
книги / Чугуны. Структура и термическая обработка
.pdfТаблица 31
Механические свойства чугунов ЧВГ, КЧ и ЧШГ
Тип чугуна |
Составматрицы, % |
В, |
0,2, |
, % |
HB |
+20 C |
||
KCV |
2 |
, |
||||||
|
|
МПа |
МПа |
|
|
кДж/м |
|
|
|
|
|
|
|
|
|
|
|
Ф – ЧВГ |
95 Ф+ 5 П |
332 |
257 |
5,6 |
146 |
68 |
|
|
Ф – П – ЧВГ |
40 Ф+ 60 П |
400 |
328 |
1,8 |
184 |
52 |
|
|
Ф – КЧ |
100Ф |
333 |
198 |
7,7 |
125 |
100 |
|
|
Ф – КЧ |
(95–99)Ф + (1–5) П |
374 |
255 |
6,6 |
137 |
126 |
|
|
Ф – ЧШГ |
100Ф |
415 |
277 |
20,4 |
152 |
137 |
|
|
Ф – П – ЧШГ |
65 Ф+ 35 П |
528 |
334 |
13,0 |
180 |
56 |
|
|
БН – ЧШГ |
35 А + 65 БН* |
800 |
720 |
2,6 |
209 |
90 |
|
|
БН – ЧШГ |
(16–17)А+ (83–84) БН |
1467 |
1413 |
1,1 |
466 |
41 |
|
|
Примечание. * Бейнит нижний.
Ударная вязкость ЧВГ снижается с увеличением СЭ и количества перлита в структуре матрицы и линейно возрастает с увеличением в структуре матрицы количества ШГ. Температура конца вязко-хрупкого перехода ТВ-Х составляет для ЧВГ в литом состоянии –55 C, а после нормализации и отжига соответственно –75 и –115 C. Содержание П ≈ 40 % в структуре матрицы считается критическим, так как при большем проценте П существенно возрастает ТВ-Х и, соответственно, повышается склонность к хрупкому разрушению.
По эксплуатационным свойствам ЧВГ практически не уступает (например, герметичность, коррозионная стойкость) или уступает незначительно (например, по окалиностойкости на 12–16 %) ЧШГ, лишь сопротивление износу у ЧВГ заметно ниже, чем у ЧШГ, но значительно выше, чем у ЧПГ.
При изготовлении деталей в общем машиностроении 90–95 % занимает обработка резанием, поэтому важно сравнить разные чугуны по обрабатываемости резанием. Это свойство у ЧВГ значительно лучше, чем у ЧШГ. Сравнение с ЧШГ и КЧ, а также рекомендуемые режимы точения, фрезерования, сверления, обработки абразивными кругами (плоское, круглое, внутреннее шлифование), приведены в справочной литературе.
51
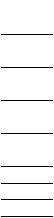
4.3. Ковкие чугуны
Ковким называют чугун, который получают из белого чугуна путем длительного графитизирующего отжига тонкостенной отливки (толщина стенки не более 50 мм). При отжиге происходит распад цементита и выделение свободного углерода – графита («углерода отжига») в компактной форме. ГОСТ 3443–85 дает три разновидности графита в ковких чугунах: нитевидная (КГ ф1), хлопьевидная (КГ ф2), компактная (КГ ф3). Наиболее характерна хлопьевидная форма. Марки и зарубежные аналоги ковких чугунов приведены в табл. 32, сравнение механических свойств ковкого чугуна с другими конструкционными материалами – в табл. 33 2, 12 . Следовательно, КЧ имеет достаточно высокую прочность, приличную ударную вязкость, более высокое, чем для стали, отношение предела текучести ( 0,2) к пределу прочности ( В) при растяжении (60–80 %) и меньшую по сравнению со сталью чувствительность к надрезам. Следует отметить хорошие литейные свойства КЧ.
