
книги / Чугуны. Структура и термическая обработка
.pdf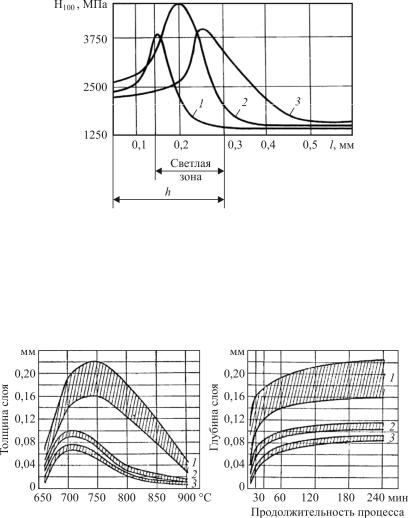
Рис. 29. Изменение микротвердости H100 по толщине слоя на сером чугуне после алитирования при температуре, С:
1 – 950; 2 – 1000; 3 – 1050
На основании данных, приведенных на рис. 30, можно заключить, что оптимальная температура алитирования 700–720 oС и выдержка около 60 мин.
а |
б |
Рис. 30. Влияние температуры (а) и времени выдержки (б) на толщину диффузионного алитированного слоя:
1 – сталь 10; 2 – чугун с шаровидным графитом; 3 – серый чугун
81
Сульфоцианирование
Комплексное насыщение поверхности деталей различными элементами – одно из направлений развития и совершенствования процессов ХТО. Так, для снижения износа деталей в период приработки применяют насыщение поверхности серой – сульфидирование, но при дальнейшей работе износ трущихся поверхностей может даже превышать износ неупрочненных поверхностей 18–20 . С целью обеспечить сочетание хорошей прирабатываемости и последующей износостойкости был разработан процесс одновременного насыщения поверхности серой, углеродом и азотом – сульфоцианирование. Как и для других процессов ХТО, известны три метода сульфоцианирования: в порошковых средах (разновидность – насыщение в обмазках), в жидких средах – в расплавах солей и в газовых средах.
Для крупных деталей, например втулок цилиндров судового дизеля диаметром 430 и высотой 1500 мм, предложен способ сульфоцианирования 19 в обмазках состава: 37 % ZnSO4; 18,5 % Na2SO4; 18,5 % K2SO4; 2,25 % KCNS; 3,75 % Na2S2O3; 6,0 % каолин; 14,0 % вода. Режим насыщения: температура
550–570oС, время 2,5 ч.
По данным работы 20 , температура сульфоцианирования
впорошках может быть в широком интервале – от 500 до 930 oС, длительность от 4 до 12 ч, но применение твердого сульфоцианирования ограничено, в отличие от распространенного в промышленности многих стран процесса в расплавах солей. Состав ванн и особенности жидкого и газового сульфоцианирования приведены
всправочной литературе по ХТО 18–20, 21 .
Структура сульфоцианированного слоя на чугуне и стали аналогична (рис. 31), но на чугуне более развита сульфидная зона (до 40–50 мм при температуре до 570–590 oС) и слабо раз-
82
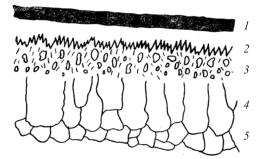
виты карбонитридная и диффузионная зоны (суммарная толщина не более 50–60 мкм) 18 . Повышение температуры процесса до 650–680 oС приводит к чрезмерному увеличению слоя сульфидов и карбидной зоны (до 80–100 мкм) и большой неравномерности толщины зоны, особенно глубоко проникающей по периметру графитных включений.
Рис. 31. Схема структуры сульфоцианированного слоя после охлаждения на воздухе: 1 – сульфидная зона; 2 – карбонитридная зона мелкоигольчатого строения (преимущественно из цементита); 3 – нитридная зона (нитриды железа в виде дисперсных выделений в смеси с остаточным аустенитом и мелкоигольчатым мартенситом); 4 – столбчатая зона твердого раствора; 5 – равноосные зерна твердого раствора
Основной характеристикой фрикционных свойств при взаимном скольжении поверхностей является зависимость коэффициентов трения от удельной нагрузки. Эта зависимость показана на рис. 32, который наглядно демонстрирует преимущество сульфоцианирования. Сульфоцианирование также повышает коррозионную стойкость в водопроводной воде и влажном воздухе и усталостную прочность 18 .
83
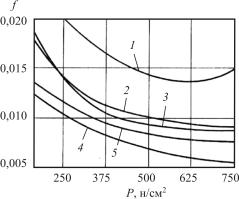
Рис. 32. Зависимость коэффициента трения f от величины нагрузки P при взаимном скольжении поверхностей двух образцов:
1, 2 – чугун СЧ 21-40–СЧ 21-40 до и после сульфоцианирования; 3, 4 – сталь 45 – СЧ 21-40 до и после сульфоцианирования;
5 – сталь 45 – бронза БрО 10-1
Хромомарганцирование
Цель такой обработки железоуглеродистых сплавов – повышение поверхностной твердости и износостойкости в условиях трения скольжения, кавитации и абразивного изнашивания.
