
книги / Производство сварных конструкций (Изготовление в заводских условиях)
..pdfРазмер
Назначение
Характеристика припуска припуска,
припуска
мм
профильный прокат: |
|
уголок, швеллер, трубы, балки с высотой |
|
стенки, мм: |
|
400 и менее |
1,0 |
более 400 |
1,5 |
Продольные угловые швы, на каждый |
1 м |
1,0
шва
•ограничения толщины разрезаемых элементов до 40 мм;
•громоздкость и сложность оборудования, высокая стои мость режущего инструмента;
•при механической резке происходит исчерпание пла стичности в поверхностных слоях зоны реза и, возможно, появ ление трещин на кромках. В тех случаях, когда после резки пре дусмотрена операция гибки в направлении поперечном относи тельно поверхности кромки, необходимо предварительно уда лить строжкой нагартованные слои на кромках.
•детали сложной конфигурации с небольшими радиусами закругления механическими способами вырезать можно только
сиспользованием методов штамповки.
Термические способы резки лишены большинства недостат ков, характерных для механических способов. Их преимущест вами являются:
•возможность резки малоуглеродистых сталей практиче ски любой толщины;
•возможность вырезки деталей любой конфигурации;
•относительная простота и компактность оборудования;
•возможность автоматизации.
К недостаткам термических способов резки следует отметить следующее:
•относительно низкая производительность; .
•не все материалы одинаково хорошо поддаются резке;
•после резки образуются остаточные напряжения;
•сравнительно низкое качество поверхности реза.
В заготовительном производстве объемы применения терми ческих и механических способов резки примерно одинаковы: на
61
долю механических способов приходится 40-^45 %.
В производстве сварных конструкций применяют следующие виды ножниц (рис. 3.5): гильотинные листовые с наклонным ножом (рис. 3.5а), двухдисковые с наклонными ножами (рис. 3.5г). однодисковые с наклонным ножом, многодисковые (рис. 3.5д), ножницы для резки уголка (рис. 3.5 е), швеллеров и дву тавров (рис. 3.5ж), пресс-ножницы (рис. 3.56, в) комбинирован ные сортовые с ручным и механизированным приводом.
Гильотинные и дисковые ножницы применяются для резки листового проката. Первые обеспечивают более высокую произ водительность, вторые позволяют осуществлять непрерывную резку заготовок неограниченной длины, что особенно важно при использовании полосового и рулонного проката.
Рис. 3.5. Схемы резки на ножницах различных типов: а) гильо тинные ножницы: б, в) комбинированные сортовые г) двухдис ковые с наклонными ножами; д) ножницы многодисковые; е)
ножницы для резки уголка швеллеров и двутавров; ж) прессножницы комбинированные сортовые 1 - нижний ноле; 2 - раз резаемый материал; 3 - прижим; 4 - верхний ноле; 5 -упор.
62
Ножницы многодисковые предназначены для продольной обрезки боковых кромок и роспуска рулонного материала на полосы. Они применяются в крупносерийном и массовом произ водстве.
Для резки швеллеров и двутавров используют ножницы, у кото рых нож совершает три движения (рис. 3.5ж): прокалывает стенку и за счет колебательного движения поочередно разрезает полки.
На комбинированных пресс-ножницах можно резать полосу, круг, квадрат, уголок, тавр, швеллер и двутавр. Пресс-ножницы позволяют осуществлять операции пробивки отверстий в листо вых и фасонных заготовках.
Для резки тонколистового металла представляют интерес пресс-ножницы (просечные станки) с числовым программным управлением движения двухкоординатного стола относительно матрицы и пуансона.
Конструкция ножниц предусматривает возможность быстрой смены пары матрица и пуансон, установленных на револьвер ную головку, что позволяет быстро изменять профиль контура реза. Совместная работа координатного стола и револьверной головки позволяют за счет шагового перемещения листа между пуансоном и матрицей осуществлять непрерывную резку (кон турную вырубку) металла по сложному контуру, что .придает просечным станкам большую универсальность и дает им неос поримое преимущество в мелкосерийном производстве.
