
2828.Экспертиза качества и разрушений
..pdf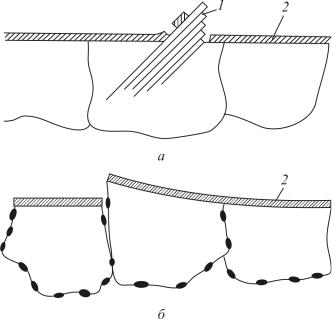
Рис. 4.73. Разрыв покровного слоя в начальный период коррозионного растрескивания: а − транскристаллитное образование трещины; б − межкристаллитное образование трещины; 1 − полосы скольжения; 2 − покровный слой
Коррозионная усталость металла – разрушение металла под воздействием периодической динамической нагрузки (знакопеременных напряжений) и коррозионных сред. Коррозионной усталости подвергаются сплавы на основе железа, никеля, алюминия, меди и многих других металлов.
Коррозионная усталость металла среди других разновидностей коррозии под напряжением встречается наиболее часто. При нахождении металла в коррозионной среде некоторое время предел его выносливости понижается, и конструкция уже не выдерживает нормальных для нее ранее напряжений. Не удается зафиксировать существование предела усталости. Развитие трещин происходит главным образом в момент, когда металлоконструкция испытывает нагрузку. В результате периодических термических напряжений в металле защитная оксидная либо любая другая пленка на его поверхности разрушается. Коррозионная среда имеет свободный доступ к открытой поверхности. Сквозь поверхностные трещины агрессивная коррозионная среда также проникает в глубь металла, интенсифицируя разрушение.
231
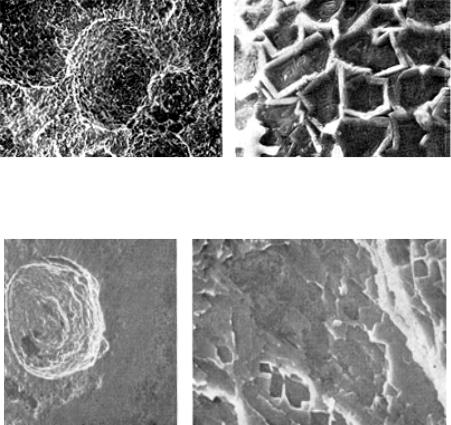
4.9. Микроскопические особенности разрушения при коррозии
Химическая и электрохимическая коррозия приводит к появлению точечной коррозии, питтингов (рис. 4.74–4.78).
Рис. 4.74. Внутрення поверхность труб водонагревателя. В результате повышенного в воде содержания кислорода возникла точечная коррозия. Микроструктура углублений определяется наличием карбидной сетки. ×200; ×2000
Рис. 4.75. Поверхность мартенситностареющей стали с результатом действия коррозии во влажной среде, содержащей ионы галогенов: между отложениями
ичистой поверхностью образовался локальный гальваноэлемент, приводящий
кточечной коррозии. ×500, ×5000
Кристаллографически ориентированные ямки видны на поверхности Ni–Co–Mo-мартенситностареющей стали, находящейся во влажной атмосфере, содержащей ионы галогенов (см. рис. 4.75). Ямки и фасетки скола можно увидеть на поверхности излома титанового сплава (см. рис. 4.78).
Локальная точечная коррозия трубы теплообменника из Cr–Ni-стали произошла в результате разрушения покровного слоя раствором перхлорэтилена (см. рис. 4.74). Сильная точечная коррозия хорошо видна на
232
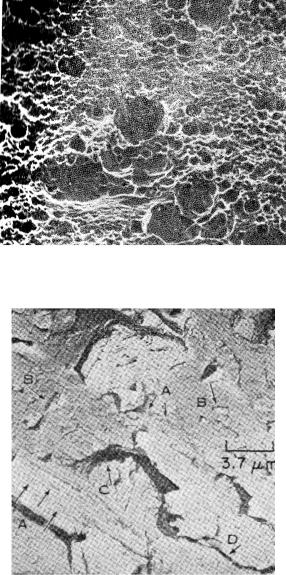
внутренней поверхности подогревателя. Микроструктура углублений определяется наличием карбидной сетки. Точечный характер коррозии отмечается на поверхности разрушения аустенитной стали Х10СrNiMoT 18–10 (см. рис. 4.76).
