
2858.Оборудование литейных цехов учебное пособие
..pdf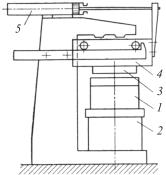
сительно траверсы по схеме рис. 3.25, б. Под действием тяги колодка при повороте траверсы будет перемещаться парал-
лельно самой себе. |
|
|
|
||||
Траверсы в виде тележек, |
|
||||||
откатывающихся |
по рельсам |
|
|||||
в нерабочее |
|
1 |
|
положение |
|
||
(рис. 3.26), нашли применение |
|
||||||
в некоторых современных кон- |
|
||||||
струкциях |
формовочных |
ма- |
|
||||
шин, в том числе автоматизи- |
|
||||||
рованных. Сила прессования, |
|
||||||
нагружающая |
траверсу |
при |
|
||||
уплотнении формы, восприни- |
|
||||||
мается выступами |
станины. |
Рис. 3.26. Схема траверсы в виде |
|||||
Передвижение |
тележки меха- |
тележки: 1 – опока; 2 – прессовый |
|||||
низируется с помощью пневмо- |
цилиндр; 3 – прессовая колодка; |
||||||
или гидроцилиндра. |
|
|
4 – траверса; 5 – пневматический |
||||
|
|
цилиндр для перемещения |
|||||
Неподвижные |
прессовые |
||||||
траверсы |
|||||||
траверсы |
также |
применяют |
|||||
|
внекоторых современных машинах. Их укрепляют на двух, трех или четырех колоннах. Прессуемая опока, наполненная формовочной смесью, подводится под траверсу на какой-либо каретке, тележке или поворотном столе. Имеются также конструкции, в которых траверса сделана в виде рамки, т.е. имеет четырехугольное отверстие по размеру опоки, через которое
вопоку из расположенного выше бункера засыпается формовочная смесь, после чего сбоку в траверсу въезжает на специальной тележке прессовая плита, являющаяся упором при прессовании опоки.
Встарых конструкциях формовочных машин применялись (и еще встречаются и работают на производстве сейчас) траверсы, откидывающиеся (вручную) назад (рис. 3.27). В новых конструкциях такие траверсы не делают из-за неудобства их ручного отвода назад, а также потому, что при их применении, особенно
51
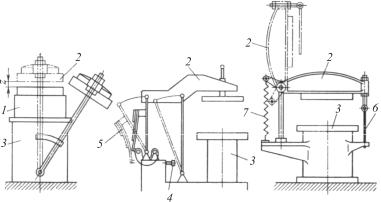
в варианте рис. 3.27, а, зазор z между прессовой колодкой и наполнительной рамкой приходится делать увеличенного размера, что ведет к перерасходу сжатого воздуха на прессование.
а |
б |
в |
Рис. 3.27. Схемы траверс, опрокидывающихся назад: а – удерживаются под силой тяжести; б – с помощью рессор; в – с помощью пружины; 1 – опока; 2 – траверса; 3 – прессовый цилиндр; 4 – упор; 5 – рессора; 6 – дополнительная тяга; 7 – пружина
Существенной особенностью в конструкции траверсы является устройство, позволяющее устанавливать по высоте плиту, к которой крепится прессовая колодка. Это необходимо при переналадке машины на другой размер высоты формуемых опок для получения минимального хода прессового поршня. Достигается такая перестановка часто тем, что плиту с колодкой ввинчивают в траверсу и закрепляют ее в нужном положении стопорным винтом. Для крепления вертикального стержня прессовой плиты в траверсе применяют также устройство типа клеммного. При этом усилие прессования передается на траверсу через разрезное кольцо, закладываемое в одну из выточек на стержне прессовой плиты (см. рис. 3.23, а).
