
книги / Ультразвуковой контроль сварных соединений
..pdf1 |
2 |
3 |
4 |
5 |
6 |
7 |
8 |
1 |
УД-2 IP |
ЖК |
|
|
С-скан |
|
220x105x35 |
Сварные стыки трубопроводов |
|
«Политест» |
|
|
|
|
|
1,5 |
0 10.. .530 с толщиной стенки |
|
|
|
|
|
|
|
|
2... 10 мм хордовыми ПЭП, |
|
|
|
|
|
|
|
|
дефектеграмма, «заморозка»; |
|
|
|
|
|
|
|
|
«мышь» |
|
«Скаруч»
«АЛТЕС-
лтд»
USN 52Р ф. «Крауткремер», Германия
USM-25 . ф. «Крауткремер», Германия
ЕРОСН-Ш ф. «Панамстрик»
США
ЭЛ |
ч |
. |
разв. А-500 |
|
4 |
Автоматическое измерение коорди |
|
|
|
|
|
|
|
|
|
|
|
|
|
нат и амплитуды сигнала |
ЭЛ 146x67 |
40 |
+ |
разв. А-30, |
-20...55 |
250x146x133 |
Два строба, автоматическое измере |
R - 552x256 |
|
|
измерение |
|
2,7 |
ние амплитуд и координат; «меню»; |
|
|
|
толщины- |
|
|
индикация кол-ва отражений при |
|
|
|
2500 резуль |
|
|
контроле многократно отраженным |
|
|
|
татов |
|
|
лучом |
ЖК 96x72- |
|
DAC |
настройка-100 |
0...+55 |
245x265x46 |
Амплитуда в дБ относительно кривой |
|
|
|
|
|
1,6 |
DAC; глубины и расстояния до про |
|
|
|
|
|
|
екции дефекта на поверхность; |
|
|
|
|
|
|
текст; изображение; каталог; «замо |
|
|
|
|
|
|
розка»; «ловкая» ручка |
ЭЛ 67x60 |
DAC |
по спец, |
разв. А-137, |
-25...70 |
2,9 |
В-развертка; вычисление координат с |
R - 320x256 |
ВРЧ |
заказу |
настройка- |
|
|
учетом кривизны поверхности; два |
|
|
|
137, измере |
|
|
строба; индикация количества отра |
|
|
|
ние ТОЛШИНЬЕ- |
|
|
жений при контроле многократно |
|
|
|
2500 резуль |
|
|
отраженным лучом; «заморозка» |
|
|
|
татов |
|
|
|

EPOCH ШВ |
ЭЛ 67x60 |
DAC |
разе. А-50, |
-20...50 289x156x48 |
ф. «Панамет- |
R - 320x256 |
|
настройка- |
1,2 |
рик» США |
|
130, измере |
||
|
|
289x177x95 |
||
|
|
|
|
ние толщины |
3,3 |
|
1000 резуль |
||
|
||
татов |
|
«заморозка», отображение радиоим пульса; автоматическое измерение амплитуды и координат; два строба
SONIC-200 |
|
ЭЛ |
40 |
|
разе. А -100, |
- |
10...50 |
2,7 |
Автоматическое распознавание ПЭП; |
ф. «Намикон» |
R - |
320x256 |
|
|
настройка- |
|
|
|
«ловкая» ручка, сменный дисплей |
Италия |
ЖК 122 мм |
|
|
100, измере |
|
|
|
|
|
|
R - |
320x240 |
|
|
ние толщины |
|
|
|
|
|
|
|
5000 резуль |
|
|
|
|
||
|
|
|
|
|
|
|
|
|
|
|
|
|
|
|
татов |
|
|
|
|
SONIC-100 |
ЭЛ и ЖК |
40 |
|
разв. А -100, |
-20...50 |
240x90x140 |
«заморозка»; часы; календарь, тек |
||
ф. «Намикон» |
|
96x73 |
|
|
настройка- |
|
|
2,6 |
стовый редактор; сменные дисплеи; |
Италия |
R - |
320x256 |
|
|
100, измере- * |
|
|
|
автоматическое измерение амплиту |
|
|
|
|
|
нис толщины |
|
|
|
ды и координат (X, Y) |
|
|
|
|
|
500 результа |
|
|
|
|
|
|
|
|
|
тов |
|
|
|
|
«Ultrasonic- |
ЖК-8 цветов |
40 |
DAC |
разв. А-50; |
- |
10...55 |
4,9 |
Функция встроенной подсказки |
|
230» |
|
96x77 |
|
|
настройка-20; |
|
|
|
|
R - 320x256 |
измерение |
|
толщины 2000 |
||
|
||
|
результатов |
1
Применение процессорных дефектоскопов существенно об легчает труд и снижает психофизиологическую нагрузку на опе ратора, поскольку освобождает его от большинства измеритель ных операций; повышает производительность контроля за счет резкого сокращения (в десятки раз) времени на настроечные опе рации при переходе с одного объекта на другой и, самое главное, повышает достоверность контроля. Последнее, в первую очередь, определяется новыми возможностями, такими как: наличие «за морозки» (накопления) сигнала и измерением максимальных па раметров сигнала в