
книги / Производство сварных конструкций (Изготовление в заводских условиях)
..pdfсят от выбранного способа сварки, толщины металла, конструк ции стыка, его пространственного положения при сварке и воз можностей точного направления электрода по стыку. В общем случае при выборе формы профиля кромки следует руково дствоваться соответствующими стандартами или отраслевыми нормативными документами. При этом необходимо стремиться к уменьшению объема наплавленного металла и, вместе с тем не создавать условия для образования дефектов. При ручной дуго вой сварке толстого металла наиболее часто применяется одно сторонняя V - образная или двухсторонняя X - образная раздел ка кромок (рис. 3.13). Угол ф выбирают так, чтобы сварщик имел возможность манипулировать электродом и обеспечивать проплавление кромок. Величину притупления кромок "с" выби рают так, чтобы обеспечивать проплавление корня шва. При та кой разделке объем наплавленного металла увеличивается про порционально квадрату толщины кромок. Применение двухсто ронней разделки кромок резко сокращает объем наплавленного металла и при правильной последовательности наложения швов уменьшает сварочные деформации, но такая разделка кромок требует кантовки свариваемых деталей, что повышает трудоем кость изготовления и требует доступа к шву с двух сторон. В качестве альтернативы рекомендуют применять несимметрич ную разделку кромок.
Рис. 3.13. Форма разделки кромок, применяемая для ручной дуго вой сварки
Широкое пространство для манипуляции электродом требу ется только в нижней части разделки. В более высоких слоях ширина V - образной разделки становится избыточной, поэтому для больших толщин ГОСТ предусматривает применение фи гурных разделок кромок (рис.3.14). Для получения такой раз-
81
делки требуется обработка резанием на кромкострогальных, ка русельных или токарных станках, что ведет к увеличению стои мости обработки, но существенно повышает качество подготов ки кромок и, следовательно, способствует обеспечению качества сварки.
Рис. 3.14. Фигурная разделка кромок.
