
Аэрокосмическая техника высокие технологии и инновации – 2015
..pdfС целью своевременного обнаружения дефектов в модулях МРС был разработан способ оперативной диагностики, с помощью которого можно оценить техническое состояние каждого модуля МРС и определить наличие и место дефекта в модуле.
В основе способа лежат положения вибродиагностики – движение любого модуля МРС характеризуется колебаниями, причем в зависимости от динамических свойств элементов и их технического состояния амплитуда и частота колебаний будет разная. Колебания модулей МРС приводят к колебаниям инструмента и заготовки при резании, что влияет на такие показатели качества обработки, как погрешность формы (волнистость) и шероховатость поверхности. Суммарная погрешность формы обработанной детали является диагностическим признаком разработанного способа.
Способ реализуется в соответствии со структурной схемой, представленной рисунке. На основании требований к МРС предварительно должен быть получен обобщенный спектр (эталонный), определяющий допустимый уровень амплитуд и диапазон частот, соответствующих допускаемым погрешностям формы (волнистости) и шероховатости обработанной поверхности детали. Текущий спектр колебаний получают во время обработки детали по информации с вибродатчиков, установленных на деталях модулей МРС. Полученный спектр сравнивают с эталонным и по отклонению определяют наличие и место дефектов в модуле МРС.
Для определения характерных частот, в которых проявляются погрешности изготовления модулей МРС, необходимо произвести моделирование колебаний инструмента и заготовки с учетом технических условий на точность изготовления и сборки модулей МРС и внешних возмущающих воздействий, которые соответствуют возможным дефектам изготовления и сборки модулей станка. Таким образом получают расчетный спектр колебаний. Поиск причины отказа проводится в определенном диапазоне частот путем идентификации частоты возмущения с доминирующей частотой, вызывающей отказ в данном частотном диапа-
131
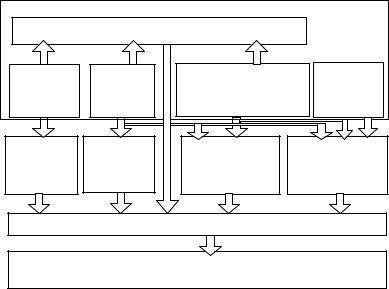
зоне. Такое представление обеспечивает возможность оперативной оценки технического состояния модулей станка непосредственно по результатам его работы. В процессе диагностики устанавливают две основные причины параметрического отказа:
1.Отказ в связи с изменением технических условий изготовления деталей приводов, в результате чего амплитуды отдельных гармоник расчетного спектра выходят за допустимый уровень эталонного спектра.
2.Отказ в связи с несоблюдением технических условий сборки станка, в результате чего амплитуды отдельных гармоник расчетного и фактического спектра погрешности формы (волнистости) и шероховатости обработанной поверхности детали превышают амплитуду эталонного спектра.
Рис. Структурная схема способа оперативной диагностики модулей МРС
Диагностика технического состояния приводов МРС в соответствии с предложенным способом позволяет:
132
1)оперативно определить источники дефектов в модулях станка и разработать мероприятия по их устранению;
2)дать рекомендации на разработку научно обоснованных технических условий на изготовление и сборку узлов многоцелевого станка на этапе проектирования.
Предложенный способ позволяет определить источники дефектов в приводах станка, при его кратковременной остановке
иминимальной разборке, а также разработать мероприятия по их устранению.
Библиографический список
1.Идрисова Ю.В., Кудояров Р.Г., Фецак С.И. Диагностика приводов металлообрабатывающих станков с автоматическим управлением: учеб. пособие для вузов. – Уфа: УГАТУ, 2013. – 153 с.
2.Перевертайло Ю.В., Кудояров Р.Г., Фецак С.И. Определение параметрических отказов станочного оборудования //
СТИН. – 2007. – № 11. – С. 9–13.
3.Зависимость показателей качества обработанной детали
от состояния динамической системы станка / С.И. Фецак, Р.Г. Кудояров, Ю.В. Идрисова, Р.Р. Башаров // СТИН. – 2015. –
№ 7. – С. 12–16.