Таблица 32
Ковкие чугуны и их зарубежные аналоги
СНГ |
США |
Германия |
Япония |
HB·10–1, |
Метал. |
|
МПа |
основа |
|||||
|
|
|
|
|||
КЧ 30-6 |
– |
– |
FCMB 270 |
163 |
|
|
КЧ 33-8 |
22010 |
GTW-35-04 |
FCMB 310 |
163 |
Ф + (3–10)% П |
|
КЧ 35-10 |
М 3210 |
GTS-35-10 |
FCMB 340 |
163 |
||
|
||||||
КЧ 37-12 |
24018 |
GTW-S-38-12 |
FCMB 360 |
163 |
|
|
КЧ 45-7 |
М 4504 |
GTS-45-06 |
FCMWP 670 |
241 |
|
|
КЧ 50-5 |
М 5003 |
GTV-45-07 |
FCMWP 490 |
241 |
|
|
КЧ 55-4 |
М 5503 |
GTS-55-04 |
FCMWP 540 |
269 |
|
|
КЧ 60-3 |
– |
– |
FCMP 590 |
269 |
П+ (0–20) % Ф |
|
КЧ 65-3 |
М 7002 |
GTS-65-02 |
– |
269 |
|
|
КЧ 70-2 |
– |
GTS-70-02 |
FCMP 690 |
– |
|
|
КЧ 80-1,5 |
М 8501 |
– |
– |
– |
|
52
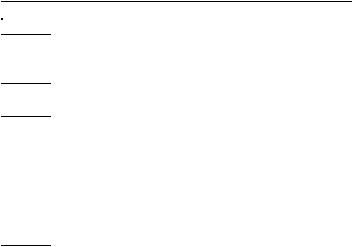
Таблица 33
Основные свойства ковкого чугуна в сравнении с другими материалами
Показатель |
Серый |
Стальконст- |
Стальлитая |
Ковкий |
Высоко- |
рукционная |
низкоугле- |
прочный |
|||
свойств |
чугун |
углеродистая |
чугун |
||
|
|
горячекатаная |
родистая |
|
чугун |
|
|
|
|
|
|
|
|
|
|
|
|
В, МПа |
120–380 |
320–670 |
390–460 |
300–750 |
400–800 |
, % |
0,25–0,8 |
8–27 |
19–25 |
1,0–18,0 |
1,0–18,0 |
HB |
163–241 |
131–269 |
121–143 |
110–273 |
156–269 |
0,2, МПа |
Нет |
180–390 |
200–300 |
220–500 |
300–420 |
KC, кГм/мм2 |
0,2–1,0 |
4–8 |
6–12 |
0,5–20,0 |
1,5–3,0 |
изг, МПа |
0,4–0,5 вр |
– |
– |
0,4–0,5 вр |
0,35–0,3 вр |
Химический состав и механические свойства ковких чугунов, согласно ГОСТ 1215–79, приведены в табл. 34, 35.
Таблица 34
Химический состав ковких чугунов
Марка |
|
|
Содержание элементов, % |
|
|
|||
чугуна |
C |
Si |
Si + C |
Mn |
P |
S |
Cr |
|
|
|
|
Ферритный |
класс |
|
|
|
|
КЧ 30-6 |
2,6–2,9 |
1,0–1,6 |
3,7–4,2 |
0,4–0,6 |
0,18 |
0,02 |
0,08 |
|
КЧ 33-8 |
||||||||
|
|
|
|
|
|
|
||
КЧ 35-10 |
2,5–2,8 |
1,1–1,3 |
3,6–4,0 |
0,4–0,6 |
0,12 |
0,02 |
0,06 |
|
КЧ 37-12 |
2,4–2,7 |
1,2–1,4 |
3,6–4,0 |
0,2–0,4 |
0,12 |
0,08 |
0,05 |
|
|
|
|
Перлитный |
класс |
|
|
|
|
КЧ 45-7 |
|
|
|
|
|
|
|
|
КЧ 50-6 |
2,5–2,8 |
1,1–1,3 |
3,6–3,9 |
0,3–1,0 |
0,10 |
0,02 |
0,08 |
|
КЧ 55-4 |
||||||||
|
|
|
|
|
|
|
||
КЧ 60-3 |
|
|
|
|
|
|
|
|
|
|
|
|
|
|
|
|
|
КЧ 65-3 |
|
|
|
|
|
|
|
|
КЧ 70-2 |
2,4–2,7 |
1,2–1,4 |
3,6–3,9 |
0,3–1,0 |
0,10 |
0,05 |
0,08 |
|
КЧ 80-1,5 |
|
|
|
|
|
|
|
53
|
|
|
Таблица 35 |
Механические свойства ковких чугунов |
|||
|
|
|
|
Марка чугуна |
В, МПа |
, % |
HB |
