
книги / Сварка и свариваемые материалы. Свариваемость материалов
.pdfЕсли, например, критическая скорость растяжения VKp со ставляет 9 мм/мин, L < 1 0 MM (ширина шва), а скорость охлаж
дения гг» =100 |
°С/с, то критический темп растяжения равен |
Вкр _ Г КР_ . |
= 1 ,5 -10-4 %/°С. |
W |
60-100-10 |
Для испытания металла шва в условиях многопроходной сварки применяют образцы, которые сваривают швом испытуе мого состава без растяжения, с последующим переплавом этого шва неплавящимся электродом на Vs часть его высоты и растяжением в процессе переплава до появления ГТ в непереплавленной части шва путем прямого или обратного изгиба образцов.
Испытания растяжением с имитацией термического цикла проводят в фазе -охлаждения до 2/з Tmzx на стержневых или пластинчатых образцах, подвергнутых электроконтактному или индукционному нагреву. Рабочая зона таких образцов может иметь строение основного металла или строение сварного шва. Главная особенность таких испытаний — назначение темпера туры максимального нагрева. Она должна соответствовать ми нимальной температуре, при которой достигается оплавление границ зерен по их периметру. Это устанавливают по темпера туре практической потери сопротивления деформированию. По ГОСТ 26 389—84 регламентируется для стали определение Тшах по температуре снижения прочности до 0,15 кг/мм2 путем нагрева под указанным напряжением и фиксировании темпера туры разрушения. Окончание деформации — при 2k T max. Вто рая особенность испытания при имитации — учет дилатации образца в ТИХ при определении показателей VKP и Вкр.
Испытания образцов в ТИХш проводят в изотермических условиях, с оценкой пластических свойств и сопротивления деформированию с малыми скоростями перемещения актив ного захвата.
Для испытания динамическим изгибом (Varestreint, Transvarestreint) применяют серию образцов, проплавляемых на толщины при варьировании радиуса оправки. В качестве ко личественного показателя находят екр — критическую величипх деформации (%), при которой возникают ГТ кристаллизаци онного и подсолидусного типа, а также измеряют длину ГТ, яв ляющуюся косвенным критерием протяженности ТИХг.
Испытания в ТИХш проводят по определению показателя критического напряжения, в условиях послесварочной упроч няющей обработки, когда в металле имеют упругие свойств.-], а запас потенциальной энергии сварного образца и закрепляю щих приспособлений ограничен. При этом определяют работе разрушения в ТИХШ и сравнивают ее с металлом, не подвер гающимся сварочному воздействию.
В качестве ицтегрального критерия режима, учитывающего величину отдельцых параметров сварки (сила тока, напряже ние на дуге, скорость сварки), предложен критерий R = q-v [квт-м/с], каждый сомножитель которого по мере увеличения оказывает негативное влияние на сопротивляемость ГТ при сварке. Его физический смысл — энерговложение на секундную длину шва. С Помощью указанного критерия выявлена типо вая зависимость BHP^f(R)> представленная на рис. 6.7. В по лулогарифмических координатах она имеет линейный харак
