
2828.Экспертиза качества и разрушений
..pdfКоэрцитивная сила может быть определена по магнитной индукции В в образце (BHс) или измерения его намагниченности J. Наиболее распространены коэрцитиметры для измерения коэрцитивной силы по намагниченности (ее обозначают JHc, или Нс), что объясняется простотой методики измерений и, кроме того, для материалов с Нс < 500 А/см значения коэрцитивной силы, определяемые по индукции и намагниченности, мало отличаются друг от друга.
К числу магнитных методов контроля структуры сталей относятся приборы, использующие эффект Баркгаузена. В настоящее время метод, основанный на использовании эффекта Баркгаузена, имеет ряд неоспоримых преимуществ перед традиционными магнитными методами неразрушающего контроля качества ферромагнитных материалов, использующих в качестве инструмента контроля одну или несколько магнитных характеристик, например коэрцитивную силу или магнитную проницаемость. Метод заключается в возбуждении в материале переменного магнитного поля и фиксации скачков ЭДС. Баркгаузена, возникающих при перемещении доменных границ под влиянием внешнего поля. Параметры получаемых при этом совокупностей скачков зависят от фазового состава материала, дисперсности фазовых составляющих стали, их конфигурации, наличия инородных включений, распределения полей напряжений, кристаллографической и магнитной текстуры и т.д., т.е. полностью характеризуют магнитное состояние материала. Основным преимуществом данного метода по сравнению с традиционными является большое количество независимых параметров, определяющих динамику магнитной структуры, что позволяет проводить многопараметровый мониторинг процессов структурообразования. На рис 3.52 приведен один из простых анализаторов шумов Баркгаузена, предназначенный для определения шлифовальных прижогов, твердости, обезуглероживания, уровня остаточных напряжений в металле.
Однако эффективность применения метода для исследования структуры и свойств ферромагнитных материалов в значительной степени зависит от его аппаратурной реализации. Это связано как с необходимостью максимального охвата множества параметров, характеризующих изменение динамики доменных границ при циклическом перемагничивании ферромагнетика внешними магнитными полями, так и с низкой интенсивностью информативных сигналов, что требует включения в состав аппаратуры усилительных устройств с малым уровнем собственных шумов и работающих в широком частотном диапазоне.
121
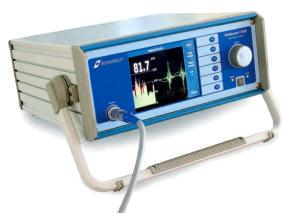
Рис. 3.52. Цифровой анализатор шумов Баркгаузена Rollscan 300
Начиная с середины 70-х гг., когда эффект Баркгаузена начал интенсивно использоваться в технических приложениях, разработано множество приборов и устройств для измерения и регистрации скачков ЭДС. Баркгаузена – от простейших приборов, регистрирующих один параметр, до измерительных комплексов, позволяющих осуществлять многопараметровый контроль. Как правило, создание такой аппаратуры было нацелено на решение конкретной задачи контроля определенной характеристики качества ферромагнитного материала. В настоящее время назрела необходимость создания универсального устройства, позволяющего регистрировать и обрабатывать информацию о магнитной структуре широкого круга ферромагнетиков в режиме реального времени с использованием современных методов спектрального анализа и математической статистики.
3.6. Анализ металлов по механическим свойствам
Данный вид контроля проводится в центральных заводских лабораториях в соответствии с требованиями технологических инструкций. Содержание и объем контроля механических свойств, поступающей на предприятие металлопродукции, определяется маркой металла, состоянием поставки и назначением в соответствии с нормативно-технической документации.
Как правило, механические свойства контролируются при испытаниях: на одноосное растяжение, на твердость, на ударную вязкость. Форма и размеры образцов для испытаний должны соответствовать требованиям ГОСТ 1497–84 и ГОСТ 9454–78.
122
3.6.1. Измерение твердости
Твердость − это сопротивление тела внедрению индентора − другого твердого тела.
Методы определения твердости по способу приложения нагрузки делятся: 1) на статические и 2) динамические (ударные). Эти методы позволяют проводить сравнительную оценку механических свойств материала за короткое время, т.е. метод является экспрессным.
