
Учебные пособия / Эдельштейн лекции по ТММ учебник
.pdf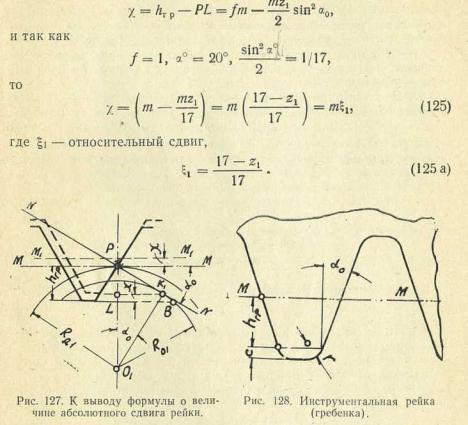
В этих формулах принято: |
радиусы |
начальных окружностей |
|
равны радиусам делительных, высоты головок зубцов hгр |
=fm, угол зацепления а° = 2 0 ° |
||
и передаточное отношение |
i 1 2 берется |
по абсолютной |
величине большей или равной |
единице (|i12|≥1). |
|
|
|
Определение положительного абсолютного сдвига рейки
При числе зубцов на колесе z 1 <ωz 1 min, во избежание заклинивания, рейку необходимо отодвинуть от делительной окружности на величину абсолютного сдвига + χ (рис. 127) (рассматривается случай, когда f= 1 , а°=20°, при этом z 1 min= 17). Если модульная прямая М М будет касаться делительной окружности, то прямая головок рейки пересечет прямую N N в точке В . В этом случае будет заклинивание, что недопустимо. Отодвинув прямую М М от делительной окружности на величину + χ(эта прямая займет положение М1М1), мы добьемся того, что прямая головок рейки пройдет через точку К1 и тем самым избежим заклинивания.
Из рис. 127 видно, что
6°. Методы изготовления зубчатых колес.
Метод копирования состоит в том, что режущим кромкам инструмента придают форму профилей, нарезаемых зубцов и, выбирая металл, заключенный между профилями (во впадинах), получают зубцы с запроектированными профилями. Эта операция может быть выполнена различными инструментами, например, дисковой фрезой, пальцевой фрезой, протяжкой и т. д.
Метод огибания (обкатки) состоит в том, что инструменту придают форму звена, находящегося в зацеплении с нарезаемым колесом. Такими инструментами могут быть: инструментальная рейка (гребенка) (рис. 128) или особое зубчатое колесо-долбяк. При нарезании инструменту и колесу, которое нарезается, придают то относительное движение, которое они имели бы, находясь в зацеп лен и и. Стружка снимается движением инструмента вдоль оси нарезаемого колеса.
Размеры нарезаемого колеса целиком зависят от размерных параметров инструмента и его установки относительно делительной окружности. Инструментальная рейка (гребенка) имеет те же параметры, что и обычная рейка. Единственное ее отличие
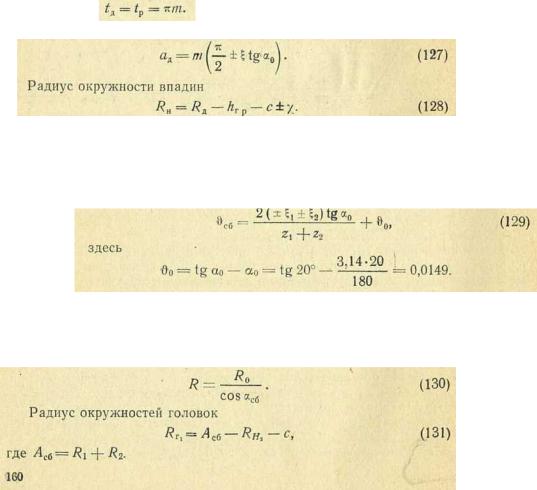
состоит в том, что головка ее удлинена на величину с = 0,25 m при f= 1,0 и с = 0,3 т при f = 0,8. Это удлинение нужно для выборки радиального зазора между головкой зубца одного колеса и основанием ножек зубцов другого.
