
655
.pdf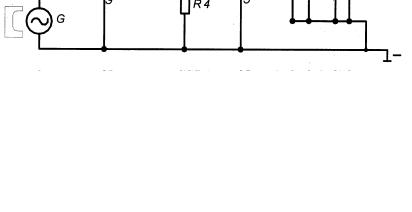
ского баланса катушки зажигания. Тогда при увеличении числа оборотов коленчатого вала ДВС вторичное напряжение снижается в КТСЗ значительно меньше, чем в КБСЗ [13, 19, 22, 29].
В качестве примера рассмотрим КТСЗ, собранную на базе транзисторного компаратора ТК-102 (см. рис. 9.3). Для уменьшения ЭДС самоиндукции в первичной цепи применяется специальная катушка зажигания типа Б114 с малым числом витков W1 и большим коэффициентом трансформации. Стабилитрон VД1 имеет напряжение стабилизации порядка 80 В. Резисторы R1, R2 изготовлены из проволоки высокого сопротивления (константан, нихром) и рассчитаны на ток 1 А. Проволочные резисторы R3, R4 рассчитаны на ток величиной 8 А. На плате, выполненной печатным способом, установлены стабилитрон VД1 и резисторы R1, R2. Эта система устраняет три основных недостатка КБСЗ (см. тему 8).
Высокая скорость нарастания напряжения в обмотках катушки зажигания КТСЗ обеспечивает более уверенное искрообразование даже при загрязненных свечах. Повышение выходного напряжения примерно в 1,3 раза по сравнению с КБСЗ позволяет увеличить искровой промежуток между электродами свечи зажигания до 0,7–0,8 мм. Это улучшает воспламенение горючей смеси в цилиндрах ДВС и приводит к более полному ее сгоранию.
Недостатки КТСЗ: потребляет относительно большую мощность от источников питания; требуется специальная катушка, которая не свободна от негативного влияния шунтирующих нагрузок R2 и С2 во вторичной цепи; рабочий диапазон температур ограничен и составляет от –40 до +60 °С; для исключения перегрева электронных приборов блок КТСЗ устанавливается в салоне ТТМ [19, 22, 24, 28].
9.4. Бесконтактные электронные системы зажигания
Принципиальная схема бесконтактной транзисторной системы зажигания с магнитоэлектрическим датчиком (БТСЗ с МЭД) представлена на рис. 9.4. При замкнутых контактах включателя S1 зажигания и при неподвижном роторе датчика G ток в управляющей цепи база – эмиттер транзистора VT1 отсутствует. Транзистор VT1 находится в состоянии отсечки. Высокое напряжение на коллекторе транзистора VT1 способствует переводу в состояние насыщения транзистора VT2, а затем и выходного коммутирующего транзистора VT3. Через открытый эмиттер-коллекторный переход транзистора VT3 в первичную обмотку W1 катушки зажигания L поступает ток, и в ее магнитном поле начинается процесс накопления энергии.
При вращении ротора МЭД положительная полуволна напряжения, генерируемая датчиком, переводит транзистор VT1 в состояние насыщения. Переход «база – эмиттер» транзистора VT2 шунтируется эмиттер-коллекторным переходом транзистора VT1, поэтому транзисторы VT2 и VT1 лавинообразно закрываются.
Рис. 9.4. Принципиальная схема батарейно-транзисторной системы зажигания с магнитоэлектрическим датчиком:
GB — АКБ; G — датчик; S1 — контакты замка зажигания; VD1 — диод; R1, R2, R3, R4 — резисторы; VТ1, VТ2, VТ3 — транзисторы типа «p–n–p»; L — катушка зажигания (W1, W2 — обмотки); Р — распределитель тока; СВ — свечи зажигания
Сила тока в первичной обмотке W1 катушки зажигания L резко уменьшается, а во вторичной обмотке W2 возникает высоковольтный импульс вторичного напряжения, который распределителем Р подается к соответствующей свече зажигания СВ.
