
Металлургия черных и цветных металлов
..pdfМмЬняр |
мяреОтеянЪ—i1 /1nwOmpU*- М?9Ий7/7МГ6□ |
||||
Ц |
|
Р&77ф?/7?а |
|
|
|
лмАфхш |
& Ш /Я7П 7 |
|
|||
/p q n frev |
|
||||
О щ ю ея |
|
||||
У/Г |
|
Feo-Fe |
2&Ю Г0 |
A&y7X7//£rf/7fiwe |
|
| |
j |
|
|||
|
Fe2Oj-Feo |
||||
CHt, |
H20 |
/2i? |
|
|
|
/яраЯяя? </&ля<7 |
//P//0ф№0УК |
£/VM70 |
|||
|
|
||||
|
|
|
|||
Рис. 111.4. Упрощенная схема модуля процесса X и Л |
|
||||
Процесс Хоялата и Лимина (X |
и Л-процесс) |
разработан |
|||
фирмой «Охалата и Ламина» (рис. III.4). Процесс восстанов |
|||||
ления |
осуществляется в ретортах, |
футерованных |
изнутри и |
снабженных нагревателями и охладителями. В реторту загру жают богатую чистую руду, а также подают газ-восстановитель, подогретый до 1370 К. Газ-восстановитель получают путем кон версии очищенного от серы природного газа водяным паром по
реакции: СН4+ Н 20 = ЗН2+ С0. После |
конверсии газ содержит |
||
58% |
Н2, 14% СО, 21 % Н20 |
и 4—5% |
С 02. Водяной пар уда |
ляют |
в котлах-утилизаторах |
и получают газ с 73 % Н2, 15— |
|
16 % |
СО и 6—7 % С02. Этот газ подогревают в трубчатых ре |
куператорах и направляют в реторты. Свежий газ-восстанови тель поступает вначале в^реторту первого цикла, в которой на ходится руда, предварительно восстановленная и подогретая до 900 °С. Восстановление в реторте этого цикла длится —2 ч. Выходящий из реторты газ проходит через конденсатор, где конденсируется водяной пар. Остающийся газ подогревается и подается в реторту второго цикла, где нагревается и частично восстанавливается свежая руда. Продолжительность этого цикла 2 ч. Газ, отходящий от этой реторты, используют для по лучения тепла и энергии. Перед выгрузкой продукта из реторт первого цикла через руду пропускают природный газ в течение 2—3 мин, при этом метан разлагается, и на губчатом железе отлагается сажистый углерод, что необходимо по условиям ста леплавильного передела продукта.
Продолжительность процесса в целом составляет 5 ч, сте пень восстановления готового губчатого железа 75—95 %. Рас ход природного газа на 1 т губчатого железа 450—600 м3 в зависимости от размеров реактора и эффективности утилиза ции тепла. Производительность установки до 500 т/сут.
Процесс восстановления оксидов железа газом-восстановителем является гетерогенным, и скорость такого процесса существенно зависит от величины поверхности реагирования. Восстановление тонкоизмельченного железоруд ного материала (например, концентрата) в кипящем слое обеспечивает высо
ки
коразвитую удельную межфазную поверхность |
реагирования газ — оксид. |
|
Ц связи с этим в 50-е годы появился ряд процессов прямого получения |
же |
|
леза, в основе которых был реактор с кипящим |
слоем,— «Новальфер», |
«Аш- |
айрон», сФиор» (США) и др. Однако эти процессы не получили промышлен ного развития по нескольким причинам. При низких температурах (ниже ten) железо получается пирофорным. В качестве восстановителя при этих темпе ратурах можно использовать только водород, причем его степень использова ния невелика. Если для увеличения скорости восстановления повысить темпе ратуру выше /Сп, то восстановленные частички спекаются, укрупняются и на рушается кипящий слой.
