
книги / Технология металлов
..pdfханизации подачи формовочной смеси |
и транспортировании |
|
опок) |
120 опок, 60 форм. |
изготовляют формы |
Н а |
в с т р я х и в а ю щ и х м а ш и н а х |
в высоких опоках. Формовочная смесь уплотняется встряхиванием за счет инерции, возникающей при ударе (рис. 90).
На столе встряхивающей машины укреплена плита с моделью, на которую ставят опоку и наполняют формовочной смесью. Стол встряхивающей машины под действием сжатого воздуха давлением 5—7 атм поднимается на некоторую высоту и с этой высоты падает, ударяясь об опору. При ударе смесь уплотняет ся. Высота подъема стола в машинах 30—100 мм и число уда
ров 10—300 в минуту. |
|
|
|
|
К такому типу машин отно |
|
|||
сится формовочная машина мо |
|
|||
дели 845 с поворотным столом. |
|
|||
Размеры |
опоки |
в |
свету |
|
1200X800 мм, высота |
ее |
450 мм. |
|
|
Часовая |
производительность — |
|
||
около 15 форм. |
|
|
|
|
И з г о т о в л е н и е фо р м на |
|
|||
в с т р я х и в а ю щ и х м а ш и н а х |
|
|||
с п о д п р е c c o i B к о й. Плотность |
|
|||
набивки |
формы, |
полученной |
Рис. 90. Схема уплотнения |
встряхиванием, |
неравномерна. |
формовочной смеси |
встряхи |
||
Поэтому более широкое примене |
|
ванием: |
|
|
|
/ — встряхивающий |
стол; |
2 — |
|||
ние получили встряхивающие ма |
модель; |
3 — опока; 4 — наполни |
|||
шины с допрессовкой верхних сло |
|
тельная рама |
опоки |
||
ев формы, например машина модели 254 |
М. Размеры |
в свету 800X700, высота ее 300 мм. Часовая производительность при полной механизации формовочного участка 45 опок.
К этому же типу машин относятся автоматические формовоч ные четырехпозиционные машины модели 94265 для изготовле ния верхних полуформ и модели 94265А для изготовления ниж них полуформ. На этих машинах изготовляют формы в опоках с размерами в свету 900 X 800, при высоте 500—600 мм.
И з г о т о в л е н и е фо р м на п е с к о м е т а х . Пескометы применяются для изготовления средних и крупных форм. Су ществуют стационарные пескометы, передвижные с бункером и консольные передвижные. Пескометом формовочная смесь по дается в опоку и уплотняется в ней под действием центробежных сил вращающихся лопаток, расположенных в головке пескомета.
На рис. 91 приведена схема устройства консольно-подвижно го пескомета. Формовочная смесь по ленточному транспортеру 1 подается в лоток 2, снабженный ситом. Просеянная смесь по ступает на транспортер 3, из него в воронку 4 и оттуда на лен точный транспортер 5. С ленточного транспортера смесь посту
пает в кожух пескометной головки б, где подхватывается лопат ками 5, укрепленными на вращающемся диске 7 (скорость вра щения 1400—1600 об/мин) и выбрасывается в опоку 10 через отверстие 11 в головке пескомета. При набивке опоки рабочий, сидящий на сиденьи 12, поворачивает и передвигает хобот песко мета. Степень уплотнения смеси зависит от скорости вращения ло паток, перемещения головки и от высоты ее над моделью 9.
Производительность пескомета 12,5 мъ/час набитой формо вочной смеси. Действующие модели пескометов этого типа —► 291,296 м.
На заводах крупносерийного и массового производства от ливок формовочные машины расположены вдоль замкнутого конвейера (рис. 92), который представляет собой ряд тележек /, непрерывно движущихся по рельсам 2 при помощи привода 3. Изготовленные на машинах формы 4 ставятся на тележки кон вейера. Сборку форм обычно производят на рольгангах 5, уста новленных у формовочных машин. Формы заливают на конвейе ре из заливочных ковшей б, подаваемых по разливочному моно рельсу 7.
