
Металлургия черных и цветных металлов
..pdfР и с. |
V.6. |
З а в и си м о с ть |
м е ж д у |
ки сл о С0],% |
||||
р од ом |
и |
у гл ер о д о м , р аств о р ен н ы м и |
||||||
в |
м е т ал л е |
м ар тен о вск о й |
п л ав к и |
Б по |
||||
д ан н ы м и ссл ед о ван и й : |
|
|
|
|
||||
/ — Г. |
Н . |
О й к са, |
Ю . |
М. |
М ак си м о ва, |
|||
Е. Л. К ал у ж с к о го ; 2 — Б . В. С т ар к а , |
||||||||
Е. |
В. |
Ч е л и щ ев а , |
3 — Г. |
Н . |
О й к са; |
|||
В — к о н ц ен тр ац и я |
к и сл о р о д а |
в м е |
||||||
т а л л е |
в р авн о веси и |
со |
ш л ак о м м а р |
|||||
тен о вско й |
п л а в к и |
|
|
|
|
|
Значение теплового эффекта невелико, и большинство ис следователей считают его слабо экзотермическим. Графическая зависимость растворенных углерода и кислорода в железе в равновесии при 1620 °С представлена гиперболой (рис. V.5).
§ 3. Возникновение и рост пузырьков монооксида углерода в расплаве металла
При малых размерах зародышевых пузырьков капиллярное давление может быть так велико, что становится непреодоли мым препятствием их образования. Сопоставление изменения давления выделения монооксида углерода рсо и внешнего дав ления рвнеш в зависимости от радиуса пузырька позволяет опре делить критический размер пузырька гкр, выше которого он устойчив и может расти (гкр>0,5-10_6 м). Для зарождения та ких пузырьков в объеме металла должно быть сильное пересы щение его кислородом, поэтому вероятность образования пу зырьков СО в металлическом расплаве очень мала. Более ве роятно образование пузырьков СО на границе фаз металл — шлак и металл — керамика.
§ 4. Кинетика окисления углерода, полировка металла, чистое кипение
Изменение содержания углерода и других составляющих ме талла и шлака представлено диаграммой плавки в период по лировки-доводки (см. рис. V.4). Присадки руды или продувка ванны кислородом интенсифицирует окисление углерода — кон
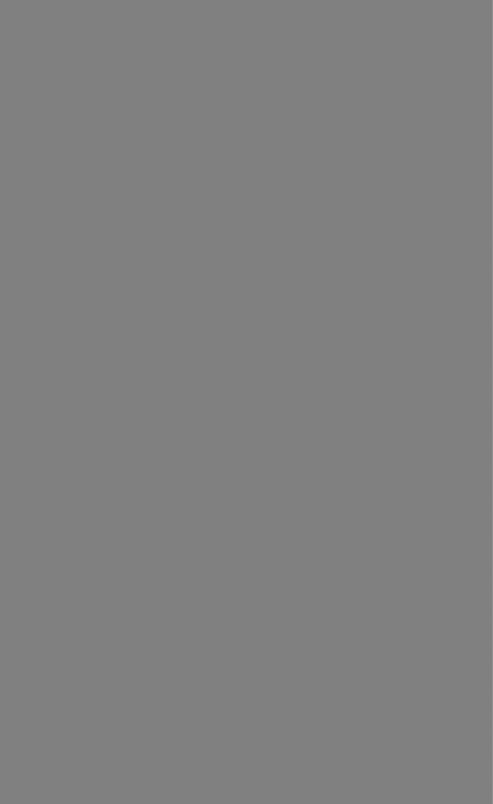
Полагаем порядок реакции по кислороду п тогда ПО]х = к , р[0];
M 3[° W M = Kx. р № |
(V.12) |
Вводим безразмерную концентрацию как отношение концентрации кислорода в данной точке [0]х к концентрации кислорода на поверхности раздела
металл —шлак у = [ 0 ] х/[0]Поъ, тогда уравнение (V.12) преобразуется
Ро Ю1п t d 2y l ( d x 2) = /Сх р 10]"ову" или
|
Ро |
_ f ! ! L — « я |
К |
X. рДО]lv JnOB |
dx2 |
1 П 1 Я - 1 |
|
Вводим безразмерную координату
'= * V K„.P I°]™B/PO
ипроводим преобразования:
d y |
d y |
|
dz |
_ |
ж I |
*х. р [01n~ l |
|||
|
dz |
|
dx |
Y |
|
Po |
|
|
|
d x |
|
