
Аэрокосмическая техника высокие технологии и инновации – 2015
..pdf
превращаются в поры. Увеличение микрозародышей пузырьков
вобъеме происходит в жидком металле в результате диффузии
вних водорода, растворенного в металле. В пузырьках атомарный водород переходит в молекулярную форму и создает в них определенное давление, уравновешивающееся внешним давлением, оказываемым на пузырек, таким образом, данный процесс оказывается направлен на установление равновесия в системе газ – металл. Для этого должно быть соблюдено условие
H k pH ,
где H – концентрация растворенного в жидком металле водорода, см3/100 г; pH – давление водорода в пузырьке макрораз-
меров; k – константа, зависящая от температуры.
Давление водорода в пузырьке должно уравновешиваться внешним давлением. В период, когда размер поры мал, она будет оставаться сферической, благодаря силе поверхностного натяжения. При росте пор в междендритном пространстве, форма поры будет заметно отличаться от сферической вследствие неодновременности затвердевания основного металла и включений [2] (рисунок).
Рассмотрим подробнее механизм электронно-лучевой сварки. Предположим, что одиночный газовый пузырек диаметром D0 находитсявжидкомметаллеванны. Дальнейшееповедениепузырька будет определяться архимедовой силой и равнодействующей сил поверхностного натяжения в неоднородно нагретой жидкости. Кроме того, пузырек будет перемещаться вместе с движением металла сварочной ванны, характер которого зависит от формы и размеровванны, местарасположенияпузырькаидругихфакторов.
В большинстве литературы динамику всплытия пузырька рассматривают без учета нестационарных связей, однако данный эффект играет важную роль в ряде многих процессов, отмеченных ранее. В связи с этим была проведена теоретическая оценка формы пузырька в различных режимах всплытия с учетом нестационарных сил.
141
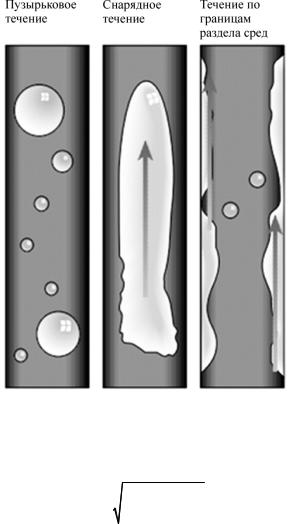
Рис. Влияние течения на форму газового пузырька при его подъеме в сварочной ванне
Диаметр пузырька при всплытии
D0 |
3 |
18 ж2 |
, |
||
ж ( ж |
г )g |
||||
|
|
|
где µж – динамическая вязкость жидкости; ρг – плотность газа (пузырька); ρж – плотность жидкости, в которой находится пузырек; g – ускорение свободного падения.
Поскольку температура в сварочной ванне распределяется неравномерно, то движущийся пузырек будет попадать в зоны с различной температурой, что приведет к изменению скорости
142
его всплывания, так как входящие в формулу величины плотности и вязкости зависят от температуры расплава.
|
|
|
|
|
|
|
|
|
|
ж a b(T Tпл ), |
|
||||
|
|
|
|||||
|
|
c |
d |
, |
|
||
|
|
|
|
||||
|
|
T 2 |
|||||
|
|
|
d |
|
|
||
|
|
|
|
|
|
||
|
пл |
|
(T Tпл ). |
||||
|
dT |
||||||
|
|
|
|
|
|
||
Здесь a,b,c,d, |
d |
– коэффициенты, зависящие от типа ме- |
|||||
dT |
|||||||
|
|
|
|
|
|
талла или сплава; Tпл, пл – температура и поверхностное натя-
жение в точке плавления, К.
Исходя из вышесказанного можно сделать вывод, что изменение любых технологических параметров сварочного процесса, приводящее к увеличению градиента температуры при перемещении поры в сварном шве, будет приводить к отклонению ее формы от сферической. Вследствие этого можно путем изменения параметров процесса контролировать рост и форму образующихся пор для улучшения качества сварных соединений.
Библиографический список
1.Зусин В.Я., Серенко В.А. Сварка и наплавка алюминия и его сплавов. – Мариуполь: Рената, 2004. – 468 с.
2.Legait P-A. Formation and distribution of porosity in Al-Si welds / A thesis submitted to the faculty of the Worcester polytechnic institute in partial fulfillment of the requirements for the degree of masters of science in material science and engineering. – May 2005.
3.Plasma – MJY boots tank trailer output. Welding Design and Fabrication. – 1983. – Vol. 56, no. 2, – P. 54–55, 59.
4.Николаев В.А., Фридляндер И.Н., Арбузов Ю.П. Свариваемые алюминиевые сплавы. – М.: Металлургия, 1990. – 296 с.
5.Оура К., Лифшиц В.Г., Саранин А.А. Введение в физику поверхности. – М.: Наука, 2006. – 490 с.
