
Металлургия черных и цветных металлов
..pdf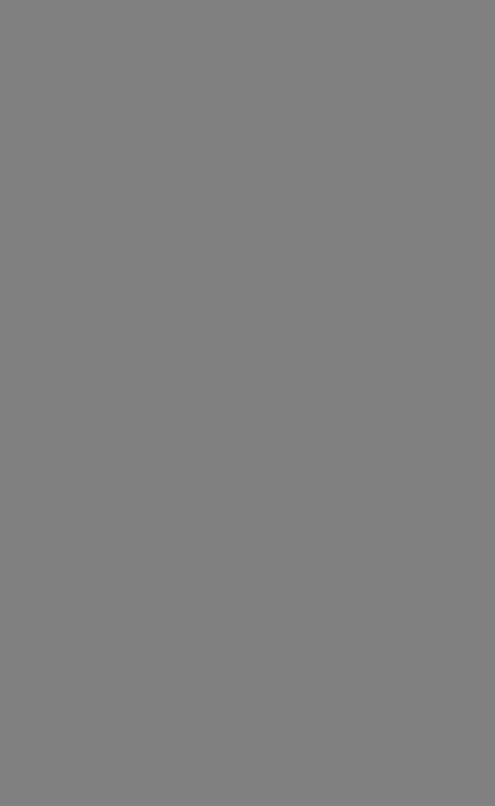
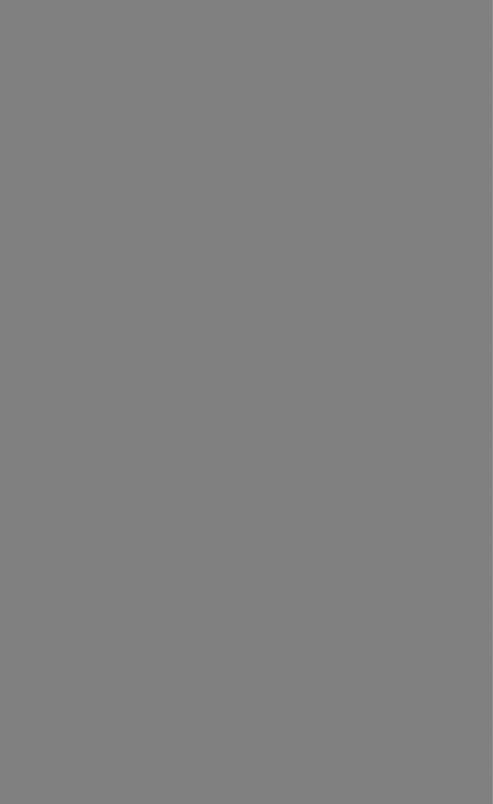
дена и меди). Тугоплавкие ^ферросплавы вводят в ковш с до полнительной обработкой металла аргоном- (феррониобий, фер рохром). Дальнейшее совершенствование легирования сталей полученных в кислородном конвертере, связано с использова
нием комплексных ферросплавов, экзотермических составов а также жидких ферросплавов и лигатур.
Коррозионностойкие стали выплавляют на жидкой заготовке (легированный чугун, полупродукт) с удалением избыточного углерода при сохранении в расплаве хрома. Попытки легиро вания металла твердым высокоуглеродистым феррохромом не посредственно в конвертере не привели к разработке эффектив ного процесса производства, коррозионностойких и жаропроч ных сталей с содержанием 12 % Сг и 0,04—0,15 % С. В то же время применение дорогого низкоуглеродистого феррохрома приводит к существенному повышению себестоимости этих ста лей. Основной задачей является окисление из легированного хромом расплава избыточного углерода при сохранении макси мально возможного содержания хрома.
