
книги / Чугуны. Структура и термическая обработка
.pdf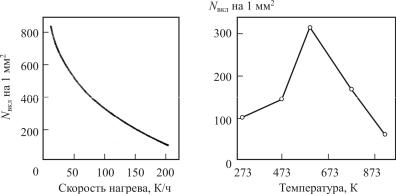
а б
Рис. 22. Зависимость числа центров кристаллизации: а – от средней скорости нагрева; б – от температуры предварительной выдержки
3. Промежуточное охлаждение до температуры 760–740 oС, при котором происходит выделение углерода из аустенита и рост включений графита.
4. На этом этапе происходит перлитное превращение – А → П (Ф + Ц) и идет вторая стадия графитизации, т.е. разлагается эвтектоидный цементит (Ц → Ф + Г). Технологически возможно два решения: либо медленное непрерывное охлаждение со скоростью не более 5 oС/ч во всем интервале температур эвтектоидного превращения (до t = 700 ± 20 oС), либо изотермическая выдержка при t = 720…740 oС (пунктирная линия на графике рис. 20) до полной графитизации цементита перлита (8–15 ч). Более надежен для получения чисто ферритной структуры матрицы вариант медленного охлаждения, при котором выделение графита происходит непосредственно из аустенита согласно стабильной диаграмме Fe–C. Во втором варианте при быстром охлаждении до температуры изотермы и недостаточной выдержке при этой температуре в структуре КЧ может присутствовать перлит.
61
5. Этап окончательного охлаждения отливок. В зависимости от конкретной марки чугуна, геометрии отливок, характера загрузки и оборудования, на котором проводили отжиг, охлаждение с температуры изотермы сразу на воздухе либо с печью до t = 600…550 oС, затем на воздухе.
Продолжительность первой и второй стадий графитизации, размеры и распределение образующегося углерода отжига существенно зависят от химического состава чугуна, особенно от содержания C + Si, сечения и массы отливок, первичной структуры, образовавшейся при затвердевании отливки. Общий цикл отжига может доходить до 70–80 ч.
4.3.2. Графитизирующий отжиг на перлитный КЧ
Этот отжиг проводят с нагревом на t = 1000…1050 oС. После первой стадии графитизации необходимо обеспечить ускоренное охлаждение отливок (см. рис. 18, режим 2) для получения перлита. Изменяя условия охлаждения и оптимизируя химический состав чугуна, можно получать разную структуру матрицы. Так, в чугунах с пониженным процентом Si (способствует графитизации) или с повышенным процентом Mn (способствует отбелу) можно подавить склонность чугуна к графитизации на второй стадии, т.е. обеспечить по простым режимам получение перлитной структуры металлической основы. Увеличение содержания серы до 0,3–0,5 % при соотношении Mn/S = 1 также способствует получению перлитной структуры. Как известно, П зернистый обладает лучшим комплексом свойств, чем пластинчатый. КЧ со структурой зернистого перлита можно получить, используя отжиг по сфероидизирующему режиму или дополнительной термической обработкой ферритного КЧ.
При сфероидизирующем отжиге после выдержки на первой стадии графитизации применяют медленное промежуточное охлаждение до 850 oС, затем ускоренное (со скоростью не менее 100 oС/ч) охлаждение до 650 oС и выдержку при этой темпера-
62
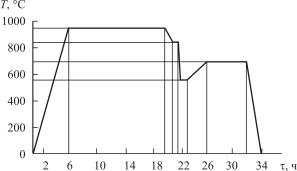
туре. В результате получают КЧ с глобулярным цементитом и хлопьевидным Г. Более надежно зернистый перлит получают при отжиге по режиму, приведенному на рис. 23. Процессы, протекающие на разных стадиях охлаждения, аналогичны описанным ранее.