133
УДК 533: 621.455
ИССЛЕДОВАНИЕ ЭЛЕКТРОГИДРАВЛИЧЕСКОЙ СИСТЕМЫ УПРАВЛЕНИЯ ГАШЕНИЕМ В РАКЕТНОМ ДВИГАТЕЛЕ ТВЕРДОГО ТОПЛИВА
А.Б. Бачурин, Е.В. Стрельников, В.А. Целищев
Уфимский государственный авиационный технический университет, Уфа, Россия
e-mail: e_strelnikov@mail.ru
Для решения одной из актуальных задач современной ра- кетно-космической отрасли, а именно – мгновенное гашение и повторный запуск твердотопливной двигательной установки, авторами проводятся исследования комбинированной электрогидравлической системы управления, сочетающей в себе подсистему поддержания постоянного давления в камере сгорания и подсистему регулирования впрыска жидкого хладагента. В статье представлены модели подсистем регулирования и приведены результаты переходных процессов в ракетном двигателе твердого топлива (РДТТ) при их комбинированном использовании.
Ключевые слова: динамическая модель, комбинированная система управления, ракетный двигатель твердого топлива, регулятор расхода, рулевая машина, тяга; хладагент.
Основной целью исследования является получение системы уравнений, описывающих работу структурно-подобных РДТТ, дальнейшее моделирование которой на ЭВМ позволит решать задачи анализа и синтеза динамических параметров систем автоматического регулирования (САР).
На рис. 1 представлены схемы подсистем регулирования комбинированной САР РДТТ, разработанной в ФГБОУ ВПО УГАТУ [1].
В состав подсистем регулирования входит: пневмогидроаккумулятор (ПГА), измеритель электрического сигнала рассогла-
134
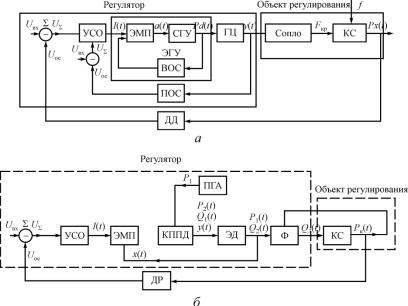
сования ( ), электронный усилитель сигнала ошибки (УСО), электромеханический преобразователь сигнала (ЭМП), электромагнитный дроссель (ЭД), клапан постоянного перепада давления (КППД), форсунка (Ф), датчик расхода хладагента из ПГА (ДР), струйный гидроусилитель (СГУ), гидроцилиндр (ГЦ), датчик давления (ДД), потенциометрический датчик обратной связи по перемещению центрального тела (ПОС) и объект регулирования – камера сгорания (КС).
Рис. 1. Функциональная схема подсистемы регулирования:
а– площади критического сечения сопла Fкр ;
б– расхода жидкого хладагента
Математические модели подсистем регулирования (давления и расхода хладагента) выглядят следующим образом:
а) для подсистемы регулирования впрыска жидкого хладагента в камеру сгорания:
135

|
|
|
|
|
|
|
|
|
|
|
|
|
|
|
|
|
|
|
|
|
|
|
|
|
|
diдр (t) |
|
|
dx(t) |
|
||||||
(Uдр |
