
630
.pdfГПКС и 4ПП-5 предназначены для проходки горизонтальных и наклонных (до ± 10°) выработок площадью от 4 до 35 м2 в грунтах с коэффициентом крепости f = 7 абразивностью до 15 мг. Производительность комбайнов 4ПП-2м обеспечивает разработку 1 м выработки сечением 12–15 м2 за 1–1,5 ч, а площадью 20 м2 – за 2,0–2,5 ч. Но для обеспечения такой производительности необходимо, чтобы в сочетании с комбайном работал конвейер типа 1ЛТП-80. Отечественные горнопроходческие комбайны избирательного действия КМШ, КП-20, КП-25, П-60 (табл. 6.1) разрабатывают грунты с коэффициентом крепости до f = 15 в выработках сечением до 40 м2 без дополнительных перемещений в забое (в зависимости от длины стрелы).
Таблица 6.1
Технические характеристики проходческих комбайнов избирательного действия
|
Показатель |
Проходческие комбайны |
|||
|
|
|
|
|
|
|
|
KМШ |
KП-20 |
KП-25 |
П-160 |
|
|
|
|
|
|
1. Диапазон сечений выработки, обрабаты- |
5-12 |
7-20 |
7-25 |
9-33 |
|
ваемый с одного положения комбайна, м2 |
|
|
|
|
|
2. |
Размах стрелы, мм |
|
|
|
|
|
ширина |
5400 |
5400 |
6200 |
6500 |
|
высота |
4300 |
4300 |
4700 |
5600 |
3. |
Предельная прочность разрушаемых |
60 |
80 |
90 |
100 |
грунтов при одноосном сжатии, МПа |
|
|
|
|
|
4. Абразивность разрушаемых грунтов, |
12 |
15 |
15 |
18 |
|
МПа |
|
|
|
|
|
5. |
Техническая производительность по грун- |
0,27 |
0,24 |
0,26 |
0,29 |
там предельной прочности, м3/мин |
|
|
|
|
|
6. |
Суммарная нормальная мощность |
|
|
|
|
электродвигателей, кВт |
76,5 |
134 |
157 |
280 |
|
|
в том числе исполнительного органа |
45 |
75 |
110 |
160 |
7. Размер комбайна в транспортном поло- |
|
|
|
|
|
жении, мм |
|
|
|
|
|
|
ширина |
1200 |
2000 |
2100 |
2700 |
|
высота |
1300 |
1500 |
1600 |
1600 |
8. |
Масса, т, не более |
7,5 |
25 |
37 |
55 |
|
|
|
|
|
|
9. |
Установленный ресурс до капремонта, м3 |
— |
8400 |
11300 |
11300 |
В процессе разработки грунт падает на приемную плиту, оснащенную нагребающими рычагами, и далее по скребковому конвейеру поступает в транспортное средство. Телескопическая конструкция стрелы позволяет выдвигать фрезу до 1,2 м и производить выемку грунта на 0,95 м ниже уровня опорной площадки. Фреза оснащена фиксаторами резцов и приводится
141
электродвигателем с водяным охлаждением с помощью эпициклического редуктора. В современных конструкциях фрез предусмотрено регулирование угла атаки резцов. Для подъема машины в целях технического обслуживания спереди и сзади нее имеются по два гидравлических аутригера
Силовой модуль гидравлического привода включает бак, три поршневых насоса, стабилизирующих давление, два шестеренчатых нагнетательных насоса, электродвигатель с водяным охлаждением, фильтры, маслоохладители и наливной насос. В системе используется минеральное масло или огнестойкие жидкости. Для защиты системы имеются датчики сигнализации уровня и температуры жидкости. Главные клапаны, сгруппированные в клапанном модуле, приводятся в действие с портативного пульта дистанционного управления, который может быть подключен к главному пульту управления на месте водителя или во вспомогательные разъемы по бокам машины.