тер, |
подтвержденный при |
испы |
|
|
|
|
|
|
|
|||||||
таниях многих Марок сталей и |
|
|
|
|
|
|
|
|||||||||
сплавов на никелевой и алюми |
|
|
|
|
|
|
|
|||||||||
ниевой |
основе. |
|
|
|
|
|
|
|
|
|
|
|
|
|
||
Максимум |
сопротивляемости |
|
|
|
|
|
|
|
||||||||
ГТ имеет место При сварке в оп |
|
|
|
|
|
|
|
|||||||||
тимальных |
режимах |
Ro, |
обус |
|
|
|
|
|
|
|
||||||
ловливающих минимальный угол |
|
|
|
|
|
|
|
|||||||||
срастания |
столбчатых |
кристал |
|
|
|
|
|
|
|
|||||||
литов в центре щВа. При R > < R 0 |
|
|
|
|
|
|
|
|||||||||
показатель |
снижается, |
так |
|
как |
|
|
|
|
|
|
|
|||||
в центре шва формируется осе |
Рис. 6.7. Схема изменения показателя |
|||||||||||||||
вой |
кристаллит, |
увеличивающий |
сопротивляемости |
ГТ |
металла шва |
(а) |
||||||||||
угол срастания между осевым и |
и его |
структуры |
(б) |
при варьирова |
||||||||||||
нии режимов сварки (qv)\ |
|
|||||||||||||||
боковым |
кристаллитами. |
|
При |
I, II, /// - —различный химсостав ме |
||||||||||||
R i > R 0 |
В Кр |
снижается |
в резуль |
|
|
талла |
шва; |
2 — |
||||||||
/ — шов |
с |
осевым |
кристаллитом; |
|||||||||||||
тате удлинения |
сварочной ванны. |
шов с |
изгибом кристаллитов; 3 — шов |
|||||||||||||
При |
изменении |
химического |
с разветвленным стыком вершин кри |
|||||||||||||
сталлитов; |
4 — шов |
с |
плоским стыком |
|||||||||||||
состава |
сплавов |
изменяется |
ве |
|
вершин |
кристаллитов |
|
|||||||||
личина |
максимума |
функции |
5 кр |
|
|
|
|
|
|
|
||||||
и интенсивность ее уменьшения по шкале аргумента R, изме |
||||||||||||||||
ряемой углом а наклона функции |
Bl<p(R) |
к оси |
|
абсцисс, |
ха |
|||||||||||
рактеризующим |
|
чувствительность |
сплавов |
к |
изменению |
ре |
||||||||||
жима сварки |
|
|
|
|
|
|
|
|
|
|
|
|
|
|||
tg « = АВ |
|
|
АВ |
- К * , |
|
|
|
|
|
|
|
|||||
|
|
A R |
|
Ig Ri/Ro |
|
|
|
|
|
|
|
|
|
|
где Кв — коэффициент чувствительности сплавов к изменению режима сварки.
В связи С тем, что положение максимума на рис. 6.7 харак теризует сопротивляемость ГТ при однотипной схеме кристал лизации, изменение показателя В1(р на нисходящей части функ ции записывается следующей формулой:
^ к р (Ri) ~ ^кр(Ло) — Кв lg — — •
АО
Составляющая BKp(R0) оценивает сопротивляемость обуслов ленную химическим составом сплава, на оптимальном режиме
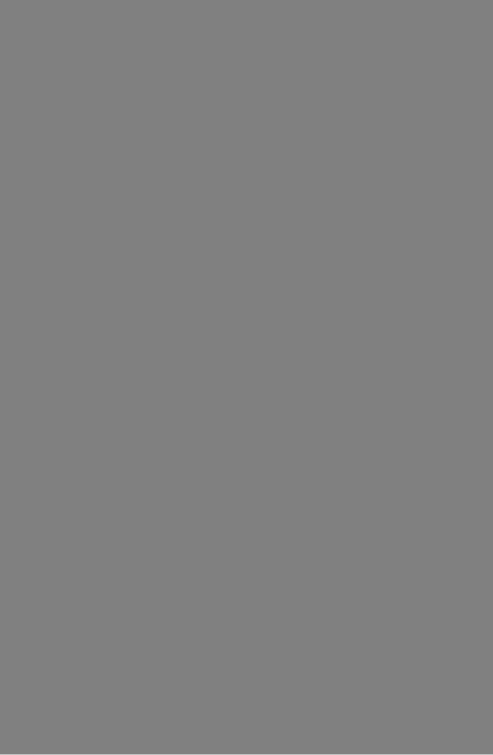
кой плите по флангам швом с катетом 20 мм. Канавки изго тавливают с шагом ЮО мм. При толщине образца >70 мм ка навки выполняют с двух сторон, они могут иметь форму пазов; при этом испытании относят к сварке по щелевой разделке.
