
2828.Экспертиза качества и разрушений
..pdf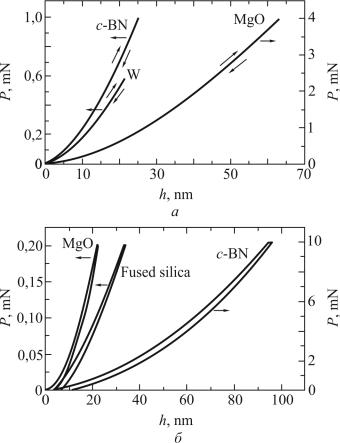
Некоторые материалы демонстрировали необратимость на начальной стадии внедрения индентора (рис. 3.66), которая, вероятно, обусловлена генерацией и движением неравновесных точечных дефектов.
Рис. 3.66. Полностью упругая разгрузка (а) и почти полностью обратимая разгрузка (б) в одних и тех же материалах при разных нагрузках
Оборудование для наноиндентирования требует высочайшей точности изготовления и настройки. Проведение испытаний подразумевает полную изоляцию материалов, так как малейшие температурные и атмосферные флуктуации способны сильно исказить результаты. Контактный нанотестинг является частью зондовых нанотехнологий и, по существу, единственным экспериментальным средством получения количественных, а не только оценочных значений величин, характеризующих совокупность механических и функциональных свойств поверхностных слоев материалов в нано- и субмикрообъемах.
141
4.ВИДЫ РАЗРУШЕНИЯ
ИИХ МАКРОСТРУКТУРНОЕ ПРОЯВЛЕНИЕ
Вшироком смысле под нарушением прочности (разрушением) понимается достижение такого состояния, когда нарушается конструктивная функция тела, и оно становится непригодным к эксплуатации.
Вболее узком смысле под нарушением прочности понимается разделение тела на части. Для пластичных материалов под разрушением следует понимать возможность появления недопустимо больших деформаций.
Разрушение, наряду с другими причинами отказа в работе, например нарушение геометрических размеров, качества поверхности и т.п., является одной из наиболее часто встречающейся причиной отказа работы изделий.
Посвоему характеру разрушение подразделяется на следующие виды. Пластическое. Происходит после существенной пластической деформации, протекающей по всему или почти по всему объему тела. Примером пластического разрушения может служить разрыв образца из отожженной меди после 100 % сужения шейки при растяжении, происходящий в результате утраты способности материала сопротивляться
пластической деформации.
Хрупкое. Происходит в результате распространения магистральной трещины после пластической деформации, сосредоточенной в области действия механизма разрушения. Хрупкое разрушение подразделяется на идеально хрупкое и квазихрупкое («как бы» хрупкое).
Идеально хрупкое или хрупкое разрушение происходит без пластической деформации. После разрушения можно заново составить тело прежних размеров из осколков зазоров между ними.
Квазихрупкое разрушение предполагает наличие пластической зоны перед краем трещины (локальная зона пластической деформации)
инаклепанного материала у поверхности трещины. Остальной, значительно больший по величине объем тела находится при этом в упругом состоянии.
Усталостное. Происходит при повторно-циклическом нагружении врезультате накопления необратимых повреждений. При этом виде разрушения на поверхности тела вначале появляются микротрещины, одна из
142
которых в результате многократного приложения нагрузки прорастает вмакротрещину с последующим полным разрушением образца или детали машин. Различают многоцикловую илималоцикловую усталость.
Многоцикловая усталость, или просто усталость, характеризуется номинальными напряжениями, меньшими предела текучести σт; повторное нагружение происходит в упругойобласти вплоть до разрушения.
Малоцикловая усталость характеризуется номинальными напряжениями, большими предела текучести σт. При каждом цикле нагружения в теле возникает макроскопическая пластическая деформация. При таком виде нагружения число циклов до разрушения не превышает 105.
Деформация и разрушение при ползучести. При достаточно высоких температурах в поликристаллическом металле границы зерен становятся более слабыми, чем сами зерна, и значительная часть деформации ползучести происходит за счет скольжения зерен относительно друг друга. Это скольжение носит характер вязкого течения, оно затруднено кинематически, так как зерна имеют неправильную форму и каждое зерно встречает сопротивление со стороны соседних. Скольжение становится возможным за счет пластической деформации зерен и сопровождается появлением межзеренных трещин, приводящих к разрушению.
