
книги / Технология металлов
..pdfстроении. При этом методе к защищаемой конструкции, напри мер изготовленной из стали, прикрепляют на болтах или другим способом листы менее стойкого в данной среде металла, в част
ности цинка. |
Такие прикрепленные листы носят название |
п р о т е к т о р а . |
Протектор защищает конструкцию от коррозии |
благодаря тому, что создается многоэлектродный элемент, в ко тором протекторы являются анодами.
Протектор может защищать от коррозии также конструкцию, изготовленную из разнообразных металлов. При этом важным является то, чтобы протектор имел в данной среде электродный потенциал более низкий, чем любой из металлов, из которых из готовлена конструкция.
Эффективность протекторной защиты зависит от природы ме таллов протектора и конструкции, от плотности прилегания про тектора к конструкции, электропроводности среды, в которой ра ботает защищаемая конструкция и т. д. Поэтому в случае выбо ра этого метода защиты учитывают влияние перечисленных факторов.
Электрозащита находит применение при защите от коррозии котлов систем конденсаторов на морских судах, различных аппа ратов в химической промышленности, если они работают в рас творах, содержащих соли металла. Для этой цели защищаемая конструкция присоединяется к отрицательному полюсу источни ка постоянного тока — динамо-машине, аккумулятору или выпрямителю, а к положительному полюсу присоединяется пла стинка какого-либо металла (чугун, свинец, сталь и т. п.), поме щенная в ту же среду (электролит), что и конструкция. Пласти на металла в этих условиях становится анодом, а защищаемая конструкция катодом. На катоде выделяется водород и околокатодный слой защелачивается. Вследствие этого такой метод за щиты от коррозии возможен лишь для конструкций, изготовлен ных из металлов, стойких в щелочах, и не рекомендуется для конструкций, изготовленных из алюминиевых сплавов. При ис пользовании электрозащиты устанавливают для данных условий напряжение и плотность тока, так как при неправильном выбо ре этих параметров -может произойти даже ускорение разру шения защищаемой конструкции.
Защита обработкой внешней среды
Этот метод защиты заключается в предварительной обработ ке коррозионной среды, или в эту среду вводят специальные до бавки, предотвращающие разъедание металла.
Предварительная обработка находит применение преимуще ственно в системах водоснабжения котлов и других агрегатов. Она состоит в удалении из воды элементов, агрессивно действу
ющих на металл конструкций. Например, кислород из-воды мо жет быть удален путем нагрева ее при пониженном давлении или пропусканием воды под слоем металлической стружки (же лезной, магниевой или цинковой), имеющей большое сродство к кислороду. Удаление кислорода из жесткой воды производят обработкой ее сульфатом или бисульфатом натрия. В питатель ной воде 1вредные в коррозионном отношении соли удаляются обработкой ее щелочью.
В химической промышленности для предохранения от разъе дания аппаратов в агрессивную среду вводят специальные до бавки. Например, при перегонке нефти, содержащей хлористый магний, в пары ее вводят аммиак. Добавкой сульфатов к уксус ной кислоте снижают ее агрессивное действие на свинец. До бавки небольшого количества хромпика к охлаждаемой воде систем двигателей внутреннего сгорания полностью предотвра щают коррозию металла.
4. ЗАЩИТНЫЕ ПОКРЫТИЯ
Наиболее широкое применение в промышленности находят защитные покрытия металла. Защитные покрытия по видам классифицируются на металлические, неметаллические и хими ческие изменения поверхностных слоев металла (рис. 61).
