
2858.Оборудование литейных цехов учебное пособие
..pdf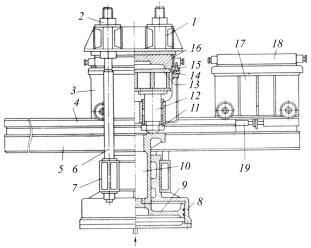
3.15. Конструкции прессовых формовочных машин
Прессовая формовочная машина мод. ПФ-5. На рис. 3.30
представлена схема пневматической поршневой прессовой формовочной машины ПФ-5 челночного типа с нижним прессованием.
Рис. 3.30. Пневматическая прессовая формовочная машина мод. ПФ-5
Машина предназначена для изготовления полуформ сравнительно малой высоты. Верхние 1 и нижние 7 траверсы соединены колонками 6 и гайками 2 в замкнутую жесткую раму. Нижние траверсы установлены на фундаменте. Прессовый цилиндр 8 жестко соединен с нижними траверсами и горизонтальными направляющими балками 5, на которых смонтирована пара направляющих рельсовых путей 4 для перемещения столов 3 и 17. Поршень 9 скреплен с промежуточным столом 10, на который опираются два пустотелых стакана 12 подвижных столов. Перемещение столов 3 и 17 осуществляется пневмоцилиндрами 19. Опока 16 и наполнительная рамка 14 фиксируются направляющими штырями 15.
61
При подаче сжатого воздуха под прессовый поршень 9 промежуточный стол 10 совместно со стаканами 12, модельной плитой 13 и моделью движутся вверх. Происходит перемещение формовочной смеси из наполнительной рамки 14 в опоку 16, т.е. прессование.
По окончании прессования подвижный стол 3 с полуформой уходит вниз, и стол садится на рельсы 4. Подвижный стол продолжает опускаться, извлекая при этом модель из готовой полуформы.
После протяжки модели стол 3 уходит влево, готовая полуформа снимается, за это время стол 17 с опокой 16 и смесью устанавливается на позицию прессования и протяжки модели. Далее цикл повторяется. В то время, когда формовщик снимает готовую полуформу 18 с правого стола, обдувает модель, устанавливает на него опоку и засыпает смесь, на левом столе прессуется вторая полуформа. Плотность формы регулируют путем изменения высоты слоя смеси. Для этих целей служат специальные упорные болты (на схеме не показаны), ограничивающие положение модельной плиты 13 по отношению к наполнительной рамке.
В зависимости от высоты опок верхняя траверса 1 может перемещаться вверх или вниз с помощью гаек 2. Ход прессовой плиты регулируется гайками 11. Величину хода прессования устанавливают с таким расчетом, чтобы плоскость модельной плиты при прессовании не доходила до плоскости лада опоки на 0,2–0,3 мм во избежание образования заливов по разъему спаренных опок.
Вибропрессовая машина с поршневым прессующим меха-
низмом мод. 226. Большинство прессовых формовочных машин, работающих с низким удельным давлением прессования 0,2– 0,4 МПа (2–4 кгс/см2), используется в мелкосерийном производстве. Они снабжаются вибраторами и представляют литой прессовый цилиндр (рис. 3.31), в котором перемещается прессовый поршень 2, несущий на себе стол 4 машины.
62
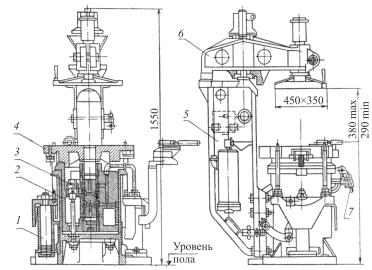
Рис. 3.31. Вибропрессовая формовочная машина мод. 226
Прессовый механизм крепится к станине-колонке 5, на которой установлена прессовая траверса 6. Штифтоподъемный механизм 1 выполнен в блоке с прессовым цилиндром. Пуск воздуха в прессовый цилиндр во многих машинах производится автоматически при установке траверсы и подготовленного комплекта (модель, опока, смесь) в рабочее положение. С этой целью некоторые машины снабжаются автоматическим клапаном давления, который выключает машину по достижении заданного давления прессования.
В вибропрессовых машинах цилиндр вибратора обычно составляет одно целое с прессовым поршнем и размещается в средней его части. В цилиндр запрессована чугунная втулка, которая служит направляющей для плунжера вибратора 3 и обеспечивает воздухораспределение при его работе.
Вибратор включается в работу при нажатии коленного клапана 7. При этом воздух из магистрали (рис. 3.32) проходит по каналам прессового поршня и поднимает плунжер 5. Когда
63
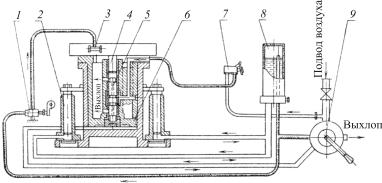
нижние отверстия каналов гильзы и плунжера совпадут, воздух подбросит плунжер вверх и ударит им по хвостовику стола 4. Затем плунжер падает вниз, и процесс повторяется. Движение плунжера происходит до тех пор, пока нажат коленный клапан 7.
