
1462
.pdfУДК 629.1.032.001
ОБ УЧЕТЕ ПАРАМЕТРОВ МЕХАНИЗМА ПОВОРОТА ПРИ ОЦЕНКЕ ЭНЕРГОЭФФЕКТИВНОСТИ ШАССИ ГУСЕНИЧНЫХ МАШИН
Р.Ю. Добрецов
Санкт-Петербургский государственный политехнический университет, Россия
Приведены условия движения, в которых производится расчетная оценка энергоэффективности шасси гусеничной машины при повороте. Рассмотрен набор частных показателей, характеризующих баланс мощности механизма поворота, и приведены результаты расчетов для серийных военно-транспортных машин.
Ключевые слова: энергоэффективность шасси, транспортное средство, гусеничные машины, трансмиссия, механизм поворота.
Традиционный подход к анализу мощностных потоков в механизмах поворота гусеничных машин подразумевает использование кинематической схемы механизма [1]. Это весьма усложняет задачу. Однако для большинства используемых механизмов поворота гусеничных машин такие потери мощности не зависят от структуры самого механизма
иопределяются его внешними параметрами [2]. В эту группу входят
ифрикционные механизмы, и механизмы, содержащие гидростатические передачи, что позволяет охватить абсолютное большинство применяемых конструкций. Гусеничная машина находится в режиме поворота около половины времени движения. При построении метода оценки энегоэффективности шасси [3] этот факт делает необходимым учет
энергетических затрат, характерных для режима поворота (рис. 1). В работе [4] приведены и обобщены статистические данные, позволяющие обосновать выбор режима движения, для которого рационально проводить сравнительную оценку шасси. Выбраны следующие параметры расчетного режима: коэффициент сопротивления повороту
µmax = 0,7, относительный радиус поворота ρ = 10, скорость V = 7 м/с.
Сточки зрения энергоэффективности механизм поворота характеризуется следующими безразмерными показателями.
51
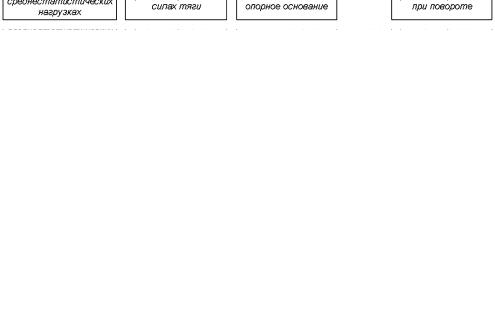
1. Относительное увеличение потребной мощности двигателя при повороте Пµ = NдвNдв.пр. Например, для механизмов на основе несим-
метричных дифференциалов П = 1. Для двухпоточного механизма с гидрообъемной передачей (или фрикционным механизмом) при трансмиссии с бортовыми коробками передач значение П при повороте вокруг центра тяжести достигает 4–5. При использовании центральной коробки передач нагрузки увеличиваются.
Рис. 1. Частные показатели эффективности работы систем шасси транспортной гусеничной машины
2. Относительная мощность, рассеиваемая при буксовании фрикционного элемента управления Пэ = NэNдв или при работе гидроста-
тической передачи. Данный показатель, в частности, позволяет сравнивать механизмы поворота по величине относительной нагруженности буксующего элемента управления, прогнозировать тепловыделение, износ фрикционных дисков и др. По значению и физическому смыслу величина Пэ близка к к.п.д.
3. Безразмерный показатель, учитывающий nρ – число фиксированных радиусов поворота, Пρ =1−1nρ . Значения Пρ [0,1] , так как
52
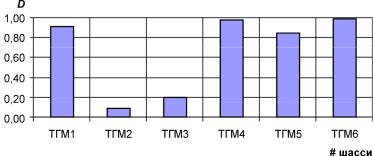
nρ [1,∞) (например, для механизмов типа «бортовой фрикцион с тор-
мозом», «простой дифференциал», «одноступенчатый планетарный механизм поворота» Πρ = 0). Для бортовых коробок передач число расчет-
ных радиусов поворота определено числом ступеней в коробке. В случае применения многопоточного механизма с гидрообъемной передачей можно считать, что nρ →∞. Следует отметить, что показатель Πρ ха-
рактеризует в первую очередь энергетические особенности механизма поворота и только косвенно – качество управления поворотом. Для оценки качества управления следует ввести дополнительные показатели.
Формирование обобщенного показателя эффективности производилось при помощи математического аппарата функций желательности (метод Харрингтона) [3]. Метод подразумевает нормировку частных показателей с учетом экстремальных значений, характерных для их величин; осреднение (используется принцип нахождения геометрического среднего); интерпретацию результатов с применением базовой оценочной шкалы метода Харрингтона.