7°. Некоторые размеры колес при внешнем зацеплении их и при нарезании колес инструментальной рейкой. Ее параметры: hГР = m, с = 0,25т, а° = 20°. (Все приводимые формулы даются без вывода. Профили зубцов не должны подрезаться инструментом.
Подрез при нарезании соответствует заклиииванию при обычном зацеплении.)
Шаг колеса по делительной окружности
(126)
Толщина зубца по делительной окружности
Инволюта угла зацепления при сборке 1-го и 2-го колеса. При нарезании колес со сдвигом инструментальной рейки толщины их становятся не равными половине шага, поэтому при сборке межцентровое расстояние не равно сумме радиусов делительных окружностей. Поэтому угол зацепления тоже изменяется и становится не равным 20°.
Угол зацепления при сборке асб находится по таблице инволют. Радиус начальной окружности
Формулы (129) - (131) выведены из предположения, что при cборке боковой зазор между зубцами отсутствует.
8°. Примеры синтеза зубчатой передачи с внешним зацеплением колес.
Рассмотрим два случая синтеза. В первом примере синтез надо осуществить по заданным передаточному отношению i1 2 ,межцентровому расстоянию Асб и модулю т. Особенности расчета: подбор чисел зубцов на колесах и назначение таких сдвигов инструментальной рейки, при которых в сборке будет выдержано заданное межцентровое расстояние Асб. Надо указать, что не следует применять отрицательный сдвиг инструмента во избежание ослабления зубцов; желательно для обоих колес назначать одинаковые сдвиги инструмента для обеспечения равнопрочности их зубцов.
Во втором примере синтез надо осуществить по заданным передаточному отношению i1 2 ,числу зубцов на малом колесе z1 и модулю т. Единственное требование, которое надо удовлетворить в этом примере, — профили зубцов не должны подрезаться инструментом.
Пример 1. Расчет внешнего прямозубого зубчатого зацепления (рис. 129).
Дано: межцентровое расстояние —Асб= 18 мм, модуль зацепления— т = 1,0 мм,
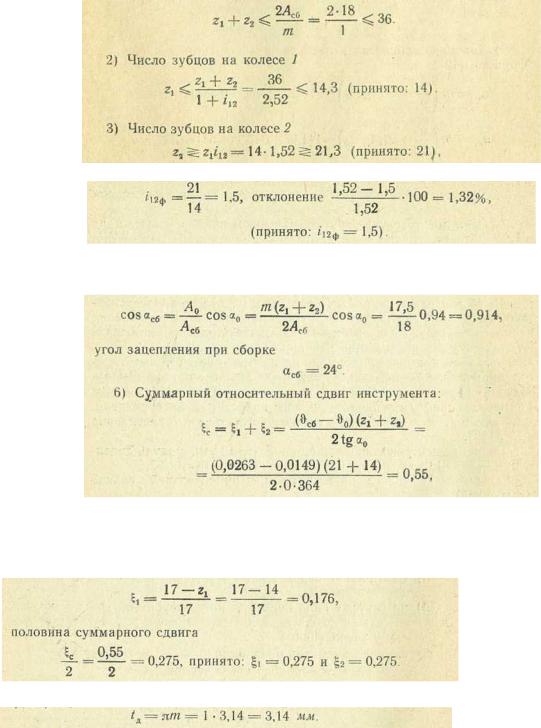
передаточное отношение — i1 2 =1,52.
Указания: 1) колеса нарезаются инструментальной рейкой (гребенкой).
Параметры рейки: модуль — т =1,0мм, профильный угол— ао = 20°, высота головки — hГ Р = т = 1,0 мм, удлинение головки — с= 0,25 т = 0,25 мм;
2)зубцы на колесах не должны подрезаться инструментом;
3)фактическое передаточное отношение может отклоняться от заданного не более чем на ±2,5%;
4)на чертеже надо показать: по три зубца на каждом колесе, теоретическую и рабочую линию зацепления, рабочие части профилей, дугу зацепления;
5)вычислить степень плавности.