В настоящее время осваивается производство сталей этого класса с особо низким содержанием углерода (0,01—0,03% С), обладающих высокой устойчивостью в агрессивных средах и однородностью структуры. Термодинамические условия окисле ния углерода расплава при содержаниях в нем 18 % Сг, харак терных для коррозионностойких сталей, улучшаются при по вышении температуры расплава и понижении парциального давления СО в газовой фазе в соответствии с данными равно
весия реакции: |
|
Сг30 4+ 4 [С] = 3 [Сг] -f- 4СО; |
|
lgКщ = lg (pcoatflac) - -12200/7" + 8,05. |
(IV.7) |
Соотношения равновесных содержаний углерода и хрома при различных температурах и давлениях СО показаны на рис. IV.7 и IV.8. Из рис. IV.7 видно, что температура очень сильно влияет на конечное равновесное с хромом содержание угле рода в металле. При содержании в нем 18 % Сг для получения низкоуглеродистого продукта необходимо иметь температуру
>1800 °С (рсо = 0,1 МПа).
Для предотвращения окисления хрома в начале плавки при обычной температуре жидкой заготовки не выше 1500 looO
в состав перерабатываемого продукта вводят кремнии, частично предохраняющий хром от окисления и способствующий ыст-
рому повышению температуры металла за счет со окисления. Другим фактором, способствующим более глубокому
обезуглероживанию ванны при сохранении в ней ХР°^ > ется уменьшение парциального давления СО на гр
талл-газ (рис. IV.8). Для достижения равновесного с хромом
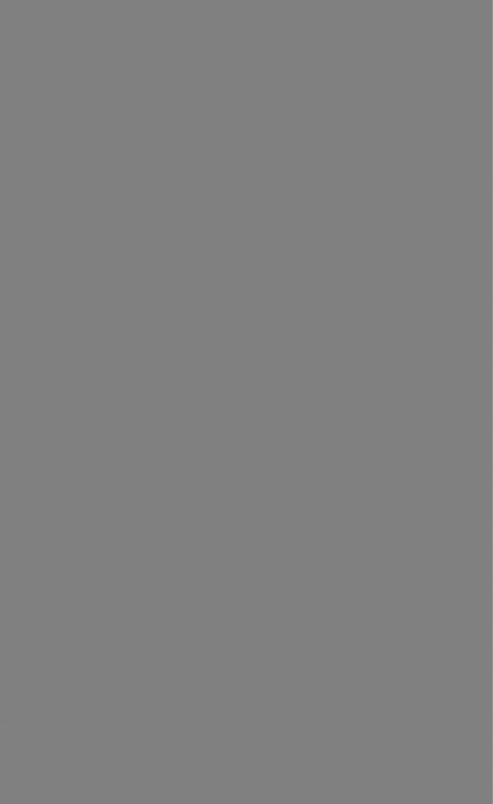
дутья большую часть продувки составляет 1 м3/(т • мин). Окис лительную продувку начинают при отношении расходов кислорода и аргона 3:1 . По мере уменьшения концентрации углерода в металле долю аргона в смеси увеличивают и заканчивают продувку при отношении кислорода к ар гону 1 : 2.
Исходным расплавом является жидкий полупродукт, вы плавленный в электропечи и легированный хромом и никелем
с содержанием 1,3—2,5 % |
С и температурой 1640—1660 °С. |
|||
В начале |
окислительной |
продувки |
в |
конвертер могут быть |
введены |
охладители — металлолом |
и |
легирующие добавки. |
Увеличение доли аргона в продувочной смеси приводит к умень шению рсо в проходящей через расплав газовой фазе и спо собствует преимущественному развитию процесса его обезугле роживания. Одновременно перемешивание ванны не ассимили руемым ею аргоном улучшает кинетические условия окисления углерода. Продолжительность окислительного периода плавки составляет 60—70 мин.