Результаты расчетного сравнения энергозатрат для шасси серийных машин различного назначения иллюстрирует рис. 2. Приведены результаты расчетов для аналогов шасси серийных основных танков: Т-72, Т-80, Т-90, Т-64 (механизм поворота – бортовые коробки передач; присвоены номера 1, 4, 5, 6); военно-транспортных гусеничных машин БМП-2, МТ-ЛБ (механизм поворота – бортовой фрикцион с тормозом; присвоены номера 2, 3). Изменение значения показателя D при наличии учета режима поворота не превысило 7 %. Результаты расчетов позволяют констатировать, что применение бортовых коробок передач в качестве многорадиусных механизмов поворота целесообразно. Оценочные расчеты показывают, что с точки зрения нагрузок на гидрообъемную
Рис. 2. Расчетные значения обобщенного показателя эффективности работы агрегатов шасси различных транспортных гусеничных машин
53
передачу или фрикционный механизм поворота в двухпоточной трансмиссии также предпочтительна схема с бортовыми коробками передач.
Таким образом, можно сделать следующие основные выводы.
1.Методика комплексной оценки энергоэффективности шасси гусеничной машины должна учитывать энергозатраты при повороте машины. В математическую модель оценки введены безразмерные коэффициенты (параметры), учитывающие особенности преобразования энергии в механизмах поворота.
2.Сравнение энергоэффективности шасси в режиме поворота должно производиться в характерных условиях движения. На основании статистических данных такие условия определены. Сравнение результатов расчетов с практикой позволяет говорить об адекватности предлагаемого подхода.
Список литературы
1.Забавников Н.А. Основы теории транспортных гусеничных машин. – М.: Машиностроение, 1975. – 448 с.
2.Шеломов В.Б., Добрецов Р.Ю. Мощности двигателя и буксования фрикционного элемента управления поворотом гусеничной машины // Научно-технические ведомости СПбГПУ. Сер. Наука и образова-
ние. – 2010. – Т. 2, № 2. – С. 87–91.
3.Добрецов Р.Ю. Объективная оценка технических характеристик шасси транспортных гусеничных машин // Тракторы и сельскохозяйст-
венные машины – 2011. – № 2 – С. 19–23.
4.Добрецов Р.Ю. Учет энергетических параметров механизмов поворота при комплексной оценке потерь мощности в шасси транспортных гусеничных машин // Научно-технические ведомости СПбГПУ. Сер. Наука и образование. – 2011. – № 1. – С. 122–128.
Об авторе
Добрецов Роман Юрьевич (Санкт-Петербург, Россия) – кандидат технических наук, профессор, доцент кафедры ДАиГМ, СанктПетербургский государственный политехнический университет (195251, г. Санкт-Петербург, ул. Политехническая, 29; e-mail: dr-idpo@ yandex.ru).
54
УДК 621.792.6
СОВРЕМЕННЫЕ СПОСОБЫ РЕМОНТА РЕЗИНОТКАНЕВЫХ РЕЗЕРВУАРОВ В ПОЛЕВЫХ УСЛОВИЯХ
А.П. Ериков1, С.А. Ерикова2
1Пермский военный институт внутренних войск МВД России, Россия 2Пермский национальный исследовательский
политехнический университет, Россия
Сформулированы основные преимущества применения в полевых условиях резинотканевых резервуаров по сравнению с другими средствами хранения горючего, определены требования к ремонту технических средств обеспечения горючим в полевых условиях, проведён анализ типов вулканизации резинотканевых изделий и определены преимущества холодной вулканизации по сравнению с горячей при ремонте резинотканевых резервуаров в полевых условиях.
Ключевые слова: резинотканевый резервуар, вулканизация, ёмкость, средства для хранения горючего, ремонт, вулканизация.
На современном этапе развития силовых структур, когда техническая оснащённость является одним из основных факторов оборонной мощи государства, особую значимость приобретает вопрос постоянного поддержания необходимого уровня работоспособности образцов вооружения и военной техники. Вопросы применения технических средств хранения и транспортирования топлива рассматривались рядом ученых [3, 4].
Резинотканевые резервуары незаменимы при массовом перемещении войск, организации складов горючего или просто запасов топлива, доставке воды в труднодоступные места и её хранении, организации пожарных водоёмов.
Резинотканевые резервуары выполняются в виде замкнутой оболочки в форме подушки и состоят из наружного атмосферостойкого резинового слоя, капронового силового слоя и внутреннего, бензостойкого резинового слоя.
