
книги / Численное моделирование колебательных 2FSI-процессов в компрессорах газоперекачивающих агрегатов
..pdfЧто касается решения аэроупругих задач для роторов компрессоров и силовых турбин ГПА, то можно выделить представленные ниже работы.
–В статье [14] описаны методы коррекции локальных дисбалансов вала, разработана модель технологического процесса изготовления и монтажа ротора с магнитными подшипниками, обеспечивающего виброустойчивость ГПА. Вопросы аэроупругости при анализе вибраций не рассматриваются;
–В работе [15] численно моделируется влияние теплового воздействия газодинамического потока на радиальное расширение основного диска ротора. Предлагается новая конструкция уплотнительного обода между статором и ротором, который обеспечивает более эффективное охлаждение и снижение величины линейного расширения основного диска. Учет воздействия давлений газодинамических сил на конструкцию компрессора не рассматривался;
–В статье [16] при использовании программного комплекса ANSYS CFX проводились исследования пространственного течения в центробежных компрессорах методами вычислительной газодинамики на многопроцессорной вычислительной технике. Авторы отмечают наличие отрывов на наружной поверхности лопаток рабочих колес, что обусловлено геометрией исследуемого компрессора. CFD- и CSD-сопряженность не учитывалась.
–В статье [2] рассматривается численное моделирование
иисследование аэроупругих колебаний лопаток рабочего колеса четвертой ступени газовой турбины с целью выявления возмож-
ности возникновения автоколебаний. В работе отмечено, что с увеличением массового расхода существует высокая вероятность возникновения автоколебаний лопаток и образования флаттера;
– В [17] проведен анализ рабочего процесса в проточной части промежуточной ступени среднерасходного центробежного компрессора с помощью ANSYS CFX 14.0 с лабиринтными уплотнениями и без них. Исключение из расчетной области междисковых зазоров и лабиринтных уплотнений привело к ожидаемому
11
увеличению КПД в выходном сечении в среднем на 1,6–1,7 %. Авторы отмечают важность учета аэроупругих процессов в лабиринтных уплотнениях при оценке вибраций компрессора.
Отдельные исследования посвящены выбору модели турбулентности при моделировании газодинамической составляющей в 1 и 2FSI-расчетах. В диссертации [18] было проведено исследование влияния различных моделей турбулентности: k–ε, k–ω, SST и BSL. Наилучшее соответствие экспериментальным данным показали расчеты с использованием моделей турбулентности k-ε и SST. В работе [16] вычислительные эксперименты также проводились с использованием SST-модели.
Помимо этого, авторским коллективом настоящей монографии с 2014 по 2018 г. выпущено более 50 научных публикаций, посвященных исследованиям и верификации 2FSI-подходов к решению прикладных наукоемких задач [19–48] и оценке аэроупругих эффектов отдельных систем ротора ГПА – рабочего колеса [49–61], лабиринтного уплотнения [62–69] и разгрузочного устройства [70–72] в 1FSI- и 2FSI-постановках. При этом конструкции рабочего колеса, лабиринтного уплотнения и разгрузочного устройства рассматривались изолированно, т.е. независимо друг от друга. Помимо этого изданы 2 монографии, где также описаны исследования аэроупругих процессов для изолированных систем ротора ГПА в 1FSI [73] и 2FSI-постановках [74].
В настоящей монографии представлены следующие результаты 2FSI-расчетов колебательных процессов ротора ГПА:
–при совместном учете конструкции вала, опор, одного рабочего колеса, разгрузочного устройства и газодинамики одного рабочего колеса;
–при совместном учете конструкции вала, опор, одного рабочего колеса, лабиринтного уплотнения, разгрузочного устройства и газодинамики лабиринтного уплотнения;
–при совместном учете конструкции вала, опор, одного рабочего колеса, разгрузочного устройства и газодинамики разгрузочного устройства;
12
–при совместном учете конструкции вала, опор, одного рабочего колеса, лабиринтного уплотнения, разгрузочного устройства и газодинамики одного рабочего колеса, лабиринтного уплотнения, разгрузочного устройства;
–при совместном учете конструкции вала, опор, трех рабочих колес, трех лабиринтных уплотнений, двух направляющих аппаратов, разгрузочного устройства и газодинамики трех рабочих колес, двух направляющих аппаратов, трех лабиринтных уплотнений, разгрузочного устройства.