При использовании современных методов автоматической сварки и современного сварочного оборудования целесообразно применять узкие и щелевые разделки с углом раскрытия кромок 3° - 15°. Сварка соединений с щелевой разделкой приводит к снижению трудоемкости и дает существенную экономию на плавленного металла, но предъявляет весьма высокие требова ния к стабильности и качеству работы сварочного оборудова ния. Как правило, требуется применять специальные следящие системы для направления электрода по стыку.
Подготовку кромок производят тепловой (кислородной или плазменной) или механической резкой. В первом случае подго товку кромок стремятся совместить с разделительной резкой заготовки. С этой целью резку выполняют двумя (для получения V - образной разделки) или тремя (для получения X - образной разделки) резаками, перемещающимися друг за другом (рис. 3.15).
Для механической резки используется как универсальное оборудование (карусельные, токарные, фрезерные станки), так и специализированное (кромкострогальные станки). При обработ ке кромок цилиндрических деталей на универсальном оборудо вании иногда возникают проблемы в обеспечении точности об работки кромок, связанные с тем, что допуски на овальность деталей во много раз могут превышать допуск на обработку
82
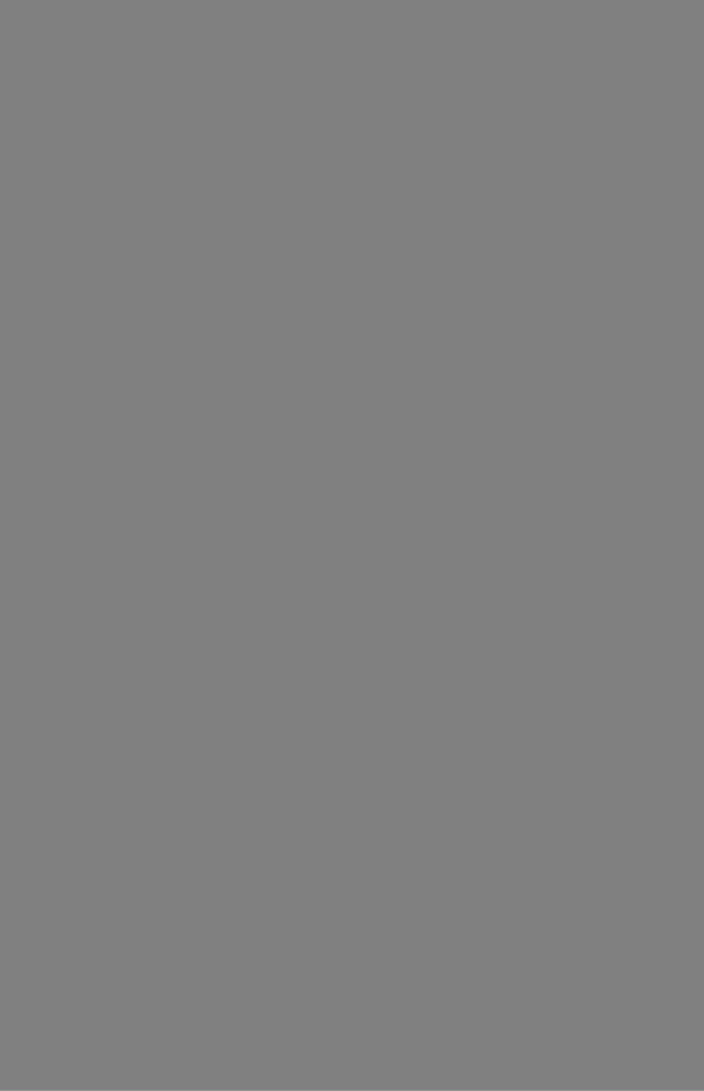
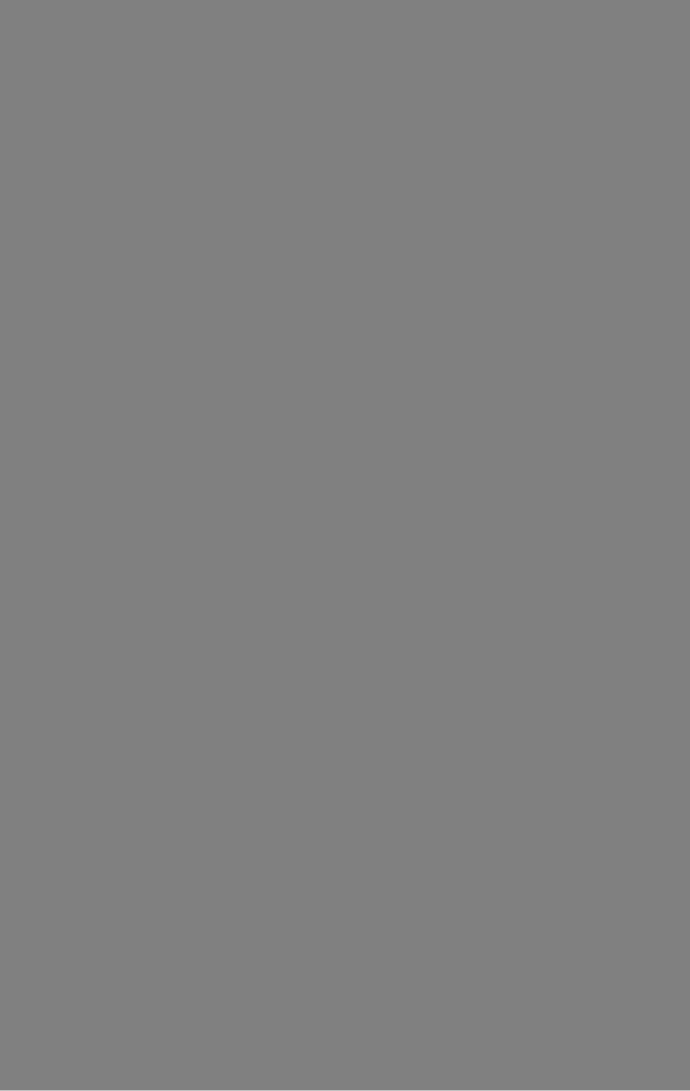
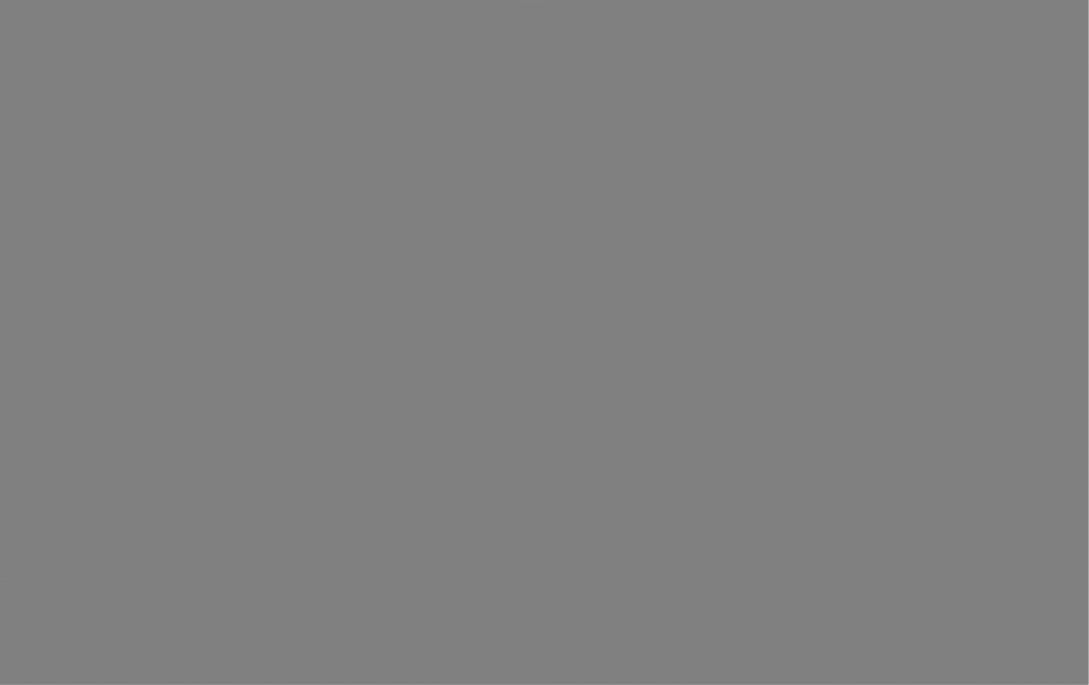
В наклонных рольгангах, для ограничения скорости переме щения, ролики располагают в наклонной плоскости под углом 1- 2°. Так как перемещение изделий осуществляется за счет сил тяжести, устанавливать привод в наклонных рольгангах нет не обходимости.
Рельсовые конвейеры представляют собой специальные те лежки, перемещающиеся по рельсовому пути, как правило, от индивидуального привода. Используется преимущественно в качестве внутри- и межцехового транспорта для перемещения крупногабаритных и тяжеловесных изделий.
Подвесные конвейеры конструктивно представляют собой монорельс, по которому перемещаются тележки с подвешенным к ним грузом. Монорельс монтируют в виде замкнутого контура по значительной производственной территории. Тележки связа ны между собой цепью, которая перемещается от нескольких приводов.