Восстановительный период проводят при отключении кисло рода и подаче в конвертер только аргона. Для восстановления из шлака хрома в конвертер вводят ферросилиций, а для под
держания необходимой |
основности — известь. Продувка арго |
ном продолжается ~ 5 |
мин. За это время основное количество |
оксидов хрома, перешедшее в шлак, успевает восстановиться. В некоторых случаях продолжительность восстановительного периода больше (см. рис. IV.9). Усвоение хрома к его концу достигает 98 % от исходного в металлошихте. Далее шлак сли вают и в конвертер вводят дополнительно шлакообразующую смесь из извести и плавикового шпата и при продувке аргоном проводят десульфурацию в течение 3 мин, за которые удаля ется большая-часть серы (до 95 %).В конечном металле содер жание примесей обычно составляет, %: С 0,02; S 0,020; О 0,005. Полученная сталь характеризуется высокими эксплуатацион ными свойствами.
Однако такой процесс потребляет большое количество ар гона (до 25 м3/т). Для его уменьшения в настоящее время практикуется замена аргона азотом, который не ухудшает свойств ряда марок коррозионностойких сталей и может в этом случае применяться как легирующий элемент для замены дефи цитного никеля. В окислительный период возможно и частичное
использование воздуха в дутье.
Кроме АОД-процесса, для тех же целей получило развитие, хотя и меньшее, паро-кислородное рафинирование хромистых расплавов. Продувку полупродукта из электропечи в этом слу чает ведут в конвертере с донными фурмами смесью пар — кис лород также в кольцевой защитной оболочке. Водяной пар иг рает роль не только разбавителя кислорода, хотя и с окисли
тельными свойствами, но и охладителя, позволяющего гибко регулировать температурный режим процесса и первичной ре акционной зоны.
После снижения содержаний углерода и кремния до задан ного уровня переходят от продувки кислородом в защитной обо лочке, чаще из водяного пара, на продувку смесью с автомати ческим регулированием ее состава. При пониженном содержа нии углерода подачу кислорода прекращают, в конвертер, как и в АОД-процессе, вводят ферросилиций и известь и продувают ванну паром для перемешивания и ускорения процессов вос становления. Для удаления из металла водорода, поглощае мого из водяного пара, последние 1—3 мин ведут продувку ар гоном с расходом 1—2 м3/т.
Степень извлечения хрома и марганца в металл в этом про цессе достигает 98 и 80 % соответственно при более низком расходе аргона и лучшей стойкости футеровки вследствие более гибкого регулирования температурного режима плавки.
Г л а в а 3. ПЛАНИРОВКА И ОБОРУДОВАНИЕ КОНВЕРТЕРНОГО ЦЕХА. ТЕХНИКО ЭКОНОМИЧЕСКИЕ ПОКАЗАТЕЛИ КИСЛОРОДНО-КОНВЕРТЕРНОГО ПРОЦЕССА
В состав кислородно-конвертерного цеха входят следующие от деления и участки: миксерное отделение, или участок перелива чугуна; отделение магнитных и сыпучих материалов; главное здание с отделением выплавки металла и разливочным отделе нием. При непрерывной разливке стали на МНЛЗ разливочный комплекс часто размещается в отдельном здании. В современ ных цехах в главном здании размещается отделение внепечной обработки стали. Отделения подготовки лома, шлакообразую щих материалов _и другие выделяются в настоящее время в са мостоятельные цехи.
Снабжение кислородно-конвертерного цеха жидким чугуном может быть организовано по двум схемам: 1) доменный цех — миксерное отделение — конвертер; 2) доменный Цех — участок перелива чугуна — конвертер. По пер вой схеме в торце цеха планируется миксерное отделение, предназначенное для снабжения конвертеров жидким чугуном, его хранения и усреднения.
Миксер представляет собой цилиндрическую емкость с горизонтальной осью вращения, футерованную огнеупорными материалами и снабженную механизмом поворота. Стандартные миксеры имеют вместимость 600, 1300 и 2500 т.