Сварка образцов проб производится на минимальных ско ростях, указанных в п. 6.З.1.5.
При наличии ГТ металл сварного соединения считают склонным к образованию трещин, а степень склонности опре деляют относительными коэффициентами длины ГТ, площади
ГТ |
по |
|
отношению |
к шву, |
|
|
|
|
|
|
|
|
||||||
а также коэффициентом пе |
|
|
|
|
|
|
|
|
||||||||||
риодичности — Числом тре |
|
|
|
|
|
|
|
|
||||||||||
щин на единице длины шва. |
|
|
|
|
|
|
|
|
||||||||||
При |
отсутствии |
ГТ |
в |
|
|
|
|
|
|
|
|
|||||||
швах, |
выполненных |
на |
ре |
|
|
|
|
|
|
|
|
|||||||
комендованных |
скоростях |
и |
|
|
|
|
|
|
|
|
||||||||
режимах |
|
сварки |
(а |
для |
|
|
|
|
|
|
|
|
||||||
образцов |
с переменной |
ши |
|
|
|
|
|
|
|
|
||||||||
риной—на |
образцах |
макси |
|
|
|
|
|
|
|
|
||||||||
мальной |
ширины |
Ьщах |
пе |
|
|
|
|
|
|
|
|
|||||||
реходят |
к |
сварке |
более |
уз |
Рис. |
6.9. |
Соотношение |
между |
критическим |
|||||||||
ких |
образцов |
либо |
к при |
|||||||||||||||
темпом |
растяжения |
£ Кр и темпом |
деформа |
|||||||||||||||
менению |
режимов |
с |
увели |
ции шва |
В в пробе |
с |
круговым |
швом |
при |
|||||||||
ченной |
скоростью |
сварки |
и |
|
варьировании критерия режима qv: |
есть; |
||||||||||||
соответственно |
мощностью |
область |
АВ—ГТ нет; |
область |
ВС — ГТ |
|||||||||||||
^*ГТ |
'’ вероятность образования |
ГТ |
при |
дей |
||||||||||||||
дуги для |
сохранения |
посто |
ствии |
возмущений; |
ош и о$ — дисперсия Вкр |
|||||||||||||
янной |
высоты |
шва |
до |
по |
|
|
и В соответственно |
|
|
|
||||||||
явления |
ГТ. |
|
|
|
|
|
|
|
|
|
|
|
|
|
Степень стойкости оценивают по коэффициенту критической ширины ( \ ---- —V ЮО % и критической скорости сварки.
\"max '
Чем больше эти коэффициенты, тем выше стойкость против ГТ для сравниваемых составов шва.
Скорость сварки меняют в пределах качественного форми рования шва. При отсутствии ГТ на всех режимах и образцах любой ширины металл сварного соединения считают стойким против ГТ.
6.3.2.4. Расчетно-экспериментальный метод оценки стойко сти против ГТ. Метод имеет два вида: детерминированный и вероятностный. При детерминированной оценке находят функ цию Вкр{Ю путем применения расчетных или машинных ме тодов, а также функцию В • (•/?) применительно к одной из кон струкций технологических проб, описанных в п. 6.3.1.6, адек ватной по геометрической жесткости исследуемой конструкции сварного узла. Затем по значениям /Сгт определяют область ре
жимов (tfm ln —Rmax, ГДв /Сгт>0 И Ив МОГУТ ВОЗНИКЭТЬ ГТ П ри
принятом химическом составе шва.
Более точно определяется рабочий диапазон режимов при вероятностной оценке стойкости против ГТ. Она отличается тем, что выявляют как значения функций BKP(R) и В (R), так и их дисперсию путем многофакторного эксперимента или рас четного анализа (рис. 6.9)
Это позволяет определить область вероятного образования ГТ при действии технологических возмущений и рассчитать ве роятность Р гт[7]
Ргт = Вер [W> S] .
