
книги / Основы конструирования авиационных двигателей и энергетических установок. Т. 1 Общие сведения. Основные параметры и требования. Конструктивные и силовые схемы
.pdfосевых и радиальных зазоров между элементами ротора и корпуса двигателя.
В зависимости от числа опор различают двух-, трех-, четырехопорные роторы, а в зависимости от числа роторов - одно-, двух- и трехвальные двигатели. Двухопорные роторы применяются при относительно коротких и жестких роторах компрессора и турбины, чаще всего - в системе газогенератора. Трехопорные роторы применяют ся в конструкциях многоступенчатых компрес соров и турбин, чаще всего - в системе наруж ных каскадов двухили трехвальных двигателей.
4.2. Силовые схемы роторов
Радиально-упорный подшипник, воспринима ющий разность осевых нагрузок на компрессор и турбину, стараются расположить исходя из со ображений его наименьшей тепловой напряжен ности, т.е. в «холодной» части двигателя, напри мер, в передней части компрессора.
На рис. 4.15 представлены примеры широко применяемых силовых схем роторов авиацион ных двигателей:
- силовая схема роторов двигателя General Electric CF-6-80- двухвальная с двухопорным ротором НД и четырехопорным ротором ВД;
General Electric CF-6-80
|
|твд| |
тнд |
|
КВД |
|
XL w / |
\ u i УУГГ 1 |
S S |
Рис. 4.15. Примеры силовых схем роторов авиационных двигателей
151
Глава 4. Силовые схемы ГТД
-силовая схема роторов двигателя PW-2037 - двухвальная с трехопорным ротором НД и двухо порным ротором ВД;
-силовая схема роторов двигателя ПС-90А - двухвальная с трехопорным ротором НД и трехо порным ротором ВД;
-силовая схема роторов двигателя RollsRoyce Trent 800 - трехвальная с трехопорным ро тором НД с межвальным расположением шари коподшипника, трехопорным ротором СД и двух опорным ротором ВД.
Силовые схемы роторов ГТД наземного при менения значительно проще. Как правило, они включают в себя одновальный ротор ВД базово го авиационного двигателя (с высокой степенью унификации конструктивных решений) или но вый специально разработанный ротор.
4.3. Силовые схемы статоров
Силовые корпуса двигателей предназначены для восприятия и суммирования усилий, дейс твующих в ГТД, и частичной передачи их в виде силы тяги (двигатели воздушных судов) на сило вые элементы самолета или крутящего момента (двигатели, как приводы к другим агрегатам) на подмоторную раму.
К силовым корпусам ГТД относят корпуса компрессора, камеры сгорания, турбины, а так же корпуса опор. Все эти корпуса собираются в единую конструкцию - статор с помощью флан цев, которые соединяются болтами, шпильками, штифтами. К силовым корпусам крепятся вход ные и выходные устройства двигателя, коробки приводов, корпуса наружного контура, устройс тва форсирования и реверса тяги. На силовых корпусах размещаются узлы крепления двигате ля к самолету или к подмоторной раме.
Силовые схемы статоров одноконтурных дви гателей различаются в основном по виду связи корпусов компрессора, камеры сгорания, турбины и опоры заднего подшипника ротора. На рис. 4.16 приведены три типовые схемы статоров однокон турного двигателя с трехопорным ротором.
На всех схемах корпус 1 компрессора непос редственно связан с корпусом 2 переднего под шипника и корпусом 3 среднего подшипников ротора. На схеме а корпус турбины 4 связан с корпусом среднего подшипника ротора через корпус 5 заднего подшипника ротора и корпус б газосборника. На схеме б задний подшипник рас положен за турбиной и его корпус 7 через кор пус турбины и корпус 8 камеры сгорания свя зан с корпусом среднего подшипника ротора. На схеме в изображена разветвленная связь кор-
а 3 |
5 |
6 |
1 |
8 |
4 |
Рис. 4.16. Типовые схемы статоров одноконтурных авиационных двигателей:
а - с «внутренней» связью; б - с «наружной» связью; в- с комбинированной связью;
1 - корпус компрессора; 2 - корпус переднего подшипника; 3 - корпус среднего подшипника;
4 - корпус турбины; 5 - корпус заднего подшип ника; 6 - корпус газосборника; 7 - корпус заднего подшипника; 8 - корпус камеры сгорания
пусов, при которой к корпусу среднего подшип ника ротора независимо крепят корпус заднего подшипника ротора, а через корпус камеры сго рания - корпус турбины.
