
2
.pdf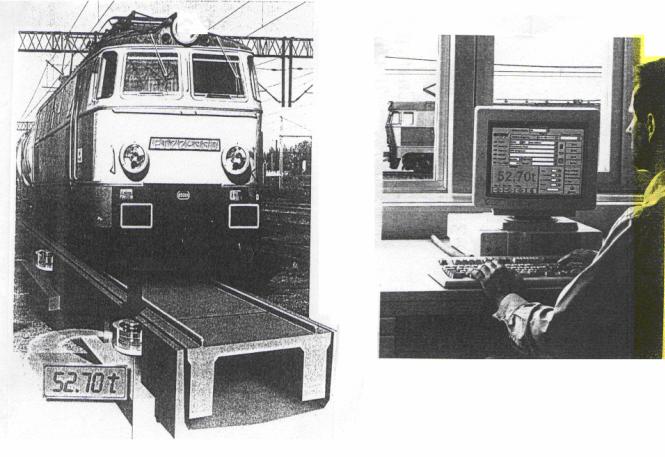
Рис. 2.53 Загальний вигляд автоматичних вагонних ваг системи “Schenck” (а) із пультом управління (б)
Останнім часом на зміну важільним вагонним вагам для технологічного і комерційного зважування запроваджуються тензометричні електронні ваги виробництва зарубіжних і українських фірм “Шенк” (рис. 2.53), “Карат”, “Пульсар” і інші. Їх різновиди передбачають зважування як в статичному, так і в динамічному, а також в статично-динамічному режимах.
Ваги для зважування в статичному режимі доцільно використовувати при навантаженні і розвантаженні вагонів на станціях з порівняно невеликими вантажопотоками, а також для зважування і реєстрації маси вантажу в комерційних документах: накладних, комерційних актах тощо.
Довжина вагової платформи в них достатня для встановлення всього вагона, а індикаторний пристрій показує масу вагона відразу.
Ці ваги забезпечують найточніше показання маси вагона з вантажем, визначають рівномірність завантаження вагона, реєструють перевантаження візків.
Ваги для зважування в динамічному режимі рекомендуються для встановлення на станціях і підприємствах з великими вантажопотоками. Ці ваги можуть встановлюватися у вигляді платформи довжиною 12–15м, або у вигляді двох-трьох секцій довжиною 4.5–5.5м для поосьового і візкового зважування. Зважування відбувається при швидкості 3–10км/год, а для технологічного зважування під час руху – до 30км/год. Ваги можуть укомплектовуватися
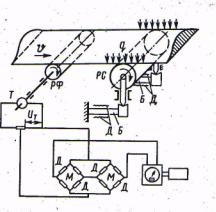
фототелевізійним комплектом, який забезпечує розпізнавання вагонів, що рухаються, їх рід, вісність тощо.
Ваги для зважування в статично-динамічному режимі поєднують всі переваги двох попередніх видів.
Комплект автоматичних ваг складають: вагова платформа, вантажоприймальні вузли, комплект датчиків, апаратура обробки, реєстрації і передачі інформації, до якої належить АЦП – аналого-цифровий перетворювач, ПРП – прилад, що реєструє і показує, ПЕОМ, принтер, модем, дублююче табло, дозувальна система та інші прилади.
Програмне забезпечення сучасних автоматичних ваг передбачає статичне зважування вагонів, зважування вагонів в русі без розчеплення з накопиченням суми маси вагонів, визначення маси поїзда в цілому без маси локомотива, запис результатів зважування на магнітний диск ПЕОМ, зберігання цих даних протягом певного часу, вивід результатів зважування на екран ПЕОМ і принтер, обмін інформацією з оператором, сигналізацію про перевищення маси вантажу проти норми, сигналізацію про перевищення швидкості руху вагонів на вагах тощо.
Для зважування навалочних та сипучих вантажів, що переміщуються безперервним потоком, застосовують конвеєрні автоматичні ваги (рис. 2.54).
