
книги / Производство сварных конструкций (Изготовление в заводских условиях)
..pdf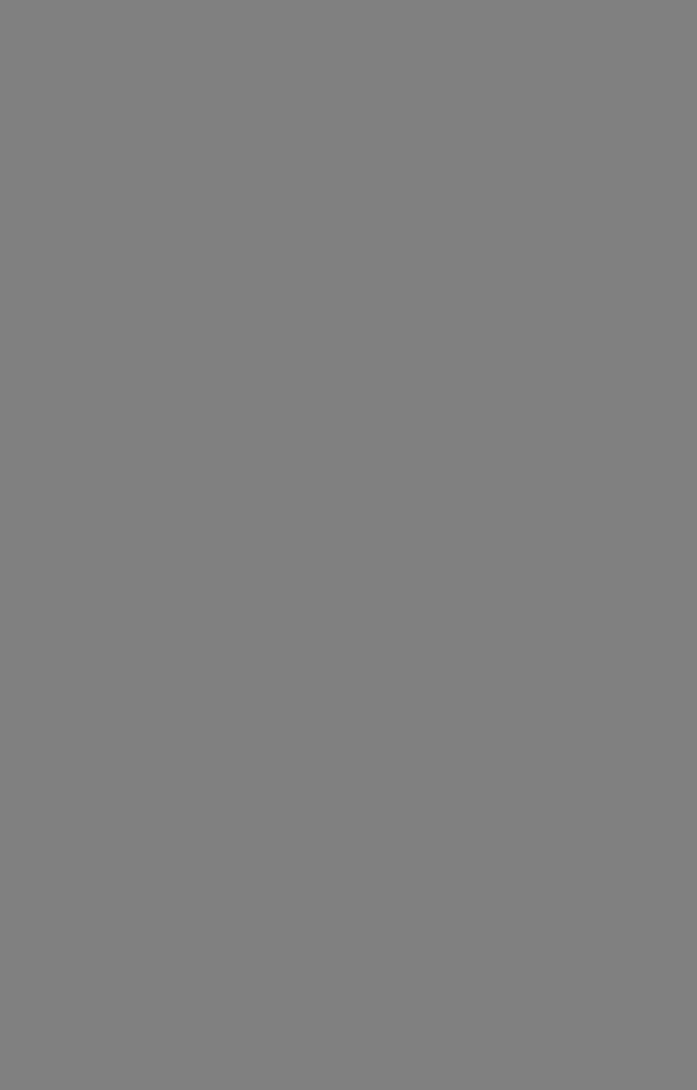
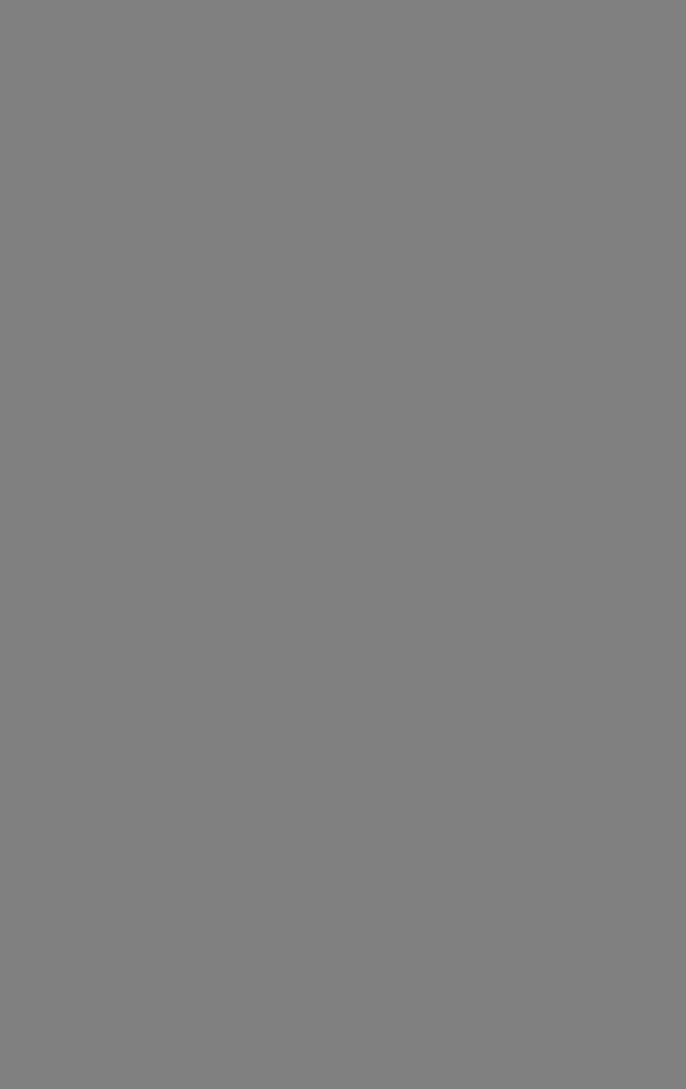
Прижимы по типу силового источника подразделяются на ручиьк и механизированные (с механическим приводом).