При большой производительности кислородно-конвертерного цеха стацио нарный миксер перестает играть роль усреднителя и буфера между домен ными и сталеплавильным цехами. В связи с этим переходят на вторую схему снабжения конвертеров жидким чугуном с использованием для его транспор тировки передвижных ковшей миксерного типа вместимостью 150, 420 и 600 т
Г — конвертерный; Д — энергетический; / — мостовые краны; |
2 — |
|
завалочная машина; 3 — конвертер; 4 —сталевоз; 5 — шлаковоз |
||
и переливом в заливочные ковши на участке |
(станции) перелива. Передвиж |
|
ной ковш-миксер представляет собой емкость |
сигарообразной |
формы (тор- |
педо-ковш) с корпусом сварной конструкции и футеровкой из шамотногб кир пича. Преимущества применения ковшей-миксеров определяется снижением капитальных и эксплуатационных затрат по сравнению с использованием миксерного отделения, а также повышением температуры чугуна, заливаемого в конвертер в среднем на 50 °С и снижением потерь металла в виде настылей.
В отделении магнитных и сыпучих материалов набирают или корректи руют массу лома в совках для загрузки в конвертер и разгружают сыпучие материалы в приемные бункера. Операции по сортировке и подготовке мате риалов упрощаются при наличии на заводе специальных цехов подготовки материалов, в первую очередь, скрапоразделочного цеха. Металлический ма териал (скрап) транспортируют в отделение выплавки металла чаще скраповозами, а сыпучие материалы (извести и других) в расходные бункера кон вертеров — транспортерами.
Отделение выплавки стали — конвертерное отделение (рис. IV. 10) — состоит из нескольких пролетов: загрузочного, конвер терного, включающего участки конвертеров, газоотводящего тракта, сыпучих материалов. На участке конвертеров распола гается машина для подачи кислорода, транспортирующее и ре монтное оборудование, подготовка ферросплавов, посты управ
ления.
Участок газоотводящего тракта имеет комплекс сооружений для улавливания, отвода, охлаждения и очистки конвертерных газов. Он состоит из котла-охладителя конвертерных газов (котла-утилизатора), газоочистки, нагнетателей-дымососов, ды мовой трубы. Отходящие из конвертеров газы имеют высокую запыленность (до 250 г/м3), содержание оксида углерода до
- |
‘ |
137 |
90 %, температуру на выходе из конвертера 1700 °С, их удель ный объем 60—80 м3/т. Их выбросы в окружающую атмосферу экологически недопустимы, и в то же время эти газы являются источником вторичных энергетических ресурсов. В связи с этим обязательная система газоотводящего тракта должна иметь устройства для утилизации физической'и химической энергии конвертерных газов и быть взрывобезопасной при подсосе воз духа.
Распространены два способа отвода и охлаждения конвер терных газов: 1) с полным дожиганием СО и утилизацией фи зического и химического тепла в системе и 2) без дожигания СО с утилизацией только физического тепла в системе. В си стемах с дожиганием используют радиационно-конвективные котлы-утилизаторы с охлаждением газов до 250—350 °С. В си стемах без дожигания имеются только радиационные котлыутилизаторы с охлаждением газов до 900—1000 °С и после дующим впрыскиванием воды. Для снижения содержаний пыли в конвертерных газах при ее количестве перед очисткой 25— 250 г/м3 и размерах частиц от <10 до >40 мкм в отечествен ных цехах применяется взрывобезопасная система мокрой га зоочистки.
Основными технико-экономическими показателями кислородно-конвертер ного процесса являются производительность конвертеров и себестоимость стали. Работу конвертеров, характеризуют годовой или часовой производи тельностью. Годовую производительность А, т/год, расчитывают по формуле
А = Т (14,40/т) ал, |
|
(IV.8) |
где Т — масса металлической шихты, т; т — длительность |
плавки, |
мин; а — |
выход годных слитков, % от массы металлической шихты; |
п — число рабочих |
|
суток в году; 1440 — число минут в сутках. Производительность |
300—350-т |
конвертеров достигает 450—500 т/ч. Это в несколько раз выше, чем часовая производительность мартеновской или дуговой электропечи.