В настоящее время нашли широкое примене ние силовые схемы статоров типа би в. Силовая схема типа а широко не распространена на дви гателях с прямым потоком газа ввиду относи тельно небольшой жесткости и сложности конс труктивного выполнения. Однако она применя ется на двигателях с петлевым потоком газа, к примеру, на промышленных ГТД или двигате лях малой мощности.
Силовые схемы статоров двухконтурных дви гателей в основном являются развитием какойлибо из вышеперечисленных схем с включени ем в нее силового корпуса наружного контура. Рассмотрим одну из таких схем статоров на при мере авиационного двигателя ПС-90А.
В силовую схему статоров газогенератора двигателя ПС-90А (рис. 4.17) входят разделитель ный корпус 7, корпус 2 КВД, наружный корпус 3
152
4.4. Опоры роторов ГТД
Рис. 4.17. Силовая схема статора двигателя ПС-90А:
1 - разделительный корпус; 2 - корпус КВД; 3 - наружный корпус камеры сгорания; 4 - внутренний корпус камеры сгорания; 5 - корпус турбины; б - задняя опора; 7 - стойки (штыри) камеры сгорания; 8 - опора шарикоподшипника ротора низкого давления; 9 - наружный корпус вентилятора; 10 - наружный корпус; /У, 12,13 - опоры ротора низкого давления; 14, 15, 16 - опоры ротора высокого давления
ивнутренний корпус 4 камеры сгорания, кор пус 5 турбины, задняя опора 6. Наружный корпус
ивнутренний корпус камеры сгорания жестко соединены между собой стойками (штырями) 7. К силовой схеме газогенератора через раздели тельный корпус жестко присоединены силовые элементы наружного контура - опора 8 шарико подшипника ротора низкого давления, наружный корпус 9 вентилятора, наружный корпус 10.
Вдвигателе применены трехопорная схе ма ротора ВД и трехопорная схема ротора НД. Опоры 11, 12, 13 - опоры ротора НД, причем опора 11 служит для восприятия осевого уси лия и передачи его на корпус газогенератора. Опоры 14, 15, 16 - опоры ротора ВД, причем опора 15 служит для восприятия осевого уси
лия и передачи его на корпус газогенератора. В опорах 11 и 15 установлены радиально-упор ные шарикоподшипники, в остальных опорах - роликовые подшипники.
Крепление двигателя ПС-90А к пилону само лета, передача силы тяги к силовым элементам пилона осуществлены деталями системы подвес ки (более подробно см. подразд. 4.5).
4.4. Опоры роторов ГТД
Опоры ГТД служат для передачи усилия от вращающихся роторов к корпусам. Опоры вос принимают значительные статические и динами ческие усилия от валов двигателя. Они должны обеспечивать достаточную жесткость силовой схемы двигателя и необходимое центрирование валов во всем диапазоне реализуемых нагрузок.
В настоящее время получили распростране ние следующие типы опор:
-опоры жесткого типа, воспринимающие усилия во всех направлениях;
-упруго-демпферные опоры, устанавлива емые преимущественно на радиальные подшип ники;
-опоры межроторного типа.
Кпреимуществам опор первого типа можно отнести достаточно простую конструкцию, воз можность передачи значительных осевых и ра диальных усилий. Недостатком жестких опор является их большая чувствительность к тем пературному градиенту, что приводит к значи тельному изменению посадки наружных колец подшипников. К опорам жесткого типа предъяв ляются высокие требования по точности меха нической обработки посадочных мест под под шипники.
