
Аэрокосмическая техника высокие технологии и инновации – 2015
..pdf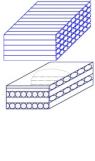
напряжениям, что в целом снижает ресурс конструкции. Среди дефектов, полученных в результате сверления, отслоение является основным. Как указывают T.L. Wong и др. [2], а также Stone R. и др. [3], в авиационной промышленности отказ деталей, состоящих из углепластиков, из-за расслоения, обусловленного процессами сверления и фрезерования, достигает 60 %.
Виды ориентации волокон
№ |
Название структуры |
Угол укладки, |
|
Схема армирова- |
|
п/п |
армирования |
(анизотропии), град |
|
ния |
|
1 |
Однонаправленная |
0 |
|
|
|
|
(Одноосно-армированнные) |
|
|
|
|
|
|
|
|
|
|
2 |
Ортотропная |
|
|
|
|
|
(продольно-поперечная, |
±90 |
|
|
|
|
двуосно-армированная) |
|
|
|
|
|
|
|
|
|
|
3 |
Трансверсально-изотропная |
±30 |
|
|
|
|
(транстропная) |
±45 |
|
|
|
|
|
±60 |
|
|
|
|
|
|
|
|
|
Лезвийная механическая обработка деталей из ПКМ вызывает в основном следующие проблемы:
1.Сложность получения высокого качества обработанной поверхности (отсутствие сколов, расслоений и вырывов волокна, необходимой шероховатости) из-за ярко выраженной анизотропии свойств и низкой адгезионной связи наполнителя со связующим ПКМ.
2.Низкая теплопроводность материала, обусловливающая плохой отвод теплоты из зоны резания.
3.Интенсивное абразивное воздействие твердого наполнителя, что приводит к низкой стойкости инструмента (в основном износ по задней поверхности).
4.Низкая производительность процесса из-за невысоких скоростей резания, так как недопустимо применение смазочноохлаждающей жидкости на водной основе (СОЖ), вследствие влагопоглощающих свойств ПКМ.
181
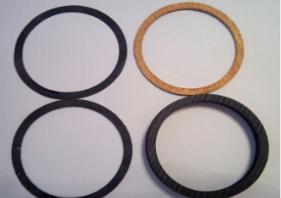
5. Выделение летучих токсичных частиц ПКМ при обработке.
Совместно с кафедрой ИТМ ПНИПУ были проведены исследования процессов лезвийной обработки ПКМ [4, 6]. Одним из направлений повышения эффективности нами был выбран для изучения процесс обработки ПКМ на гидроабразивной и лазерной установке. Произведена резка образцов из ВКУ-29, ВКУ-39 и ВПС-33 на лазерной установке с охлаждением зоны резания азотом, а также резка на установке гидроабразивной резки (необходимо отметить, что при резке на установке гидроабразивной резки использовалось меньшее давление подачи воды, была слита вода из ванны, а также использовались добавки, оказывающие водоотталкивающие действие). Результаты обработки образцов из ПКМ представлены на рис. 1.
Рис. 1. Вид образцов из ВКУ-29 и ВПС-33, изготовленных на гидроабразивной и лазерной установках
При изучении полученных первых образцов было выявлено следующее:
1. При гидроабразивной резке:
– полностью отсутствуют сколы, вырывы армирующего волокна и трещины на торцах, которые появляются при лезвийной обработке;
182
–почти полностью исчезло выделение токсичных веществ, сопровождающее процесс лезвийной обработки;
–отсутствует износ режущего инструмента, происходит равномерный износ расходных материалов;
–отсутствуют оплавленные участки связующего, что обусловлено низкой температурой в зоне резания;
–шероховатость обработанной поверхности соответствует установленным требованиям;
–возможность обрабатывать ПКМ с металлическими армирующими наполнителями;
–при получении отверстий полностью исчез дефект отслоения (является основным при сверлении);
– повысилась производительность процесса обработки
в1,5 раза, а трудоемкость в нормо-часах снизилась на 40 %;
–возможность применения только ограниченной номенклатуры деталей по форме;
–отсутствует возможность открытия глухих отверстий.