Роль защитных покрытий главным образом преследует цель изолировать металл от внешней среды с тем, чтобы предохра нить от агрессивного действия микроэлементов поверхность ме талла. Это достигается сплошным и 'беспористым покрытием. Выбор вида покрытия определяется условиями службы, в кото рых будет находиться металл. Например, для защиты неметал лических изделий, используемых в бытовых условиях и не испы тывающих динамических нагрузок, достаточно бывает нанесения
однослойного лакокрасочного |
покрытия |
или химической обработ |
|
ки |
поверхности металла воронением |
или фосфатированием. |
|
Для |
защиты металлических |
конструкций (подъемных кранов, |
портовых сооружений, мостов, вагонов, наружных деталей авто мобилей, тракторов, сельскохозяйственных машин, велосипедов и т. п.), подвергающихся более агрессивному воздействию атмо сферы, применяются лакокрасочные покрытия, более сложные по составу и способам нанесения. Кроме защиты изделий и кон струкций от воздействия коррозии, их поверхности подвергай^ декоративной отделке. Для лакокрасочных покрытий применяют никелевые и хромовые покрытия. Для декоративных покрытий, хотя и в ограниченных масштабах (главным образом для цвет ных металлов), применяют разноцветные эмали, серебро, золо то, платинит и т. д.
Металлические изделия и конструкции, работающие в жидких средах, в воде, растворах солей, кислот и щелочей, для защиты
от коррозии подвергают металлическим и неметаллическим по
крытиям.
Изделия, соприкасающиеся с водой или атмосферной влагой, подвергают цинкованию и кадмированию; изделия, работающие в растворах серной кислоты, — свинцеванию, а изделия, которые работают в органической среде пищевых продуктов, подвергают никелированию и лужению. К неметаллическим покрытиям от носят эмалирование, облицовку кислотоупорными плитками,
Р ис. 61. К л асси ф и к ац и я покры тий
кислотоупорным цементом, покрытие фенолальдегидными смо лами, каменноугольным пеком, резиной и другими подобными материалами и композициями. По химической стойкости в ряде агрессивных сред они являются незаменимыми, как например, резина или фенолальдегидные смолы в растворах соляной кисло ты. Основными недостатками большинства неметаллических за щитных покрытий являются их невысокая теплопроводность и неудовлетворительная стойкость при температурах выше 150° С.
Металлические покрытия
В промышленности широкое распространение получили сле дующие способы металлических покрытий: гальваническое по крытие, плакирование, металлизация, диффузионный и горячий способ покрытий.
Гальв^^ичвскии способ покрытия состоит в нанесении на по верхность металлических конструкций тонкого слоя другого ме талла из ®одного раствора его соли. Этим способом производят покрытия цинком, оловом, кадмием, свинцом, никелем, медью, хромом, серебром, золотом, а также их сплавами. По защитным
свойствам гальванические |
.покрытия |
подразделяют |
на анодные |
и катодные. |
производят |
металлом, |
электродный |
А н о д н ы е покрытия |
потенциал которого в данной среде ниже электродного потен циала покрываемого металла, т. е. происходит электрохимиче ское замещение основного металла. Примером анодного покры тия являются покрытия железа цинком и кадмием. Анодные покрытия при нарушении их оплошности преимущественно сами разрушаются. Они не боятся царапин и других (внешних нару шений слоя.
К а т о д н ы е покрытия производят металлами, электродный потенциал которых в данном электролите выше потенциала ос новного металла. К катодным покрытиям железных сплавов от носятся покрытия оловом, медью, никелем и другими металла ми. Катодные покрытия механически защищают основной металл от коррозии. При нарушении сплошности покрытия, т. е. при на несении царапины, механических повреждениях, разъедания за щитные действия катодных покрытий^ пропадают и происходит интенсивная коррозия основного металла. Защитная способ ность катодных покрытий зависит главным образом от их сплошности.
Гальванические покрытия металлических изделий производят в гальванических ваннах. Для этой цели производят подготовку поверхности изделий (обдиркой, шлифовкой, полировкой, обез жириванием, травлением и т. д.) для удаления окислов, мине ральных масел, жира, шлака, пыли й других загрязнений. В процессе покрытия катодом служит покрываемое изделие, ано дом— осаждаемый металл или нерастворимый свинцовый анод. Электролитом являются кислые, щелочные или цианистые рас творы. Толщина слоя покрытия составляет 0,005—0,03 мм. При гальваническом покрытии используют постоянный ток. Источни ками постоянного тока служат выпрямители и низковольтные мотор-генераторы на 6 , 9 и 12 в с силой тока > 1500 а.
