
Технология переработки нефти и газа. Часть 1. Первичная переработка не
.pdf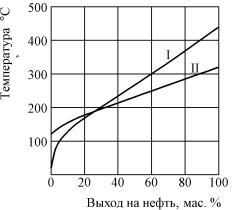
Следовательно, количество жидкости (GR), оставшейся после
однократного испарения, равно |
|
GR = G0 (1 – e), |
(6.2) |
где G0 – количество исходного сырья; |
|
е – доля отгона (доля паров) при температуре t. |
|
Если пары отделить от жидкости, а последнюю нагреть до тем- пературы t2, то система будет характеризоваться точкой L2, а количе- ство жидкости будет составлять
GR2 = G0 (1 – e1)(1 – е2), |
(6.3) |
где е1 – доля отгона при первичном нагреве сырья до температуры t; е2 – доля отгона при вторичном нагреве жидкости, оставшейся
после первичного нагрева, до температуры t2.
Таким образом, при однократном нагреве до температуры t2 вся смесь переходит в паровую фазу, а при двухкратном нагреве до этой же температуры часть сырья в количестве GR2 остается в жидком со- стоянии.
Следовательно, при использовании ОИ для полного испарения сырья необходим нагрев до меньшей температуры, чем при много- кратном испарении. С другой стороны, при многократном испарении жидкость содержит значительно меньшее количество легкокипящего компонента В (точка R2 с со-
ставом x0), чем при однократ- ном (точка R с составом x), т.е. четкость разделения ком- понентов при многократном испарении выше.
Аналогичная картина на- блюдается и при анализе кри- вых ИТК и ОИ нефти (рис. 6.2).
На рисунке видно, что температура начала кипения на кривой ОИ выше, а конца кипения – ниже, чем на кри-
вой ИТК (которая характеризует многократное испарение).
191
Следовательно, важным преимуществом процесса ОИ при раз- гонке нефти является высокая доля отгона при одной и той же темпе- ратуре нагрева, что позволяет проводить процесс разделения при бо- лее низких температурах и избежать разложения сырья в результате перегрева. Для повышения же четкости погоноразделения метод ОИ применяют в сочетании с ректификацией (многократным контактиро- ванием пара и жидкости на специальных распределительных устрой- ствах (тарелках или насадке), при котором протекают процессы, ана- логичные многократному испарению).
6.2.2.Перегонка нефти и нефтяных фракций
вприсутствии испаряющего агента
Перегонка нефти и ее фракций в присутствии испаряющего агента позволяет повысить концентрацию высококипящих компонен- тов в остатке без повышения температуры перегонки. Этот эффект связан со снижением парциального давления отгоняемой фракции, а значит – и температуры ее перехода в паровую фазу. В производст- венной практике в качестве испаряющего агента широко используется перегретый водяной пар (рис. 6.3, а). Кроме того, могут применяться инертные газы (N2, СО2), углеводородные газы, керосино-газойлевые фракции. Применение испаряющего агента, в частности водяного па- ра, позволяет снизить температуру перегонки на 10–20 °С при дости- жении той же доли отгона.
Несмотря на широкое применение в качестве испаряющего агента водяного пара, он имеет ряд недостатков:
–большой расход тепла на получение перегретого пара;
–большой расход охлаждающей воды на конденсацию пара. Хорошие результаты достигаются при использовании в качестве
испаряющего агента инертного газа, но его применение не получило широкого распространения из-за громоздкости используемого обору- дования (перегреватели газа, конденсаторы), низкого коэффициента теплоотдачи газа и трудностей с полным извлечением отгоняемого нефтепродукта из газового потока.
192
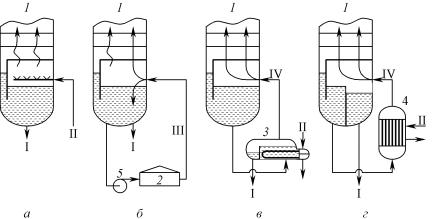
Рис. 6.3. Схемы подвода тепла в низу ректификационных колонн: 1 – колонны; 2 – печь; 3 – ребойлер (испаритель);
4 – прямоточный кипятильник; 5 – насос.
I – остаток; II – водяной пар; III – горячая струя (парожидкостный поток);
IV – паровой поток
Более удобны для использования в качестве испаряющего агента легкие нефтяные фракции. Причем чем ниже температура кипения испаряющего агента, тем ниже температура перегонки. Однако при- менение очень низкокипящих продуктов приводит к значительным потерям его в процессе перегонки.