2. При лазерной резке:
–также полностью отсутствуют сколы, вырывы армирующего волокна и трещины на торцах, которые появляются при лезвийной обработке;
–незначительно уменьшилось выделение токсичных веществ, сопровождающих процесс лезвийной обработки (требуется применение дополнительной вентиляции);
–отсутствует износ режущего инструмента, происходит равномерный износ расходных материалов;
–остаются оплавленные участки с подтеками связующего, что обусловлено высокой температурой в зоне резания (необходимо доработать систему охлаждения);
–шероховатость обработанной поверхности соответствует установленным требованиям;
–возможность обрабатывать ПКМ с металлическими армирующими наполнителями;
–при получении отверстий полностью исчез дефект отслоения (является основным при сверлении), но появились дефекты на выходе отверстия в виде наплыва связующего;
183
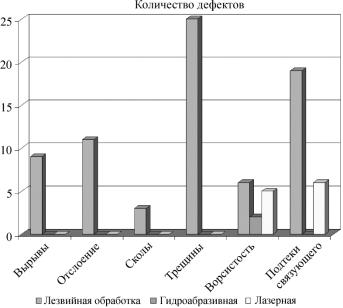
– повысилась производительность процесса обработки
в1,7 раза, трудоемкость в нормо-часах снизилась на 60 %;
–возможность применения только ограниченной номенклатуры деталей по форме;
–такжеотсутствуетвозможностьоткрытияглухихотверстий. Соотнесем количество дефектов и количество изготовлен-
ных деталей и препрега ВПС-33. Полученные данные представлены на диаграмме (рис. 2).
Рис. 2. Диаграмма соотношения количества дефектов и количества 50 обработанных деталей из препрега ВПС-33
Таким образом, на основании полученных результатов можно сделать вывод о том, что применение установок гидроабразивной и лазерной резки позволяет повысить качество изготовления деталей из ПКМ (как ячеистых, так и слоистых), а также повысить производительность в среднем в 1,5 раза. При гидроабразивной резке отсутствует термическая деструкция
184
матрицы, возможность резки конструкций большой толщины. Остается опасность насыщения композита водой. При лазерной резке достигаются малая ширина реза, высокая скорость резки, обработка маложестких деталей. Недостатки: термическая деструкция матрицы, выделение токсиного дыма и пыли. Ультразвуковая обработка показала высокую точность, низкую шероховатость, отсутствие или минимальное расслоение материала. Ее недостатками являются низкая производительность, быстрый износ дорогостоящего инструмента.
Важной задачей остается решение проблем, связанных с получением глухих отверстий, а также обработкой объемных
икрупногабаритных деталей. В данной статье рассмотрены пути
ивозможности повышения эффективности лезвийной обработки деталей из ПКМ.
Для исследования процессов повышения эффективности обработки использовали предложенную В.М. Ярославцевым [5] модель систематизации улучшения процессов резания. Теперь перейдем к дальнейшему изучению процессов обработки высокопрочных ПКМ.
Основной проблемой, возникающей при обработке деталей из ПКМ, является отслоение и ворсистость армирующих волокон. Исследование технологии обработки деталей из ПКМ методом лезвийной обработки показало, что требуется использование инструмента с очень острой режущей кромкой, большим задним углом и малым радиусом режущей кромки для обеспечения среза волокон с низкой шероховатостью рабочих поверхностей для улучшения отвода стружки и снижения сил трения между поверхностями инструмента и заготовки. Кроме того, важно обеспечить высокую стойкость инструмента, поскольку армирующие волокна и компоненты матрицы ПКМ могут интенсивно изнашивать и разрушать режущую кромку, что приводит к увеличению силы резания и тепловыделения, а также снижению качества обработанных поверхностей. В качестве инструментальных материалов, обеспечивающих приемлемую изно-
185
состойкость, используют твердые сплавы, твердые сплавы с упрочняющими покрытиями, кубический нитрид бора, поликристаллические спеченные и CVD-алмазы. Перспективным является инструмент с алмазными, получаемыми по технологии CVD, и алмазоподобными (АПП) покрытиями. В ходе изучения процесса механической обработки ПКМ было выявлено, что радиус режущей кромки для обработки деталей из ВПС-33 (0,002–0,003 мм) может применяться в два раза больше, чем при обработке деталей из ВКУ-29 (0,0007–0,001 мм). Влияния размера заднего угла не было выявлено, в среднем он составляет 15°. Скорость резания при обработке деталей из ВПС-33 оптимально составляет 1000 м/мин, а для обработки деталей из ВКУ29 оптимальной является скорость 150–500 м/мин. Величина подачи при обработке деталей из ВПС-33 оптимально составляет 0,05–0,25 мм/об, а для обработки деталей из ВКУ-29 оптимальной является подача 0,01–0,15 мм/об.