К преимуществам опор второго типа мож но отнести возможность самоустановки опоры
впроцессе работы, меньшую массу, чем у опор первого типа, возможность некоторогодемпфиро вания передаваемых усилий, меньшую чувстви тельность к температурным градиентам. Недос татки опор данного типа - относительная слож ность конструкции, ограничение использования из-за гибкости. Проявление динамических явле ний в таких опорах требует их доводки в про цессе разработки.
Опоры межроторного типа не нуждаются в прямой связи с корпусами двигателя. Они пе редают нагрузку на силовые корпуса через тот ротор, на который опираются. Опоры этого ти па наиболее компактны, но требуют серьезной
153
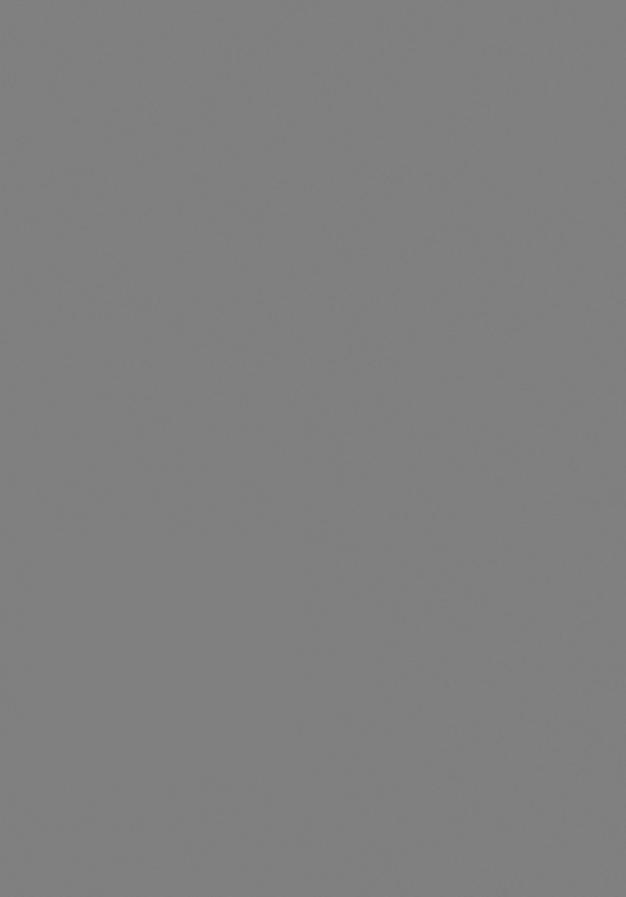
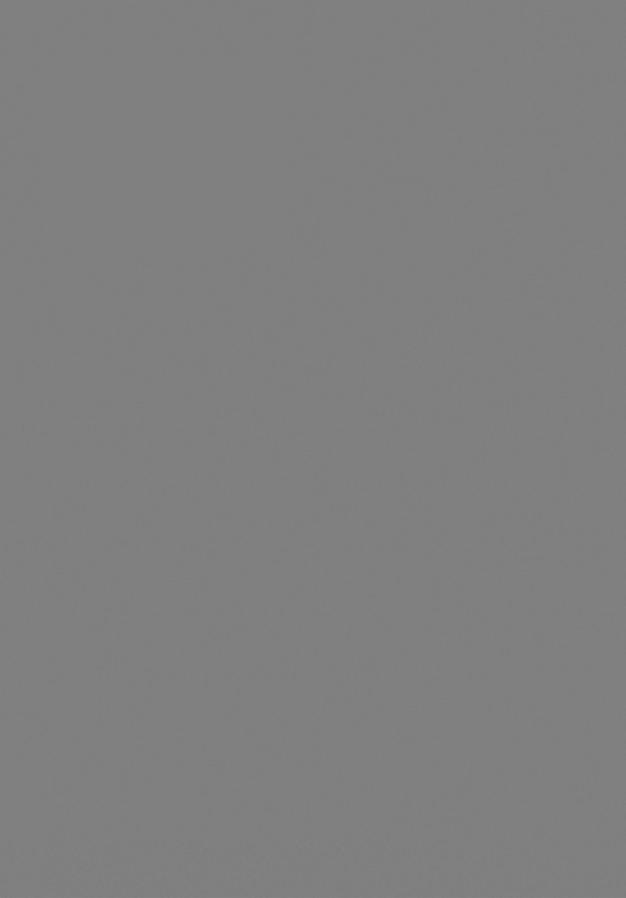
Глава 4. Силовые схемы ГТД
минимальные радиальные размеры в зонах пар трения (поворотные лопатки компрессора, шес теренчатые насосы маслосистемы, заслонки воз душных систем и т.д.).