Рис. 3.32. Пневматическая схема машины мод. 226
При повороте рукоятки воздухораспределителя 9 в положение прессования воздух проходит под прессовый поршень 6, поднимает его и прижимает опоку к прессовой плите. При обратном повороте рукоятки воздух выйдет из цилиндра и поршень со столом и опокой опустится. Затем рукоятка воздухораспределителя устанавливается на вытяжку, воздух попадает в резервуар с маслом 8 и выдавливает его под поршни вытяжных цилиндров 2. Поперечины штоков посредством рычагов связаны с уравнительным валом, поэтому штифты поднимаются равномерно без перекоса. Винт уравнительного вала нажимает на шпиндель проходного клапана 1, и воздух приводит в действие специальный вибратор для расталкивания модели при ее вытяжке 3.
При отключении подачи воздуха в масляный резервуар масло перетекает в бак, и поршни вытяжного механизма опускаются.
64
Технические характеристики машины: |
|
Размеры опок, мм................................................. |
500×400×150 |
Производительность, полуформ/ч...................................... |
100 |
Максимальный ход прессования, мм ................................. |
170 |
Усилие прессования, кН................................................... |
62,50 |
Удельное давление прессования, Па............................ |
3,2·105 |
Расход свободного воздуха на 1 цикл, м3 ........................... |
0,4 |
Вопросы для повторения
1.Назовите способы уплотнения прессованием.
2.Охарактеризуйте преимущества и недостатки процесса прессования песчано-глинистых форм.
3.Какие факторы влияют на характер распределения плотности смеси по высоте опоки при прессовании? Постройте эпюру распределения плотности.
4.Что такое верхнее и нижнее прессование?
5.Условие определения высоты наполнительной рамки.
6.Какой основной недостаток многоплунжерного прессо-
вания?
7.Давление прессования. Какие силовые приводы применяют при прессовании?
8.Конструкции траверс в прессовых формовочных маши-
нах.
4.ВСТРЯХИВАЮЩИЕ ФОРМОВОЧНЫЕ ЛИТЕЙНЫЕ МАШИНЫ
4.1. Особенности уплотнения форм встряхиванием
При уплотнении смеси на встряхивающей формовочной машине (рис. 4.1.) стол 2 с поршнем, вместе с модельно-опочной оснасткой 3, 4, 5 и смесью 6 под действием сжатого воздуха, поступающего через впускное окно А, поднимается на некоторую высоту (h = 50…80 мм). Находящийся в подпоршневом
65
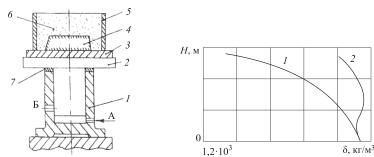
пространстве воздух через выхлопное окно Б уходит в атмосферу, давление под поршнем резко снижается, стол под действием силы тяжести падает и ударяется о станину 1, и смесь под действием сил инерции уплотняется. Для смягчения удара на станине размещают упругие прокладки 7 из плотной резины, дерева и других материалов.
Рис. 4.1. Схема встряхивающего |
Рис. 4.2. Распределение степени |
механизма |
уплотнения смеси по высоте |
|
формы |
Продолжительность действия уплотняющих сил очень незначительна, и необходимое уплотнение может быть достигнуто только после 20–60 ударов. С увеличением числа ударов приращение степени уплотнения уменьшается, так как при этом происходит накопление «пластических и упругих деформаций в смеси, перемещение ее из одних участков формы в другие, обтекание модели и выравнивание структуры смеси.
После некоторого числа ударов приращение уплотнения прекращается – наступает так называемая стабилизация уплотнения. Следовательно, для каждого случая можно найти и задать такой режим работы (т.е. оптимальное число ударов при данной высоте встряхивания), при котором качество уплотнения будет высоким, а расход энергии минимальным.
Степень уплотнения смеси при встряхивании по высоте опоки распределяется неравномерно (рис. 4.2, кривая 1). Наи-
66
большее уплотнение – в нижней части, у модельной плиты, так как при ударе на этот слой действует сила инерции всей массы смеси, находящейся в опоке.
По мере удаления от модельной плиты вверх плотность смеси уменьшается. Верхний слой ее почти совсем не уплотняется, так как масса его незначительна. Поэтому после уплотнения встряхиванием верхний слой формы обычно доуплотняют одним из следующих способов: трамбованием при помощи ручных или пневматических трамбовок; помещением в опоку некоторого избытка формовочной смеси (в объеме наполнительной рамки) для компенсации уменьшения объема смеси при ее уплотнении, а также для создания дополнительного давления; нагружением формы (т.е. встряхиванием с добавочным грузом); подпрессовкой.
При подпрессовке давление прессовой колодки передается по всей высоте формы, уменьшаясь с глубиной (см. рис. 4.2, кривая 2).