При сверлении деталей из ПКМ применяют скорости резания 100–200 м/мин при низких подачах в диапазоне 0,02–0,1 мм/об, ана входе и выходе сверла для устранения расслаивания снижают величину подачи.
Заключение
Полученный опыт при обработке изделий из ПКМ показал, что эффективность обработки можно значительно повысить, если при изготовлении ПКМ учитывать не только требуемые свойства получаемой конструкции, но и то, каким образом будет обрабатываться полученный ПКМ.
В работе были рассмотрены основные проблемы обработки ПКМ. Выявлено, что основным способом обработки ПКМ является лезвийная механическая обработка, способы гидроабразивной резки эффективны, но не всегда целесообразны (как правило, из-за габаритов изделий), а резка на плазменных и лазерных установках недопустима из-за невысокой температуры плавления связующих смол, что приводит к выделению токсичных веществ.
186
При решении задач повышения эффективности обработки предприятиями совместно с кафедрой инновационных технологий машиностроения ПНИПУ были проведены исследования по таким направлениям, как: обработка ПКМ абразивным трением при сверлении; точение кожухов из ВПС-33 с технологическими заполнителями (парафин, пластмасса, вода); повышение скорости резания и увеличение сечения срезаемого слоя (но, как правило, свойства ПКМ не позволяют применять высокие скорости резания); метод точения с предразрушением срезаемого слоя [7]; кинематические методы (вибрационное резание при сверлении панелей ЗПК авиационных двигателей, сверление и фрезерование на роботе «Кука»); криогенная обработка (охлаждение жидким азотом при использовании уже существующей технологии, которая используется при термической обработке в вакуумных печах). Необходимо завершить и отработать применение специально спроектированного многолезвийного инструмента с поликристаллическим алмазным покрытием.
Процесс механической лезвийной обработки ПКМ в настоящее время целиком не изучен. Для выполнения современных требований к обработке ПКМ нет возможности использовать систематизированные рекомендации, известны лишь частные решения. Все существующие эмпирические зависимости не учитывают анизотропные свойства обрабатываемых ПКМ. Основной целью проводимых исследований является повышение эффективности обработки ПКМ на основе разработки и исследования технологических возможностей, новых путей стабилизации динамики процесса механической обработки изделий из ПКМ.
Проведение данных исследований, применение на практике методов более эффективной механической обработки композитов позволяет существенно повысить производительность и качество обработки изделий на машиностроительных предприятиях, а также снизить затраты на обработку.
187
Библиографический список
1.Drilling of Fibre Reinforced Plastic Laminates / L.M.P. Durao, A.G. Magalhaes, A.T. Marques, A.M. Baptista, M. Figueiredo // Materials, Science Forum. – 2008. – Vol. 587–588. – P. 706–710.
2.Wong T.L., Wu S.M., Croy G.M. An analysis of delamination in drilling composite materials // 14 th National SAMPE technology conference.-Atlanta, GA, USA, 1982.
3.Stone R., Krishnamurthy K. A neural network thrust force controller to minimize delamination during drilling of graphiteepoxy laminates // Int. J Mach Tools Manuf. – 1996.
4.Макаров В.Ф., Мешкас А.Е., Ширинкин В.В. Исследование процессов механической обработки деталей авиационно-космичес- кой техники из новых композиционных материалов // Новые материалыитехнологиивмашиностроении. – 2015. – Вып. 22.