Широкое применение в качестве испаряющего агента (взамен водяного пара) получают керосино-газойлевые фракции (используют- ся при перегонке мазутов и тяжелых фракций).
6.2.3. Перегонка нефти и нефтяных фракций под вакуумом
Перегонку нефти и нефтяных фракций при атмосферном давле- нии проводят, как правило, при температурах, не превышающих 350– 370 °С, т.к. дальнейшее повышение температуры усиливает протека- ние реакций термокрекинга перегоняемых углеводородов. В связи с этим высококипящие нефтяные продукты перегоняют под вакуумом.
В случае использования вакуума при нагреве до 410–420 °С удается отбирать дистилляты с температурой кипения при атмосферном дав-
193
лении до 480–500 °С, а при использовании глубокого вакуума и наса-
дочных колонн с низким гидравлическим сопротивлением – до 580 °С.
Существующими методами удается |
поддерживать вакуум |
в верхней части вакуумной колонны на |
уровне 2,66–6,66 кПа |
(20–50 мм рт. ст.). Чем ниже удается создать вакуум, тем более глу- бокий отбор масляных фракций можно провести. В сочетании с ис- пользованием насадочных контактных устройств с низким гидравли- ческим сопротивлением удается отобрать дистилляты с температурой кипения 550–580 °С с получением в остатке утяжеленного гудрона.
6.2.4. Экстрактивная и азеотропная ректификация
Методы ОИ с использованием вакуума и испаряющего агента позволяют достаточно четко разделить нефть на составные фракции. Однако они не позволяют выделить из нефти очень узкие фракции и индивидуальные углеводороды (в частности, сырье для нефтехими- ческих процессов). Это связано с тем, что углеводороды, входящие в состав нефти, очень часто образуют близкокипящие, или азеотроп- ные, смеси (например, бензол и циклогексан имеют температуры ки-
пения 80,1 и 80,75 °С соответственно) и не поддаются разделению даже с использованием методов четкой ректификации.
Для разделения таких смесей и выделения индивидуальных угле- водородов применяют азеотропную и экстрактивную ректификацию.
Эти методы основаны на том, что в систему вводится дополни- тельное вещество, присутствие которого увеличивает разницу в лету- честях разделяемых углеводородов, и тогда даже с применением обычных методов перегонки удается выделить нужный углеводород.
Если вводимый углеводород менее летуч, чем разделяемые ве- щества, то его вводят с верха колонны и выводят с низа вместе с ос- татком. Такая ректификация называется экстрактивной, а вводимое вещество – растворителем (экстрагентом). Ввод в систему раствори- теля ведет к изменению коэффициентов относительной летучести из- за различной растворимости в нем отдельных компонентов.
194
Основные требования к растворителю:
–достаточно высокая температура кипения, для того чтобы компоненты, отводимые с ним в виде смеси, могли быть ото- гнаны;
–хорошая растворяющая способность, а значит, малый его
расход.
Если добавляемое вещество более летучее, чем разделяемые компоненты, то его вводят в колонну вместе с сырьем, а выводят с парами с верха колонны. Эту разновидность ректификации называ- ют азеотропной, а вещество, добавляемое в систему, – уводителем.
Основные требования к уводителю:
–он должен обеспечивать образование азеотропа с одним или несколькими компонентами смеси;
–должен иметь температуру кипения, близкую к температуре кипения отгоняемого вещества, что позволяет достичь наи-
большей разницы между температурой кипения азеотропа
идругих компонентов;
–уводитель должен легко выделяться из азеотропной смеси. Однако применение экстрактивной и азеотропной ректификации
требует подготовки сырья – оно должно выкипать в максимально уз- ких температурных пределах. Поэтому данным видам ректификации должны предшествовать методы обычной (четкой) ректификации, по- зволяющие получить узкие фракции.
6.3. Подвод и отвод тепла в колонны ректификации
Важным элементом технологии ректификации нефти и нефтяных фракций является подвод и отвод тепла в колонне, поскольку ректи- фикация – это термодинамический процесс с непрерывным подводом и отводом тепла, что позволяет формировать температурный профиль по высоте колонны и, соответственно, движущую силу процесса рек- тификации. Чем больший тепловой поток подводится (и отводится) в колонне, тем больше будет в колонне кратность орошения (отноше- ние количества орошения к количеству отводимого верхнего продук- та), тем выше четкость ректификации. Однако при этом также будут
195
возрастать энергетические затраты на процесс ректификации (расход тепла на испарение, воды или воздуха – на конденсацию паров).
