
книги / Ультразвуковой контроль сварных соединений
..pdfЗначительный объем информации о дефекте может быть по лучен при измерении условной высоты АН и условной ширины АХ дефекта по обратному и зеркальному сигналам и сравнению
полученных численных значений между собой. Измерение этих информативных признаков производится по принципам, изло женным в ГОСТ 14782 - 86.
В случае небольших размеров дефектов (b < а) измерение
крайних сигналов может быть выполнено как при одновременном перемещении искателей, так и при одном неподвижном искателе (обычно первом). Для дефектов значительных поперечных разме
ров (Ь>а) измерения АН и АХ должны производиться при
построчном сканировании по асимметричной или симметричной схеме.
Ширину огибающей последовательности зеркальных' сигна лов измеряют на экране дефектоскопа при постоянном уровне чувствительности, установленном при эталонировании (Аут=const), либо на определенном уровне от максимальной
амплитуды измеряемого сигнала (обычно принимают =
= 0,5А^ max ). Иногда полезно за опорный уровень принимать уро
вень максимального обратного сигнала.
При измерении первым способом условный размер пропор ционален амплитуде зеркального сигнала и соответственно будет уменьшаться с увеличением глубины залегания дефекта. При из мерении вторым способом условный размер не зависит от 4, и, следовательно, от глубины залегания. В этом случае он несет ин формацию о размерах дефекта по сечению.
Соотношение условных размеров по А ^ и А^ позволяет су
дить о типе дефекта и ориентации плоскостных дефектов в вер тикальной плоскости.
6.4.Временные способы определения
ВЕЛИЧИНЫ ДЕФЕКТОВ
Временные способы подразделяются на собственно времен ные, когда регистрируется временная задержка прихода послан ной волны, обусловленная ее обеганием по поверхности дефекта,
идифракционно-временные, основанные на явлениях дифракции
итрансформации объемных и поверхностных волн на трещинах.
При наличии трещины на поверхности контролируемого из делия, вдоль которой распространяется поверхностная волна, часть энергии отражается от границы раздела плоскость - трещи на и нижней части трещины; часть, дифрагируя, распространяет ся вокруг трещины и часть трансформируется в объемные попе речные и продольные волны. Измеряя с помощью двух ПЭП вре мя распространения поверхностной волны вокруг трещины и по лагая, что на всем пути скорость неизменна, определяют ее глу бину.
Этот метод наиболее эффективен при контроле трещин в из делиях, в которых действует растягивающее напряжение. При отсутствии таких напряжений трещины имеют небольшое рас крытие и большая часть энергии проходит через нее.
В работе [30] предложены временные способы измерения глубины трещин, основанные на регистрации дифрагированной продольной или поперечной волны. При этом о глубине трещи ны hf судят по времени запаздывания дифрагированной волны
(рис. 6.10) [22, 23]. Преимуществом данного метода является то, что амплитуда регистрируемого сигнала практически не зависит от наклона трещины и состояния поверхностей изделия и тре щины. Таким методом можно измерять глубину трещин в изде лиях с неэквидистантными поверхностями. Точность метода, как и методов, основанных на использовании поверхностных волн, в основномопределяется точностью измерения времен ных интервалов.
Амплитуда дифрагированного луча зависит от углов и типов волн падающего луча, а также от степени раскрытия трещины. Стянутая трещина прозрачна для падающего луча и на ней ди фракции не возникает. Амплитуда дифрагированного луча, реги стрируемого приемником, тем больше, чем больше угол между падающим и дифрагированными лучами.
Временное разрешение максимально, когда в треугольнике дифракции, стороны которого составляют лучи (опорный, па дающий и дифрагированный), угол 2у = 140°. С этой же целью целесообразно применение поперечных волн.
Высота внутренних трещин (не выходящих на поверхность) определяется путем измерения времени задержки At между ди
фрагированными сигналами от верхней и нижней вершины де фекта. Применяя раздельные излучающий и приемный ПЭП с углами ввода а } и а 2, вначале находят максимум сигнала, ди
фрагированного на верхнем конце трещины, и измеряют время его прихода, а затем раздвигают ПЭП и измеряют время прихода дифрагированного сигнала на нижнем конце трещины при его максимальной амплитуде.
Рис. 6.10. Измерение величины трещины по времени задержки дифрагированных сигналов:
а - при прозвучиваиии двумя П Э П с Двух сторон дефекта; 6 - при прозвучивании одним П Э П и оценке ДЛР по задержке между импульсами в двойном сигнале
Высоту трещины определяют из выражения hf = cAf/(seca, + seca2).
