
книги / Сварка и свариваемые материалы. Свариваемость материалов
.pdf
|
|
ХИМИЧЕСКИЙ СОСТАВ СТАЛЕЙ, % |
|
|
|
|
||
Сталь |
С |
Мп |
Si |
Сг |
Ni |
Мо |
Си |
|
13ХГМРБ |
0,10—0,16 |
0,9— 1,2 |
0,17—0,37 |
0,9— 1,3 |
До |
0,3 |
0,3—0,4 |
< 0 ,3 |
14Х2ГМРБ |
0,10—0,16 |
0,9— 1,2 |
0,17—0,37 |
1 ,1 -1 ,5 |
До |
0,3 |
0,4—0,5 |
< 0 ,3 |
14Х2ГМРЛ |
0,10—0,17 |
0,9— 1,2 |
0,20—0,40 |
1,4— 1,7 |
До |
0,3 |
0,45—0,55 |
< 0 ,3 |
14Х2ГМ |
0,10—0,16 |
0,9— 1,2 |
0,17—0,37 |
1,3— 1,7 |
До |
0,3 |
0,4—0,5 |
< 0 ,3 |
12Г2СМФАЮ |
0,09—0,15 |
1,3— 1,7 |
0,4—0,7 |
— |
До |
0,3 |
0,15—0,25 |
< 0 ,3 |
12ГН2МФАЮ |
0,09—0,16 |
0,9— 1,2 |
0,3—0,5 |
0,2—0,5 |
1,4— 1,75 |
0,15—0,25 |
< 0 ,3 |
|
12ХГН2МФБАЮ |
0,09—0,16 |
0,9— 1,3 |
0,3—0,5 |
0,5—0,9 |
1,4— 1,70 |
0,3—0,4 |
< 0 ,3 |
|
12ХГН2МФБДАЮ |
0,09—0,16 |
0,6— 1,1 |
0,2—0,5 |
0,6—0,9 |
1,4— 1,75 |
0,4—0,6 |
0,5— 1,0 |
|
12ХГН2МФДРА |
0,10—0,14 |
0,95— 1,20 |
0,15—0,35 |
0,8— 1,2 |
1,7—2,1 |
0,5—0,7 |
0,7— 1,0 |
|
14ХГН2МДАФБ |
0,12—0,17 |
1,1— 1,4 |
0,17—0,35 |
0,9— 1,3 |
1 ,7 -2 ,2 |
0,2—0,3 |
0,3—0,6 |
|
14ХГ2САФД* |
0,12—0,18 |
1,4— 1,9 |
0 ,4 -0 ,7 |
0,5—0,8 |
До |
0,3 |
— |
0,3—0,6 |
12ГНЗМФАЮДР-СШ |
0,10—0,15 |
1,2— 1,5 |
0 ,1 7 -0 ,3 7 |
— |
2,8—3,2 |
0,3—0,4 |
0,3—0,5 |
|
12ХГНЗМАФД-СШ |
0,10—0,15 |
1,0— 1,3 |
0,2—0,5 |
0,6— 1,0 |
2,5—3,0 |
0,4—0,55 |
0,5— 1,0 |
|
14ХГНМДАФБРТ* |
0,12—0,17 |
1,1— 1,4 |
0,17—0,37 |
0,9— 1,3 |
0,9— 1,3 |
0,2—0,3 |
0,6—0,9 |
|
|
|
|
|
|
S |
| |
Р |
Сталь |
V |
Nb |
А1 |
N- |
в |
не более |
||
|
|
|
|
|
|
|||
13ХГМРБ |
_ |
0,01—0,03 |
0,02—0,08 |
|
0,001—0,004 |
0,035 |
|
0,035 |
14Х2ГМРБ |
— |
0,01—0,04 |
0,02—0,08 |
|
0,001—0,004 |
0,035 |
|
0,035 |
14Х2ГМРЛ |
— |
— |
— |
— |
0,001—0,004 |
0,035 |
|
0,035 |
14Х2ГМ |
— |
— |
— |
— |
— |
0,015 |
|
0,030 |
12Г2СМФАЮ |
0,07—0,15 |
— |
0,05—0,10 |
0,015—0,03 |
— |
0,035 |
|
0,035 |
12ГН2МФАЮ |
0,05—0,10 |
— |
0,05—0,10 |
0,02—0,03 |
— |
0,035 |
|
0,035 |
12ХГН2МФБАЮ |
0,05—0,10 |
0,02—0,06 |
0,05—0,10 |
0,02—0,03 |
— |
0,035 |
|
0,035 |
12ХГН2МФБДАЮ |
0,05—0,10 |
0,02—0,06 |
0,03—0,08 |
0,015—0,03 |
— |
0,035 |
|
0,035 |
12ХГН2МФДРА |
0,08—0,14 |
— |
0,02—0,05 |
— |
До 0,004 |
0,025 |
|
0,025 |
14ХГН2МДАФБ |
0,10—0,20 |
0,03—0,08 |
0,03—0,10 |
0,010—0,025 |
— |
0,008 |
|
0,020 |
14ХГ2САФД* |
0,08—0,16 |
— |
0,03—0,07 |
0,010—0,02 |
— |
0,020 |
|
0,035 |
12ГНЗМФАЮДР-СШ |
