении его в сталь совместно с Мо повышает, кроме того, ее длительную прочность и
сопротивление |
ползучести. |
Поло |
|
|
|
|
Т А Б Л И Ц А |
П Л |
|||||||
жительное |
влияние Мо |
на |
увели |
|
|
|
|
||||||||
ДЛИТЕЛЬНАЯ ПРОЧНОСТЬ ПРИ |
|
||||||||||||||
чение прочности стали при по |
|
||||||||||||||
РАЗЛИЧНЫХ ТЕМПЕРАТУРАХ |
|
||||||||||||||
вышенных |
температурах |
его |
в |
|
|||||||||||
количествах |
0,5— 1,0 % |
объясня |
|
|
Предел длительной |
|
|||||||||
ется |
способностью |
|
повышать |
|
|
прочности, |
МПа, |
|
|||||||
температуру |
рекристаллизации |
Марка стали |
|
при температуре, °С |
|
||||||||||
железа |
и |
участием |
в |
образова |
|
450 |
500 |
550 |
565 |
580 |
600 |
||||
нии упрочняющей |
металл |
фазы |
|
||||||||||||
|
|
|
|
|
|
|
|
||||||||
Лавеса Fe2Mo. V совместно с |
С |
15ХМ |
265 |
137 |
63 |
|
|
|
|
||||||
обеспечивает |
упрочнение |
стали |
78 |
59 |
|
||||||||||
высокодисперсными |
|
карбидами |
12Х1МФ |
— |
157 |
88 |
— |
||||||||
VC и |
способствует |
стабилизации |
15Х1М1Ф |
— |
186 |
108 |
88 |
68 |
— |
||||||
карбидной |
фазы |
как |
элемент, |
12Х2МФСР |
— |
— |
— |
— |
88 |
68 |
|||||
обладающий |
значительным |
срод |
|
|
|
|
|
|
|
|
|||||
ством |
к углероду. |
|
|
механических свойств изделий из |
перлитных |
||||||||||
Оптимальное сочетание |
|||||||||||||||
жаропрочных |
сталей достигается |
применением нормализации |
(или |
закалки) |
с последующим высокотемпетурным отпуском. При этом обеспечивается струк тура, состоящая из дисперсной ферритокарбидиой смеси. У хромомолибдено ванадиевых сталей, особенно в случае применения закалки, появляется бейнитная структурная составляющая.
С в о й с т в а с т а л е й Необходимая жаростойкость и достаточная стабильность кратковременных
механических свойств |
в течение |
100 000 ч ( ~ 1 0 лет) |
обеспечиваются |
для |
|||||
сталей 12МХ и 15ХМ при температуре |
эксплуатации |
до |
550 |
°С, для сталей |
|||||
12Х1МФ, 15Х1М1Ф, |
15Х1М1ФЛ |
до |
570 °С и для |
стали |
12Х2МФСР |
до |
|||
600 °С. Значения пределов |
длительной |
прочности |
сталей |
на |
базе 105 ч |
при |
|||
различных температурах [1, |
2] приведены в табл. |
12.1. |
|
|
|
|
12.2. Свариваемость сталей
Металлургическая свариваемость жаропрочных перлитных ста лей, определяемая отношением металла к плавлению, метал лургической обработке и последующей кристаллизации шва. не вызывает существенных осложнений. Технология сварки и сварочные материалы на современном уровне обеспечивают не обходимую стойкость металла шва против образования-горячих трещин и высокие характеристики, предъявляемые к основному металлу.
Тепловая же свариваемость осложняется склонностью свар ных соединений к образованию холодных трещин и разупрочне нием свариваемого металла в зоне термического влияния сварки.
12.2.1. Сопротивляемость XT
Холодные трещины — хрупкие разрушения сварных соединений жаропрочных перлитных сталей, могут возникать в процессе сварки или непосредственно после ее окончания в результате образования метастабильных структур (троостита, мартенсита) в участках околошовной зоны, нагретых вышетемпературы Ас3 вследствие дополнительного охрупчивания сварных соеди нений под влиянием водорода и действия «силового» фактора. Последний определяется величиной и характером сварочных напряжений. Суммирование напряжений, вызванных неравно мерным нагревом и структурными превращениями, может при вести к исчерпанию пластичности охрупченных участков свар ного соединения и вызвать его разрушение.
Образование метастабильных закалочных структур в около шовной зоне определяется во многом системой легирования ста лей. Так, в одних и тех же условиях сварки хромомолибдено ванадиевые стали в большей степени склонны к образованию холодных трещин по сравнению с хромомолибденовыми.