Рис. 2.54 Блок-схема конвеєрних автоматичних ваг для зважування сипучих вантажів:
РФ – фрикційний ролик; РС – лічильно-вимірювальний ролик; Б – пружна балка; Д – датчик; Т – тахогенератор; М – електричний міст;
q – погонне навантаження на конвеєр; V – швидкість конвеєра
Фрикційний ролик РФ через тахогенератор Т передає в схему моста М інформацію про швидкість руху стрічки конвеєра, а лічильно-вимірювальний ролик РС – про навантаження, сприйняте датчиками Д. Дротяні тензометри наклеєні на пружну балку Б і зібрані за диференціальною схемою. Оскільки електрична напруга генератора Uт пропорціональна погонному навантаженню q, а число обертів – швидкості руху конвеєра V, лічильник безперервно накопичує суму ваги вантажу, що переміщується конвеєром.
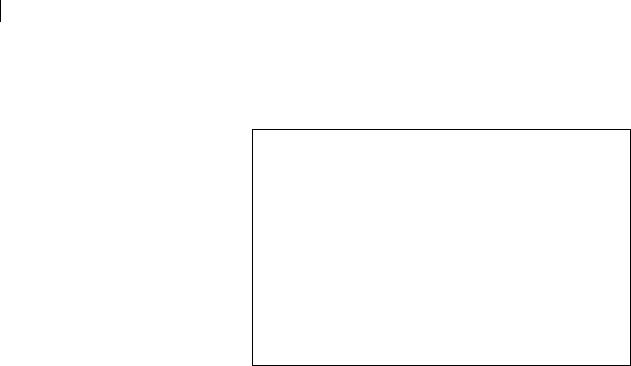
Контрольні питання до теми 2.5
1.Як класифікуються ваги, що використовуються для зважування вантажів?
2.Навести основні технічні особливості будови ваг, що використовуються на залізничному транспорті?
3.Навести основні технічні параметри, від яких залежить точність зважування вантажів.
4.Навести основні вимоги до експлуатації вагонних ваг при зважуванні вагонів.
5.Охарактеризувати основні вимоги до утримання ваговимірювальних пристроїв.
6.Як обладнується вагоповірочнй вагон?
7.Як плануються ремонти, огляди і повірка ваг?
8.Пояснити принцип будови і роботи тензометричних ваг.
9.Пояснити принцип дії тензометричного датчика.
10.Пояснити принцип будови і роботи конвеєрних автоматичних ваг.
11.Навести загальну характеристику і принципи застосування автоматичних електронних ваг типу “Шенк”, “Карат”, “Пульсар” та інших перспективних ваговимірювальних систем.
2.6 Основи проектування і розрахунки пристроїв вантажного господарства
Всі споруди і пристрої вантажного господарства за своєю потужністю і переробною спроможністю повинні забезпечувати своєчасне виконання запланованого обсягу вантажних операцій, повне збереження вантажів, своєчасне оброблення рухомого складу, а також механізацію вантажних робіт з додержанням вимог нормативних актів з питань охорони праці.
Стаття 10 Статуту залізниць України
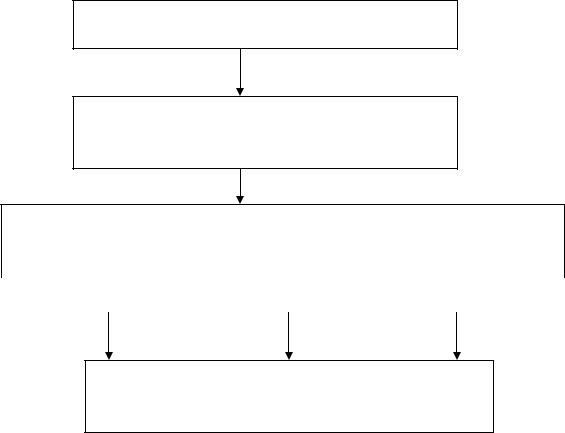
Визначення проектних річних обсягів перевезень вантажів з урахуванням перспективи їх зростання
Вибір рухомого складу для перевезення вантажів. Розрахунки максимальних добових розмірів вантажо- і вагонопотоків, місткості складів
Вибір декількох варіантів схем механізації переробки вантажів і типів складів. Розрахунки кількості машин, штату працівників, лінійних розмірів і площі складів. Техніко-економічні розрахунки ефективності кожного варіанту
|
1 варіант |
|
2 варіант |
|
3 варіант |
|
|
|
|
|
|
|
|
Порівняння показників усіх варіантів. Вибір найбільш ефективного варіанту механізованої
переробки вантажів
Рис. 2.55 Загальна блок-схема проектування пунктів вантажної роботи
2.6.1 Основні принципи проектування пунктів вантажної роботи
Перед проектуванням складів і площадок для переробки заданого обсягу вантажів необхідно провести вибір рухомого складу і декількох найбільш раціональних схем комплексної механізації переробки цих вантажів.