Рис. 23. Режим отжига на перлитный ковкий чугун
Дополнительная термическая обработка, позволяющая получить перлитный КЧ – это закалка ферритного КЧ с нагревом на 930–980 oС, охлаждением в масло и последующим отпуском на требуемую твердость или нормализацией с отпуском или без отпуска. В результате получают перлитные чугуны с различной формой и степенью дисперсности перлита.
4.3.3. Обезуглероживающий отжиг
Цель такого отжига – получить белосердечный КЧ (светлый блестящий излом) с малым количеством углерода отжига и неоднородной структурой по сечению отливки. Наружный полностью обезуглероженный слой (несколько миллиметров) имеет структуру феррита, далее содержание углерода повышается и появляются участки перлита, количество которого к центру отливки увеличивается. Структура в середине отливки – перлит и графит, окруженный ферритом. Содержание углерода в центре
63
отливки меньше, чем в исходном белом чугуне. Такой чугун является единственным конструкционным чугуном, который применяют для сварно-литых конструкций, так как он обладает хорошей свариваемостью и не требует термической обработки после сварки.
Обезуглероживающий отжиг проводят в окислительной атмосфере с нагревом на 1000–1050 oС и выдержкой, которая зависит от состава чугуна, толщины стенки отливки, необходимой степени обезуглероживания и среды, в которой ведут процесс. Время обычно составляет 10 ч на 1 мм толщины стенки. Скорость охлаждения до температуры выгрузки 650 oС должна быть 20–40 С/ч. Общее время цикла минимум 100–110 ч. Процесс ведут либо при засыпке отливок смесью исходной руды с песком в контейнерах, либо в газовой среде, что более экономично. Рекомендуемый состав газа: 8 % CO2, 26–28 % CO, 24–26 % H2, 12–14 % H2O 9 . Скорость окисления и обезуглероживания зависит от количества CO2, H2 и H2O в атмосфере печи, содержания углерода на поверхности отливок и скорости диффузии углерода от центра отливки к поверхности. Обезуглероживанию активно способствуют пары воды в атмосфере печи. Исходный чугун должен иметь пониженное содержание Si (0,4–0,8 %), способствующего графитизации, так как переход углерода в твердый раствор из графита более затруднен и длителен, чем из цементита. Для предотвращения графитизации также повышают до 0,15–0,25 % содержание серы. Рекомендуемое содержание фосфора и хрома менее 0,1 и 0,05 % соответственно. Рекомендуемое количество углерода 2,8–3,4 %.
В окислительной среде при высоких температурах происходит непрерывное окисление и обезуглероживание поверхности (без графитизации), что вызывает диффузию углерода из центра к поверхности, и при последующем медленном охлаждении формируется описанная ранее структура отливки
(рис. 24).
64
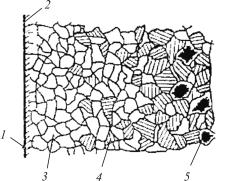
Рис. 24. Схема структуры отливки из белосердечного КЧ: 1 – поверхность отливки; 2 – поверхностное окисление; 3 – феррит; 4 – перлит; 5 – графит
4.3.4. Термическая обработка ковкого чугуна
Выше описаны процессы отжига, которые позволяют получить КЧ различных марок с различной вторичной структурой с широким интервалом механических свойств. Дальнейшее изменение структуры металлической основы для повышения прочности и износостойкости получают за счет последующей термической обработки. Это может быть нормализация, улучшение, старение, поверхностное упрочнение путем поверхностной закалки или химико-термической обработки (азотирование, сульфидирование и др.). Например, после закалки ферритного КЧ с нагревом на 720–750 oС, охлаждения в воде и естественного старения в течение четырех суток получают следующие свойства: В = 410…480 МПа, 0,2 = 340…370 МПа при относительном удлинении δ = 8…10 % 9 .