|
|
|
|
|
| |
|
|
|
Находим вторую производную: |
|
|||||||
d * y ___d |
|
/ |
dy |
\ |
dz |
d |
/ |
dy \ |
|
dx |
dx |
4 dx J |
dx |
dz |
\ |
dx ) |
|||
|
|
|
|
Л—1 |
|
|
|
|
|
|
|
|
JOK |
|
|
|
|
|
|
хд/^ |
X. p iw JnOB |
dz |
|
|
|
||||
|
Po |
|
|
|
|
d y
dz
* / |
^x. p [°)пов' |
d |
\/ |
Po |
dz |
Продолжая решение до конца, получаем
(V.13)
(V.14)
(V-15)
А |
Кх.рЮСв’ А |
|
|
|
|
|
(V.16) |
||
dx2 |
po |
|
dz2 |
|
|
|
|
|
|
Из уравнений (V.14) Н(V.16) получаем |
|
|
|
(V.17) |
|||||
d ty ^ d z 2) == у п . |
|
|
|
|
|
|
|
||
|
Приняв, что реакция по кислороду |
первого порядка |
|
(л=1), уравнения |
|||||
(V.15) и (V.17) упрощаем: |
|
|
|
|
|
|
|||
z = |
xVKx. р/Ро ; |
|
|
|
|
|
|
|
(V.18) |
d*y/(dz*) = у. |
|
|
|
|
|
|
|
(V.19) |
|
|
Уравнение (V.19) решаем подстановкой P ^ d y / d z , |
тогда P d P /d y —y и ин |
|||||||
тегрирование его |
j P d P = J |
дает: |
|
|
|
|
|||
P 2 = у* + С или |
P |
d yld z = |
— VY2+C |
|
|
(V.20) |
|||
|
Интегрируя последнее уравнение, |
f |
___ ^ ___= |
_ f |
|
d z , получаем |
|||
|
|
/------- |
|
\ |
|
||||
|
|
|
|
e, \ |
|
|
|||
In ( y + V ^ + C ) = |
— г + С'. |
|
J Vv* + c |
|
J |
||||
|
|
|
|
|
(V.21) |
Отсчет глубины ведем |
от границы ш лак — металл, |
где [0]*= [0]п о», Y =1 |
|||||||
и 2 = 0 ; |
при очень глубокой ванне z=oo, [О]* = 0 и d y / d z -0. В оспользовавш ись |
||||||||
этими граничными |
условиями, подставив найденные постоянные |
С = 0 |
и |
С '= |
|||||
= 1п 2 в уравнение |
(V .21), получим: |
|
|
|
|
|
|||
In 2у = |
— 2 + In 2 |
или |
In у = |
— 2 |
|
|
|
|
|
и в окончательной |
форме |
|
|
|
|
|
|
|
|
Y = e x p ( — г). |
|
|
|
|
|
|
(V .22) |
||
Воспользуемся уравнением (V.22) в развернутом |
виде: |
|
|||||||
у = ЮиО]„ов = ехр (—хл/Кх. рфо }. |
|
|
|
(V.23) |
|||||
Из |
уравнения |
видно, |
что |
л/P'olKx. Р |
для |
л=1 |
и |
||
V Ро/(^х. р [0]ЙГв) |
для |
любого |
порядка |
реакции |
могут |
служить масштабом реакционной зоны. Проникновение кисло рода, а следовательно, и развитие реакции в глубь фазы могут
быть для п= 1 оценены величиной -у/р01Кх.р как масштабом реакции, так как проникновение кислорода в глубину металли ческой фазы зависит от соотношения скорости переноса кисло рода и скорости реакции. Рис. V.6 графически отображает урав нение (V.23). Разные отношения /Сх.р/Ро определяют разный наклон прямых; с увеличением отношения усиливается падение концентрации кислорода, на меньшей глубине заканчивается возможность реагирования углерода и кислорода и действи тельно po/Кх.р является масштабом реакции.