Двигатель режущей фрезы, ходовой двигатель и двигатели гидравлической системы имеют водяное охлаждение. Система охлаждения состоит из резервуара, лопастного насоса и четырех радиаторов. Вентилятор охлаждения и насос имеют электрические приводы, в качестве хладагента используются вода и антифриз 50/50. Средняя производительность разработки грунта комбайнами типа «Паурат» Т3.20 (Е-242), «Фест-Альпине АТМ-
105» в зависимости от крепости грунтов составляет от 34 до
140 м3/ч.
Комбайны такого типа имеют высоту резания около 6,6 м и ширину 9,1 м (рис. 6.1). Высота резания может быть увеличена за счет опускания погрузочного стола или подсыпки на подошву отработанной горной массы.
Комбайны избирательного действия могут быть укомплектованы боковой режущей фрезой, грузоподъемным механизмом для монтажа арок, гидравлическим анкерным агрегатом, дополнительным дизельно-гидравлическим силовым модулем передвижения и др.
Проходку тоннелей с использованием комбайна с исполнительным органом избирательного действия можно отнести к гибким технологиям. Комбайн позволяет открыть дополнительный фронт работ из вспомогательной выработки, вести проходку в меняющихся инженерно-геологических условиях, разрабатывать выработку любой конфигурации. Энергопотребление современных высокопроизводительных комбайнов не превышает 1000 кВт/ч. Комбайновая проходка позволяет применять
142
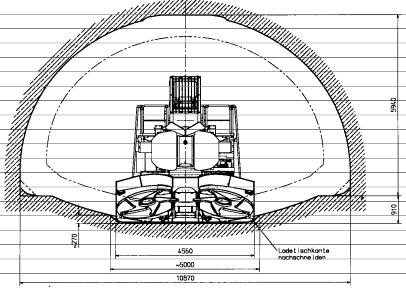
Рис. 6.1. Размеры сечения, разрабатываемого комбайном «Фест-Альпине АТМ-105»
различные типы крепи (металлическая арочная, монолитная бетонная и железобетонная, набрызгбетонная в сочетании с анкерами, сборная из чугунных и железобетонных элементов) и обеспечивает полную механизацию горнопроходческих работ. К недостаткам проходки тоннелей с использованием комбайнов со стреловым исполнительным органом можно отнести возможность вывалообразования в слабоустойчивых грунтах, повышенное пылеобразование в забое, многостадийность возведения крепи.
6.2.2. Безвзрывные способы разработки грунтов
Если для грунтов с коэффициентом крепости f < 15 найдены альтернативные буровзрывному способы разработки, то для крепких скальных грунтов таких технологий пока нет. Казавшаяся перспективной разработка скалы лучом лазера не достигла уровня практического использования. Лазерное оборудование расходует при резке бетона на глубину 30 см около 25 кВт-мин на 1 см реза, поэтому его целесообразно использовать в особых случаях при малом объеме работ. Нет пока технологических решений предлагавшейся артиллерийской проходки. Более успешные направления (шпуровое, бесшпуровое и комбинированное) требуют нестандартных подходов при их воплощении.
143
Шпуровое разрушение грунтов. В настоящее время распростра-
нен шпуровой метод разрушения негабаритов и монолита с помощью гидроклиньев статического действия (легких переносных и тяжелых навесных). В Японии выпускают гидроклинья с рабочей частью из специальных резин, в Канаде разработана технология, при которой гидроклин производит рабочий ход в направлении от дна шпура к поверхности, что повышает эффективность выломки грунта. Так, гидроклин мощностью 1,5 кВт одним рабочим ходом в шпуре диаметром 75 мм способен выламывать до 2 м3 грунта.
Известны еще два варианта шпуровой технологии: применение расширяющихся химических составов на основе гидратирующих соединений, которые создают разрывающее усилие в шпуре по мере протекания химической реакции, и машин импульсного действия, вбрызгивающих в шпур воду с высокой кинетической энергией.