6.4. Холодные трещины (XT)
6.4.1. Природа и причины образования XT
Холодные трещины (XT) объединяют категорию трещин в сварных соединениях, формальными признаками которых яв ляются появление визуально наблюдаемых трещин практиче ски после охлаждения соединения; блестящий кристаллический излом трещин без следов высокотемпературного окисления [8]. XT — локальные хрупкие разрушения материала сварного со единения, возникающие под действием собственных сварочных напряжений. Размеры XT соизмеримы с размерами зон свар ного соединения. Локальность разрушения объясняется частич ным снятием напряжений при образовании трещин, а также ограниченностью зон сварного соединения, в которых возможно развитие трещин без дополнительного притока энергии от внеш них нагрузок.
Характерными особенностями большинства случаев возник новения XT являются следующие:
1) наличие инкубационного периода до образования очага трещин;
2) образование трещин происходит при значениях напря жений, составляющих менее 0,9 кратковременной прочности материалов в состоянии после сварки.
Эти особенности позволяют отнести XT к замедленному разрушению материала.
К образованию XT при сварке склонны углеродистые и ле гированные стали [8], некоторые титановые [9] и алюминиевые сплавы [1].
При сварке углеродистых и легированных сталей XT могут образоваться, если стали претерпевают частичную или полную закалку. Трещины возникают в процессе охлаждения после сварки ниже температуры 150 °С или в течение последующих нескольких суток. XT могут образовываться во всех зонах сварного соединения и иметь параллельное или перпендику лярное расположение по отношению к оси шва. Место образо вания и направление трещин зависят от состава основного ме
талла и шва, соотношения компонент сварочных напряжений и некоторых других обстоятельств. В практике холодные тре щины в соответствии с геометрическими признаками и харак тером излома получили определенные названия: «откол» — про дольные в ЗТВ, «отрыв» — продольные в зоне сплавления со стороны шва (аустенитного), «частокол» — поперечные в ЗТВ и др. (рис. 6.10). Наиболее частыми являются XT вида «откол».
Образование XT начинается с возникновения очага разру шения, как правило, на границах аустенитных зерен на околошовном участке ЗТВ, примыкающих к линии сплавления (рис. 6.11). Протяженность очагов трещин составляет несколько
рис. 6.10. В11Д холодных трещин в сварных |
Рис. 6.11. Межкристаллитный харак- |
||
соединениях легированных |
сталей: |
тер разрушения на участке очага хо- |
|
/ — «откол»; |
2 — «частокол»; |
3 —«отрыв» |
лодной трещины (А) и смешанный на |
|
4 — продольные в шве |
|
участке ее развития (В) |
диаметров аустенитных зерен. При этом разрушение не сопро вождается заметной пластической деформацией и наблюдается как практически хрупкое. Это позволяет отнести XT к меж кристаллическому хрупкому разрушению. Дальнейшее разви тие очага в микро- и макротрещину может носить смешанный или внутризеренный характер.
Отмеченные выше закономерности послужили основанием для формулирования предположительных механизмов разру шения при образовании очагов XT. Эти механизмы в разных вариантах включают два основных процесса: низкотемператур ную ползучесть [8, 10] и диффузионное перераспределение во дорода. /
Низкотемпературная ползучестьУ реализуется путем разви тия микроплабтической деформации (МПД) в приграничных зонах зерен [8]. МПД обусловлено наличием в структуре све жезакаленной стали незакрепленных, способных к скольжению Краевых дислокаций при действии сравнительно невысоких на пряжений. Особенно высока плотность дислокаций в мартен сите непосредственно после воздействия термического цикла. Величина МПД лежит в диапазоне 10_6—10-4 и проявляется при напряжениях выше предела неупругости стл (или микроско-
пического предела текучести) (рис. 6.12). МПД является тер мически активируемым процессом, т. е. ее Скорость зависит от температуры и величины приложенных напряжений. После «от дыха» способность закаленной стали к МПД исчезает. Конеч ные высокая твердость и предел текучести закаленной стали — результат старения, при котором происходит Закрепление дис локаций атомами углерода. Особенности развития МПД до статочно хорошо объясняют приведенные выше закономерно сти замедленного разрушения.