Плакированием получают биметалл для замены цветных ме таллов или специальных сталей и для защиты от коррозии ме таллов и сплавов. Основой (сердцевиной) биметалла служит преимущественно низкоуглеродистая сталь. В зависимости от наз начения получают различные биметаллы. Сталь — медь исполь зуется в виде листов, лент, проволоки в электропромышленности, машиностроении, бумажной, текстильной промышленностях, для с-пецизделий и др. Сталь — медноцинковые сплавы (томпак—■ латунь) используется в виде листов, лент при изготовлении ме дицинской, лабораторной аппаратуры, в электротехнической про мышленности. Обычно латунь применяют с содержанием 70% Си, 30% Zn и томпак, содержащий 90% Си и 10% Zn. Биметалл из стали и медноникелевых сплавов применяется для штампован
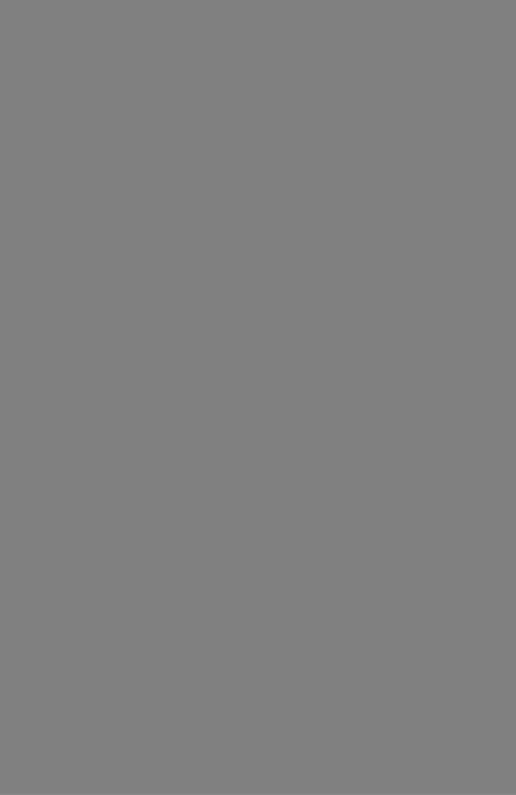
поверхности детали в виде наслаивающихся чушек, ’покрывает ее твердым слоем.
Преимуществом шопирования перед другими способами является возможность покрытия различными металлами круп ных конструкций в собранном виде и изделий из любых мате риалов, а также небольшие затраты на основное оборудование и простота процесса. К недостаткам относится образование зна чительной пористости, недостаточная прочность сцепления по крытия с поверхностью детали и невысокие защитные свойства против коррозии, а также повышенные потери металла при рас пылении.
Диффузионное покрытие металлами заключается в совмест ном нагреве до высокой температуры покрываемых изделий из металла или сплава покрытия в порошке. Этим способом произ водят аллитирование для покрытия деталей алюминием, хромизацию — покрытие хромом; силицирование — покрытие крем нием или сплавами; хромоаллитирование — хромом, алюминием; хромосилицирование — хромо-кремнием. Диффузионный способ применяется также и для покрытия железа цинком, получивший название шерардизации, с целью защиты против воздействия атмосферы.
а. Аллитированием называется процесс образования диффу зионным путем в поверхностных слоях изделия из стали, чугуна или меди жаростойкого сплава этих металлов. Технология аллитирования стальных и чугунных изделий состоит в основном в следующем. После очистки поверхности от загрязнений жира
ми, ржавчиной |
изделия загружаются в цементационные ящики |
с герметически |
закрывающимися крышками. Перед загрузкой |
на дно ящика насыпается слой аллитирующей смеси в порошке. Изделия загружают в ящик в несколько рядов и каждый ряд засыпают смесью толщиной 25—30 мм. После загрузки изделий и засыпки их смесью содержимое ящика накрывают железным листом, зазоры между листом и стенками ящика промазыва ются специальной замазкой. Затем на лист до верхней крышки ящика насыпают чугунную стружку или древесный уголь с пе ском, после чего ящик закрывают железной крышкой, зазоры между крышкой и ящиком замазывают огнеупорной глиной или обмазкой. В крышке делают отверстия диаметром 3—5 мм для выхода паров воды во время нагрева.