Подшипники качения классифицируют по следующим признакам:
1)по направлению воспринимаемой нагруз ки относительно оси вала - радиальные, ради ально-упорные, упорные;
2)по форме тел качения - шариковые, роли
ковые.
В опорах роторов ГТД применяются, как пра вило, однорядные шариковые и роликовые под шипники с сепараторами. Наличие сепаратора позволяет распределить тела качения (шарики, ролики) равномерно по окружности. При этом исключается их взаимное задевание (трение) и обеспечивается стабильный процесс распре деления нагрузки (рис. 4.20).
Соотношение габаритных размеров подшип ников качения определяет их серию: сверхлегкую, особо легкую, легкую, легкую широкую, сред нюю, среднюю широкую и тяжелую.
В ГТД применяются преимущественно под шипники сверхлегкой, особо легкой, легкой и средней серий.
Для российских подшипников качения харак теристика типа и исполнения, точности изготовле ния, его конструктивных особенностей заложена в условном обозначении, узаконенном государс твенным стандартом ГОСТ 3189-89[4.3].
Условное обозначение подшипника состоит из основного и вспомогательного (рис. 4.21). Основное обозначение - цифровое, максималь ное количество цифр - семь.
Порядковый номер цифр в основном обозна чении считают справа налево.
*1 - внутренний диаметр подшипника.
Рис. 4.20. Типы подшипников ГТД:
а - шариковый подшипник - воспринимает все
виды нагрузок; б - роликовый подшипник -
воспринимает только радиальные нагрузки
Число из первых двух цифр от 04 до 99, ум ноженное на 5, даст внутренний диаметр под шипника. Числа менее 04 обозначают внутрен ние диаметры:
00 - 10 мм, 01 - 12 мм, 02 - 15 мм, 03 - 17 мм. *2 - серия подшипников по наружному диа
метру:
9 и 8 - сверхлегкая,
1 и 7 - особо легкая,
2 - легкая,
5 - легкая широкая,
3 - средняя,
6 - средняя широкая,
4 - тяжелая,
5 - особо тяжелая (только для упорных под шипников).
*3 - тип подшипника (форма тел качения и на правление воспринимаемой нагрузки):
0 - шариковый радиальный однорядный,
1 - шариковый радиальный сферический двух рядный,
2 - роликовый радиальный с короткими ци линдрическими роликами,
3 - шариковый радиальный сферический двух рядный,
4 - роликовый радиальный с длинными цилин дрическими роликами или иглами,
5 - роликовый радиальный с витыми роликами,
6 - шариковый радиально-упорный,
7 - роликовый конический,
8 - шариковый упорный,
9 - роликовый упорный.
* 4 - условное обозначение конструктивной разновидности подшипника.
*5 - условное обозначение серии по ширине и высоте подшипника.
*6 - условное обозначение материала деталей подшипника (например, *8, *9 и т.д.).
*7 - условное обозначение специальных тех нических требований (например, *10 и т.д.).
* 8 - Р (PI, Р 2 ...)- детали подшипников из теплостойких сталей.
*9 - Л (Л1, Л2...) - сепаратор из латуни.
*10 - У (У1, У2...) - дополнительные тех нические требования к шероховатостям повер хности деталей, к радиальному зазору и осевой «игре», к покрытию.