этом режиме при многократном сканирова нии дефекта; проведением настройки дефектоскопа в камераль ных условиях, что снижает уровень ошибок; задание через «ме ню» времени прохождения УЗК в призме, что повышает точность измерения координат; одновременное измерение двух координат дефекта, что необходимо при контроле сложных по геометрии объектов, например, угловых швов врезки «труба в трубу»; запо минание осциллограммы дефектного участка и его анализ в ка меральных условиях с привлечением специалистов более высоко го уровня; архивирование результатов контроля (осциллограмм и комментариев к ним) на ПЭВМ для дальнейшего мониторинга за поведением дефектов, оставшихся в конструкции.
Ультразвуковой дефектоскоп «EPOCH III» может быть снаб жен дополнительной платой памяти и ручным сканеромкодировщиком положения («мышь»), что позволяет получать масштабную двухцветную индикацию поперечного сечения объ екта контроля (В-развертка).
Японский прибор «SM-I» с цветным дисплеем позволяет получить четырехцветную (в зависимости от амплитуды сигна ла) индикацию поперечного сечения изделия, но не в масштабе. В приборе отсутствует датчик положения при работе в режиме получения развертки «В», и оператор должен сам синхронизи ровать перемещение преобразователя со скоростью развертки (2; 4; 8; 16 с).
Одним из основных недостатков ультразвукового контроля
.традиционным ручным методом является, то, что после него не остается объективных документов (дефектограмм), по которым можно было бы контролировать работу самих операторов. Это обуславливает зависимость оценки качества шва от квалифика ции, психофизиологического состояния и условий работы опера тора. Иными словами, можно констатировать, что достоверность
ручного контроля почти целиком определяется персональной надежностью оператора. Поэтому очевидна необходимость авто матизации ультразвукового контроля.
Развитие автоматизации ультразвукового контроля идет по. пути многофункциональности и роботизации операций сканиро вания и измерения. Быстродействующие средства контроля соз даются на основе применения аналоговых и цифровых методов обработки многомерного сигнала, а также многоканальных аку стических систем с одновременным или коммутируемым дейст вием. В координатах амплитуда, частота, время строятся двух- и трехмерные изображения акустических полей, что позволяет оценивать тонкую структуру отражающей поверхности.
Механизированное сканирование позволяет облегчить труд оператора, исключить ошибки, связанные с несоблюдением рег ламента сканирования при поиске дефектов, а в некоторых слу чаях даже повысить общую производительность контроля (с уче том подготовительно-вспомогательных операций).
Для дефектоскопии протяженных сварных стыковых соеди нений металлоконструкций толщиной 4...40 мм эффективно ис пользуется автоматизированная установка «Сканер-9312».
Механизм сканирования установки состоит из восьмиканаль ного акустического блока на магнитных колесах, электродвигате ля, датчиков пройденного пути и слежения за сварным' швом и емкости для контактной жидкости.
В состав установки входит восьмиканальный дефектоскоп, принтер и аккумуляторные батареи. Установки обеспечивают проведение контроля со скоростью 1 м/мин.
Автоматическая ультразвуковая установка «АВТОКОНМГТУ» предназначена для ультразвукового контроля качества кольцевых сварных соединений трубопроводов диаметром 530... 1420 мм с толщиной стенки 5;..25 мм (рис. 4.4).
