
2858.Оборудование литейных цехов учебное пособие
..pdf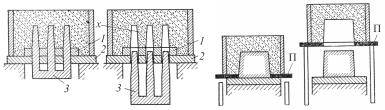
валивающимися, или протяжными. Сначала ребра проваливаются вниз через прорезы в модельной плите, после чего опоку снимают с оставшейсяневысокой части модели, поднимая штифтами.
Благодаря тому что болваны х при протяжке ребер модели имеют поддержку, они не обваливаются. Поэтому протяжку применяют при формовкевысоких, трудно вынимаемых моделей.
Протяжка может быть осуществлена и при помощи штифтового подъема (рис. 1.4). В таком случае опока находится на особой протяжной плите, имеющей вырез по контуру модели. После уплотнения смеси опока с протяжной плитой снимается штифтами с модели.
а |
б |
а |
б |
Рис. 1.3. Схемапротяжкиспровали- |
Рис. 1.4. Схемапротяжкимодели |
||
вающейся моделью: а и б – последо- |
с помощьюштифтового подъема: |
||
вательныеположения; 1 – неподвижная |
аиб– последовательные |
||
часть модели; 2 – модельнаяплита; 3 – |
положения; П – протяжная |
||
проваливающаяся (протягивающаяся) |
|
плита |
|
|
часть модели |
|
|
Протяжная плита при этом поддерживает опасные кромки формы х. При такой схеме не требуется наличия свободного места под столом машины. Поэтому ее чаще применяют в современных прессовых и встряхивающих машинах, в которых место под столом машинызанято прессовым или встряхивающим цилиндром.
Выполнение выреза в протяжной плите точно по контуру модели – трудоемкая и кропотливая работа. Вырез должен быть сделан с зазором относительно модели в 0,1–0,2 мм и обычно еще с заливкой баббитом. Поэтому для упрощения часто его
11
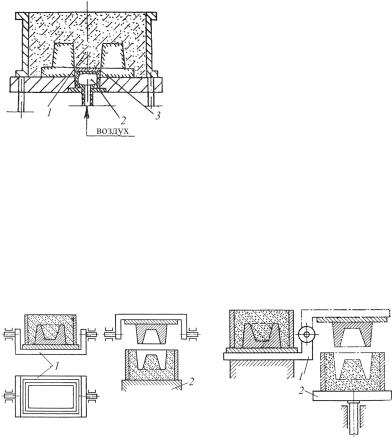
выполняют по упрощенному контуру, очерченному вокруг контура модели, несколько отступив от него.
В некоторых конструкциях при извлечении модели в полость между болваном и моделью подают сжатый воздух. На рис. 1.5 показана оснастка со специальной вставкой из эластичного материала с полостью 2.
При подаче сжатого воздуха верхняя часть вставки поднимается и упирается в выступ болвана 1. Для того чтобы верхний торец вставки был плоским и не нарушал отпечаток, в полость вставляется пластина 3. Давление воздухарегулируется дросселем.
Машины с поворотом фор-
мы на 180°. Принцип действия этих машин заключается в том, что уплотненная форма или стержневой ящик с набитым
стержнем переворачивается на 180°, после чего в таком перевернутом положении форма или стержень опускается на стол приемного устройства.
а |
б |
а |
б |
Рис. 1.6. Схемадействия поворотной |
Рис. 1.7. Схемадействия перекид- |
||
плиты: а и б – последовательные |
ного стола: а и б – последователь- |
||
положения; 1 – поворотнаяплита; |
ные положения; 1 – перекидной |
||
2 – приемноеустройство |
стол; 2 – приемный стол |
||
12 |
|
|
|
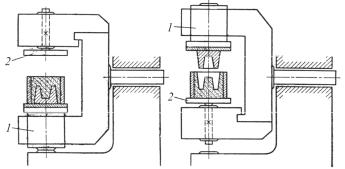
На практике применяют три конструктивные схемы машин: с поворотной плитой (рис. 1.6), с перекидным столом (рис. 1.7) и с поворотом всего корпуса машины – поворотные (рис. 1.8).