Ящики с изделиями загруж-ают в печь и постепенно нагре вают до температуры 150° С. При этой температуре в течение 30 мин. происходит просушивание содержимого в ящике, после чего температуру печи повышают, пока внутри ящика не создается температура 970—1000° С. При этой температуре дают вы держку в течение 5— 6 час. После выдержки печь с ящиками охлаждают до 400—500° С, затем ящики выгружают из печи.
Выгруженные ящики в дальнейшем охлаждают на воздухе, не открывая их. С целью устранения хрупкости диффузионного слоя на изделиях после аллитирования их подвергают отжигу. Для этого их повторно загружают в ящики, засыпают смесью древесного угля с песком, ящики герметически закрывают и за гружают © отжигательные печи, нагревают до 900° С и при этой температуре охлаждают.
Состав аллитированных смесей рекомендуется следующий: а) для стали, состоящей из 49% порошкообразного сплава железоалюминий, 49% окиси алюминия в порошке и 2% хлористого алюминия; б) для аллитирования чугуна 99,5% (с содержанием железа 43%), сплава железоалюминия в порошке и 0,5% хло ристого аммония. При использовании данной смеси глубина диф фузионного слоя на чугунных изделиях после 2 -часовой выдерж ки при температуре 975° С составляет 0,08 мм, при температуре 1050° С — 0,15 мм, а после 6 -ча'совой выдержки при этой же тем пературе глубина слоя увеличивается до 0,25—0,35 мм. Жаро стойкость аллитированного чугуна повышается приблизительно
в1 0 раз.
б.Хромизация является процессом насыщения поверхност ных слоев стали хромом путем диффузии при высокой темпера туре. Диффузии хрома в сталь способствует легкое образование твердых растворов железа с хромом в месте контакта. Сталь после хромизации обладает повышенной стойкостью против кор розии в азотной кислоте, морской воде, в атмосферах, содержа щих сернистые газы, сероводород, углекислоту и т. п. Жаро
стойкость такой стали повышается до температур 750—800° С. С повышением температуры свыше 800° С вследствие обеднения поверхностных слоев хромом (хром диффундирует в сталь) жа ростойкость стали резко падает.
Хромизация может быть осуществлена обработкой изделий в твердых материалах, измельченных в порошок (твердая хро
мизация), а также в атмосфере |
газов (газовая хромизация). |
При т в е р д о й х р о м и з а ц и и |
изделий используют металли |
ческий хром в порошке или феррохром с малым содержанием углерода. Изделия укладывают в железные ящики, засыпают смесью, состоящей из порошка металлического хрома или фер рохрома, каолина и хлористого аммония. Каолин вводят в смесь для предотвращения ее от спекания. Ящики после загрузки в них изделий и смеси закрывают двойными железными крышками, пространство между последними заполняют чугунной крошкой. Зазоры между крышками и ящиком замазывают огнеупорной глиной, смешанной с жидким стеклом. После этого ящики с из делиями устанавливают в печи и проводят хромизацию. Составы материалов, процессы хромизации и глубина диффузионных сло ев приведены в табл. 1 1 .