§ 4. Установки получения металла во вращающихся печах
Ряд способов прямого получения железа основан на использо вании вращающейся печи в качестве восстановительного реак тора. Шихтовые материалы, содержащие руду, и восстанови тель (уголь или коксик), а также известняк или доломит в ка честве десульфуратора загружают с одного конца печи (рис. III.5). С другого конца печи сжигают топливо. Материалы при вращении печи перемещаются от одного ее конца к другому. Продукты сжигания топлива движутся вдоль печи навстречу шихтовым материалам. При движении в печи шихтовые мате риалы нагреваются, и затем железо восстанавливается из окси дов. Газы, образующиеся при взаимодействии углерода с окси дами, дожигают, обеспечивая дополнительное поступление тепла и возможность регулирования температурного режима в печи. Восстановленное железо может быть получено в виде криц (сферических частиц), если температура в печи —1350 °С или губчатым (при температурах восстановления до П00 °С). После выгрузки из печи продукт охлаждают, подвергают маг нитной сепарации и используют как полупродукт для домен ных и электродуговых печей.
Процессы восстановления во вращающихся печах имеют ряд положительных сторон. Процесс этот достаточно гибкий. Можно использовать железорудное сырье с различными химиче скими и гранулометрическими составами, а также разные виды топлива. К недостаткам этих способов относятся сравнительно невысокая производительность, менее благоприятные условия теплопередачи, чем в шахтной печи, необходимость выдержи вать температурные пределы в зависимости от температуры размягчения шихты.
§ 5. Получение металла восстановлением оксидных расплавов
Получение металла восстановлением оксидных расплавов из давна привлекало внимание металлургов. При таком восстанов лении имеется ряд преимуществ по сравнению с твердофазным восстановлением оксидов и доменным процессом. Не требу-
Рис. |
III.5. |
Схема |
получения |
кричного железа |
во вращающейся печи: |
/ — зона |
предварительного |
подо* |
|||||
грева; |
// — зона восстановления; /// — зона крнцеобраэовання; |
/ — установка для дробления руды; 2 — бун |
|||||||||||
кер; |
3 — смеситель |
шихты; |
4 — вращающаяся |
трубчатая печь; |
5 — бункер |
угольной |
пыли |
н горелка; а — |
|||||
ленточный |
охладитель; |
7 — шаровая |
мельница; |
8 |
— магнитный сепаратор; |
Г —топливо; |
Р — руда; |
ПП — |
|||||
промпродукт |
магнитной |
сепарации; |
Ш — шлак; |
К — |
крица |
|
|
|
|
|
ется окускование железорудных материлаов, не нужен дорого стоящий кокс, полагают, что не требуется обогащение руд, во многих случаях повышается гибкость процесса и ряд других
преимуществ.
В 50-е годы появился ряд проектов, разработок и установок по высокотемпературному восстановлению железа из распла вов. Восстановительный газ получают частичным сжиганием пылевидного угля, распыленного мазута или природного газа в воздухе, обогащенном кислородом. Количество окислителя подбирают таким, чтобы обеспечить восстановительную атмо сферу в продуктах сгорания. Дутье обогащают кислородом для того, чтобы получить достаточно высокую температуру факела. В последующем было несколько проектов и предложений по получению металла восстановлением оксидных расплавов, од нако практического применения они не нашли.
В последив, годы вновь возрос интерес к высокотемператур ным способам получения металла. Сформулированы основные принципы, определяющие конкурентоспособность процесса вос становления в расплаве по сравнению с доменным процессом. Процесс должен удовлетворять следующим условиям: должен быть таким, чтобы можно было использовать тонкоизмельченные руды или концентраты непосредственно, исключив про цессы агломерации или окомкования; обусловливать возмож ность использования наиболее дешевых из возможных топлив без физических или химических ограничений. При этом должно быть полное использование восстановительного агента, т. е. в отходящих газах не должно быть СО (Н2); вследствие высо ких температур отходящих газов' их объем должен быть мини мальным, чтобы избежать избыточных потерь тепла; должен быть легко управляем; должен работать при максимально воз можных скоростях, чтобы обеспечить максимальную удельную производительность при низких капитальных затратах; должен быть непрерывным, чтобы обеспечить хорошее управление и низкие капитальные затраты.
Рассмотрим несколько вариантов высокотемпературных про цессов. Восстановление оксидных расплавов, может быть осу ществлено в одну стадию или с предварительным восстановле нием железорудного сырья. Энергетическое обеспечение про цесса может быть за счет электроэнергии или сжигания топлива твердого (угля) .или газообразного. В качестве восста новителя используют уголь или газ. Способы восстановления в расплаве привлекают еще и тем, что можно использовать руду или концентрат, а также уголь любой крупности, в то.' числе и мелкий.