1-й этап расчета — подбор чисел зубцов.
1) Сумма чисел зубцов
4) Фактическое передаточное отношение
2-й этап расчета — определение размеров колес.
5) Косинус угла зацепления при сборке
ϑсб найдено по углу асб, а ϑо по углу ао из таблицы инволют.
7)Сдвиг инструмента для каждого колеса: по формуле (125 а) находят минимальный допустимый относительный сдвиг инструмента для колеса 1, при котором не будет подреза профиля зубца,
8) Шаг колес по
9) Толщины зубцов по делительной окружности вычисляют по формуле (127):
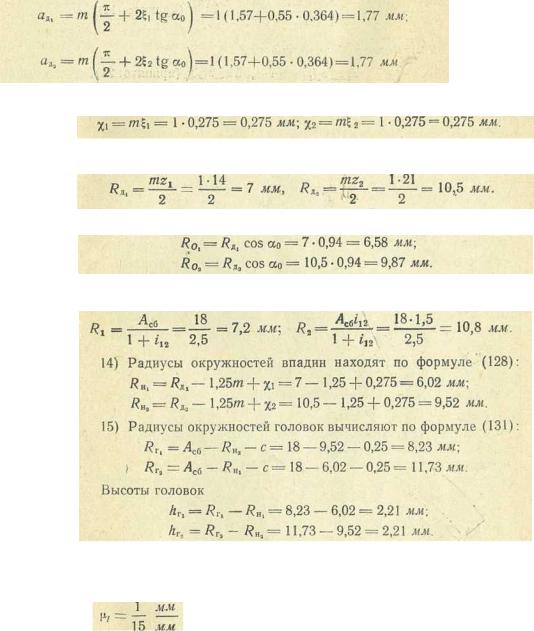
10)Абсолютные сдвиги инструмента находят по формуле (125 а):
11)Радиусы делительных окружностей определяют по формуле (119):
12)Радиусы основных окружностей вычисляют по формуле ( 120) :
13)Радиусы начальных окружностей определяют соответственно по формулам (111) и (111а):
3-й этап — вычерчивание картины зацепления (рис., 129).
1)Отмечаем положения центров вращения колес O1 и O2 на расстоянииАсб= 18 мм.
Масштаб построения принимаем
(все размеры на чертеже увеличены в 15 раз).
2)Из центров O1 и O2 проводим соответствующими радиусами пять окружностей: головок, начальную, делительную, основную и основания ножек.
3)Через полюс зацепления Р проводим линию NN,касательно к основным
окружностям. Отмечаем точки касания этой линии с этими окружностями — точки К1 и К2 . Линии O1 O2 и O1 K1 а также O1 O2 и O2 K2 образуют между собой угол зацепления при сборке асб.
4)Перекатыванием прямой NNпо основным окружностям, точкою Р ее, вычерчиваем эвольвенты Э1 и Э2 .
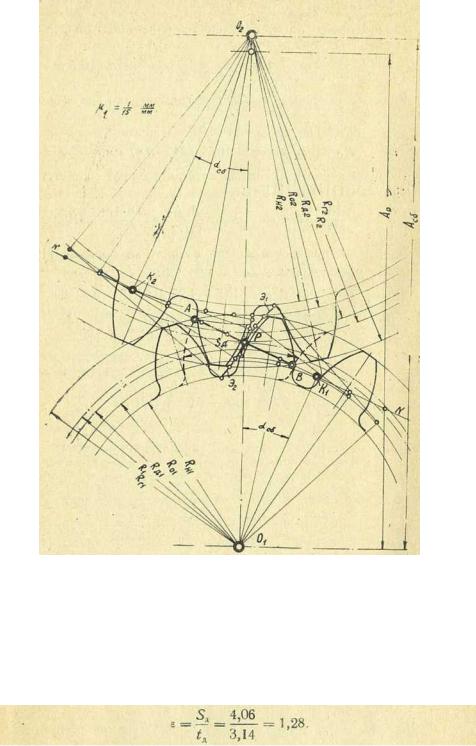
Рис. 129. Картина зацепления колес при проектировании зацепления по заданным: межцентровому расстоянию, модулю и передаточному отношению,
5)Отмечая на делительных окружностях толщины зубцов и шаг, строим по три зубца на каждом колесе.