В металлическом расплаве сталеплавильной ванны концен трация кислорода более или менее постоянная. Очевидно, эта
концентрация |
близка к равновесной и при меньшей концен |
|||||||||||
|
|
|
|
трации |
углерод |
|
не |
окисляется. |
||||
|
|
|
|
Возьмем |
|
достаточно |
высокую |
|||||
|
|
|
|
реальную |
концентрацию |
кисло |
||||||
|
|
|
|
рода |
в |
сталеплавильной |
ванне |
|||||
|
|
|
|
0,02 %, |
соотнесем |
эту |
величину |
|||||
|
|
|
|
к насыщению |
железа |
кислоро |
||||||
|
|
|
|
дом |
на |
разделе |
шлак — металл |
|||||
|
|
|
|
0,23%. |
Горизонтальная |
линия 1 |
||||||
|
|
|
|
отображает это предельное |
соот |
|||||||
|
|
|
|
ношение: |
lg (0,02/0,23) = lg |
0,09. |
||||||
|
|
|
|
Очевидно, выше |
этой |
линии воз |
||||||
|
|
|
|
можно окисление |
углерода, ниже |
|||||||
|
|
|
|
горизонтали невозможно. Решим |
||||||||
|
|
|
|
уравнение |
(V.23) для |
различных |
||||||
Рис. V.6. Определение глубины зоны |
точек по глубине ванны |
при раз |
||||||||||
реагирования углерода с |
кислородом |
личных |
соотношениях |
Кх.р1Ро= |
||||||||
от |
поверхности |
раздела |
металл — |
= 1; 25; |
100 — точки пересечения |
|||||||
шлак: |
|
|
||||||||||
/ — 1в 0.02/0,23-lg 0,09; 2 - К х р/ро=1; |
с горизонталью 1 определяют пре |
|||||||||||
9 - |
*х. р/&>-25; 4 - |
Кх. р/ро-100 |
дел |
глубины реагирования |
угле- |
рода 25; 5; 3 мм при соответствующих соотношениях скорости химической реакции и массопереноса кислорода. Очевидно, что глубина 25 мм предельная для любого сталеплавильного про цесса в подовых печах. Ценность решения задачи заключается не только в аналитическом определении возможной глубины развития реакции обезуглероживания, но и в физическом пред ставлении зоны реагирования. В результате обезуглерожива
ния у границы |
металл — шлак возникает |
сильное перемешива |
ние, создающее |
переходную зону между |
металлом и шлаком |
из смеси трех фаз: металла, шлака, газа. Такая зона эмульги рования универсальна для процесса обезуглероживания в лю бых сталеплавильных процессах, связанных со взаимодейст вием шлаковой и металлической фаз. Высота этой трехфазной зоны в мартеновской ванне в зависимости от интенсивности ки пения колеблется от нескольких до сотен миллиметров, а ве личина межфазной поверхности металл — шлак в сотни раз превышает номинальную площадь ванны. Содержание углерода в металле переходной зоны значительно меньше, чем в объеме металла. В металле переходной зоны окисляется большая доля углерода ванны (до 40%). Окисление углерода складывается из перехода (FeO) из шлака в металл и реакции с углеродом:
(FeO) = [FeO] — 121,057
[С] + [FeO] = [Fe] + СО + 45,971
IQ + (FeO) = [Fe] + CO—75,086 кДж/моль.
Переход (FeO) определяет эндотермичность обезуглерожи вания металла под шлаком. Средняя скорость окисления угле рода в период чистого кипения 0,30—0,10 % С/ч.