0,04—0,08 |
— |
0,02—0,05 |
0,008—0,02 |
0,002—0,004 |
0,010 |
|
0,020 |
12ХГНЗМАФД-СШ |
0,05—0,10 |
— |
До 0,08 |
0,008—0,02 |
— |
0,012 |
|
0,025 |
14ХГНМДАФБРТ** |
0,10—0,20 |
0,03—0,08 |
0,05—0,10 |
0,015—0,025 |
0,002—0,004 |
0,015 |
|
0,025 |
* 0.01—0.05Ti; ** 0,03-0,08Ti
оо
со
МЕХАНИЧЕСКИЕ СВОЙСТВА СТАЛЕЙ (НЕ МЕНЕЕ) |
ТАБЛИЦА 10.2 |
|||||
|
|
|
|
|
КС и, Дж /см*, при |
|
Сталь |
Толщина, |
а0,2* |
МПа |
*8- |
—40°С |
—70°С |
|
мм |
МПа |
X |
|||
13ХГМРБ |
10—50 |
590 |
690 |
14 |
39 |
29 |
14Х2ГМРБ |
1 0 -5 0 |
588 |
686 |
14 |
39 |
— |
14Х2ГМРЛ |
> 4 0 |
588 |
686 |
14 |
34 |
— |
14Х2ГМ |
3—30 |
588 |
686 |
16 |
39 |
— |
12Г2СМФАЮ |
10—32 |
588 |
686 |
14 |
34 |
— |
12ГН2МФАЮ |
16—40 |
588 |
686 |
14 |
— |
29 |
12ХГН2МФБАЮ |
16—40 |
736 |
834 |
12 |
— |
29 |
12ХГН2МФБДАЮ |
20—40 |
785 |
883 |
15 |
—1 |
29 |
12ХГН2МФДРА |
4—20 |
980 |
1078 |
10 |
29 |
— |
14ХГН2МДАФБ |
3 - 5 0 |
685 |
780 |
16 |
39* |
— |
14ХГ2САФД |
16—40 |
588 |
686 |
14 |
39 |
— |
12ГНЗМФАЮДР-СШ |
4—40 |
685 |
780 |
16 |
78* |
59* |
12ХГНЗМАФД-СШ |
3—50 |
980 |
1080 |
14 |
— |
59 |
14ХГНМДАФБРТ |
6—20 |
785 |
980 |
12 |
39 |
29 |
* KCV
Эффективно введение в высокопрочную низколегированную сталь не больших количеств азота (0,02—0,03 %) и нитридообразующих элементов — алюминия, ванадия, ниобия. По механическим свойствам и хладостойкости нитридсодержащие высокопрочные стали превосходят стали такого же химического состава, изготовленные по обычной технологии. Наличие мелко
дисперсных нитридов |
в стали способствует уменьшению |
их склонности |
||||
к росту |
аустенитного |
зерна при сварке. Поэтому нитридсодержащие |
стали |
|||
весьма |
перспективны |
|
для сварных конструкций. На практике хорошо |
себя |
||
зарекомендовала |
нитридсодержащая |
высокопрочная |
сталь |
марки |
||
12ГН2МФАЮ. |
|
|
|
|
|
10.2. Свариваемость сталей
Основными показателями свариваемости низкоуглеродистых бейнитно-мартенситных сталей являются сопротивляемость сварных соединений холодными трещинам и хрупкому разру шению и механические свойства зоны термического влияния, которые прежде всего связаны с фазовыми превращениями и структурными изменениями в стали при сварке. На основе этих показателей определяют технологические и конструктивные ус ловия получения сварных соединений, удовлетворяющих экс плуатационные требования к сварной конструкции.