Процесс механической резки на ножницах основан на упру гопластическом деформировании и скалывании металла под давлением ножа, в результате чего на кромке металла возможно исчерпание запаса пластичности и образование трещин. Именно по этой причине механическую резку на гильотинных и сорто вых ножницах, а также на штампах не следует выполнять при изготовлении деталей:
•из сталей с нормативным пределом текучести более 350 МПа;
•толщиной более 25 мм из сталей с нормативным пределом текучести более 275 МПа;
•толщиной более 16 мм из сталей с нормативным пределом текучести 285-350 МПа.
Механическую резку листового проката на гильотинных ножницах и штампах запрещается производить при изготовле нии деталей из любых марок стали:
63
• конструкций I и II групп1 в соответствии с классифика цией СНиП Н-23-81*, работающих на растяжение, продольные кромки которых после сборки и сварки остаются свободными, в том числе стыковых накладок;
• фасонок стропильных и подстропильных ферм, пролет ных строений транспортерных галерей, а также фасонок прочих конструкций группы I в соответствии с классификацией СНиП И-23-81 *.
Кромки деталей после механической резки не должны иметь трещин, расслоений, заусенцев и завалов более 1 мм.
Применение механической резки допускается без ограниче ний, если после резки производится механическая обработка кромок на величину не менее 0,2 толщины листового проката.
Отрезные станки применяют для резки труб, фасонного сор тового материала. На отрезных станках можно резать материал большего сечения, чем на ножницах, а качество резки более вы сокое. Однако трудоемкость резки на отрезных станках значи тельно выше, чем при резке на ножницах. Поэтому отрезные станки применяют для резки профилей, которые невозможно резать на ножницах. Например, для резки труб больших сече ний, профилей под углом или в случаях, когда необходимо обес печить высокую точность резки. В производстве деталей свар ных конструкций применяются отрезные станки с дисковыми пилами, трубоотрезные станки, а также станки с абразивными отрезными кругами.
Термическая резка применяется для листового металла сред них и больших толщин и труб большого диаметра. С помощью термической резки может производиться как прямолинейная,
1 СНиП Н-23-81* предполагает деление строительных стальных конструкций на четыре группы в зависимости от ответственности и условий работы:
Группа I. Сварные конструкции либо их элементы, работающие в особо тя желых условиях или подвергающиеся непосредственному воздействию ди намических, вибрационных или подвижных нагрузок
Группа II. Сварные конструкции либо их элементы, работающие при стати ческой нагрузке (растянутые, растяну го-изгибаемые и изгибаемые элементы)
Группа III. Сварные конструкции либо их элементы, работающие при стати ческой нагрузке (сжатые и сжато-изгибаемые элементы)
Группа IV. Вспомогательные конструкции зданий и сооружений
64
так и фигурная резка металла толщиной до 300 мм и более. Основными видами термической резки являются: кислород
ная (газовая) и плазменно-дуговая (плазменная).
Кислородная резка применяется для малоуглеродистых и низколегированных сталей толщиной от 5 до 300 мм.
Плазменно-дуговая резка применяется для:
•малоуглеродистых и низколегированных сталей толщи ной 2^28мм;
•коррозионностойких сталей толщиной до 60-80мм;
•алюминиевых сплавов;
•меди и ее сплавов.
Термическая резка может производиться вручную и на ма шинах. Машинная резка позволяет вырезать детали с высокой точностью, исключая трудоемкие операции разметки, обеспечи вая высокую производительность, и поэтому является одним из наиболее прогрессивных технологических процессов. Универ сальные машины для термической, кислородной и плазменно дуговой резки могут иметь следующие конструктивные схемы исполнения: портальные, портально-консольные и шарнирные.
После термической резки кромки деталей должны быть очи щены от грата.