Рис. 4.76. Аустенитная стальХ10СrNiMoT. Под воздействием хлоридсодержащей атмосферы образуются повреждения, подобные проколам острой иглой. ×400
Рис. 4.77. Рельеф разрушения по механизму внутризеренного скола образца из стали 4315. Видны гребни отрыва (А), язычки (В), неглубокие ямки (С) и вторичные трещины (D). Разрушение вызвано коррозией под напряжением в 3,5%-ном растворе NaCl. ×2680
233
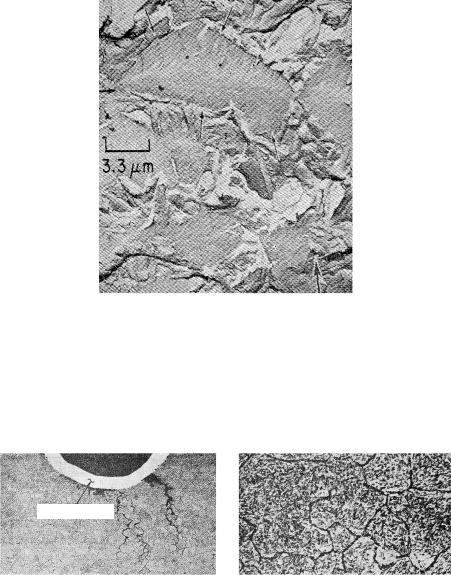
Рис. 4.78. Поверхность излома титанового сплава Ti–6Al–4V, разрушенного в результате коррозионного растрескивания в метаноле. ×3000
Под влиянием аммиака на поверхности излома возникают поверхности транс- и межкристаллитного скола (рис. 4.79). Коррозионная усталость металла сопровождается развитием межкристаллитных и транскристаллитных трещин, которые разрушают металл изнутри.
Слой никеля
Рис. 4.79. Разрушение шпильки из нержавеющей стали с 12 % Cr в результате коррозии под напряжением. Неправильная термическая обработка привела к выделениюкарбидовпограницамзерениобусловиламежкристаллитноерастрескивание
4.10. Жидкометаллическая хрупкость
Жидкометаллическая хрупкость – явление охрупчивания металлов и сплавов под действием расплавов в условиях растягивающих напряжений (рис. 4.80).
234

Рис. 4.80. Схема двух крайних типов изменения пластичности металла под действием расплава и растягивающей нагрузки F: а – пластифицирование металла при высокой растворимости расплава в твердой фазе и/или образование интерметаллида; б – возникновение и рост трещины при малой растворимости расплава в деформированном металле
Необыкновенно быстрое разрушение происходит тогда, когда некоторые жидкие металлы вступают в контакт с наиболее высокопрочными алюминиевыми сплавами или сталями. Так, ртуть или жидкие амальгамы приводят к растрескиванию алюминиевых сплавов при незначительных растягивающих напряжениях.
В различных областях промышленного производства и технологических процессов всегда существует значительный риск внезапного разрушения металлических материалов, если приходится иметь дело с жидкими металлами. Разрушение деталей и конструкций
впроцессе сварки и пайки наблюдалось неоднократно. Имеют место поломки осей при перегреве и расплавлении подшипников скольжения, разрушение покрытых кадмием стальных пружин, когда им приходится в течение некоторого времени работать в условиях высоких температур. Использование жидких металлических теплоносителей
ватомных реакторах также требует предупреждения возможности разрушения конструкций в результате появления хрупкости под действием жидкого металла.
Одно из возможных объяснений природы возникновения хрупкости металлов под действием расплавов заключается в изменении межфазной свободной энергии на границе твердой и жидкой фаз. Считается, что поступление жидкого металла в вершину трещины может вести к уменьшению прочности связи между разделяющимися атомами твердой фазы. Это эквивалентно уменьшению свободной энергии на единицу площади поверхностей, которые образуются прираспространении трещины.
Причиной жидкометаллической хрупкости является диффузия атомов активного компонента по структурным дефектам деформируемого металла, которая вызывает локальное понижение температуры плавления материала, образование там жидкой фазы, зарождение и рост трещины.
