
2828.Экспертиза качества и разрушений
..pdf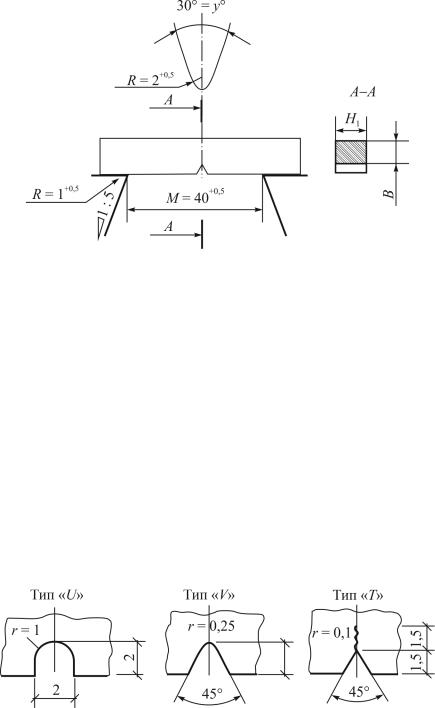
Рис. 3.58. Расположение образца на опорах
Ударную вязкость KС, Дж/см2 (кгс·м/см2), вычисляют по формуле
KС = K/S0, |
(3.10) |
где K – работа удара, Дж (кгс·м); S0 – начальная площадь поперечного сечения образца в месте концентратора, см2, вычисляемая по формуле
S0 = Н1B, |
(3.11) |
где Н1 – начальная высота рабочей части образца, см; B – начальная ширина образца.
В соответствии с ГОСТ 9454–78 предусмотрены испытания образцов с концентратором напряжений трех видов (рис 3.59): U-образным (радиус надреза r = 1 мм); V-образным (r = 0,25 мм) и Т-трещина усталости, созданная в основании надреза. Соответственно ударную вязкость обозначают: KCU, KCV, KСТ.
Рис. 3.59. Форма надрезов на образцах, предназначенных для испытания на динамический изгиб
131
Критерием ударной вязкости является KCU. Она включает две составляющие:
KCU = KСз + KСр, |
(3.12) |
где KСз – работа зарождения трещины; KСр (≈KСТ) – работа распространения трещины. Чем острее надрез, тем меньше KСз. Критерий KСТ является критерием трещиностойкости, оценивающим сопротивление материала распространению трещины.
За результат испытания принимают работу удара или ударную вязкость для образцов с концентратором вида U и V и ударную вязкость для образцов с концентратором вида Т.
Работу удара обозначают двумя буквами (KU, KV или KТ). Первая буква (K) – символ работы удара, вторая буква (U, V или T) – вида концентратора. Последующие цифры обозначают максимальную энергию удара маятника и ширину образца.
Допускается обозначать ударную вязкость двумя индексами (аi): первый (а) − символ ударной вязкости; второй (i) − символ типа образца. Для обозначения работы удара и ударной вязкости при пониженной и повышенной температурах вводится цифровой индекс, указывающий температуру испытания. Цифровой индекс ставят вверху после буквенных составляющих.
3.6.5. Испытания на трещиностойкость
Определение характеристик трещиностойкости (вязкости разрушения) проводят при статическом нагружении в соответствии с ГОСТ 25.506–85. Для определения характеристик трещиностойкости испытывают с записью диаграмм «нагрузка – смещение» («Р – ν») или «нагрузка – прогиб» («Р – f») образцы с предварительно нанесенной усталостной трещиной. По результатам испытаний определяют следующие основные характеристики трещиностойкости:
–силовые − критические коэффициенты интенсивности напряже-
ний K (или KI): KIC, KC , KQT, KC;
–деформационная − раскрытие в вершине трещины δC;
–энергетические − критические значения J-интеграла JC или JIC. Для определения вязкости разрушения применяются образцы,
представленные на рис. 3.60. Для корректного проведения испытаний необходимо, чтобы толщина образцов соответствовала табл. 3.2.