6)Теоретическая линия зацепления определится отрезком K1 К2 , а ее рабочая часть — отрезком АВ. Рабочие части профилей отмечены двойными линиями. Дуга зацепления найдена на делительной окружности, ее длина SД =4,06 мм.
7)Степень плавности определяют по формуле (112):
Пример 2. Расчет внешнего зубчатого зацепления (рис. 130).
Дано: модуль зацепления — т = 1,0 мм, передаточное отношен и е — i12=1,5, число зубцов на меньшем колесе —z1 = 14.
Указания: 1) Колеса нарезаются инструментальной рейкой(гребенкой). Параметры рейки: модуль — т= 1,0 мм, профильный угол — а0 = 20°, высота
головки — hгр= т.= 1.0 мм, удлинение головки с = 0,25 т — 0,25 мм.
2)Зубцы на колесах не должны подрезаться инструментом.
3)На чертеже надо показать: по три зубца на каждом колесе, теоретическую и рабочую линию зацепления, рабочие части профилей, дугу зацепления.
4)Вычислить степень плавности.
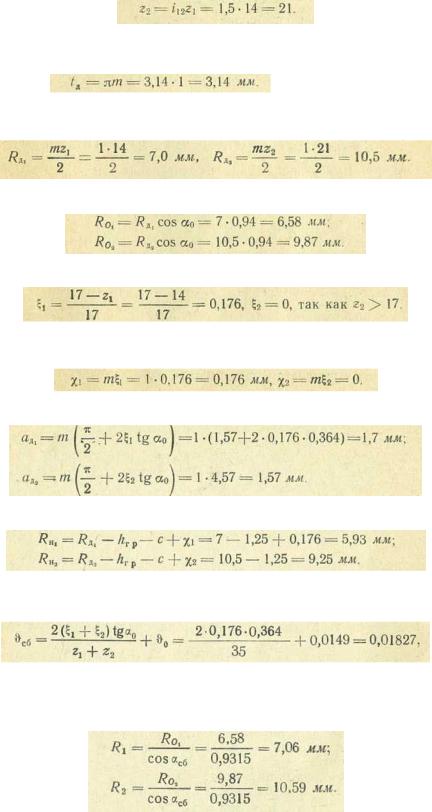
1-й этап расчета — определение числа зубцов на колесе 2
2-й этап расчета — определение размеров колес и зацепления их. 1) Шаг колес по делительной окружности
2) Радиусы делительных
окружностей
3) Радиусы основных окружностей
4)Относительный сдвиг инструмента
5)Абсолютный сдвиг инструмента
6)Толщина зубцов по делительной окружности
7)Радиусы окружностей впадин (ножек)
8)Инволюта (полярный угол) угла зацепления (угла сборки) и угол зацепления при сборке
этому значению ϑсб = 0,01827 соответствует угол асб = 21°20̍, найденный по таблице инволют (а0 = 20°, ϑ0 = 0,0149).
9) Радиусы начальных окружностей
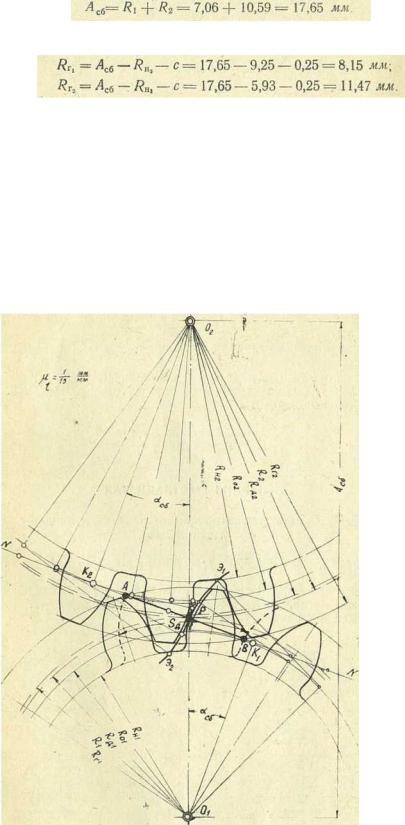
10)Межцентровое расстояние
11)Радиусы окружностей головок
3-й этап. Вычерчивание картины зацепления (рис. 130).