143
УДК 62.03
УСОВЕРШЕНСТВОВАНИЕ ТЕХНОЛОГИЧЕСКОГО ПРОЦЕССА ИЗГОТОВЛЕНИЯ КОМПОЗИТНЫХ МАТЕРИАЛОВ
С ИСПОЛЬЗОВАНИЕМ КОМПОНЕНТОВ ВЫСОКОТЕМПЕРАТУРНОГО ОТВЕРЖДЕНИЯ
М.Н. Драганюк, В.Г. Маханьков
Сибирский государственный аэрокосмический университет имени академика М.Ф. Решетнева, Красноярск, Россия
e-mail: midraganyuk@yandex.ru
Общей целью работы является техническое и технологическое обеспечение производства изделий из композитных материалов (стеклопластики, углепластики) в условиях ограниченной оснащенности, с целью достижения максимально низкой стоимости изготовления изделий. Работа направлена на проведение экспериментальных исследований, целью которых является оптимизация технологического процесса изготовления композитных материалов (КМ). Для проведения экспериментов был разработан, изготовлен и проверен на работоспособность сушильный шкаф, предназначенный для высокотемпературного отверждения изделий из КМ при температуре до 200 ºС согласно технологическому процессу.
Ключевые слова: композитные материалы, высокотем-
пературное отверждение КМ, SolidWorks, Flow Simulation, су-
шильный шкаф.
В современном мире композитные материалы заменяют металлы в областях, в которых они применялись в течение долгого времени. Корпусные элементы самолетов, ракет, надводных судов, выполненные из композитных материалов, успешно применяются наряду с аналогичными изделиями из металла [1, 2]. Однако промышленное производство изделий из композитных материалов – достаточно дорогой и трудоемкий процесс. Основной целью проекта является максимальная оптимизация технологии изготовления такихКМ, какстеклопластикииуглепластики.
144
Основными целями работы являются:
1)определение марки смолы и отвердителя, которые в оптимальной пропорции обеспечивают максимальные механические характеристики;
2)определение оптимальной программы нагрева при отверждении;
3)определение влияния пластификаторов в различных пропорциях на механические характеристики получаемого КМ;
4)анализ и синтез полученных данных [3].
В первую очередь была создана модель сушильного шкафа для изготовления деталей из композитных материалов с возможностью использования компонентов высокотемпературного отверждения. Для этого 3D-модель будущего изделия была проанализирована в среде SolidWorks Flow Simulation, которая является частью системы автоматизированного проектирования SolidWorks. На основе проведенных анализов был изготовлен сушильный шкаф, представленный на рисунке.
Конструкция сушильного шкафа позволяет проводить термическую обработку изделий из композитных материалов размерами не более 1400×400×350 мм (Д×Ш×В). Такие габариты позволяют осуществлять как одновременное изготовление нескольких небольших изделий, так и отверждение довольно крупных.
Нагревательным элементом изготовленного изделия являются шесть галогеновых ламп мощностью 1500 Вт каждая. Подключение выполнено последовательно-параллельно с расчетной суммарной мощностью 3000 Вт и с возможностью увеличения рабочей мощности до 4500 Вт. Данное ограничение связано с тем, что использование установки большей мощности может повлечь проблемы, связанные с повышением тока в бытовых источниках электропитания выше расчетного. Регулирование температуры осуществляется пропорционально-интегро-диффе- ренцирующим (ПИД) регулятором, обеспечивающим нагрев по заданной программе, а также поддержание температуры.
145
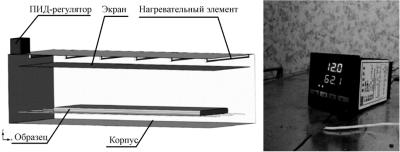
В процессе сборки и наладки шкафа была выявлена проблема, которая заключается в больших тепловых потерях, обусловленных большой наружной поверхностью шкафа (3,5 м2). Температура внутри достигала лишь 60–70 ºС, при расчетной 180 ºС.
Первоначальным решением этой проблемы было использование высокотемпературного герметика. Это обеспечило дополнительную герметизацию соединений и технологических отверстий. Однако данный способ лишь немного улучшил результаты, позволив добиться температуры в 90 ºС. В дальнейшем было принято решение о применении теплоизоляционных материалов на основе минеральной ваты для обшивки внутренней поверхности духового шкафа. Минеральная вата зашивалась с помощью вязальной проволоки в брикеты из алюминиевой фольги, после чего крепилась на внутренние стенки шкафа. Использование этого метода позволило повысить рабочую температуру до необходимых значений.
Рис. Схема сушильного шкафа (а) и ПИД-регулятор (б)
В результате был изготовлен сушильный шкаф, который позволяет получать изделия из композиционных материалов с использованием компонентов высокотемпературного отверждения в условиях с ограниченной оснащенностью. Стоимость данного оборудования оказалась низкой при условии самостоятельного изготовления. Намечены основные пути развития работы, поставлены задачи на ближайшее будущее.
146
Библиографический список
1.Буланов И.М., Воробей В.В. Технология ракетных и аэрокосмических конструкций из композитных материалов. – М.: Изд-во МГТУ им. Н.Э. Баумана, 1998. – 514 с.