Подвесные конвейеры классифицируют как грузонесущие; грузотянущие; грузотолкающие.
Вгрузонесущих конвейерах груз подвешивается на конвейер
иснимается без остановки конвейера.
Вгрузотянущих конвейерах груз перемещается на специаль ной тележке по рабочей площади производственного участка. Перемещение тележки обеспечивается посредством присоеди нения ее специальным тросом к тележке монорельса. Для оста новки перемещения необходимо отсоединить трос от привода монорельса. Такая схема позволяет прерывать перемещение гру за без остановки привода конвейера и накапливать его непо средственно на транспортирующей тележке. При такой схеме используется не только объемное пространство цеха, но и рабо чие площади.
Грузотолкающие конвейеры представляют собой два парал лельно установленных в вертикальной плоскости цехового про странства монорельса. По нижнему монорельсовому пути пере мещается грузонесущая тележка, а по верхнему - грузотолкаю щая тележка. Такое устройство расширяет возможность транс портера, например, использовать его как накопитель, не занимая при этом дефицитные производственные площади.
Подвесные конвейеры являются перспективным и наиболее широко используемым транспортом при производстве сварных
86
конструкций, так как позволяют рационально использовать объ
емы производственны х помещений, освобождая дефицитные
рабочие площ ади, и перемещать изделия, как в горизонтальной, так и в вертикальной плоскости.
Н епреры вное ритмическое перемещение изделий в автомати ческих линиях осуществляется с помощью шаговых конвейеров.
И х применяю т в тех |
случаях, когда требуется точное позицио |
нирование деталей |
относительно сварочного автомата, и бы |
строе перем ещ ение |
их с одной позиции на другую. Примером |
ш агового конвейера |
может служить система тележек с гидро |
подъем никам и, установленных на рельсовом пути с определен ным ш агом и связанных между собой приводным тросом. На каж дом рабочем месте с помощью гидроподъемника изделия подним аю т вверх, все тележки перемещаются на один шаг. По сле этого гидроподъемник опускает груз на очередное рабочее
место для выполнения соответствующей операции.