Безвзрывной способ разрушения грунтов и конструкций с помощью невзрывчатых разрушающих веществ основан на ис-
пользовании модифицированной негашеной извести. Невзрывчатые разрушающие материалы, содержащие оксид кальция (65–95 % по массе), получают путем совместного помола продукта обжига карбоната кальция и модифицирующих добавок. При смешивании невзрывчатых разрушающих составов с водой образуется суспензия, которая за счет гидратации порошка твердеет и увеличивается в объеме с развитием в частично или полностью замкнутой полости давления 80–120 МПа, что приводит к образованию и развитию трещин, а через 12–20 ч – к разрушению объекта. Интенсивность трещинообразования зависит от температуры среды, прочностных характеристик материала объекта, степени армирования, расстояний до обнаженных поверхностей. Повышение температуры среды способствует ускорению трещинообразования. Величина давления зависит от содержания в порошке СаО. Способ безвзрывного разрушения не требует электрической и пневматической энергии, не вызывает шума, сейсмических колебаний, выбросов твердых или газообразных продуктов. Невзрывчатые разрушающие материалы можно использовать во взрывоопасных и пожароопасных зонах, стесненных условиях (вблизи зданий и сооружений, транспортных магистралей, коммуникаций, населенных пунктов), где невозможно применить взрывчатые вещества. Областями применения являются: разрушение скальных грунтов, включая ликвидацию негабаритов; рыхление фундаментов; разруше-
144
ние монолитных бетонных и железобетонных конструкций, в том числе под водой.
Невзрывчатое разрушающее вещество НРВ-80 (ТУ У БВ 2.7.00030937) представляет собой порошок серовато-белого цвета, пылящий, негорючий, взрывобезопасный, обладающий щелочными свойствами (рН = 12,5). Порошок поставляется в мешках массой по 45 кг, жидкий пластификатор – в пластиковых бутылках. Расход сухого вещества на 1 м шпура D = 40 мм составляет 1,5 кг. Расход рабочей смеси невзрывчатого расширяющегося материала на 1 м шпура D = 32 мм составляет 1,5 кг, D = 40 мм – 2,0 кг. Удельный расход невзрывчатого материала для разрушения скальных грунтов и бетонных конструкций составляет 8,0...…16,7 кг/м3 разрушаемого объекта. При разрушении железобетонных конструкций расход увеличивается на 30 %.
Технологический процесс состоит из подготовки объекта к разрушению (удаление оборудования, очистка его от грязи и мусора, обкопка и разметка участков разрушения и т. д.), бурения шпуров в соответствии со схемой, приготовления рабочей суспензии и быстротвердеющей забойки (в случае необходимости), заполнения шпуров рабочим составом и забоечным материалом, распыления жидкости на поверхности объекта для повышения интенсивности трещинообразования, разборки объекта (оголение и резка арматуры, удаление частей разрушенного объекта из зоны разрушения).
При подготовке к разрушению строительных конструкций должны выполняться: обследование объекта, разработка технологической карты (регламента работ), подготовка и проверка оборудования, инструктаж персонала и пр.