§ 5. Применение кислорода в мартеновском процессе
Кислород для сжигания топлива подается в факел трубками диаметром 25—32 мм, уложенными с двух сторон газового кес сона. При обогащении воздуха кислородом объем продуктов сгорания уменьшается, что повышает температуру факела, а также теплопередачу и коэффициент использования тепла. Факел становится жестче и короче воздушного. Обогащение по зволяет повысить тепловую нагрузку и окислительную способ ность печи. Обычно обогащают воздух до 24—25 % при сред нем расходе кислорода 27—50 м3/т. Обогащение дутья кисло родом особенно целесообразно в наиболее теплоемкие пе риоды— завалки и плавления. Интенсификация процесса уве личивает приход тепла от окислительных реакций и особенно от догорания выделяющегося монооксида углерода над поверх ностью расплавов:
Степень обогащения воздуха кислородом, |
21 |
25 |
28 |
30 |
|
% |
. . . |
||||
Тепловая нагрузка на клапане, ГДж/ч |
92,53 |
85,83 |
75,78 |
72,85 |
|
Тепло от догорания СО, ГДж/ч |
14,23 |
34,75 |
48,15 |
51,92 |
|
Общая тепловая нагрузка, |
ГДж/ч |
106,76 |
120,58 |
123,98 |
124,77 |
Практика работы 200-т мартеновских печей на шихте с 65— 70 % чугуна, отапливаемых смешанным газом при обогащении воздушного дутья 30 % и расходе кислорода 61 м3/т, показала: увеличение производительности на 69 % (37,2 т/ч, без подачи Ог 22 т/ч); сокращение удельного расхода топлива на 46,2% (удельный расход условного топлива 80,5 кг/т, без кислорода 150,1 кг/т); сокращение длительности плавки на 42%, (5 4 18 мин вместо-8 ч 56 мин без кислорода). Введение кислорода непосредственно в металлическую ванну интенсифицирует окис ление, при этом не требуется тепла на нагрев, плавление и раз ложение железной руды. При продувке ванны скорость окис ления углерода в 1,5—2 раз больше, чем при использовании кислорода для сжигания топлива. Резкое локальное повышение температур до 2300 °С при вводе кислорода в ванну сопровож дается отрицательными явлениями, приводит к испарению же леза, образованию пыли, что изнашивает свод, регенераторы, затрудняет работу и уменьшает выход стали. Пылеобразование уменьшают заглублением фурмы в расплав, при этом часть ис паряющегося железа будет конденсироваться в верхних слоях расплава. Добавлением пара к кислородному дутью снижают локальные температуры в результате эффекта диссоциации паров воды.
Продувка ванны в период доводки при удельном расходе кислорода 3—5 м3/т дополнительно сокращает плавку на 5— 8% и удельный расход топлива на 6—10%. Наиболее эффек тивно комбинированное применение кислорода: в течение всей плавки подают кислород для горения и продувают ванну в огра ниченный, рационально выбранный период — преимущественно в период доводки. Подают кислород в ванну через свод печи водоохлаждаемыми фурмами. Давление кислорода 0,71— 1,0 МПа; удельный расход 5—8 м3/т, если продувка осущест вляется в период полировки, и 10—15 м3/т — в периоды плав ления и полировки.
Г л а в а 6. ПЕРЕДЕЛ ВЫСОКОФОСФОРИСТЫХ ЧУГУНОВ. КАЧАЮЩИЕСЯ ПЕЧИ
§ 1. Мартеновский передел высокофосфористых чугунов
Переработка высокофосфористых чугунов возможна специаль ным переделом, при этом, кроме стали, получают фосфатные шлаки, иначе передел будет нерентабельным. В связи с этим
плавка разделяется на два периода: в первом проводится концентрированно дефосфорация, во втором— окисление примесей подобно полировке-доводке обычного мартенования.
Передел фосфористого чугуна в 350-т качающихся мартенов ских печах по способу «Азовстали» состоит в следующем: при выпуске готовой продукции большую часть, а иногда весь ко нечный шлак оставляют в печи, металла оставляют ~ 10 т. Со став шихты: 30—35 % скрапа, 65—70 % чугуна, 12—14 % же лезной руды, 6—8 % известняка. Состав чугуна: 0,5 % Si, 1,7— 2,2 % Мп, 0,06% S, 1,5—1,6% Р. Завалку скрапа производят на жидкий шлак. В периоды завалки и прогрева применяют кислород, обогащая дутье до 26%. После заливки чугуна пре кращают подачу кислорода в факел, но ванну продувают кис лородом с расходом 10—13 м3/т. Через 30—50 мин основную массу шлака удаляют с содержанием 12—14 % Р2О5. Добавки известняка и окалины создают обновленный шлак более высо кой основности, к расплавлению Достигающей 1,5. К расплавле нию в металле оказывается 1,4—1,6 % С и 0,15—0,20 % Р. Руд ное кипение проводится при добавках окалины и железной руды; создается второй фосфатный шлак с 14—16% Р2О5, ко торый тоже удаляется. Добавками извести, боксита, окалины формируется шлак, под которым заканчивается рудное и чистое кипение. В металле остается 0,020—0,025 % Р> основность ко нечного шлака 2,8—3,5 при содержании 5—7 % Р2О5 . Особен ностью способа является высокоокислительные условия на про тяжений всего процесса, обеспечивающие глубокое удаление фосфора.