5.Ярославцев В.М. Разработка методологии поиска новых методов обработки и ее практическая реализация // Вестник МГТУ им. Н.Э. Баумана. – 2007. – С. 56–70.
6.Мешкас А.Е., Ширинкин В.В., Макаров В.Ф. Исследование современных процессов механической обработки деталей авиационно-космической техники из новых композиционных материалов // Новые технологии: материалы XII Всерос. конф., посвященной 70-летию победы / РАН. – М., 2015 – Т. 2. – С. 65–73.
7.Ярославцев В.М. Высокоэффективные технологии обработки изделий из композиционных материалов: учеб. пособие. – М.: Изд-во МГТУ им. Н.Э. Баумана. 2012. – С. 4–6.
8.Каталог: Инструментальные решения Sandvik Coromant Россия/СНГ / ООО «Сандвик». – 2014. – С. 2–8.
9.Марков А.М. Технологические особенности механической обработки деталей из композиционных материалов // Наукоемкие технологии в машиностроении. – 2014. – №7. – С. 3–5.
10.Оценка структурных дефектов углеродных волокон и полимерных композиционных материалов на их основе: учеб. пособие / Ю.М. Миронов, Ю.В. Храповицкая, М.О. Макеев, В.А. Нелюб. – М.: Изд-воМГТУим. Н.Э. Баумана. – 2011. – С. 1–2.
188
11.Комков М.А., Тарасов В.А. К изучению дисциплины «Технология производства композитных конструкций ракетнокосмической техники»: учеб. пособие. – М.: Изд-во МГТУ им.
Баумана, 2012. – С. 1–5.
12.Ричардсон М. Промышленные полимерные композиционные материалы / под ред. П.Г. Бабаевского. – М.: Химия, 1980. – С. 472.
13.Перепелкин К.Е. Армирующие волокна и волокнистые полимерные композиты. – М.: Научные основы и технологии, 2009. – С. 658.
14.Нильсен Л. Механические свойства полимеров и полимерных композиций. – М.: Химия, 1978. – 310 с.
15.Полимерные композиционные материалы. Прочность
итехнологии / С.Л. Баженов, А.А. Берлин, А.А. Кульков, В.Г. Ошмян. – М.: Интеллект, 2009. – 352 с.
16.Полимерные композиционные материалы. Свойства. Структура. Технологии / под ред. А.А. Берлина. – СПб.: Про-
фессия, 2009. – С. 560.
189
УДК 621.91
ОБРАБОТКА ДЕТАЛЕЙ РКТ С НАЛИЧИЕМ СЛОЖНЫХ ПОВЕРХНОСТЕЙ
В.М. Хилько, А.А. Ильченко, Т.Г. Орешенко
АО «Красноярский машиностроительный завод», Красноярск, Россия e-mail: Anael_fire@list.ru
Рассматривается последовательность разработки технологии изготовления изделий ракетно-космической техники (РКТ). Приводится пример использования современных программных средств. Рассмотрены основные этапы разработки управляющих программ для станков с ЧПУ. Показано применение CAD/CAM-систем при обработке сложных поверхностей.
Ключевые слова: CAD-система, CAM-система, верификация, постпроцессор.
Современное машиностроение предполагает функционирование многочисленных взаимосвязанных технических средств различных объектов производства на основе компьютерной техники, современного оборудования с числовым программным управлением и применение САПР конструкторско-техноло- гического назначения. Подготовка УП, обеспечивающих 3-, 4-
и5-осевую обработку, вручную становится очень трудоемкой
ипрактически невыполнимой. В настоящее время в производство широко внедряются программные продукты САПР – системы
CAD/CAM/CAE, обеспечивающие сквозное проектирование. В качестве объекта разработки представлены детали с наличием сложных поверхностей. Подобные детали преимущественно изготавливаются для изделий ракетно-космической отрасли и судостроения. При разработке технологии изготовления и управляющей программы использовано лицензионное программное обеспечение: CAD-система SolidWorks и CAM-система
MasterCAM, с модулем MasterCAM Multi-Axis, позволяющим
190