
книги / Экономика и организация производства на предприятиях машиностроения
..pdf
По сравнению с последовательным движением при параллель- но-последовательном движении достигается сокращение цикла Тт за счет частичного параллельного выполнения работ на смежных операциях, поэтому используется данный вид движения при условии большого числа изделий в партии n и большой продолжительности
операций tшт.
Производственный цикл Тц включает в себя кроме Тт другие составляющие: время естественных процессов и время перерывов нетехнологического цикла, внутри- и междусменных перерывов. Тогда длительность (в календарных днях)
Тц = |
1 |
[Т + Т |
] + Тест , |
|
|||
|
Sqf |
т м.о |
24 |
|
|
где Тт – длительность технологического цикла при соответствующем виде движения партии изделий, ч; Тм.о – продолжительность межоперационных перерывов; S – число смен в сутках на предприятии; q – длительность одной смены, ч; ƒ – коэффициент перевода рабочего времени в календарное; Тест – время естественных процессов, ч.
Коэффициент параллельности показывает сокращение дли-
тельности производственного цикла при параллельном движении по сравнению с последовательным:
Kпар = Тц.пар .
Тц.посл
10.2. Организация производственных процессов в пространстве. Производственная структура предприятия
Производственная структура машиностроительного предприятия – это состав цехов, производственных участков, вспомогательных и обслуживающих подразделений и формы их производственных взаимосвязей.
201
Цех – организационно обособленное подразделение предприятия, состоящее из ряда производственных и вспомогательных участков и обслуживающих звеньев. Цех выполняет операции, обусловленные характером кооперации труда внутри предприятия. На большинстве промышленных предприятий цех является их основной структурной единицей. Часть мелких и средних предприятий может быть построена по бесцеховой структуре. В этом случае предприятие делится непосредственно на производственные участки. Некоторые наиболее крупные предприятия в организационно-административном отношении строятся по корпусной системе на основе объединения под единым руководством ряда цехов, хозяйств.
Кцехам основного производства относятся цехи, изготавливающие основную продукцию предприятия. Это заготовительные (литейные, кузнечно-прессовые и др.), обрабатывающие (механической обработки деталей, холодной штамповки, термической и др.), сборочные цехи.
Квспомогательным относятся цехи, которые способствуют выпуску основной продукции, создавая условия для нормальной работы основных цехов. Это цехи: инструментальные, ремонтно-меха- нические, ремонтно-энергетические, ремонтно-строительные, модельные, штамповые и др.
Подсобные цехи осуществляют подготовку основных материаловдля основныхцехов, изготавливают тару для упаковки продукции.
Кобслуживающим хозяйствам производственного назначения относятся: складское хозяйство, транспортное хозяйство, санитарнотехническое хозяйство, ЦЗЛ.
Производственнаяструктурапредприятияприведенанарис. 10.2. Производственная структура предприятия определяет разделение труда между его цехами и обслуживающими хозяйствами, т.е. внутризаводскую специализацию и кооперирование производства. Специализация принимает следующие формы: технологическую,
предметную или предметно-технологическую.
При технологической специализации предприятие (цех, участок) выполняет определенные технологические процессы (литейные, сборочные, механические).
202
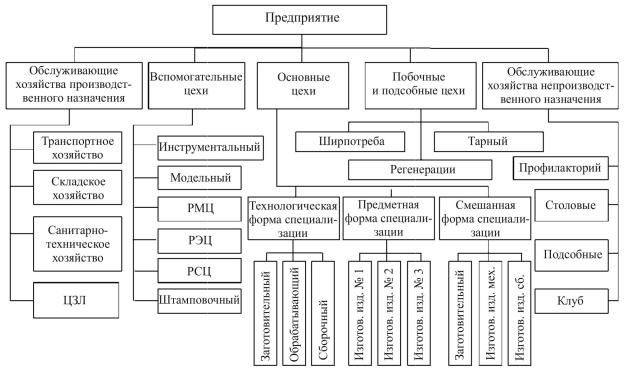
203
Рис. 10.2. Производственная структура предприятия
Пр е и м у щ е с т в а этой формы специализации: применяются наиболее прогрессивные и рациональные техпроцессы с более полной загрузкой оборудования, площадей, персонала, материалов.
Врезультате этого обеспечивается более низкая себестоимость изготовления. Засчет большей гибкости облегчается обновление продукции.
Н е д о с т а т к и : усложняется и удорожается кооперирование внутри предприятия и вне его; ограничивается персональная ответственность за результат деятельности по качеству, срокам поставки. Применяется такая специализация в единичном имелкосерийном производстве.
При предметной специализации на предприятии (в цехе, на участке) изготавливается законченное изделие, сборочная единица или деталь (шасси, валы, шестерни).