В настоящее время стойкость конвертеров составляет 600—2000 плавок, а продолжительность ремонтов — 3—6 сут в зависимости от вместимости кон вертеров. В кислородно-конвертерных цехах обычно имеются два, а в послед нее время чаще три конвертера, причем постоянно работают соответственно один или два. Простои не должны превышать в указанных случаях 50 и 33 % календарного времени.
Длительность или цикл плавки определяется временем между последо
вательными заливками чугуна в конвертер и складывается |
из длительности |
||
продувки и вспомогательных операций (завалки |
скрапа |
и |
сыпучих, заливки |
чугуна, слива металла и шлака, корректировки |
состава |
и |
температуры ме |
талла). Длительность плавки не пропорциональна |
вместимости конвертеров, |
|
а увеличивается с возрастанием их |
вместимости более медленно. Так, в 100-т |
|
конвертере цикл плавки составляет |
28—40 мин, а |
в 300-т — 40—50 мин. |
Выход годных слитков зависит от потерь металла при про дувке и способа разливки. В большинстве случаев он состав ляет 89—91 % от массы металлической шихты. Этот показа тель является недостаточным и зависит от неиспользованных резервов совершенствования кислородно-конвертерного про цесса в направлении снижения потерь металла.
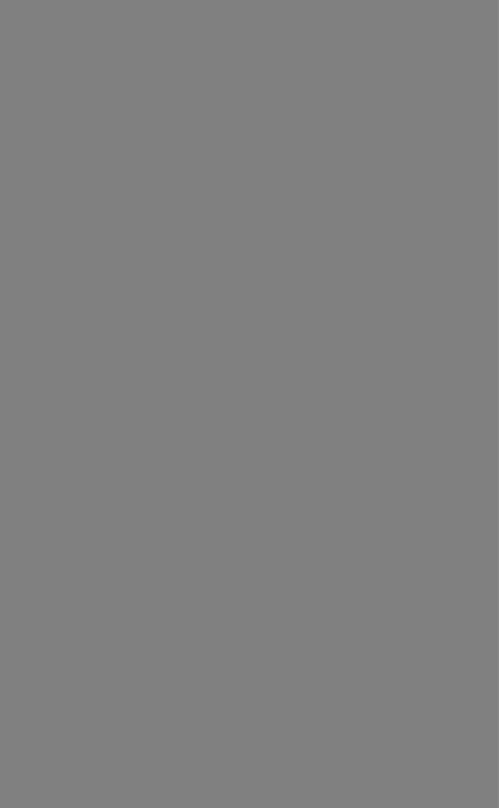
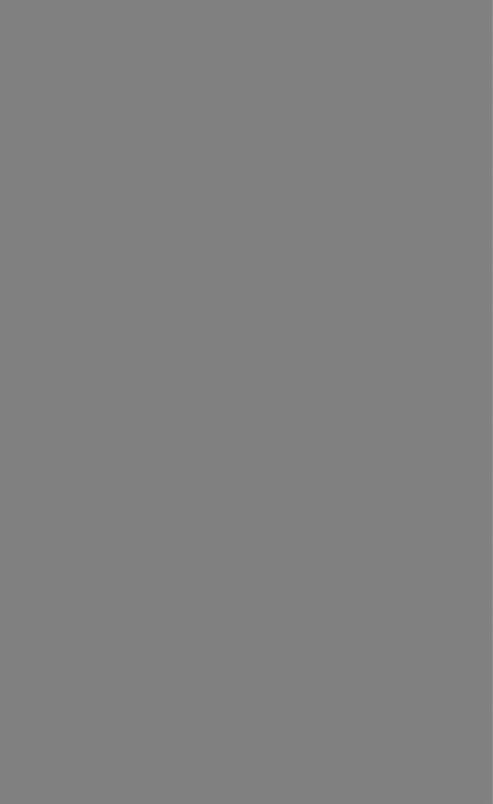