В связи с тем, что растворимость диффузионно подвижного водорода при нормальной температуре в низколегированных сталях мала, а между его концентрацией и равновесным парци альным давлением в газовой фазе существует квадратичная зависимость, водород способен создавать в несплошностях ме талла значительные давления, что может приводить к образо ванию микротрещин (флокенов) в охрупченных участках свар ного соединения. Так, при температуре 20 °С и концентрации водорода в металле 5 мл/100 г давление его в несплошностях жаропрочной перлитной стали может достигать 0,0981 • 10® МПа (10е ат). При 200 °С давление водорода в несплошностях сни жается примерно на три порядка [3]. В связи с этим для сварки рекомендуется использовать низководородные сварочные мате риалы (электроды с основным покрытием, осушенные защитные газы, прокаленные флюсы).
Действие «силового» фактора во многом определяется жест костью сварной конструкции, которая связана с толщиной сва риваемых элементов. Это обстоятельство также необходимо учитывать при выборе методов предотвращения образования холодных трещин.
Одним из наиболее надежных средств предотвращения воз никновения холодных трещин является сопутствующий сварке
местный или общий подогрев изделия. Подогрев уменьшает раз ницу температур металла в зоне сварки и на периферийных участках, что снижает напряжения первого рода, вследствие чего пики этих напряжений в околошовных участках металла сглаживаются. Подогрев также уменьшает скорость охлажде ния металла, что предотвращает превращение аустенита в мар тенсит, которое сопровождается резким увеличением удельного объема металла, вызывающим появление структурных напря жений.
Повышение температуры свариваемого металла способст вует эвакуации водорода из сварного соединения в связи со значительным увеличением диффузионной подвижности водо рода.
Кроме того, повышение температуры металла при любом его структурном состоянии увеличивает его пластичность, а сле довательно, и деформационную способность. Повышение пла стичности сварного соединения имеет такое же важное значение для предотвращения образования холодных трещин, как и сни жение напряжений, поскольку трещины образуются в резуль тате исчерпания деформационной способности металла под дей ствием напряжений.
При сварке теплоустойчивых сталей необходимо ограничи вать не только'нижний, но и верхний предел температур подо грева. Излишне высокие температуры подогрева приводят к распаду аустенита в высокотемпературной области с образо ванием грубой феррито-перлитной структуры, не обеспечиваю щей необходимую длительную прочность и ударную вязкость сварных соединений.
Поскольку перераспределение напряжений и структурные превращения могут происходить и после окончания сварки, в некоторых случаях необходимы дополнительные меры, пре дотвращающие образование холодных трещин в сварных со единениях. К ним, например, относится выдержка сварных соединений после окончания сварки при 150—200 °С в течение несколькиих часов для завершения превращения остаточного аустенита и эвакуации водорода.
12.2-2. Разупрочнение в зоне термического влияния
Применение в качестве термической обработки сталей норма лизации (или закалки) с последующим отпуском осложняет их свариваемость в связи с возникновением в зонах термического влияния сварки участков разупрочнения, где металл был на грет в интервале температур Ас3— температура отпуска стали. Кратковременные прочностные свойства сварных соединений при этом снижаются по сравнению с основным металлом на 5—10 %, а длительная прочность может быть снижена на 20 %,
если стали упрочнялись закалкой, например для паропроводной стали 12Х1МФ. Степень разупрочнения зависит не только от ре жимов термической обработки стали, но и от параметров про цесса сварки. Повышение погонной энергии процесса сварки вызывает большее разупрочнение свариваемой стали.
Мягкая разупрочненная прослойка в зоне термического влияния сварки может явиться причиной локальных разруше ний жестких сварных соединений в процессе эксплуатации, осо бенно при изгибающих нагрузках.
Разупрочнение металла околошовной зоны могло бы быть устранено перекристаллизацией при применении вместо от пуска сварных соединений нормализации с отпуском. Однако высокотемпературная термическая обработка сварных соеди нений не может быть подобно отпуску осуществлена местно, так как это приводит к разупрочнению близлежащих участков ме талла, а объемная термическая обработка сварных конструк ций ограничивается габаритными размерами печей и рядом других трудностей.
12.2.3. Изменение свойств в зоне сплавления при эксплуатации
При температурах эксплуатации 450—600 °С следует считаться с возможностью развития диффузионных процессов между ос новным металлом и металлом шва. В первую очередь это отно сится к углероду, который является одним из наиболее диф фузионно подвижных элементов, входящих в состав металла. Миграциия углерода из стали в шов или наоборот может на блюдаться даже при небольшом различии в легировании их карбидообразующими элементами (например, стал 12Х1МФ — шов 10ХЗМ1БФ). Образование в процессе эксплуатации обезуглероженной (ферритной) прослойки по одну сторону линии сплавления и карбидной гряды по другую приводит к снижению длительной прочности и пластичности сварного соединения и, как следствие, к локальному (по зоне сплавления) разруше нию.