Подвод тепла в колонну ректификации осуществляется потоком сырья, а также с низа отгонной части. Возможности подвода тепла с сырьевым потоком обычно ограничены из-за термического разложе-
ния сырья (предельные температуры нагрева – 350–360 °С в атмо-
сферной части и 400–420 °С в вакуумной части при перегонке мазута). В случае, когда в колонне отгоняются легкие дистилляты и некоторый перегрев низа колонны не вызывает протекания реакций крекинга, в низ колонны вводится дополнительный тепловой поток. Это осуще- ствляестя либо с помощью выносного кипятильника (ребойлера) (рис. 6.3, в, г), либо «горячей струи» (циркуляция остатка колонны че-
рез печь и подача нагретого до 300–350 °С парожидкостного потока в отгонную часть) (рис. 6.3, б).
Подводимое тем или иным способом в низ колонны тепло испа- ряет часть жидкой фазы и создает необходимый подпор паров в от- гонной части.
Отвод тепла осуществляется только в укрепляющей (верхней) части колонны и служит для создания жидкого потока внутреннего орошения тарелок. В простых колоннах (не имеющих отбора боковых дистиллятов) тепло всегда отводится с верха колонны (острое, холод- ное испаряющееся орошение). В сложных колоннах тепло может от- водиться в нескольких сечениях по высоте колонны (неиспаряющее- ся, или циркуляционное, орошение). Как правило, в сложных колон- нах используют комбинированное орошение – верхнее испаряющееся и циркуляционное орошения.
Холодное испаряющееся орошение осуществляется по следую-
щей схеме: пары, выходящие с верха колонны, конденсируются
вконденсаторе-холодильнике и собираются в емкости орошения, от- куда часть возвращается на верхнюю тарелку колонны в виде холод- ного испаряющегося орошения, а балансовое количество отводится
ввиде готового продукта (рис. 6.4, а).
196
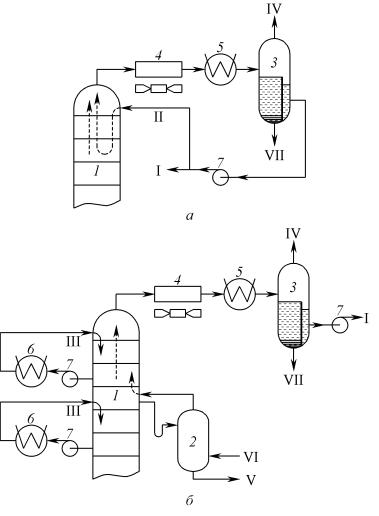
Рис. 6.4. Схемы отвода тепла из ректификационных колонн: 1 – колонна; 2 – отпарная колонна; 3 – сепаратор-отстойник;
4 – воздушный холодильник-конденсатор; 5 – водяной холодильник-конденсатор; 6 – теплообменник; 7 – насос.
I – бензин; II – холодное испаряющееся орошение; III – циркуляционное орошение;
IV – углеводородный газ; V – боковой дистиллят (керосин);
VI – водяной пар; VII – вода
197
Необходимое количество возвращаемого в колонну холодного испаряющегося орошения Gх.исп (кг/ч) определяется по формуле
Gх.исп = |
3600Qх.исп |
, |
(6.4) |
|
qп |
− qжхк |
|||
|
t ,D |
t , |
|
|
где |
Qх.исп |
– |
количество тепла, которое нужно снять из колонны при |
|
|
|
помощи холодного испаряющегося орошения, Вт; |
qп |
и qж |
– |
энтальпии паров и жидкой фазы при температуре верха |
t ,D |
t ,хк |
|
|
колонны (tD) и температуре на выходе из холодильника- конденсатора (tхк) (обычно 30–40 °С) соответственно, Дж/кг.
Холодное неиспаряющееся или циркуляционное орошение проис-
ходит по следующей схеме: часть жидкой фазы с любой тарелки по высоте колонны прокачивается через теплообменник, холодиль- ник, и охлажденный поток возвращается на ту же или вышележащую тарелку. В результате создается дополнительный поток флегмы для осуществления процесса ректификации (рис. 6.4, б).