Пример расшифровки обозначений подшип ника. Подшипник 6-80202Т2С15 - шариковый радиальный однорядный с двумя защитными шайбами, изготовлен из стали ШХ-15 с габа ритными размерами по ГОСТ 7242-70 [4.4], по 6-му классу точности, с радиальным зазо ром по основному ряду, с температурой отпус ка 250 °С (Т2), заполнен пластичной смазкой ВНИИ НП-207 (С 15),
156
4.4. Опоры роторов ГТД
Вспомогательное обозначение
|
|
Основ ное обозначение |
|
|
|
|
|
|||
х х - х |
|
|
|
|
|
|
|
Г |
|
■Л |
х |
х |
х |
х |
х |
х |
а |
х |
в |
х |
Класс точности Ряд радиального зазора (0 - основной ряд и т.д.)
Рис. 4.21. Условное обозначение подшипника
0 2 - внутренний диаметр подшипника, рав ный 15 мм;
2 - серия наружного диаметра - легкая;
0 - тип подшипника - радиальный шариковый;
08 - конструктивная разновидность - с двумя защитными шайбами;
0 - серия ширины - нормальная. Дополнительно заводы-изготовители авиаци
онных подшипников указывают индивидуаль ный номер подшипника и номер партии - год и месяц изготовления подшипника.
Перед постановкой в изделие заводы-изгото вители авиационных двигателей маркируют под шипники: указывается место установки и номер двигателя (номер комплекта).
4.4.4.2. М атериалы подшипников
Кольца и тела качения подшипников работа ют при значительных сосредоточенных нагруз ках, вызывающих высокие контактные напря жения, в условиях многоциклового воздействия. Одновременно рабочие поверхности этих дета лей подвергаются истиранию вследствие про скальзывания, сопровождающего процесс вра щения подшипника.
Контактные напряжения в рабочих зонах мо гут достигать весьма больших значений (поряд ка 4000 МПа).
В связи с этим к подшипниковым материалам предъявляется ряд специфических требований, основное из которых наличие высокой твердо сти. Твердость колец и тел качения подшипни ков, как правило, должна быть не менее 59 HRC. В ряде случаев для специфических условий применения, когда нагрузки на подшипники малы, допускается использование материалов, имеющих твердость в пределах 45...50HRC.
Кроме этого, подшипниковые материалы долж ны обладать высокими прочностными характе ристиками, сопротивлением износу, удовлетво рительными усталостными свойствами, вязкос тью (сопротивлением хрупкому разрушению). Для определенной группы подшипников необ ходимо, чтобы материалы могли противостоять воздействию повышенных температур и агрес сивных сред (тепло- и коррозионностойкие под шипниковые материалы).
Материалы для деталей подшипников харак теризуются высокой структурной и размерной стабильностью. Для достижения указанного ком плекса свойств необходимо, чтобы подшип никовые материалы обладали минимальной за грязненностью неметаллическими включениями, удовлетворительной макроструктурой, отсутстви ем микронесплошностей, регламентированными структурными характеристиками перлита, мар тенсита, карбидной составляющей и т.п. Прини мая это во внимание, подшипниковые материалы можно разделить на три основные группы.
Первая группа - стандартные подшипниковые материалы, включающие в себя высокоуглеро дистые хромистые твердокалящиеся стали и низ коуглеродистые легированные конструкционные стали с поверхностным упрочнением.
Вторая группа - теплопрочные и коррозион но-стойкие высокоуглеродистые легированные стали и сплавы.
Третья группа - неметаллические материалы. При создании авиационных двигателей про слеживается тенденция к увеличению удельной мощности, снижению массы и повышению рабо чей температуры деталей опор. Поэтому для де талей авиационных подшипников в большинстве случаев приходится использовать специальные
157
Глава 4. Силовые схемы ГТД
материалы. Например, к низколегированным хро мистым сталям, широко применяемым в общем машиностроении, прежде всего добавились кор розионно-стойкие стали, теплопрочные цементи руемые стали, а также различные виды керамики.
Отечественная промышленность при произ водстве подшипников использует следующие ма териалы:
-Ш Х15-Ш - хромистая высокоуглеродистая твердокалящаяся сталь, изготавливаемая мето дом электрошлакового переплава. Подшипники, изготовленные из этой стали, могут работать при температуре до 120 °С. Для повышения рабочей температуры подшипников необходима допол нительная термообработка стали (отпуск при более высокой температуре), но при этом твер дость стали уменьшается. В этом случае под шипники из данной стали применяются при тем пературах эксплуатации ниже 200 °С.
