
книги / Производство сварных конструкций (Изготовление в заводских условиях)
..pdf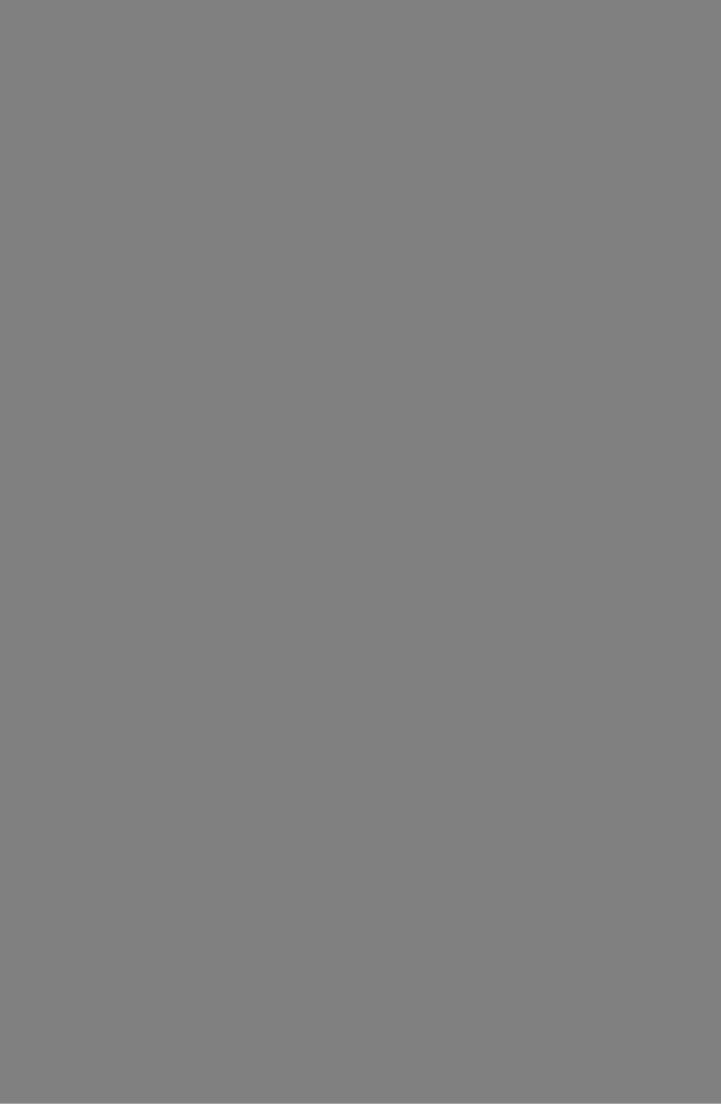
материала, что и свариваемые элементы с толщиной, не превы шающей толщину стенки свариваемого сосуда.
Наличие подкладных колец облегчает сборку стыка и цен тровку соединяемых элементов, обеспечивает гарантированное проплавление кромок и отсутствие непроваров в корне шва даже в тех случаях, когда возможно значительное колебание парамет ров режима сварки.
Однако во многих случаях применение такой технологии ог раничено по следующим причинам:
1.В районе сварного соединения с подкладным элементом появляется более высокая концентрация напряжений при на гружении сосуда, что обуславливает снижение его работоспо собности.
2.Зазор между подкладкой и стенкой сосуда способствует скоплению влаги или хранящегося продукта, что может привес ти к снижению коррозионной стойкости соединения из-за разви тия щелевого эффекта в полости между внутренней поверхно стью стенки сосуда и подкладным кольцом.
3.Увеличивается металлоемкость конструкции, что в неко торых случаях является немаловажным фактором.
Втех случаях, когда по условиям эксплуатации применение остающихся подкладок не допускается, сварку замыкающего шва приходится выполнять на весу, без подкладного кольца. Сборку выполняют на прихватках с использованием наружных (обычно цепных) центраторов. При разработке технологии свар ки необходимо уделять особое внимание обеспечению стабиль ности параметров режима в процессе выполнения шва, т.к. в противном случае возможно появление непроваров или прожо гов. Негативное влияние могут оказать колебания напряжения в электрической сети цеха, изменение длины дугового промежут ка, нестабильная скорость подачи электродной проволоки и др.
Сварку кольцевых стыков тонкостенных сосудов обычно вы полняют в среде защитных газов. Для вращения изделия исполь зуют роликовые вращатели, но для сосудов малого диаметра (~ до 500мм) целесообразно применять цапфовые вращатели, по зволяющие закреплять сосуд по его продольной оси, что повы шает стабильность поддержания заданной величины дугового промежутка.