Для проведения аэроупругих 2FSI-исследований при совместном учете конструкций основных элементов ротора была разработана совместная геометрическая модель, включающая твердотельную конструкцию элементов и газодинамические области тракта компрессора.
Вместе с тем для построения сеточных моделей использовалось специализированное программное обеспечение для турбомашин TurboGrid и ICEM CFD, позволяющее строить блочные O-grid-топологии для корректного разрешения пограничного слоя
врамках SST-модели турбулентности. При этом сеточные модели для газодинамических областей были построены структурированно в 2D-постановке и симметрично развернуты в 3D с целью исключения влияния асимметрии сетки на результаты моделирования. Сеточные модели вблизи лопаток были также размножены на 360°. Вместе с тем сведено к минимуму влияние асимметрии сеточных моделей твердотельных элементов конструкции ротора ГПА.
13
ГЛАВА I. ОБЗОР СУЩЕСТВУЮЩИХ ПОДХОДОВ. ОСОБЕННОСТИ ПРИМЕНЕНИЯ 2FSI-ПОСТАНОВКИ ПРИ ЧИСЛЕННОМ МОДЕЛИРОВАНИИ АЭРОУПРУГИХ КОЛЕБАТЕЛЬНЫХ ПРОЦЕССОВ В КОМПРЕССОРАХ ГАЗОПЕРЕКАЧИВАЮЩИХ АГРЕГАТОВ
1.1. ИЗВЕСТНЫЕ ПОДХОДЫ К УРАВНОВЕШИВАНИЮ РОТОРОВ И ВАЛОПРОВОДОВ ТУРБОМАШИН
Уравновешивание роторов турбомашин проводится в ходе балансировки и сборки с целью обеспечения их динамической устойчивости.
На динамическую устойчивость валопроводов оказывают влияние как механические, так и газодинамические факторы. В интересах быстрого и эффективного поиска причин низкой динамической устойчивости роторов и валопроводов следует минимизировать влияние механических факторов, приводящих к повышенным вибрациям и изгибам конструкции.
Валопроводы газоперекачивающих агрегатов, включающие в себя роторы привода, трансмиссию и исполнительные механизмы, являются наиболее важной, но и одновременно наиболее напряженной частью. Их динамическое состояние определяет как надежность, так и ресурс работы.
Наиболее негативным фактором, приводящим к сокращению ресурса и снижению рабочих характеристик, являются вибрации. Особенно жесткое влияние на валопровод оказывают вибрации в рабочем диапазоне частот. Также роторы подвергаются и модальным изгибам. При этом в настоящее время отсутствуют технологии балансировки роторов с несовпадающими балансировочными и рабочими осями (поверхностями). Кроме того, при
14
монтаже трансмиссий возникают дисбалансы из-за эксцентриситета их установки.
В настоящее время, в интересах повышения надежности работы и увеличения ресурса, проводятся следующие мероприятия:
–увеличение площади опор и повышение несущей способности подшипников;
–повышение точности изготовления составляющих элементов валопроводов;
–применение высокочастотного балансировочного оборудования;
–применение колодок из композиционных материалов для подшипников;
–использование смазки с демпфирующими свойствами;
–увеличение количества смазочных материалов в зоне
трения;
–использование электромагнитных подвесов. Повышение виброустойчивости валопроводов подобным
образом существенно усложняет конструкцию газоперекачивающих агрегатов и требует применения большого количества ручного труда, а повышение качества материалов и увеличение точности изготовления в настоящее время стало наиболее дорогостоящей проблемой машиностроения. Что касается изгибов роторов, то их минимизация обеспечивается сложным комплексом мер конструкторского и технологического обеспечения
[14, 40–43, 47, 48].