1)Отмечаем положения центров колес О1и О2 на расстоянии Асб = 17,65 мм. Масштаб чертежа принимаем µl = 1/15 мм/мм (все размеры на чертеже увеличены в 15 раз).
2)Из центров О1и О2соответствующими радиусами проводим пять окружностей: головок, начальную, делительную, основную и основания ножек (окружность ножек).
3)Через полюс зацепления Р проводим линию NN, касательно к основным окружностям.
Отмечаем точки К1 и K2 касания этой линии с основными окружностями. Линии O1 O2 и O1 K2 а также O2 O2 и O1 K2 , образуют между собой угол зацепления при сборке асб.
4)Перекатыванием прямой NN по основным окружностям, точкою Р ее, вычерчиваем эвольвенты Э1 и Э2.
Рис. 130. Картина зацепления колес при проектировании зацепления по заданным: числу зубцов на одном колесе, модулю и передаточному отношению.
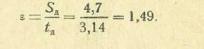
5)Отмечаем на делительных окружностях толщины зубцов и шаг; строим по три зубца на каждом колесе (недостающую часть ножки зубца выполняем прямой, проходящей через центр вращения колеса. Место сопряжения профиля ножки с окружностью основания ножек скругляем дугой окружности с радиусом, равным 0,4 m).
6)Теоретическая линия зацепления определится отрезком К1 К2- а ее рабочая часть
— отрезком АВ.
Рабочие части профилей отмечены двойными линиями. Дугу зацепления находим по делительной окружности: SД= 4,7мм.
7)Степень плавности
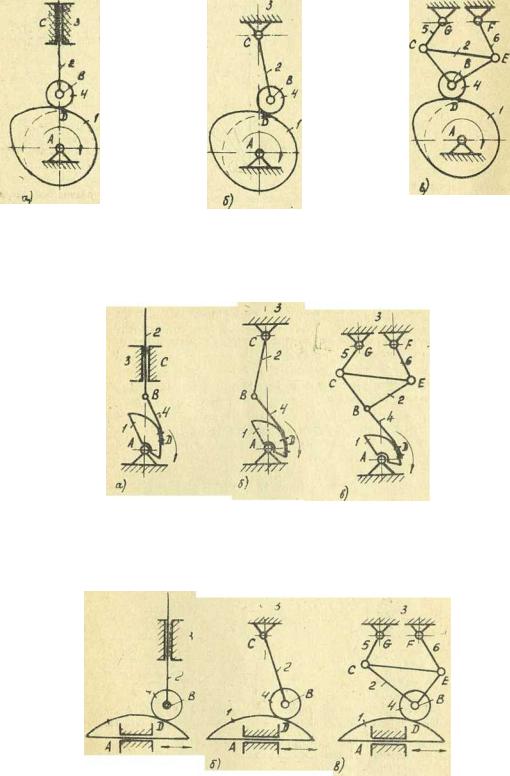
ЛЕКЦИЯ ШЕСТНАДЦАТАЯ § 18. Синтез (проектирование) плоских кулачковых механизмов
1ᵒ Кулачковые механизмы можно подразделить на следующие основные типы:
I. Кулачок 1входит во вращательную кинематическую пару А со стойкой 3 (рис. 131), штанга 2 входит в кинематическую пару 4-го класса с кулачком.