61
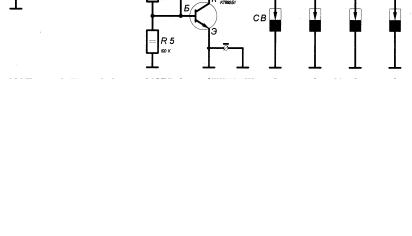
9.5. Электронная приставка для системы зажигания
Электронная приставка для системы зажигания, схема которой представлена на рис. 9.5, предназначена для дополнительной установки на машине с КБСЗ с целью устранения ее принципиальных недостатков. Новая электронная приставка по существу преобразует исходную систему зажигания (КБСЗ) в КТСЗ.
. 9.5.
|
|
: |
|
П |
; R1–R5 |
; R6* — |
- |
|
|
; |
|
1, 2 |
; VD1 |
; VР1 |
«м–к–м»; VР2 |
|
«к –м–к»; L |
; |
|
|
|
тока; |
|
При подключении электронной приставки изменяются характеристики системы зажигания:
–увеличивается наибольшая мощность искрообразования;
–увеличивается напряжение вторичной обмотки;
–снижается величина тока, проходящего через контакты, и тем самым, устраняется эрозия их поверхностей;
–регулируется мощность искрообразования в зависимости от температурного состояния ДВС;
–исключаются нагрев и выгорание элементов при включенном зажигании и неработающем ДВС и др.
Мощность искры зажигания зависит от температурного состояния VT2 и на горячем ДВС уменьшается, а на холодном — увеличивается, облегчая его запуск (рис. 9.5). При замыкании контактов прерывателя S импульс энергии проходит через емкость С1, кратковременно открывая VT1 и VT2. В момент размыкания S емкость С2 сглаживает пик импульса напряжения (напряжения самоиндукции) на первичной обмотке катушки зажигания. R5 и R6* ограничивают максимальное напряжение на коллекторе транзистора VT2, которое может «пробить» его (см. рис. 9.5).
При достижении на базе напряжения требуемой величины транзистор VT2 приоткрывается и ограничивает его дальнейший рост. Напряжение базы VT2 зависит от величины напряжения на переходе «база – эмиттер», которое, в свою очередь, зависит от температуры транзистора. Таким образом, температурный режим VT2 косвенно определяет величину тока первичной обмотки и тем самым мощность искрообразования на свече зажигания в зависимости от температуры (ДВС).
При размыкании контактов прерывателя S транзисторы VT1 и VT2 закрываются. Это приводит к образованию импульса во вторичной обмотке W2 (см. рис. 9.5) и возникновению искры на свече.
При длительно замкнутых контактах S ток через С1 постепенно убывает при его зарядке. Транзисторы VT1 и VT2 плавно закрываются, защищая катушку зажигания от перегрева.
Резистор R6* является подстроечным и обеспечивает стабилизацию выходного напряжения. Его номинал подбирается в зависимости от используемой катушки зажигания. На схеме (см. рис. 9.5) величина R6* указана для катушки Б115. Характеристики первичной обмотки катушки зажигания Б115: Ri = 1,6 Ом, I < 8А, Ui < 330 В. Коэффициент трансформации К = 68.
62
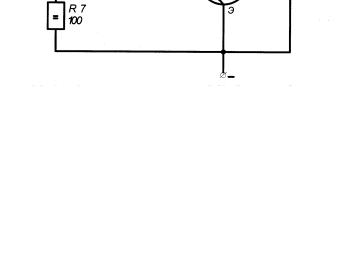
Для катушки Б116 ― Ri = 0,6 Ом, Ii < 20 A, Ui < 160 В, К = 154, величина R6* = 11 кОм. Для этой катушки в качестве VT2 лучше использовать транзистор типа КТ898А.