Поверхностную закалку для ферритного и перлитного КЧ проводят с нагревом ТВЧ до температуры 1050–1100 oС 75–125 с, охлаждением в воде с последующим отпуском. Твердость обработанной поверхности 45–55 HRC. Таким образом, КЧ по разнообразию свойств сравним с ВЧ и углеродистой сталью, что наглядно
65
демонстрирует табл. 33. Кроме того, КЧ имеет хорошие антифрикционные свойства, малую чувствительность к влиянию низких температур, т.е. удовлетворительно работает при пониженных температурах. Все это обусловило широкое применение КЧ в разнообразных условиях эксплуатации как по виду напряженного состояния, так и по воздействию внешней среды для ответственных деталей в различных отраслях общего машиностроения (табл. 36).
|
Таблица 36 |
||
Области применения ковкого чугуна |
|
||
|
|
|
|
Область примене- |
|
Структура |
|
Примерная номенклатура деталей |
металлической |
||
ния |
|||
|
основы |
||
|
|
||
Сельскохозяйствен- |
Муфты, втулки,корончатыегайки, буксы, |
Ферритная и |
|
ное итракторное |
храповики, скобы, кронштейны, звездочкии |
перлитная |
|
машиностроение |
звеньяприводных цепей,вилкикарданных |
|
|
|
валов, ступицы и др. |
|
|
Автомобильное |
Задниймост, картер ичашки дифференциала, |
|
|
машиностроение |
рычаги, втулки, тормозные колодки, ступи- |
|
|
|
цы, коленчатые валы |
|
|
Текстильное маши- |
Сновальныеинабойныекруги,крючки,звенья |
Ферритная |
|
ностроение |
приводныхцепей,шестерни,подшипники |
|
|
Судо-, котло-, |
Головки, хомутики, гайки, глушители, порш- |
|
|
вагоно-, мото- и |
ни, клапаны и другие деталивоздушныхтор- |
|
|
дизелестроение |
мозов, подшипники, кронштейны, тяговые |
|
|
|
сцепления, клинья, кольца, крышки, скобы |
|
|
Электропромыш- |
Крючья ишапки изоляторов,клеммы, рас- |
|
|
ленность |
пределительные ящики, держатели проводов, |
|
|
|
частимоторов, коромысла |
|
|
Санитарно-техни- |
Соединительные ящики: угольники, отводы, |
|
|
ческое, пожарное и |
муфты, фланцы, ниппели, гайки, детали зам- |
|
|
строительное обо- |
ков, дверные, оконные и другие приборы |
|
|
рудование |
|
|
|
Производствоинст- |
Гаечные и разводные ключи, ручки, цилинд- |
|
|
румента имедицин- |
ры, крышки, подкладки |
|
|
ского оборудования |
|
|
|
Оборудование раз- |
Деталишвейныхмашин,токарныхстанков, |
Ферритная и |
|
личного назначения |
насосов,формовочныхмашин,дробеметных |
перлитная |
|
|
барабанов,дорожныхистроительныхмашин, |
|
|
|
аэраторов,автопогрузчиков,конвейеров, |
|
|
|
транспортеров,прессов,редукторовит.д. |
|
66
5. ТЕРМИЧЕСКАЯ ОБРАБОТКА ЧУГУНА
Все структурно-чувствительные свойства чугуна, как и свойства стали, можно существенно изменить путем термической обработки. В чугунах при нагреве-охлаждении протекают такие же фазовые превращения, как и в стали, с некоторым осложнением вследствие наличия графита в структуре чугуна. Следовательно, основные виды термической обработки аналогичны обработке стали 12, 13, 16 .
Цели термической обработки:
снятие внутренних напряжений и стабилизация размеров отливки;
исправление отбела (дефект отливки серого чугуна);
снижение твердости и улучшение обрабатываемости ре-
занием;
повышение механических и служебных (эксплуатационных) свойств – износостойкости в первую очередь.
Классификация основных видов термической обработки и решаемые задачи приведены в табл. 37.
Как следует из таблицы, первые три цели достигаются за счет различных видов отжига, последняя цель – закалкой с последующим отпуском или нормализацией. Существенное изменение износостойкости, кроме поверхностной закалки, обеспечивается применением химико-термической обработки (ХТО), основные виды которой будут рассмотрены далее.