Представим ряд реакторов с теоретическими значениями энергетических и материальных расходных показателей. Пусть в реакторе имеется расплав железорудного концентрата. В ка-
|
д |
<&SifJ**(7S,7%) |
|
Нг 7777^(72,7%) |
|
|
N2 ?4 7 м Зф % ) |
|
СаО 47кг |
й |
|
|
Я еем & J2 * е |
|
MW0&//7&?/7? |
|
|
|
|
|
7408к г |
/&ГЛ77ХР |
2070*3 cmvifif* |
Ш ак270кг |
|
|
Msma/м |
|
|
| m o /re |
|
|
Рис. I ll .6. Расходные показатели в реакторе с восста- новлением оксидных расплавов
|
|
еогм |
М/мсродная |
Л&//Ц&//77/Х7/7? |
|
||
2f88/гг |
|
||
|
СаО i |
|
|
|
fJ79 |
|
|
/ш |
zP fe |
780 |
|
077 |
|
||
m s |
% |
Пр/7А'/77/7П |
|
ll/ШК |
4 |
г^Оип///Ц/у |
|
KZ/cwqax? |
087K0K7V |
||
087кг |
у/Ш Ш |
7498*3 |
|
207 |
000 |
084 |
|
778 |
\Г \т *г |
077 |
220 |
709 |
|
2J0 |
92 |
Рис. 111.7. Расходные показатели для реактора с восстанов* леннем в расплаве при различной степени возврата тепла от дожигания газа в расплаве; температура расплава 1720 К, температура отходящих газов 1870 К, цифры сверху вниз со ответственно для степени возврата в расплав тепла от дожи гания газов— 10, 20, 40, 100 %
честве восстановителя используется уголь, а энергетическое обеспечение процесса осуществляется за счет частичного (до СО) сжигания угля в кислороде. Температура расплава и тем пература отходящих газов 1720 К. Предполагаем, что догора ния СО и Н2 в реакторе не происходит и, следовательно, нет поступления тепла в реактор за их счет.
Расчетные (на 1 т железа) значения расходных показателей для этого случая приведены на рис. II 1.6. Совершенно очевидно, что в этом случае большое количество тепла выносится из ре актора с отходящими газами. Как следствие этого, большой удельный расход топлива. Снизить расход топлива можно, если дожигать с помощью кислорода газы, покидающие расплав, и непосредственно в реакторе использовать часть этого тепла в ванне расплава. Удельный расход топлива будет уменьшаться
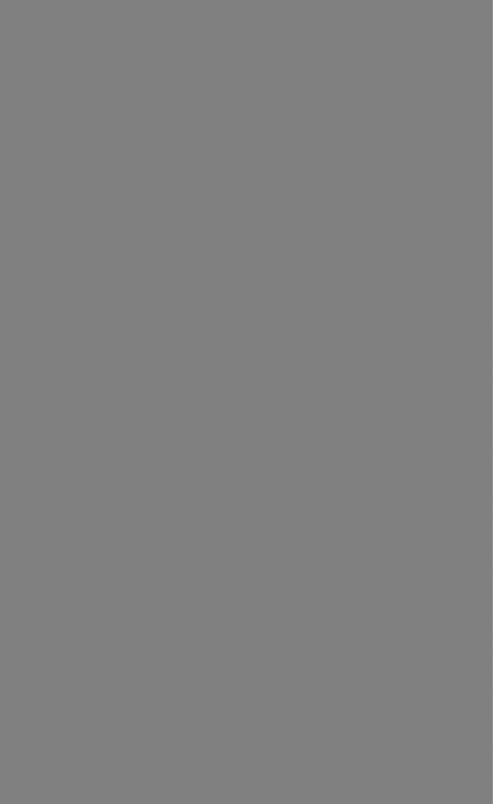
§ 6. Двух- и многостадийные процессы
Рассмотренные процессы предусматривают осуществление про цесса восстановления расплава в одном реакторе. В то же время восстановление может быть проведено в две стадии и более. Фактически эта группа восстановительных процессов, осуществляемых в одном агрегате (например, в доменной печи), проводится в двух реакторах, каждый из которых регулируется независимо. Один (или более) реактор используется для пред варительного восстановления, плавильный реактор — для окон чательного восстановления и, кроме того, установка — для пре образования энергии. В этом случае используется физическая и химическая энергии отходящих газов. Это позволяет оптими зировать систему в целом для повышения ее экономичности.