Ручные прижимы применяются во вспомогательных, фиксирую щих и зажимных механизмах. К ним относятся: клиновые, винтовьь рычажные эксцентриковые или байонетные.
Ручные прижимы должны быть спроектированы самотормо...
щими. К их достоинствам относится относительная простота, но они требуют непосредственного воздействия сборщика, и, как правило, не обеспечивают высокую производительность. Их применяют в мелкосерийном производстве.
В качестве привода механизированных прижимов применяют пневматические цилиндры, пневмашланги, пневматические камеры, гидравлические цилиндры, электромагниты, постоянные магниты, электромеханические и вакуумные устройства.
Использование прижимов с механизированным приводом значи тельно сокращает время, затрачиваемое на сборку, особенно, ес.и требуется закрепить изделие одновременно в нескольких мест;-х. Широкое применение получили пневматические прижимы, приво димые в действие сжатым воздухом (в среднем 4 ати.). Однако при таком давлении размеры цилиндров, требуемые для обеспечения за данного усилия закрепления, могут оказаться значительными.
Для их уменьшения прибегают к дополнительному использова нию рычажной или клиновой системызакрепления.
Гидравлический силовой привод, развивая значительные усилия зажима, позволяет регулировать эти усилия в широком диапазоне с помощью предохранительных или редукционных клапанов.
Гидроцилиндры далее при значительных усилиях имеют сравни тельно небольшие габаритные размеры, что позволяет создавать компактную конструкцию приспособления. Однако для каждого приспособления требуется специальная установка с гидроаппарату рой, обеспечивающей подачу рабочей жидкости в гидроцилиндры. Кроме того, качество изготовления и монтажа гидравлической сис темы должны исключать попадание масла на свариваемые детали, чтобы исключить появлениедефектов.
Недостатком всех механизированных прижимов является то, что они не обеспечивают условия самоторможения. При нарушении пи тания может произойти самопроизвольное раскрепление изделия.
В связи с этим для обеспечения безопасности работы, особенно в случае, когда в процессе сборочно-сварочных работ изделие требует-
103
ся вращать или кантовать, используют механизированные прижимы совместно с немеханизированными (клиновые, эксцентриковые и др.), которые должны быть спроектированы как самотормозящие, чтобы при нарушении электрического или пневматического питания удерживали детали в закрепленном состоянии.
Методика конструирования приспособлений
Проектирование приспособления для сборочно-сварочных опера ций тесно связано с разработкой технологического процесса изготов ления данного изделия. Конструктор приспособления в качестве ис ходных данных получает техническое задание от технолога, который определяет в общих чертах схему приспособления.
В задачи технолога входит: выбор места установки технологиче ских баз и прижимов; установление маршрута изготовления изделия; выбор средств механизации транспортных операций; уточнение со держания технологических операций с разработкой эскизов изготов ления и указанием размеров промежуточных сборочных единиц, дающих представление об установке и закреплении заготовки; уста новление оптимальных режимов сварки; определение штучного вре мени изготовления изделия; выбор типа и моделей вспомогательного
исварочного оборудования;
Взадачу конструктора приспособления входят: уточнение и кон кретизация принятой технологом схемы приспособления, выбор кон струкции и размеров установочных элементов приспособления, оп ределение величины усилия для закрепления деталей и уточнение схемы и размеров зажимного устройства, определение размеров на правляющих деталей приспособления, общая компоновка приспо собления с установлением допусков на изготовление деталей и сбор ку приспособления.