kосQдр (t))Kу Rдрiдр (t) Lдр |
|
|
|
|
|
Kпэ |
|
|
|
|
, |
||||||||||||||||||||||||
|
|
dt |
|
|
dt |
|||||||||||||||||||||||||||||||
|
|
|
|
|
|
|
|
|
|
|
|
|
|
|
|
|
|
|
|
|
|
|
|
|
|
|
|
|
|
|
|
|||||
|
|
|
|
d 2 x(t) |
|
|
|
|
|
|
|
|
|
dx(t) |
|
|
|
|
|
|
|
|
|
|
|
|
|
|||||||||
|
|
|
|
|
|
|
|
|
|
|
|
|
|
|
|
|
|
|
|
|
|
|
|
|
|
|
||||||||||
mдр |
|
|
|
dt2 |
K fiдiдр (t) b др |
dt |
cдрx(t), |
|
|
|
|
|
|
|||||||||||||||||||||||
|
|
|
|
d |
2 y |
|
|
(t) |
|
|
|
|
|
|
|
|
|
|
|
|
|
dy |
|
(t) |
|
|
|
|
|
|
|
|
||||
|
m |
|
к |
A( p (t) p (t)) |
b |
|
к |
c y (t), |
|
|
|
|||||||||||||||||||||||||
|
|
|
|
|
|
|
|
|
|
|
|
|
|
|
||||||||||||||||||||||
|
к |
|
|
|
dt |
2 |
|
|
|
2 |
|
3 |
|
|
|
|
k |
|
dt |
|
к к |
|
|
|
|
|
|
|||||||||
|
|
|
|
|
|
|
|
|
|
|
|
|
|
|
|
|
|
|
|
|
|
|
|
|
|
|
|
|
|
|
||||||
|
|
|
|
|
|
|
|
|
|
|
|
2( p1 p2 (t)) |
|
|
|
|
|
|
|
|
|
|
2( p2 (t) p3 (t)) |
|
||||||||||||
кbк yк (t) |
|
|
|
|
|
|
дрbдрx(t) |
|
|
|
|
|
|
|
|
|
|
|||||||||||||||||||
|
|
|
ж |
|
|
|
|
ж |
|
|
|
|
|
|||||||||||||||||||||||
|
|
|
|
|
|
|
|
|
|
|
|
|
|
|
|
|
|
|
|
|
|
|
|
|
|
|
|
|
|
|
|
|
|
|||
|
|
|
W |
|
dp (t) |
A |
|
dy (t) |
|
|
|
|
|
|
|
|
|
|
|
|
|
|
|
|
|
|
|
|
||||||||
|
|
|
|
0 |
|
|
|
|
2 |
|
|
|
к |
, |
|
|
|
|
|
|
|
|
|
|
|
|
|
|
|
|
|
|
|
|||
|
|
|
|
|
|
|
|
|
|
dt |
|
|
|
|
|
|
|
|
|
|
|
|
|
|
|
|
|
|
|
|||||||
|
|
|
2E dt |
|
|
|
|
|
|
|
|
|
|
|
|
|
|
|
|
|
|
|
|
|
|
|
|
|||||||||
|
|
|
|
b x(t) |
|
2( p2 (t) p3 (t)) |
|
|
|
|
|
|
|
|
|
|
|
|
|
|
|
|
||||||||||||||
|
|
|
|
|
|
|
|
|
|
|
|
|
|
|
|
|
|
|
||||||||||||||||||
|
|
|
|
|
|
|
|
|
|
|
|
|
|
|
|
|
|
|
|
|
||||||||||||||||
|
|
др |
|
|
др |
|
|
|
|
|
|
|
ж |
|
|
|
|
|
|
|
|
|
|
|
|
|
|
|
|
|
|
|
|
|||
|
|
|
|
|
|
|
|
|
|
|
|
2( p3 (t) pк t ) |
W0 dp3 (t) , |
|
|
|
|
|
|
|
|
|||||||||||||||
|
|
|
F N |
|
|
|
|
|
|
|
|
|||||||||||||||||||||||||
|
|
|
|
|
|
|
|
|
|
|
|
|
||||||||||||||||||||||||
|
|
|
|
ф |
|
ф |
|
|
|
|
|
|
|
ж |
|
|
|
|
|
2E |
|
dt |
|
|
|
|
|
|
|
|
|
|||||
|
|
|
|
|
|
|
|
|
|
|
|
|
|
|
|
|
|
|
|
|
|
|
|
|
|
|
|
|
|
|
||||||
V |
|
|
|
d |
|
|
|
|
|
|
|
|
RT |
|
с A(k)Fкр |
|
|
|
|
k |
1 |
|
||||||||||||||
|
|
|
св |
|
|
|
|
|
pк (t) тSu(t) |
|
v |
k |
|
|
|
|
|
|
|
pк (t) |
|
|
|
|
HхYх (t); |
|||||||||||
|
|
|
|
|
dt |
|
|
|
|
|
RTк |
|
RTк |
|||||||||||||||||||||||
RTк |
|
|
|
|
|
|
|
|
RTк |
|
|
|
|
|
|
|
|
|||||||||||||||||||
|
|
|
|
|
|
|
|
|
|
|
|
|
|
|
|
|
|
|
|