52
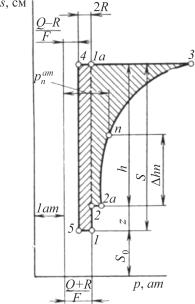
3.13. Рабочий процесс и расчет прессового механизма
Индикаторная диаграмма пневматического прессового цилиндра
Рассмотрим рабочий процесс пневматического прессового цилиндра формовочной машины по индикаторной диаграмме (рис. 3.28). Предположим, что имеется прессовая машина с верхним прессованием и с обычным расположением механизма, а именно с неподвижной во время прессования траверсой
ипрессовой колодкой и поднимающимся прессовым поршнем со столом, на котором расположены модельная плита, опока
инаполнительная рамка. Перед началом прессования между прессовой колодкой и верхней кромкой наполнительной рамки имеется зазор z, см.
Рис. 3.28. Схема индикаторной диаграммы прессового цилиндра пневматической формовочной машины
53

При построении индикаторной диаграммы ход поршня s
всм будем откладывать по ординате, а абсолютное давление
вцилиндре р в ат – по абсциссе.
Точка 1 начала хода вверх будет иметь, очевидно, следующие координаты:
1) ординату, равную приведенной высоте вредного пространства прессового цилиндра, см:
s0 = VF0 ,
где V0 – объем вредного пространства, см3; F – площадь поршня, см;
2) абсциссу, соответствующую избыточному давлению, ат: p1 = QF+ R ,
где Q – вес поднимаемых частей (поршня, стола, модельноопочнойоснастки иформовочной смеси), кгс; R – сила трения, кгс.
На участке хода 1–2, на протяжении которого выбирается зазор z между прессовой колодкой и поверхностью формовочной смеси в наполнительной рамке, давление под поршнем не изменяется.
Начиная с точки 2 и до конца хода вверх, происходит прессование формы, и давление под прессовым поршнем растет с увеличением сопротивления формы уплотнению.
Если начальная плотность смеси в опоке была δ0 = 1 г/см3, то согласно уравнению Н.П. Аксенова [2]
δ=1+ Cp0,25 |
(3.11) |
сопротивление формы уплотнению в начальный момент прессования р0 = 0. Здесь С – коэффициент уплотняемости, С = 0,4…0,6, его величина зависит от свойств смеси и размеров прессуемой формы. Линия прессования индикаторной диаграммы покажет плавное нарастание давления от точки 2.
54
Если же, как это обычно бывает на практике, начальная плотность смеси δ0 > 1 г/см3, то сопротивление формы уплотнению в начальный момент прессования не равно нулю и на основании уравнения (3.11) составляет, кгс/см2
p = δ0 −1 4 . 0 C
В этом случае в момент начала прессования на индикаторной диаграмме получится скачок давления в цилиндре в соответствии с этой величиной р0 между точками 2 и 2а диаграммы.
При построении индикаторной диаграммы промежуточные точки на участке прессования легко могут быть найдены аналитически.
Пусть требуется найти промежуточную точку n, лежащую на расстоянии hn см по оси хода, считая от начала прессования. Тогда избыточное давление в цилиндре pn ат, соответствующее этой точке, определим следующим образом.
На основании формулы для высотынаполнительной рамки[1]
|
|
h = H |
|
δn −1 |
|
|
|
|
(3.12) |
|
|
|
|
|
δ0 |
|
|
|
|
|
|
можно написать |
|
|
|
|
|
|
|
|
|
|
|
|
|
|
|
|
|
|
|
|
|
h |
= |
H + h − |
h − Vм |
|
δn |
−1 |
, |
|||
n |
|
|
|
n |
F |
|
δ |
0 |
|
|
|
|
|
|
|
о |
|
|
|
|
где H – высота смеси в опоке (после прессования), см; h – высота наполнительной рамки; см; Vм – объем модели, см3; Fо – площадь опоки, см2; δn – средняя степень уплотнения формы, соответствующаяточке n индикаторной диаграммы, г/см3. Отсюда имеем
|
|
|
|
|
|
|
|
|
|
|
|
|
|
|
|
|
hn |
|
|
|
|
δ |
n |
= δ |
0 |
|
|
|
|
|
+ 1 . |
|
|
|
|
Vм |
|
||||||
|
|
|
H + h − |
h |
− |
|
|
|||
|
|
|
|
|
||||||
|
|
|
|
|
|
n |
Fо |
|
|
|
|
|
|
|
|
|
|
|
|
|
55

Определив δn, находим на основании уравнения (3.11) величину необходимого давления прессования (кгс/см2) в точке n:
p = δn −1 4 . n C
Наконец, зная pn на прессовой колодке, находим избыточное давление (ат) в прессовом цилиндре:
pц = pn FF0 + QF+ R ,
где F – площадь прессового поршня, см2.