Чтобы оптимизировать параметры акустической системы, це лесообразно использовать выражение, определяющее условие получения максимального дифрагированного сигнала Адф;
- V 4 > = f ^ e x p { - 8 , 5 10-3( 150 - аэ)2} ^ ® ,
где В - постоянная, зависящая от размеров пьезоэлемента и величины зерна.
Для продольных волн оптимальный угол ввода а = 65°, для
поперечных оц = 40°. В тонкостенных изделиях для измерения высоты трещины наиболее целесообразно применять продольные волны (с*) = 60...70°), а в толстостенных - поперечные волны
(а, = 37...47°).
Метод имеет тенденцию к занижению истинного размера на 1,5 мм. Абсолютная ошибка в определении размеров дефектов по сечению шва составляет ±1,5 мм.
6.5.Измерение дефектов типа «цепочек»
При разбраковке очень важной является возможность распо знавания сплошного непрерывного дефекта, например непровара, от цепочки дефектов типа шлаковых включений и пор.
Возможность разрешения двух рядом находящиеся отражате лей характеризуется фронтальной разрешающей способностью ПЭП. Она определяется минимальным расстоянием между дефек тами Lp , залегающими в плоскости, перпендикулярной акустиче
ской оси пучка, при котором эти дефекты в процессе перемещения ПЭП по поверхностиизделия регистрируются раздельно.
Если перемещать ПЭП по поверхности изделия в плоскости, в которой находятся оба дефекта, то суммарная амплитуда эхосигнала А в зависимости от расстояния между дефектами Lp бу
дет изменяться, как показано на графиках рис. 6.11. Максимальный сигнал имеет место, когда преобразователь
расположен над одним из дефектов. Если преобразователь распо ложен между дефектами, то при небольших расстояниях эхосигнал, пришедший от более дальнего дефекта, интерферирует с эхо-сигналом от ближнего дефекта и в зависимости от фазовых соотношений или усиливает, или ослабляет суммарный эхосигнал. Этим объясняется довольно сложный характер графика. Когда преобразователь расположен посередине, между дефекта ми, разность фаз от двух дефектов равна нулю.
Можно считать, что два дефекта выявляются раздельно, если минимальный и максимальный эхо-сигналы отличаются по вели
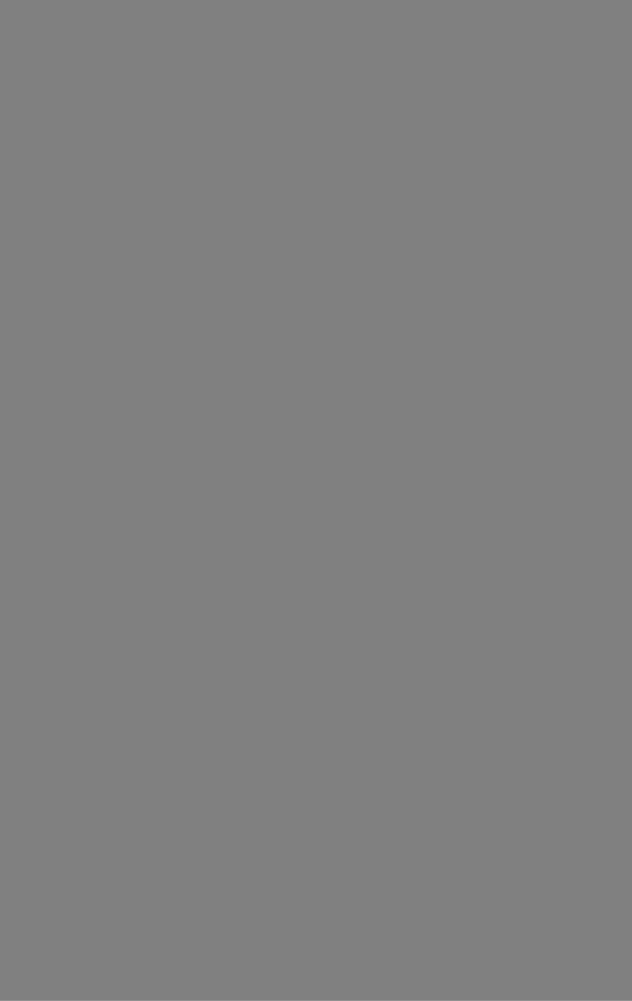
умноженное на отношение длины волны ультразвука к радиусу пьезоэлемента
Рис. 6.12. Изменение уровня разрешения М. =Ат„ -А^ь» дБ» от расстоянии между плоскодонными отражателями (lb =2 мм) в горизонтальной плоскости:
г = 85 мм; / - ПЭП;/= 1,8 МГц; 2а = 18 мм; р = 40°; 2 - ПЭП;/= 2,5 МГц; 2а= 12 мм; р = 40°
При контроле реальных изделий вследствие естественных на рушений рассмотренной геометрии прозвучивания и неидектичности дефектов эти соотношения не будут точно соблюдаться. Поэтому фронтальная разрешающая способность в реальных ус ловиях будет выше, чем для моделей дефектов (т.е. Lp - мень
ше). Если при перемещении преобразователя на расстояние меньше фронтальной разрешающей способности появляется не сколько эхо-сигналов, это не означает, что в шве имеется столько же дефектов.