-8Х4В9Ф2-Ш (ЭИ347Ш) - легированная вольфрамом теплопрочная подшипниковая сталь, изготавливаемая методом электрошла кового переплава. Подшипники, изготовленные из этой стали, могут работать при температуре до 450 °С, поэтому широко применяются в опо рах основных валов ГТД. По сравнению со ста лью ШХ15-Ш данная сталь менее технологична
иимеет более высокую стоимость.
-95Х18-Ш - коррозионно-стойкая высокох ромистая сталь, изготавливаемая методом элект рошлакового переплава. В зависимости от темпе ратуры эксплуатации подшипников применяют два варианта термообработки деталей: с низким отпуском 150... 160 °С и с отпуском на вторичную твердость при 400...420°С. Подшипники издан ной стали применяются, как правило, в местах не имеющих циркуляционной смазки (шарнирные подшипники для крепления двигателя в мотогон доле, подшипники тросовой системы и т.п.).
В настоящее время для производства авиа ционных подшипников качения иностранные производители подшипников используют сле дующие материалы:
-AISI 52100высокоуглеродистая хромис тая сталь, получаемая методом вакуумно-ду гового переплава. Подшипники, выполненные из этой стали, могут работать при температуре до 120 °С. Для стабильной работы при более высокой температуре (до 205 °С) необходима дополнительная термообработка стали, но при высокой температуре твердость стали уменьша ется. Отечественный аналог - сталь ШХ15-Ш;
-М50 - молибденовая теплопрочная сталь. Высокая чистота материала достигается мето дом двойного вакуумного переплава (вакуумно индукционная выплавка с последующим ваку
умно-дуговым переплавом). В настоящее время М50 является преобладающей сталью, исполь зуемой для производства авиационных подшип ников, работающих при высокой температуре. Подшипники, выполненные из этой стали, мо гут работать при температуре до 320 °С. У стали М50 существует «барьер», когда из-за боль шой скорости вращения (приблизительно при d'N = 2,4 -106 (мм • об/мин), где d - внутренний диаметр подшипника (мм), N - скорость враще ния вала (об/мин)), натяга при посадке и изгиба ющих или деформирующих напряжений на до рожке качения подшипника появляются окруж ные растягивающие напряжения, превышающие величину 190 МПа. Эти напряжения увеличи вают общие напряжения материала, появляю щиеся вследствие контакта при качении, что приводит к усталостному выкрашиванию и рас трескиванию вращающегося кольца. Подшип ники, выполненные из стали М50, рекомендует ся использовать при d'N до 2-106 (мм-об/мин). В отечественной подшипниковой промышлен ности применяется аналог - высоковольфрамовая теплопрочная сталь ЭИ347-Ш;
-М50 Nil - цементируемая сталь, основан ная на стали М50, со сниженным содержани ем углерода (0,12 %). Так же как и М50, сталь М50 Nil получается методом двойного вакуум ного переплава. Эта сталь рекомендуется для применения при значении параметра d'N от 2 -106 до 2,4 -106 (мм • об/мин). Стойкость стали к напря жениям растяжения достигается благодаря тому, что при цементации в цементируемом слое возни кают остаточные сжимающие напряжения. В оте чественной промышленности нет теплопрочных цементируемых подшипниковых сталей;
-М50 SuperNil - это сталь М50 Nil, термооб работанная по специальному технологическому процессу. В результате специальной термообра ботки остаточные внутренние сжимающие напря жения получаются больше, чем у стали М50 Nil. М50 SuperNil рекомендуется для применения при d'N от 2,5 -106 до 3 -106 (мм *об/мин);
-AISI 440С - коррозионно-стойкая сталь, имеющая незначительную усталостную про чность в связи с низкой твердостью из-за осо бенностей структуры материала (наличие из быточных карбидов). Применение этой стали
вавиационной промышленности ограничено. Отечественный аналог - сталь 95X18;
-C ronidur 3 0 - азотируемая мартенситная нержавеющая сталь. Этот материал, созданный
вГермании для подшипников качения, проде монстрировал улучшение коррозионной стойкос ти в сто раз по сравнению с AISI 440С и в пять раз увеличение срока службы подшипников по срав
158
нению со сталью М50. Cronidur 30 отличается от применяемых для подшипников сталей высо ким содержанием хрома.