Для измерения твердости существует несколько шкал (методов измерения):
1.Метод Бринелля – твердость определяется по диаметру отпечатка, оставляемому металлическим шариком, вдавливаемым в поверхность. Твердость вычисляется как отношение усилия, приложенного к шарику,
кплощади отпечатка (причем площадь отпечатка берется как площадь части сферы, а не как площадь круга (твердость по Мейеру)); размерность единиц твердости по Бринеллю Па (кгс/мм²). Число твердости по Бринеллю по ГОСТ 9012–59 записывают без единиц измерения. Твердость, определенная по этому методу, обозначается HB, где H = hardness (англ. твердость), B – Бринелль.
2.Метод Роквелла – твердость определяется по относительной глубине вдавливания металлического шарика или алмазного конуса в поверхность тестируемого материала. Твердость, определенная по этому методу, является безразмерной и обозначается HR, HRB, HRC и HRA; твердость вычисляется по формуле HR = 100 − kd, где d – глубина вдавливания наконечника после снятия основной нагрузки, а k – коэффициент. Таким образом, максимальная твердость по Роквеллу соответствует
HR = 100.
3. Метод Виккерса – твердость определяется по площади отпечатка, оставляемого четырехгранной алмазной пирамидкой, вдавливаемой в поверхность. Твердость вычисляется как отношение нагрузки, приложенной к пирамидке, к площади отпечатка (причем площадь отпечатка берется как площадь части поверхности пирамиды, а не как площадь ромба); размерность единиц твердости по Виккерсу – кгс/мм². Твердость, определенная по этому методу, обозначается HV.
4. Методы Шора. Методом вдавливания твердость определяется по глубине проникновения в материал специальной закаленной стальной иглы (индентора) под действием калиброванной пружины. В данном методе измерительный прибор именуется дюрометром. Обычно метод
123
Шора используется для определения твердости низкомодульных материалов (полимеров). Методом отскока определяют твердость очень твердых (высокомодульных) материалов, преимущественно металлов, по высоте, на которую после удара отскакивает специальный боек.
В некоторых случаях используется ряд других методов определения твердости: Кузнецова – Герберта – Ребиндера (по затуханию колебания маятника, опорой которого служит исследуемый металл), Польди (вдавливание стального шарика одновременно в образец и эталон), Мооса (царапание), Бухгольца (сопротивление механическим воздействиям).
Измерение твердости регламентируется следующими документами:
–ГОСТ 8.062–85 «Государственная система обеспечения единства измерений. Государственный специальный эталон и государственная поверочная схема для средств измеренийтвердости по шкалам Бринелля»;
–ГЭТ 33–85 «Государственный специальный эталон единиц твердости по шкалам Бринелля»;
–ГОСТ 24621–91 (ISO 868–85) «Определение твердости при вдавливании с помощью дюрометра (твердость по Шору)»;
–стандарты ISO 2815, DIN 53153 и др.
Для инструментального определения твердости используются приборы, именуемые твердомерами. Методы определения твердости в зависимости от степени воздействия на объект могут относиться как к неразрушающим, так и к разрушающим методам.
Существующие методы определения твердости в целом не отражают какого-нибудь одного определенного фундаментального свойства материалов, поэтому не существует прямой взаимосвязи между разными шкалами и методами, но существуют приближенные таблицы, связывающие шкалы отдельных методов для определенных групп и категорий материалов. Данные таблицы построены только по результатам экспериментальных тестов и не существует теорий, позволяющих расчетным методом перейти от одного способа определения твердости к другому.
3.6.2.Испытания на растяжение
Впроцессе испытания на растяжения определяют следующие величины: предел упругости, предел текучести, условный предел текучести, предел прочности, истинное сопротивление разрушению, относительное удлинение, относительное сужение.
124
Пределом упругости σуп называется напряжение, при котором остаточное удлинение достигает 0,05 % от расчетной величины образца и определяется по формуле
σуп |
= |
Р0,05 |
, |
(3.1) |
|
||||
|
|
F0 |
|
где Р0,05 – нагрузка, соответствующая пределу упругости; F0 – площадь. Пределом текучести σт называется наименьшее напряжение, при котором образец деформируется (течет) без заметного увеличения на-
грузки:
σт = |
РТ |
, |
(3.2) |
|
F0 |
||||
|
|
|
где РТ – нагрузка, соответствующая пределу текучести.