6 .6 . С п о с о б ы р а с п о зн а в а н и я т и п а д е ф е к т о в
Информация о типе дефекта может быть получена путем ана лиза индикатрисы рассеяния, т.е. анализа распределения ампли тудно-частотных и амплитудно-временных характеристик рас сеяния на дефекте поля. В зависимости от вида измеряемых па раметров, метода их получения и обработки можно провести ус ловную классификацию информативных признаков:
1) анализ пространственного распределения амплитуд эхосигналов на одной частоте и, в частности, по выбранным фикси рованным направлениям: в. вертикальной и горизонтальной плос костях;
2) амплитудно- и фазочастотный анализ эхо-сигналов в од ном или нескольких направлениях (спектральный метод);
3)анализ временных характеристик дифрагированных и трансформированных на дефектах волн;
4)анализ характеристик поляризации отраженных от де фектов линейно-поляризованных сдвиговых волн;
5)методы ультразвуковой голографии и томографии. Оценка допустимости обнаруженного в сварном шве дефекта
должна максимально полно и точно отражать степень потенци альной опасности дефекта для эксплуатационной прочности шва.
Потенциальная опасность дефекта определяется его формой. Элементы тонкой структуры несплошности, по которым произ водятся ее идентификация и оценка степени опасности, в частно сти, остро га края дефекта, измеряются десятыми и сотыми доля ми миллиметра, что не позволяет производить оценку этого па раметра в применяемом для дефектоскопии частотном диапазоне ультразвуковых волн. При контроле возможно распознавание элементов структуры, больших длины волны акустического из лучения А.,т.е. больше0,4...0,5 мм.
По этой причине возможности ультразвукового контроля в идентификации дефектов принципиально ограничены.
Сопоставление результатов выполненных автором исследо ваний морфологических (профиль поверхности) и отражательных характеристик дефектов позволило сформулировать количест венные признаки плоскостных и объемных дефектов [92].
Трещиноподобные и объемные дефекты имеют резко отлич ные числовые выражения морфологических и отражательных характеристик у различных типов и в то же время достаточно тесно коррелированы между собой в пределах одного типа (табл. 6.1). При этом средние значения отражательных характе ристик реальных дефектов различных типов приняты за эталоны классов в системе распознавания.
На уровне значимости 0,1 плоскостным предлагается считать
дефект, у которого djL <0,1, a tg26/, <0,12 (или 5 ^ <2,3 мм2).
Для того чтобы обеспечить достоверную идентификацию де фектов, проводимую при штатном контроле на производстве, к информативным признакам предъявляются следующие требова ния:
•возможность представления информации о типе дефекта в виде количественного критерия (числового выражения);
•высокий уровень распознавания, определяемый расстояни ем Х 0 между эталонами классов в пространстве признака.
Это расстояние X должно превышать Х 0 для выбранного
коэффициента правдоподобия, учитывающего статистиче ские характеристики дефектности и стоимость ошибок идентификации;
•простота измерения и, в частности, серийно выпускаемой аппаратурой (стандартными дефектоскопами и ПЭП);
•возможность распознавания дефектов, заложенных в тол щине сварного шва.