Конструктивно выполнена в виде двух блоков: электронно го блока принтером; механизма сканирования на магнитных колесах с электроприводом и акустическим блоком. Акустиче ский контакт обеспечивается с помощью ферромагнитной жид кости. Скорость контроля 1...2 м/мин. Общая масса установки не более 40 кг.
Преимуществом установки является возможность контроля сварных швов на расстоянии более 20 м от электронного блока, что очень важно на трассе прокладки газо-нефтепровода.
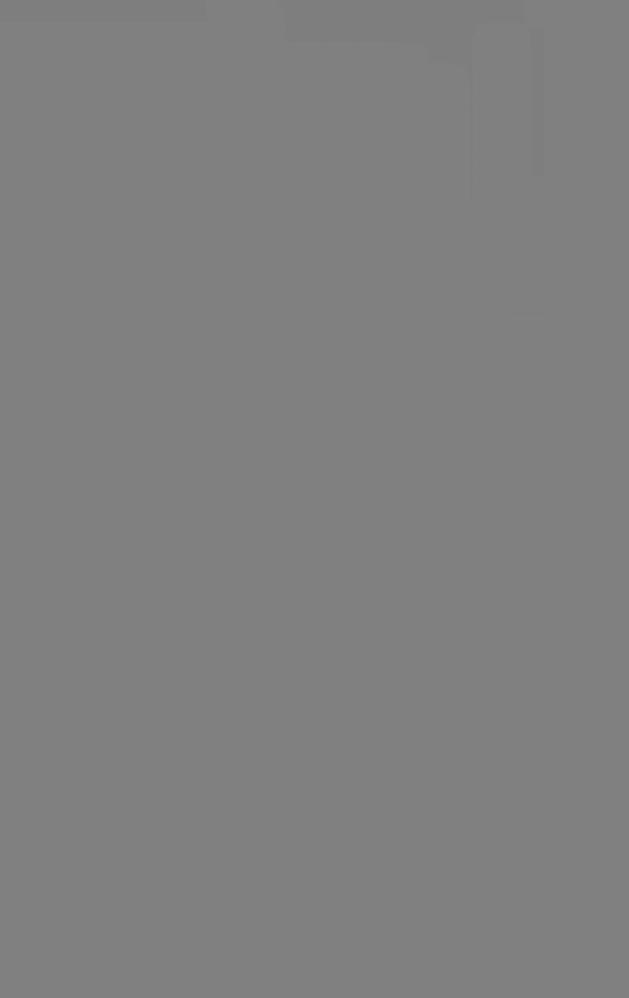
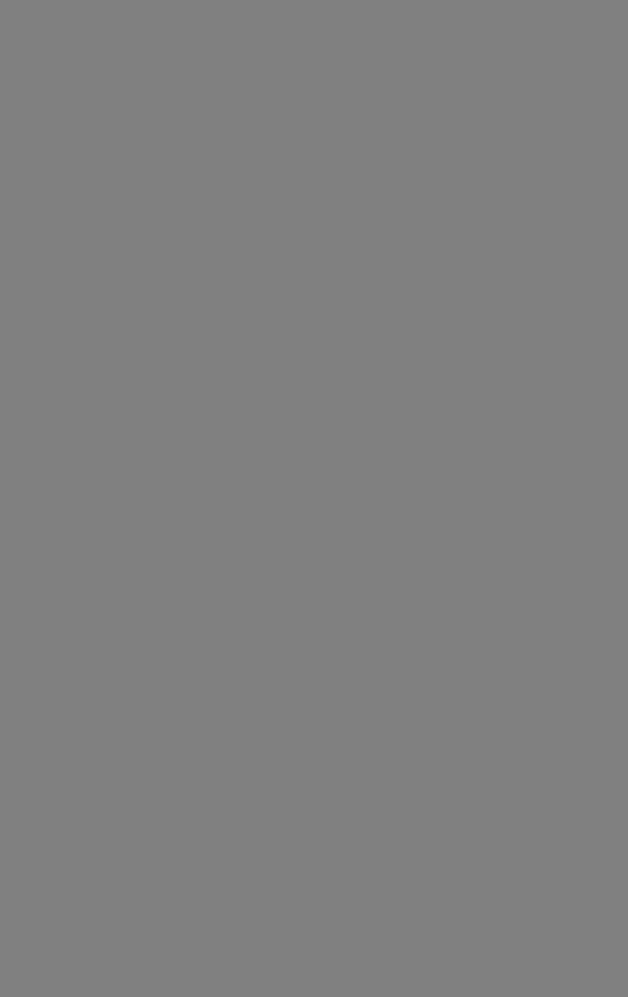
В нем возможно закрепление преобразователей любых ти пов. Крепление сканера к поверхности на магнитах или ваку умных присосках. Площадь стандартного участка сканирования 460x500 мм.