Способ вынимания и относительное положение модели и формы во всех этих схемах одинаковы. Для вытяжки модели из формы должно быть осуществлено относительное вертикальное перемещение модельной плиты и формы. В машинах с поворотной плитой в одних конструкциях приемное устройство перемещается по высоте, а модельная плита вместе с поворотной плитой остаются неподвижными. В других конструкциях, наоборот, поворотная плита вместе с модельной плитой поднимаются, а форма остается на неподвижном приемном столе. В машинах с перекидным столом ось поворота перекидного стола обычно не перемещается по высоте. Поэтому приемное устройство передвигается по вертикали и опока при вытяжке модели опускается на нем. В поворотных машинах (см. рис. 1.8) корпус машины вместе со встряхивающим и прессовым механизмом и уплотненной формой поворачивается на 180°, после чего модель вытягивается вверх при обратном ходе прессового механизма, а форма остается напрессовой плите, скоторой и удаляется.
а б
Рис. 1.8. Схема поворотной машины: а и б – последовательные положения; 1 – встряхивающе-прессовый механизм;
2 – прессовая плита
13
Формовочные машины с поворотом формы на 180° (см. рис. 1.6–1.8) следует применять, когда форма или стержень имеет массивные и высокие, трудно вынимаемые болваны. При других способах вынимания модели эти болваны, находясь на весу, могут обваливаться.
Машины с поворотом формы на 180° при прочих равных условиях имеют вдвое большее число ходов на операции извлечения модели. Поэтому они менее производительны, чем машины со штифтовым подъемом или с протяжкой модели, и их следует применять лишь в тех случаях, когда они технологически необходимы. Большей частью (но не всегда) они бывают нужны для формовки нижних опок и обычно не нужны для формовки верхних опок, так как в них, во избежание обвалов при сборке и заливке, не располагают тяжелых и сырых болванов. Для нижних опок машины с поворотом формы на 180° удобны также тем, что они выдают полуформы разъемом вверх, т.е. в рабочем для сборки положении.
По методу приведения в действие (по роду привода) сило-
вые формовочные и стержневые машины (т.е. имеющие не ручной, а механизированный привод) делятся на следующие типы: 1) пневматические; 2) гидравлические; 3) пневмогидравлические; 4) механические; 5) электромагнитные.
Пневматический привод наиболее распространен, так как в литейном цехе сжатый воздух используется и для других механизмов и машин.
Гидравлический привод широко применяется в случаях, когда необходимо создать высокие удельные давления прессования. Использование индивидуальных гидростанций на машинах позволяет реализовать все преимущества гидравлики высокого давления вотношении компактности механизмови плавности хода.
Пневмогидравлический привод используется большей частью для обеспечения плавности хода отдельных механизмов машин. В них энергия сжатого воздуха передается с помощью рабочей жидкости.
14
Механический привод от электродвигателей весьма экономичен. Он является наилучшим только для пескометов. Для приведения в действие ротора метательной головки вал его соединяют с валом двигателя без редукторов и передач.
Электромагнитный привод конструктивно прост. Стол машины, являясь сердечником электромагнита, перемещается по вертикали, если в катушку подать электрический ток. Этот привод весьма экономичен, так как в нем электроэнергия непосредственно преобразуется в механическую, обеспечивая движение рабочих органов машины.
По степени автоматизации формовочные машины можно подразделить на неавтоматические; полуавтоматические, включаемые при каждом новом цикле; автоматические, управляемые
спомощью автоматических аппаратов и устройств, без участия человека
По конструктивной компоновке и методу агрегатиро-
вания формовочные машины разделяются на однопозиционные; двухпозиционные челночные; многопозиционные проходного типа; многопозиционные карусельного типа. Наибольшее распространение получили однопозиционные (проходные), реже встречаются двухпозиционные и трехпозиционные (челночные)
сдвумя комплектами оснастки. В последнее время появились двухпозиционные автоматы с двумя комплектами оснастки, стол которых периодически поворачивается на 180° вокруг вертикальной оси.
Воднопозиционных автоматах отсутствует сложный привод карусели или тележки и механизм торможения, что увеличивает их надежность. Более перспективными являются трехпозиционные челночные автоматы, так как они производительней однопозиционных. На них могут формоваться одновременно верхняя и нижняя полуформы. Многопозиционные карусельные автоматы не нашли широкого применения, так как они занимают большую площадь, чем однопозиционные, имеют сложный привод карусели и менее надежны.