При большой скорости движения конвейера заливочная пло щадка §, на которой стоит рабочий, заливающий формы, дви жется со скоростью конвейера. Залитые металлом формы на конвейере проходят через охладительную камеру 9 и поступают в отделение выбивки. Здесь при помощи пневматического подъ емника 10 формы с конвейера снимаются и выбиваются на вы-
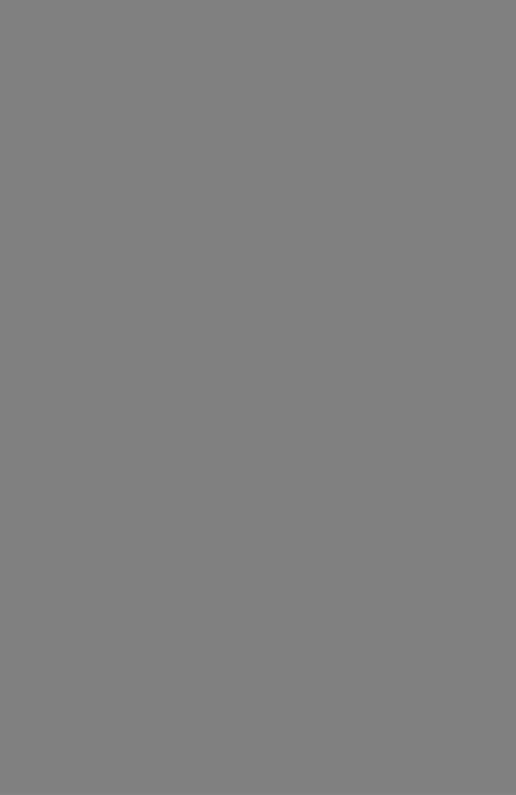
Площадь сечения питателей |
определяют |
по следующей |
фор |
||
муле: |
|
|
|
|
|
|
F n m |
= |
М/ 0,31 • Н р СМ* ’ |
|
|
где |
Q — вес отливки, кг; |
|
|
|
|
|
t — время заливки, сек.; |
|
|
||
|
Нр — расчетный напор, см; |
для чугуна |
|
||
|
М — коэффициент |
расхода, равный |
0,27— |
||
|
0,55, для стали 0,3— 0,41, для |
сплавов цветных ме |
таллов 0,6—0,7.
Расчетный напор Нр определяют по формуле
^_ 2Н0С — Р2
П Р — 2С *
где Н0— высота стояка от уровня металла до подвода в фор му, см;
С — максимальная высота отлив'ки, см; Р — высота отливки до места подвода металла в фор
му, см.
Соотношение размеров литниковой системы принимают сле дующим:
/^стояка • Fшл • -Рпит = (1 >25 — 1,4): 1,1 : 1.
Изготовление стержней
Стержни представляют собой часть литейной формы. Во вре мя заливки формы стержни окружают металлом, поэтому они должны обладать по сравнению с формой более высокой проч ностью, газопроницаемостью, податливостью, огнеупорностью и легко выбиваться из отливки.
Прочность стержней увеличивается введением в состав стер жневых смесей связующих добавок, установкой внутри стержня каркаса и сушкой стержней.
Газопроницаемость стержня повышается в результате обра зования внутри него специальных вентиляционных каналов, вы ходящих в знак.
Податливость и выбиваемость повышаются в результате вве дения в состав стержневой смеси органических добавок и умень шения количества глины, а огнеупорность смеси — в результате введения высокоогнеупорных материалов.
Стержни изготовляют в стержневых ящиках и при помощи шаблонов. При индивидуальном и мелкосерийном производстве отливок стержни изготовляют ручным способом в деревянных стержневых ящиках. При крупносерийном и массовом произвол-
стве их изготовляют в металлических стержневых ящиках на прессовых, встряхивающих, пескодувных и пескострельных ма шинах. Первые два типа машин принципиально не отличаются от машин, применяемых для изготовления форм. На пескодув-
Рис. 94. Схема пескодувной стержневой машины:
1 — пневматический стол; 2 — стержневой ящик; 3 — пескодувный резервуар; 4 — клапан дутья
ных и пескострельных машинах стержень изготовляется вдува нием стержневой смеси в ящик с помощью сжатого воздуха.
Пескодувные машины работают по принципу интенсивного смешения воздуха со стержневой смесью (рис. 94).