Для контроля сварных швов труб диаметром от 130 мм и бо лее предназначен сканер типа «MS-P-2» той же фирмы. Сканер снабжен магнитными колесами, а также тонкой стальной лентой с пластиковым покрытием для контроля труб из немагнитных материалов. Длина стандартного участка сканирования 400 мм (вдоль шва).
Все сканеры обеспечивают получение цветного изображения 2-х или 3-х мерной развертки типов А, В, С и F (недектированный сигнал).
Пять цветовых палитр и спектр из 128 цветов позволяет с большим разрешением оценивать амплитудный спектр сигналов от отражателей.
Мультитехнологическая интеллектуальная система ультра звукового контроля «JSONIC» ф. «Sonotron Ltd.» (Израиль) со стоит из дефектоскопа USD-10, электронного блока, встроенного Ь промышленный или обычный компьютер, и системы акустиче ских координатных датчиков, разработанных ранее в НИИМостов ЛИИЖТа.
В реальном времени на мониторе, а затем на твердой копии автоматически в реальном времени воспроизводятся изображения дефектов в плане и продольном сечении шва (развертка С).
Установки обеспечивают высокую достоверность, поскольку в процессе сканирования производится автоматическая коррек ция результатов с целью исключения погрешностей. В частности, визуализация дефектов осуществляется с поправками на текущие координаты преобразователя и угол его разворота; на мониторе отображаются участки с нарушением акустического контакта, что позволяет повторно их просканировать и др.
Измерение проекционных размеров и координат с варьирова нием уровней и способов отсечки может проводиться ретроак тивно («контроль после контроля») в камеральных условиях.
Принципиально новый уровень возможностей ультразвукового контроля - это голографические и томографические системы, по зволяющие реконструировать 3-х мерное изображение дефекта.
Такие системы с когерентной обработкой сигнала могут ра ботать при очень маленьких уровнях сигнала и значительном
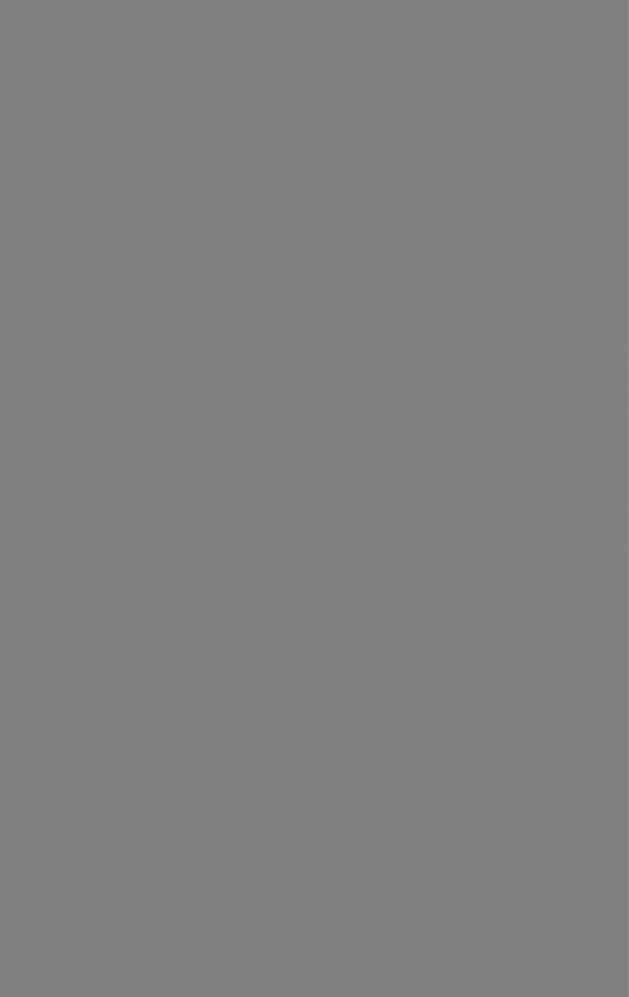
нению с полезным сигналом от дефекта. Это и электрошлаковые сварные швы заготовок роторов турбин толщиной до 1700 мм, стальные и чугунные литые конструкции, аустенитные сварные швы и многие другие. Стандартная ультразвуковая аппаратура, даже при переходе на низкие частоты, не позволяет решать эти проблемы.