2.Гардымов Г.П., Мешков Е.В., Пчелинцев А.В. Композиционные материалы в ракетно-космическом аппаратострое-
нии. – СПб.: Спецлит, 1999. – 272 с.
3.Любин Дж. Справочник по композиционным материалам. – М.: Машиностроение, 1988. – 447 с.
147
УДК 533.69
ЧИСЛЕННОЕ МОДЕЛИРОВАНИЕ ОБТЕКАНИЯ ТАНДЕМА ЦИЛИНДРОВ
Е.В. Сорокин
Пермский национальный исследовательский политехнический университет, Пермь, Россия
e-mail: evgensorokin92@gmail.com
Проведен газодинамический анализ обтекания тандема цилиндров дозвуковым потоком воздуха. Выполнена верификация расчетных данных с экспериментом NASA и получено качественно правильное описание ряда параметров потока при обтекании тандема цилиндров с учетом использования RANS модели турбулентности в 2D-постановке.
Ключевые слова: тандем цилиндров, численное моделирование, RANS модель турбулентности, газодинамические характеристики.
Снижение шума в гражданской авиации является актуальной задачей. Как известно, различают два основных источника шума самолета – шум от двигателя и аэродинамический шум. В настоящее время шум двигателей настолько уменьшился, что ненамного превышает аэродинамический шум. Поэтому не менее актуальной задачей становится изучение аэродинамического шума.
Аэродинамический шум обтекания планера самолета обусловлен пульсациями аэродинамических сил на крыле, турбулентным пограничным слоем и вихрями, образующимися при обтекании поверхностей крыла, фюзеляжа и хвостового оперения, а также турбулентными следами за плохо обтекаемыми выступами. При заходе на посадку, при выпущенных стойках шасси и отклоненных предкрылках и закрылках основные источники шума обусловлены срывом потока из-за этих выступающих в поток элементов.
148
Ввычислительной аэроакустике существует два основных подхода: прямое численное моделирование и гибридные методы. Поскольку во многих случаях требуется вычисление флуктуирующей части давления, определяющей акустическую компоненту, на расстояниях, значительно превышающих характерный размер исследуемого тела, то подход, связанный с прямым численным моделированием шума, является неэффективным. Альтернативой является определение уровня шума интегральными методами, которые представляют собой двухэтапные методы, основанные на раздельном расчете генерации шума и его распространения. На первом этапе производится газодинамический расчет, в процессе которого информация о нестационарных характеристиках потока сохраняется на так называемых контрольных поверхностях. На втором этапе с использованием этой информации производится расчет распространения звука до положения слушателя с помощью соответствующих интегральных формул или акустических аналогий.
Внастоящей работе был проведен первый этап и апробирована методика моделирования турбулентного обтекания тандема цилиндров и расчета газодинамических характеристик, необходимых для дальнейшего аэродинамического расчета. Результаты расчета сравнивались с экспериментальными данными, полученными в NASA [1]. Отметим, что для данной тестовой задачи помимо результатов натурного эксперимента имеется значительный объем результатов вычислительных экспериментов, проводившихся различными исследователями [2, 3].
При проведении вычислительного эксперимента использовалась двумерная прямоугольная расчетная область с размерами 2×1,4 м. Геометрия расчетной области, обтекаемых цилиндров и адаптивная сетка были построены в пакетах ANSYS CFX и ICEM CFD. Дополнительно выполнялось сгущение сетки вблизи поверхности цилиндров. Все ячейки сетки являются гексаэдрами. Общее количество ячеек в двумерном случае составляло 79834. Расчетная область задачи представлена на рис. 1.
149
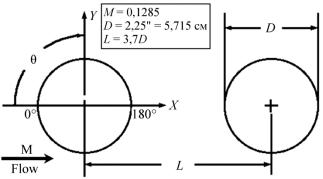
Рис. 1. Расчетная схема обтекания тандема цилиндров
В расчете использовались следующие исходные данные: скорость набегающего потока V = 44 м/с, число Рейнольдса Re = 1,66·105, плотность ρ = 1,2047 кг/м3, динамическая вязкость µ = 1,8369·10–5 Па·с. Диаметр цилиндра D = 0,05715 м, расстояние между центрами цилиндров составляет 3,7D. Шаг расчета по времени был принят равным 10–5 с. Общее время счета составляло 0,5 с. Значения невязок 10–7. Число Куранта не превышало значения Cu = 0,5. На входе в расчетную область задавалась скорость набегающего потока 44 м/с и значения параметров модели турбулентности исходя из степени турбулентности потока = 1 %; на выходе – давление = 0; для значений параметров турбулентности на стенках цилиндра использовались пристеночные функции, а также условия прилипания и непротекания.
Расчет проводился с использованием модели турбулентности k–w SST. Данная модель является разновидностью стандартной k–w-модели и была разработана Ментером. Данная модель эффективно сочетает устойчивость и точность стандартной k–w-модели впристеночныхобластяхиk–e-моделинаудаленииотстенок.
Результатами вычислительного эксперимента, которые использовались для сравнения с данными эксперимента, являются:
1. Коэффициент лобового сопротивления для первого и второго цилиндров.
150