Коррозионное разрушение. Происходит за счет химических и электрохимических процессов и реакций. Коррозия часто не изменяет механические свойства материала, а приводит к постепенному равномерному уменьшению размеров нагруженной детали, например вследствие постепенного растворения. В результате напряжения, действующие в опасном сечении, растут, и, когда они превысят допустимый уровень, произойдет разрушение.
Разрушение под действием жидких металлов.
Разрушение при износе. Возникает при трении или других формах воздействия тел друг на друга.
4.1. Хрупкое разрушение. Описание с позиции линейной механики
Хрупкое разрушение является сложным процессом, и оно может рассматриваться:
–атомном уровне;
–на уровне структуры материала;
–на основе механики сплошной среды.
143
Хрупкое разрушение на атомном уровне предполагает поочередный − от атома к атому − разрыв межатомных связей, что в целом представляет собой распространение трещины. На уровне структуры хрупкое разрушение − это процесс разделения кристалла по плоскостям спайности под действием нормальных напряжений. С позиции механики разрушения хрупкое разрушение рассматривается как результат действия только упругих напряжений и связанных с ними упругих деформаций.
Последний из указанных подходов имеет особенно большое прикладное значение, поскольку позволяет найти способы оценки возможности хрупкого разрушения на образцах и изделиях. Решающие результаты получены в том разделе механики, где используется линейная зависимость между напряжениями и деформацией (закон Гука).
Развитие трещины − основной этап хрупкого разрушения.
Любой материал, какой бы технологической обработке он ни подвергался, всегда обладает каким-либо несовершенствами: большим количеством вакансий или межузельных атомов, большой первоначальной плотностью дислокаций, микротрещинами, включениями, дефектами изготовления. Каждое из этих несовершенств определенным образом влияет на прочность детали, т.е. на развитие в ней трещины. До 40-х гг. XX в. наличие дефектов в деталях машин или элементах конструкций при расчетах на прочность не учитывалось. Считалось, что при достижении предельного значения напряжения конструкция мгновенно разрушается, т.е. процесс развития трещин во внимание не принимался. Однако анализ катастроф гражданских и промышленных объектов в авиации, в морском судоходстве показал, что развитие трещины занимает значительный период, предшествующий не только пластическому разрушению, но и усталостному и даже хрупкому. Во всех этих случаях разрушение происходило без заметных остаточных деформаций. Наблюдения показали, что развитие трещины – сложный процесс, и знание его закономерностей имеет огромное значение для практики.
Определяющей стадией хрупкого разрушения является этап развития разрушающей трещины. Зарождение же трещины подготавливается дефектами, которые в большинстве случаев есть в металле. При невысоких напряжениях они не опасны.
При больших нагрузках они могут оказаться неустойчивыми, способными к быстрому росту, слиянию друг с другом и образованию магистральных трещин, приводящих к разрушению конструкций. Есть
144
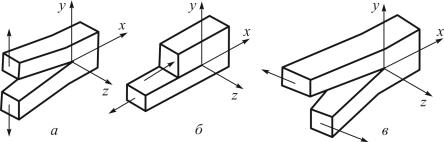
много примеров катастрофического разрушения газопроводов, корпусов судов, мостов, самолетов, ракет в результате трещинообразования. Это свидетельствует о недостаточности оценки прочности с помощью традиционных подходов по упругому или пластическому состоянию конструкций.
Поэтому большое значение приобретает анализ закономерностей развития трещины. Трещины начинают развиваться задолго до полного разрушения при усталостном, пластическом и даже хрупком разрушении. Длительность процесса разрушения, т.е. рост трещины до полного разрушения, занимает значительную часть «жизни» детали, доходя до 90 % и выше. Главное при эксплуатации детали – не наличие у нее трещины, а темп ее роста. Рассмотрим, какие типы трещин встречаются на практике.
Раскрытие трещины в твердом теле может быть осуществлено тремя различными путями (рис. 4.1).
Рис. 4.1. Возможные типы трещин в связи с видом приложения напряжения
При нормальных напряжениях возникает трещина типа «разрыв» (тип I) (рис. 4.1, а), когда берега трещины перемещаются перпендикулярно плоскости трещины. При плоском сдвиге образуется трещина типа «сдвиг» (тип II) (рис. 4.1, б): перемещения берегов трещины происходят в плоскости и перпендикулярно ее фронтальной линии. Трещина типа «срез» (тип III) (рис. 4.1, в) образуется при антиплоском сдвиге: перемещения берегов трещины совпадают с плоскостью трещины и параллельны ее направляющей кромке.