Исходя из этого, заданную динамическую устойчивость роторов следует обеспечивать их сборкой на основе валов, уравновешенных в нескольких плоскостях.
Для обеспечения многоплоскостного уравновешивания валов, являющихся базовой деталью роторов ГПА, необходимо описать положение локальных дисбалансов роторов. При этом на стадии проектирования определяются поверхности, в пределах которых не могут размещаться плоскости коррекции [45, 46]. В пределах доступных поверхностей определяются плоскости
15
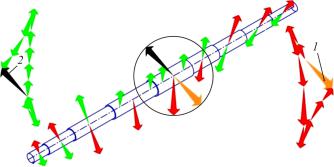
коррекции и рассчитываются коэффициенты поправки масс уравновешивающих грузов kу [75]:
kу |
Zi , |
(1.1) |
|
Zу |
|
где Zi и Zу – продольные координаты расчетной и приведен-
ных (доступных) плоскостей.
Предпочтительное размещение плоскостей коррекции – совпадение или симметрия относительно плоскостей дисбалансов. Пример такого расположения приведен на рис. 1.1.
Рис. 1.1. Схема предпочтительного уравновешивания вала при описанном распределении дисбалансов по его длине:
1 – суммарный начальный дисбаланс, 2 – суммарный расчетный уравновешивающий дисбаланс
Расчет величин локальных дисбалансов I по результатам измерения эксцентриситетов поверхностей и масс участков (конечных элементов) валов проводится по следующей формуле:
I |
D |
D2l , |
(1.2) |
8 |
i |
i |
|
где Di – биение поверхности участка, Di |
– ее диаметр, l – ее |
||
длина, – плотность материала. |
|
|
16
Соответствующие рассчитанным дисбалансам уравновешивающие массы mk определяются согласно зависимости:
m |
|
D D l . |
(1.3) |
k |
4 |
i i i |
|
Алгоритм проектирования технологического процесса рас- четно-объемной подготовки вала к сборке включает последовательное проведение конструкторских работ (разделение вала на участки (конечные элементы) или разработка твердотельной модели вала, расчет координат центров масс участков и их плоскостей коррекции) и, исходя из принятого конструкторского решения, – проведение технологических работ [23, 24, 26].
Технологические работы выполняются с использованием программного обеспечения: исходные данные вводятся на каждую модель однократно, а результаты измерений – на каждый вал отдельно. Маркируются места всех посадочных поверхностей, диаметрально противоположные максимальному радиальному биению.
Заданная динамическая устойчивость валов и роторов с несовпадающими рабочими и балансировочными осями обеспечивается последующей коррекцией монтажных дисбалансов.
Для удлиненных роторов и роторов со скрещивающимися осями проводится многоплоскостная коррекция, для роторов с пересекающимися осями и распределенной массой – коррекция не менее чем по двум плоскостям.
Для присоединяемых роторов с пересекающимися осями, одной собственной опорой и консольным размещением колес коррекцию необходимо производить в одной плоскости.
После уравновешивания начального дисбаланса вала устанавливаются элементы подшипников, вследствие чего появляются монтажные дисбалансы, которые компенсируются заданными локальными остаточными дисбалансами (рис. 1.2).
Как отмечено ранее, на стадии проектирования определяются поверхности, в пределах которых не могут размещаться плоско-
17

сти коррекции. Для роторов с заранее заданными параметрами эксцентриситетов установки в пределах доступных поверхностей определяются плоскости коррекции и рассчитываются массы имитирующих грузов, компенсирующих монтажные дисбалансы.