Приготовление рабочей смеси осуществляют следующим образом. В емкость вливают, например, 2 л воды и 150...…200 мл пластификатора. Затем постепенно высыпают 6 кг порошка, интенсивно размешивая смесь до получения однородной массы хорошей текучести. Время перемешивания не более 5...…8 мин. Количество воды в рабочей смеси НРВ-80 не должно превышать 30...…35 %, ее температура в летний период должна составлять 10– 20 °С, в зимний период – 20–50 °С. Увеличение содержания воды способствует замедлению процесса образования трещин, но уменьшает вероятность выброса материала из шпура. Для исключения выброса рекомендуется применять шпуры диаметром не более 40 мм. Число шпуров определяется их диаметром и требуемыми габаритами блоков (в зависимости от ручной или механизированной разборки). Рациональной является глубина
145
шпуров, составляющая 90…...95 % от толщины разрушаемого объекта. Шпуры располагают в одну линию параллельно открытой поверхности. Расстояние между шпурами должно составлять 200…...250 мм, расстояние от шпуров до открытой поверхности – не более расстояния между шпурами. Уменьшение расстояния между шпурами ускоряет процесс разрушения объекта, но вызывает повышенный расход порошка. Если за один прием требуемые параметры разрушения объекта не достигаются, необходимо произвести второй цикл, соблюдая схему расположения шпуров. Если объект характеризуется повышенным водопоглощением, шпуры перед заполнением рабочей смесью необходимо заполнить водой или водным раствором поверхностно-ак- тивного вещества (ПАВ), например 0,1%-ным водным раствором смачивателя ДБ на 30 мин, затем удалить жидкость сжатым воздухом или другим способом, после чего шпуры заполнить рабочей смесью. ПАВ предпочтительнее воды, так как ПАВ обеспечивает снижение необходимой энергии разрушения. Шпуры заливают рабочей смесью до устья. После заливки смеси необходимо защитить устья шпуров от атмосферной влаги и прямого нагрева солнечными лучами. При появлении трещин рекомендуется полить объект водой или водным раствором ПАВ, что способствует увеличению раскрытия трещин. При работе с невзрывчатым расширяющимся составом необходимо соблюдать меры безопасности: использовать защитные очки, респиратор и рукавицы, так как невзрывчатое вещество НРВ-80
— щелочная среда и вызывает ожоги при попадании на кожу; нельзя заглядывать в шпуры, залитые рабочей смесью, так как возможен самопроизвольный выброс смеси, особенно в жаркое время года; при попадании вещества на кожу или в глаза необходимо обильно промыть это место водой. Хранить порошок НРВ необходимо в сухом помещении на деревянных поддонах при температуре не выше 20 °С. Применение невзрывных разрушающих составов при проходческих работах сдерживается из-за их относительно медленного действия (несколько часов даже при использовании специальных ускорителей).
В последние годы за рубежом разработан ряд способов созда-
ния в шпуре импульса радиального давления. В США серийно выпускается устройство «Кор Крекер» в виде сменного навесного рабочего оборудования гидравлического экскаватора, предназначенного для шпурового разрушения грунтов прочностью на сжатие до 7000 МПа (известняки, граниты). На дно шпура опускают таблетку алюминиевого сплава. Навесное устройство,
146
представляющее собой высокопрочный стальной ударник, погружается в шпур до контакта с таблеткой. При их соприкосновении по стержню наносится удар энергией 140 кДж, под действием которого сплав приобретает свойства вязкопластичной жидкости, передающей ударный импульс в радиальном направлении на стенки шпура. Устройство «Кор Крекер» создает значительные шум и вибрацию, зато удельная себестоимость дробления грунта составляет всего 15 % по сравнению с навесным гидроударником.
Японская фирма «Тайсэй кэнсэцу» выпускает патроны «Гансайзер» физико-химического действия, развивающие в шпуре импульс давления 150–300 МПа, достаточный для мелкого дробления грунтов с прочностью на растяжение 2...…18 МПа. Патрон содержит нагреватель и водонаполненный рабочий компонент. Первый представляет собой смесь порошков оксида алюминия с инициатором окислительно-восстановительной реакции, второй – так называемую кристаллическую воду (особый вид квасцов). После разогрева компонента в химическом нагревателе развивается быстротечная реакция с выделением теплоты, под действием которой вода из квасцов высвобождается и испаряется, а пар создает давление в шпуре. Из 1 кг состава образуется около 330 л пара, а так как скорость реакции «Гансайзера» отстает от скорости детонации взрывчатых веществ и порождает волну дозвуковой скорости (около 330 м/с), вибрация от его действия составляет лишь около 30 % уровня вибрации при взрывных работах, уровень шума не превышает 20 дБ. Выпускаемые патроны массой 60, 120 и 200 г рекомендуется использовать с забойкой глубиной не менее 60 см.
