
Аэрокосмическая техника высокие технологии и инновации – 2015
..pdfТак, при значении φ = 2 и 4 В плотность тока i остается постоянной в течение эксперимента, что может свидетельствовать о растворении материала в активном состоянии. При значении φ = 6 и 8 В наблюдается снижение плотности тока с течением времени, чтоможет подтверждатьпассивацию поверхностианода.
Библиографический список
1.Электронно-лучевая наплавка в вакууме: оборудование, технология, свойства покрытий / В.Е. Панин, С.И. Белюк, В.Г. Дураков [и др.] // Сварочное производство. – 2000. – № 2. –
С. 34–38.
2.Гнюсов С.Ф., Дураков В.Г., Гнюсов К.С. Вакуумная элек- тронно-лучевая наплавка карбидосталей. I. Особенности технологии наплавки и подготовки композиционных наплавочных смесей // Сварочное производство. – 2007. – № 11. – С. 8–12.
3.Янюшкин А.С., Шоркин В.С. Контактные процессы при электроалмазном шлифовании. – М.: Машиностроение-1, 2004. – С. 217–229.
4.Рахимянов Х.М., Янпольский В.В. Анодное растворение быстрорежущей стали Р6М5 и ее составляющих в водных растворах // Сб. науч. тр. Новосибирского государственного технического университета. – 2003. – № 4. – С. 141–147.
5.Янпольский В.В., Козич Т.В. Электрохимическое растворение покрытий из порошковых материалов // Инновации в машиностроении: тр. 4-й междунар. науч.-практ. конф., Новосибирск, 2–4 октября2013 г. – Новосибирск: Изд-во НГТУ, 2013. – С. 74–78.
6.Электрохимическое растворение покрытий из порошковых материалов / А.Н. Моисеенко, Х.М. Рахимянов, М.И. Никитенко, В.В. Янпольский, Б.А. Красильников // Обработка металлов: Технология. Оборудование. Инструменты. – 2011. – №2 (51). – С. 3–5.
7.Рахимянов Х.М., Моисеенко А.Н., Янпольский В.В. Электроалмазная обработка напыленных износостойких покрытий // Инженерия поверхностного слоя деталей машин: сб. тр. Междунар. науч.-практ. конф., г. Кемерово, 9–11 декабря 2009 г., Кеме-
рово: Изд-во КузГТУ, 2009. – С. 365–369.
221
УДК 621.791.947.55
ОСОБЕННОСТИ ИЗНОСА КАТОДА ПРИ ТОНКОСТРУЙНОЙ ПЛАЗМЕННОЙ РЕЗКЕ
А.А. Локтионов, Н.П. Гаар, С.Ю. Десятов, Е.В. Малахов
Новосибирский государственный технический университет, Новосибирск, Россия
e-mail: loktionov@corp.nstu.ru
Работа посвящена исследованию износа катода при тонкоструйной плазменной резке конструкционной стали Ст.3 толщиной 20 мм. Определено, что после прохождения катодом свыше 80 м реза и совершении 320 пробивок он подвергается катастрофическому износу. Глубина износа тугоплавкой вставки при этом составляет 1,8 мм.
Ключевые слова: расходные элементы плазмотрона, тонкоструйная плазменная резка, катод, износ.
Катод при тонкоструйной плазменной резке является одним из расходных элементов плазматрона [1]. Его функция заключается в создании плазменной дуги в процессе обработки, так как он является одним из электродов. Таким образом, в процессе обработки он испытывает постоянное температурное воздействие, и на нем протекают эмиссионные процессы. И хотя катод состоит из корпуса и запрессованного в него тугоплавкой вставки, он подвержен постоянному износу.
Износ катода отрицательно сказывается на возможности протекания самого процесса обработки в целом [2]. При выходе его из строя в результате катастрофического износа невозможно получить в первоначальный момент поджиг плазменной дуги, а соответственно, и начало развития процесса разделения материала. Если такое состояние катода «проглядеть» при обработке сложноконтурной детали, то прекращение горения дуги в процессе обработки в любом, неизвестном наперед месте контура
222
может привести к браку. С другой стороны, необходимость смены катода в результате такого износа в процессе резки сопряжена с необходимостью вывода плазматрона на исходную позицию и корректировки процесса после его смены. Это потребует увеличения времени изготовления изделия. Если же износ еще не катастрофичен, но близок к этому, то на детали возможно получение брака в виде недорезов, «рваных» кромок реза. Таким образом, своевременная замена катода позволяет не только получить изделия заданной точности, но и не увеличить время на изготовления изделия. Однако литературных источников по рассматриваемому вопросу практически нет, что делает данную тему актуальной для производства, в том числе в авиастроении, где применяются листовые конструкции.