Кромки листовых деталей конструкций, остающиеся после сборки и сварки свободными и работающие на растяжение, должны иметь шероховатость поверхности не более 0,3 мм. До пускается наличие отдельных мест на кромках деталей, не отве чающих указанным требованиям, а также выхватов, не выводя щие размер детали за пределы допусков, исправленных плавной зачисткой абразивным кругом или заваркой по специальной технологии с последующей зачисткой мест исправления абра зивным кругом, перемещаемым вдоль кромки.
В последние годы интенсивное развитие получила лазерная резка. По сравнению с традиционными методами в области раскроя листо вого проката (штамповкой, газопламенной и плазменной резкой), лазерная резка обладает рядом неоспоримых преимуществ:
•высокая скорость;
•идеальная поверхность реза;
•отсутствие необходимости дополнительной обработки;
•высокая производительность процесса;
65
•экономия материала благодаря малой ширине реза;
•незначительная зона термического воздействия;
•изготовление изделий любой сложности в единичных экзем плярах благодаря использованию цифровых систем управления;
•высокая повторяемость сложных изделий в любых коли чествах;
•отсутствие деформации материала;
•используя возможности лазерной резки, можно раскроить по сложному кошуру практически любой листовой материал;
•отсутствует механическое воздействие на обрабатываемый материал.
В основе лазерной обработки лежит тот факт, что лазерный луч можно сконцентрировать на поверхности материала в пятно диамет ром в десятые дож миллиметра. Если при этом лазер обладает доста точной мощностью, то происходит расплавление, испарение мате риала. Обычно в станках для резки перемещается лазерный резак над неподвижным материалом с помощью координатного стола с число вым программным управлением.
В основном для обработки материалов используются два класса лазеров: твердотельные и газовые. Наиболее распространенные твер дотельные лазеры на неодимовом стекле и итгрий-алюминиевом гра нате с длиной волны около 1 микрона и газовые углекислотные лазе ры с длиной волны около 10 микрон.
В промышленности наиболее распространенным технологиче ским процессом лазерной обработки является резка стальных листов
толщиной до 20 мм (алюминиевых до 10 мм) по сложному контуру. Ее применяют для вырезки таких деталей, как прокладки, кронштей ны, панеж, приборные щитки, двери, декоративные решетки, диско вые пилы. Весьма эффективным оказалось применение лазерной рез ки фигурных изделий на стадии освоения новой продукции, так как из-за высокой гибкости лазерного оборудования значительно сокра щаются сроки освоения новых изделий.