К ним относятся машина модели 287 производительностью 240 стержней в час и полуавтоматическая машина модели 28А10.
Стержневые ящики, применяемые для работы на этих маши нах, имеют каналы на разъеме для выхода воздуха. В углубле ниях кармана и в углах ящиков устанавливают венты, имеющие щели или отверстия, запаянные тонкой сеткой, через отверстия которой воздух выходит, а песок проходить не может.
В пескострельных машинах сильного смешения воздуха со стержневой смесью не наблюдается (рис. 95).
Рис. 95. Схема пескострельной машины:
1 — рабочий резервуар периодически загруженный стержневой смесью; 2 — гильза с зазорами; 3 — вер тикальные щели; 4 — горизонтальные щели; 5 — ко нусная насадка; 6 — клапан; 7 — реверсивер для пода чи сжатого воздуха; S — шибер; 9 — бункер
К ним относятся машина модели 305, полуавтоматические машины 28БЗ, 28Б5 и др. Их техническая характеристика сле дующая:
|
|
Модель |
|
|
305 |
28БЗ |
28Б5 |
Максимальный вес стержня, к г |
7 |
5 |
16 |
Производство стержней в час |
— |
250 |
200 |
По шаблонам обычно изготовляют стержни цилиндрической формы из песчано-глинистых смесей и применяют для отливки труб и деталей, подобных им по форме.
Сушка форм и стержней
Формы для получения отливки весом свыше одной тонны подвергают сушке, так как сырые формы имеют недостаточную прочность для отливок подобного веса. Стержни, как правило, также подвергают сушке. В процессе сушки повышается проч ность и газопроницаемость. Связующие добавки, находящиеся в
риалом (лужение, фосфотирование, оцинкование и т. п.), чтобы избежать образования раковин в отливке в месте установления жеребейки. Сечение ножки жеребейки принимают 0,5—0,7% от толщины стенки отливки. При малой толщине ножка жеребейки может преждевременно (до затвердевания отливки) расплавить ся и не обеспечить устойчивости стержня. При большой толщине жеребейка может не свариться с металлом отливки.
Правильность установки стержней проверяют шаблоном, пос ле чего нижняя половина формы покрывается верхней и уста навливается-литниковая чаша. Во избежание подъема верхней половины формы в процессе заливки металлом обе половины формы скрепляют между собой или кладут на них груз*
2. С ВО Й С ТВА Л И Т Е Й Н Ы Х С П Л А В О В
В литейном производстве применяют такие сплавы, которые обладают хорошими литейными свойствами, позволяющими по лучать из них высококачественные фасонные отливки сложной конфигурации. Чистые металлы обычно имеют худшие литейные свойства, чем сплавы и поэтому почти не применяются для про изводства отливок.
Литейные сплавы должны обладать в основном следующими свойствами:
1. Невысокой температурой плавления. Чем ниже температу ра плавления сплава, тем легче его расплавить и нагреть до тре буемой для заливки в формы температуры.
Литейные сплавы имеют следующие примерные пределы температуры плавления: сталь — 1420—1520° С; чугун — 1150— 1250° С; бронза — 1000—1150° С; латунь — 900—950° С; алюмини евые сплавы -- 580—630° С; магниевые сплавы — 600—650° С, цинковые сплавы — 390—420° С.
2.Высокой жидкотекучестью в расплавленном состоянии, обеспечивающей хорошую заполняемость литейной формы при изготовлении тонкостенных отливок.
3.Малой усадкой при затвердевании и охлаждении, обеспе чивающей получение отливок без усадочных раковин, рыхлот и внутренних напряжений.
4.Не должны в жидком состоянии поглощать газы, чтобы от ливки не имели газовых раковин и обладали лучшими механи ческими свойствами.
5.Незначительной ликвацией (неоднородностью), обеспе чивающей более однородные свойства в различных частях от ливок.
6.Мелкокристаллической структурой после охлаждения, обес печивающей высокие механические свойства отливок.