212
При сварке сосудов из титановых сплавов необходимо уде лить внимание защите от окружающей атмосферы не только ме талла шва, но и основного металла, нагреваемого до температур выше 400 °С. С этой целью на сварочную головку устанавлива ют камеру (козырёк) дополнительно защищающую зону сварки, а с внутренней стороны сосуда устанавливают камеры для под дува защитного газа.
После сварки производят контроль герметичности сосуда. Для этих целей используется несколько способов. Если к плот ности швов предъявляются высокие требования, то применяют методы течеискания с использованием гелиевых или галоидных течеискателей. В обычных случаях применяют пневматические методы. В сосуде создают небольшое избыточное давление и помещают его в ванну с водой. Места нарушения герметичности определяют по выделяющимся пузырькам воздуха. Данный ме тод применяется только для оценки герметичности сосуда. Для оценки прочности применяют гидравлические испытания, на гружая сосуд до давления, превышающее номинальную величи ны на 25%. Нагружение сосуда для этих целей газом (воздухом) недопустимо.
7.3. Изготовление сосудов из металла средней толщины
Диаметр и длина сосудов из металла средней толщины тако вы, что в большинстве случаев стандартные размеры листового проката не позволяют изготовить цилиндрическую часть из од ного листа. В связи с этим для их изготовления используют одну из двух технологий.
Первая - изгиб листовой заготовки относительно поперечной (короткой) оси листа, сварка продольного шва коротких обечаек и затем изготовление цилиндрической части сосуда пугем сварки кольцевыми швами нескольких коротких обечаек между собой.
Вторая - изготовление плоского полотнища требуемых раз меров путем сварки между собой листовых заготовок, затем гиб ка полотнища для получения цилиндрической обечайки и сварка продольного шва.
Вторая схема облегчает сборку и сварку стыков, так как все они располагаются в одной плоскости, но возникают определен ные сложности кантовки крупногабаритного полотнища для сварки швов с противоположной стороны. Кроме того, для по-
213
лучения цилиндрической обечайки требуются специализирован ные вальцы с длинной валков, превышающей длину сосуда, как правило, длиной более 10 м. Такую схему изготовления можно реализовать только в условиях специализированного крупносе рийного производства. В настоящее время единственным пред приятием, на котором действует поточная линия с такой схемой изготовления сосудов, является завод тяжелого машиностроения в г. Мареуполь (Украина), выпускающий железнодорожные цис терны объемом 60м3 и 120м3.
Первая схема является универсальной, использует типовое, широко распространенное оборудование для гибки металла, сборки и сварки сосудов и поэтому находит более широкое при менение.
Рассмотрим эту технологию более подробно. Цилиндрические сосуды собирают из нескольких обечаек и
двух полусферических или эллиптических днищ. К точности изготовления деталей предъявляют достаточно жесткие требо вания. Так, например, их относительная овальность в любом по перечном сечении не должна превышать 1%, угловатость кро мок в районе продольных сварных швах не должен превышать f = 0,1s + 3 мм, но не более 5 мм по отношению к проектному профилю, смещение кромок не должно превышать b = 0,1s, но не более 3 мм, для кольцевых стыков - не более 5мм.
Подготовку кромок под сварку выполняют механической об работкой, допускается эту операцию выполнять путем термиче ской резки или строжки (кислородной, воздушно-дуговой, плаз менно-дуговой) с последующей механической обработкой (рез цом, фрезой, абразивным инструментом). Требуемая глубина ме ханической обработки после термической резки (строжки) зависит от восприимчивости конкретной марки стали к термическому цик лу резки (строжки) и указывается в нормативной документации.
Кромки деталей, подлежащие сварке, и прилегающие к ним участки должны быть очищены от окалины, краски, масла и других загрязнений.
Обечайки вальцуют из одиночного листа, а при большом диаметре из двух листовых заготовок, сваренных поперечными швами. Нормативные документы не допускают более двух про дольных швов на каждой обечайке. Современные гибочные вальцы с микропроцессорным управлением позволяют осущест-
214
влять гибку с точно заданной кривизной заготовки по всему пе риметру без предварительной подгибки кромок, что позволяет обеспечить требуемую точность. Однако многие предприятия до сих пор имеют в своем распоряжении трехвалковые вальцы ста рого образца. Для предотвращения угловатости кромок в данном случае рекомендуется следующий технологический прием (рис. 7.10). На начальном и заключительном этапах гибки лист изги бают на большую, чем требуется величину так, чтобы в районе стыка обе кромки располагались в одной плоскости. Это позво ляет при сварке обеспечить плотное прилегание свариваемых кромок к подкладке, что повышает качество сварки, но искажает форму обечайки в месте расположения сварного шва. Для полу чения правильной цилиндрической формы после сварки произ водят калибровку обечайки на тех же вальцах.