235
4.11. Разрушение в результате контакта тел (изнашивание)
4.11.1. Основные понятия. Виды износа
Процесс трения всегда сопровождается износом, который постепенно приводит механическую систему в состояние непригодности. Многие детали машин и механизмов подвергаются интенсивному износу. Увеличение срока службы быстроизнашивающихся деталей различного назначения − важнейшая проблема современного машиностроения
идругих отраслей техники, в решении которой ведущую роль играют металлургия и литейное производство. Для классификации видов износа прежде всего необходимо рассмотреть понятия «износ», «износостойкость», «изнашивание» и «интенсивность изнашивания», которые приняты и используются в повседневной практике. Интенсивный износ сопряженных поверхностей − один из существенных каналов утечки материальных и энергетических ресурсов, поэтому разработке эффективных методов борьбы с ним в последнее время уделяется огромное внимание. При трении сопряженные поверхности изнашиваются, что приводит к изменению их взаимного положения.
Износ – изменение размеров, формы, массы твердых тел или состояния их поверхностей вследствие либо остаточной деформации от постоянно действующих нагрузок, либо разрушения поверхностного слоя при трении.
Всоответствии с ГОСТ 27674–88 изнашивание классифицируется как процесс отделения материала с поверхности твердого тела и увеличения его остаточной деформации.
Износостойкость (износоустойчивость) – сопротивление материалов деталей машин и других трущихся частей износу. Износостойкость оценивается, например, уменьшением массы литой детали за время работы, ее линейных размеров или изменением объема детали.
Следует отметить, что изнашивание − это прежде всего процесс взаимодействия поверхностей, который сопровождается не только их микрорезанием, деформированием и нагреванием, но и изменением механических свойств, структуры, фазового состава и химической активности поверхностных слоев.
Впроцессе длительного воздействия на поверхность детали микро-
имакроскопических абразивных частиц происходит износ, оцениваемый по уменьшению размеров, объема, массы деталей в абсолютных
236
или относительных единицах. Износ, отнесенный к пути трения, объему выполненной работы, работе трения и т.д., является показателем интенсивности изнашивания.
Износ и интенсивность изнашивания определяют и по другим косвенным признакам. Чаще всего под износом принято понимать постоянное срабатывание поверхности деталей в результате процесса трения. Износ, отнесенный к промежутку времени процесса трения, определяет скорость изнашивания.
Практика эксплуатации машин и другого оборудования показывает, что большая его часть теряет работоспособность не вследствие поломок, а в результате износа отдельных деталей. Высказано мнение о необходимости исследования износа и сопутствующих процессов, реализующихся при трении, и показано, что взаимодействие поверхностей при трении проявляется в формировании дискретных контактов − пятен, в котором участвуют выступы и покрывающие их пленки, а также прилегающие к этим выступам соседние участки материала. Считается, что силы, приложенные к разным участкам пятен контакта, образующихся при относительном движении сопряженных поверхностей, неодинаковы, а температура материалов, даже в пределах площади контактов, различна. Это приводит к различной реакции локальных микрообъемов материалов при износе трением.
Принят ряд классификаций по видам износа при трении, построенных в основном на базе внешних условий и признаков процесса. Различают также четыре главные формы износа и несколько второстепенных (сопутствующих) процессов, которые часто классифицируются как самостоятельные виды износа.
1.Адгезионный износ возникает в условиях трения, когда два гладких тела скользят друг по другу и частицы материала, вырванные с одной поверхности, прилипают к другой. Этот вид износа имеет место, когда атомы контактирующих поверхностей входят в близкий контакт. На площадях контакта при скольжении поверхностей всегда существует вероятность того, что из-за адгезионных сил разрушение этого контакта происходит не по первоначальной поверхности раздела одногоматериала, а внутри него.
2.Абразивный износ возникает в условиях трения, когда более твердые шероховатые поверхности скользят по более мягким, царапают или пропахивают ее, образуя свободные частицы. Абразивный износ может возникнуть и тогда, когда твердые частицы попадают между поверхностями фрикционной связи и изнашивают их.
237
3.Коррозионный износ имеет место, когда контакт поверхностей происходит в коррозионных средах. В процессе скольжения образующиеся на поверхности пленки разрушаются и коррозионное воздействие распространяется в глубь материалов.
4.Поверхностная усталость наблюдается во время многократного скольжения или качения по одним и тем же поверхностям с непрерывно повторяющимися циклами нагружения и разгрузки. Поверхностная усталость наблюдается во время многократного скольжения или качения по одним и тем же поверхностям с непрерывно повторяющимися циклами нагружения и разгрузки.
По ГОСТ 27674–88 различают механическое, коррозионно-механи- ческое и электроэрозионное изнашивание.