Рис. 1.2. Схема предпочтительного распределения обеспеченных параметров дисбаланса: А – монтажные дисбалансы, Б – заданные локальные остаточные дисбалансы
Вместе с тем проводится двухплоскостная балансировка рабочих колес в оправках с коррекцией дисбалансов в местах их расположения, позволяющая обеспечить минимизацию остаточных векторов дисбалансов. При этом количество плоскостей коррекции должно быть равно количеству элементов колес, а также совпадать с положением плоскостей локальных дисбалансов этих элементов. На стадии проектирования необходимо определить положение центра массы элемента относительно торцовой поверхности ступицы [48].
Предпочтительное размещение плоскостей коррекции – боковые поверхности и внешние углы образующей колес (рис. 1.3). Предпочтительное направление коррекции колес – совпадающее с их локальными дисбалансами при съеме металла и диаметрально противоположное – при установке грузов.
После установки уравновешивающих и имитационных грузиков уравновешивание элемента при подготовке к сборке проводится по стандартной схеме двухплоскостной динамической балансировки [43].
18
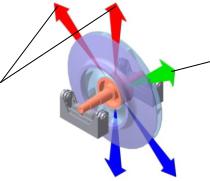
3
2
1
Рис. 1.3. Предпочтительное размещение дисбалансов на рабочем колесе: 1 – корректирующие дисбалансы, 2 – монтажные дисбалансы, 3 – допустимый остаточный дисбаланс
Заданная динамическая устойчивость роторов при сборке обеспечивается установкой отдельных элементов на ротор с диаметрально противоположно направленными дисбалансами:
–заранее заданный дисбаланс элемента совпадает по направлению с максимальным радиальным биением его внешней образующей и противоположно направлен относительно максимального радиального биения посадочной поверхности на валу (обеспечивается совмещением маркированных мест);
–заранее обеспеченный дисбаланс комплекта лопаток колеса турбины (компрессора) равен по величине и противоположно направлен относительно дисбаланса ротора, поставленного на сборку колес (заданный дисбаланс комплекта лопаток обеспечивается введением виртуального ступенчатого дисбаланса). Дисбаланс ротора состоит из собственного остаточного дисбаланса и дисбаланса, определяемого эксцентриситетом усредненной окружности гнезд лопаток.
Предпочтительное положение локальных и монтажных дисбалансов приведено на рис. 1.4.
Управляемая сборка ротора, обеспеченная подготовкой вала и всех элементов ротора, паспортизацией параметров остаточ-
19
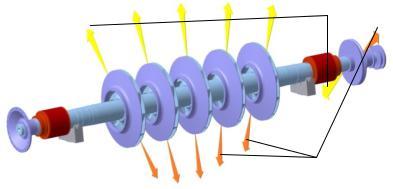
ных, заданных и локальных дисбалансов, обеспечивает взаимное уравновешивание дисбалансов в совпадающих или близких плоскостях [23, 24]. При этом на стадии проектирования необходимо определять положение плоскостей коррекции, массы и положение центров масс элементов, а также прогнозировать уровни дисбалансов и рассчитывать пределы уровней дисбалансов, исходя из конструкции роторов.
1
2
Рис. 1.4. Схема предпочтительного распределения дисбалансов при сборке ротора: 1 – локальные остаточные дисбалансы, 2 – монтажные дисбалансы
Алгоритм проектирования технологического процесса рас- четно-эксцентриситетной сборки ротора включает последовательное проведение конструкторских работ (разделение вала на участки (конечные элементы) или разработка твердотельной модели вала, расчет координат центров масс участков и их плоскостей коррекции) и, исходя их принятого конструкторского решения, – проведение технологических работ.
Технологические работы выполняются с использованием программного обеспечения, исходные данные вводятся на каждую модель однократно, а результаты измерения – на каждый ротор отдельно. Вместе с тем паспортизируются параметры остаточных дисбалансов роторов.
20