
книги / Производство сварных конструкций (Изготовление в заводских условиях)
..pdfфабрикатов на вагонетках по поперечному пути на складское место 1 участка. Отличительная особенность организации про изводства на ОАО «Уралмаш» состоит в том, что в заготови тельном производстве предприятия создан цех комплектации и на участок подают только полный комплект деталей для задан ного изделия.
3000
Рис.5.5. Общий вид рамы экскаватора ЭКГ-4,6
В технологическом стенде 2 производится сборка решетки нижнего настила рамы, а также закрепление всех элементов на прихватках.
17i
Рис.5. б. Технологическая схема участка сборки и сварки рамы экскаватора ЭКГ-4,6.
Затем рама поступает для сварки на позиционеры 3, где сва риваются детали решетки между собой и с настилом. Следует обратить внимание на характерную для организации поточного производства особенность - наличие накопителя 4, служащего для синхронизации работы оборудования. В случае нарушения цикла изготовления, собранные узлы можно временно хранить на складской площадке 4 (накопителе), расположенной перед позиционерами. После сварки на позиционере 3 раму передают мостовым краном на сборочно-сварочные стеллажи 5, где зачи щают швы и устанавливают остальные элементы. Окончатель ная сварка производится на позиционерах 6, углубленных в при ямках (рис. 5.3).
По окончании сварки рама поступает на площадки 7, 8 для очистки и визуального контроля качества швов. Готовые узлы передаются с помощью вагонеток для выполнения последую щих операций механической обработки и грунтовки.
Сборка рамы. Жесткие требования к точности изготовления сварных рам определяют целесообразность применения сбороч ных кондукторов. Для сборки решетки рамы используется стенд, показанный на рис. 5.7.
Конструкция стенда позволяет выполнять с необходимой точностью геометрию изделия, а применение пневматических прижимов дает возможность резко сократить время закрепления элементов и облегчить работу слесаря-сборщика.
Стенд представляет собой жесткую раму 7, изготовленную из двутавровых балок, закрытую сверху толстым листом, на кото рый приварен ряд опорных пластин. Их наличие значительно сокращает объем механической обработки базовой поверхности рамы приспособления, т.к механически обрабатывают не зсю поверхность, а только выступающие опорные пластины. На пла-
172
стины устанавливают обработанные по плоскости сопряжения опорные базовые элементы - упорные стойки 3, 8, которые обес печивают возможность получить правильную геометрию верти кальных листов собираемого узла.
Рис. 5.7. Приспособление для сборки решетки рамы.
Для поджатая вертикальных листов на раме стенда установ лено 19 пневмаприжимов 2. Необходимо обратить внимание на характер размещения упорных стоек 3 и прижимов 2 относи тельно фиксируемых элементов (вертикальных листов изделия). Упорные стойки должны быть расположены так, чтобы свароч ные деформации не приводили к заклиниванию детали в при способлении и не препятствовали ее извлечению, т.е. все упоры
173
должны быть размещены по одну сторону фиксируемой детали, а прижимы - по другую. В показанном на рис. 5.7. сборочном приспособлении деталь после сварки можно извлечь, если сдви нуть ее по диагонали, как показано стрелкой.
Определенные сложности возникают при сборке корпусов подшипников 1 и 5 с диафрагмами решетки рамы. Фиксация их положения осуществляется оправками с разжимными кулачка ми, действующими от поворота винта (рис. 5.8).
В корпусе оправки 1 размещена гильза 2, на конце которой имеется центрирующая втулка 3. При сборке вручную переме щают гильзу и вводят в корпус подшипника центрирующую втулку. Затем с помощью винта 7 перемещают сухарь внутри центрирующей втулки, который раздвигает в радиальном на правлении сухари 5, расположенные в двух параллельных плос костях, фиксируя положение корпуса подшипника по отноше нию к решетке рамы. Перемещения гильзы обеспечивает воз можность извлечения собранной рамы из приспособления.
Рис. 5.8. Разжимной фиксатор с ручным приводом.
Подобным образом производится фиксирование положения картера и подшипника, но оправка 6 имеет пневматический при вод.
Внутри рамы стенда выполнена разводка трубопровода сжа того воздуха из магистрали ко всем цилиндрам.
При сборке решетки рамы производится прихватка всех лис тов в вертикальном положении друг к другу.