Определение ресурса катода производилось на машине термической резки Термит ППл, реализующей технологию тонкоструйной плазменной резки (HiFocus 130i, производства Германии), установленной на кафедре технологии машиностроения НГТУ. Для эксперимента был выбран катод S002х, предназначенный для резки большого спектра конструкционных сталей и сплавов на основе меди и алюминия. В качестве обрабатываемого материала был использован листовой прокат из конструкционной стали Ст.3 толщиной 20 мм. Эксперимент проводился при производственном раскрое деталей различной конфигурации из выбранного материала с регистрацией для каждого из катодов, участвующих в эксперименте, количества пробивок и пройденного пути. В эксперименте участвовало 4 катода при одинаковых режимах резки: ток резки 130А при скорости резки 1 м/мин.
Катодом № 1 было пройдено 5 м пути и 15 пробивок. После прохода указанного пути и пробивок внешний вид катода практически не изменился. Катодом № 2 было пройдено 84 м реза и совершено 314 пробивок. Катодом № 3 было пройдено 80 м реза и совершено 320 пробивок. Катодом № 4 было пройдено 82 м реза и совершено 330 пробивок. По прохождении указанной длины пути и величины пробивок были произведены смены катодов из-за прекращения процесса поджига дуги, т.е. произо-
223
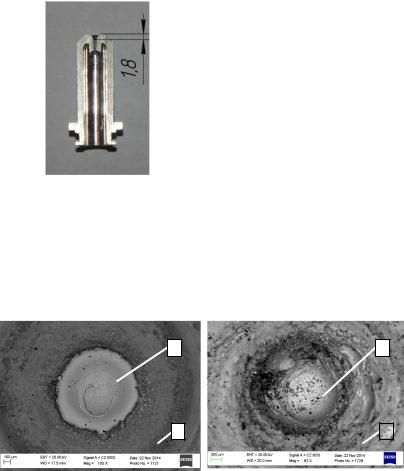
шел катастрофический износ катода. Для всех катодов, достигших катастрофического износа, перед прекращением поджига
|
дуги наблюдалось |
изменение |
|
шумового фактора резки с появ- |
|
|
лением характерного свиста. |
|
|
Внешний вид одного из катодов |
|
|
(катод № 2), подверженного ка- |
|
|
тастрофическому износу, пред- |
|
|
ставлен на рис. 1. |
|
|
Проведенные |
измерения |
|
катодов с катастрофическим из- |
|
|
носом показали, что глубина |
|
Рис. 1. Катод с критическим |
износа тугоплавкой вставки для |
|
износом тугоплавкой вставки |
всех исследуемых катодов равна |
|
|
1,8 и более миллиметров. |
Для сопоставления внешнего вида катода после незначительного износа (катод № 1) и после катастрофического износа (катод № 3) при помощи растровой электронной микроскопии были сделаны снимки внешнего вида (рис. 2).
1 |
1 |
2 |
|
2 |
Катод № 1 |
Катод № 3 |
Рис. 2. Внешний вид тугоплавкой вставки катода с разной степенью износа: 1 – тугоплавкая вставка; 2 – корпус катода
Анализ полученных снимков указывает на тот факт, что при незначительном износе тугоплавкой вставки ее поверхность остается на прежнем уровне, без видимого заглубления и про-
224
дуктов реакции (от процесса горения плазменной дуги). Внешний вид катода с катастрофическим износом указывает на значительное заглубление тугоплавкой вставки в тело корпуса катода и образование на вставке продуктов горения. Кроме того, наблюдается разрушение корпуса катода.
Таким образом, катастрофический износ катода S002х при тонкоструйной плазменной резке конструкционной стали Ст.3 толщиной 20 мм наступает после прохода 80 и более метров реза при количестве пробивок более 315. При этом величина катастрофического износа тугоплавкой вставки составляет 1,8 мм. Следовательно, насколько катод близок к катастрофическому износу, можно косвенно определить, измерив величину его выработки, если нет возможности оценить количество пройденного пути и совершенных им пробивок. Кроме того, еще одним косвенным признаком того, что в ближайшее время произойдет катастрофический износ катода, т.е. процесс резки будет прекращен, может служить изменение шум-фактора процесса резки с доминированием характерного свиста.