Насыщение ведут в порошковых смесях ферромарганца и феррохрома с добавками Al2O3 и NH4Cl в контейнерах с плавкими затворами, соотношение FeMn : FeCr от 1:2 до 3:2. Температура процесса 950–1050 oС, время 4–8 ч. Фазовый состав, толщина и микротвердость слоя зависят от состава порошковой смеси и технологических параметров процесса. Форма включений графита на фазовый состав и толщину слоя практически не влияет. Во всех случаях на поверхности присутствует карбидный слой (карбиды типа Cr23C6 и Cr7C3, легированные Mn и Fe) с микротвердостью 11 000–17 500 МПа. За карбидным слоем следует переходная зона, в которой почти отсутст-
84
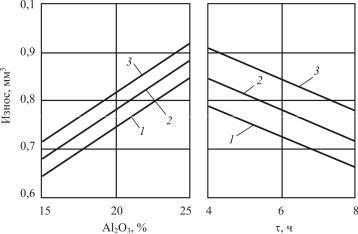
вуют включения графита и толщина которой в 2–3 раза больше карбидной зоны 18, 19 . Износостойкость СЧ, ВЧ и КЧ по сравнению с исходным состоянием повышается в 2–2,5 раза и зависит от состава насыщающей смеси и режима насыщения (рис. 33). Кавитационная стойкость хромомарганцированных слоев также выше, чем исходных и хромированных чугунов. По жаростойкости и сопротивлению электрохимической коррозии они уступают хромистым чугунам.
а |
б |
Рис. 33. Зависимость износостойкости чугуна СЧ 28-48 от условий хромомарганцирования: а – от содержания Al2O3 в смеси при насыщении 6 ч при 1000 С:
1– 55 % Мр1 + x3 %Al2O3 + (45 – x3) % ФХр75 + 3 % NH4Cl;
2– 40 % Мр1 + x3 %Al2O3 + (60 – x3) % ФХр75 + 3 % NH4Cl;
3– 25 % Мр1 + x3 %Al2O3 + (75 – x3) % ФХр75 + 3 % NH4Cl;
б – от продолжительности насыщения при 1000 С в смеси
(40 % Мр1 + 40 % ФХр75 + 20 %Al2O3) + x4 % NH4Cl (1, 2, 3 – 2, 3 и 4 % NH4Cl соответственно)
85
Силицирование
Одна из причин недостаточно широкого распространения силицирования сталей и чугунов – трудность получения беспористых слоев с высоким содержанием кремния, имеющих хорошую сцепляемость с сердцевиной.
При газовом силицировании в среде H2 + SiCl4 при 960–990 oС на сером чугуне (СЧ) получены прочно связанные с основой покрытия. Насыщение при 870–930 oС приводило к образованию легко отслаивающихся от основы слоев.
Стойкость СЧ против абразивного изнашивания в результате повышается в 2,5 раза при трении скольжения между опытным образцом и вкладышем из стали ШХ15 с твердостью 62 HRC с подачей суспензии из 50 % Al2O3 (с размерами частиц 10 мкм), 20 % олеиновой кислоты, 30 % стеарина и керосина, разжижающего смесь до вязкости машинного масла. Давление на трущуюся поверхность 3000 МПа, скорость вращения 400 об/мин.
Более перспективным для чугунов является процесс хромосилицирования, основное назначение которого, как и для сталей, повышение износостойкости, жаростойкости, коррозионной и кавитационной стойкости.
Применяют преимущественно хромосилицирование в порошковых смесях при t = 950…1100 oС в течение 4–10 ч. Процесс ведут в герметичных контейнерах. Возможно также хромосилицирование из паст с использованием защитной обмазки и в жидкой среде. Структура, фазовый и химический состав слоев зависят от состава насыщающей среды, температуры и времени насыщения. Результаты на серых, ковких и высокопрочных чугунах практически аналогичны. Слой состоит из карбидной зоны (Cr, Fe)23(C,Si)6 + (Cr,Fe)7(C,Si)3 с микротвер-
достью H50 = 10 000…13 000 МПа. В переходной зоне возможно образование зоны альфа-фазы с пониженной до 6000–7000 МПа микротвердостью и меньшим количеством, чем в сердцевине,
86
включений графита. Толщина этой зоны зависит от условий процесса и колеблется от 40 до 120 мкм.
Кавитационная стойкость серого гильзового чугуна повышается в 4–6 раз. Например, жидкое хромосилицирование при 1100 oС в течение 4 ч в смеси 57 % Na2SiO3 + 20 % NaCl + + 15 % Cr2O3 + 8 % CK 25 повышает кавитационную стойкость чугуна СЧ 28-48 в 5 раз 18 .
Износостойкость в условиях сухого трения скольжения повышается в 1,8–2,1 раза, причем тем больше, чем толще слой.