Новинкой является разработка канадской компании «Норанда» плазменного бластера. Принцип действия бластера основан на том, что заряд электроэнергии порядка 3,5 ГВт, сконцентрированный в конденсаторе, разряжается в электролит, заключенный в шпуре. Под действием разряда электролит превращается в плазму с давлением около 2 ГПа, обеспечивающим разрывное усилие в шпуре глубиной до 50 см. В качестве электролита используют глинистый раствор или обычную воду. При этом не выделяется токсичных газов, практически исключаются разлет осколков грунта, сотрясение окружающего массива, задымление, загрязнение подземных вод. По энергоемкости плазменный бластер, пока существующий в виде навесного оборудования для дробления негабаритов, оказался конкурентоспособным: его средние показатели, по данным промышленных испы-
147
таний, составили от 0,19 до 0,48 кВт•ч на 1 м3 отбитой горной массы. За один плазменный взрыв расходуется энергия, как за пять минут работы бытового электроутюга, а стоимость электроэнергии дробления негабарита массой 6 т составляет менее 1 цента.
Бесшпуровое разрушение грунтов. Среди нетрадиционных ме-
тодов бесшпурового разрушения крепких скальных грунтов наиболее высокого уровня технической и технологической проработки в настоящее время достиг способ резания грунта высоконапорной водяной струей, давление которой в экспериментах достигало 200 МПа и выше. Однако до сих пор этот способ не находит массового практического применения из-за высокой энергоемкости. Немецкие специалисты подсчитали, что при использовании оснащения фрезы стрелового комбайна гидронасадками, работающими при давлении 145 МПа, удельные затраты энергии на 1 м3 разрушаемого грунта на приводе фрезы снижаются со 130 до 85 кВт•ч, но с учетом энергозатрат на подачу воды они фактически увеличиваются до 310 кВт•ч. В Японии разработан метод повышения эффективности высоконапорной водяной струи введением в нее примеси абразива (как правило, гранатовой крошки), но и это само по себе вызывает удорожание работ.
Проведенные в последние годы исследования микроструктуры высоконапорной струи позволили обнаружить некоторые ее свойства, дающие возможность существенно повысить эффективность резания крепких материалов при существенной экономии энергозатрат. Оказалось, что каждая микрокапля при соударении с поверхностью грунта воздействует на нее ударным импульсом, значительно превышающим собственное давление струи. Например, капля, отделившаяся от стационарной струи с давлением 70 МПа, может дать пиковое мгновенное давление порядка 560 МПа. Это позволяет надеяться, что в случае дробления струи на отдельные капли в квазинепрерывном режиме можно будет резать более крепкий грунт, чем обычной струей, практически без увеличения энергозатрат. Для этого достаточно, чтобы пиковые значения нагрузок от распыленной струи превышали прочность грунта на сжатие в 1,45–3,95 раза.
В настоящее время предложены принципиальные схемы устройств, которые предположительно могут обеспечить дробление струи. В частности, поршневой регулятор давления, встраиваемый в боковой отвод камеры перед гидронасадкой; роторный рассекатель струи, встраиваемый в сопло; резонансная
148
камера, встраиваемая в сопло и создающая при прохождении струи периодические вихревые процессы, период которых совпадает с собственным периодом колебаний конструкции камеры (резонансная вибрация камеры способствует формированию капель); пластинчатый электровиброизлучатель — электромагнитное устройство вибрирования струи в сверхзвуковом диапазоне посредством выпущенного в камеру штока-сердечника; механизм сообщения струе периодических высоковольтных электрических разрядов с емкого конденсатора (при диапазоне напряжений от 1 до 100 кВт и периодичности 5–400 мкс), действием которых в струе формируются плазменные промежутки. Последние не только дробят струю на микрокапли, но и способствуют повышению их кинетической энергии своим высоким давлением. Перечисленные устройства предложены учеными разных стран и находятся на различных стадиях конструктивной проработки.
