
Технология переработки нефти и газа. Часть 1. Первичная переработка не
.pdf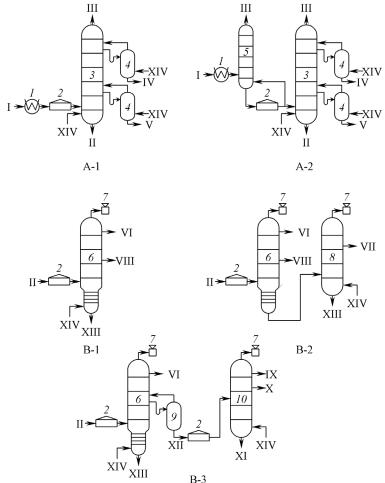
Рис. 6.5. Варианты схем атмосферных (А-1, А-2)
ивакуумных (В-1, В-2, В-3) ступеней АВТ:
1– подогреватель; 2 – печь; 3 – атмосферная колонна; 4 – отпарная колонна (стриппинг); 5 – обензинивающая колонна; 6 – вакуумная колонна;
7 – вакуумсоздающая система; 8 – доиспаритель гудрона; 9 – вакуумный приемник; 10 – вакуумная колонна для разгонки масляных дистиллятов.
I – нефть; II – мазут; III – бензин; IV – керосин; V – дизельное топливо; VI, VII – легкий и тяжелый вакуумные газойли; VIII – вакуумный газойль; IX, X, XI – легкий, средний и тяжелый масляные дистилляты;
XII – широкая фракция (300–550 °С); XIII – гудрон; XIV – водяной пар
201
Далее в соответствии с принятым вариантом переработки нефти составляется общий и поступенчатый материальный баланс дистил- ляции нефти.
Переработка нефти на установке прямой перегонки (атмосферно- вакуумной трубчатке – АВТ) – это многоступенчатый процесс, вклю- чающий стадии отбензинивания, атмосферной и вакуумной перегонки, стабилизации и вторичной перегонки бензинов. В связи с этим рас- сматривается как общий, так и поступенчатый материальный баланс перегонки нефти. Проанализируем общий материальный баланс по конечным продуктам перегонки каждой ступени с характеристикой каждого из них.
Исходная нефть (100 мас. %). Поступает на установку с содер- жанием минеральных солей от 40 до 300 мг/л и содержанием во-
ды 0,2–1,0 мас. % (1 и 2 группа).
Углеводородный газ. Его выход зависит от содержания в нефти растворенного после промысловой подготовки газа. Если нефть легкая (плотность 0,8–0,85), то выход газа может составлять 1,5–4,8 мас. %. Для тяжелых нефтей выход меньше (0,3–0,8 мас. %). Если нефть про- шла дополнительную стабилизацию на промысле, то выход газа равен нулю. До 90 % данного газа отбирается в отбензинивающей колонне. По составу это насыщенные углеводороды С1–С4 с примесью С5. Низ- кое давление и малое количество этого газа не позволяют использовать его непосредственно как сырье для установок ГФУ. В основном его применяют в качестве топлива на печах АВТ. Хотя в случае сжатия данного газа до давления 2–4 МПа возможна его переработка и на ус- тановке ГФУ.
Сухой углеводородный газ стабилизации бензина – это часть лег-
ких углеводородов С1–С3, оставшаяся растворенной в бензине. Выход достаточно мал (0,1–0,2 мас. %). Может перерабатываться на ГФУ (давление до 1,0 МПа), но из-за малого количества направляется в га- зовую линию и используется в качестве газового топлива в печах.
Головка стабилизации бензина (сжиженная). Состоит в основ-
ном из углеводородов С3 и С4 с примесью С5. Выход 0,2–0,3 мас. %.
202
Используется в качестве компонента сжиженного бытового газа или газового моторного топлива для автомобилей.
Легкая головка бензина. Фракция н.к. – 85 °С. Выход на нефть 4– 6 мас. %. Октановое число в зависимости от химсостава не превыша- ет 70 пунктов (чаще 60–65) моторным методом (ММ). Используется для приготовления нефтяных растворителей или направляется на ката- литическую изомеризацию для повышения октанового числа до 82– 85 пунктов и добавления в товарные автомобильные бензины.
Бензиновая фракция (85–180 °С). Выход на нефть в зависимости от ее фракционного состава может лежать в пределах 10–14 мас. %. Октановое число низкое (45–55 пунктов по ММ), поэтому данную фракцию направляют на каталитический риформинг, где за счет пре- вращения н-алканов и нафтенов в ароматические углеводороды ее ок- тановое число повышается до 88–92 пунктов (ММ). Катализат рифор- минга используют как базовый компонент автомобильного бензина.