В общем случае трещину можно описать этими тремя типами. Чаще всего в технике встречается трещина типа I, так как большая часть элементов конструкций разрушается в случае, если берега трещины перпендикулярны плоскости трещины.
145

Теоретические оценки прочности показали, что напряжение, при котором происходит разрушение твердого тела, может быть вычислено по формуле
σmax = |
γE |
, |
(4.1) |
|
|||
|
a |
|
где γ − энергия поверхностного натяжения; Е − модуль Юнга; а − расстояние между атомами.
Если из рассчитываемого материала изготовить образец и разрушить его, то можно получить значение технической или экспериментальной прочности. Сопоставление ее с теоретической прочностью показывает, что техническая прочность в десятки и даже сотни раз меньше теоретической. Объяснение столь резкой разницы впервые было дано в 1920 г. академиком А.Ф. Иоффе на следующем примере: им были испытаны два кристалла поваренной соли, второй из которых он выдерживал некоторое время в горячей воде. Если прочность первого кристалла равнялась нескольким мегапаскалям, то прочность второго была более высокой – около 2000 МПа, что лишь в 2 раза меньше теоретического значения прочности для поваренной соли.
Такое существенное различие в экспериментальных прочностях объясняется тем, что первый образец имел большое количество поверхностных дефектов (щербины, царапины, трещины), второй же образец, лишившись поверхностного слоя, освободился от них. Отсюда вывод: чем совершеннее структура материала, тем ближе его техническая прочность к теоретической.
Интенсивные исследования в области получения чистых металлов позволили еще в 30-х гг. достигнуть чрезвычайно высокой технической прочности на кварцевых нитях (σВ = 13000 МПа), а на стеклянных нитях техническая прочность равнялась σВ = 6000 МПа. Позднее в Физикотехническом институте им. А.Ф. Иоффе профессором А.В. Степановым были получены нитевидные монокристаллы («усы») некоторых металлов с прочностью около 10000 МПа. Если учесть, что прочность большинства конструкционных сталей колеблется в пределах 300–1000 МПа, то огромная разница в прочности налицо: исправление дефектной структуры кристаллов увеличивает их прочность на несколько порядков и приближает ее к теоретическому значению, которое можно приближенно считать равным
σВ (теор) 0,1Е. |
(4.2) |
146

Эксперименты по упрочнению кристаллов, а также многочисленные случаи преждевременного разрушения конструкций и сооружений при напряжениях, значительно меньших расчетных, показали недостаточность развитых представлений о прочности как о постоянной материала. Такое значительное различие между теоретической и реальной прочностью материалов на современном уровне объясняется технологическими нарушениями сплошности материала – трещинами.
Исправление дефектной структуры кристаллов увеличивает их прочность на несколько порядков и приближает ее к теоретическому значению.
Несоответствие между теоретической прочностью межатомных связей и экспериментальной прочностью натолкнуло английского ученого А. Гриффитса на мысль, что большое расхождение в прочностях объясняется наличием мелких трещин в однородном материале, которые приводят к большой концентрации напряжений в упругом состоянии.
Рассмотрим бесконечную пластину единичной толщины с центральной поперечной трещиной длиной 2l. Края трещины неподвижны, а напряжение в ней равно σ (рис. 4.2, а).
Рис. 4.2. Освобождение энергии упругой деформации при росте трещины
На рис. 4.2, б приведена диаграмма «нагрузка – удлинение». Запасенная в пластине упругая энергия представлена площадью ОАВ. Если длина трещины увеличится на величину dl, то жесткость пластины уменьшится (линия ОС); это означает, что нагрузка несколько уменьшится, поскольку края пластины неподвижны. Следовательно, упругая энергия, запасенная в пластине, уменьшится до величины, равной ОСВ.
147
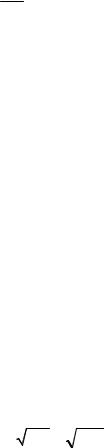
Увеличение длины трещины от l до l+dl приведет к высвобождению упругой энергии, равной по величине площади ОАС.