Рассматриваемые резервуары имеют небольшой вес по сравнению с другими ёмкостями для хранения горючего, удобны в эксплуатации и хранении, легко монтируются и демонтируются при перевозке их с
55
объекта на объект, что делает их мобильными. Для размещения резинотканевых резервуаров может использоваться неподготовленная площадка, а монтаж может быть осуществлён в течение максимально короткого времени с минимальным количеством рабочего персонала.
Исходя из вышеперечисленного назовем основные преимущества резинотканевых резервуаров по сравнению с другими средствами хранения горючего: длительный срок эксплуатации, быстрота и удобство доставки в требуемый район, небольшой вес и малые габариты в транспортном состоянии, возможность размещения и использования в труднодоступных районах и на неподготовленных площадках, широкий температурный диапазон эксплуатации, инертность к хранимому веществу, низкая стоимость при изготовлении и трудозатраты при развёртывании и свёртывании.
В случае выхода из строя ремонт резинотканевых резервуаров в полевых условиях на первоначальном этапе, как правило, осуществляется в отрыве от ремонтных органов. В связи с этим к ремонту предъявляется ряд специфических требований: возможность реализации ремонта непосредственно на месте повреждения; простота технологических процессов; минимальная трудоёмкость и продолжительность; универсальность применяемых методов и средств для ремонта любого вида корпусно-ёмкостного оборудования в широком диапазоне размеров и форм повреждения; отказ от применения громоздкого ремонтного оборудования; снижение требований к квалификации обслуживающего персонала; возможность осуществления ремонта независимо от климатических условий и времени года.
В настоящее время наиболее эффективным методом оперативного устранения повреждения резинотканевых резервуаров является вулканизация. При вулканизации каучук и резина вступают в реакцию между собой под воздействием химических элементов.
За основу технологии примем известный способ устранения дефектов поверхности резинотканевых изделий, который включает в себя следующие операции: очищаются и обезжириваются повреждённые и близлежащие поверхности; путем сжатия уменьшается поверхность дефекта; наносится клеевой состав; производится сушка; прикладывается и прижимается пластырь; проводится холодная или горячая вулканизация; убираются наплывы и неровности.
Существует два типа вулканизации оболочек резинотканевых резервуаров, которые также характерны для ремонта автомобильных шин и транспортерных лент – это горячая и холодная вулканизация. При го-
56
рячей вулканизации на повреждённое место воздействуют высокой температурой, в результате чего происходит склеивание повреждённых поверхностей, а холодная вулканизация проводится при помощи активатора бутилового слоя.
Одним из наиболее эффективных типов является горячая вулканизация, так как она максимально приближена к производству самой резины, что позволяет достичь свыше 90 % от прочности резинотканевого слоя. Для горячей вулканизации используются специальные клеи с каучуковыми добавками и резиновые (резинотканевые) пластины из сырой резины. К преимуществам горячей вулканизации по сравнению с другими методами относятся прочность, долговечность и быстрота ремонта. Однако стоит отметить и недостатки: необходимость использования и перемещения специального оборудования (пресс), работа оборудования от электросетей.
К преимуществам холодной вулканизации можно отнести отсутствие специального оборудования, возможность склейки на месте и сравнительно небольшое время, необходимое для проведения работ.
Недостатками холодной вулканизации являются: проведение работ только при плюсовых температурах; уменьшение надёжности соединения при сильной запылённости и влажности.
При выполнении вулканизации с соблюдением технологии прочность холодной сварки достигает 70 % от прочности резинотканевого слоя.
Таким образом, можно сформулировать ряд преимуществ холодной вулканизации по сравнению с горячей:
–уменьшение времени на ремонт примерно в два раза за счёт того, что после вулканизации холодным способом резервуар можно использовать по истечении двух часов;
–многократное уменьшение себестоимости ремонта за счет исключения из технологического процесса дорогостоящего оборудования;
–возможность производить ремонт непосредственно на месте выхода резервуара из строя;
–при соблюдении технологии ремонта и качественных расходных материалов гарантируется надёжность соединения до полного износа резервуара.
Анализируя типы вулканизации, используемые при ремонте резинотканевых резервуаров, можно сделать вывод, что в полевых условиях, особенно при недостатке времени на ремонт, наиболее эффективной будет холодная вулканизация.
57
Список литературы
1.Косов А.А. Способы и средства ремонта тонкостенных оболочек технических средств службы горючего в полевых условиях. – СПб., 1997.
2.Ериков А.П., Ерикова С.А. Современные способы и средства ремонта в полевых условиях технических средств обеспечения горючим // Актуальные вопросы совершенствования системы технического обеспечения: материалы всерос. науч.-практ. конф. – Пермь, 2014. –
С. 46–50.