Керосиновая фракция. Ее могут отбирать по двум вариантам. Первый вариант – отбор авиационного керосина (фракция 140–230 °С). Выход 10–12 мас. %. После гидроочистки и внесения необходимых присадок используется как готовое товарное реактивное топливо. Вто- рой вариант – получение компонента зимнего или арктического ди- зельного топлива (фракция 140–280 °С или 140–300 °С). Выход 14– 18 мас. %. Используется как компонент зимнего или арктического ди- зельного топлива после гидроочистки и депарафинизации (при необ- ходимости, если не удовлетворяет требованиям по сере и по темпера- турам помутнения и застывания).
Дизельная фракция. Выход 22–26 мас. %, если ранее отбирается авиакеросин, и 10–12 мас. %, если ранее отбирается компонент зим- него или арктического дизельного топлива. Используется как компо- нент зимнего или летнего дизельного топлива. При необходимости подвергается гидроочистке и депарафинизации.
Легкая газойлевая фракция. Выход 0,5–1,0 мас. %. Пределы вы-
кипания 100–250 °С. Она является результатом деструкции мазута при нагреве его в печи перед подачей в вакуумную колонну. В состав входят как насыщенные, так и ненасыщенные алканы. Используется
203
как компонент дизельного топлива (с применением гидроочистки) или добавляется в легкое котельное топливо.
Легкий вакуумный газойль. Фракция 240–380 °С. Выход на нефть 3–5 мас. %. Боковой погон вакуумной колонны. Использует- ся как компонент летнего дизельного топлива.
Вакуумный газойль. Основной дистиллят вакуумной перегонки мазута по топливному варианту. Пределы выкипания 350–500 °С
(350–550 °С). Выход на нефть 21–25 мас. % (26–30 мас. %). Исполь-
зуется в качестве сырья в процессах каталитического крекинга или гидрокрекинга для получения высокооктанового бензина, авиацион- ного керосина, высокоиндексных масел и других продуктов. Если нефть позволяет получать высокоиндексные базовые масла, то в ка- честве боковых погонов выводят масляные дистилляты, например: 350–420 °С (10–14 мас. % на нефть) и 420–500 °С (12–16 мас. %
на нефть). Масляные погоны направляют на селективную очистку от асфальто-смолистых соединений и депарафинизацию для получения базовых (средневязкого и вязкого) дистиллятов масел.
Гудрон. Остаток вакуумной перегонки мазута. Выкипает при температуре выше 500 или 550 °С. Выход на нефть составляет от 10 до 20 мас. % в зависимости от содержания в ней асфальто- смолистых веществ и тяжелых углеводородных фракций. Использу- ется гудрон по нескольким направлениям:
–как компонент тяжелых котельных топлив;
–как остаточный битум или как сырье для получения окислен- ного и компаундированного битума;
–как сырье для процесса коксования;
–как сырье для получения базового остаточного масла.
Кроме перечисленных целевых продуктов перегонки нефти, на установке АВТ получаются несколько отходов переработки.
Сточная вода с установки ЭЛОУ – вода, использованная для промывки нефти от солей. Ее количество от 1 до 3 мас. % на нефть. Эта вода содержит от 10 до 30 г/л солей (рН = 7,0–7,5), деэмульгатор, до 1 мас. % эмульгированной в воде нефти.
204
Конденсат водяного пара. Образуется при конденсации водяного пара, подаваемого в ректификационные колонны (испаряющий агент), используемого как эжектирующий агент, как теплоноситель в ребойлерах. Конденсат из колонн и эжекторов загрязнен нефтепро- дуктами и сернистыми соединениями. Его количество – 2,5–3,0 мас. % на нефть. Он направляется на блок ЭЛОУ для промывки нефти (поскольку не содержит солей) или на очистку. Чистый конденсат (с ребойлеров) поступает на повторную генерацию водяного пара.
Неконденсируемый газ с эжекторов. Это смесь легких углеводо-
родов (до С7), H2S, воздуха и водяного пара. Выход около 0,05 мас. % на нефть. Направляется в печь для дожига горючих составляющих, чтобы избежать загрязнения воздуха углеводородами.
6.6. Расчет ректификационных колонн
Задачей расчета каждой из колонн, входящих в состав установки прямой перегонки нефти, является определение ее температурного режима и основных размеров. Для каждой из колонн эта задача реша- ется с рядом особенностей.