Вибір рухомого складу для перевезення вантажів повинен проводитися з таким розрахунком, щоби забезпечити найкраще використання вантажопідйомності і місткості вагонів, застосування сучасних високопродуктивних вантажно-розвантажувальних машин і механізмів, передової технології переробки цих вантажів, збереження їх при перевезенні.
Навантаження на вагони приймається на підставі фактичного середнього статичного навантаження вагонів цими вантажами на станціях і в цілому на залізниці.
Схеми комплексної механізації вантажних робіт і технологічні цикли роботи машин приймаються в залежності від роду та характеру вантажу, роду рухомого складу, з урахуванням застосування передових методів праці, використання сучасних серійних вантажно-розвантажувальних машин і вантажозахватних пристроїв. Одночасно приймаються відповідні типи складів чи площадок.
Раціональна схема механізації повинна забезпечити:
• комплексну механізацію переробки вантажу на всіх етапах технологічного процесу;
•полегшення умов праці;
•зростання продуктивності праці і скорочення кількості робочої сили;
•скорочення простою рухомого складу;
•мінімальний розмір капітальних вкладень;
•зниження собівартості переробки вантажу.
Для кожного виду вантажу підбирається декілька (2–3) конкуруючих схем механізації, які розраховуються за всіма параметрами. Остаточний вибір кращого з них здійснюється в результаті виконання техніко-економічних розрахунків.
2.6.2 Розрахунки основних параметрів складів і фронтів на вантажних пунктах
Для проектування чи вибору типового проекту вантажного складу необхідно знати його основні параметри: потрібну місткість, площу, довжину, ширину, висоту, розміри навантажувально-розвантажувальних фронтів. Ці параметри визначаються за обсягом вантажопереробки складу, який планується, і у відповідності з режимом роботи вантажного району.
Режим роботи вантажного району може бути детермінованим, (стійким, ритмічним) або недетермінованим (неритмічним, випадковим).
При детермінованому режимі вагони, автомобілі та інші транспортні засоби поступають під вантажні операції приблизно через однакові інтервали часу; кількість вагонів в подачі і тривалість виконання вантажних операцій майже не відрізняються від середнього значення, з відхиленнями в певних передбачених межах коливань.
При випадковому характері роботи час прибуття та кількість транспортних засобів у подачі іноді значно відрізняються від середнього значення і в розрахунках тоді користуються, як правило, методами теорії масового обслуговування.
Великим вантажним районам зі стійкими вантажопотоками найчастіше притаманний детермінований режим роботи. Нижче приводиться методика розрахунку параметрів складу при детермінованому режимі роботи.
Згідно з проектом або плановим річним об’ємом вантажопотоку визначають вантажопотік у розрахункову добу (добу максимального прибуття або відправлення вантажів):
|
Qпр(від) |
k |
|
|
|
QД = |
річ |
|
н |
; т/доб, |
(2.15) |
365 |
|
|
|||
|
|
|
|
|
де kн – коефіцієнт нерівномірності прибуття або відправлення вантажів, який визначається як відношення максимального добового вантажопотоку до середньодобового; для орієнтовних розрахунків може прийматися від 1,1 до 1,4, більші значення можна приймати для сільськогосподарських вантажів, потоки яких мають сезонний характер, менші – для промислової сировини та продукції, вантажопотоки яких більш стійкі і ритмічні;
365 – кількість діб, що складають календарний рік;
Qрічпр(від) – заданий (плановий) річний вантажопотік; якщо він не
визначений, то його можна розрахувати на підставі даних про відправлення і прибуття вантажів на складі протягом року; розрахунок може виконуватися для відправлення і для прибуття окремо (якщо ці вантажі зберігаються в різних складах) або разом (при сумісному зберіганні).