Всвязи с этим сварочные материалы, предназначенные для сварки жаропрочных перлитных сталей, должны обеспечивать химический состав металла шва, близкий к химическому со ставу основного металла.
Вотдельных случаях при необходимости отказаться от по догрева и термической обработки (отпуска) сварных соедине ний могут быть использованы сварочные материалы, обеспе чивающие получение металла шва на никелевой основе (покры тые электроды ЦЛ-Зб, проволока для аргонодуговой сварки Св-08Н60Г8М7Т). Возможность применения этих сварочных
материалов основана на том, что диффузионная подвижность
элементов в сплавах на никелевой основе при 450—600 °С зна чительно меньше, чем в низколегированных сталях перлитного класса.
12.3. Технология сварки и свойства сварных соединений
Основными способами сварки, используемыми при изготовлении конструкций из жаропрочных перлитных сталей, являются ду говая и электроконтактная. Электроконтактная сварка исполь зуется в основном для выполнения стыковых соединений труб поверхностей нагрева котлов в заводских условиях. В подав ляющем большинстве других случаев используется дуговая сварка покрытыми электродами, в защитных газах и под флю сом.
Общими рекомендациями по всем видам дуговой сварки яв ляются: оптимальная подготовка свариваемых кромок, тепло вые условия сварки и режимы термической обработки сварных соединений.
Подготовка кромок деталей под сварку производится с по мощью механической обработки. Допускается применение кис лородной или плазменно-дуговой резки с последующим удале нием слоя поврежденного металла толщиной не менее 2 мм.
Дуговую сварку производят при температуре окружающего воздуха не ниже 0 °С с предварительным и сопутствующим сварке местным или общим подогревом. Пределы изменения температуры подогрева в зависимости от марки стали и тол щины свариваемого изделия приведены в табл. 12.2.
ТАБЛИЦА 12.2
ТЕМПЕРАТУРА ПРЕДВАРИТЕЛЬНОГО И СОПУТСТВУЮЩЕГО ПОДОГРЕВА
Марка стали |
Толщина сваривае |
Температура подо |
||
мых деталей, мм |
грева, |
°С |
||
12МХ, 12ХМ, |
15ХМ |
< 1 0 |
|
|
|
|
10—30 |
150—300 |
|
|
|
> 3 0 |
2 0 0 -350 |
|
2ХМЛ, 12Х1МФ |
< 6 |
— |
|
|
|
|
6—30 |
200—350 |
|
|
|
> 3 0 |
250—400 |
|
15Х1М1Ф, 20ХМФЛ, |
15Х1М1ФЛ |
< 6 |
— |
|
|
|
6—30 |
250—400 |
|
|
|
Свыше 30 |
3 0 0 -450 |
|
|
|
|
1 |
|
П р и м е ч а н и я : 1. |
При многопроходной автоматической |
сварке под |
флюсом |
|
Допускается снижение минимальной температуры подогрева на 50 °С. |
|
|||
2. Аргонно-дуговую сварку корневого слоя труб допускается |
выполнять без подо |
|||
грева. |
|
|
|
|
Без термической обработки сварные соединения жаропроч ных перлитных сталей не обладают эксплуатационой надеж ностью ввиду структурной неоднородности и наличия остаточ ных сварочных напряжений. Поэтому большинство сварных конструкций подвергают термической обработке. Исключение составляют сварные соединения из хромомолибденовых сталей толщиной менее 10 мм и из хромомолибденованадиевых сталей при толщине менее 6 мм.