Изнашивание деталей машин и механизмов принято классифицировать по причинам, в соответствии с которыми различают:
– механическое;
– коррозионно-механическое;
– абразивное;
– гидроабразивное;
– газообразивное;
– эрозионное;
– кавитационное;
– усталостное;
– окислительное;
– электроэрозионное изнашивание;
– фреттинг-коррозию.
С практической точки зрения важнейшее значение имеют два вида износа:
– вызванное трением скольжения (рис. 4.81);
– вызванное трением качения (рис. 4.82).
К основным явлениям и процессам при трении и изнашивании относятся: схватывание, перенос материалов, задирание, выкрашивание
иотслаивание.
Различают схватывание 1-го рода (холодный задир) и 2-го рода (горячий задир).
Установлено два наиболее решающих фактора, влияющих на процесс схватывания трущихся тел: их температура и нагрузка.
238
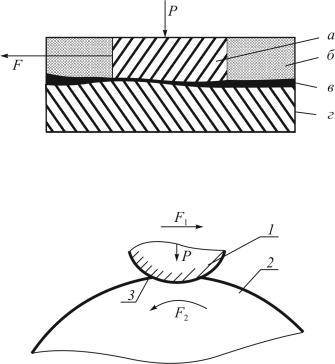
Рис. 4.81. Схема износа при трении скольжением: F – направление движения;
Р– усилие давления; а – контактирующее тело 1; б – окружающая среда;
в– промежуточное вещество; г – контактирующее тело 2
Рис. 4.82. Схема износа при трении качения: F1 – направление движения ролика 1; F2 – направление движения вала 2; 3 – упругая деформация при переменном нагружении; Р – усилие давления
Начало процесса заедания может быть вызвано изменением различных факторов, например увеличением скорости скольжения, нагрузки, температуры контактируемых поверхностей, уменьшением вязкости смазывающего материала и других факторов. В процессе заедания резко возрастает интенсивность изнашивания поверхностей, что приводит к росту динамических нагрузок и выходу из строя деталей узла. Из-за заедания происходит заклинивание узла механизма.
Распространена и теория износа пластичных металлических сплавов посредством отслаивания тонких «листков» от поверхности детали в результате возникновения на определенной и примерно постоянной глубине остаточных напряжений, вызванных скоплением дислокаций, под воздействием другой детали, работающей в режиме скольжения.
В процессе износа при скольжении материалы под действием напряжений работают на срез, а в процессе трения износа при качении развиваются нормальные напряжения. При длительном нагружении под
239
действием переменных давлений это приводит к выкрашиванию частиц на поверхности, т.е. образованию раковин (питтинга).
Если наряду с нормальными напряжениями развиваются также
икасательные, то происходит проскальзывание, в наибольшей степени способствующее процессу износа. Нагружение, сочетающее скольжение
икачение, возможно, например, в зубчатых передачах.
Износ при скольжении, вызываемый вращением, образуется в вершинах опор и в шаровых подпятниках. Это тот вид износа, при котором имеет место эффект вращения при относительном смещении соприкасающихся участков поверхности. Все три типа износа могут проявиться в смешанных формах.
4.11.2. Износ при трении скольжения
Виды изнашивания притрении скольжения представлены на рис. 4.83. Следует исходить из того, что в пределах микрообластей ни одна поверхность не является гладкой. Всегда существует определенная шероховатость. Две поверхности, впервые приложенные друг к другу под небольшим давлением, соприкасаются только в небольшом числе возвышающихся точек и линий. При первом движении поверхностей относительно друг друга возвышения и заусеницы одной поверхности сталкиваются с заусеницами и возвышениями другой. Возвышения на поверхности детали, изготовленной из относительно легче деформируемого материала, изгибаются в направлении движения; эта поверхность подвергается сглаживанию и накату. В результате происходит деформационное упрочнение поверхности, что препятствует ее дальнейшему деформированию. Продолжение деформации возможно только при увеличении местного или
общего эффективного давления на данную поверхность.
В часто встречающихся случаях твердотельного скольжения пар, когда твердое тело скользит по мягкому, на поверхности этого более мягкого тела можно заметить бороздчатый рисунок. В начальной стадии скольжения четко обнаруживается направление пластической деформации. С макроскопической точки зрения приработка двух поверхностей приводит к образованию «зеркала», т.е. образованию поверхностей, приработанных до блеска. На концах такого зеркала можно видеть развальцованные в направлении движения язычки, которые в виде тонких слоев лежат на первоначальной поверхности. Описанный выше процесс приработки не приводит к большому износу; частицы износа на этой начальной стадии малы и окислены.
240