Условным пределом текучести σт называется напряжение, при ко-
тором остаточное удлинение достигает 0,2 % от расчетной длины образца:
σ0,2 |
= |
Р0,2 |
. |
(3.3) |
|
||||
|
|
F0 |
|
где P0,2 – нагрузка, соответствующая пределу текучести.
Пределом прочности σВ называется напряжение, отвечающее наи-
большей нагрузке РВ, предшествующей разрушению образца: |
|
||
σВ = |
РВ |
. |
(3.4) |
|
|||
|
F0 |
|
Истинным сопротивлением разрушению SK называется напряже-
ние, определяемое отношением нагрузки РK в момент разрыва образца к площади поперечного сечения FK образца в шейке после разрыва:
SK |
= |
РK |
. |
(3.5) |
|
||||
|
|
FK |
|
Относительным удлинением δ называется отношение абсолютного удлинения, т.е. приращения расчетной длины образца после разрыва (lK – l0), к его первоначальной расчетной длине l0, выраженное в процентах:
δ = |
lK − l0 |
100 %, |
(3.6) |
|
l0
где lK – длина образца после разрыва.
125
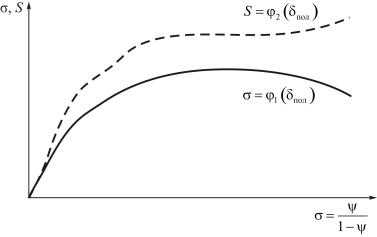
Относительным сужением ψ называется отношение абсолютного сужения, т.е. уменьшения площади поперечного сечения образца после разрыва (F0 – FK), к его первоначальной площади его поперечного сечения выраженное в процентах, где FK – площадь поперечного сечения образца после разрыва.
ψ = |
F0 − FK |
100 %. |
(3.7) |
|
|||
|
F0 |
|
Относительным удлинением и сужением характеризуется пластичность металла.
На рис. 3.53 приведена истинная диаграмма растяжения (истинное напряжение S − полная деформация δ) и экспериментально получаемая диаграмма (напряжение σ − полная деформация δ), а на рис. 3.54 − две диаграммы растяжения – при большом и малом относительном удлинении, построенные в координатах «напряжение σ (нагрузка Р) – удлинение ∆l».
Рис. 3.53. Условная и истинная диаграмма разрушения при испытании на растяжение
Для испытаний на растяжение металла круглого, квадратного и шестигранного сечения от партии отбирают две пробы длиной 60 мм от любого конца проката.
Для испытаний на растяжение проволоки, поступающей в бухтах для изготовления пружин, от одной бухты каждой партии отбирается проба длиной 600 мм, а для проволоки диаметром ≤ 0,9 мм – одна проба длиной 1500 мм на расстоянии не менее 1 м от конца бухты.
126
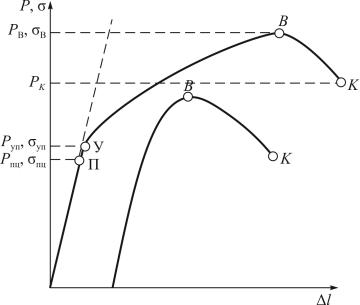
Рис. 3.54. Два типа диаграмм испытания на растяжение
вкоординатах «нагрузка Р − удлинение ∆l»
и«напряжение σ − удлинение ∆l»
Для испытаний на растяжение листового проката от одного листа отбирают две пробы длиной 250 мм и шириной 50 мм вдоль направления прокатки, а от листов из алюминиевых и магниевых сплавов – поперек прокатки. Для лент и полос от одного рулона каждой партии отбирается проба длиной 400 мм на расстоянии не менее 1 м от конца рулона.
3.6.3. Испытания на изгиб
Испытания на изгиб (ГОСТ 14019–80) проводятся по двум схемам: 1) сосредоточенной нагрузкой, приложенной в середине пролета
(рис. 3.55). В этом случае наибольший изгибающий момент
Мизг = Pl/4, |
(3.8) |
где Р – изгибающая нагрузка; l – расстояние между опорами, на которых установлен образец;
2) двумя равными, симметрично приложенными (на равных расстояниях от опор) сосредоточенными нагрузками, создающими на определенном участке чистый изгиб (рис. 3.56). Расстояние от опоры а целесообразно принимать равным 1/3 расчетной длины образца.