Преры вистое перемещ ение осуществляют:
•универсальными средствами (электрокарами, автопогруз чиками, тележками, кранами и электрическими тельферами);
•специальными пульсирующими конвейерами, шаговыми транспортерами, рольгангами, склизами, толкателями.
3 . 3 В с п о м о г а т е л ь н о е о б о р у д о в а н и е д л я в з а и м н о г о
о р и е н т и р о в а н и я и п е р е м е щ е н и я с в а р и в а е м о г о и з д е л и я и
св а р о ч н о г о у с т р о й с т в а
Качество сварного соединения и производительность сварки зависят от положения шва в пространстве и его доступности для сварочного инструмента. При использовании сварки плавлением предпочтение необходим о отдавать нижнему положению или полож ению "в лодочку". В связи с этим в процессе изготовления конструкции возникает необходимость выполнять кантовку или поворот изделия.
Для механизации этих операций используют: поворотные столы; роликовые стенды; кантователи; вращатели; позиционе ры; манипуляторы; сварочные колоны и тележки.
По в о р о т н ы е с т о л ы предназначены для вращения изделий с
марш евой скоростью вокруг одной оси и установки их в удоб
н ую позицию для сборки, сварки или отделке. Поверхность по-
87
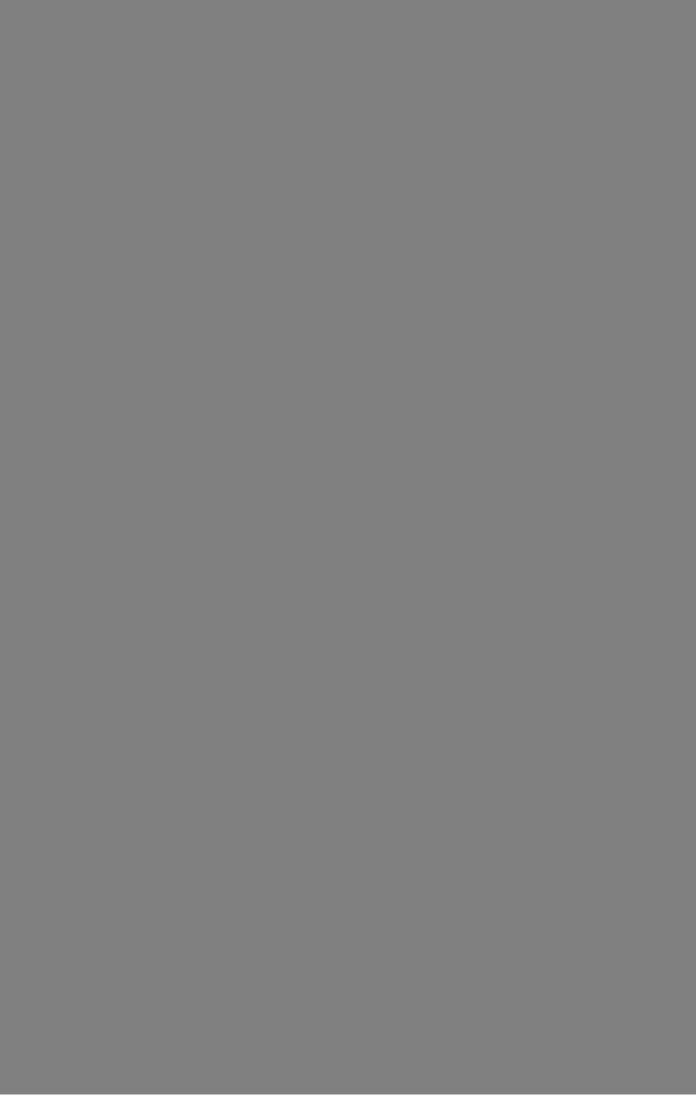
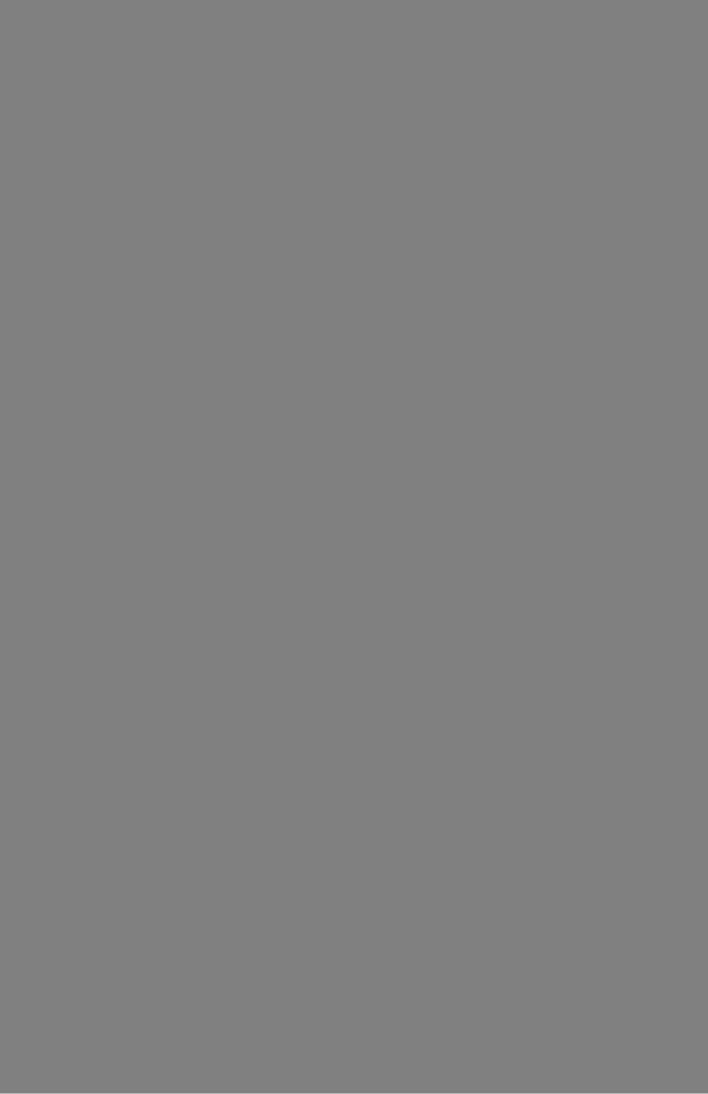
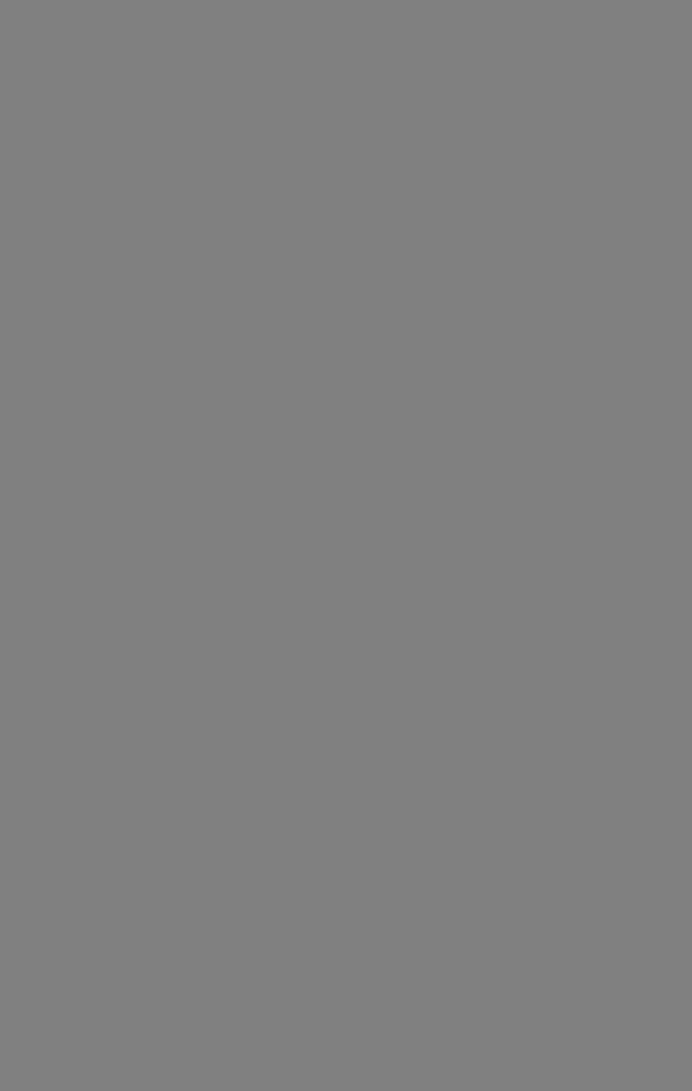