Вкачестве исходных данных конструктор приспособления должен располагать: чертежами деталей, входящих в сборочную единицу, чертежом готового изделия и техническими требова ниями его приёмки; технологическим процессом сборки и свар ки изделия, из которого следует: последовательность и содер жание операций; принятая схема базирования; используемое вспомогательное, сборочное и сварочное оборудование, опти мальные режимы сварки, а также запроектированная производи тельность с учётом времени на установку, закрепление и снятие изготовляемого изделия. Кроме того, конструктор должен рас полагать ГОСТами и нормалями на узлы сборочно-сварочных
104
приспособлений, а также иметь базу данных, содержащую типо вые и унифицированные узды и детали приспособлений.
Конструктором учитываются технологические возможности изго товления приспособления в местных производственных условиях и программа выпуска изделия для выбора наиболее рентабельной его конструкции, особенности выбранного процесса сварки итребования к отдеже готового приспособления иего частей.
На чертежах деталей и сборочных единицах приспособления должны быть указаны их размеры, допуски, шероховатость поверх ностей, а также марка, таёрдость, термическая обработка материала и особые технические требования.
Из технологического процесса конструктор получает сведения о сварочном и вспомогательном оборудовании, на котором наме чается вести сборку и сварку. Ему необходимо знать основные размеры этого оборудования, связанные с установкой приспособ ления. Целесообразно ознакомиться с конструкцией используемо го оборудования и технологическими особенностями выбранного процесса сварки непосредственно в цехе, что позволит наиболее полно выяснить особенности проектируемого приспособления, найти выгоднейшее расположение, как всего оборудования, так и органов его управления. Весьма полезно изучить опыт эксплуата ции аналогичных приспособлений и учесть замечания руководя щего и обслуживающего персонала.
Тщательная проработка исходных данных может привести конст руктора к более рациональной схеме приспособления, изменение схемы базирования следует согласовать стехнологом.
В соответствии с выбранной схемой и требованиями задания на проектирование производится конструктивная разработка приспо собления. Она включает необходимые расчёты на прочность и жёст кость и завершается созданием рабочих чертежей.
Если в процессе сборки изделие подвергается кантовке, то рас чёт механизма вращения следует производить для наиболее не благоприятного (создающего наибольший вращающий момент) положения изделия. Для уменьшения вращающего момента целе сообразно предусматривать возможность регулируемой баланси ровки приспособления.
Для сварочного приспособления необходим учётдополнительных усилий, которые могут возникнуть в результате усадки изделия от сварки. При этом существенными являются требования, предъявляе-
105
мые к приспособлению в части снижения сварочных деформаций в изделии. Если не ставить цель уменьшить деформации, то следует либо предусмотреть возможность смещения изделия, либо допустить упругую деформацию приспособления совместно с изделием. В по следнем случае допускаемая деформация не должна превосходить требования расчёта на жёсткость и прочность.
Приспособление, имеющее целью снизить сварочные деформации изделия, должно обладать повышенной жёсткостью. При этом надо иметь в виду следующее: усилие от усадки оказываются настолько большими, что предотвратить продольное или поперечное сокраще ние зоны сварного соединения за счёт жёсткости закрепления в при способлении обычно не удаётся. Поворот сечений может быть огра ничен в более значительной степени и поэтому основное внимание следует обращать на предотвращение изгиба свариваемого изделия.
Сучётом вышесказанного можно выделить три характерных случая.
1.Снижение остаточных сварочных деформаций достигается пу тём предварительного изгиба или растяжения свариваемых элемен тов при закреплении их в приспособлении. Расчёт приспособления на прочность и жёсткость должен учитывать наличие дополнительных усилий, необходимых для деформирования закрепляемого изделия.
2.Жёсткое закрепление в приспособлении позволяет уменьшить временные деформации во время сварки. В этом случае расчёты на жёсткость и прочность должны выполняться с учётом моментов от усадочных усилий.