Библиографический список
1.Рахимянов Х.М., Локтионов А.А. Разновидности катодов, применяемых для плазменной резки, и влияние степени износа их на точность формообразования // Проблемы повышения эффективности металлообработки в промышленности на современном этапе: материалы 10-й Всерос. науч.-практ. конф. – Но-
восибирск, 2012. – С. 68–71.
2.Рахимянов Х.М., Локтионов А.А. Влияние износа расходных элементов на точность формообразования при тонкоструйной плазменной резке // Обработка металлов (технология, оборудование, инструменты). – 2011. – № 4. – С. 14–18.
225
УДК 621.9.01; 621.791.947.55
ЛАЗЕРНО-ЭЛЕКТРОХИМИЧЕСКАЯ ОБРАБОТКА ТРУДНООБРАБАТЫВАЕМЫХ МАТЕРИАЛОВ
Н.П. Гаар, А.А. Локтионов, Н.В. Герасимов, К.А. Солодовников
Новосибирский государственный технический университет, Новосибирск
e-mail: gaar@corp.nstu.ru
Описаны особенности лазерно-электрохимической обработки. На основе экспериментальных данных показана возможность повышения производительности электрохимической обработки представителей труднообрабатываемых материалов (нержавеющей стали, титанового сплава, вольфрамо-кобальто- вого сплава) при использовании лазерно-электрохимической обработки.
Ключевые слова: лазерно-электрохимическая обработка, электрохимическое растворение, труднообрабатываемые токопроводящие материалы.
Лазерно-электрохимическая размерная обработка является разработкой кафедры технологии машиностроения Новосибирского государственного технического университета [1]. Отмечена Серебрянной медалью XL Международного салона Inventions Geneva 2012 г. Данный способ обработки различных токопроводящих материалов является одним из направлений развития электрохимической размерной обработки. Перспективность ла- зерно-электрохимической обработки подтверждена экспериментами, приведенными в работах [2–5].
Данный способ обработки может использоваться в различных отраслях промышленности для изготовления деталей из труднообрабатываемых токопроводящих материалов, в том числе в аэрокосмической промышленности.
226
Особенность лазерно-электрохимической обработки материала заключается в следующем. Токопроводящий материал электрохимически растворяется под действием электрического тока в токопроводящей среде. Введение лазерного излучения в зону обработки, непосредственно на обрабатываемый материал или в межэлектродное пространство в зависимости от сочетания обрабатываемого материала и рабочей среды (электролита), позволяет получить целую гамму механизмов активации процесса растворения [6]. Правильный выбор сочетания параметров лазерного излучения и электрохимической системы (состав электролита, напряжение), в свою очередь, приведет к тому, что в месте введения лазерного излучения, благодаря полученным эффектам, произойдет увеличение скорости электрохимического растворения материала. При этом необходимая для активации электрохимического растворения мощность лазерного излучения рассчитывается [7] и такова, что при данном способе обработки не происходит ни существенного изменения структуры обрабатываемого материала, ни даже закипания электролита.
Перспективность предлагаемой лазерно-электрохимичес- кой обработки [1] заключается в том, что используемое лазерное излучение содержит в себе не одну, а несколько длин волн (инфракрасного и ультрафиолетового спектра излучения) в одном пучке. Такое сочетание длин волн позволяет задействовать большее число механизмов активации электрохимического растворения, по сравнению с применением одной длины волны, что подтверждается и данными работы [8].
Экспериментальные исследования по лазерно-электрохи- мической обработке таких труднообрабатываемых материалов, как вольфрамо-кобальтовый сплав ВК-8 и нержавеющая сталь 12Х18Н9Т, показали, что скорость электрохимического растворения возросла в 34 [4] и 33 [9] раза по сравнению с традиционной электрохимической обработкой соответственно. Для титанового сплава ОТ-4 применение лазерно-электрохимической обработки позволило добиться электрохимического растворения
227
материала с приемлемой скоростью в электролитах, в которых при традиционной электрохимической обработке растворения не наблюдалось [3].
Все экспериментальные исследования реализовались на специально спроектированной установке, описанной в работах
[10, 11].
Библиографический список
1.Пат. 2451582 Российская Федерация, МПК 54 B23H5/00, B23K28/02, B23H3/00, B23K26/00. Способ размерной обработки металлов и сплавов / Х.М. Рахимянов, А.И. Журавлев, Н.П. Гаар, А.А. Локтионов; заявитель и патентообладатель: Новосиб.
гос. техн. ун-т. – № 2010128204/02; заявл. 07.07.2010; опубл. 27.05.2012; Бюл № 15. – 11 с.