10.2.1. Фазовые превращения и структурные изменения при сварке
Общие сведения о фазовых превращениях и структурных изме нениях в стали при воздействии термического сварочного цикла получают из терминокинетических диаграмм непрерывного рас пада аустенита.
Устали 14Х2ГМР в диапазоне скоростей охлаждения o>e/s—
=35-1-0,5 °С/с превращение аустенита происходит в мартенсит ной и бейнитной областях (рис. 10.1). При ДОб/5>18 °С/с образу ется низкоуглеродистый мартенсит с твердостью HV 380. Умень-
Рис. 10.1. Термокинетическая диаграмма
распада аустенита стали 14Х2ГМР. Цнфры в кружках обозначают твердость
(HVю)
Рис. 10.3. Термокинетнческая диаграмма Распада аустенита стали 14ХГН2МДАФБ.
Цифры в кружках обозначают твердость
(ЯУ.о)
Рис. 10.2. Термокинетическая Диаграмма распада аустенита стали 12ГН2МФАЮ. Цифры в кружках обозначают твердость
(HVю)
Рис. 10.4. Термокинетнческая диаграмма Ёаспада аустенита стали 12ХГН2МФБДАЮ. 1ифры в кружках обозначают твердость
(HV\o)
Шение скорости охлаждения приводит к развитию бейнитного Превращения, повышению температуры его начала и снижению твердости. При замедленных скоростях охлаждения (ш6/5« =«0,8 °С/с) повышается температура бейнитного превращения и Увеличиваются размеры ферритных игл.
Кинетика превращения аустенита стали 12ГН2МФАК) (рис. 10.2) исследовалась для интервала скоростей охлаждения ^ 6 /5 = 75^1,6 °С/с. При этих условиях превращение происходит в мартенситной и бейнитной областях. Ферритное и перлитное превращения отсутствуют. При Юб/5 = 75 °С/с мартенситное пре вращение начинается при 440 °С и заканчивается при 250 °С, твердость мартенсита HV 380. В интервале скоростей охлажде ния 36—2,7 °С/с превращение аустенита с образованием бейнит- но-мартенситной структуры происходит при температурах: на чало 515—620 °С, конец 270—420 °С. С уменьшением скорости
|
|
|
охлаждения |
количество |
мартен |
|||||||||
|
|
|
ситной |
составляющей. уменьша |
||||||||||
|
|
|
ется. |
При |
a)6/s = 36 °С/с |
количе |
||||||||
zoo I |
1 |
|
ство бейнита в структуре состав |
|||||||||||
|
|
ляет |
около |
15%, |
а |
при |
о>в/ 5 |
= |
||||||
|
/ 2 |
|
||||||||||||
100 |
Л |
|
= 2,5°С/с — 90%; |
твердость |
при |
|||||||||
|
|
этом изменяется от HV 330 до |
||||||||||||
|
|
|
HV 213. |
При |
0 )6/5 = 1,6 °С/с |
про |
||||||||
6 ^ |
|
исходит |
|
полностью |
бейнитное |
|||||||||
|
|
|
превращение |
в интервале темпе |
||||||||||
|
|
|
ратур |
|
635—465°С; |
твердость |
||||||||
-100 |
zoo |
m воо воо юоот,°с |
HV 205. |
|
|
|
14ХГН2МДАФБ |
и |
||||||
о |
У |
сталей |
|
|||||||||||
Рис. Ю.5. Изменение временных на |
12ХГН2МФБДАЮ |
превращение |
||||||||||||
аустенита |
в диапазоне скоростей |
|||||||||||||
пряжений |
при |
охлаждении защемлен |
||||||||||||
ных образцов из стали 14ХГН2МДАФБ |
охлаждения |
|
ovs=50—0,6 °С/с |
|||||||||||
(термоцнклы |
нагрев — охлаждение |
в |
||||||||||||
(1—6) |
соответствуют рис. 10.3) |
происходит |
мартенситной |
и |
||||||||||
|
|
|
бейнитной |
областях |
(рис. |
10.3 |
||||||||
и 10.4). При скорости охлаждения, превышающей о)6/5 =Ю |
°С/с, |
у них развивается только мартенситное превращение.. При ско ростях охлаждения ttV5 = 2,3°C/c происходит бейнитное превра щение, отсутствуют выделения доэвтектоидного феррита, что свидетельствует о высокой устойчивости аустенита этих марок сталей.