5.1. Химико-термическая обработка чугуна
ХТО чугунных отливок, как и ХТО стальных деталей, проводят с целью изменения структуры и свойств поверхности без изменения структуры и свойств сердцевины (центра) детали. При ХТО чугуна графитная структура практически не
67
меняется, все изменения происходят в структуре металлической основы (матрицы). Эти изменения аналогичны происходящим в сталях.
Для чугунов применяют как насыщение неметаллами (азотирование, сульфидирование), так и диффузионную металлизацию – насыщение металлами (алитирование, хромирование). Основное назначение применяемых видов ХТО и рекомендации по технологии процессов для отливок из серого чугуна приведены в табл. 38.
Как видно из таблицы, практически все приведенные обработки позволяют повысить износостойкость поверхности детали, хотя основное назначение каждой обработки индивидуально. Формирование слоя и физико-химической основы процессов такие же, как в сталях: получение насыщающего элемента в атомарном состоянии; осаждение на поверхности и «схватывание» с поверхностью; диффузия, т.е. формирование слоя вглубь. Основные технологические параметры процессов ХТО: температура, время, активность насыщающей среды. Процессы можно вести в твердой, газовой и жидкой среде. Для всех процессов требуется качественная подготовка обрабатываемой поверхности (очистка, обезвоживание).
Азотирование
Основное назначение азотирования – повышение износостойкости за счет формирования в поверхностном слое соединений азота с легирующими элементами (Al, Cr и др.) – нитридов. Устойчивость нитридов возрастает в следующей последо-
вательности: Ni → Co → Fe → Mn → Cr → Mo → W → Nb → V → Ti → Zr 17–19 . Для обычных чугунов основное практическое значение имеют нитриды алюминия AlN, кремния Si3N4, магния Mg3N2.
68
|
|
Классификация видов термической обработки серого чугуна |
Таблица 37 |
||||||
|
|
|
|||||||
|
|
|
|
|
|
|
|
|
|
|
Наименование |
Основныетехнологическиепараметрыпроцесса |
Структурные, |
Исходная |
|
Назначение |
|||
|
|
|
|
|
структура |
Конечная |
|||
|
термической |
Скорость |
Темпе- |
Время |
|
фазовые |
химико-термической |
||
|
обработки |
нагрева |
ратура |
выдержки |
Охлаждение |
превращения |
металличе- |
структура |
обработки |
|
|
|
нагрева, С |
|
|
|
скойосновы |
|
|
|
1 |
2 |
3 |
4 |
5 |
6 |
7 |
8 |
9 |
|
Отжигнизко- |
70–100 С/ч |
500–600, |
В зависимости |
Медленное |
Нет |
Перлито- |
Практиче- |
Снятие внутренних |
|
температурный |
|
легирован- |
отконфигура- |
с печью |
|
ферритная, |
скине |
напряжений, повы- |
|
(искусственное |
|
ныйчугун |
ции детали, |
20–50 С/чдо |
|
перлитная |
изменяется |
шениевязкости, |
|
старение) |
|
до630 |
отгабаритов |
температуры |
|
|
|
стабилизацияразме- |
|
|
|
|
отливки |
250 С |
|
|
|
ровдетали, сниже- |
|
|
|
|
(2–8 ч) |
|
|
|
|
ниедеформации |
|
|
|
|
|
|
|
|