При длительном нагружении по границам зерен развива ется локальная МПД. В результате последней реализуется
7
Рис. 6.12. Характер деформирования све- |
Рис. 6.13. Схема Зингера—Стро образова |
||
жезакаленной |
стали; |
ад — микроскопиче- |
ния трещин при проскальзывании по гра |
ский |
предел |
текучести [8] |
ницам зерен |
межкристаллическое разрушение по схеме Зинера—Стро, пред полагающей относительное проскальзывание и поворот зерен по границам (рис. 6.13).
Действие диффузионного водорода при образовании XT наиболее соответствует одному из механизмов обратимой во дородной хрупкости [8]. Ее особенность заключается в том, что в условиях медленного нагружения источники водородной хрупкости образуются вследствие диффузионного перераспре деления водорода и исчезают через некоторое время после сня тия нагрузки. Разновидностью обратимой хрупкости является водородная статическая усталость, которая проявляется при длительном действии постоянных напряжений, превышающих некоторую критическую величину. Для описания процесса раз рушения используются различные механизмы: молекулярного давления, адсорбционный, максимальных трехосных напряже ний и др. При этом важная роль отводится взаимодействию водорода с дислокациями.
Основными |
факторами, обусловливающими образование |
|
XT, являются: |
|
|
1) |
структурное состояние металла сварного соединения, ха |
|
рактеризуемое |
наличием составляющих мартенситного и бей- |
нитного типа (5Д, размером действительного аустенитного
зерна (d3);
2) концентрация диффузионного водорода в зоне зарожде
ния очага трещины (Нд) 5
3) уровень растягивающих сварочных напряжений I рода
(<Тсв).
Критической структурно-водородное и напряженное состоя ние в ЗТВ, обусловливающее образование XT, может быть опи
сано регрессионными уравнениями, полученными статистиче ской обработкой результатов испытаний на замедленное раз рушение (см. стр. 190) [11, 12]. Критериями критического со стояния служат критические значения одного из факторов тре-
щинообразования |
(SKP, Яд.кР, Ор.кР) при учете действующих |
||||
значений |
других |
факторов. Уравнения |
5КР, ЯД.КР, ар.кр пред |
||
ставляют |
собой |
семейство |
поверхностей |
в координатах 5 Д, Яд, |
|
С при ( Т с в / с г о . 2 = |
const (рис. |
6.14). Пространству ниже этих по |
верхностей с определенной вероятностью соответствует отсут
ствие XT в ЗТВ |
сварного соединения, выше — их образование. |
|
Образование |
XT возможно |
также при сварке некоторых а |
и а+Р титановых сплавов [9]. |
Механизм и причины образова |
ния трещин в титановых сплавах менее исследованы, чем для случая сварки легированных сталей. Установлено, что они имеют характер замедленного разрушения. При этом период до разрушения значительно больше, чем у сталей, и может до стигать несколько десятков суток. Образование трещин свя зано с метастабильным состоянием металла шва и зоны тер мического влияния после сварки, обусловливающим их пони женную пластичность.
Склонность технического титана и малолегированных а-сплавов к XT связывают с интенсивным ростом зерна при сварке и насыщением газами (Н2, 0 2, N2) свыше допустимой концентрации. Водород, имеющий пониженную растворимость в a-фазе (до 0,001 %), способен образовывать хрупкий гидрид титана. Последний образуется со значительным положитель ным объемным эффектом (15,5%) и наряду с охрупчиванием металла может привести к повышению уровня микронапряже ний 2-го рода. Водород также способен адсорбироваться на границах зерен, снижая их когезионную прочность. Отмечено, что действие водорода усиливается при одновременном насы щении металла сварного соединения кислородом и азотом. За медленный характер разрушения, по-видимому, объясняется диффузионным перераспределением водорода и релаксацион ными процессами в зонах локального действия пиков микро напряжений, в том числе и по границам зерен.