Из керамических материалов, используемых для производства высокоскоростных подшипни ков качения, лучше всего зарекомендовал себя нитрид кремния /Si3N4/. Особенности этого материала - высокая прочность, высокая твер дость, коррозионная стойкость и низкая плот н о сть - позволяют применять его при более высоких температурах и снизить массу. В то же время увеличение срока службы может быть до стигнуто путем снижения тепловыделения, на пряженности материала и износа подшипника. Коррозия может быть полностью исключена как причина отказа.
В настоящее время нитрид кремния широко используется для изготовления подшипников. Наибольший эффект дают комбинированные подшипники (подшипники с керамическими те лами качения и стальными кольцами).
Чисто керамические подшипники из-за вы сокой стоимости применяются только в осо бых случаях: при работе без смазки в условиях очень высоких температур. Вследствие этого их применение в авиации в обозримом будущем ограничено.
Для изготовления сепараторов авиацион ных подшипников используются следующие материалы:
-безоловянистые бронзы;
-латунь;
-магниевый чугун;
-стали, имеющие закалку до 35.. .40 HRC3;
-алюминиевые сплавы;
-текстолит.
При этом сепараторы из алюминиевых спла вов и текстолита используются в подшипниках, рабочая температура которых не превышает 150 °С. Для остальных материалов рабочая тем пература может быть 300 °С и выше.
В отдельных случаях (например, в подшипни ках главных валов) на сепараторы наносят анти фрикционное покрытие:
-свинцово-оловянистое (при рабочей тем пературе до 250 °С);
-серебро (при рабочей температуре 300 °С
ивыше).
Коэффициент теплового расширения матери ала сепаратора должен быть близок, насколько это возможно, к коэффициенту теплового рас ширения материалов наружного и внутренне го колец, а также тел качения подшипника. Это необходимо для обеспечения стабильных (или минимально изменяемых) зазоров в подшипнике в процессе работы.
4.4. Опоры роторов ГТД
4.4.4.3. Условия работы и особенности конструкции подшипников ГТД
ВГТД подшипники опор работают в условиях сравнительно высоких радиальных и осевых на грузок, высоких окружных скоростей. Кроме того, на работоспособность подшипников оказывают значительное влияние такие факторы, как темпе ратурное состояние опоры, организация подачи смазки на тела качения, наличие частиц загрязне ний в масле, точность изготовления, а также конс труктивные особенности непосредственно самих подшипников.
Вопорах роторов ГТД применяются исклю чительно подшипники качения: однорядные ша риковые - для восприятия радиальных и осевых нагрузок и однорядные роликовые - для вос приятия радиальных нагрузок. Основные типы
иконструктивные особенности шариковых под шипников показаны на рис. 4.22.
Подшипник а применяется как радиально упорный. Радиус беговой дорожки в нем несколь ко больше радиуса шара. Под действием осевой силы в подшипнике линия контакта смещается на угол контакта а, величина которого и опреде ляет величину нагрузки. Направление восприни маемых нагрузок - радиальных и осевых - в обе стороны. Величина допустимой осевой нагрузки может достигать до 70 % от неиспользованной допустимой радиальной нагрузки.
Подшипник б имеет разъемное наружное кольцо с большой глубиной канавки и увели ченный угол контакта а, что позволяет воспри нимать большие радиальную и осевую нагрузки.
В таких подшипниках шарики имеют контакт с беговыми дорожками в трех точках, их называ ют трехточечными.