Добовий розрахунковий обсяг вантажопотоку при сумісному зберіганні вантажів, що прибувають і відправляються, визначається за формулою:
|
Qпр |
k пр +Qвід |
k від |
|
||
QД = |
річ |
н |
річ |
н |
; т/добу, |
(2.16) |
|
|
365 |
|
|||
|
|
|
|
|
|
де Qрічпр – річний обсяг прибуття вантажів, т;
Qрічвід – річний обсяг відправлення вантажів, т;
kнпр – коефіцієнт нерівномірності прибуття вантажів; kнвід – коефіцієнт нерівномірності відправлення вантажів
Місткість складу в тоннах – це кількість тонн вантажів, які повинні розміститись в ньому; визначається за формулою;
Єскл =QД Тзб kскл ; т, |
(2.17) |
де Тзб – тривалість зберігання вантажу на складі, діб; орієнтовні терміни приводяться в таблиці 2.10;
kскл – коефіцієнт складування, який враховує застосування прямого варіанту; для орієнтовних розрахунків приймається від 1 до 0,8.
Необхідну площу складу (м2) можна визначити методами середнього навантаження та елементарних площадок.
Метод середнього навантаження більш простий і, як правило, використовується при орієнтовних розрахунках; метод елементарних площадок більш точний, але громіздкий, його зручніше використовувати при контейнерних і пакетних перевезеннях.
Площа складу методом середнього навантаження визначається за формулою:
Fскл = kпр |
Єскл |
; м2, |
(2.18) |
|
|||
|
q |
|
де kпр - коефіцієнт, який враховує додаткову площу для проходів працівників, проїздів вантажно-розвантажувальних машин і автомобілів, місця для встановлення ваг, приміщень прийомоздавальників тощо, величина передбачається проектом і приймається не меншою, ніж вказано в таблиці 2.10.
Навантаження на підлогу (т/м2) однорідного вантажу розраховується за формулою:
q = h γ ; т/м2, |
(2.19) |
де h – проектна висота укладання вантажу в штабелі, м; γ – щільність або об’ємна маса вантажу, т/м3.
Розміри загальної площі далі уточнюються з урахуванням відповідного її планування, розмірів вантажних місць, способів їх укладання та типів вантажно-розвантажувальних машин і обладнання. На план складу наносять штабелі, проходи та проїзди, площадки для приймання, видачі та сортування вантажів тощо. Головні проїзди повинні забезпечувати можливість розвороту навантажувачів та інших засобів механізації.
Для розрахунку необхідної площі складу методом елементарних площадок за основу беруть розміри штабелів, стелажів, пакетів і проходи між ними, які визначаються умовами штабелювання в залежності від засобів механізації, що застосовуються в складі.
Площу елементарної площадки, яка багаторазово повторюється на складі, з урахуванням проходів та проїздів можна визначити за формулою:
∆F =(Lш +аш ) (Вш +bш ); м2, |
(2.20) |
де Lш і Bш – довжина та ширина штабеля, м ;
аш і bш – ширина поздовжнього та поперечного проїздів (проходів), м (0,9–1м для пішохідного руху, 4м для навантажувачів, не менше 0,7м – між краном та рухомим складом).