§ 2. Качающиеся мартеновские печи
Качающиеся печи дают возможность изменять положение ра бочего пространства печи. Между подвижным пространством печи и неподвижными головками оставлены зазоры. Эти за зоры дают возможность наклонять печь в сторону задней стенки для полного удаления металла и в сторону передней стенки для выпуска шлака. Вся печь опирается на балочную клетку н два поперечных сегмента. Сегменты опираются на катки, уложенные в станинах, которые закреплены на железо бетонных опорах. Остальные элементы конструкции сущест венно не отличаются от элементов стационарных печей.
Глав а 7. ПРОИЗВОДСТВО СТАЛИ
ВКИСЛЫХ МАРТЕНОВСКИХ ПЕЧАХ
§1. Кислая сталь и кислая мартеновская печь
Процесс проводится в печи, футерованной кварцевыми (>95 % SiC>2) материалами, обычно скрап-процессом на твер дой завалке или дуплекс-процессом (основная — кислая печь). Для ответственных плавок используют шихтовую заготовку, выплавленную в основной мартеновской печи. Содержание уг лерода по расплавлении должно быть'выше верхнего предела в готовой стали на 0,6—0,8%. Содержание кремния в металле по расплавлении должно быть не более 0,1 %, если будет больше, то металл будет раскислен, и ванна будет кипеть вяло. После плавления образуется шлак состава: 0,1—0,3 % СаО, 46—48 % Si02, 28—30 % FeO, 21—23 % MnO, 2,0 % MgO. В по следующем в результате взаимодействия расплава с футеров кой печи шлак обогащается кремнеземом к концу плавки до 60 %.
§ 2. Активный и кремневосстановительный процессы
Существуют две разновидности процесса в кислой печи: а) про цесс с ограниченным восстановлением кремния, или активный процесс-, б) с высоким восстановлением кремния, или кремне восстановительный процесс. При разогреве ванны создаются условия восстановления кремнезема углеродом, марганцем и железом по реакциям:
(Si02) + 2 |
[С] = [SiJ + 2СО, AG° =611,27—3,347, кДж; |
(V.24) |
||
(Si02) + |
2 [Mn] = [Si]+2 (MnO), |
AG° = 134,8— 1,307, кДж; |
(V.25) |
|
(Si02) + |
2 |
[Fe] = [Si] + 2 (FeO); |
AG° = 347,5—0,547, кДж. |
(V.26) |
Реакции восстановления кремнезема могут развиваться на границах металл — шлак и металл — под. В активном процессе восстановление (ЭЮг) ограничивается добавками известняка. Известь связывает кремнезем, высвобождает оксид железа FeO, который, окисляя углерод, препятствует восстановлению крем незема. При содержании в шлаке 5,0—6,0 % СаО восстанов ление кремнезема приостанавливается, а окисление углерода усиливается. Торможение восстановления кремнезема обеспечи вается также присадками железной руды. Восстанавливаю щийся кремний переходит в металл, непрерывно его раскисляя и снижая содержание растворенного кислорода.
Кремневосстановительный процесс характерен восстановле нием кремния до 0,17—0,20 %, а иногда до 0,35 %. При восста-
J 78
новлении кремния до 0,25 % отпадает необходимость раскис лять металл ферросилицием. Период кипения в кремневосстано вительном процессе мало чем отличается от периода кипения активного процесса. Среднюю скорость выгорания углерода на уровне 0,25—0,40 % С/ч поддерживают малыми присадками руды. Во второй половине кипения скорость обезуглероживания замедляется до 0,10—0,12 % восстановленного кремния, шлак к этому времени содержит до 50—52 % Si02. К этому времени восстановление кремнезема происходит не только углеродом, марганцем, но и железом. При горячем ходе печи марганец восстанавливается до 0,35—0,45 %. Сталь кислого процесса со держит меньше растворенных газов, так как силикатные шлаки менее газопроницаемы. Среднее содержание газов в стали:
.0,006—0,015 % 0 2, 2—4 см3/ 100 г Н2 и 0,0010—0,0015 % N. Ме ханические свойства кислой мартеновской стали стабильнее свойств основной. Если прочностные свойства можно считать одинаковыми, то пластические (относительное сужение, удар ная вязкость) выше у кислой стали. Меньшее содержание вред ных примесей и включений в кислой стали позволяет получить большие слитки с меньшей неоднородностью свойств и состава. Кислую сталь применяют для элементов машин особой ответ ственности. Однако развитие кислого мартенования ограничи вается его дороговизной и успешным развитием качественного сталеварения в электропечах.