132
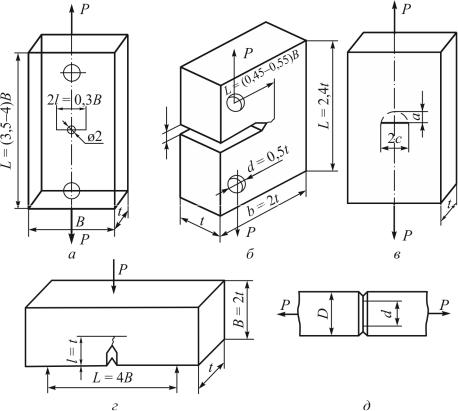
Рис. 3.60. Основные образцы для испытаний на вязкость разрушения: а – плоский прямоугольный с центральным отверстием; б – прямоугольный компактный образец с краевой трещиной для испытаний на внецентренное растяжение; в – плоский прямоугольный с центральной трещиной; г – плоский прямоугольный с краевой трещиной для испытаний на трехточечный изгиб; д – цилиндри-
ческий с кольцевой трещиной для испытаний на осевое растяжение
Таблица 3 . 2
Толщина образцов для испытаний на трещиностойкость в зависимости от соотношения прочности и модуля Юнга
Соотношение σТ/Е |
Толщина d, мм |
До 0,005 |
100 |
0,005...0,0057 |
75 |
0,0057...0,0062 |
63 |
0,0062...0,0065 |
50 |
0,0065...0,0071 |
38 |
0,0071...0,0080 |
25 |
0,0080...0,0095 |
13 |
0,0095 и более |
6,5 |
133
Величина KIc играет в механике разрушения доминирующую роль, определяя вязкость разрушения материала при достижении критической интенсивности напряжения, и имеет размерность МПа·м1/2 или Н/мм3/2.
Важность данной характеристики общепризнанна. Она имеет широкое применение в случае, когда пластическая деформация в ее вершине незначительна, т.е. трещина продолжает выполнять роль концентратора напряжений. Именно в этих случаях коэффициент интенсивности напряжений может быть измерен, а разрушение с точки зрения механики может считаться хрупким. Значения KIС для некоторых материалов представлены в табл. 3.3.
|
|
|
Таблица 3 . 3 |
|
Значение KIС для некоторых конструкционных материалов |
||||
|
|
|
|
|
Название материала |
Марка |
σТ, МПа |
|
K1с, МПаxм1/2 |
Легированная сталь |
25ХН3МФА |
745 |
|
120 |
Титановый сплав |
ВТ3-1 |
1010 |
|
52 |
Алюминиевый сплав |
Д16 |
290 |
|
33 |
3.6.6. Определение критической температуры хрупкости
Ударная вязкость из всех характеристик механических свойств наиболее чувствительна к понижению температуры. Поэтому испытания на ударную вязкость при пониженных температурах используют для определения порога хладноломкости – температуры или интервала температур, в которые происходит снижение ударной вязкости.
Хладноломкость – свойство металлического материала терять вязкость, хрупко разрушаться при понижении температуры. Хладно-лом- кость проявляется у железа, стали, металлов и сплавов, имеющих объемноцентрированюную или гексагональную плотноупакованную решетку. Она отсутствует уметаллов с гранецентрированной куби-ческойрешеткой.
На переход от вязкого разрушения к хрупкому указывают изменения строения излома и резкое снижение ударной вязкости (рис. 3.61) в интервале температур (tв – tх) (граничные значения температур вязкого и хрупкого разрушения).
Строение излома изменяется от волокнистого матового при вязком разрушении (t ≥ tв) до кристаллического блестящего при хрупком разрушении (t < tx). Порог хладноломкости обозначают интервалом температур (tв – tн) либо одной температурой Т50, при которой в изломе
134
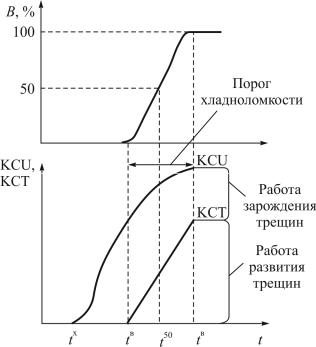
образца имеется 50 % волокнистой составляющей, и КСТ снижается наполовину. На рис 3.62 представлены сериальные кривые хладноломкости со структурой феррита (Ф), перлита (П) и смешанных структур с 25 % и 50 % перлита.