2.Рахимянов Х.М., Гаар Н.П. Анодное поведение компонентов нержавеющей стали в условиях лазерной интенсификации // Инновации в машиностроении: материалы 2-й Междунар. науч.-практ. конф. – Кемерово, 2011. – С. 157–160.
3.Анодное поведение титанового сплава марки ОТ-4 при интенсификации лазерным излучением процесса электрохимического растворения / Х.М. Рахимянов, К.Х. Рахимянов, А.И. Журавлев, Н.П. Гаар, А.А. Локтионов // Обработка металлов (технология, оборудование, инструменты). – 2011. – № 2. –
С. 11–13.
4.Рахимянов Х.М., Гаар Н.П. Электрохимическая обработка твердого сплава ВК8 в условиях лазерного воздействия длинной волны 1,06 мкм в хлориде натрия // Проблемы повышения эффективности металлообработки в промышленности на современном этапе: материалы 9-й Всерос. науч.-практ. конф. – Но-
восибирск, 2011. – С. 77–79.
5.Рахимянов Х.М., Гаар Н.П. Анодное поведение хрома
вводном растворе хлорида натрия при интенсификации лазерным излучением процесса электрохимического растворения //
Механики XXI века. – 2010. – № 9. – С. 41–43.
228
6.Рахимянов Х.М., Рахимянов К.Х., Гаар Н.П. Оценка механизмов активации процесса электрохимической размерной обработке нержавеющей стали // Обработка металлов (технология, оборудование, инструменты). – 2010. – № 3. – С. 19–21.
7.Рахимянов Х.М., Гаар Н.П. Математическое моделирование при лазерной термоактивации электрохимической раз-
мерной обработке // Современные технологические системы в машиностроении: материалы Междунар. науч.-техн. конф. –
Барнаул, 2006. – С. 45–47.
8.Летохов В.С. Селективное действие лазерного излучения на вещество // Успехи физических наук. – 1978. – Т. 125, № 1. –
С. 57–96.
9.Гаар Н.П. Анодное поведение нержавеющей стали 12Х18Н9Т в условиях лазерной активации процесса электрохимической размерной обработки // Наука. Технологии. Инновации: материалы Всерос. науч. конф. молодых ученых. – Новоси-
бирск, 2010. – С. 262–264.
10.Рахимянов Х.М., Журавлев А.И., Гаар Н.П. Установка для исследования электрохимических процессов в условиях лазерной активации процесса электрохимической размерной обработки // Научный вестник НГТУ. – 2010. – № 2. – С. 135–144.
11.Установка для исследования материалов в условиях ла- зерно-электрохимической обработки комбинированным излучением / Х.М. Рахимянов, Б.А. Красильников, Н.П. Гаар, А.И. Журавлев, А.А. Локтионов // Обработка металлов (технология, оборудование, инструменты). – 2012. – № 3. – С. 30–32.
229
УДК 669.017:539.4; 669.017:539.52
СТРУКТУРНЫЕ И МЕХАНИЧЕСКИЕ АСПЕКТЫ ФОРМИРОВАНИЯ ПОЛОС АДИАБАТИЧЕСКОГО СДВИГА
М.А. Соковиков, Д.А. Билалов, В.А. Оборин, В.В. Чудинов, С.В. Уваров, О.Б. Наймарк
Институт механики сплошных сред УрО РАН, Пермь, Россия e-mail: sokovikov@icmm.ru
Проведено экспериментальное и теоретическое исследование механизмов локализации пластического сдвига при динамическом деформировании металлов. Механизмы связываются с коллективными эффектами в ансамбле микродефектов в пространственно-локализованных областях. Инфракрасное сканирование in-situ зоны неустойчивости и последующее изучение дислокационной субструктуры подтвердили предположение о решающей роли неравновесных переходов в ансамблях дефектов при развитии локализованного пластического течения. На основе уравнений, отражающих связь неравновесных переходов с механизмами структурной релаксации и пластического течения, проведено моделирование локализации пластической деформации.
Ключевые слова: локализация пластической деформации, полосы адиабатического сдвига, динамическое нагружение, микродефекты, численное моделирование.
Длительное время доминирующим объяснением механизма неустойчивости и локализации пластической деформации при высоких скоростях нагружения было представление о термопластической неустойчивости. Предполагалось, что тепло, выделяемое в процессе пластической деформации, за малые характерные времена не успевает отводиться, что приводит к термическому разупрочнению и дальнейшему росту пластической деформации. Реализуется лавинообразный процесс, приводящий к скачкообразному росту температур в области локализации
230