Пр е и м у щ е с т в а данной формы специализации: сокращается и упрощается внутреннее и внешнее кооперирование, повышается ответственность за качество и дисциплину поставок, облегчается внедрение поточных методов и комплексной механизации, сокращается длительность циклов, упрощается планирование, повышается производительность.
Н е д о с т а т к и : усложняется переход на новый выпуск продукции (требуется новое оборудование, перепланировка).
Применяется предметная специализация в массовом и серийном производстве. Предметная форма специализации имеет две
разновидности: п р е д м е т н о - з а м к н у т у ю ( обработка предметов труда относительно узкой номенклатуры с применением типовых технологических процессов) и п р е д м е т н о - г р у п - п о в у ю ( обработка предметов труда более широкой номенклатуры, родственных по конструктивно-технологическим и органи- зационно-плановым признакам).
204
10.3. Организационные формы производственных процессов
Непоточные формы организации производственных процессов
Выбор предприятием стратегии организации производства, ориентированной на процесс, наиболее распространен в машиностроении.
В условиях единичного, мелкосерийного и серийного производства применяются главным образом непоточные формы организации производственного процесса.
Широкая номенклатура выпуска и небольшое количество изготавливаемой продукции в пределах каждой номенклатурной позиции плана не позволяют обеспечить полную загрузку рабочих мест и их узкую специализацию.
Пути организации производственных процессов:
1.Групповое расположение оборудования (технологическая специализация), маршрутный технологический процесс.
2.Произвольное (свободное) расположение оборудования в условиях гибкого производства. Концентрация операций на одном рабочем месте приводит к сочетанию преимуществ технологической
ипредметной специализации.
3.Организация предметно-замкнутых участков (ПЗУ) с предметным принципом специализации. Возможно построение ПЗУ со свободным маршрутом движения изделий либо с однонаправленным (поточным) перемещением изделий по оборудованию (переходная форма от непоточной к поточной).
При групповом расположении оборудования количество потребного оборудования в каждой группе
nоб.расч = |
∑1i Qitij |
, |
ФдKв.н |
205
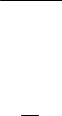
где Qi – программа запуска i-го изделия, шт; tij – норма времени на изготовление единицы i-го изделия по j-му виду работ; Kв.н – коэффициент выполнения норм времени по j-му виду работ; Фд – действительный фонд времени работы оборудования, ч.
Потребное количество оборудования сопоставляется с фактическим (принятым) количеством по данной группе, и рассчитыва-
ется коэффициент загрузки оборудования |
Kз = |
nоб.расч |
. |
n |
|||
|
|
об.факт(прин.) |
|
При построении производственного процесса по принципу концентрации операций количество оборудования
nоб = Qi (1 + Kп ) ,
qчФд
где Kп – коэффициент, учитывающий потери времени по организа- ционно-техническим причинам; qч – часовая (цикловая) производительность оборудования, шт/ч;
qч = Qц ,
Тц
гдеQц – количество изделий, обрабатываемых за цикл, шт.; Тц – длительностьциклаизготовления изделия, ч.
ПЗУ обеспечивают замкнутый цикл изготовления изделий. Номенклатура изделий для ПЗУ меньше, стабильность выпуска выше.
Организация поточного производства
Признаки, преимущества и классификация поточного производства. Поточное производство – форма организации производства, основанная на ритмичной повторяемости согласованных во времени технологических операций, выполняемых на специализированных рабочих местах, расположенных в последовательности технологического процесса изготовления одного или нескольких изделий.
206
Принципы организации производственных процессов при поточном производстве:
–прямоточность;
–непрерывность;
–параллельность;
–пропорциональность;
–ритмичность;
–гибкость.
Предпосылки организации поточного производства:
–стабильность номенклатуры изделий и повторяемость их выпуска;
–достаточнобольшойобъемпроизводстваоднотипныхизделий;
–высокий уровень отработанности конструкции и соответствие ее требованиям спроса;
–возможность целесообразного расчленения операций и разделения труда, эффективного использования рабочих мест;
–возможность применения переналаживаемых поточных линий со свободным ритмом и предметно-замкнутых участков.
Преимущества:
–высокий технологический и организационно-экономический уровень;
–применениепрогрессивных, ресурсосберегающих технологий;
–обеспечение высокого качества изделий с низкими издержками.
Классификация поточных линий:
1. По степени непрерывности процесса:
–механизированные и автоматизированные непрерывно-поточ- ныелинии(НПЛ);
–механизированные прерывно-поточные линии (прямоточные ППЛ);
–предметно-замкнутые участки.
2. По форме специализации изделий:
–с предметной специализацией;
–с подетальной специализацией;
–с технологической специализацией.