После установки литых подшипников в диафрагмах рамы ус танавливают верхний настил и центрируют отверстие централь-
174
ной отливки пневматической оправкой стенда (рис. 5.4). Затем прикрепляют настил к вертикальным листам с помощью уси ленных прихваток, так как эти прихватки должны удерживать раму весом около 15 т. При сварке позиционер предназначен для установки деталей, закрепленных на планшайбе, в удобное по ложение для сварки «в лодочку».
Сварка рамы разбивается на две стадии: сварка решетки по сле сборки ее в механизированном стенде и окончательная свар ка после закрытия вторым настилом и установки всех деталей.
В зависимости от характера выполнения сварочных работ ис пользуются разные схемы размещения позиционеров. Позицио неры 3 (рис. 5.6) установлены на фундаменте высотой 650 мм над уровнем пола цеха, каждый из них имеет площадку (рис.5.2), на которой размещается сварщик при выполнении сварки решетки.
Позиционеры 6 (рис. 5.6) этой же конструкции установлены в специальные углубления, чтобы окончательная сварка произво дилась на уровне пола цеха (рис. 5.3). Поэтому позиционеры не имеют рабочих площадок.
Раму можно поворачивать вокруг оси вращения от 0 до 360° и наклонять от 0 до 85°.
После окончания сварки решетки рамы планшайба устанав ливается в горизонтальное положение, раскрепляются крепеж ные устройства и узел мостовым краном передается на следую щую операцию - закрытие нижним настилом.
После установки настила и всех элементов рамы окончатель ная сварка выполняется на позиционере, установленном в уг лублении. Кроме крепления изделий на планшайбе и отсутствия сварочной площадки в технологии сварки на этом рабочем месте по сравнению с рабочим местом сварки решетки существенной разницы нет.
Замыкает цикл изготовления нижних рам зачистка и разметка припусков на механическую обработку.
175
6. РЕШЕТЧАТЫЕ КОНСТРУКЦИИ
6,1. Приемы сборки в индивидуальном и мелкосерийном производстве
Решетчатые конструкции весьма разнообразны по размерам и формам. К ним относятся фермы, состоящие из двутавров, швеллеров, уголков, труб, опоры буровых установок для глубо ководного бурения, состоящие из труб диаметром от 200 до 2000 мм; решетки арматуры железобетона, изготовленные из прутков диаметром 4-г32 мм.
Общим для таких конструкций является необходимость со единения между собой нескольких отдельных стержней в узел. Сварные соединения имеют относительно малую протяженность и располагаются в различных пространственных положениях. При изготовлении решетчатых конструкций наибольшее приме нение находит ручная дуговая и механизированная сварка в за щитных газах проволокой сплошного сечения и порошковой самозащитной проволокой. Рациональное конструирование уз лов позволяет в некоторых случаях применить высокопроизво дительную контактную сварку. Для узлов с нахлесточными со единениями перспективным является применение пайки.
При изготовлении ферм, стержни которых состоят из парных элементов, широко используется метод копирования. Сущность метода заключается в следующем. По разметке собирают и сва ривают полуферму, состоящую из одиночных элементов (рис.6.1 а); производят ее кантование и закрепляют на стеллаже косын ками вверх. Затем, используя эту полуферму в качестве копира, производят сборку деталей следующей полуфермы как по шаб лону. Для этого детали полуфермы 2 (элементы верхнего и ниж него пояса, раскосов, стоек и др.) раскладывают на копире 1 (рис. 6.1 б), совмещая их с одноименными деталями. После скрепления между собой деталей полуфермы 2 сварными швами, ферму снимают с копира, кантуют на 180° и дополняют её недос тающими элементами. Для того чтобы исключить накопление по грешностей при сборке последующих полуферм, подменять по- луферму-копир в процессе изготовления не рекомендуется.