КЧ 30-6 |
294 |
6 |
100–163 |
КЧ 33-8 |
323 |
8 |
100–163 |
КЧ 35-10 |
333 |
10 |
100–163 |
КЧ 37-12 |
362 |
12 |
110–163 |
КЧ 45-7 |
441 |
7* |
150–207 |
КЧ 50-5 |
490 |
5* |
170–230 |
КЧ 55-4 |
539 |
4* |
192–241 |
КЧ 60-3 |
588 |
3 |
200–259 |
КЧ 65-3 |
637 |
3 |
212–269 |
КЧ 70-2 |
686 |
2 |
241–285 |
КЧ 80-1,5 |
784 |
1,5 |
270–320 |
Примечание. *По согласованию с потребителем допускается понижение на 1 %.
Для обеспечения комплекса свойств прочность/пластичность в готовой отливке необходимо задать и обеспечить такое содержание углерода и кремния, чтобы при заданной толщине стенки отливки и массы отливки чугун после кристаллизации до отжига имел структуру доэвтектического белого чугуна без включений пластинчатого графита. Если в литой структуре появится включение ПГ, то при последующем отжиге будет формироваться не компактный, а пластинчатый графит (окончательный брак). Ввиду этого отливки ковкого чугуна всегда имеют ограничения по толщине (не более 50 мм) и массе (не более 250 кг), кроме того, при конструировании должны быть обеспечены плавные переходы сечений и минимальная разностенность. Для получения чугуна высоких марок необходимо обеспечивать низкое содержание углерода (2,3–2,9 %) и количество кремния в пределах 0,7–1,4 %. При меньшей концентрации Si снижается отжигаемость чугуна, т.е. затрудняется второй этап получения КЧ (отжиг исходного белого чугуна), концентрация выше верхнего предела может привести к выделению графита при кристаллизации отливки.
54
Основные компоненты состава влияют следующим образом. Марганец (Mn) необходим в количестве 1,7 S плюс 0,1–0,3 MnS – для связывания серы в тугоплавкий сульфид. Если необходимое соотношение Mn и S не выдержано, то как марганец, так и сера замедляют в процессе отжига графитизацию при эвтектоидном превращении (вторая стадия графитизации). Оптимальным для ферритного чугуна считают отношение Mn/S = 3, а для перлитного Mn/S = 0,95…1,0. Высокосернистые перлит-
ные КЧ (0,25–0,4 % Mn и 0,3–0,55 % S) имеют высокую изно-
состойкость при абразивном износе.
Содержание фосфора должно быть ≤ 0,12 %, так как уже при 0,15–0,20 % Р в структуре при кристаллизации образуется много фосфидной эвтектики, которая сильно охрупчивает чугун. Для повышения пластичности и особенно для КЧ, работающих при повышенных динамических нагрузках, концентрация фосфора допускается не более 0,05 %.