Комбинированные методы разрушения грунтов. Возможности использования различных нетрадиционных технологий в качестве вспомогательных в целях расширения области применения твердосплавного породоразрушающего инструмента в грунтах прочностью на сжатие 175 МПа и более, где возможности вольфрамовых сплавов исчерпываются, исследовались во многих направлениях, включая высоконапорные водяные струи, лазеры, газоструйные устройства и др., но конкурентоспособности эти разработки не достигли. Вместе с тем, исследования позволили установить, что нагревание грунта свыше 480–500 °С обеспечивает резкое повышение эффективности твердосплавного инструмента и снижает его износ. В качестве перспективного способа нагрева грунта в последние годы выделилось микроволновое облучение на базе стандартного промышленного оборудования рабочей частотой 2,45 ГГц.
В США проведены испытания вращательного бурения скважины диаметром 50 мм одноперым долотом по сверхкрепким базальтам и крепким гранодиоритам прочностью на сжатие соответственно 440 и 282 МПа. Для нагрева грунтов использовали микроволновый генератор фирмы «Галф радиэйшн» с регулируемой выходной мощностью до 25 кВт и типовым алюминиевым волноводом. Повышение производительности бурения в сочетании с микроволновым нагревом получилось 6,5-кратным при заметно меньшем износе буровой коронки. Дальнейшая программа исследований предполагает эксперименты со стержневыми резцами и дисковыми шарошками. Ряд технических
149
решений, обеспечивающих экономичность и универсальность оборудования, умеренную энергоемкость, свободный доступ к забою и в то же время исключающих такие недостатки, как сотрясения грунтового массива, опасность, шум, переборы грунта, разрабатывают в Японии. Один из вариантов предполагает изоляцию всего забоя или отдельных его зон контурными щелями и последующее разрушение грунта в каждой зоне. Ограниченные контурными щелями блоки грунта можно разрабатывать и буровзрывным способом, причем при этом достигается экономия ВВ (до 2,5–3 раз) и снижение вибрации (до 6 раз).
Перспективным направлением является прорезание щелей в грунте высоконапорной водоабразивной струей. Фирма «Рамекс Системс Инк» (США) разработала оборудование ударно-скалы- вающего действия, предназначенное для работы по крепким скальным грунтам без их предварительного ослабления. На принципе ударно-скалывающего действия работает созданная фирмой «Роджер» (Канада) в 1988 г. буросбоечная машина, оснащенная ротором с тремя пневматическими бурильными молотками. В США ведут работы по созданию машин буровзрывной разработки грунтов слабыми взрывами в непрерывном режиме. Так, фирма «Мэшин Дизайн Инженерс Инк» провела эксперименты, показавшие, что разработка забоя в крепких скальных грунтах возможна с помощью шпуровых зарядов по 90 г (диаметром 10 мм и глубиной 91 см по сетке 46 46 см) с удельным расходом ВВ 490 г на 1 м3 грунта. Малое расстояние между шпурами гарантирует гладкое оконтуривание выработки, а непрерывность процесса заряжания и взрывания – скорость продвижения забоя выработки (диаметром 4,6 м) 1,2 м/ч. Технология требует подготовки к взрыву ВВ 10,9 кг/ч и связана с выделением 0,9–1,0 м3/мин взрывных газов, что вполне допустимо. Но для обеспечения технологических параметров время бурения шпура не должно превышать 2 мин даже при одновременной работе по четырем шпурам. Это потребовало создания специального оборудования и решения проблемы позиционирования исполнительных механизмов, безопасности взрывных работ без использования промышленных патронов и детонаторов (что неэкономично). Оборудование выполнено в виде трехпозиционной револьверной головки во взрывозащищенном исполнении (кожух из брони) и с полуавтоматическим управлением. Применяется серийная бурильная машина вращательноударного действия, буровая штанга диаметром 7,6 мм с промывочным каналом и одноперым долотом с твердосплавной встав-
150