При разработке приспособлений выбор размещения базовых эле ментов и расположение прижимов должен учитывать направление деформации изделия от сварки с тем, чтобы после выполнения сбо рочной или сварочной операций извлечение изделия из приспособле ния не вызывало затруднений.
Точность изготовления приспособления определяется требова ниями к точности сборки изделия. Целесообразно при проектирова нии расстояния между базовыми поверхностями назначать с учётом ожидаемой деформации изделия от сварки.
Последовательность конструирования приспособления
Конструирование приспособления целесообразно начинать с уточнения конструкции изделия и схемы базирования, предложенной технологом. Зная принятую в технологическом процессе базировку деталей, точность и шероховатость базовых поверхностей, конструк-
106
тор определяет тип и размер установочных элементов, их количество и взаимное положение. Решение этого вопроса должно быть увязано с требуемой точностью свариваемой конструкции.
Зная из технологического процесса места приложения сил для за крепления отдельных деталей и величиныусадочных сил, вызванных процессом сварки, конструктор определяет величину сил закрепле ния. Исходя из регламентированного времени на закрепление и от крепление заготовки, типа приспособления (одно - или многомест ные), формы и точности деталей, а также величины силы закрепле ния, выбирают тип зажимного устройства и определяют его основ ные размеры. Выявляют вспомогательные устройства, (медные под кладки, флюсовые подушки) устанавливают их конструкцию и раз меры. При их выборе следует в максимальной степени использовать имеющиеся нормали и стандарты.
Разработку общего вида приспособления обычно начинают с на несения на лист контуров свариваемого изделия. Обычно изделие показывают условными линиями (тонкими, штрихпункгирными или вычерчивают цветным карандашом) для того, чтобы оно выделялось на чертеже приспособления.
Разработку общего вида ведут методом последовательного нане сения отдельных элементов приспособления вокруг контуров заго товки. Сначала вычерчивают установочные детали, затем зажимные устройства, вспомогательные устройства для поворота изделия идля перемещения сварочных головок. Вслед за этим определяют контуры корпуса приспособления, который объединяет в единое целое пере численные выше элементы.
На общем виде приспособлений указывают габаритные разме ры и размеры, которые необходимо выдержать при сборке и от ладке приспособления, даётся нумерация деталей и спецификация с указанием использованных нормалей и стандартов. Общий вид может содержать технические требования, которые должны быть выполнены при сборке приспособления. Далее выполняют дета лировку, причём рабочие чертежи разрабатывают обычно только на специальные детали.
3.5. Операции по уменьшению деформаций и напряжений, возникающих при сварке
Причины, по которым необходимо уделять внимание этому вопросу при проектировании сварочного производства, обу-
107
словлены тем, что практически все способы сварки сопровож даются неравномерным нагревом изделия, в результате чего температурные деформации могут вызывать изменение проект ного положения деталей при сварке, размеры и форму готовой конструкции.
Различают временные и остаточные напряжения и деформа ции.
Временные: способствуют образованию горячих трещин, из меняют пространственное расположение свариваемых кромок (вызывают смещение и угловатость кромок), что осложняет ав томатизацию и роботизацию сварки, ухудшает отвод тепла от кромок, изменяет зазор в стыке.
Остаточные деформации: ухудшают товарный вид конст рукции; затрудняют последующую сборку сварных узлов; за трудняют балансировку сварной конструкции; снижают точ ность изготовления и увеличивают объем механической обра ботки после сварки.
Остаточные напряжения: увеличивают накопленную в конструкции потенциальную энергию, что усиливает негатив ные последствия разрушения; снижают сопротивление коррози онному растрескиванию; способствуют развитию хрупкого раз рушения и образованию холодных трещин.
Таким образом, напряжения и деформации, возникающие при сварке, не только увеличивают трудоемкость изготовления, но и мо гут существенно повлиять на ее эксплуатационные характеристики.