6.6.1. Отбензинивающая колонна
При расчете данной колонны первоначально принимают число и тип тарелок. Рекомендуются клапанные, клапанные прямоточные тарелки или тарелки с S-образными элементами.
Вукрепляющей части обычно устанавливают 10–14 тарелок;
вотгонной части – 6–8 тарелок.
Затем определяют давление в сепараторе бензина (Рс). Давление в нем зависит от содержания светлых фракций и газа. Его принимают или рассчитывают из условия полной конденсации паров бензина (углеводороды С4–С5 и выше) при температуре конденсатора-холо- дильника (45–50 °С при воздушном охлаждении, Рс = 300–450 кПа; 35–40 °С при водяном охлаждении Рс = 180–250 кПа).
Далее рассчитывают давления по высоте колонны:
Рверха = Рс + ∆ Рверх-сепар, |
(6.9) |
Рввода сырья = Рверха + Nу∆ Рт, |
(6.10) |
205

Рниза = Рввода сырья + Nо∆ Рт, |
(6.11) |
где Nу и Nо – число тарелок в укрепляющей и отгонной частях соот- ветственно;
∆ Рверх-сепар – гидравлическое сопротивление (перепад давления) на участке от верха колонны до сепаратора (обычно 30–
50 кПа).
∆Рт – гидравлическое сопротивление одной тарелки (обычно
0,6–0,8 кПа).
Следующий шаг – определение температурного режима работы колонны.
Температура входа нефти в колонну либо предварительно из- вестна из расчета теплообменной аппаратуры, либо ее принимают равной 220–230 °С.
Температуру низа колонны принимают из условия Qгорячей струи
Qвхода нефти
0,14 0,16. При этом обычно tниза – tвхода = 10 16 °С.
Далее определяют долю отгона нефти на входе в колонну, при- меняя графический или аналитический методы (решая уравнения равновесия фаз).
После этого находят температуру верха колонны с учетом пар- циального давления паров бензина.
Зная температуры всех входящих и покидающих колонну пото- ков, составляют тепловой баланс. По разнице между теплом, вводи- мым в колонну и выводимым из нее, определяют количество тепла, которое надо снять орошением. Далее рассчитывают количество орошения и его кратность по отношению к верхнему продукту.
Диаметр колонны определяется исходя из количества паров в наиболее нагруженном ее сечении (для отбензинивающей колонны это сечение под верхней тарелкой, где отводится тепло острым испа- ряющимся орошением) и допустимой скорости паров (зависит от многих параметров, например, от расстояния между тарелками, типа тарелок, разницы плотностей паровой и жидкой фаз, поверхно- стного натяжения и др.).
206

D = 0,886 |
Vсек |
, |
(6.12) |
|
uдоп |
||||
к |
|
|
||
|
|
|
где – объемный расход паров в наиболее нагруженном сече- нии, м3/с;
– допустимая скорость паров, м3/(м2 с).
Высоту колонны определяют как сумму высот всех ее техноло- гических частей, а именно: высоты, занятой тарелками, высоты эва- парционного пространства, высоты верха и низа колонны, высоты по- стамента колонны.
6.6.2. Расчет основной атмосферной колонны
Расчет данной колонны также начинают с выбора типа и числа тарелок. Тип тарелок обычно выбирают тот же, что и в отбензини- вающей колонне. Рекомендуемое число тарелок – 50, иногда 55–56. Они распределяются следующим образом:
–в верхней укрепляющей части – 12–16;
–в средней секции – 12–14;
–в нижней секции (до ввода сырья) – 10–12;
–в отгонной части – 4–6;
–в стриппингах – по 4 тарелки.
Расчет атмосферной колонны ведут аналогично отбензиниваю- щей, но с учетом ряда особенностей.
Поскольку компонент бензина, отбираемый сверху этой колон- ны, тяжелее, то давление вверху принимают близким к атмосферному
(130–150 кПа).
Характерные сечения колонны: верх колонны, сечение под та- релкой первого циркуляционного орошения, под тарелкой вывода фракции дизельного топлива, эвапарационное пространство и низ ко- лонны.
Температуру ввода отбензиненной нефти принимают равной
350–370 °С и определяют долю отгона при давлении эвапарационного пространства.
207
Далее находят температуры всех дистиллятов и остатка колон- ны. Количество водяного пара, подаваемого в низ атмосферной ко- лонны, 1–4 мас. % на мазут. В стриппинги – 4–6 мас. % от отводимой через стриппинг фракции.
Следующий шаг – расчет давления в каждом характерном сече- нии колонны, а также в местах отвода дистиллятов.