Хром, как карбидообразующий элемент, стабилизирует цементит и тормозит графитизацию при отжиге как на первом, так и на втором этапе. Рекомендуемое содержание Cr 0,06–0,08 %. При большем содержании Cr необходимо использовать при выплавке комплексные модификаторы, содержащие азот для образования нитридов хрома, что снижает отрицательное влияние Cr на графитизацию. Сложность модифицирования КЧ в том, что необходимо избежать графитизации при выплавке и затвердевании отливки и способствовать графитизации, увеличить скорость графитизации при отжиге. Ввиду этого модифицирование КЧ требует точного соблюдения режима модифицирования и точного соотношения стабилизирующих (например, Bi, Te) и графитизирующих (Al, B, Ti) модификаторов. Первые предотвращают графитизацию при охлаждении толстостенных отливок, вторые ускоряют графитизацию при отжиге, что сокращает продолжительность отжига и позволяет получать (в зависимости от режимов отжига) различную структуру металлической основы, т.е. ферритные или перлитные КЧ. Оба типа модификаторов
55
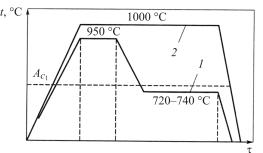
применяют совместно, используя лигатуры, содержащие различные элементы в определенных сочетаниях.
Таким образом, структура и свойства КЧ формируются
вдва этапа: 1 – получение отливки со структурой белого чугуна; 2 – отжиг данной отливки. В зависимости от требований к различным маркам КЧ различают отжиг графитизирующий и обезуглероживающий. В результате графитизирующего отжига получают черносердечный чугун (излом бархатистый темно-се- рый), структура матрицы – феррит, перлит или феррито-перлит. Результат обезуглероживающего отжига – чугун белосердечный (блестящий светлый излом) со сложным изменением структуры металлической основы от феррита на поверхности к перлиту
вцентре отливки, причем в середине отливки графит находится
вокружении феррита.
4.3.1. Графитизирующий отжиг на ферритный КЧ
Процесс ведут в нейтральной или слабоокислительной среде с использованием защитных атмосфер, с нагревом на 950–1000 C. Режим выдержки и последующего охлаждения зависит от требуемой структуры и свойств для данной марки чугуна. Общая схема режима обработки белого чугуна на ковкий и схема образования структур при графитизации приведены на рис. 18, 19. Типовой режим отжига отливок на ферритный КЧ приведен на рис. 20.
Рис. 18. График режима отжига белого чугуна на ковкий черносердечный (1) и белосердечный (2)
56
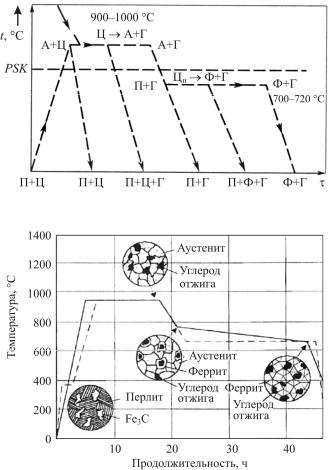
Рис. 19. Схема образования структур при графитизации
Рис. 20. Типовой режим отжига отливок на ферритный ковкий чугун
Возможный конкретный режим и агрегат для его реализации приведены на рис. 21 15 . Агрегат состоит из двух толкательных печей 1 и 2 (типа СТЗ) и промежуточной камеры 3 с перетаскивателем, герметически изолированной от окружающего пространства. Движение поддонов с деталями по печи обеспечивается толкателем 4. Загрузка-выгрузка печей боковая через спе-
57
циальные камеры, позволяющие обеспечивать работу печей с контролируемой атмосферой. Применяют эндо- и экзоатмосферы КГ-ВО, ПСО-06, ПСО-09. Камеры перед загрузкой и выгрузкой продувают контролируемой атмосферой. Отливки размещают на литых поддонах размером 600 850 мм. Масса деталей на поддоне 290 кг, масса поддона 70–80 кг. Масса поддона от массы загруженных из него деталей не должна превышать 25–30 %. Печи двухрядные, темп толкания при данном режиме 1 ч, производительность агрегата 580 кг/ч. Загрузку и выгрузку производят попарно с помощью рольганга, вспомогательных толкателя и вытаскивателя. Все механизмы агрегата работают от гидравлических устройств. Электродвигатели 5 для обслуживания насосов, канал 6 для маслопроводов находятся в подвале 7. Все механизмы агрегата работают в автоматическом режиме. Для поддержания температурного режима в агрегате разработана автоматическая система регулирования (АСР) технологических параметров.