Глав а 8. СЖИГАНИЕ ТОПЛИВА
ВМАРТЕНОВСКОЙ ПЕЧИ
§1. Мартеновская печь как теплообменный агрегат
Мартеновская печь как теплообменный агрегат подчиняется законам тер модинамики. Первый закон лежит в основе теплового баланса плавки. Второй закон выражен следующим: так как движущей силой теплопередачи в тепло обменной системе является разность температур, то интенсифицировать тепло обмен в мартеновской печи возможно увеличением разности температур между факелом и поверхностью шихты или расплавов. Выплавить сталь, если темпе ратурный уровень в печи <1480 °С, невозможно. Даже высококалорийное топ ливо, сжигаемое с холодным воздухом, выделяет тепла столько, что после нагрева продуктов сгорания до 1480 °С остается четвертая часть для нагрева ванны и самой печи. Этого количества недостаточно. Если же воздух нагреть в регенераторах, то 50—60 % тепла топлива используется полезно. При регенерировании тепла температурный уровень, считая его по температуре отходящих газов, достигает 1700—17506С. В этом случае полезное тепло как разность между теплом внесенным и теплом отходящих газов будет доста точно для сталеварения. Без регенерации тепла сталеварение в мартеновских печах невозможно.
§ 2. Газовые потоки
Для транспортирования большого количества газов в марте новской печи, преодолевающих к тому же сложный путь, дол жна быть тяга. При естественной тяге разрежение создается
трубой и определяется уравнением Дртр = Ятр(увоэд—Удим)- Продукты сгорания, уходящие в трубу, уносят 30—35 % тепла топлива, сжигаемого в печи. Установка котлов-утилизаторов экономически целесообразна, при этом дым отводится дымосо сом, установленным за котлом. Воздух со стороны головки, об разующей факел, поступает за счет избыточного давления пе ред сжигательными устройствами. Движение воздуха и газа происходит при расходовании кинетической энергии поступаю щих потоков. Напор воздуха и газа в любой точке определя ется уравнением
Е = Лет -f- ЛдИН= Лст-(-(y0W0/2g) (1 |
ОС/), |
|
||
где ЛсТ, Лдин — статический |
и динамический |
напоры газов; Wo и |
||
уо — скорость |
и плотность |
газов |
в данной |
точке при нормаль |
ных условиях; |
а — температурный коэффициент линейного рас |
ширения газов; g — ускорение свободного падения. Факел фор мируется за счет скоростей потоков окислителя и газа, особенно последнего. Выходная скорость газового потока не менее 50— 55 м/с. Чем выше скорость и больше угол встречи воздушного и газового потоков, тем . выше турбулентность и смешение. На клоны газового и воздушных пролетов головки на 10—20° при жимают факел к ванне. Хорошо организованный факел обеспе чивает полноту сгорания топлива, для этой цели дают избыток
воздуха 1,15—1,20. Характерный состав |
продуктов сгорания |
в мартеновской печи, %: С 02 7—15; Н20 |
10—21; N2 70—74; 0 2 |
до 3; СО 0,5. При хорошо организованном факеле его темпера тура на отдельных участках достигает 1830—1870 °С.
§ 3. Теплопередача в печи
Передача тепла теплопроводностью следует закону:
q7 = KiS (T .-T .y d ,
где |
q-t — тепло, переданное |
при установившемся |
процессе че |
||
рез |
однородный слой толщиной d, |
Вт |
(кДж/ч); |
S — площадь; |
|
(Т\—Г2) — температурный |
перепад |
по |
двум сторонам слоя; |
Ат — константа. Передача теплопроводностью происходит, глав ным образом, в твердых телах. Теплопроводностью прогрева ется керамика насадки регенераторов, твердая шихта от нагре тых поверхностей вглубь.