Таблиця 2.10 - Експлуатаційні параметри типових складів
|
|
Тривалість зберігання, діб |
Середнє |
Коефіцієнт, |
||
Вид вантажу |
Вид вантажного |
|
|
наван- |
який |
|
До |
Після |
таження на |
враховує |
|||
складу |
||||||
|
відправлення |
прибуття |
підлогу |
додадкову |
||
|
|
|||||
|
|
|
|
складу т/м2 |
площу |
|
1 |
2 |
3 |
4 |
5 |
6 |
|
Тарні та штучні |
Криті склади і |
|
|
|
|
|
вантажі |
1,5 |
2,0 |
0,85 |
1,7 |
||
платформи |
||||||
вагонними відправками |
|
|
|
|
||
|
|
|
|
|
||
|
|
|
|
|
|
|
Тарні та штучні |
Криті склади і |
2 |
2,5 |
0,4 |
2,0 |
|
вантажі дрібними |
||||||
платформи |
||||||
відправками |
|
|
|
|
||
|
|
|
|
|
||
Контейнери |
Площадки |
1,0 |
2,0 |
0,5 |
1,9 |
|
Великовагові вантажі |
Площадки |
1,0 |
2,5 |
0,9 |
1,6 |
|
Колісні вантажі |
Площадки |
1,0 |
2,5 |
- |
- |
|
Лісоматеріали навалом |
Площадки |
2,5 |
3,0 |
1,1 |
1,5 |
|
Цемент, вапно |
Спеціалізовані |
2,5 |
2,5 |
0,5 |
1,6 |
|
навалом |
криті склади |
|||||
|
|
|
|
|||
Гіпс, крейда |
Спеціалізовані |
- |
2,5 |
1 |
1,5 |
|
навалом |
криті склади |
|||||
|
|
|
|
|||
Мінеральні добрива |
Спеціалізовані |
- |
2,5 |
1,1 |
1,5 |
|
навалом |
криті склади |
|||||
|
|
|
|
|||
Промислові товари |
|
|
|
|
|
|
широкого вжитку |
Спеціалізовані |
1,5 |
2,0 |
0,25 |
1,7 |
|
(трикотаж, взуття, |
криті склади |
|||||
|
|
|
|
|||
одежа тощо) |
|
|
|
|
|
|
Меблі |
Спеціалізовані |
1,5 |
2,0 |
0,25 |
1,7 |
|
криті склади |
||||||
|
|
|
|
|
||
Папір |
Спеціалізовані |
1,5 |
2,0 |
1,1 |
1,7 |
|
криті склади |
||||||
|
|
|
|
|
Загальна площа складу методом елементарних площадок визначиться:
Fскл = nпл ∆F ; м2, |
(2.21) |
де nпл - кількість елементарних площадок , яка дорівнює відношенню загальної місткості складу Eскл до місткості елементарної площадки ∆E:
nпл = |
Єскл |
; шт, |
(2.22) |
|
|||
|
∆Е |
|
де ∆E – місткість елементарної площадки, т.
Ширина критих складів, критих та відкритих платформ повинна встановлюватись проектом в залежності від кількості і виду вантажу, що переробляється, характеру операцій, які з ним проводяться і засобів механізації та автоматизації, які при цьому застосовуються. В усіх випадках ширина складу повинна бути не меншою, ніж 18 метрів. В експлуатації ще можуть знаходитись склади шириною 12 і 15м.
Довжина складу визначається діленням площі на ширину складу:
Lcкк = |
Fскл |
; м, |
(2.23) |
B |
|||
|
скл |
|
|
Одержану при цьому довжину складу необхідно порівняти з довжиною вантажного фронту з боку залізничних колій та з боку під’їзду автомобілів і прийняти більше значення.
Фронтом вантажних робіт називають частину складських колій (у м), призначену безпосередньо для навантаження або розвантаження однорідних вантажів. Розміри фронту також визначаються числом вагонів, що встановлюються на корисній довжині складської колії, яка може бути використана для одночасного навантаження (розвантаження) вантажів.
Під фронтом подачі розуміють корисну довжину колій, яка може бути використана для розміщення всіх одночасно поданих вагонів на об’єкт вантажних операцій. На фронті подачі може бути розміщено більше від тої кількості вагонів, які одночасно перероблюються на фронті навантаження (розвантаження).