Процесс уплотнения встряхиванием – наиболее распространенный широкоуниверсальный, достаточно простой и надежный способ формовки, в наибольшей степени приближающийся к технологическим требованиям по распределению плотности по высоте формы. Этот процесс не отличается высокими требованиями к смеси и оснастке. Однако он, наряду с указанными преимуществами, обладает рядом существенных недостатков:
–длительность процесса, особенно с учетом дополнительного уплотнения верхних слоев смеси;
–многостадийность операции уплотнения;
–высокие энергозатраты;
–динамичность действия, требующая сооружения громоздких фундаментов;
–тяжелые условия труда (шум, сотрясения и пр.);
–трудность создания надежно действующих устройств для автоматической стабилизации плотности набивки форм;
67

– трудность автоматизации всего комплекса операций процесса изготовления форм.
Вместе с тем, чтобы избежать многих из перечисленных недостатков, применяют встряхивающие механизмы в комбинации с прессующими. Встряхивание и одновременное прессование позволяют несколько сократить длительность цикла уплотнения, уменьшить количество стадий в процессе и облегчить его автоматизацию. Помимо этого, во встряхивающе-прессовых механизмах удары большей частью гасятся внутри машины, поэтому фундаменты для них могут быть менее громоздкими.
В последние десятилетия процесс встряхивания вытесняется более современными способами уплотнения: импульсным, пескодувно-прессовым и др.
За меру уплотняющего воздействия при встряхивании принимают удельную работу а (Дж/м2), сообщенную смеси за n ударов стола
a = G hnη, Fо
где G – сила тяжести формовочной смеси, Н; Fо — площадь опоки, м2; h – высота подъема встряхивающего стола (высота падения), м; n – коэффициент, учитывающий потери живой силы падающих частей машины вследствие трения и противодавления воздуха; η = 0,3–0,7,
или же работу, отнесенную к 1 Н силы тяжести смеси в опоке G1
(Дж/Н)
aо = G hnη. G1
Обе формулы не учитывают энергию, которую получает форма в момент упругого удара падающего стола о неподвижные части машины. Эта энергия также уплотняет форму, составляя 10–15 % общей энергии удара.
68
Для определения зависимости средней степени уплотнения формовочной смеси (кг/м3) от удельной работы встряхивания проф. Н.П. Аксеновымбыло предложено эмпирическоеуравнение
δср = (1+ Ka0,3 )103 ,
где K – коэффициент уплотняемости формы встряхиванием, K = = 0,35…0,55; a – удельная работа встряхивания, кгс·дм/см2.
Уравнение встряхивания имеет пределы применения [18] и позволяет получить зависимость, близкую к действительной только при определенных значениях a (наиболее часто встречающихся на практике). Как и эмпирическое уравнение прессования, уравнение встряхивания отклоняется от опытных данных при весьма больших значениях a, приближающихся к моменту стабилизации уплотнения. Кроме того, отклонения могут наблюдаться и в области весьма малых значений a, если в действительных условиях δo ≠ 1. Указанные отклонения, однако, практического значения не имеют.
Изменение высоты встряхивания h в пределах 20–100 мм не влияет на получаемую степень уплотнения δ при условии постоянства удельной работы a. Однако при увеличении h одна и та же работа a сообщается смеси при меньшем числе n ударов встряхивания однойформы, и производительность машинывозрастает.
Слишком большое число ударов встряхивания n на одну форму может привести к частичному разрыхлению формы и даже к возникновению трещин в форме.
4.2. Классификация встряхивающих механизмов
Классифицировать встряхивающие механизмы можно по роду привода, по степени амортизации ударов, по характеру рабочего процесса, по типу воздухораспределения.
Встряхивающий механизм в современных формовочных машинах чаще всего выполняется пневматическим, с давлением воздуха p0 = 6·105 Па (6 кгс/см2).
69
Принципиально возможно создание механизмов, у которых подъем рабочего стола с модельно-опочной оснасткой осуществлялся бы при помощи вращающихся кулачков определенного профиля.
Возможно создание встряхивающих механизмов на базе мощных электромагнитов, обеспечивающих подъем стола и оснастки с заданной частотой.
При создании новых машин выбор того или иного типа привода обусловлен большей частью совокупностью факторов, обеспечивающих удобную эксплуатацию всего комплекса оборудования формовочного передела.
Различают механизмы без амортизации ударов, со смягчением ударов и с полной амортизацией ударов.
Под амортизацией понимается поглощение живой силы ударов падающих масс внутри самого встряхивающего механизма.
Пневматический встряхивающий механизм без амортизации ударов приведен на рис. 4.3. При впуске воздуха во встряхивающий цилиндр (рис. 4.3, а) происходит наполнение цилиндра и подъем поршня со столом. После того как поршень пройдет путь Se, он открывает выхлопное отверстие. Несмотря на продолжающееся поступление свежего воздуха в цилиндр, давление в нем резко падает, так как воздух из него уходит в атмосферу через выхлопное отверстие (одно или несколько), которое делается большего сечения, нежели впускное. Пройдя еще некоторый путь по инерции, поршень останавливается в верхнем положении (рис. 4.3, б) и затем падает. Происходит удар встряхивающего стола о фланец цилиндра. Удар этот целиком передается на фундамент машины.
При больших размерах машины эти удары вызывают весьма заметное сотрясение грунта. Поэтому встряхивающие механизмы без амортизации и смягчения ударов следует применять только в небольших и средних машинах.
70