Давление в точке 3 диаграммы (в конце хода прессования) соответствует окончательной степени уплотнения δ или деформации смеси в опоке на всю высоту h наполнительной рамки.
Вточке 3 прессовый цилиндр переключается на выхлоп,
иизбыточное давление в нем падает до величины (Q – R)/F (точка 4). Это давление сохраняется до конца хода поршня вниз (до точки 5).
Вся площадь индикаторной диаграммы fi = Пл. 1–2–2a–
–3–4–5 см2 равна работе сжатого воздуха в кгс·см, отнесенной к 1 см2 площади поршня. Эта работа расходуется на прессование
ипреодоление трения при ходе поршня вверх и вниз. Работа
прессования выражается площадью 2–2а–3–1а, работа трения – площадью прямоугольника 1–1а–4–5 и равна 2RS кгс·см на 1 см2 площади поршня, где S = h + z – ход поршня в см.
Индикаторный расход свободного воздуха на одно прессование найдем, если из количества воздуха в объеме цилиндра в точке 3 диаграммы, пересчитанного на атмосферное давление, вычтем количество воздуха, оставшееся во вредном пространстве после выхлопа (в точке 5). Пренебрегая разностью темпера-
тур воздуха в цилиндре в точке 3 и атмосферного воздуха, а также остатком воздуха во вредном пространстве и принимая, кроме того, что давление воздуха в цилиндре в точке 3 диаграм-
56
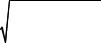
мы равно давлению воздуха в сети, получим расход свободного воздуха (м3 св. в.) на одно прессование:
V |
= FS 1+ ε |
)( |
p |
0 |
+1 10−6 |
, |
(3.13) |
инд |
( |
|
) |
|
|
где ε – величина вредного пространства цилиндра в частях объема, описываемого поршнем; ε = V0/Vц = V0/FS = S0/S; p0 – избыточное давление воздуха в сети, ат.
Расчет прессового механизма формовочной машины
Расчет прессового механизма формовочной машины в основном сводится к расчету площади прессового поршня. Из уравнения полной силы прессования (3.13), где
|
|
|
πD2 |
|
|
S = pF + Q + R = pF = p |
|
ц |
, |
(3.14) |
|
|
4 |
||||
о |
о |
0 |
|
|
|
определяется диаметр прессового поршня: |
|
|
|
D = |
4( pFо + Q + R) |
. |
|
||
ц |
πp0 |
|
|
|
Здесь p – давление прессования в конце хода прессования, кгс/см2; Fо – площадь опоки, см2; Q – вес поднимаемых при прессовании частей машины, включая и полезную нагрузку, кгс; R – сила трения, кгс; р0 – расчетное максимальное избыточное давление воздуха в прессовом цилиндре, равное (в конце хода прессования) давлению воздуха в сети, кгс/см2.
Усилие Q + R на преодоление веса поднимаемых частей и трения обычно составляет не более 0,1–0,15 от силы прессования pFо. Вес поднимаемых частей с нагрузкой в машинах с верхним прессованием и расположением прессового механизма внизу составляет обычно, по эмпирическим данным, Q = = (0,13…0,22)Fо. Отношение Fо/F для тех же машин чаще всего
находится в |
пределах 1,8–2,2. Избыточное давление воздуха |
в сети может |
колебаться в широких пределах, практически |
|
57 |
от 4,5 до 7 ат. Поэтому при расчетах частей машин на прочность надо принимать большее значение р0 (7 ат), а при расчете площади поршня – меньшее значение p0 (4,5 ат) или близкое к нему, во всяком случае не более 5,0 ат. Силу трения при расчетах принимают R < 0,25Q. В случае применения саморазжимающихся поршневых колец из специальной маслостойкой резины силу трения колец можно определить расчетным путем.