15
Достаточно известны многопозиционные формовочные автоматы с плавающей оснасткой. Такие автоматы применяются обычно в мелкосерийном и единичном производстве. Модельные плиты в таких автоматах установлены на специальных спут- никах-подставках, не скрепленных с основным транспортирующим органом. Модельная плита на спутниках проходит все технологические операции. Затем готовая полуформа снимается с модельной плиты и идет на сборку, а модельная плита возвращается по параллельному конвейеру на рабочие позиции.
2. УСТРОЙСТВА И МЕХАНИЗМЫ ДОЗИРОВАНИЯ СМЕСИ
Процесс дозирования смеси состоит из трех последовательно выполняемых технологических переходов: подача смеси, получение дозы (порции), выдача дозы. Механизмы подачи смеси передают смесь из бункера или цеховой смесераздаточной системы в дозатор. К этим механизмам относятся затворы (клапанные, шиберные и секторные), обеспечивающие периодическую подачу материала, и питатели (ленточные, пластинчатые), обеспечивающие непрерывную подачу материала.
Дозатор – механизм получения дозы, обеспечивает образование необходимой дозы смеси по объему, весу или по времени. При дозировании по объему необходимая доза образуется путем заполнения смесью полости заданного объема. В формовочных и стержневых машинах применяется дозирование главным образом по объему (коробчатые, шиберныеили секторные дозаторы).
Назначение механизмов выдачи дозы – передача дозы из полости дозатора в рабочую полость опоки (наполнительная рамка является тоже объемным дозатором). К числу механизмов выдачи дозы относятся также механизмы распределения или разравнивания смеси и механизмы среза излишков смеси (если процесс выдачи дозы сопровождается распределением смеси в опоке).
16
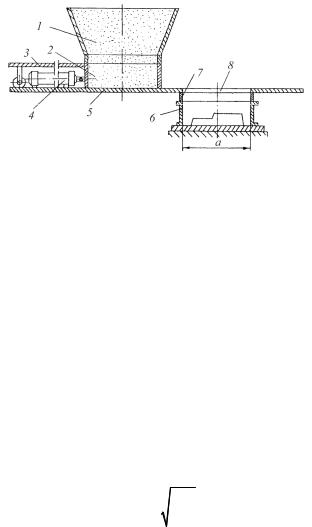
2.1. Коробчатые дозаторы
Схема коробчатого дозатора представлена на рис. 2.1.
Рис. 2.1. Схема коробчатого дозатора
Под бункером 1 со смесью расположена коробка 2, которая перемещается пневмоили гидроприводом 4 по плите 5. Разгрузка смеси из коробки в опоку 6 с наполнительной рамкой 7 производится через окно 8 в плите. При перемещении коробки со смесью для разгрузки отверстие бункера перекрывается заслонкой 3.
Длина хода дозирующей коробки определяется по формуле [13]
l = (0,6...0,8)l1 +1,5a, |
(2.1) |
где a – размер опоки в свету; l1 – расстояние от внутреннего края выпускного отверстия бункера l до края окна; обычно принимают l1 = hk/tgφ, hk – высота дозирующей коробки, φ – угол естественного откоса смеси.
Время разгрузки коробки tсм определяется по формуле
tсм = kсм |
2hk , |
(2.2) |
|
g |
|
где kсм = 1,3–1,5 – коэффициент, учитывающий трение смеси о стенки коробки.
17
Скорость движения коробки определяется по формуле
|
|
|
v |
|
= |
a |
. |
|
|
|
|
(2.3) |
|
|
|
|
tсм |
|
|
|
|||||
|
|
|
кор |
|
|
|
|
|
|
|
||
Пробег коробки можно принять 0,5а, объем дозирующей |
||||||||||||
коробки при пробеге 0,5а |
|
|
|
|
|
|
|
|
|
|
||
V |
= k |
(abh |
− V |
|
) |
δ |
+ a2b tgφ |
, |
(2.4) |
|||
|
|
|||||||||||
кор |
|
зап |
оп |
|
|
мод |
|
δ0 |
4 |
|
|
|
|
|
|
|
|
|
|
|
|
|
|
где a, b – размер опоки в свету; hoп – высота опоки; Vмод – объем наименьшей модели; δ0, δ – плотность смеси начальная и конеч-
ная; kзап = 1,1–1,2 – коэффициент запаса.