207
3. По количеству наименований изделий:
–однономенклатурные (массово-поточные);
–многономенклатурные (серийно-поточные).
4.По стабильности работы:
– непереналаживаемые;
– переналаживаемые.
5.По способу поддержания ритма:
– с регламентированным ритмом;
– со свободным ритмом.
6.По месту выполнения операций:
– на рабочем месте;
– на конвейере.
7.По способу транспортной связи:
– с жесткой связью;
– с гибкой связью.
Выбор организационных форм поточных линий определяется
тактом работы линий, степенью синхронизации операций техпроцесса, уровнем загрузки рабочих мест на линии.
Такт – промежуток времени между запуском (выпуском) смежных предметов труда на линии:
r = |
Ф′д |
, |
(10.2) |
|
|||
|
Qзап |
|
где Фд′ – действительный фонд времени работы линии с учетом по-
терь на регламентированные перерывы (в смену, сутки, месяц); Qзап – количество запускаемых на поточную линию предметов труда за тот же период времени, шт.
С учетом регламентированных перерывов (Тпер) и планируемого уровня потерь предметов труда по техническим причинам (брак, разрушающий контроль) такт
r = |
Тсм − Тпер |
|
, |
|||
|
+ |
|
а |
|
||
|
Qвып.см 1 |
|
|
|
||
|
100 |
|||||
|
|
|
|
208

где Тсм – продолжительность смены, мин; Тпер – время перерывов в смену, мин; Qвып.см – сменная программа выпуска, шт.; а – процент потерь по техническим причинам. В случае, когда передача по операциям осуществляется транспортными партиями, рассчитывается ритм поточной линии:
R = rp,
где р – величина транспортной (передаточной) партии.
Непрерывно-поточные линии (НПЛ) используются при полной синхронизации процесса в массовом и крупносерийном производстве. Обеспечивается непрерывная загрузка оборудования и рабочих.
Синхронизация операций – деление техпроцесса на операции, по продолжительности равные или кратные такту потока. Способы синхронизации операций: дифференциация, концентрация, комбинирование.
Необходимое число рабочих мест (единиц оборудования) для каждой операции
Срi расч = |
tштi |
, |
(10.3) |
|
|||
|
r |
|
где tштi – штучное время на i-й операции, мин.
При неполной синхронизации Срi расч не равно целому числу, поэтому его увеличивают до ближайшего целого числа и определяют Срi прин (принятое).
Далее рассчитывают коэффициент загрузки рабочих мест на каждой операции:
K |
зi |
= |
Cp расч , |
|
|
|
Ср прин |
|
и средний коэффициент загрузки рабочих мест на поточной линии:
Kзiср = ∑m Cpi расч . 1 Cpi прин
209
В массовом производстве Kз.ср ≥ 80…85 %, в серийно-поточ- ном – 70…75 %. Kз не может быть > 1.
Распределительный конвейер – линия, оснащенная механиче-
ским транспортом, адресующая предметы труда по рабочим местам. Сама работа производится на стационарных рабочих местах у конвейера.
Для таких конвейеров необходимо определить шаг конвейера (l0) – расстояние между осями двух рядом расположенных предметов труда на конвейере, м. Шаг конвейера l0 определяется габаритами изделия, корректируется с учетом допустимой скорости конвейера (от 0,1 до 4,0 м/мин):
v = |
l0 |
, |
(10.4) |
к |
r |
|
где vк – скорость движения конвейера, м/мин.
Длина рабочей части конвейера (Lp.к) определяется на основе его планировки и вариантов расположения оборудования (вдоль конвейера, шахматный порядок промежутков между рабочими местами для обслуживания).
В общем случае
|
|
|
|
|
|
m |
|
|
|
|
|
|
Lp.к = l0 ∑Cpi прин. |
(10.5) |
|||||
|
|
|
|
|
|
1 |
|
|
|
Длина формовочно-заливочно-выбивного конвейера |
|||||||||
|
Lр.к = Lформ + Lзал + Lохл + Lвыб, |
||||||||
где Lформ – длина формовочного участка, м; |
|
||||||||
|
|
|
|
|
|
m |
|
||
|
|
|
Lформ = ∑Cpl0 . |
|
|||||
|
|
|
|
|
|
1 |
|
|
|
Lформ определяется по габаритам формовочных машин. |
|||||||||
Длина участка заливки |
|
|
|
|
|
||||
|
t |
шт.1 |
t |
шт.1 |
+ t |
шт.2 |
|
|
|
Lзал = |
|
vк + |
|
|
vк − l0 |
(Чф −1), |
|||
|
60 |
|
|
60 |
|
||||
|
|
|
|
|
|
|
210