Склонность к XT наблюдается у а + р-сплавов титана, леги рованных главным образом эвтектоиднообразующими р-стаби- лизирующими элементами (Fe, Сг, Мп и др.). Образование трещин связывают с выделением в процессе фазовых превра щений хрупких фаз. В процессе охлаждения после сварки при
распаде |
p-фазы |
возможно |
образование |
метастабильных а', |
Р(ост) и |
хрупкой |
©-фаз, а |
также хрупких |
интерметаллидных |
соединений. Образование интерметаллидов возможно при пе реходе метастабильных фаз со временем в стабильное состоя ние. Выделение to-фазы и интерметаллидов на границах зерен ведет к снижению пластичности и повышению склонности к об разованию XT.
Рост зерна в указанных сплавах ограничен в связи с отно сительно высокой концентрацией легирующих элементов. Охрупчивающее действие водорода проявляется в меньшей степени у этих сплавов по сравнению с а-сплавами, поскольку растворимость водорода в p-фазе на несколько порядков больше, чем в a-фазе. Замедленный характер разрушения, повидимому, объясняется развитием во времени превращений в метастабильных фазах и релаксационными процессами в зо нах действия межфазных напряжений на границах зерен.
Склонность к XT наблюдается при сварке некоторых высо колегированных термоупрочняемых алюминиевых сплавов си
стем Al—Mn—Zn и A1-:Zn—M&—1Си [1]. Природа и механизм образования Трещин еще недостаточно исследованы. Их воз никновение связывай с выделением хрупких интерметаллид-
ных фаз в процесе ст^Рения ПРИ охлажДении ПРИ сварке и в послесварочный период- В РезУльтате дисперсионного твердения имеет место оТноситеДьное упрочнение тела зерна по отноше нию к приграничным зонам. В процессе релаксаций сварочных напряжений нроисхоДит локальное накопление пластических деформаций на гранйцах зеРених перенапряжение и замед ленное разрушение.
6.4.2. Способы и КритеРии °Ченки склонности к XT
Способы оценки склойности к трещинам можно классифициро
вать по следующим осН°вным признакам: |
|
||
1) |
характеру |
процедуры оценки — на косвенные и прямые; |
|
2) |
характеру |
показателей склонности — на |
качественные, |
полуколичеетвенные Иколичественные; |
склонности — |
||
3) |
характеру |
использования показателей |
сравнительные и приклаДныеКосвенные способы позволяют получать оценку склонности
к трещинам расчетным путем без непосредственного испыта
ния материалов.
Прямые способы предусматривают сварку технологических проб, специализированные испытания сварных соединений или образующих его материалов в условиях, имитирующих сва
рочные.
Критерии оценки или показатели склонности к трещинам, как правило, выражаются через характеристики одного или совокупности изменяющихся факторов, обусловливающих об разование трещин. Качественные критерии не имеют количест венного выражения и по существу имеют смысл «материалы склонные» или «несклонные» к трещинам. Количественные критерии имеют численное выражение, связанное с изменением одного из факторов, контролирующих процесс образования трещин, и однозначно оценивают склонность (стойкость или сопротивляемость) к трещинам. Если при определении показа телей склонности к трещинам одновременно изменяются не сколько активных факторов, а критерий оценки является чис ловой характреистикой одного из них, то есть следует считать полуколичественным.
Способы оценки, критерии которых могут быть использо ваны только для сопоставления материалов или технологиче ских вариантов сварки по их склонности к трещинам, относят к сравнительным. Количественные критерии, которые могут быть использованы для оценки стойкости сварных соединений конструкций против трещин, относят к прикладным.