Подшипник в имеет разъемное внутреннее кольцо с двумя точками контакта и неразъемное наружное кольцо со специальным профилем бе говой дорожки, который также обеспечивает кон такт с шариком в двух точках с увеличением утла контакта а. Такие подшипники (с четырехточеч ным контактом) могут воспринимать еще более высокие радиальные и осевые нагрузки. Однако следует учитывать, что увеличение точек контак та не проходит бесследно и приводит к увеличе нию тепловыделения при работе подшипника, что требует, в свою очередь, увеличения подачи масла для обеспечения съема тепла. Подшипники с четырехточечным контактом обеспечивают восприятие максимальных радиальных и осе вых нагрузок при минимальном осевом люфте подшипника.
Нередки случаи, когда отдельные элементы подшипников проектируются с учетом инди
159
Глава 4. Силовые схемы Г Т Д
видуальных особенностей конструкции опор, требований технологии и т.д. На рис. 4.22 при ведены такие конструктивные особенности под шипников. Подшипник г имеет наружное коль цо с отверстиями для подачи масла для смазки шаров. Аналогичные отверстия могут выпол няться на внутренних кольцах подшипников. Наружное кольцо подшипника д имеет фланец для крепления к корпусу опоры. Подшипник е имеет на наружном кольце специальный буртик для крепления съемного приспособления для демонтажа подшипника.
Основные типы роликовых подшипников, применяемых в ГТД, приведены на рис. 4.23.
На подшипниках а и б осевая фиксация ро ликов осуществлена бортами, расположенными на подвижном внутреннем кольце и на непод вижном наружном кольце соответственно. У ро ликовых подшипников для компенсации значи тельных температурных перемещений вала или корпусных деталей внутреннее или наружное кольцо могут выполняться значительно более широкими. Учитывая большую степень интегра ции подшипниковых узлов в конструкцию опор, довольно часто роль наружного или внутреннего кольца возлагают на детали корпуса или ротора, что позволяет уменьшить диаметральные раз меры опор. В этом случае применяют подшип ники в и г. На этих же исполнениях на кольцах подшипника показаны отверстия для подвода масла на ролики.
Важным элементом конструкции подшип ника, определяющим его работоспособность, является сепаратор, в частности его центров ка. Центрировать сепаратор можно как по на ружному, так и по внутреннему кольцу. В каж
а
а |
б |
в |
дом из этих способов есть свои преимущества и свои недостатки.
При центровке сепаратора по внутреннему кольцу (рис. 4.24) происходит следующее: под действием неуравновешенной силы Р сепаратор прижимается к кольцу, его внутренняя повер хность будет изнашиваться в секторе, который был легким. Таким образом, легкая часть сепа ратора будет становиться еще более легкой, а не уравновешенная сила сепаратора с центровкой по внутреннему кольцу в процессе износа будет увеличиваться. При центровке по внутреннему кольцу температурное расширение сепаратора приводит к увеличению зазора между кольцом и сепаратором, что исключает возможность за клинивания последнего.
При центровке сепаратора по наружному кольцу (см. рис. 4.24) явление износа сепарато ра в «тяжелом» секторе приводит к уменьшению неуравновешенной силы. Отрицательной сторо ной такой центровки является то, что при измене нии температурного режима работы подшипника возможно расширение сепаратора с уменьшением зазора между ним и наружным кольцом до нуля с последующим заклиниванием сепаратора в на ружном кольце.
Необходимо отметить, что центровка сепа ратора по наружному кольцу улучшает условия смазки, так как появляется возможность подачи масла в увеличенный зазор между сепаратором и внутренним кольцом, уменьшает удельное дав ление на поверхности центрирования, обеспечи вает лучший отвод тепла от подшипника через более холодное наружное кольцо.
Для работы подшипника важное значение имеет точность и качество изготовления как са-
|
■ Я |
1 |
I f f g |
|
ypm |
l E B l |
I H -J T - |
|
|
|
г |
д |
е |
Рис. 4.22. Типы и особенности шариковых подшипников, применяемых в ГТД:
а - двухточечный; б -трехточечный с разъемным наружным кольцом; в - четырехточечный с разъемным внутренним кольцом; г - с подводом масла через наружное кольцо; д - с фланцевым креплением наружного кольца к корпусу опоры; е - с технологическим буртом для демонтажа
160