Условие, необходимое для роста трещины, следующее:
dU |
= |
dW |
, |
(4.3) |
|
|
|||
dl dl |
|
где U – упругая энергия; W – энергия, необходимая для роста трещины. Иными словами, продвижение трещины, образование ее поверхностей происходит за счет упругой энергии, запасенной к этому моменту в пластине.
Основываясь на расчетах, А. Гриффитс получил выражение для dU/dl в виде
dU = πσ2l
(4.4)
dl E
на единицу толщины пластины, где Е – модуль упругости.
Величину πσ2l/E называют скоростью высвобождения упругой энергии, или трещинодвижущей силой.
Поверхностная энергия пластины, связанная с наличием в ней трещины,
W = 4γl, |
(4.5) |
где γ – удельное поверхностное натяжение, вводимое для твердого тела по аналогии с таким же понятием для жидкости.
Энергию, расходуемую на распространение трещины, найдем следующим образом:
|
dW |
= 2γl. |
(4.6) |
|
|
||
|
dl |
|
|
Приравнивая правые части (4.4) и (4.6), получим |
|
||
2El = πσ2l. |
(4.7) |
Вследствие этого возникает хрупкое разрушение, которое характеризуется коэффициентом интенсивности напряжений
KI = σk πlk = 2Eγ . |
(4.8) |
Этот коэффициент имеет размерность Н/мм3/2.
148
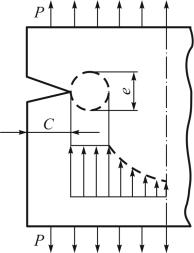
При достижении критического напряжения трещина начинает развиваться неустойчиво, происходит хрупкое разрушение.
В вязких материалах, например металлах, при вершине трещины образуются пластические деформации. Для образования новой зоны пластических деформаций при вершине трещины необходима большая энергия.
Модель развития трещины для пластического материала показана на рис. 4.3.
Рис. 4.3. Пластическая деформация в вершине трещины
Предполагается, что при нагружении пластины с надрезом в зоне надреза на расстоянии с от края пластины появляется пластическая зона диаметром е, в которой действует постоянное напряжение. По мере удаления от этой зоны напряжение падает. Поскольку пластическая зона должна быть образована в процессе роста трещины, то энергию, необходимую для распространения трещины, считают равной энергии, необходимой для образования этой трещины. Это означает, что в металлах величина dW/dl определяется главным образом энергией деформации в пластической зоне; поверхностная энергия в этом случае настолько мала, что ею пренебрегают. Исходя из этих соображений, Д. Ирвин, развивая идею А. Гриффитса, предложил величину
dU |
= πσ2l = G |
(4.9) |
|
dl |
|||
E |
|
149

назвать силой, необходимой для распространения трещины на 1 см. Если сила распространения трещины G превысит критическое значение Gk, то трещина будет распространяться самопроизвольно. Таким образом, критерием разрушения является
G > Gk. |
(4.10) |
||
Для плоского напряженного состояния |
|
||
G = πσ2l , |
(4.11) |
||
E |
|
||
а при плоском деформированном состоянии |
|
||
G = (1− µ2 ) |
πσ2l |
, |
(4.12) |
|
|||
|
E |
|
где µ – коэффициент Пуассона материала; l – длина трещины, мм; σ – действующее напряжение, МПа; Е – модуль упругости материала, МПа.
Величина G достигает своего критического значения при критическом значении lσ2k т.е. опасность разрушения определяется величиной
lσ2k . Если в это произведение включить π, то получим ту же зависимость, которая в свое время была получена А. Гриффитсом:
KIC = σk πlk . |
(4.13) |
Предельное значение коэффициента k Д. Ирвин обозначил через
KIC и назвал коэффициентом вязкости разрушения.
Важность данной характеристики общепризнанна. Она имеет широкое применение в случае, когда пластическая деформация в ее вершине незначительна. т.е. трещина продолжает выполнять роль концентратора напряжений. Именно в этих случаях коэффициент интенсивности напряжений может быть измерен, а разрушение с точки зрения механики может считаться хрупким.
При расчетах на прочность материалов с трещинами при хрупком разрушении в первую очередь учитываются размеры трещины и напряжения. Для определения размеров трещин на практике необходимо применять современные методы дефектоскопического контроля: ультразвук, рентгеноскопию, акустическую эмиссию и другие, что позволяет прогнозировать наступление критического состояния конструкции,
150