В связи с расширением номенклатуры конструкционных ма териалов, в частности, увеличением объема применения неме таллических материалов и металлов со специальными свойства ми, появились способы резки, использующие абразивные мате риалы в виде сформованных абразивных инструментов или по рошков. Наибольшее распространение получили абразивные
66
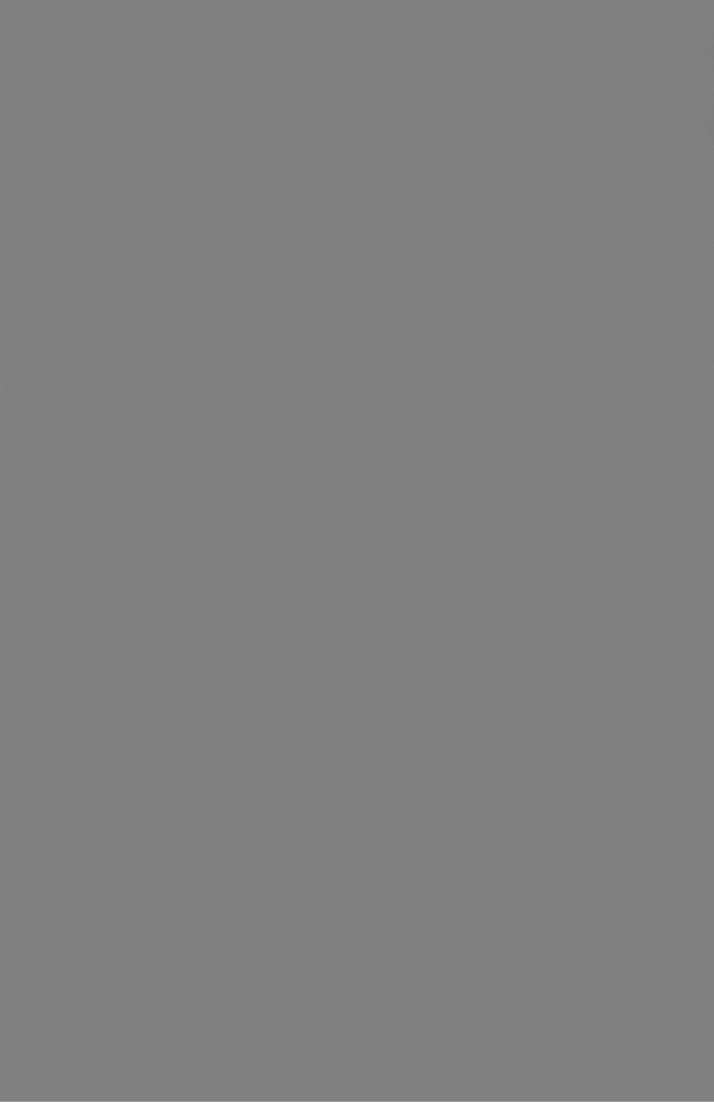
облегчает удаление из зоны реза расплавленного металла и ту гоплавких фракций, что значительно расширяет возможности кислородной резки в отношении качества резки таких конструк ционных материалов, как, например, аустенитные стали, медные
иалюминиевые сплавы и др.
Вконце прошлого века появилась новая технология резки с использованием абразивного порошка - гидроабразивная резка.
Впроцессе резки водяной струей с абразивом вода выполняет функцию носителя. Резка осуществляется за счет съема мате риала, вызываемого ударением твердых частиц. Схема процесса гидроабразивной резки (ГРА) показана на рис. 3.6.
Сфокусированная водяная струя с абразивом прорезает в заго товке узкую щель. Во время резки водяная струя с абразивом с постоянной скоростью резки проводится по заготовке. Процесс разрезания происходит в результате эрозионного воздействия на материал высокоскоростного потока твёрдых частиц. Скорость процесса эрозии зависит от кинетической энергии частиц, механи ческих свойств разрезаемого материала, угла атаки, формы частиц.
Вкомплекс для водоструйной резки входят: насос высокого давления; режущая головка; координатный стол и приводы пе ремещений режущей головки, управляемые системой числового программируемого управления; система разводки высокого дав ления и подачи абразива.
Давление воды составляет 200...400МПа (2000-4000 ати),
диаметр сопла - 1,0... 1,5 мм, размер абразивных частиц - 0,2...0,25 мм.
Данный способ позволяет разрезать детали толщиной до 150 мм, при максимально возможной толщине 300 мм.
Благодаря высокой точности и качеству поверхности резки, детали, как правило, не требуют дополнительной обработки.
Наиболее перспективным является применение гидроабра зивной резки для получения деталей из аустенитных сталей, ти тановых и алюминиевых сплавов, для которых применение тра диционных методов резки вызывает определенные технологиче ские трудности.
Применение микропроцессорных систем управления движе нием инструмента и высокая точность резки позволяют полу чать детали со сложным контуром. Примеры деталей, вырезан ных данным способом, показаны на рис 3.7.