Несмотря на то, что при проектировании сварной конструкции должны быть приняты необходимые меры для снижения сварочных напряжений и деформаций, нередко эти меры оказывается недоста точно эффективными. Поэтому при разработке технологии изготов ления сварных конструкций вопросам уменьшения и устранения на пряжений и деформаций, возникающих при сварке, необходимо уде лять повышенное внимание, а в случае необходимости предусматри вать дополнительные технологические операции для исправления деформаций и снятия остаточных напряжений.
Основываясь на теории образования сварочных напряжений и деформаций, которая была рассмотрена при изучении дисцип лины «Проектирование сварочных конструкций», можно выде лить следующие группы методов уменьшения остаточных на пряжений, деформаций и перемещений: регулирование теплово-
108
го воздействия на конструкцию; сборка конструкции с учетом предполагаемых деформаций и перемещений деталей при свар ке (метод компенсации); рациональная последовательность вы полнения сварных швов.
Рассмотрим примеры практического использования этих ме тодов.
Регулирование теплового воздействия на конструкцию
В процессе сварки тепло, введенное в сварнре соединение, расходуется на расплавление металла и образование соедине ния; на нагрев участков, расположенных рядом со швом и на нагрев технологической оснастки. Из перечисленных только первая составляющая является необходимой для получения со единения. Нагрев участков, расположенных рядом со швом яв ляется неизбежным. Именно доля тепла, введенная в этот уча сток, определяет величину остаточных деформаций. Тепло, от веденное в технологическую оснастку, уменьшает долю тепла, пошедшего на нагрев околошовной зоны и в этом отношении может рассматриваться как средство уменьшения деформации конструкции при сварке.
Таким , образом, для уменьшения сварочных деформаций не обходимо стремиться к тому, чтобы уменьшить долю тепла, по шедшего на нагрев околошовной зоны.
Это может быть достигнуто использованием высококонцен трированных источников энергии для сварки, позволяющее пе рераспределить поступающую энергию в пользу расплавления металла и образования сварного соединения. В порядке умень шения этой доли различные способы сварки плавлением можно расположить в следующем порядке: газовая сварка; дуговая сварка; сварка электронным лучом; лазерная.
Второй путь - увеличение оттока тепла в технологическую оснастку (рис.3.33), что приводит к уменьшению ширины зоны пластических деформаций. С этой целью сварку рекомендуется вести на подкладках из высокотеплопроводных (например, ме ди) материалов. Для увеличения интенсивности отвода тепла рекомендуется подкладки дополнительно охлаждать водой. Для достижения большего эффекта производят охлаждение, не толь ко подкладки, но и прижимов. Этим приемом борьбы с дефор мациями следует пользоваться с осторожностью, т.к. при этом возрастает скорость охлаждения и увеличивается вероятность
109
появления холодных трещин. Кроме того, если сварка произво дится во влажной атмосфере (например, вблизи побережья), то возможно появление пористости (особенно при сварке алюми ниевых сплавов) из-за конденсации влаги на металле впереди дуги. В качестве средства борьбы с пористостью молено реко мендовать охлаждение оснастки водой, температура которой соответствует температуре окружающей среды.
Рис. 3.33. Уменьшение сварочных деформаций за счет отвода тепла в технологическую оснастку
С целью уменьшения остаточных сварочных деформации, обусловленных продольным укорочением шва и околошовной зоны, молено рекомендовать вместо однопроходной сварки вы полнять сварку швов за несколько проходов, уменьшив тем са мым величину погонной энергии. При этом следует иметь в ви ду, что деформации сварных соединений, обусловленные попе речным сокращением при многослойной сварке больше, чем при сварке шва с таким же поперечным сечением за один проход.
Угловые деформации сварных соединений связаны с нерав номерным нагревом по толщине. Для их уменьшения применя ют сварку с сопутствующим нагревом шва с противоположной стороны дополнительным источником тепла (рис. 3.34).
К методам регулирования тепловложения можно отнести "метод теплового домкрата" (рис. 3.35).
При ремонте трещины на замкнутых конструкциях типа шкивов, зубчатых колес, маховиков из-за реакции окружающих участков де тали в сварном шве могут появиться остаточные напряжения в попе речном к шву направлению и вызвать появление трещин. Для уменьшения остаточных напряжений рекомендуется перед сваркой нагреть участки детали, окружающие ремонтируемый участок (рис.
110