Печи нагревают литыми нихромовыми нагревателями (подовые и сводовые), которые могут быть заменены газовыми радиационными трубами.
В первой печи отливки нагреваются до 1000 oC (зона 1, 2), выдерживаются длительное время (8 ч, зона 3) для протекания первой стадии графитизации (графитизация эвтектического цементита), а затем в четвертой зоне отливки охлаждаются до 780 oC. Охлаждение обеспечено установкой после промежуточного сводика между третьей и четвертой зонами специальных труб для подачи холодного воздуха. Охлажденные до 780 oC отливки передаются в промежуточную камеру 3, откуда с помощью вытаскивателя – во вторую печь. В зоне 5 и 6 печи 2 отливки медленно охлаждаются (20 ч) до t = 700 oC; при этом происходит эвтектоидное превращение и обеспечивается вторая стадия графитизации, т.е. распад эвтектоидного цементита – Ц → (Ф + Г). Для качественной графитизации охлаждение должно быть со скоростью не более 5 oС/ч.
58
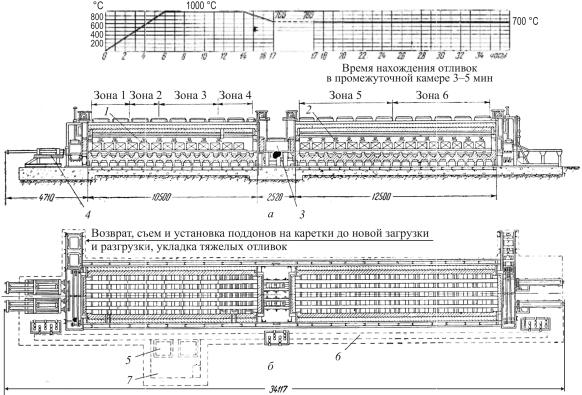
59
Рис. 21. Агрегат для отжига на ковкий чугун: а– график режима нагрева и разрез печи; б – вид печи сверху
Данный агрегат рассчитан на обработку 12–14 т литья в сутки. Обрабатывать можно детали различной массы и размеров. Для мелких деталей предусмотрены составные поддоны. Такой поддон состоит из собственно поддона и второй части – обечайки или ящика без дна, который специальными приливами (шипами) устанавливается в гнезда поддона и с помощью клиньев удерживается на нем.
Таким образом, отжиг на ферритный КЧ состоит из следующих пяти этапов (см. рис. 18, режим 1):
1.Нагрев исходного литого белого чугуна со структурой
П+ Ц + Л (П + Ц) до температуры 950 ± 20 oC, т.е. значительно
выше температуры эвтектоидного превращения Aс1. При нагреве
перлит превращается в аустенит, частично растворяется избыточный Ц в аустените и начинается образование центров графитизации. Для более полного протекания процессов нагрев должен быть медленным со скоростью не более 50 С/ч. Возможно применение нагрева с остановкой при t = 300…400 oС (левая пунктирная линия на графике рис. 20) в течение 3–5 ч, что способствует увеличению числа центров графитизации (рис. 22), особенно для чугуна, модифицированного небольшим количеством Al (0,05–0,08 %) 4, 6, 9 . Образование центров графитизации происходит гетерогенно вследствие неоднородности состава аустенита и нарушения сплошности матрицы (усадочные и диффузионные микропоры, колонии вакансий и прочее, т.е. любые микронесплошности). При низких температурах микрополости могут формироваться вследствие различия коэффициентов объемных изменений матрицы и любого включения. Центрами графитизации могут являться и те скопления атомов углерода, которые возникли при эвтектической кристаллизации белого чугуна.
2. Выдержка (6–12 ч), необходимая для протекания и полного завершения первой стадии графитизации, т.е. распада цементита ледебурита с образованием аустенита, насыщенного углеродом, и компактного графита (углерода отжига).
60