68
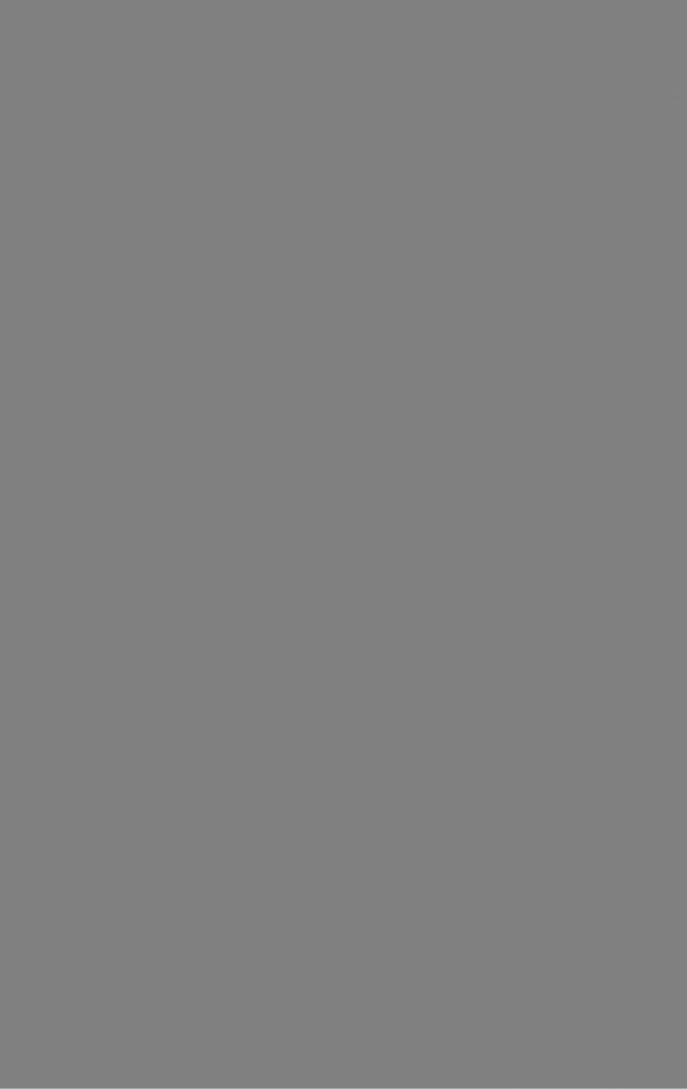
исключают деформацию заготовки, оплавление и пригорание материала в прилегающей зоне.
Таблица 3.3.
Скорость гидроабразивной резки различных материалов в мм/мин
М атериал |
|
|
Толщина, мм |
|
|
|
||
5 |
10 |
15 |
20 |
25 |
50 |
100 |
||
|
||||||||
нерж. сталь |
1200 |
500 |
250 |
220 |
150 |
70 |
25 |
|
титан |
1300 |
600 |
350 |
300 |
200 |
100 |
30 |
|
алюминий |
2800 |
1200 |
600 |
700 |
500 |
200 |
70 |
|
гранит |
4000 |
1800 |
1200 |
800 |
500 |
300 |
100 |
|
стеклопластик |
4500 |
2200 |
1200 |
800 |
400 |
300 |
100 |
|
углепластик |
5500 |
2200 |
1200 |
750 |
350 |
250 |
80 |
|
мрамор |
6000 |
2700 |
1200 |
1300 |
700 |
450 |
150 |
|
стекло |
6500 |
3000 |
2000 |
1400 |
700 |
500 |
160 |
•Позволяет обрабатывать сложный профиль с любым ра диусом закругления более 0,1-3,0 мм.
•Молено получать поверхность деталей с шероховатостью Ra 0,5-1,5 мкм.
•Экономичность процесса. Скорость резания - высокая. Малая ширина реза (1...3 мм) позволяет экономить дефицитные материалы при их раскрое. Среднее потребление воды в абразив- но-жидкостном режущем устройстве невелико - около 3-4 л/мин.
•Доступность. Использование таких относительно недо рогих компонентов, как вода и кварцевый песок в качестве абра зива, делает процесс доступным.
•Универсальность установки, позволяющая резать на од ной установке самые разнообразные материалы;
•Возмоясность резки заготовок, состоящих из различных материалов (например: резина + железо + пластик).
Для оптимизации выбора способа резки необходимо четко представлять, что является приоритетной целью выбора: прин ципиальная возможность резки данного материала; скорость резки; точность резки; исключение механического или теплово го воздействия на деталь в процессе резки; наибольшая универ сальность установки; минимальный уровень вредных воздейст-
70