Скорость охлаждения заметно влияет на величину времен ных напряжений в температурной области фазового у «-пре вращения (рис. 10.5). Различие в кинетике структурных пре вращений приводит также к изменению величины остаточных растягивающих напряжений в образцах. С повышением скоро сти охлаждения w^/ь в интервале 0,6—50 °С/с у стали 14ХГН2МДАФБ они уменьшаются от 240 до 150 МПа.
10.2.2. Сопротивляемость сварных соединений образованию ГТ и. XT
Низкоуглеродистые бейнитно-мартенситные стали имеют огра ниченное содержание С, Ni, Si, S и Р. Поэтому при соблюдении режимов сварки и правильном применении присадочных мате
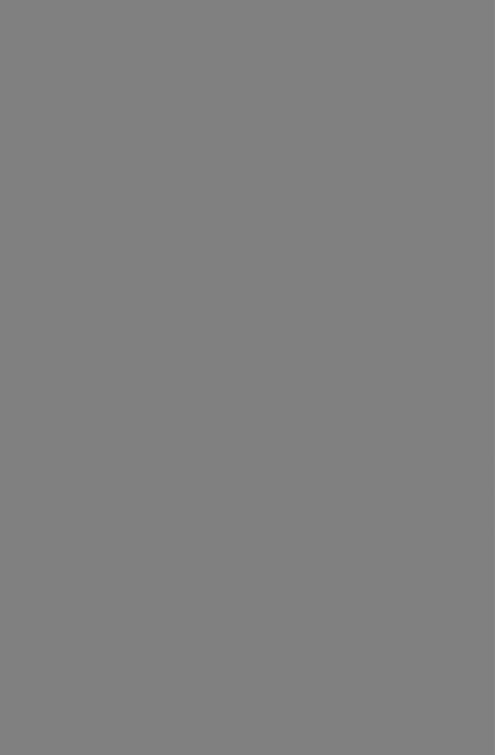
швов. В угловых и стыковых соединениях листового проката сталей толщиной более 12 мм возможно образование ламелярных трещин. Они располагаются в основном металле, направ лены параллельно границе сплавления и могут вызывать разру шения типа отрыва. Примеры холодных трещин в сварных со единениях легированных сталей приведены на рис'. 10.6.
Рис. 10.7. Влияние скорости охлаждения wg/5 и насыщенности швов водородом на
склонность к замедленному разрушению проб имплант из стали 14Х2ГМР:
1 — w ъ/5= \ В 0С ,‘с : [Н]Д И (Г3,0 |
мл/100 г ; 2— |
||
ш6/5в 1® ‘С/с\ |
[Н]диф=12,5 мл/ЮО г;5—ш6/5= |
||
=»9 °С/с; 1Ы|диф =3,0 |
мл/100 |
г,; 4 — u>6/5 = |
|
=9 "С/с; |
[Н]диф |
=12,6 |
мл/100 г |
Рис. 10.9. Влияние скорости охлаждения w$/5 и насыщенности швов* водородом на
склонность к замедленному разрушению проб имплант из стали 14ХГН2МДАФБ (обозначения — см. рис. 10.7)
0,01 |
0,1 |
1 |
ЮГ, Ч |
Рис., Ю.8. Влияние скорости охлаждения ш6/5 и насыщенности швов водородом на
склонность к замедленному разрушению проб имплант из стали 12ГН2МФАЮБ (обозначения — см. рис. 10.7)
Рис. 10.10. Влияние скорости охлаждения ш6/5 и насыщенности швов водородом на
склонность к замедленному разрушению
проб имплант из стали 12ХГН2МФБДАЮ (обозначения — см. рис. 10.7)
Сопротивляемость сварных соединений образованию холод ных трещин оценивают по результатам испытаний специальных проб. Результаты испытаний на замедленное разрушение по методу имплант образцов из сталей 14Х2ГМР, 12ГН2МФАЮ, 14ХГН2МДАФБ и 12ХГН2МФБДАЮ приведены на рис. 10.7— 10.10. Сварку этих образцов, установленных в отверстиях же
стко закрепленной в испытательной установке базовой пла стины толщиной 20 мм, осуществляли в один проход электро дами АНП-2 4,0 мм на режиме: /=170 А, У=26 В, v = 9 м/ч. Скорость охлаждения сварного соединения варьировали (w6/5 =
= 20 и 13 °С/с), изменяя начальную температуру пластины. |
Ко |
личество диффузионного водорода ([Н]ДИф = 3—4 и |
12— |
13 мл/100 г) в наплавленном металле определяли хроматогра фическим методом. Нагружение образцов начинали при их ох лаждении после сварки до температуры 120—100 °С.