За критическую температуру хрупкости (порог хладноломкости) можно принять:
–температуру, при которойвпервые замечено понижение вязкости;
–интервал температур «вязкохрупкого перехода» от наибольшей вязкости до наименьшей;
–температуру Т50 (получение 50 % по площади волокнистого излома). Чаще всего для ряда температур выбирают ударную вязкость
KСU(T) или KCV(T), а затем исходя из этих показателей определяют интервал температур вязкохрупкого перехода. Для сдаточных норм стандартами чаще всего задается только ударная вязкость при минимально возможной температуре эксплуатации.
Схематическое изображение температурных зависимостей характеристик трещиностойкости показаны на рис. 3.63.
Рис. 3.61. Влияние температуры испытания на процент вязкой составляющей в изломе (В), ударную вязкость материала KCU, KCT
135
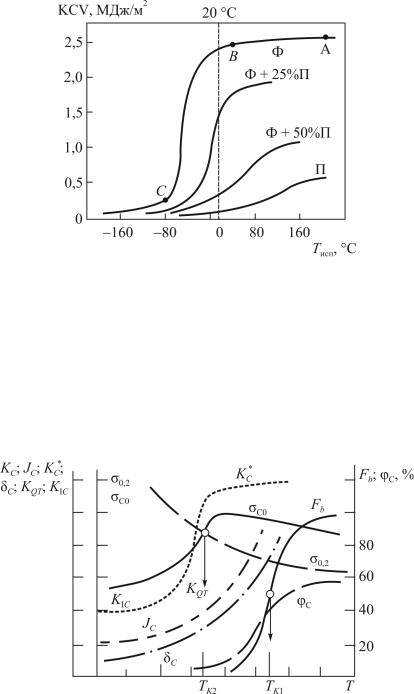
Рис. 3.62. Сериальные кривые для сталей со структурой феррита, перлита и смешанной структуры «феррит − перлит».
Точка В − начало перехода, С – конец перехода
Критические температуры TK1 и TK2 получают при испытаниях серии образцов для определения характеристик трещиностойкости в соответствии с требованиями стандарта.
Переход от вязких разрушений к квазихрупким определяют по первой критической температуре TK1, а от квазихрупких к хрупким по второй критической температуре TK2.
Рис. 3.63. Схематическое изображение температурных зависимостей характеристик трещиностойкости, а также предела текучести
и номинального разрушающего напряжения
136
Для определения TK1 и TK2 строят зависимости «FB – T» (процент вязкой составляющей в изломе FB – температура испытаний T) и «σC0 – T» (номинальные разрушающие напряжения в опасном сечении σC0 – температура испытаний Т).
По температурной зависимости «FB – T» при FB = 50 % устанавливают TK1, а при σC0 = σ0,2 по температурной зависимости «σC0 – T» устанавливают TK2. При этом предел текучести σ0,2 определяют при соответствующей температуре испытаний Т.
Если при разрушении в рассматриваемом диапазоне температур четко выраженный переход от вязкого разрушения к квазихрупким не устанавливается, то величину TK1 устанавливают как минимальную температуру по сужению в зоне разрушения ϕC, составляющему 0,8 от максимального, соответствующего полностью вязкому разрушению, или по ϕC = 25 %.
Определение процента вязкой составляющей FB в изломах испытанных образцов проводят макрофрактографическим методом. Определение FB в изломах образцов типов 1, 2, 3 и 4 основаны на измерении площади хрупкой составляющей Пхр. Процент вязкой составляющей в изломах FB вычисляют по формуле
|
|
|
П |
хр |
|
(3.13) |
|
FB |
= 1 |
− |
|
100 %, |
|||
П0 |
|||||||
|
|
|
|
|
где Пхр – площадь хрупкой составляющей в изломе.
3.6.7. Силовой нанотестинг в исследовании механических свойств поверхности
До середины ХХ в. популярными методами экспресс-анализа механических свойств было макроиндентирование и определение твердости по Бринеллю. Твердость находили из соотношения НВ = Р/А, где А – площадь отпечатка, Р – сила, действующая на стальной шарик.