87
СПИСОК ЛИТЕРАТУРЫ
1.Франценюк И.В., Франценюк Л.И. Альбом микроструктур чугуна, стали, цветных металлов и их сплавов. – М.: Академкнига, 2004. – 190 с.
2.Двоеглазов Г.А. Материаловедение: учеб. для вузов. – Ростов-н/Д.: Феникс, 2015. – 445 с.
3.Материаловедение: учеб. для вузов / Б.Н. Арзамасов, В.И. Макарова, Г.Г. Мухин, Н.М. Рыжов, В.И. Силаева. – 8-е изд., стер. – М.: Изд-во МГТУ им. Н.Э. Баумана, 2008. – 646 с.
4.Богачев И.Н. Металлография чугуна. – 2-е изд., доп. и испр. – Свердловск: Металлургиздат, 1962. – 392 с.
5.Гуляев А.П. Металловедение: учеб. для втузов. – 6-е изд., перераб. и доп. – М.: Металлургия, 1986. – 542 с.
6.Бунин К.П., Малиночка Я.Н., Таран Ю.Н. Основы металлографии чугуна. – М.: Металлургия, 1969. – 415 с.
7.Шишляев В.Н. Железоуглеродистые литейные сплавы: учеб. пособие. – Пермь: Изд-во Перм. гос. техн. ун-та, 2002. – 161 с.
8.Гольдштейн Я.Е., Мизин В.Г. Модифицирование и микролегирование чугуна и стали. – М.: Металлургия, 1986. – 271 с.
9.Чугун: справ. / А.Д. Шерман, А.А. Жуков, Э.В. Абдуллаев, И.О. Пахнющий. – М.: Металлургия, 1991. – 575 с.
10.Попов А.А., Попова Л.Е. Изотермические и термокинетические диаграммы распада переохлажденного аустенита: справ. термиста. – М.; Свердловск: Машгиз, 1961. – 430 с.
11.Георгиев М.Н., Симонов Ю.Н. Трещиностойкость железоуглеродистых сплавов: монография. – Пермь: Изд-во Перм. нац. исслед. ун-та, 2013. – 418 с.
12. Справочник по машиностроительным материалам: в 4 т. Т. 3. Чугун / П.П. Берг, П.Н. Бидуля, В.П. Гречин, Я.М. Дов-
88
галевский; под ред. Г.И. Погодина-Алексеева. – М.: Машгиз, 1959. – 359 с.
13.Материаловедение в машиностроении: учеб. для бакалавров / А.М. Адаскин, Ю.Е. Седов, А.К. Онегина, В.Н. Кли-
мов. – М.: Юрайт, 2012. – 535 с.
14.Применение отливок из высокопрочного чугуна с шаровидным графитом в тракторном и сельскохозяйственном машиностроении: метод. рекомендации. – М.: Изд-во ЦНИИТЭИтракторсельхозмаш, 1980. – 61 с.
15.Вишняков Д.Я., Ростовцев Г.Н., Неустроуев А.А. Оборудование, механизация и автоматизация в термических цехах: учеб. пособие. – М.: Металлургия, 1964. – 467 с.
16.Новиков И.И. Теория термической обработки металлов: учеб. для вузов. – 4-е изд., перераб. и доп. – М.: Металлур-
гия, 1986. – 480 с.
17.Гольдштейн М.И., Грачев С.В., Векслер Ю.Г. Специальные стали: учеб. для вузов. – 2-е изд., перераб. и доп. – М.:
Изд-во МИСиС, 1999. – 408 с.
18.Химико-термическая обработка металлов и сплавов: справ. / Г.В. Борисенок, Л.А. Васильев, Л.Г. Ворошнин, Н.С. Горбунов. – М.: Металлургия, 1981. – 424 с.
19.Минкевич А.Н. Химико-термическая обработка металлов и сплавов. – 2-е изд., перераб. – М.: Машиностроение, 1965. – 491 с.
20.Криулин А.В. Сульфоцианирование стали и чугуна. – М.: Машиностроение, 1965. – 244 с.
21.Термическая обработка в машиностроении: справочник / под ред. Ю.М. Лахтина, А.Г. Рахштадта. – М.: Машино-
строение, 1980. – 783 с.
89
ГОСТ
1.ГОСТ 3443–87. Отливки из чугуна с различной формой графита. Методы определения структуры. – М., 1988.
2.ГОСТ 1412–85. Чугун с пластинчатым графитом для отливок. Марки. – М., 1986.
3.ГОСТ 1215–79. Отливки из ковкого чугуна. Общие технические условия. – М., 1980.
4.ГОСТ 7293–85. Чугун с шаровидным графитом для отливок. Марки. – М., 1986.
5.ГОСТ 28394–89. Чугун с вермикулярным графитом для отливок. Марки. – М., 1990.
6.ГОСТ 1585–85. Чугун антифрикционный для отливок.
Марки. – М., 1986.
7.ГОСТ 7769–82. Чугун легированный для отливок со специальными свойствами. Марки. – М., 1983.
90