127
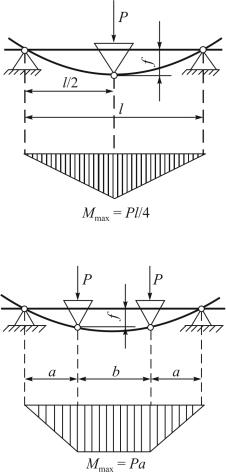
Рис. 3.55. Схема испытаний на сосредоточенный изгиб
Рис. 3.56. Схема испытаний на чистый изгиб |
|
При чистом изгибе |
|
Мизг = Pa/2. |
(3.9) |
Результаты испытаний по второй схеме более точные, так как наибольшие напряжения возникают на определенном участке длины образца, и поэтому оценивается не одно (случайное) сечение, как в первом случае, а значительный объем образца.
При испытаниях на изгиб можно подсчитать напряжения, соответствующие различным нагрузкам, а также определить стрелу прогиба образца f. Это определение проводится либо по кривой, полученной на диаграммном приборе машины, либо с помощью специальных приборов – прогибомеров.
128

На рис. 3.57 представлены типичные диаграммы изгиба для пластичных (рис. 3.57, а), малопластичных (рис. 3.57, б) и хрупких (рис. 3.57, в) материалов.
Рис. 3.57. Диаграммы изгибов: а – пластичный материал; б – малопластичный; в – хрупкий
Максимум нагрузки часто совпадает с появлением первой трещины. Иногда образование трещин сопровождается резкими перегибами на ниспадающей ветви диаграммы.
Предел прочности при изгибе в этом случае σизг = Mизг/W, где W (момент сопротивления) – геометрическая характеристика поперечного сечения бруса, показывающая сопротивляемость бруса изгибу в рассматриваемом сечении.
При изгибе можно определить пределы пропорциональности, упругости и текучести с точным замером деформаций.
Величина прогиба fразр характеризует пластичность; она зависит от материала, длины образца, момента инерции, от отношения высоты
кширине и способа приложения нагрузки.
Взависимости от вида нагружения изменяется и характер напряженного состояния. При испытании на растяжение главные нормальные напряжения направлены вдоль направления растяжения и одинаковы во всех точках поверхности перпендикулярной оси образца. При испытании на
129
изгиб главные нормальные напряжения параллельны поверхности образца, и их величина максимальна на поверхности. При испытании на кручение на поверхности образца образца возникают максимальные касательные напряжения в плоскости, перпендикулярной оси образца.
Напряженное состояние оказывает большое влияние на характер разрушения. Так, касательные напряжения способствуют пластической деформации и увеличивают работу, необходимую для разрушения.
3.6.4. Определение ударной вязкости
Очень часто детали в процессе работы испытывают действие не только плавно возрастающих нагрузок, но одновременно подвергаются и ударным (динамическим) нагрузкам. Поэтому необходимо знать, насколько хорошо сопротивляется металл действию на него этих нагрузок. Для испытания на ударную вязкость от листов, полос толщиной не менее 11 мм, от труб с толщиной стенки не менее 14 мм, прутков диаметром не менее 16 мм от любого конца рядом с пробой для испытаний на растяжение отбирают две пробы размером 11×11×60 мм для изготовления образцов размером 10×10×55 мм. От проката толщиной до 10 мм отбирают две пробы для изготовления образцов размером 5×10×55 мм. Для испытаний на ударную вязкость при минусовых температурах отбирают три пробы.
При получении результатов, не соответствующих сертификату, испытание повторяют на удвоенном количестве образцов. Если при повторных испытаниях получены отрицательные результаты хотя бы на одном образце, то вся партия металла бракуется. Результаты механических свойств металла отражают в паспорте входного контроля с приложением таблиц испытаний.
Метод основан на разрушении образца с концентратором посередине одним ударом маятникового копра. Концы образца располагают на опорах. В результате испытания определяют полную работу, затраченную при ударе (ударную вязкость). Испытание на удар проводится на специальном приборе, называемом маятниковым копром, изломом надрезанного образца, свободно установленного на две опоры копра (рис. 3.58), падающим с определенной высоты массивным маятником.
Под ударной вязкостью следует понимать работу удара, отнесенную к начальной площади поперечного сечения образца в месте концентратора напряжения.
130