Для измерения микротвердости нагрузка была уменьшена до ~1 Н и шарик был заменен алмазной пирамидой, позволяющей локализовать нагружение в области порядка нескольких кубических микрометров. Так появился микротвердомер. В этом методе измеряется диагональ восстановленного отпечатка
Нµ= 1,8544Р/d2. |
(3.14) |
137
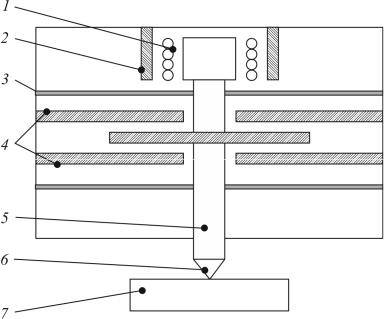
Более полувека назад появился метод непрерывного вдавливания алмазной пирамиды с одновременной регистрацией глубины отпечатка h и величины нагрузки – метод кинетической твердости. Полученные значения твердости иногда отличались в два раза. Непрерывная продолжающаяся миниатюризация продуктов высоких технологий повысила интерес к изучению механических свойств материалов в субмикро- и нанометровом диапазоне. Это стало актуально для тонкопленочных износостойких покрытий, микроэлектромеханических устройств, имплантированных элементов интегральных схем. В этой связи начиная с середины 80-х гг. метод непрерывной регистрации стали квалифицировать как метод наноидентирования. Схема нанотвердомера представлена на рис. 3.64.
Рис. 3.64. Схема нанотвердомера: 1 – катушка индуктивности; 2 – постоянный магнит; 3 – пластинчатая пружина; 4 – пластины конденсатора; 5 – стержень индентора; 6 – индентор; 7 – образец
Вкачестве индентора используют трехгранную призму Берковича.
Уэтого индентора радиус закругления вершины пирамиды намного меньше, чем у обычно применяемой для измерения микротвердости четырехгранной пирамиды, в современных приборах его значение достигает 40 нм. Поэтому применение индентора Берковича позволяет проводить испыта-
138
ния при существенно более низких нагрузках, чем в случае применения четырехгранного индентора Виккерса. Силовой привод – электромагнитный или электростатический. Смещение штока определяют емкостным методом, разрешающая способность которого составляет 10–12–10–13 м.
Примеры использования силового нанотестинга в исследовании меха-
нических свойств поверхности. Как уже отмечалось, по мере уменьшения области деформирования меняются все структурно-чувствительные характеристики материала. Каким образом изменяются при этом механизмы перехода от упругой к пластической деформации и природа самого пластического течения? Это важно, например, для высокоплотной записи атомарным острым зондом на относительно мягкий носитель.
Причины специфики механических свойств материалов в динамических наноконтактах многочисленны:
–высокие градиенты напряжений, деформаций и концентрации структурных дефектов;
–большая стесненность деформируемого объема;
–высокое контактное давление;
–высокая скорость относительной деформации (105–106 с–1);
–большая роль специфической структуры поверхности;
–нарастание роли поверхностных сил по мере уменьшения размеров контактного пятна;
–трудности зарождения дислокационных петель, зародышей новой
фазы;
–смена механизмов деформации и разрушении.
Типичные примеры Р–h-диаграмм приведены на рис. 3.65.
На этих кривых можно выделить ряд характерных участков: монотонного роста h с увеличением нагрузки, скачкообразного приращения h и медленного роста h при постоянной нагрузке. Интересно отметить, что скачки происходят не только на стадии нагружения, но и при выдержке под максимальной нагрузкой и даже при разгрузке. Несмотря на то, что индентор Берковича номинируется как остроконечная трехгранная пирамида, кончик реального индентора в первом приближении можно считать сферическим с эффективным радиусом R, который имел имел радиус 220 нм.
Таким образом, при глубинах до десятков нанометров испытание происходит в результате погружения не треугольной пирамиды, а сферы. Нагрузка возрастала по закону Герца P~h3/2, как для упругого взаи-
139

модействия твердого шарика с поверхностью. Разгрузка до скачка деформации в большинстве случаев приводила к полностью обратимому (упругому) поведению материала.
Рис. 3.65. Скачкообразная деформация на пределе текучести при наноиндентировании монокристаллов KCl (а) с различным содержанием примеси CaCl2 (1 – 0,01 %, 2 – 0,3 %) и при разных скоростях деформирования (ε, s–1: 1, 2 – 2, 3 – 1,2·105, 4 – 1,7·105), монокристаллов CaF2 (б) (1 – поверхность скола, 2 – поверхность после механической полировки), монокристаллов InP и LiNbO3 (в), кубического нитрида бора и фторида лития (г), металлов различной твердости (д). Скачки возможны не только принагружении, но ипри разгрузкеотпечатка (е)
140