Рис. 131. Кулачковые механизмы с вращающимся кулачком: а — с возвратно-поступательным движением штанги; б — с возвратно-вращательным движением штанги; в — со сложным движением штанги.
II. Кулачок 1входит во вращательную кинематическую пару А со стойкой 3 (рис. 132), штанга 2 связана с кулачком гибким звеном 4,
Рис. 132. Кулачковые механизмы с вращающимся кулачком и гибким звеном: а — с возвратно-поступательным движением штанги; б — с возвратно-вращательным движением штанги; в — со сложным движением штанги.
III. Кулачок 1входит в поступательную кинематическую паруА со стойкой 3 (рис. 133), штанга 2 связана входит в кинематическую пару 4-го класса скулачком.
Рис. 133. Кулачковые механизмы с поступательным движениемкулачка:
а— с возвратно-поступательным движением штанги; б— с возвратно-вращательным движением штанги; в — со сложным движениемштанги.
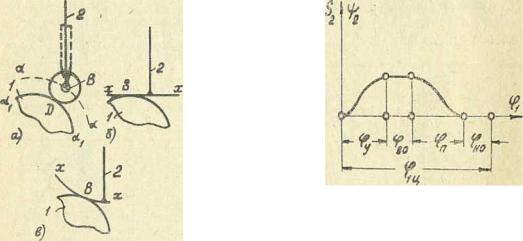
IV. Кулачок 1входит в поступательную кинематическую пару А со стойкой 3, штанга 2 связана с кулачком гибким звеном 4.
Кулачковые механизмы I и III типов называются механизмами с жесткими звеньями, а II и IV — с гибкими звеньями.
Теория механизмов II и IV типов подробно разработана в диссертации ст. преподавателя кафедры ТММ ВЗМИ В.А. Пименова В работе показано, что каждому кулачковому механизму с гибким звеном можно найти эквивалентный с жесткими звеньями, поэтому к ним (к кулачковым механизмам с гибкими звеньями) применимы методы кинематического анализа и синтеза, разработанные для механизмов с жесткими звеньями.
Для кулачковых механизмов I и III типов элементами кинематической пары 4-го класса на штанге могут быть: а) острие — точкаВили круглый ролик (рис. 134, а), б) тарелка — плоскость хх(рис. 134,6), грибок — любая кривая хх (рис. 134, в).
Форма профиля кулачка для всех типов этих механизмов находится одним и тем же методом, поэтому мы рассмотрим только следующие типы: I, а с роликом на штанге; I, а с тарелкой на штанге; I, б с роликом на штанге (рис. 131, а и б; рис. 134, а и б).
Рис. 134. Элементы кинематической пары четвертого класса |
Рис.135. |
График функции положения штанги |
на штанге:
а— острие (точка) или круглый ролик;
б— плоская тарелка; в — грибок.
2ᵒ. Приступая к проектированию кулачкового механизма, надо располагать такими данными: принципиальной схемой механизма, законами движения кулачка и штанги, некоторыми начальными размерными параметрами.
Применительно к кулачкам I типа закон движения кулачка задают обычно в форме ω1= const, т. е. считают, что он движется равномерно. Для штанги надо знать: фазовые углы и функцию положения ее (рис. 135) для каждой фазы движения S2 = S2(φ1) (тип I, а ) и ψ2=ψ2(φ1)(тип I, б ) .
Различаются следующие фазы движения штанги: фаза удаления, когда штанга удаляется от вала кулачка, этой фазе отвечает угол поворота кулачка φу; фаза верхней остановки, когда штанга стоит в наибольшем удалении от вала кулачка, этой фазе соответствует угол φво; фаза приближения, когда штанга приближается к валу кулачка, ей отвечает угол φп; фаза нижней остановки, она определяется углом φно.
Цикл работы механизма нами принят равным одному обороту кулачка.
Вместо функции положения штанги иногда задают ее вторую производную для каждой фазы движения: S''2= S''2(φ1) илиψ''2=ψ''2(φ1) , а также максимальный ход штанги
S2max или ψ2max.