ог
Рнс III 9. Схема |
установки Инред: |
3 — подвод первичного кислорода; |
|||
|
а |
плавильная |
камера; |
||
4 ~~ от*оляшиеЬ'газы* |
5 -п о д во д |
вторичного кислорода; |
6 — бункер рудного |
||
к о ^ц ен тта; 7 -б у н кер известняк.; |
бункер угля; |
» - .о э .р . т ; 10 — |
|||
котел-утилизатор; |
/i — компрессор |
|
|
|
Существует целый ряд опытно-промышленных установок по реализации описанной выше схемы процесса.
Рассмотрим принципиальную схему процесса Инред (рис. III.9), разрабатываемую в Швеции с 1972 г. На первой стадии осуществляют нагрев и предварительное восстановление руды в охлаждаемой камере сгорания. Подаваемое топливо частично сгорает, частично подвергается коксованию. Из первого реак тора предварительно восстановленные и нагретые частицы руды вместе с частицами кокса поступают в плавильно-восста новительный реактор с графитовыми электродами. С шихтой подают также известняк. В верхнюю часть реактора подается кислород через сопла, расположенные так, что газовый поток с частицами руды и коксика закручивается, образуя вихревой поток по центру камеры.
Уголь частично сгорает в кислороде, а оксиды железа пла вятся и восстанавливаются до вюстита перед попаданием в зону окончательного восстановления. В зоне горения температура достаточно высокая ( —1900 °С). Несгоревший уголь попадает в зону окончательного восстановления в виде ококсованных гранул. Энергетическое обеспечение процесса осуществляется за счет сжигания угля, а в зоне окончательного восстановле ния— за счет электроэнергии, а также перегретых оксидов и излучения факела. Температура в зоне окончательного восста новления —1600 °С. Результатом быстрого плавления является то, что в зоне окончательного восстановления скапливается вяз кая масса из расплава вюстита с вкраплениями мелких ча стиц кокса, извести и губчатого железа. Восстановленный ме талл (чугун) периодически выпускают из печи. Чугун содер жит 3—4 % С, 0,5—1 % Si, 0,5—1 % Мп. Фосфор из руды полностью восстанавливается и переходит в чугун. В Инредпроцессе расходуется ~600 кг некоксующегося угля на 1 т ме талла. Этого количества угля достаточно для производства электроэнергии (400 кВт*ч/т) и кислорода, необходимых для процесса.
Рекомендательный библиографический список
Бардин И. П. и отечественная металлургия.— М.: Наука, 1983.— 285 с.
Гиммельфарб А. И., Кименов А. М., Тарасов Б. Г. Металлизация и эле:> гроплавка железорудного сырья — М.: Металлургия, 1981.— 152 с.
Тулин А. И., Кудрявцев В. С., Пчёлкин С. А. и др. Развитие бескоксовой металлургии.— М.: Металлургия, 1987.— 328 с.
. . . ПРОИЗВОДСТВО СТАЛИ Раздел I V В КОНВЕРТЕРАХ
Гл а в а 1. КИСЛОРОДНО-КОНВЕРТЕРНЫЙ ПРОЦЕСС
§1. Общая характеристика процесса
Конвертерный процесс является первым из промышленных спо собов массового производства жидкой (литой) стали. Он по явился раньше мартеновского и электросталеплавильного про цессов. Начиная с 1855—1878 гг., когда были осуществлены бессемеровский и томасовский процессы в конвертерах с дон ным воздушным дутьем, конвертерное производство длительное время было главным способом получения стали для машино строения, строительства и транспорта.
Отличительными особенностями конвертерного производства являются высокие скорости окисления примесей перерабаты ваемого жидкого чугуна при минимальной длительности про дувки (10—30 мин), простота конструкции конвертера и уп равления его работой, малые капитальные затраты на единицу продукции. Эти преимущества выявились уже в первых вариан тах конвертирования— бессемеровском и томасовском процес сах. В них же в определенной мере проявился рациональный подход к выбору способа производства по виду перерабаты ваемого сырья. Так, бессемеровский процесс, хотя и вынуж денно, применяли только для чугунов из руд с низким содер жанием фосфора и серы при достаточном содержании в этих чугунах кремния как главного источника тепла при бессемеро вании. Томасовский же процесс использовали для передела вы сокофосфористых руд (доля которых в европейских железоруд ных запасах была >28% ), в нем фосфор служил главным ис точником тепла.