Высокая сопротивляемость сварных соединений низкоугле родистых легированных сталей образованию трещин обеспечи вается в случае, когда содержание диффузионного водорода в наплавленном металле не превышает 3,5—4,0 мл/100 г. Бо лее высокая концентрация водорода приводит к снижению со противляемости соединений образованию холодных трещин [5]. При выбранных условиях испытаний ( [ Н ] ДИф = 2,8—3,0 мл/100 г и ^ 6/5 = 1 3 °С/с) у сварных соединений сталей 14Х2ГМР и 12ГН2МФАЮ замедленное разрушение не происходит (точка 3 на рис. 10.7 и 10.8). Для предотвращения образования холод ных трещин в сталях 14ХГН2МДАФБ и 12ХГН2МФБДАЮ не обходимы ограничения допускаемых скоростей охлаждения. По диапазонам допускаемых скоростей охлаждения зоны термиче ского влияния, обеспечивающих достаточную сопротивляемость образованию холодных трещин, рассматриваемые стали могут быть расположены в следующий ряд:
1)134-18 °С/с 14Х2ГМР, 13ХГМРБ, 14ХГ2САФД и 12ГН2МФАЮ;
2)74-12 °С/с 14ХГНМДАФБРТ и 14ХГН2МДАФБ;
3)wQ/5 = 44-6 °С/с 12ХГН2МФБДАЮ.
Для предотвращения образования холодных трещин при сварке соединений большой толщины и «жесткости» следует применять предварительный подогрев. Как правило, он назна чается при сварке металла толщиной свыше 20 мм. Темпера тура подогрева 80—100 °С. При сварке металла толщиной свыше 40 мм температура подогрева 100—150 °С. Выполнение предварительного подогрева протяженных разделок кромок ме талла таких толщин — достаточно трудоемкая операция. В этом случае возможно ограничение температуры подогрева до 80— 100 °С за счет введения дополнительного послесварочного на грева сварных соединений в интервале 150—200 °С. Такой про грев производится с поверхности металла шва, причем темпера
тура после сварки перед подогревом должна |
быть не менее |
150 °С. Время нагрева назначается из расчета |
1,5—2 мин на |
1 мм толщины соединения. При температуре окружающего воздуха<0 °С необходим предварительный подогрев свариваемых кромок до 100—120 °С для металла всех толщин менее 30 мм и при 130—150 °С для металла больших толщин. Подогрев
сварных соединений наиболее эффективен, если его осуществ лять равномерно по всей длине с двух сторон от разделки кро мок не менее 100 мм.
Стойкость сварных соединений против образования холод ных трещин может быть также повышена применением техно
логии сварки с «мягкими прослойками», при |
которой первые |
|
слои многослойного шва выполняются менее |
|
прочным и бо |
лее пластичным металлом по сравнению с |
последующими |
слоями. В отдельных случаях («жесткие» соединения большой толщины) малопрочные пластичные швы в один-два слоя на кладываются в процессе заполнения разделки кромок. При сварке под флюсом для выполнения мягких слоев могут быть рекомендованы сварочные проволоки Св-ЮГА, Св-08ГС (ГОСТ 2246—70), при сварке покрытыми электродами — электроды УОНИ-13/45, (ГОСТ 9467—75), при сварке в углекислом газе — проволока Св-08Г2С (ГОСТ 2246—70).
10.2.3. Выбор тепловых режимов сварки
Выбор технологии сварки низкоуглеродистых бейнитно-мартен- ситных сталей, обеспечивающий требуемые служебные и тех нологические свойства сварных соединений, возможен при ус ловии учета влияния химического состава и толщины основного металла, параметров режима сварки и температуры подогрева соединения, химического состава материалов, содержания во дорода в металле шва, разделки кромок и типа соединений.