|
|
|
|
|
|
|
|
|
|
|
|
|
|
|
|
|
б) для подсистемы регулирования давления в камере сгорания Fкр :
|
|
|
|
|
|
|
|
|
di(t) |
Kпэ |
d (t) |
Kу Uвх Kос pк (t) , |
||||||||||||||
Rэмпi(t) L |
dt |
|
|
dt |
|
|||||||||||||||||||||
|
|
|
|
|
|
|
|
|
|
|
|
|
|
|
|
|
|
|
|
|
||||||
|
|
|
|
|
|
|
Uвх |
|
|
|
|
|
|
|
|
|
|
|
|
|
|
|
||||
|
где K |
|
|
|
|
|
, |
|
|
|
|
|
|
|
|
|
|
|
|
|
||||||
|
ос |
|
|
|
|
|
|
|
|
|
|
|
|
|
|
|
|
|
|
|
||||||
|
|
|
|
|
pк max |
|
|
|
|
|
|
|
|
|
|
|
|
|
||||||||
|
|
|
|
|
|
|
|
|
|
|
|
|
|
|
|
|
|
|
|
|
||||||
|
|
2 (t) |
|
|
|
|
|
|
|
|
|
|
|
|
|
|
|
|
|
|
|
|
||||
J d |
K |
|
|
i(t) K |
|
|
(t) b |
d (t) |
C |
|
(t), |
|||||||||||||||
|
|
dt2 |
|
|
|
|
|
mi |
|
|
|
m |
|
|
|
m |
|
dt |
|
эмп |
|
|||||
|
W |
|
|
A y(t) |
|
|
|
dp |
|
(t) |
A |
dy(t) |
|
|
|
|
||||||||||
|
|
|
|
|
|
|
|
|
||||||||||||||||||
0 |
|
|
|
|
|
|
|
|
Cн |
|
d |
|
|
|
|
|
|
|
||||||||
|
|
|
|
|
E |
|
|
|
|
|
|
|
|
dt |
|
|
dt |
|
|
|
|
|
||||
|
|
|
|
|
|
|
|
|
|
|
|
|
|
|
|
|
|
136
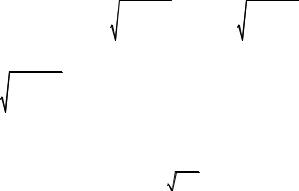
|
|
|
|
|
|
|
1 |
|
|
|
|
|
p |
d |
(t) |
|
|
|
|||
|
mQт |
|
|
(1 |
z |
(t)) 1 |
|
|
|
|
(1 |
||||||||||
|
|
Pm |
|||||||||||||||||||
|
|
Q |
|
|
|
|
2 |
|
|
|
|
|
|
|
|
||||||
|
|
|
|
|
|
|
|
|
|
|
|
|
|
|
|
|
|
|
|
||
|
при z (t) zn , |
|
|
|
|
|
|
|
|
|
|
||||||||||
|
|
|
|
|
|
pd (t) |
|
|
|
|
|
|
|
|
|
|
|
|
|||
|
|
1 |
|
, |
при zmax z (t) zn , |
|
|
|
|||||||||||||
|
|
|
|
|
|
||||||||||||||||
|
|
|
|
|
|
|
Pm |
|
|
|
|
|
|
|
|
|
|
|
|||
|
|
|
|
|
|
|
|
|
|
|
|
|
|
|
|
|
|
|
|
|
|
|
d 2 y(t) |
Ap |
(t) |
b |
dy(t) |
F |
|
С |
|||||||||||||
m |
dt2 |
|
|
|
dt |
|
|
|
|||||||||||||
|
|
|
|
|
|
d |
|
п |
|
|
|
тр |
|
п |
|||||||
dpк (t) |
|
|
|
1 |
|
|
|
|
|
|
|
|
|
|
|
|
|
||||
|
|
|
|
|
|
|
|
|
|
|
|
|
|
|
|
|
|
|
|
||
|
dt |
|
|
V |
|
|
|
|
|
|
|
|
|
|
|
|
|
||||
|
|
|
|
|
|
|
св |
|
|
|
|
|
|
|
|
|
|
|
|
|
|
|
|
|
f y(t) |
p |
(t) p (t)Su(t) |
. |
|||||||||||||||
(F |
|
||||||||||||||||||||
|
кр |
|
|
|
|
|
|
|
к |
|
к |
|
|
|
|
|
|
||||
Общие уравнения: |
|
|
|
|
|
|
|
|
|
||||||||||||
|
|
u(t) u1 pк (t) , |
pк (t) тRTк , |
z (t)) 1 |
|
pd (t) |
|
Pm |
|||
|
|
y(t),
dVdtсв Su(t).
) ,
Основные параметры и коэффициенты, используемые в моделях подсистем регулирования, полностью описаны в источнике [2].
По результатам моделирования комбинированной САР с учетом моделей (1) и (2) были получены графики переходных процессов (рис. 2).
Как видно из графиков, управление гашением происходит по заранее заданной программе. Необходимая величина внутрикамерного давления устанавливается через 0,05 с при расходе хладагента 3,4·10–4 м3/с. В момент времени t = 2 с, при достижении уровня давления, соответствующего значению минимально необходимого, регулятор расхода хладагента (РР) уменьшает расход. Гидроагрегат РР отрабатывает управляющее воздействие на изменение расхода хладагента из форсунок. Через 0,1 с устанавливается заданный расход хладагента. Благодаря регулированию расхода хладагента с помощью РР и изменению Fкр
с помощью рулевой машины устанавливается необходимая ве-
137
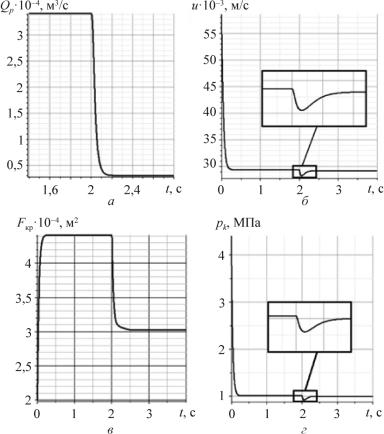
личина давления, скорости горения и газоприхода. Давление в двигателе стабилизируется за 0,2 с без перерегулирования и поддерживается на заданном уровне, позволяющем сократить время повторного запуска. Рулевая машина успевает отрабатывать возмущение, и на величине давления в камере сгорания изменение расхода хладагента из форсунок не сказывается, т.е. качество работы регуляторов в САР не зависит друг от друга.
Рис. 2. Переходные процессы в электрогидравлической системы управления гашением РДУ: а – изменение расхода хладагента через регулятор; б – изменение скорости горения; в – изменение площади критического сечения сопла; г – изменение давления в камере
138
Таким образом, была получена математическая модель комбинированной системы управления, удовлетворяющая требованиям мгновенного гашения РДТТ (за (0,03–0,05) с) и позволяющая сократить время подготовки двигателя к повторному запуску, за счет поддержания в камере сгорания минимального необходимого давления.
Библиографический список
1.Пат.2443895 РФ, МПК F02K9/92 F02K9/86. Регулируе-
мый ракетный двигатель твердого топлива / Ю.М. Ахметов, А.Б. Бачурин, Е.В. Стрельников, В.А. Целищев. Заявл. 02.09.2010; опубл. 27.02.2012.
2.Электрогидравлическая система управления гашением твердотопливной двигательной установки / А.Б. Бачурин, Е.С. Литвинов, В.А. Целищев, Е.В. Стрельников // Вестник УГАТУ. – 2015. – Т. 19, № 3 (69). – С. 81–91.
139
УДК 621.791
ИЗМЕНЕНИЕ ФОРМЫ ПОР ПОД ДЕЙСТВИЕМ ТЕХНОЛОГИЧЕСКИХ ПАРАМЕТРОВ
ПРИ ЭЛЕКТРОННО-ЛУЧЕВОЙ СВАРКЕ
Т.Г. Орешенко, О.П. Якубович
АО «Красноярский машиностроительный завод», Красноярск, Россия e-mail: veisver@mail.ru
Электронно-лучевая сварка (ЭЛС) – процесс получения неразъемных соединений, широко применяемый в аэрокосмической отрасли. Авторами рассмотрено влияние технологических параметров процесса на форму пор при ЭЛС. Показана возможность контроля роста и формы образующихся пор путем изменения параметровпроцессадляулучшениякачествасварныхсоединений.
Ключевые слова: пористость, сварка, электронный луч, сварочная ванна, алюминиевые сплавы.
Порообразование в металле шва при сварке относится к сложным физико-химическим явлениям. Его развитие протекает в несколько стадий: формирование зародышей газовых пузырьков, развитие пузырьков в объеме сварочной ванны в процессе диффузии и коалесценции, дегазации ванны за счет всплывания пузырьков [1]. Возникновение пористости в шве существенно снижает прочность сварных соединений корпусных конструкций, полученных электронно-лучевой сваркой, что негативно сказывается на надежности изделий в целом, что недопустимо
вракетно-космической технике.
Впромышленном алюминии и сплавах на его основе имеют-
ся готовые зародыши |
пузырьков. Поэтому образование пор |
в алюминиевых сплавах |
зачастую следует рассматривать как |
процесс развития микрозародышей в пузырьки макроразмеров. Микрозародыши возникают в междендритном пространстве, в местах расположения включений, примесей, легирующих элементов. После кристаллизации оставшиеся в металле пузырьки
140