Затем составляют тепловой баланс колонны и рассчитывают количество тепла, которое надо снять орошением (острым и цирку- ляционным).
Диаметр колонны определяют в нескольких сечениях. Если рас- считанные диаметры в разных сечениях существенно различаются, то колонну принимают состоящей из частей с разными диаметрами, если нет, то диаметр колонны принимают равным наибольшему рас- четному значению.
6.6.3. Колонна стабилизации
Данную колонну рассчитывают по той же методике, что и от- бензинивающую колонну. Стабилизационная колонна отличается от последней большим давлением в сепараторе, т.к. в ректификате находятся газы С1–С4. Выше и кратность орошения (примерно 3–4).
6.6.4. Колонна вторичной перегонки бензина
Расчет ведут по методике стабилизационной колонны.
6.6.5. Технологический расчет блока вакуумной перегонки
Этот блок имеет ряд специфических особенностей. Как и для атмосферной части, расчет начинают с выбора типа и числа тарелок. Рекомендуются клапанные или ситчатые тарелки с отбойными эле- ментами. В последние годы широко внедряются регулярные насадки (они обладают низким гидравлическим сопротивлением).
Общее число тарелок в укрепляющей секции – 16 (топливный вариант) или 20 (масляный вариант).
208
Давление в верху колонны принимают равным 5,33–6,66 кПа (40–50 мм рт. ст.) и с учетом перепада давления на тарелках находят давление в характерных сечениях.
Температуру нагрева мазута обычно задают в интервале 390– 420 °С. Далее определяют долю отгона (аналитическим или графи- ческим методом).
Особенностью работы вакуумной колонны является то, что с верху ее в паровой фазе не отбирается дистиллят, а весь поток паров конденсируется с помощью верхнего циркуляционного орошения. С верха колонны уходит водяной пар, легкие газойлевые фракции, углеводородный газ, образовавшийся при крекинге мазута, инертный газ, СО2, Н2S.
Температуру верха вакуумной колонны обычно принимают рав-
ной 60–80 °С.
Важным элементом вакуумной колонны является ее конденса-
ционно-вакуумсоздающая система (рис. 6.6).
Эта система состоит из четырех ступеней.
1 ступень – верхнее циркуляционное орошение, с помощью ко- торого конденсируются пары легкого газойля, но не конденсируется водяной пар. Температура паров над тарелками верхнего циркуляци-
онного орошения 60–70 °С.
2 ступень – выносные конденсаторы воздушного и водяного ох- лаждения, в которых вынесенные из колонны водяные и углеводо- родные пары должны быть сконденсированны с максимальной пол- нотой.
3 ступень – барометрический конденсатор смешения, в кото- ром за счет прямого контакта с водой конденсируются наиболее лег- кие углеводороды (недостатком является загрязнение воды нефте- продуктами и необходимость ее очистки). Позднее барометрический конденсатор был заменен на закрытую абсорбционную систему. В этом случае углеводороды поглощаются абсорбентом (тяжелое ди- зельное топливо).
209
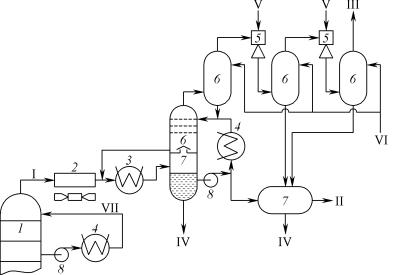
Рис. 6.6. Схема конденсационно-вакуумсоздающей системы АВТ:
1 – вакуумная колонна; 2, 3 – воздушный и водяной конденсаторы паров; 4 – водяной холодильник; 5 – паровой эжектор; 6 – абсорбер;
7 – сепаратор; 8 – насос.
I – парогазовая смесь; II – фракция легкого газойля; III – неконденсируемые газы; IV – конденсат водяного пара; V – водяной пар; VI – абсорбент;
VII – верхнее циркуляционное орошение
4 ступень – вакуумный насос (эжектор), обычно имеющий 2 или 3 ступени. В водяных конденсаторах этих ступеней (абсорберах) так- же конденсируется часть углеводородов за счет повышения давления от рабочего (5–6 кПа) до атмосферного (100–105 кПа) (в случае аб- сорберов часть неконденсируемых углеводородных газов поглощает- ся абсорбентом).
6.7. Перегонка нефти с ректификацией
Задачей прямой перегонки нефти является не только разделение ее на фракции, но и обеспечение заданных свойств этих фракций (по фракционному составу и физико-химическим свойствам). Для этого паровая и жидкая фаза, получаемые в ходе однократного испа-
210