Критериями при определении диапазона режимов сварки и температур предварительного подогрева служат допустимые максимальная и минимальная скорости охлаждения металла зоны сплавления.
Максимально допустимые скорости охлаждения сталей при нимаются таким образом, чтобы предотвратить образование холодных трещин в металле околошовной зоны. Величину этой скорости охлаждения определяют экспериментальным путем по результатам испытаний технологических проб или же расчет ным путем [3, 6—9].
Для предотвращения неблагоприятного изменения струк туры и снижения ударной вязкости металла зоны перегрева необходимо ограничивать минимальную скорость охлаждения. Чрезмерно высокие погонные энергии сварки приводят к об разованию у линии сплавления крупнозернистых структур с низкими показателями ударной вязкости. Кроме того, дли тельное пребывание отдельных зон основного металла при тем пературах, превышающих температуру отпуска стали, может способствовать разупрочнению металла. У легированных сталей с увеличением погонной энергии сварки интенсивность разуп рочнения значительно меньше, чем снижение ударной вязко-
Форма по- |
|
|
|
|
q/v, кДж/см, при толщине металла, мм |
|
|
|
|
|
|
|
|||
перечного се г с |
6 |
|
|
|
|
|
|
|
36 |
|
|
|
|
|
|
чениякромок |
|
8 |
10 |
16 |
20 |
25 |
30 |
|
|
40 |
|
50 |
|
||
И И |
20 |
<10,0 |
<16,0 |
<23,0 |
<33,0 |
<40,0 |
|
|
|
|
|
|
|
|
|
50 |
< 9,0 |
<15,0 |
<20,0 |
<30,0 |
<35,0 |
— |
— |
|
— |
|
— |
|
— |
|
|
|
|
|
|
|
|||||||||||
|
20 |
6,3—13,3 8,3—16,2 11,6—19,5 |
16,2—24,1 |
1 |
\ |
|
|
|
1 |
_ |
1 |
_ |
|
||
|
17,9—32,4 22,9—38,3 |
21,6—47,81 |
— |
|
|||||||||||
х / / Л t \ \N |
100 |
— |
— |
— |
13,3—25,0 |
18,7—30,0I 20,0—37,4 |
|
— |
|
— |
|
||||
150 |
|
— |
— |
— |
13,3—23,7' 15,8—29,1 |
18,7—36,6i |
20,0—41,0| |
25,8—49,9 |
26,2—51,! |
||||||
|
|
|
РЕКОМЕНДУЕМЫЕ ТЕМПЕРАТУРА ПРЕДВАРИТЕЛЬНОГО |
|
|
|
ТАБЛИЦА |
10.4 |
|||||||
|
|
|
|
|
|
|
|
|
|||||||
|
|
|
ПОДОГРЕВА И ПОГОННАЯ ЭНЕРГИЯ СВАРКИ СТАЛИ 12ГН2МФАЮ |
|
|
|
|
|
|||||||
поперечного |
подогрева |
|
16 |
20 |
24 |
28 |
|
|
32 |
|
36 |
|
40 |
|
|
сечения кромок |
|
|
|
|
|
|
|
||||||||
|
|
20 |
14,0—33,0 |
17,5—42,0 |
19,5—50,0 |
20.5— |
60,0 21,0—65,0 |
21.5— |
70,0 21,5—75,0 |
||||||
|
|
100 |
|
9,5—25,0 |
12,0—33,0 |
13,0—40,0 |
13.5—45,0 |
13,5—50,0 |
13.5—55,0 |
14,0—60,0 |
|||||
|
|
20 |
12,5—33,0 |
16,0—40,0 |
20,0—49,0 |
23,5—55,0 |
27,5—60,0 |
31,0—70,0 |
34.5— |
75,0 |
|||||
ш |
|
100 |
|
9,0—25,0 |
11,5—30,0 |
14,5—35,0 |
17,0—44,0 |
20,0—55,0 |
21,5—55,0 |
23.5—65,0 |
|||||
|
|
|
|
|
|
|
|
|
|
|
|
|
|
|
i
20 |
17.0-43,0 |
22,0—50,0 |
27.0— 60,0 31,5—70,0 |
35,5—80,0 |
38,0—85,0 |
40.0— |
90,0 |
||
100 |
13.0— |
33,0 |
15,5—40,0 |
19.0—45,0 |
22,0—55,0 |
24,0—60,0 |
25,5—65,0 |
26.0— |
70,0 |