Рис. 7.10. Последовательность операций гибки и сварки обечаек при использовании трехвалковых вальцов
Сосуды со стенками средней толщины из низкоуглеродистых и низколегированных сталей изготавливают преимущественно с помощью автоматической сварки под флюсом. Продольный стык обечайки собирают на прихватках с помощью простейших стяжных приспособлений и устанавливают на роликовый стенд. Для формирования корня шва применяют флюсовую подушку. При диаметре сосуда более 600... 1000 мм появляется возмож ность выполнять сварку изнутри сосуда. В этом случае рекомен дуется применять двухстороннюю разделку кромок, позволяю щую уменьшить требуемый объем наплавленного металла. Ис ходя из удобства установи обечайки на флюсовой подушке, пер вым выполняют шов изнутри. Обечайку, установленную на ро ликовом стенде (рис. 7.11), поворачивают свариваемыми кром-
215
нами вниз и под обечайку подводят флюсовую подушку, пред ставляющую собой желоб из гибкого материала и устройства поджатия флюса в виде пневмошлангового прижима. При пода че сжатого воздуха в пневмошланг он изменяет форму сечения и поджимает желоб с флюсом к стыку. Следует обратить внима ние, что недостаточное усилие поджатия флюса приводит к ухудшению формирования шва. Для сварки изнутри используют сварочный трактор, перемещающийся по временным направ ляющим. Начинают и заканчивают сварку шва на выводных планках, имеющих толщину и форму разделки кромок такую же, как обечайка.
Рис. 7.11. Флюсовая подушка для сварки продольных швов обе чайки. 1 - обечайка; 2 - роликовая опора; 3 - корпус флюсовой подушки; 4 - привод вертикального перемещения корпуса по душки; 5 - желоб с флюсом; 6 - пневмошланговый прижим; 7 - сварочный автомат.
После сварки изнутри обечайку кантуют на 180° и сваривают шов с наружной стороны. Для сварки используют подвесной сварочный автомат, закрепленный на тележке портального или глагольного типа. Реже используют автомат, перемещающийся вдоль консоли сварочной колоны или с помощью консоли. Для сварки шва с наружной стороны флюсовая подушка не требуется.
Сборка и сварка кольцевых стыков между обечайками, а также обечайками и днищами является более трудоемкой операцией.
Продольные швы смежных обечаек и швы днищ сосудов ре комендуется смещать относительно друг друга на величину
2 1 6
трехкратной толщины наиболее толстого элемента, но не менее чем на 100 мм между осями швов.
Для механизации сборки кольцевых стыков роликовый стенд можно оборудовать сборочной скобой на тележке (рис. 7.12).
Тележка передвигается вдоль стенда по рельсовому пути. На стройка скобы в вертикальной плоскости осуществляется тягой. При сборке стыка, обечайки устанавливают на роликовый стенд, затем продвигают скобу 1 вдоль обечаек так, чтобы опора 12 первого гидроцилиндра 11 располагалась под первой обечайкой, а вторая 13 - в плоскости собираемого стыка. Включением ци линдра 11 закрепляют первую обечайку. После того, как торце вой цилиндр 2, придвигая вторую обечайку к первой, установит требуемый зазор в стыке, включением гидроцилиндра 10 вырав нивают кромки, закрепляют стыкуемые обечайки и закрепляют стык прихватками.
А~А
Рис. 7.12. Скоба для сборки кольцевых стыков обечаек:1 - сбо рочная скоба; 2, 10, 11 - пневмоцилиндры; 3 - кронштейн; 4 - опора; 5 - тележка; б - роликовая опора; 7 -рельсовый путь;8, 9 - элементы пневмопривода; 12, 13 - регулируемыеупоры.
Затем выключают гидроцилиндры, отводят прижимы, обе чайки поворачивают на требуемый угол и в такой лее последова тельности включают гидроцилиндры, собирают стык для закре пления обечаек на следующем участке. Прихватки должны иметь высоту не более 2/3 толщины стенки сосуда, длиной 5... 10 толщин с шагом 50... 100 толщин, но не более 500 мм.
2 1 7
Перед началом сварки должно быть проверено качество сборки соединяемых элементов, а также состояние стыкуемых кромок и прилегающих к ним поверхностей. При сборке не допускается под гонка кромок ударным способом или местным нагревом.