В практических расчетах при определении расхода воздуха на одно прессование необходимо также учитывать и протечку его через уплотнительные соединения поршневого механизма.
Площадь сечения впускного отверстия можно определить из уравнения сплошности потока воздуха
fвпvв = Fvп,
откуда
fвп = Fvп ,
vв
где vв – скорость воздуха в сети, м/с; средняя скорость подъема поршня при прессовании vп = 0,015…0,02 м/с.
3.14. Автоматический клапан давления
Степень уплотнения смеси при прессовании является функцией лишь давления прессования, которое в пневматических прессующих механизмах зависит только от давления воздуха в прессовом цилиндре. Поэтому решение задачи автоматической стабилизации плотности набивки форм в этих машинах сводится в основном к переключению на выхлоп прессового цилиндра по достижении в нем заданного давления воздуха. Для этой цели обычно на подводящем воздух трубопроводе устанавливают автоматический клапан давления.
В качестве примера на рис. 3.29 изображена схема такого клапана. При установке прессовой траверсы в рабочее положение ролик 4 нажимает на рычаг 5, и клапан 7 опускается, закры-
58
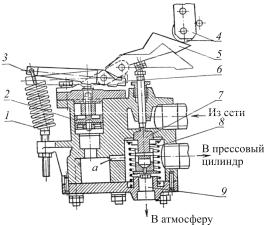
вая выхлопное отверстие 9. Воздух попадает в прессовый цилиндр, и начинается прессование смеси. Одновременно воздух проходит по каналу а и давит на поршень 2, который через рычаг 3 нагружен пружиной 1. Пружина может растягиваться только после достижения заданного давления под поршнем 2.
Регулировкой натяжения пружины устанавливается желаемая степень уплотнения формы. При достижении заданного давления воздуха поршень 2 поднимается, поворачивая рычаг 3, выступ 6 которого соскакивает с выступа рычага 5. При этом клапан 7 под действием пружины 8 закрывает доступ сжатому воздуху и открывает отверстие 9 для сообщения прессового цилиндра с атмосферой.
Рис. 3.29. Автоматический клапан давления
В машинах с нижним прессованием установка клапана давления не имеет смысла, так как ход поршня в этом случае должен быть всегда одним и тем же (до упора) независимо от давления воздуха в прессовом цилиндре.
Для интенсификации процесса уплотнения прессовые машины могут снабжаться специальными вибраторами, тогда они называются вибропрессовыми.
59
Положительное влияние вибрации на процесс уплотнения заключается главным образом в значительном уменьшении внешнего и внутреннего трения формовочной смеси, что способствует лучшему протеканию пластических деформаций и облегчает перемещение смеси между опокой и моделью.
При действии вибрации на формовочную смесь происходит непрерывное изменение взаимного расположения частиц, создаются новые комбинации их в системе, благоприятные для уплотнения формы.
Продольные волны вибрации, распространяясь в смеси, проходят через различные по плотности и упругости фазы (твердые зерна песка, воздушные промежутки, жидкие пленки связующего вещества). Чем менее однородна смесь, тем быстрее гасятся в ней колебания и тем продолжительнее должен быть процесс вибропрессования. По достижении определенной плотности и структуры смеси вибрирование формы не вызывает увеличения уплотнения.
Эффект вибрации обеспечивается подбором рациональных конструктивных факторов, к которым относятся величина возмущающих сил, создаваемых вибраторами, жесткость крепления оснастки и др.
Направление вибрации влияет как на плотность набивки формы, так и на условия вытяжки модельного комплекта. Если колебания, создаваемые вибратором, по направлению совпадают с движением прессующего модельного комплекта, то плотность набивки формы резко увеличивается, при этом условия вытяжки модели из формы остаются почти неизменными. Если направление вибрации перпендикулярно к направлению прессования, улучшается процесс вытяжки модели.
Для улучшения условий вытяжки модельного комплекта из формы, увеличения степени и равномерности уплотнения ее рекомендуется устанавливать вибраторы внутри моделей или на наружной стороне модельной плиты под некоторым углом к плоскости стола машины.
60