176
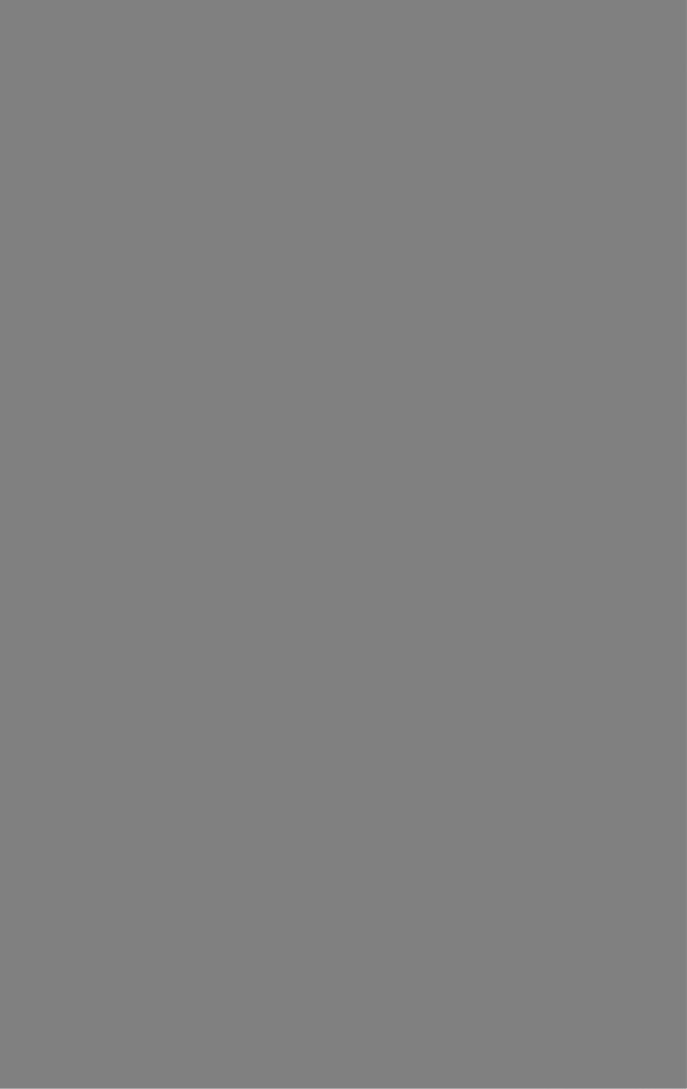
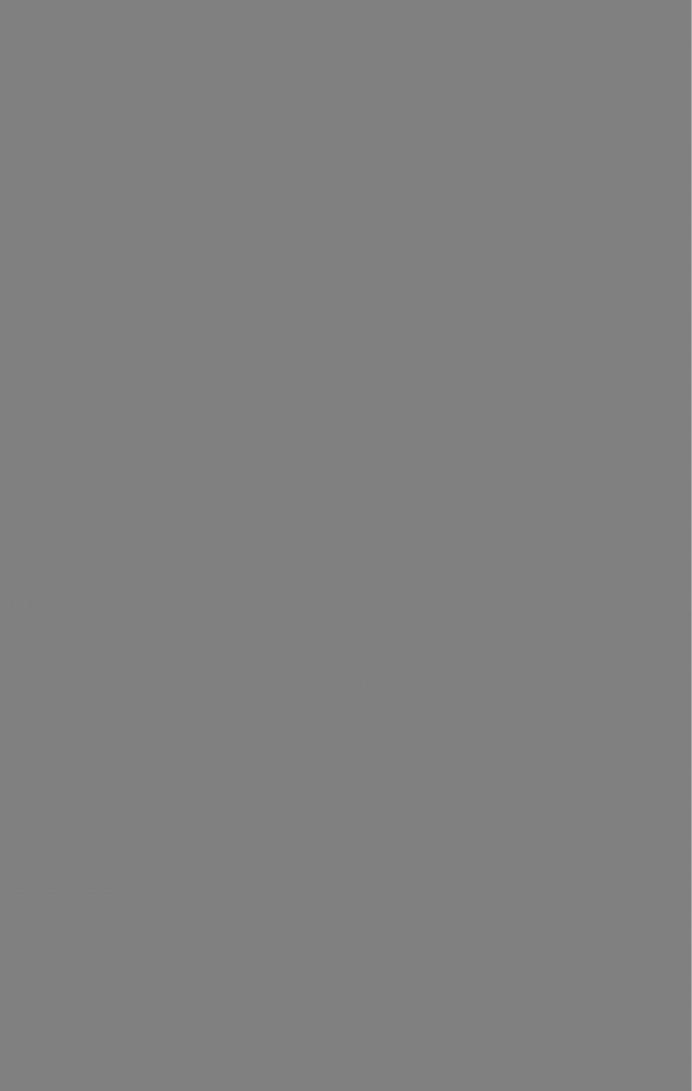
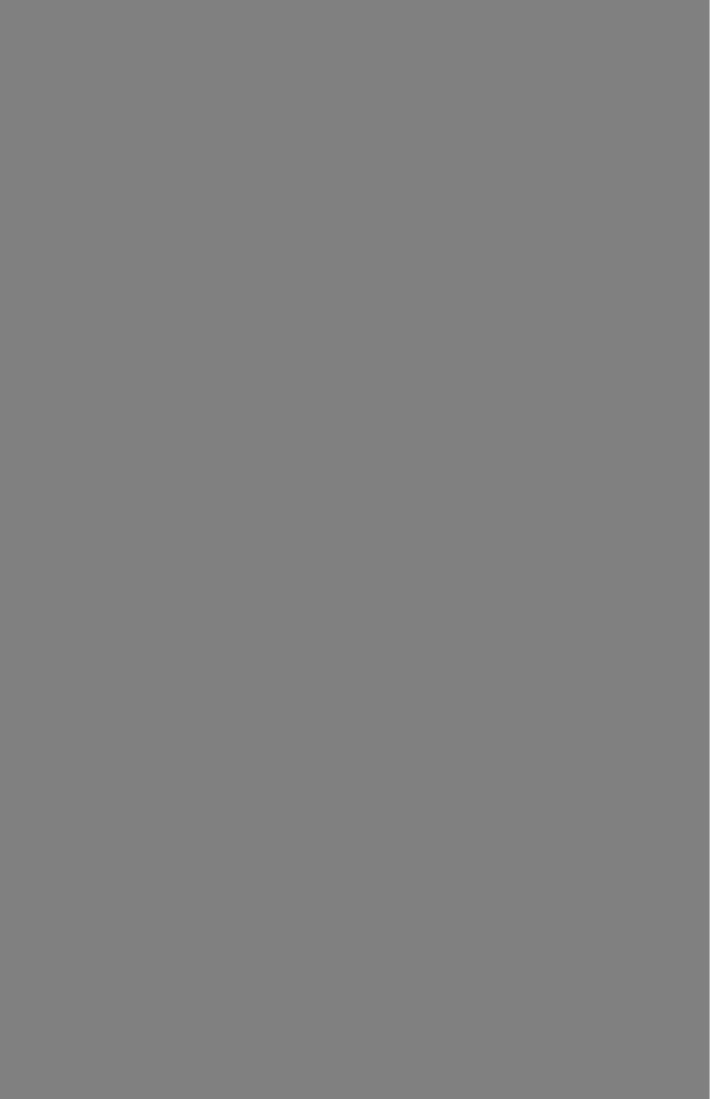
и национальными стандартами заказчика. Основным междуна родно-признанным нормативным документом является стандарт Американского института нефти API RP2A - Практические ре комендации для проектирования, расчета и сооружения стацио нарных морских платформ, в котором отражен опыт сооружения морских буровых платформ. В части технологии сварки требо вания, как правило, основываются на стандарте Американского общества сварщиков AWS - Structural Welding Code AWS D 1.1.
Трудоемкость и качество выполнения сборочных и свароч ных операций в условиях цеха, на монтажной площадке пред приятия изготовителя и при монтаже на месте эксплуатации су щественно различаются. Очевидно, что в условиях цеха проще обеспечить наиболее высокое качество изготовления, так как появляется возможность автоматизировать процесс, выполнить сварку в удобном положении, исключить неблагоприятное влияние окружающей среды. Поэтому необходимо стремится к тому, чтобы максимальный объем работ при сооружении таких конструкций был выполнен в условиях цеха, однако при этом возникают проблемы транспортировки крупногабаритных кон струкций к месту эксплуатации.
Чрезвычайно большие габариты опор морских буровых плат форм практически исключают возможность использования тра диционных для решетчатых конструкций схем сборки, когда стержневые элементы собирают в узел путем непосредственного соединения между собой раскосов, стоек, поясных элементов. Так же исключено применение метода копирования для сборки. Определенные трудности при сборке и сварке возникают в ре зультате того, что концы трубчатых стержневых элементов в месте соединения имеют сложный криволинейный контур.
При сооружении больших решетчатых, опор всю конструк цию расчленяют на сборочные единицы, а изготовление и мон таж ведут в три этапа.
При расчленении на сборочные единицы необходимо прини мать во внимание следующее:
Габариты; масса; размерность - они в значительной степе ни определяют транспортабельность, удобство сборки, доступ ность сварных соединений для сварки и последующего контроля качества;
180