12 Н. А. Баринов и др,
|
|
|
|
Составы материалов |
|
|
Т а б л и ц а |
11 |
||
|
|
|
|
|
|
|
|
|
||
|
|
|
|
|
Режим хромизацин |
|
|
Глубина |
||
Металли |
Феррохром |
Хлористый Каолин |
|
|
Марка |
|||||
продолжи |
диффузи |
|||||||||
ческий |
% |
|
аммонии |
% |
темпера |
стали |
онного |
|||
хром, % |
|
|
% |
|
тура, °С |
тельность |
|
слоя, м м |
||
|
|
|
|
|
|
час. |
|
|
|
|
65 |
— |
|
5 |
30 |
1150 |
5 |
|
10 |
0,050 |
|
65 |
|
5 |
30 |
1150 |
5 |
|
45 |
0,018 |
||
65 |
— |
|
5 |
30 |
1150 |
5 |
|
У 10 |
0,018 |
|
— |
60 |
|
3 |
37 |
990 |
24 |
|
45 |
0,022 |
|
__ |
60 |
|
3 |
37 |
990 |
24 |
|
У10 |
0,020 |
|
65 |
— |
|
5 |
30 |
1100 |
24 |
|
У10 |
0,023 |
|
Г а з о в а я |
х р о м и з а ц и я |
осуществляется |
следующим |
об |
||||||
разом. В герметически |
закрывающуюся реторту |
загружают из |
делия, хромизирующий материал, порошкообразный металличе ский хром и феррохром; через реторту пропускают смесь газов хлороводорода и водорода. При температуре около 1000° С про исходит взаимодействие железа с образующимся хлоридом хрома. Вытесненный хром диффундирует в поверхностные слои изделия. Толщина образующегося диффузионного слоя находит ся в прямой зависимости от температуры газовой смеси, продол
жительности процесса и обратной |
зависимости |
от содержания |
|
углерода в стали. |
насыщения |
поверхности изде |
|
в. |
Сьлицирование — процесс |
лий кремнием при высоких температурах. Изделия из углероди стой стали и чугуна после силицирования приобретают свойст
ва, присущие свойствам железокремнистых сплавов. |
Повышает |
||
ся их сопротивление окислению при |
температурах |
до |
850° С, |
повышается коррозионная стойкость |
в среде азотной, |
соляной |
|
и других кислот. |
|
|
|
Силицированию подвергают изделия из углеродистой стали для кислотопроводов; насосов, перекачивающих кислоты; раз личной аппаратуры, применяемой в нефтяной, химической, бу
мажной и других |
отраслях |
промышленности, работающих |
в агрессивных средах. |
|
|
Силицирование подразделяется на твердое и газовое. |
||
Технологический |
процесс |
т в е р д о г о с и л и ц и р о в а н и я |
аналогичен процессу аллитирования в порошке. При твердом силицировании применяют порошкообразные смеси, состоящие из 50—95% ферросилиция (содержащего 75—90% Si), шамота или кварцевого песка. Шамот или песок вводят для того, чтобы не произошло спекания смеси. Иногда в смесь вводят от 2 до 50% поваренной соли или хлористого аммония, способствующих повышению скорости диффузии кремния в железе.
Толщина получаемого диффузионного слоя на изделиях за
висит ог температуры процесса, времени выдержки |
изделий |
|
в печи и от состава смеси. Например, |
при температуре |
1200° С |
и выдержке изделия в .печи в течение 1 0 |
час. © смеси, состоящей |
|
из 75% ферросилиция, 20% шамота и 5% поваренной соли, глу |
бина диффузионного слоя получается 0,88—0,90 мм. Технологи ческий процесс г а з о в о г о си л и ц и р о в а н и я во многом сходен с газовой хромизацией. Изделия закладывают в гермети чески закрывающуюся реторту, засыпают порошком карбида кремния, ферросилиция или смесью этих материалов, нагревают до 950—1000° С. В реторту подают хлор или хлороводород. Во время пропускания хлора и хлороводорода в реторте образуются
пары хлористого кремния SiCU, которые |
взаимодействуют |
с поверхностью силицируемого изделия. В |
результате этого |
взаимодействия протекает обменная реакция вытеснения крем ния из SiCU железом
|
4Fe + |
3SiCl4 -> 3Si + 4FeCl3. |
Выделившийся |
атомарный кремний диффундирует в сталь, |
|
а пары хлорного |
железа |
и непрореагировавший хлор направ |
ляются из реторты в вытяжную вентиляцию через водяной за твор. При этом процессе силицирования получают диффузион ный слой толщиной 0,51—1,38 мм.
г. Хромоалитиро©ание и хромосилицирование. Это процессы насыщения поверхностного слоя стали хромом и алюминием, или хромом и кремнием диффузионным путем. Процессы ведут при высоких температурах. Сталь, подвергнутая хромоалитиро ванию или хромосилицированию, становится более жаростойкой, чем сталь, подвергнутая хромизации или силицированию. Напри мер, хромосилицированная сталь жаростойка до температуры 1000° С. а хромоалитированная — до 1050° С. Сущность этих про цессов сходна с процессами хромизации и силицирования.
д. Шерардизация — процесс нанесения защитного слоя цинка на стальные детали путем совместного нагрева их с цинковой пылью при температуре, близкой к температуре плавления цинка.
Шерардизация применяется преимущественно для покрытия мелких скобяных изделий и деталей электрооборудования. По крытия достаточно стойки против воздействия наружной.атмо сферы, но менее стойки, чем цинковые электролитические по крытия.
Сущность технологического процесса шерардизации состоит в следующем: изделия с очищенной от загрязнений и окислов поверхностью совместно с цинковой пылью и окисью цинка в по рошке загружаются в барабан. На 100 кг загружаемых изделий вводится от 5 до 10 кг смеси, состоящей из 90% цинковой пыли
12*
и 10% окиси цинка. Окись цинка вводится для того, чтобы смесь не спекалась.
Барабан с изделиями и смесью нагревается в газовой или электрической печи до 440° С. При этой температуре процесс шерардизации длится в течение 2—4 час. После выдержки ба рабан охлаждают до комнатной температуры и его разгру жают.
Процесс шерардизации совершается по обычным для диффу зии законам, т. е. слой покрытия тем больше, чем выше темпера тура нагрева и продолжительнее процесс покрытия. При покрытии неответственных изделий (гаек, болтов) толщина 0,05—0,06 мм считается достаточной.
Горячие способы покрытия, подразделяются на цинкование, лужение и свинцевание. Для этого очищенные от загрязнения и окислов детали погружают в ванны с расплавленными метал лами и выдерживают их там. Во время погружения и выдержки детали ее поверхности смачивается покрываемым металлом и частично сплавляется с последней. В результате на поверхности деталей отлагается тонкий слой покрытия. Толщина покрытия зависит от продолжительности выдержки и температуры, при которой производится покрытие.
Горячим способом покрывают листовой металл, проволоку, трубы, различные стальные и чугунные детали. Недостатками горячего покрытия являются: трудность регулирования получе ния равномерной толщины слоя покрытия и невозможность от пуска при покрытии закаленных деталей.
а. Цинкование производят для покрытия листов железа, раз личных стальных и чугунных деталей. Для этого изделия, под готовленные для покрытия, погружают в ванну с расплавленным цинком. В ванне поддерживают температуру 450—480° С. Во время цинкования на поверхности деталей образуется железо цинковый сплав, внутренний слой которого, обогащенный желе зом (около 80%), представляет собой интерметаллическое со единение FeZn3, а внешний слой, обогащенный цинком до 20%, является соединением FeZn7. При выгружении изделий из ванны поверх слоя железоцинкового сплава образуется слой чистого цинка с образованием при кристаллизации «цинковых цветов»-
б. Лужение применяют для листового железа, пищеварных котлов, различной посуды и др. Для этой цели, например, отож женные железные листы подвергают травлению в слабом рас творе серной кислоты с целью удаления с поверхности листов пленок и окислов. Травление считается законченным, если по верхность листа приобрела равномерную светло-серую окраску. Перед погружением в ванну для лужения, листы обрабатывают полупроцентной соляной кислотой. Затем листы пропускают че рез слой расплавленного хлористого цинка для удаления влаги