Принципиально повысить соотношение полезный сигнап/шум может применение специальных методов генерирования и обработки полученного сигнала. В частности, в активно разра батываемых в МЭИ специальных ультразвуковых дефектоскопах применяются фазоманипулированные зондирующие сигналы, синфазное накопление, квадратичная и корреляционная обработ ка сигналов и др. Созданные на этой основе приборы обеспечи вают проведение дефектоскопии многослойных конструкций с очень* большим затуханием, неоднородных по акустическим свойствам и т.п.
4.2: Преобразователи
4.2.1. Классификация и общие требования
Для возбуждения и приема ультразвуковых колебаний ис пользуют ультразвуковые преобразователи (ПЭП). Их классифи цируют по способу создания акустического контакта с изделием; способу включения пьезоэлементов в электрическую схему де фектоскопа и расположению электрода относительно пьезоэле мента; по ориентации акустической оси относительно поверхно сти изделия; характеристикам направленности акустического поля; ширине полосы рабочих частот [79], числу пьезоэлементов, динамике сканирования в плоскости падения.
Критерии классификации ПЭП по способу создания акусти ческого контакта, ориентации акустичеокой оси и способу вклю чения пьезоэлементов в электрическую схему дефектоскопа при ведены в п. 2.2.
Здесь рассмотрены критерии ПЭП, характеризующие акусти ческие параметры тракта.
С позиций направленности поля излучения ПЭП классифи цируются на плоские (поршневые), у которых характеристика направленности определяется выражением (3.6); фокусирующие, обеспечивающие сужение поля в заданной локальной зоне вдоль оси; широконаправленные веерные, формирующие диаграмму
направленности, близкой к П-образной с резким переходом на границе свет-тень.
С позиций ширины полосы рабочих частот выделяют узкопо лосные ПЭП, у которых ширина полосы меньше одной октавы, и широкополосные, у которых ширина полосы пропускания боль ше одной октавы (отношение максимальной и минимальной час тот на уровне 0,5 больше двух).
Число пьезоэлементов в ПЭП также является классификаци онным признаком (одно-, двух- и многоэлементные). Обычно многоэлементные ПЭП называются акустическими системами, или матрицами. К последним также относятся мозаичные ПЭП в виде фазоуправляемых решеток, формирующих заданную на правленность акустического поля за счет последовательного воз буждения пьезоэлементов по выбранному временному закону.
По способу расположения электрода относительно пьезоэлемента различают ПЭП с контактным электродом и бесконтактным (разнесенным). В последнем случае возбуждение пьезоэлемента осуществляется через зазор, заполненный диэлектриком,
По динамике сканирования выделяют ПЭП и акустические системы с фиксированным и переменным углом ввода (качающийся луч), регулируемым автоматически или вручную.
4.2.2.Конструкция преобразователей и их основные характеристики
Преобразователь является сложным электроакустическим прибором, состоящим из следующих основных элементов: собст венно преобразователя упругих колебаний в электромагнитные и наоборот, протектора (защитного донышка) или акустической задержки (призмы), демпфера, корпуса, токоподвода (рис. 4.7).
В качестве приемно-излучающего элемента в подавляющем большинстве случаев используют пластины из керамики (цирконата титаната свинца или титаната бария), обладающей пьезоэф фектом, или, реже, пьезокварца X- и У-среза с металлизирован ными поверхностями-электродами.
Толщину d пьезоэлектрической пластины выбирают из ус
ловия, чтобы ее собственная частота соответствовала частоте возбужденных или принимаемых УЗ-колебаний, т.е. d - X n/ 2 = = сп/2 / 0 /где А.п и сп - соответственно длина волны и скорости
звука в материале пьезопластины.