Необходимое количество циркуляционного орошения (кг/ч) оп- ределяется по формуле
Gцо = |
3600Qцо |
, |
(6.5) |
|
qtж − qtж |
||||
|
1 |
0 |
|
|
где Qцо – количество теплоты, которое необходимо снять циркуля- ционным орошением, Вт;
qж , qж – энтальпии жидкой фазы при температуре выхода из колон-
t1 t0
ны (t1) и температуре ввода в колонну (t0) соответственно, Дж/кг.
Циркуляционное орошение применяется в случае переработки агрессивного сырья, особенно в присутствии водяного пара. В данном случае меньшей коррозии подвергаются холодильники и большей – холодильники-конденсаторы.
Применение циркуляционного орошения позволяет разгрузить вышележащие секции по жидкой фазе, усилить предварительный по- догрев сырья и снизить тепловую нагрузку печей.
Обычно в сложной колонне организуется не более двух цирку- ляционных орошений – по числу отбираемых боковых погонов.
198
6.4. Четкость ректификации при перегонке нефти и ее фракций
При разделении на фракции таких сложных смесей, как нефть, часть компонентов распределяется между смежными дистиллятами, образуя так называемую область температурного «налегания».
Из теории ректификации известно, что распределение компонен- тов сложной смеси между смежными фракциями определяют три фак- тора: свойства смеси (относительные летучести входящих в нее ком- понентов), число тарелок в колонне (Nт) и флегмовое число (ϕ – отно- шение количества орошающей жидкости к количеству ректификата (верхнего продукта) данной простой колонны или секции).
Поскольку нефть – сложная смесь большого числа углеводоро- дов и других соединений, которая выкипает монотонно (непрерывно), то первый из этих факторов можно не учитывать. Разделительная способность колонн установки АВТ определяется в основном двумя факторами – Nт и ϕ .
Под термином четкость ректификации в колоннах АВТ пони- мают величину температурного интервала между концом кипения легкокипящего дистиллята и началом кипения смежного ему тяжело- го дистиллята (температурное налегание фракций). Так, для основной колонны атмосферного блока установки АВТ для основных фракций эти интервалы составят:
∆ tб= |
tкб.к− |
tнк.к ; |
(6.6) |
∆ tк= |
tкк.к− |
tнд.к ; |
(6.7) |
∆ t д= |
tкд.к− |
tнм.к , |
(6.8) |
где tб, tк, tд, tм – температуры начала и конца кипения бензиновой, керосиновой, дизельной фракций и мазута соответст- венно, °С.
В связи с понятием «четкость ректификации» возникает во- прос, к какому уровню четкости разделения надо стремиться при рек- тификации нефти и ее фракций. Ответ не однозначен. При разделении газовых смесей на отдельные компоненты или бензина на узкие
199
фракции эта четкость должна быть максимальной (область темпера- турного налегания компонентов –минимальной).
При перегонке нефти на топливные и масляные компоненты чет- кость ректификации носит подчиненный характер и определяется нормами на другие физико-химические свойства нефтепродуктов. На- пример, фактический состав дистиллятов АВТ в пределах нормируе- мых значений температур обычно подбирается экспериментально так, чтобы обеспечивались такие показатели, как температура вспышки, плотность, температура начала кристаллизации и др.
6.5. Материальный баланс перегонки нефти. Характеристики получаемых продуктов
и направления их использования
Принципиальную технологическую схему установки прямой пе- регонки нефти выбирают после уточнения варианта переработки неф- ти (топливный, топливно-масляный или комплексный).
Атмосферная часть схемы перегонки (рис. 6.5) может быть одно- колонной (А-1) и двухколонной (А-2) с предварительным отбензино- ванием нефти. Выбор зависит от содержания в нефти газов и серы (особенно меркаптановой), т.е. определяется, в первую очередь, ее ти- пом и классом.
Схема вакуумной ступени установки прямой перегонки нефти может иметь следующие варианты (см. рис. 6.5):
В-1 – одноколонная схема с получением как топливных, так и масляных дистиллятов;
В-2 – одноколонная схема с доиспарителем гудрона, где отго- няется тяжелый дистиллят с температурой конца кипе-
ния 540–560 °С;
В-3 – двухколонная схема масляного профиля, где в первой ко- лонне отделяют фракции до 350 °С (легкий вакуумный га- зойль) и широкую фракцию 350–550 °С, которая, в свою очередь, после нагрева разделяется на масляные дистил- ляты во второй колонне.
200