
книги / Технология металлов
..pdf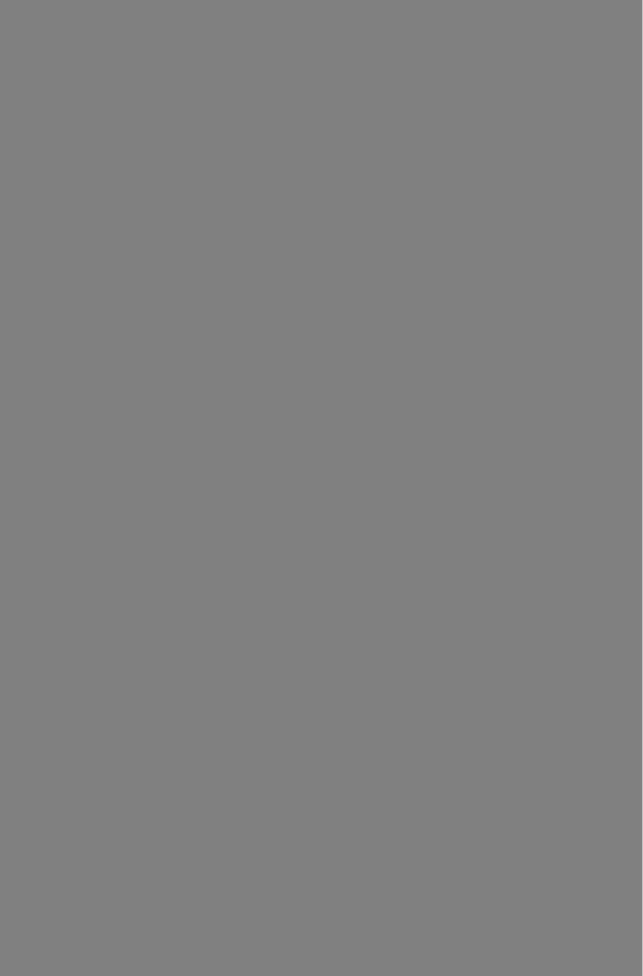
Сущность кислого процесса плавки состоит в окислении уг лерода, марганца и кремния в металле лод слоем шлака. Шлак при плавке содержит избыток кремнезема, последний вступает в соединение с закисью железа» образует 2FcO «SiO*. В связыва нии закиси железа принимают участие н кислые материалы фу теровки печи. Все это способствует более полному раскислению металла.
В настоящее время применяют два способа ведения плавки в кислых печах:
1.Активный способ с ограниченным восстановлением кремния;
2.Крсмневосстаковитсльный, или пассивный способ.
При активном способе незначительное количество кремния восстанавливается из шлака, поэтому в конце плавки сталь до полнительно раскисляют ферросплавами.
Кремнсвосстановнтельный процесс ведут без дополнительно го раскисления стали. В данном процессе раскисление стали осу ществляется полностью за счет восстановления кремния из шла* ка и футеровки пода и стен печи.
Сталь, получаемая в кислых мартеновских печах более высо кого качества, чем сталь, получаемая в основных печах, меньше содержит неметаллических включений и газов. Кислая мартенов ская сталь идет на изготовление коленчатых валов двигателей и роторов, шариковых и роликовых подшипников, артиллерийских орудий и других изделий особо ответственного назначения.
Применение кислорода при плавке стали а мартеновских печах
Применение кислорода при плавке стали в мартеновских пе чах позволяет интенсифицировать процесс окисления примесей в металле й повышать производительность печей. Кислород в мартеновских печах используют в основном четырьмя способами: а) обогащают кислородом воздух до 30% О?, подаваемого для интенсификации горения топлива; б) подают кислород в метал лическую ванну для окисления примесей в металле и лучшего перемешивания ванны; в) комбинируют кислород с другими имтарификаторами; г) предварительно продувают чугун кнелородом в миксере или в ковше для окисления примесей. При исполь зовании кислорода производительность в мартеновских печах, повышается на 10—20%, расход топлива снижается на 15—20%; процесс плавки протекает более равномерно.
Производство стали в электропечах
В мартеновских почах можно перерабатывать твердые отхо ды производства, получать точно, заданный химический состав стали, хорошо раскислять металл, получать одновременно боль-
шое количество однородного металла; применяя отдельные спо собы плавки, можно получать увеличенный выход металла до 105% восстановлением руды.
Наряду с положительными качествами пламенные печи име ют и недостатки, так как газы принимают участие в химических процессах, они окисляют, помимо обычных примесей, находя щиеся в металле легирующие элементы (ванадий, титан и др). и насыщают металл. Вследствие этого получение легированных сталей затруднено.
Производство стали в электропечах является более совершен ным способом, чем в мартеновских печах. При плавке стали в электропечах отсутствует окислительное пламя и имеется незна чительный доступ воздуха, в результате в печи создается вос становительная атмосфера. Металл меньше окисляется и насы щается окислами. Возможность получения более высоких темпе ратур в печах позволяет получать стали и специальные сплавы с большим содержанием тугоплавких легирующих элементов. В электрических печах плавки можно вести с перерывами. Это является важным при работе печей в литейных цехах. В настоя щее время в основном применяются два типа электропечей—ду говые и индукционные-
Устройство дуговых печей
Дуговые печи построены на использовании тепла электриче ской дуги, образующейся между графитовыми (или угольными) электродами и металлической ванной, развивающей тем пературу до 3500° С и выше. Печь (рис. 5) состоит из цилиндри ческого кожуха со сферическим днищем. Эти части изнутри футеруют теплоизоляционной и огнеупорной кладкой так, что образуется рабочее пространство печи. Свод печи делается отъемным, его выкладывают из динасового или хромомагнези тового кирпича в железном каркасе-кольце. В последнее время для увеличения срока службы на некоторых заводах применяют водоохлаждаемые своды в виде металлических конструкций с теплоизолирующей прослойкой из огнеупорных материалов.
Печь имеет загрузочное окно и выпускное отверстие для вы пуска металла. Загрузочное окно закрывается футерованной дверкой, которая поднимается и опускается специальным меха низмом. Печь установлена на два опорных сегмента на направ ляющих фундамента для поддержания и наклона при помощи механизма как в сторону -выпуска металла, так и в сторону за грузочного окна. В своде печи делают три отверстия для элек тродов. Электроды закрепляют в электрододержателях. Подъем и опускание электрододержателей с электродами в процессе плав ки осуществляется автоматической блокировкой. Питающий.
электрический так подают от понижающего трансформатора по гибкому кабелю и медным шинам к электродам.
Первичная обмотка трансформатора питается током высоко го напряжения 6000—30000 в, который преобразуется в ток низ кого напряжения нескольких ступеней от 90 до 280 в. Мощность
|
|
|
|
трансформатора в основном |
||||||||
|
|
|
|
определяется |
емкостью |
пе |
||||||
|
|
|
|
чи. |
При |
плавке |
твердой |
|||||
|
|
|
|
шихты |
в |
зависимости |
от |
|||||
|
|
|
|
марки |
получаемой |
стали, |
||||||
|
|
|
|
расход |
электрической |
энер |
||||||
|
|
|
|
гии |
колеблется |
в |
пределах |
|||||
|
|
|
|
от 600 до 950 кет • ч/т полу |
||||||||
|
|
|
|
чаемого |
металла. |
Диаметр |
||||||
|
|
|
|
электродов также зависит от |
||||||||
|
|
|
|
емкости |
печи. |
|
Графитовые |
|||||
|
|
|
|
электроды |
-по |
|
сравнению |
|||||
|
|
|
|
с |
угольными |
|
электродами |
|||||
|
|
|
|
обладают |
более |
высокой |
||||||
|
|
|
|
прочностью |
и |
|
меньшим |
со |
||||
|
|
|
|
противлением |
электрическо |
|||||||
|
|
|
|
му току. Дуговые |
печи |
для |
||||||
|
|
|
|
плавки |
стали |
|
применяются |
|||||
Рис. 5. Дуговая |
печь: |
различной |
емкости: |
от |
1,5 |
|||||||
/ — кожух |
печи; |
2 — днище |
печи; 3 — под |
до |
180 т. |
Печи |
емкостью |
|||||
печи; 4 |
— свод |
печи; 5 — электроды |
свыше |
10 |
т |
используют |
||||||
|
|
|
|
обычно на металлургических заводах, а печи меньшей емкости — в сталелитейных цехах для получения фасонных стальных от ливок.
Плавка стали в дуговых печах
При плавке стали в дуговых печах шихта состоит из стально го лома, чугуна, железной руды, флюсов, раскислителей и ферро сплавов для введения легирующих добавок.
Плавку ведут основным и кислым процессами. Для плавки стали основным процессом под и стены печи футеруют основными материалами, а для плавки кислым процессом — кислыми мате риалами.
Основной процесс плавки стали ведут с полным, частичным окислением или без окисления примесей.
Плавку с полным окислением примесей проводят в тех случа ях, когда необходимо переплавить шихтовые материалы с повы шенным содержанием фосфора, серы и получить сталь с мини мальным количеством этих элементов.
Для окисления примесей после расплавления шихты в печь добавляют руду. Окислы железа окисляют примеси в металле
(Si, Mn, Р и С), в результате образуется железистый шлак, содержащий (Fe0 )3 -P20 5 . Такой шлак способствует удалению фосфора из металла. Для образования более прочного соедине ния ангидрида фосфора в шлак добавляют свежеобожженную известь с целью получения фосфорно-кальциевой соли в шлаке по реакции
(FeO) 3 • Р2Об + 4СаО (Са04) Р20 5 + 3 FeO + 112 400 кал.
Эта реакция протекает успешно, так как металл не нагрет до высокой температуры. В этот период обычно ванна кипит в результате частичного окисления углерода. Полученный фосфо ристый шлак сливают.
При выплавке высокоуглеродистой стали и в тех случаях, когда содержание углерода в окислительный период понизилось в металле ниже заданных пределов, после удаления шлака, ван ну науглероживают. Для этого в печь* загружают электродный бой, кокс, а в отдельных случаях чушковый чугун с малым со держанием вредных примесей — фосфора и серы. Во время на углероживания металла загрузочное окно плотно закрывают во избежание поступления в пространство печи кислорода воздуха. Для усвоения углерода металлом дают выдержку 5—7 мин.,
после чего наводят |
новый шлак, загружая флюсующую смесь |
в количестве до 4% |
от веса металла. Флюсующая смесь состоит |
на 80% из свежеобожженной извести и на 2 0 % из плавикового шпата.
Во вновь образовавшемся шлаке в начальный период содер жание окислов (FeO и МпО) обычно колеблется от 5 до 8 %. Для уменьшения содержания этих окислов в шлак добавляют раскислительную смесь, состоящую из извести, молотого фер росилиция и кокса. Под действием этой смеси в шлаке уменьша ется содержание FeO до 1,0% и Мп до 0,4%. Шлак такого соста ва является активным десульфуратором металла. После раскис ления металла его доводят до заданного состава, вводят необ ходимые добавки, а при необходимости и легирующие элементы. Окончательное раскисление стали производят алюминием. Такой процесс называется плавкой под б е л ым шл а к о м .
Выплавку инструментальных сталей и подобных им в основ ном ведут под к а р б и д н ы м шл а к о м. На первой стадии восстановительного периода плавка ведется так же, как и под белым шлаком. Затем на поверхность шлака в печь загружает ся карбидообразующая смесь. Смесь состоит из извести, плави кового шпата и молотого кокса. В зоне электрических дуг в пе чи, т. е. в области высоких температур, происходит взаимодей ствие окиси кальция с углеродом кокса, образование карбида кальция и окиси углерода по реакции
СаО ЗС = СаС2 -\- СО.
5 Н. А. Баринов и др.
Карбид кальция увеличивает раскислительную и обессери вающую способность шлака. Для ускорения образования карби да кальция в шлаке все неплотности в печи герметически закры вают.
Процесс раскисления и десульфурации металла под карбид ным шлаком протекает по реакции
3 FeO + СаС2 = СаО + 3Fe + 2 СО; 3МпО + СаС2 = СаО + 3Мп + 2 СО;
СаС2 + 3 FeS + 2 СаО = 3 CaS + 3Fe + 2 СО; Саб + MnS + С = CaS -f- Мп + СО.
В результате протекающих реакций содержание FeO и МпО в шлаке понижается до Десятых долей процента, содержа ние серы в металле уменьшается др следов. Для полного рас кисления в конце плавки добавляют раскислители — ферроси лиций и алюминий. Для получения легированной стали вводят легирующие добавки, металл быстро нагревают до заданной тем пературы, выдерживают 10—15 мин., а затем выпускают в ковш для разливки.
Плавку с частичным окислением примесей ведут на чистых (по содержанию вредных примесей) исходных материалах. В состав шихты при плавке не вводят железную руду. Процесс окисления примесей в основном протекает в период расплавле ния шихты, в результате чего частично понижается содержание кремния, марганца, углерода и фосфора в металле. Образую щийся шлак сливают и дальше ведут плавку под белым или кар бидным шлаком.
В отдельных случаях ведут плавку без окисления примесей — методом переплава. Для этого загружают в печь шихту, состоя щую из отходов стали, близкой по составу к той марке, которую необходимо получить. При этом процессе плавки первичный (железистый) шлак из печи не удаляют, так как со шлаком уда ляются легирующие элементы— хром, титан, ванадий и др. Восстановительный период плавки методом переплава можно вести как под белым, так и под карбидным шлаком. Примене ние этого процесса для переплава отходов приводит к экономии дорогостоящих ферросплавов.
Кислый процесс плавки стали. Плавка в кислых дуговых пе чах нашла широкое распространение при производстве фасон ных стальных отливок. Плавка в кислых дуговых печах ведет ся под кислым шлаком, содержащим до 65% Si02. Так как сера и фосфор при кислых шлаках из металла почти не удаляются, металлическую шихту, состоящую в основном из стального ло ма, используют с низким содержанием серы (0,03% S) и фосфо ра (0,03% Р).
При расплавлении шихты на поверхности металла образует ся шлак, содержащий 38—46% Si, 22—28% FeO, 18—26%'MnO и 6 —7% СаО. Кипение ванны, во время которого из металла удаляются газы и неметаллические составляющие, так же важ но, как и при основном процессе плавки. Однако активное окис ление'углерода в металле затрудняется из-за того, что закись железа активно соединяется с кремнеземом, образуя 2 FeO • Si02. Для повышения интенсивности кипения повышают температуру в печи и добавляют в ванну железную руду в количестве от 2 до 4% от веса металла. В результате присадки руды содержа ние закиси железа в шлаке повышается до 35%. По мере выго рания углерода в металле содержание закиси железа в шлаке снижается до 15—17%. Шлак такого состава частично сливают и в печь вводят свежие шлакообразующие добавки — кварце вый песок, шамотный бой, известь. Для ускорения раскисления вновь наводимого шлака присаживают в печь 0 ,1 —0 ,2 % от веса плавки молотого ферросилиция и 0 ,1 —0 ,2 % от веса плавки мо лотого кокса или древесного угля. Получив нормальный шлак (он имеет светло-зеленый, светло-дымчатый или дымчатый цвет), содержащий 50—56% Si02, 9—1 2 % FeO, 2 ,0 —3,0% Fe20 3, 4,0—6 ,0 % А120 3, 18—20% МпО, до 5,0%’ СаО и 0,06—0,08% Р2 0 5, и отрегулировав содержание углерода, приступают к раскис лению стали. Раскисление стали производят силикомарганцем, ферросилицием и алюминием. Алюминий обычно вводят в ковш во время выпуска стали из печи.
Плавка стали в кислых дуговых печах по сравнению с плав кой в основных печах имеет следующие преимущества: более повышенная стойкость футеровки рабочего пространства печи, меньшие тепловые потери вследствие большой глубины ванны при равной емкости печей и более высокая производительность
всвязи с меньшей затратой времени на плавку.
Кнедостаткам этого процесса относят: потребность в ших товых материалах с малым содержанием фосфора и серы и воз никающие затруднения получения стали с узким пределом по содержанию кремния.
Применение кислорода при плавке стали JB электропечах
Г
В последние годы при плавке стали в электропечах приме няют кислород. Кислород вводят в печь для ускорения расплав ления шихты и вместо железной руды для окисления примесей в металле. При введении кислорода развиваются окислительные процессы в металле и в рабочем пространстве печи, поэтому сокращается время расплавления шихты и нагрева металла. Добавка руды в печь для окисления примесей приводит к по нижению температуры металла, а введение кислорода для этой
5*
цели повышает температуру его на 100—120° С. Повышение температуры особенно активизирует процесс окисления углеро да. Это является важным при выплавке нержавеющих марок сталей и подобных им с низким содержанием углерода, а также при плавке стали в больших электропечах, когда в состав ших ты вводят 60—80% чугуна.
В результате продолжительность плавки сокращается на 20—30%, расход электроэнергии уменьшается на 2 0 % и сталь получается по стоимости ниже стоимости мартеновской стали и более высокого качества. Кислород вводят в печь при помощи водоохлаждаемых труб.
Плавка стали в индукционных печах
Для плавки стали применяют печи без железного сердечни ка. Индукционная печь (рис. 6 ) состоит из индуктора, представ
|
|
|
|
ляющего |
собой |
первичную |
||||
|
|
|
|
обмотку |
трансформатора, и |
|||||
|
|
|
|
тигля, |
изготовленного |
из |
||||
|
|
|
|
огнеупорного |
материала, |
|||||
|
|
|
|
в |
котором |
производится |
||||
|
|
|
|
плавка стали. Индуктор |
из |
|||||
|
|
|
|
готовляется |
в виде катушки |
|||||
|
|
|
|
из медной трубки, по кото |
||||||
|
|
|
|
рому во время плавки цир |
||||||
|
|
|
|
кулирует вода. К индуктору |
||||||
|
|
|
|
при помощи |
гибкого кабеля |
|||||
|
|
|
|
или |
медных |
шин |
подается |
|||
|
|
|
|
электрический ток от мотор- |
||||||
|
|
|
|
генератора |
или |
лампового |
||||
|
|
|
|
генератора с частотой от 500 |
||||||
Рис. |
6. Индукционная печь: |
|
до 2500 пер/сек. На крупных |
|||||||
|
печах понижают частоту до |
|||||||||
/ — тигель; |
2 — теплоизолирующая |
про |
||||||||
слойка; 3 — индуктор; |
4 — каркас |
печи; |
50 |
пер/сек. Мощность |
гене |
|||||
|
5 — металл; |
6 — шлак |
|
раторов |
принимают |
от |
1 , 0 |
|||
|
|
|
|
до 0,3 квт/кг загружаемого металла в печь. Мощность и частоту тока определяют >в зависимости от емкости тигля и рода пере плавляемой шихты.
Тигли изготовляют как из кислых, так и основных огнеупор ных материалов в зависимости от назначения выплавляемой марки стали или сплава. В качестве кислого материала для из готовления тиглей применяют кварцитовый порошок и до 1,5% (вес.) порошка борной кислоты. Последний используют как связующую добавку. Для изготовления основных тиглей исполь зуют магнезитовый порошок и в виде связующей добавки—■ борную кислоту в количестве 3 % от веса порошка.
Тигель располагают внутри индуктора. Между тиглем и ин дуктором делают прокладку из теплоизолирующего материала. Индуктор и тигель размещают в каркасе, который устраивают из немагнитной стали. Каркас печи с^индуктором и тиглем мо жет наклоняться для выпуска стали из печи.
Во время плавки в индукционных печах нагрев металла про исходит за счет образования переменного магнитного поля во круг индуктора и вихревых токов в металле. Шлаки нагревают ся за счет тепла, содержащегося в металле. Средняя температура шлака ниже температуры металла. Поэтому активных обмен ных реакций между шлаком и металлом не протекает. Вследст вие этого вредные примеси (сера и фосфор) из металла не уда ляются. С учетом этого шихту используют с низким содержа нием вредных примесей и с таким расчетом, чтобы после рас
плавления |
получить |
заданный |
состав |
металла. |
Плавку ве |
дут быстро, |
в конце |
плавки в |
металл |
вводят |
раскислители, |
а при необходимости — легирующие добавки. Преимуществом процесса плавки в индукционных печах является то, что в них можно нагревать металл до очень высоких температур и без особых трудностей вести плавку под вакуумом. Соответственно, кроме обычных марок, можно выплавлять различные высоко легированные стали (нержавеющие, жаростойкие и др.), а так же сплавы специального назначения. Емкость современных пе чей колеблется в пределах от 50 кг до 10 т. Сталь в индукцион ных печах получают для отливки слитков и изготовления фа сонных отливок.
Разливка стали
Выплавленную сталь в тех или иных печах выпускают в ков ши и из последних разливают на слитки. Для этой цели при меняют в основном ковши со стопорными устройствами (рис. 7).
Стцлеразливочный ковш состоит из кожуха, изготовленного из листовой стали, внутренняя поверхность которого футерова на шамотным кирпичом. Для увеличения жесткости кожуха на него надеты кольца. Среднее кольцо имеет две цапфы для за хвата крюками разливочного крана. В дне ковша установлен специальный кирпич с отверстием, в который установлен раз ливочный стакан. Во время разливки стали отверстие разливоч ного стакана открывается или закрывается стопором при по мощи специального механизма.
Стопор состоит из железной штанги, на конец которой на винчивается шамотная пробка, а выше надеты шамотные труб ки для предохранения от расплавления жидкой сталью. После выпуска стали в ковш ее выдерживают в течение нескольких минут. Во время выдержки происходит более полное выравни-
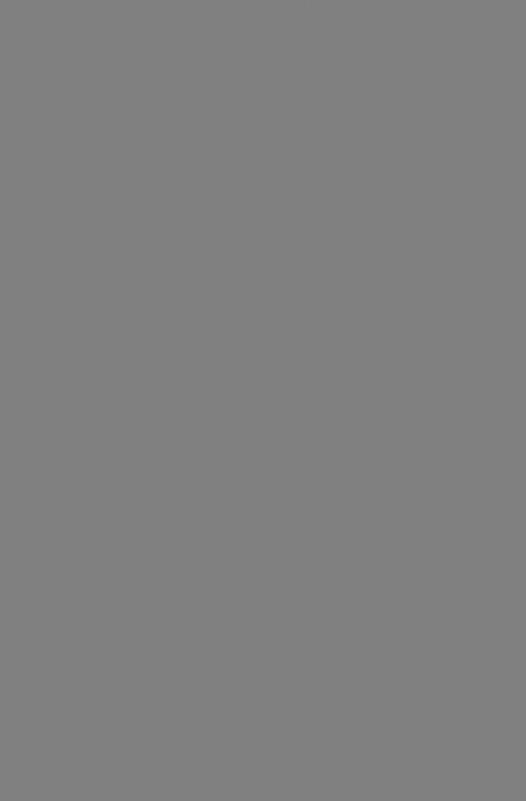