Температура плавления и заливки сплавов в формы
Под температурой плавления сплава понимают температуру ликвидуса на диаграмме состояния. В реальных сплавах обычно присутствуют не два компонента, как это указывается на диаг раммах состояния, а три, четыре и более. Это затрудняет определение по диаграммам температуры плавления сплава, В каждом частном случае температуру плавления сплава уста навливают опытным путем или определяют расчетно, исходя из влияния отдельных компонентов сплава на температуру пла вления.
Температуру сплава, при которой заливают формы, всегда принимают выше температуры его плавления, чтобы получить нужную жидкотекучесть для лучшего заполнейия форм. Кроме того, при более высокой температуре разливки сплава легче вы деляются неметаллические включения в особенности из жидкой стали и чугуна. Однако разница в температурах заливки сплава в форму и его плавления ограничивается определенными преде лами, зависящими как от свойств самого сплава, так и от осо бенностей получаемых из данного сплава отливок. Например, чем сложнее отливки и чем тоньше их стенки, тем больше должна быть эта разница. Но при этом следует учитывать, что заливка сплава при высокой температуре в песчаные формы усиливает пригар формовочных смесей к отливкам, в особенности при по лучении отливок из тугоплавких сплавов — стали и чугуна. Кро ме этого, повышение температуры разливки в ряде случаев при водит к получению крупнокристаллической структуры в от ливках, что понижает их механические свойства, к развитию усадочных раковин и рыхлот, поглощению газов и повышению
склонности сплава к ликвации и образованию горячих |
трещин |
в отливках. Учитывая все эти факторы, температуру |
заливки |
каждого сплава устанавливают опытным путем в зависимости от его химического состава и особенностей получаемых отливок. На качество получаемых отливок влияет также и температура выпуска сплава из плавильного агрегата, которая всегда бывает выше температуры разливки сплава. Разница между температу рой выпуска сплава и плавления его называется температурой перегрева. При более высокой температуре перегрева большое количество твердых фаз растворяется в жидком сплаве и жид котекучесть сплава бывает лучше. Зависимость между темпера турой разливки и плавления сплава железа с углеродом при ведена на рис. 97.
Температура плавления некоторых легированных сталей не сколько ниже, чем углеродистых, имеющих то же содержание углерода, а температура разливки их близка к температурам
разливки соответствующих углеродистых сталей, за исключе нием высоколегированных (табл. 21).
Т а б л и ц а 21
Температура плавления и разливки стали различного состава
|
|
|
|
|
|
Т ем п ература, °С |
|
|
|
Сталь и ее элементы |
плавления | |
разливки |
|||
|
|
|
|
|
|
||
Низкоуглеродистая |
0,2% |
С . |
1525 |
1560—1635 |
|||
Среднеуглеродистая, |
0,4% |
С |
1515 |
1550—1615 |
|||
Высокоуглеродистая, |
1,0% |
1480 |
1510—1570 |
||||
Низколегированная: |
|
|
|
|
|||
0,25% |
С, |
1,4% |
М п ................. |
1500 |
1550—1590 |
||
0,25% С, 1,0% Мп, 0,6% Мо |
1500 |
1550—1580 |
|||||
0,3% |
С, 0,6% |
Мо |
|
1515 |
1560—1600 |
||
0,4% |
С, |
0,8% |
Сг . . . . |
1510 |
1560—1600 |
||
0,4% С, 0,8% Сг, 1,6% Ni |
1500 |
1550—1600 |
|||||
Высоколегированная: |
|
_ |
_ |
||||
0,1% С, 16% Сг. 8 % Ni. |
|||||||
0,2% С, 18% Сг, 8 % Ni |
1500 |
1550—1580 |
|||||
0,2% |
С, |
13% Сг |
|
|
1510 |
1560—1590 |
|
1,0% |
С, |
13% Мп |
|
1380 |
1440—1490 |
||
1,3% |
С. |
13% Мп |
|
1350 |
1420—1470 |
Рис. 97. Зависимость значений между температу рой разливки и плавлением сплавов железа с угле родом:
1 ^ - стали; 2 — коксового чугуна; 3 — серого чугуна
У легированных сталей разница между температурой плав ления и температурой разливки больше, чем у углеродистых сталей. Это вызвано меньшей жидкотекучестью легированных сталей вследствие содержания в них легирующих элементов.