3.Цимберов Д.М. Фитерер Д.В. Методика минимизации потерь нефтепродуктов при управлении обеспечением пространственно распределенных объектов // Экономика и менеджмент систем управле-
ния. – 2013. – № 1, 2(7). – 80 с.
4.Цимберов Д.М. Кубачев С.К. Особенности совершенствования системы нефтепродуктообеспечения в горных условиях // Устойчивое развитие горных территорий. – Владикавказ, 2011. – № 4(10).
Об авторах
Ериков Алексей Петрович (Пермь, Россия) – доцент, Пермский военный институт внутренних войск МВД России (614030, г. Пермь,
ул. Гремячий Лог, 1; е-mail: yerikov@yandex.ru).
Ерикова София Алексеевна (Пермь, Россия) – студентка, Пермский национальный исследовательский политехнический университет
(614990, г. Пермь, Комсомольский пр., 29; е-mail: erikova1996@ yandex.ru).
58
УДК 629.113
ЭЛЕКТРОМАГНИТНАЯ МУФТА ПРИВОДА ВЕНТИЛЯТОРА СИСТЕМЫ ОХЛАЖДЕНИЯ ДВС
А.Ю. Ерофеев, А.А. Бердников
Пермский военный институт внутренних войск МВД России, Россия
Существует несколько видов привода вентилятора системы охлаждения двигателя: механический, электрический, гидравлический, электромагнитный. Каждый из них обладает характерными преимуществами и недостатками. В статье рассматривается модернизация электромагнитной муфты, обеспечивающей надежную работу привода вентилятора, отключение вентилятора в автоматическом режиме и позволяющей сохранять работоспособность привода даже в случае неисправности электрической цепи.
Ключевые слова: электромагнитная муфта, привод вентилятора, система охлаждения.
С развитием современного общества непрерывно возрастает роль различных видов техники, в том числе автомобильной. Основным агрегатом любого автомобиля является двигатель, надежная работа которого в том числе обеспечивается системой охлаждения. Поддержание рабочей температуры охлаждающей жидкости в системе охлаждения осуществляется посредством радиатора, обдув которого производится вентилятором. Соответственно, привод вентилятора является немаловажным элементом в обеспечении нормальной работы как двигателя, так и автомобиля в целом.
Существует несколько видов привода вентилятора: механический, электрический, гидравлический и электромагнитный. Каждый из них обладает характерными преимуществами и недостатками. Однако привод с электромагнитной муфтой, наиболее прост в конструкции, что делает его дешевле и доступнее, а также позволяет производить отключение вентилятора и его включение в автоматическом режиме. Так, например, на двигателях семейства КамАЗ применяется привод с электромагнитной муфтой. Основным его недостатком является то, что в случае выхода из строя электрической цепи обдув вентилятора не производится, что может привести к перегреву и выходу из строя двигателя.
59
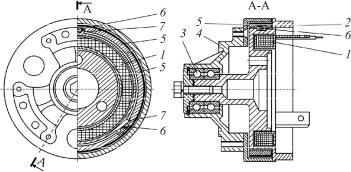
Решить данную проблему позволяет предлагаемая конструкция электромагнитной муфты (рисунок). Данная муфта работает следующим образом. При нормальной работе двигателя колодки под действием распорных пружин и центробежных сил плотно прижаты к ступице вентилятора. При этом вентилятор вращается, обдувая радиатор. Термобиметаллический датчик, находящийся в рубашке охлаждения, управляет работой электромагнитной катушки. При необходимости отключить вентилятор электрическая цепь катушки замыкается, в результате чего вокруг нее создается электромагнитное поле. Под действием электромагнитных сил колодки притягиваются к шкиву, образуя зазор между ними и ступицей. В результате этого вентилятор перестает работать. При повышении температуры охлаждающей жидкости до рабочей цепь катушки размыкается, и колодки возвращаются в исходное положение.
Рис. Электромагнитная муфта привода вентилятора: 1 – неподвижная электромагнитная катушка; 2 – шкив; 3 – подшипник; 4 – ступица вентилятора; 5 – колодки с фрикционными накладками; 6 – распорные пружины; 7 – выступы шкива
Для обеспечения работы данной муфты должно выполняться следующее условие:
Fмагн > Q + Fупр, |
(1) |
где Fмагн – магнитная сила, создаваемая электромагнитной катушкой, Н; Fупр – сила упругости пружин, Н;
F = 40 550B2Sg, |
(2) |
магн |
|
где B – электромагнитная индукция в катушке, Тл; S – площадь сечения катушки, мм2; g – ускорение свободного падения, м/с; Q – сила инерции, возникающая при вращении колодок, Н,
60