Дефект
Трещины
Таблиг^а 6.1
Характеристики дефектов
Параметры макрогеометрии
Оценка |
д , |
Д// |
sh> |
1н, |
■ |
IJL |
djL |
|
мм |
|
мм |
ММ |
|
|
|
|
|
момента |
|
|
|
|
|
|
||
|
|
|
|
|
|
|
|
|
Среднее |
0,95 |
0,07 |
0,66 |
2,6 |
0,12 |
0,28 |
0,1 |
‘ |
выбо |
+0,18 |
|
|
|
|
|
|
|
рочное |
-0,04 |
|
|
|
|
|
|
|
|
|
|
|
|
|
|
|
|
Средне |
0,87 |
0,06 |
0,62 |
0,73 |
0,12 |
|
|
|
квадра |
|
|
|
|
|
|
|
|
тичное |
|
|
|
|
|
|
|
|
отклоне |
|
|
|
|
|
|
|
|
ние |
|
|
|
|
|
|
|
|
Коэффи |
|
|
0,93 |
0,28 |
1,0 |
|
|
|
циент |
|
|
|
|
|
|
|
|
вариа |
|
|
|
|
|
|
|
|
ции |
|
|
|
|
|
|
|
|
Объемные
Среднее
выбо
рочное
Средне
квадра
тичное
отклоне
ние
1
±0,04
0,15
Дефект |
момента |
п |
дБ/ |
|
|
Оценка |
|
ЭЛ/др |
|
|
|
|
||
|
|
|
град |
|
|
Среднее |
0,96 |
1,15 |
|
Трещины |
выборочное |
+ 0,12 |
|
|
Среднеквад |
0,4 |
2,8 |
||
|
||||
|
ратичное |
|
|
|
|
отклонение |
|
|
|
|
Коэффициент |
|
|
|
|
вариации |
|
|
|
Объемные |
Среднее |
2,01 |
0,55 |
|
ратичное |
ТО,23 |
|
||
|
выборочное |
|
||
|
Среднеквад |
0,36 |
1,8 |
|
|
отклонение |
|
|
|
|
|
дефек |
|
|
Дефект |
Оценка |
ты |
|
|
|
|
|||
|
|
|
||
|
момента |
|
|
|
|
|
■4o6p/4j> |
■^обр |
|
|
|
ДБ |
|
|
|
Среднее |
-1 5 |
|
|
|
выборочное |
|
|
|
Л |
|
|
|
|
X |
Среднеквад |
5,8 |
|
|
X |
|
|||
$ |
ратичное |
|
|
Нотклонение
|
Коэффициент |
0,21 |
|
вариации |
' |
Объемные |
Среднее |
+ 6,5 |
ратичное |
' |
|
|
выборочное |
|
|
Среднеквад |
5,1 |
|
отклонение |
|
Параметры поля |
|
|
|||
дА |
один ПЭГI |
|
|
|
|
А |
Интервал кор |
SA |
|||
д& ’ |
|
реляции |
v = - £ |
||
А ' |
А |
||||
1А, мм |
|||||
дБ/ |
дБ . |
|
|||
град |
|
верт. |
гор. |
|
|
0,52 |
3,8 |
2...4 |
2,65 |
0,28 |
|
1,7 |
2,7 |
0,4...0, |
0,93 |
|
|
|
|
6 |
|
|
|
0,35 |
|
0,5...0, |
0,35 |
|
|
|
|
67 |
|
|
|
4,2 |
|
|
|
0,21 |
|
3,1 |
|
|
|
|
Параметры поля ЭЗМ
стационарная поверхность
|
|
^обр/^э |
|
|
|
а = 50“ |
|
наклонный |
У - кварц |
||
асим. |
сим. |
SV |
SH |
|
|
0,023... |
0,24 |
|
|
0,093 |
|
0,11 |
0,32 |
0,17... |
0,24... |
|
|
0,18 |
0,28 |
Правильный выбор информативных признаков описания де фектов, т.е. таких признаков, в которых сосредоточена наиболее существенная для распознавания информация, является одной из важнейших и необходимых предпосылок успешного решения задачи распознавания в целом.
Выполненные исследования характеристик дефектов позво лили предложить информативные признаки, удовлетворяющие этим требованиям, установить их числовые значения и границы измерения.
Коэффициент формы дефектов Кф, предложенный
В.Г. Щербинским и В.Е. Белым, определяется в виде отноше ния амплитуд сигналов - отраженного от дефекта обратно к искателю А^6р и испытавшего двойное зеркальное отражение
от дефекта и внутренней поверхности изделия при прозву-
чивании дефекта двумя однотипными наклонными ПЭП (рис. 6.13а).
в
Рис. 6.13. Измерение коэффициента К+ объемного (1) н плоскостного (2) дефектов:
а - в толстостенных соединениях; б - в прутках, валах; в - в тонкостенных свар ных швах; Лавр.; А%- амплитуды эхо-сигналов, принятых первым и вторым ПЭП