|
|
|
Отжигнизко- |
Медленно |
680–750 |
В зависимости |
Медленное |
Распадцемен- |
Перлит, |
Феррит+ |
Снижениетвердости, |
|
температурный, |
до500 С |
|
оттребуемой |
до250 С для |
титаперлита |
перлит+ |
перлит, |
улучшение обраба- |
|
графитизи- |
дляслож- |
|
конечной |
сложных |
|
феррит |
феррит |
тываемости,повы- |
|
рующий |
ных дета- |
|
структуры |
деталей |
|
|
|
шениепластичности, |
|
|
лей |
|
(1–4 ч) |
|
|
|
|
ударнойвязкости. |
|
|
|
|
|
|
|
|
|
Прочность чугуна |
|
|
|
|
|
|
|
|
|
снижается |
|
Отжигвысоко- |
Тоже |
850–950 |
Достаточная |
Медленное |
Распад |
Свободный |
Перлит+ |
Уменьшениетвердо- |
|
температурный, |
|
|
дляполного |
с печью, |
свободного |
цементит+ |
феррит, |
сти,улучшение |
|
графитизи- |
|
|
распада |
выдержка |
цементитаи |
перлит |
феррит |
обрабатываемости, |
|
рующий |
|
|
свободного |
при А1 |
частичноили |
|
|
повышение |
|
(смягчающий) |
|
|
цементита |
|
полностью |
|
|
пластичности |
|
|
|
|
(0,5–5ч) |
|
цементита |
|
|
|
69 |
|
|
|
|
|
перлита |
|
|
|
|
|
|
|
|
|
|
|
|
70
Продолжение табл. 37
1 |
2 |
3 |
4 |
5 |
6 |
7 |
8 |
9 |
Нормализа- |
Тоже |
850–950 |
Достаточная |
Навоздухе |
Насыщение |
Перлит + |
Перлит,сорби- |
Увеличениесвязан- |
циясерого |
|
|
длянасыще- |
|
аустенитауг- |
феррит, |
тообразный |
ного углерода, по- |
чугуна |
|
|
нияаустенита |
|
леродом иего |
феррит |
перлит |
вышение твердости, |
|
|
|
углеродом |
|
превращение |
|
|
прочности, износо- |
|
|
|
(0,5–3ч) |
|
в перлит |
|
|
стойкости |
|
|
|
|
|
|
|
|
|
Нормализа- |
Тоже |
850–950 |
Достаточная |
Навоздухе |
Распад свобод- |
Свободный |
Тоже |
Понижение твердо- |
цияотбелен- |
|
|
для разложе- |
|
ного цементита |
цементит+ |
|
сти,улучшениеоб- |
ного чугуна |
|
|
нияцементи- |
|
|
перлит |
|
рабатываемости. |
|
|
|
та (0,5–5 ч) |
|
|
|
|
Повышениемехани- |
|
|
|
|
|
|
|
|
ческихсвойств |
Закалка |
Тоже |
850–930 |
Достаточная |
Вода,масло |
Превращение |
Перлит. |
Продуктырас- |
Повышениетвердо- |
|
|
|
длянасыще- |
|
переохлажден- |
Перлит + |
падапереохлаж- |
стидоHB =500, |
|
|
|
нияаустенита |
|
ного аустенита |
феррит |
денного аусте- |
повышениепрочно- |
|
|
|
углеродом |
|
|
|
нита:мартенсит, |
сти,износостойкости |
|
|
|
(0,5–3 ч) |
|
|
|
троостит, сор- |
|
|
|
|
|
|
|
|
бит,остаточный |
|
|
|
|
|
|
|
|
аустенит |
|
Изотермиче- |
Простые |
830–900 |
Достаточная |
Закалочная |
Изотермиче- |
Тоже |
Продуктыизо- |
Повышениетвердо- |
ская закалка |
детали |
|
дляпрогрева |
средас тем- |
скоепревраще- |
|
термического |
стидоHB =500, |
|
ускоренно, |
|
(0,2–1,5ч) |
пературой |
ниеаустенита |
|
превращения |
повышениепрочно- |
|
сложные |
|
|
250–450 С |
|
|
аустенита:бей- |
сти,резкое увеличе- |
|
до 550 С |
|
|
|
|
|
нит, троостит, |
ниеизносостойкости |
|
замедленно |
|
|
|
|
|
сорбит, остаточ- |
|
|
|
|
|
|
|
|
ныйаустенит |
|