Усилие передвижения дозирующей коробки при отсутствии роликов
P |
= k |
( f |
см |
− f ')P + fG |
|
, |
(2.5) |
кор |
|
зап |
|
к |
|
|
где P – вертикальное усилие от давления смеси,
P = |
δR |
, |
(2.6) |
|
fсмk |
||||
|
|
|
где δ – плотность смеси, δ = 1,2·10–3 кг/см3; R – гидравлический радиус выпускного отверстия; fсм – коэффициент трения материала о материал, fсм = tgφ; φ – угол естественного откоса материала; k = (1–sinφ)/(1+sinφ). Для формовочной смеси φ = 38°; fсм = 0,78; k = 0,238; f = 0,06(v + 1,7) – коэффициент трения мате-
риала о плиту; f = 0,4…0,5; Gк – вес коробки; v – скорость перемещения коробки.
2.2. Шиберные дозаторы
Необходимая доза образуется в коробке 1 (рис. 2.2), ограниченной двумя шиберами: нижним 2 и верхним 3, получающими одновременное перемещение от пневмоцилиндра 4. При
18
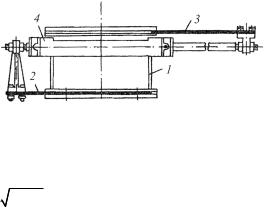
движении штока пневмоцилиндра влево верхний шибер 3 отсекает материал в бункере, а нижний выдает набранную дозу через выпускное отверстие коробки.
Рис. 2.2. Схема шиберного дозатора
Для нормальной работы коробки должно сохранятся условие vш>vтех, где vш = l/t – скорость движения шибера; vтех = l / tgφ gh / 2 – технологически необходимая скорость; l –
длина хода пневмоцилиндра; t – время его срабатывания; φ – угол естественного откоса смеси; h – расстояние между шиберами.
Объем дозирующей коробки определяется по формуле
Vкор = kзап (abhоп − Vмод ) |
δ |
. |
(2.7) |
|
|||
|
δ0 |
|
(Обозначения см. в формуле (2.4).)
Шиберные дозаторы имеют преимущества перед коробчатыми: меньше габаритные размеры и более простая конструкция. Недостаток – большая просыпь смеси.
Усилие передвижения шиберов определяется по формуле
P = k |
f 'P + f |
( |
P + 2G . |
зап |
зап |
ш ) |
(Обозначения см. в формуле (2.5).) Здесь Gш – вес шибера; kзап = 1,1…1,2 – коэффициент запаса.
Для учета дополнительного сопротивления материала, перерезаемого при закрытии верхнего шибера, необходимо ввести
коэффициент kзакр = 1,3…1,5, т.е. Pшиб = kзакрPзап.
19
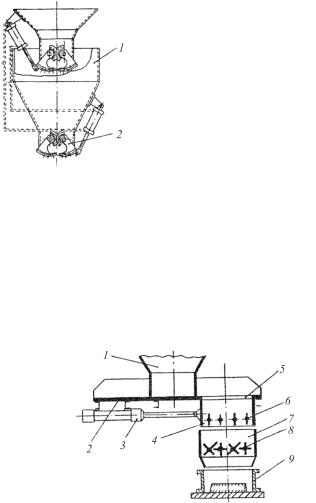
2.3. Челюстные дозаторы
Челюстная дозирующая коробка (рис. 2.3) 1 ограничена сверху и снизу двумя челюстными затворами 2, работающими поочередно. Челюстные затворы сложнее шиберных и больше их по габаритным размерам, поэтому в формовочных автоматах при-
меняются редко.
В том случае, когда между дозатором и наполнительной рамкой нет промежуточных элементов, дозатором служит опока с наполнительной рамкой, а количество смеси, находящееся в коробке 1,
превышает избыток смеси и воз-
Рис. 2.3. Схема челюстного вращается в бункер. дозатора
2.4. Коробчатый дозатор с жалюзийным затвором
Жалюзийный затвор (рис. 2.4) состоит из дозирующей коробки 4, которая жестко связана с горизонтальной плитой 2, имеющей отверстие 5, и перемещается в горизонтальном направлении приводом 3.
Рис. 2.4. Жалюзийный дозатор
20