Довжина фронту подачі вагонів визначається за формулою:
L = |
nв lзч |
+а |
м |
; м, |
(2.24) |
п |
Zп |
|
|
||
|
|
|
|
довжина вантажного фронту для навантаження (розвантаження) вагонів за формулою:
L |
= |
nв lзч |
+а |
м |
; м, |
(2.25) |
ван. |
|
Zп Zзм |
|
|
||
|
|
|
|
|
де nв – розрахункова кількість вагонів, які поступають на вантажний фронт або відправляються з нього протягом доби, визначається за формулою:
nв = |
QД |
; ваг., |
(2.26) |
|
qв |
|
QД – вантажопотік в розрахункову (максимальну) добу, т ; qв– середнє навантаження вагона, т ;
lзч – зчіпна довжина вагона певного типу (між осями автозчепів), м; Zп – кількість подач вагонів протягом доби;
Zзм – кількість змін (перестановок) вагонів на вантажному фронті в одній подачі;
ам – збільшення вантажного фронту, необхідне для маневрування локомотивними або іншими засобами (орієнтовно 15–25м).
Довжина фронту вантажних робіт із боку під’їзду автомобілів визначається за формулою:
La = |
QД lф ta |
; м, |
(2.27) |
|
|||
|
qa T |
|
де lф – частина довжини фронту, який приходиться на один автомобіль у залежності від способу його постановки (вздовж складу, перпендикулярно складу, під кутом 30-45°), м;
tа – середня тривалість операцій з одним автомобілем (включаючи) час на під’їзд до складу і від’їзд), год.
qа – середнє навантаження нетто одного автомобіля, т; Т – тривалість роботи вантажного району, год.
Довжина фронту для одного автомобіля визначають за формулами: при розміщенні автомобілів вздовж складу:
lф = lа +С'; м, |
(2.28) |
при розміщенні автомобілів перпендикулярно складу:
lф = ba + С" ; м, |
(2.29) |
де lа – довжина автомобіля без причепа (4,2÷4,4 м) або з причепом
(4,5÷7м);
ba – ширина автомобіля (2,0÷2,6:м);
С' – відстань між автомобілями при послідовному розміщенні (4,2÷4,4 м); С" – відстань між автомобілями при перпендикулярному розміщенні
(1,5м).

Довжина будь-якого складу чи площадки повинна бути більшою або дорівнювати довжині вантажного фронту: Lскл ≥ Lвр; Lскл ≥ Lа і бути кратною для критих складів 12м, для відкритих платформ – 3м, для площадок – 4м. Для типових критих складів ангарного типу заводського виготовлення довжина складу повинна бути кратною 72м – довжині одної секції.
Довжина критого складу з внутрішнім чи зовнішнім розташуванням колій не повинна перевищувати 300м. Типові проекти механізованих складів ангарного типу мають довжину 72, 144, 216, 288м.
Приклад. Визначити основні параметри складу для зберігання і переробки тарно-штучних вантажів на піддонах, що прибувають вагонними відправками.
Річний вантажопотік на склад становить Qрічпр = 180тис. т ; коефіцієнт
нерівномірності потоку вантажів kн = 1,1; коефіцієнт складування kcкл = 0,8; середнє навантаження для критого вагона qв = 45т; число подач вагонів за добу Zп = 2; число змін (перестановок) на вантажному фронті Zзм = 2; середня тривалість операцій з одним автомобілем tа = 0,25год; середнє навантаження одного автомобілю q = 3т; тривалість роботи вантажного району Т = 7год.
Розрахунок вантажопотоку у розрахункову (максимальну) добу виконується за формулою 2.15:
QД =180000365 1,1 =543 т/доб.
Місткість критого складу визначається за формулою 2.17, прийнявши Тзб із таблиці 2.10 (Тзб = 2 доби):
Єскл =543 2 0,8 =869 т.
Площа складу визначається за формулою 2,18:
Fскл =1,7 0869,85 =1738 м2.
Приймаючи ширину типового складу Вскл=18м, визначаємо його довжину за формулою 2.23:
Lскл=1738 : 18 = 97 м
і, заокруглюючи до величини, кратної 12м, одержуємо Lскл =108м. Середньодобову кількість вагонів, що поступають на вантажний фронт,
визначаємо за формулою 2.26:
пв = 543 : 45 = 12 вагонів.
Довжина вантажного фронту з боку залізничного транспорту визначається за формулою 2.25: