
Аэрокосмическая техника высокие технологии и инновации – 2015
..pdf
упрочняющая вибрационная обработка (ВиОУО), отделочноупрочняющая центробежно-ротационная обработка (ОУЦРО), обработки дробью (ОД).
При исследовании основных технологических параметров методов отделочно-упрочняющей обработки гибкой гранулированной средой (ОУО ГГС) – производительности процесса и качества обработанной поверхности – одним из важнейших является вопрос теоретического моделирования процесса единичного взаимодействия частиц среды (стальных полированных шариков) с поверхностью обрабатываемой детали. Разработка теоретических зависимостей, описывающих форму и размеры следов обработки, позволяет в дальнейшем перейти к теоретиковероятностному описанию распределения следов на поверхности детали, что, в свою очередь, дает возможность разработать модель формирования профиля шероховатости и физикомеханических свойств поверхности детали.
Величина деформации поверхностного слоя в значительной степени определяется физико-механическими свойствами материала обрабатываемой детали, а также количеством взаимодействий, приходящихся на каждую точку обрабатываемой поверхности [1]. Контактные напряжения, возникающие в зоне обработки под действием шарика, зависят не только от усилия соударения, но и от его размера и высоты исходных микровыступов.
Контактная поверхность, вследствие ее зависимости от угла соударения и формы исходной шероховатости, имеет сложную пространственную форму. В случае обработки стальными полированными шариками представляется возможным принять эллипсоидную форму номинальной контактной поверхности. Это значительно упрощает дальнейшие теоретические расчеты.
Глубину внедрения шарика можно определить по зависимости
hmax 2 Vэф R sin |
ч |
|
, |
3ks c |
|
||
|
s |
51
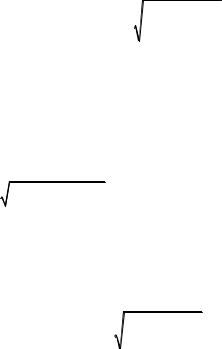
где Vэф – эффективная скорость частицы (определяется особенно-
стями конкретного вида обработки); R – радиус частицы, – угол встречи частицы с поверхностью детали; ч – плотность материала частицы; ks – коэффициент, учитывающий влияние шероховатости детали; c – коэффициент несущей способности контактнойповерхности; s – пределтекучести материаладетали.
Для обработки дробью эта зависимость выглядит следующим образом:
hmax 1,6 KL R |
Pдин ч |
, |
|
ks c s см |
|||
|
|
где Рдин – динамическое давление; KL – коэффициент потерь, учитывающий расстояние до обрабатываемой детали и плотность потока шариков (определяется при проведении экспериментальных исследований); см – плотность смеси.
Пятно контакта частицы среды с поверхностью детали представляет собой эллипс, размеры полуосей которого
b R2 R h max 2 , a 2 ctg f h max b ,
где f – коэффициент трения частицы по поверхности детали.
Среднее арифметическое отклонение профиля установившейся шероховатости при ОУО ГГС можно определить по зависимости
Ra уст k |
R |
|
hmax a b lед |
, |
|
R2 |
|||||
|
|
|
где lед – единичная длина; kR – эмпирический коэффициент.
При решении технологических задач для отделочноупрочняющих методов обработки в гранулированных средах важное значение имеет аналитический расчет ожидаемого значения глубины упрочненного слоя и степени упрочнения. Зна-
52
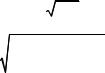
чительные исследования в этой области проведены И.В. Кудрявцевым, В.П. Пшибыльским, Е.Г., Папшевым и др. [2–4]. На основании приведенных ими зависимостей и с учетом собственных исследований можно определить глубину упрочненного слоя и степень упрочнения для обработки в гибких гранулированных средах по формулам:
|
hн 3k |
a b , |
|
|
||
|
h |
|
2 |
h |
|
, |
max |
max |
|||||
|
R |
|
|
R |
|
где k – коэффициент, зависящий от степени наклепа.
Для деталей, используемых в авиационной промышленности, большой интерес представляют усталостные испытания. Исследования были направлены на определение влияния параметров обработки на усталостную долговечность обрабатываемых образцов из различных сталей и алюминиевых сплавов, применяемых при изготовлении деталей летательных аппаратов. Установлено, что ОУО ГГС повышает усталостную долговечность деталей в 1,5–1,6 раз. Выявлены оптимальные условия обработки и технологические режимы для различных методов ОУО ГГС.
По результатам проведенных теоретических и экспериментальных исследований разработана обобщенная теория формирования параметров качества поверхностного слоя при отделоч- но-упрочняющей обработке в гибкой гранулированной среде, которая прошла комплексную экспериментальную проверку в условиях ОАО «Роствертол» и может быть использована для проектирования технологических процессов, обеспечивающих повышение качества поверхностного слоя деталей летательных аппаратов. Проведены успешные промышленные испытания на реальных деталях вертолетов. На основе предложенной обобщенной теории разработана методика оптимизации и САПР технологических процессов ОУО ГГС.
53
Библиографический список
1.Тамаркин М.А. Теоретические основы оптимизации процессов обработки деталей свободными абразивами: дис. … д-ра техн. наук. – Ростов н/Д, 1995.
2.Повышение прочности и долговечности крупных деталей машин поверхностным наклепом / И.В. Кудрявцев [и др.]. – М.: НИИИНФОРМТЯЖМАШ, 1970. – 144 с.
3.Папшев Д.Д. Отделочно-упрочняющая обработка поверхностным пластическим деформированием. – М.: Машино-
строение, 1978. – 152 с.
4.Пшебыльский В.П. Технология поверхностной пластической обработки. – М.: Металлургия, 1991. – 476 с.
54
УДК 621.9.
ПРОЕКТИРОВАНИЕ СМЕННЫХ МНОГОГРАННЫХ ПЛАСТИН ДЛЯ ТОКАРНОЙ ОБРАБОТКИ ЖАРОПРОЧНЫХ
И ТИТАНОВЫХ СПЛАВОВ
С.В. Михайлов, А.С. Михайлов, М.Ю. Глумин
Костромской государственный технологический университет, Кострома, Россия
e-mail: michsv@yandex.ru
Изложены особенности проектирования сложнопрофильных сменных многогранных пластин, работающих в условиях повышенных деформаций, сил и температур резания. Представлены результаты испытаний опытных образцов пластин при точении жаропрочных сплавов.
Ключевые слова: резание труднообрабатываемых материалов, сменные многогранные пластины, проектирование инструмента, управление стружкообразованием.
Всовременном машиностроении, особенно в авиационной
иракетной технике, все большее распространение получают жаропрочные и титановые сплавы с высокими показателями прочности и теплостойкости. Основными проблемами, с которыми приходится сталкиваться при резании таких материалов, являются: 1) высокие силы и температура в зоне резания; 2) концентрация сил резания вблизи режущей кромки; 3) цикличность
стружкообразования, склонность к вибрациям при резании; 4) интенсивное лункообразование и повышенный износ по задней поверхности; 5) большая зависимость работоспособности инструмента от скорости резания; 6) возникновение проточин на главной режущей кромке; 7) выкрашивание нерабочих кромок сходящей с резца стружкой; 8) повышенное влияние геометрии инструмента на параметры качества поверхностного слоя, в том числе на глубину наклепанного слоя и остаточные напряжения.
55
Высокая прочность и большое содержание карбидов, низкая теплопроводность, химическая активность обрабатываемых материалов с твердыми сплавами приводят к смешанному механизму абразивного, адгезионного и диффузионного износов сменных многогранных пластин (СМП). Все эти условия вызывают необходимость применения инструментов, изготовленных из твердых сплавов, обладающих более высокими режущими свойствами: высокой теплостойкостью, хорошей сопротивляемостью износу и стабильностью режущих свойств. Повышенные требования предъявляются и к геометрии инструмента, оказывающей существенное влияние на механику резания и его выходные характеристики. За счет оптимизации геометрических параметров режущих пластин достигается уменьшение силы резания и контактных давлений на рабочих поверхностях лезвия; уменьшение наклепа обработанных поверхностей деталей; уменьшение цикличности стружкообразования; повышение стойкости к лункообразованию; обеспечивается равномерность износа по длине режущей кромки; уменьшение проточин на инструменте; стабильное дробление стружки в процессе резания; устранение причин выкрашивания нерабочих кромок сходящей
срезца стружкой.
Вкачестве исходных данных построения модели сложнопрофильных пластин использовались физико-механические свойства обрабатываемого и инструментального материала, режимы резания, начальные геометрические параметры пластины
(φ, φ1, r, α). Расчет формы и размеров рабочих поверхностей СРП осуществлялись в следующей последовательности: 1) подбирались начальные геометрические параметры пластины с учетом требований к прочности режущей пластины и качества поверхностного слоя обрабатываемых изделий; 2) рассчитывались параметры зоны резания: толщина а1 и ширина b1 срезаемого
слоя, угол схода стружки , длины пластического l0 и полного l контакта стружки с передней поверхностью инструмента, угол наклона условной поверхности сдвига β1 и коэффициент утол-
56
щения стружки ka; 3) с учетом требований к форме стружки с помощью программы PrognosChip выполнялось профилирование передней поверхности СРП; 4) рассчитывалось значение минимально допустимого радиуса завивания в вертикальной плоскости; 5) рассчитывались параметры схода стружки: внешний радиус витка стружки R0, шаг спирали стружки Ph, угол наклона оси спирали стружки θ; 6) проверялось условие дробления стружки по величине критической кривизны стружки; 7) определялась ширина упрочняющей фаски f или укороченной передней поверхности f < a1; 8) рассчитывался радиус округления режущей кромки; 9) выполнялся расчет сил резания и параметров качества поверхностного слоя обрабатываемой детали. Расчетные зависимости, используемые при проектировании СМП, приведены в работе [1].
В результате проектирования и анализа различных вариантов конструкций предложена новая геометрия передней поверхности пластины с улучшенными условиями отвода стружки из зоны резания. Эффективность стружкообразования повышена за счет управления пространственным завиванием стружки. С целью дополнительного вращения стружки в боковой и поперечной плоскостях стружкозавивающая поверхность выполнена с переменным вдоль режущей кромки профилем. По мере удаления от вершины пластины формы поперечных сечений канавки изменяются от вогнутой дуги окружности до выпуклой, при этом радиусы сечений стружкозавивающей поверхности в главных секущих плоскостях меняются по закону, обратному арксинусу [2]. Твердотельные модели пластин SNMG 120412 SM, СNMG 120408 SM показаны на рисунке.
Опытные образцы пластин изготовлены на ООО «Вириал», г. Санкт-Петербург, из сплава VHS1012. Исследование работоспособности пластин проводилось на операции точения детали «Кольцо» из жаропрочного сплава ХН50ВМТЮБ-ВИ (ЭП648ВИ) на токарно-лобовом станке с ЧПУ SPR 63M. Режимы резания: скорость резания v = 25 м/мин, подача s = 0,12 мм/об, глу-
57
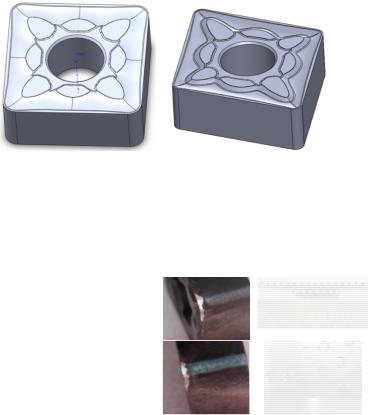
бина резания 2 мм. Время резания 130 мин. Износостойкость пластин сравнивалась с аналогом CNMG 120408-TF фирмы Iscar (таблица).
Рис. Твердотельные модели пластин
SNMG 120412 SM, СNMG 120408 SM
Результаты сравнительных испытаний СМП
№ п/п |
Пластина |
Износ, мм |
Фото износа |
Вид стружки |
1 |
CNMG 120408-TF |
0,5 |
|
|
|
IС907 |
|
|
|
|
|
|
|
|
2 |
СNMG 120408 SM |
0,5 |
|
|
|
|
|
|
|
Исследования показали, что по стойкостным характеристикам пластина CNMG120408E-SM VHS1012 сопоставима с пластиной CNMG 120408-TF IС907. В диапазоне глубин резания t = = 1,5…5 мм, подач s = 0,15…0,6 мм/об образующаяся при резании стружка имела форму, благоприятную для ее дробления при взаимодействии с вращающейся заготовкой. Переменный профиль стружкозавивающей канавки способствует более благо-
58
приятному распределению термомеханических нагрузок вдоль режущей кромки резца, следствием чего является более равномерное распределение износа СМП. Специальная форма канавки вызывает отклонение оси спирали стружки от плоскости резания, уменьшая вероятность касания стружки с неработающими кромками пластины и их выкрашивания.
Разработанная геометрия пластины может быть рекомендована для обработки нержавеющих, жаропрочных и титановых сплавов.
Библиографический список
1.Михайлов С.В. Компьютерное прогнозирование и системный анализ причинно-следственных связей процессов образования, завивания и дробления сливной стружки. – Кострома: Изд-во Костром. гос. технол. ун-та, 2009. – 159 с.
2.Патент 2237549 С1 Российская Федерация, МПК7 В 23
В27/00. Сменная режущая пластина / С.В. Михайлов, Д.С. Сквор-
цов. – №2003105381/02; заявл. 25.02.2003; опубл. 10.10.2004, Бюл. №28. – 24 с.
59
УДК 621.9.048.3
ВОЗМОЖНОСТИ ПОВЫШЕНИЯ ЭФФЕКТИВНОСТИ ГИДРОАБРАЗИВНОЙ РЕЗКИ ТОЛСТОЛИСТОВЫХ АВИАЦИОННЫХ МЕТАЛЛОВ
А.В. Верченко
Донской государственный технический университет, Ростов-на-Дону, Россия
e-mail: alex290292@mail.ru
Целью работы являлось исследование влияния режимов гидроабразивного резания на шероховатость обработанной поверхности, а также выявление основных видов дефектов данной технологии, возможности повышения эффективности процесса резания и пути уменьшения дефектов. В работе представлены экспериментальные данные, которые позволили определить возможностиисключения образованиязаусенцанаостромвнешнемугле.
Ключевые слова: гидроабразивная резка, шероховатость реза, волнистость реза, заусенец, подача.
Гидроабразивная резка – наиболее современный и эффективный способ получения как заготовок, так и деталей из толстолистовых авиационных материалов. Процесс резания происходит тонкой струей смеси воды с абразивом, испускаемой с высокой (сверхзвуковой) скоростью под высоким давлением порядка 6000 бар. В качестве абразива используется гранатовый песок с твердостью 7,5–8 (Mohs). Процесс представляет собой эрозионное разрушение под действием рабочей струи, где абразив снимает слои микростружки, а вода эвакуирует продукты из зоны резания. Основными преимуществами гидроабразивной резки являются высокая производительность при больших толщинах резания (сталь до 300 мм), отсутствие остаточных напряжений на кромке реза, возможность резания практически любых металлов и неметаллов, возможность выреза фигурных профилей и деталей сложной формы.
60