Сварку кольцевых стыков сосудов со средней толщиной стенки выполняется, как правило, с двух сторон. Выполнение первого слоя на весу, требует тщательной сборки и ограничения размера зазора по всей длине шва. Поэтому роликовые стенды обычно оборудуют флюсовыми подушками (рис. 7.13), позволяющими производить сварку первого слоя шва без жесткого ограничения зазора в стыке.
Рис. 7.13. Флюсоременная подушка для сварки кольцевых швов.
Поджатие флюса при сварке кольцевых швов может осуще ствляться с помощью подушки ременного типа. Движение рем ня и подача флюса к месту горения дуги происходит вследствие сил трения. Флюс из бункера насыпается на верхнюю ветвь ремня, натянутого между двумя свободно вращающимися отно сительно своих осей роликов, и плотно контактирует с поверх ностью обечаек в нижней части стыка. При вращении обечаек, ремень перемещается за счет сил трения, а флюс поступает под обечайку, прижимаясь к стыку.
Первый слой выполняют изнутри обечайки, а второй - свари вают с наружной. При толщине стенки сосуда более 12 мм свар-
2 1 8
ку под слоем флюса обычно выполняют за несколько проходов. Если ось обечайки, по каким либо причинам имеет наклон, то при вращении она может самопроизвольно перемещаться в осе вом направлении, вследствие чего в процессе сварки стык будет смещается от первоначально установленного положения элек трода. При большом количестве оборотов смещение стыка от проектного положения может привести к появлению дефектов в шве типа непроваров и несплавления кромок. Для предотвраще ния осевого перемещения (тренда) роликовый стенд преднаме ренно устанавливают с наклоном к горизонтальной плоскости, а торец обечайки упирают в вертикально расположенный ролико вый упор, препятствующий осевому смещению обечайки.
При сварке кольцевого стыка возникает проблема токоподвода к обечайке. Не рекомендуется подвод тока осуществлять через один из опорных роликов, т.к. стабильность подвода тока по такой схеме низкая, следствием чего может быть низкое ка чество сварки. Более правильно токоподводящий кабель при креплять к корпусу обечайки струбциной. Для предотвращения наворачивания кабеля на обечайку струбцина и кабель должны иметь вращающийся контакт типа ось - втулка.
Днища изготовляют путем гибки под прессом из одного лис та, чаще из круглой заготовки, сваренной из нескольких листов. При этом расположение швов должно соответствовать рекомен дациям рис. 7.1. Допускается собирать и сваривать днища из от дельных штампованных лепестков.
При организации производства сосудов следует иметь в виду, что диаметры днищ стандартизованы. Часто предприятия, изго тавливающие сосуды, получают готовые днища.
После штамповки торцы днища обрезают под требуемую по технологии форму кромок, после чего подают на сборку с ци линдрической частью. Сборку осуществляют по предварительно приваренным фиксирующим планкам, равномерно расположен ным по контуру в торцевой части к корпусу сосуда (рис. 7.14). Вертикальное расположение корпуса сосуда облегчает сборку. После закрепления днища и цилиндрической части прихваточными швами планки удаляют и производят сварку сначала внут реннего шва, а затем - наружного. Технология сварки практиче ски не отличается от сварки кольцевых стыков обечаек.
2 1 9
4
Рис. 7.14. Сборка днища с корпусом сосуда. 1 - корпус сосуда; 2 - направляющие планки;3 - днище; 4 - петли для транспорти ровки днища
При выполнении сварки в замкнутом пространстве необхо димо во внутреннюю полость сосуда подавать сжатый воздух. Сварочные работы в замкнутом пространстве должны выпол нять не мене двух рабочих: один сварщик находится внутри со суда и выполняет сварку, другой рабочий находится с наружной стороны и осуществляет наблюдение за ходом выполнения ра бот с целью обеспечения безопасных условий работы.
Если выполнить процесс сварки с двух сторон невозможно, то сварку по согласованию с проектной организацией допускается выполнять только с наружной стороны на остающейся подкладке.
После сварки все элементы, используемые для временного крепления, должны быть удалены, а места их присоединения зачищены абразивным инструментов. Приварка временных кре плений и удаление их после сварки основного изделия должны производиться по технологии, исключающей образование тре щин и закалочных зон в металле изделия.
7,4. Изготовление толстостенных сосудов
Крупногабаритные сосуды котельных и других установок при толщине стенок до 90-ь120 мм изготавливают обычно из вальцованных или штампованных из листа обечаек, сваренных между собой продольными и поперечными (кольцевыми) шва ми. Для котельных сосудов, типа барабанов, характерно боль шое количество штуцеров, необходимых по условию обеспече ния процессов циркуляции воды и сепарации пара.
220