По мере универсализации сталеплавильных процессов с ориентированием на сырье более широкого состава такой под ход несколько утратил свое значение. В настоящее время выбор схем и способов производства в зависимости от вида сырья вновь выступает на первый план. Это вызвано необходимостью комплексной переработки исходных материалов с извлечением возможно всех ценных компонентов.
Наряду с отмеченными выше преимуществами, классические конвертер ные процессы — бессемеровский и томасовский — имели и существенные недо статки, приведшие к их вытеснению другими сталеплавильными процессами. Конвертерный металл, выплавленный с применением воздушного дутья при недостаточно управляемом и малоактивном шлаковом режиме, перестал от вечать возросшим требованиям промышленности к стали повышенного каче ств. Недостатком конвертерной стали являлась ее склонность к хрупкости при низких температурах и холодной деформации, из-за высоких содержаний
в металле азота (0f0I0—0,015 %) наряду с повышенными содержаниями серы, фосфора и оксидов (неметаллических включений). Кроме того, в конвертерах с воздушным дутьем существенная часть приходной стороны теплового ба ланса расходовалась на нагрев азота. Это не позволяло использовать в кон вертерах заметных количеств металлолома, быстро накапливаемого промыш ленностью.
Большинство из указанных проблем частично решалось переходом на мартеновское и позже электросталеплавильное производство стали, хотя и требующие более сложного оборудования и больших капитальных затрат, но менее производительные
Возрождение и быстрое развитие конвертерного производ ства в последние 30—35 лет связаны с разработкой новых его вариантов, позволивших резко улучшить качество получаемого продукта, а также расширить рудную базу и значительно уве личить долю используемого металлолома. Начало этого воз рождения было обусловлено появившейся возможностью ис пользовать в конвертерах большие количества технического кислорода, получаемого фракционным сжижением воздуха на заводских кислородных станциях. Сохранение принципа подачи дутья снизу, применявшегося в классических процессах, не поз воляло перейти на продувку концентрированным кислородом без разбавителей из-за неудовлетворительной стойкости донных фурм. Кардинальным решением проблемы стало создание кис лородно-конвертерного процесса с использованием нового прин ципа продувки — подачи дутья из технически чистого кислорода сверху на ванну жидкого металла, перерабатываемого в кон вертере.
Впервые техническая возможность применения кислорода для продувки жидкого чугуна была показана Н. И. Мозговым в 1933 г. На основании про
веденных исследований на опытных с 1936 |
г. и промышленном 12,5-т |
конвер |
тере была отработана в 1945—1952 гг, |
технология конвертерной |
плавки |
с подачей кислорода сверху через водоохлаждаемую форму практически в со
временном варианте. |
Соответствующие исследования были выполнены и |
Э Австрии, начиная с |
1949 г. Там же в в 1952—1954 гг. появились и первые |
кислородно-конвертерные цехи с ЛД конвертерами вместимостью до 30 т. При использовании вместо воздуха технического кислорода, содержащего
97,5—99,5 % 0 2, резко снизилось содержание азота в конвертерной стали до пределов, обычных для мартеновского металла и ниже. Процесс оказался го раздо более гибким в отношении регулирования шлакового режима и возмож ностей удаления фосфора и серы по сравнению с томасовским процессом. Та ким образом на данном этапе была решена проблема повышения качества конвертерного металла и выплавки в конвертерах стали мартеновского сор тамента.
Одновременно с устранением недостатков классических способов конвер тирования кислородно-конвертерный процесс сохранил достоинства этих спо собов — высокую производительность, малые капитальны^ затраты, простоту оборудования и обслуживания конвертеров, хотя и привел к более интенсив ному дымообразованию и менее интенсивному перемешиванию металла в объеме (последнее сказалось в основном при переходе на конвертеры боль шой вместимости).
Кислородно-конвертерный процесс позволяет перерабаты вать чугуны, полученные из руд самых различных месторожде-