При изготовлении конструкций из жаропрочных перлитных сталей используют обычно отпуск. Его преимущество заключа ется в том, что он может быть использован в качестве местной термической обработки. Отпуск стабилизирует структуру (твер дость) сварного соединения и снижает остаточные напряжения. С увеличением содержания хрома, молибдена, ванадия и дру гих элементов, повышающих релаксационную стойкость сталей, температура отпуска и время выдержки должны увеличиваться. Особую опасность представляет отпуск сварных соединений хромомолибденованадиевых сталей при пониженных темпера турах в связи с возможностью дисперсного твердения, вызван ного выпадением в околошовной зоне карбидов ванадия и об разованием трещин при термической обработке. Недостатком отпуска является невозможность полного выравнивания струк туры, в частности устранения разупрочненной прослойки в зоне термического влияния сварки. Последнее может быть достиг
нуто, как уже отмечалось выше, |
применением печной термиче- |
||||||
|
|
|
|
|
Т А Б Л И Ц А 12.3 |
||
РЕЖИМЫ ОТПУСКА СВАРНЫХ СОЕДИНЕНИЯ. ВЫПОЛНЕННЫХ |
|||||||
|
|
|
ДУГОВОЙ СВАРКОЙ |
|
|
||
|
Толщина |
Минималь |
|
Толщина |
Минимальная |
||
|
ная продол |
|
|||||
|
сваривае |
|
сваривае |
продолжи |
|||
Марка стали |
жительность |
Марка стали |
|||||
мых |
|
мых дета |
тельность |
||||
|
деталей, |
мм |
выдержки, |
|
лей, мм |
выдержки, ч |
|
|
ч |
|
|||||
|
|
|
|
|
|
Отпуск, 7\ °С = 715± 15
12МХ |
10 |
|
12ХМ |
1 0 -2 0 |
1 |
15ХМ |
20—40 |
2 |
20ХМЛ |
4 0 -8 0 |
3 |
|
> 8 0 |
4 |
Т, |
°С = 735± 15 |
— |
12Х1МФ |
< 6 |
|
20ХМФЛ |
6 - 1 0 |
1 |
|
1 0 -2 0 |
2 |
|
ю 0 1 О |
|
40—80 |
|
> 8 0 |
|
т\ °С 745±15 |
15Х1М1Ф |
< 6 |
15Х1М1ФЛ |
6 - 1 0 |
12Х2МФСР |
10—20 |
|
20—40 |
4 0 -8 0 > 8 0
3
4
5
_
1
2
3
5
7
П р и м е ч а н и е . Скорость нагрева сварных соединений из хромомолибденованадневых сталей в интервале Б00—700 °С должна быть не менее 60 °С/ч.
ской обработки всей конструкции, что в большинстве случаев не представляется возможным. Рекомендуемые режимы отпуска сварных соединений, выполненных дуговой сваркой, приведены в табл. 12.3.
12.3.1. Сварка покрытыми электродами
Для ручной дуговой сварки жаропрочных перлитных сталей используются электроды с основным (фтористо-кальциевым) покрытием, изготовленные на малоуглеродистой сварочной про волоке с введением легирующих элементов через покрытие. Ос новной тип покрытия обеспечивает повышенную раскисленность металла шва при малом содержании в нем водорода и неметал лических дисперсных включений, а также достаточно надежную газовую защиту плавящегося металла от азота воздуха. Это позволяет получить сочетание высоких прочностных и пласти ческих свойств швов. Однако для электродов с покрытием этого типа характерна повышенная склонность к образованию пор в швах при удлинении дуги, наличии ржавчины на поверхности свариваемых кромок и небольшом увлажнении покрытия. В связи с этим рекомендуются сварка предельно короткой ду гой, тщательная очистка свариваемых поверхностей и сушка электрода перед их применением. Электроды малого диаметра (ЦЛ-38, ЦЛ-39), используемые в основном для монтажной сварки труб поверхностей нагрева котлов, отличаются повы шенной надежностью газовой защиты плавящегося металла, что позволяет обеспечить плотные швы в условиях, когда поддер живать короткую дугу достаточно сложно.
Для сварки хромомолибденовых сталей 12МХ, 15ХМ и 20ХМЛ используются электроды типа Э-09Х1М (ГОСТ 9467—75) марок ЦУ-2ХМ диаметром 3 мм и более и электроды ЦЛ-38 диаметром 2,5 мм.
Для сварки хромомолибденованадиевых сталей 12Х1МФ, 15Х1М1Ф, 20ХМФЛ и 15Х1М1ФЛ — электроды типа Э-09Х1МФ марок ЦЛ-20, ЦЛ-45 диаметром 3 мм и более и электроды ЦЛ-39 диаметром 2,5 мм.
Сварка осуществляется на постоянном токе обратной поляр ности. Сила сварочного тока выбирается в зависимости от диа метра электрода и положения шва в пространстве. Сварка осу ществляется узкими валиками без поперечных колебаний элек трода с тщательной заваркой кратера перед обрывом дуги.
В отдельных' случаях, когда применение подогрева свари ваемых изделий и последующей термической обработки свар ных соединений невозможно или необходима сварка перлитных жаропрочных сталей с аустенитными, допускается использова ние электродов на никелевой основе марки ЦТ-36 или аргонодуговой сварки проволокой Св-08Н60Г8М7Т.