Для повышения надежности схемы (см. рис. 9.5) используется составной транзистор VT2. Элементы и приборы данной схемы (рис. 9.6) являются дополнением к схеме, рассмотренной
на рис. 9.5 (вместо VT2). Клеммы подключения имеют одинаковые наименования. Вместо транзистора КТ892Б1 устанавливаются два транзистора КТ814А, что повышает надежность системы зажигания при эксплуатации.
Рис. 9.6. Принципиальная схема составного транзистора (вместо VT2 на рис. 9.5):
VT2, VT3 — транзисторы типа «n–p–n» (КТ814А); R7 — резистор; VD2 — диод
9.6. Преимущества и недостатки электронных систем зажигания
Для оценки преимуществ и недостатков любых систем зажигания необходимо в первую очередь рассчитать и сравнить их энергию искрообразования. Рассмотрим энергию искрообразования в контактной батарейной системе зажигания (КБСЗ). Наиболее распространенной катушкой зажигания данной системы является катушка типа Б1. Основными характеристиками первичной обмотки катушки Б1 являются: индуктивность, равная 8,5 мГ, максимальный ток разрыва Ip (при пуске ДВС) ― 4 А при напряжении ―12 В.
Максимальная энергия WLmax , накопленная в магнитном поле катушки Б1, определяется по формуле
|
|
LIp2 |
8,5 10−3 42 |
|
||
W |
= |
|
= |
|
≈ 0,070 Âò ñ. |
(9.2) |
|
|
|||||
Lmax |
|
2 |
|
2 |
|
|
|
|
|
|
|
Экспериментально установлено, что для обеспечения бесперебойной работы системы зажигания ДВС при искровом напряжении 12–14 кВ минимальная энергия магнитного поля катушки должна составлять не менее 0,025–0,030 Вт·с [2, 7, 16, 28].
Вышеприведенный расчет накопленной в КБСЗ энергии показывает, что ее вполне хватает при пуске ДВС. Фактическая величина энергии искрообразования, идущей на создание вторичного напряжения U2max, оказывается значительно меньше расчетной как при малых оборотах ДВС (из-за бесполезных потерь на дугообразование между контактами прерывателя), так и максимальных (из-за существенного уменьшения тока разрыва в первичной цепи катушки зажигания) [15, 22, 28].
В реальных условиях энергия искрообразования КБСЗ может оказаться близкой к нижнему пределу, что не позволяет иметь достаточный запас по вторичному напряжению U2max для надежной работы ДВС. На это влияют следующие факторы: шунтирующее действие нагара на изоляторах и электродах свечи; приведенная емкость вторичной цепи; неоптимальный зазор между контактами прерывателя (непосредственным образом влияющий на время их замкнутого состояния); погрешности установки и регулировки угла опережения момента зажигания и т.д. В зимний период дополнительное снижение энергии искрообразования наблюдается и вследствие уменьшения
63
напряжения на АКБ при работе стартера, что затрудняет (а часто и делает невозможным) пуск ДВС [3, 12, 13].
Электронная система зажигания (см. рис. 9.5) полностью разгружает контакты прерывателя от тока первичной обмотки катушки зажигания. Это практически ликвидирует окисление и эрозию контактов S, значительно уменьшает отклонение от оптимального угла опережения зажигания и тем самым позволяет длительное время эксплуатировать систему зажигания без регулировки.
Увеличение тока первичной обмотки, коэффициента трансформации и, в конечном итоге, вторичного напряжения катушки зажигания позволяет увеличить зазоры между электродами свечей до 0,7– 0,8 мм. Повышение энергии искрового разряда и увеличенная длина искры способствуют более полному сгоранию горючей смеси и повышению мощности и приемистости ДВС. Особенно это проявляется при использовании электронной приставки на автомобилях старых марок, в которых установлена КБСЗ.
Таким образом, после проведенного анализа существующих систем зажигания можно утверждать, что электронные системы зажигания имеют следующие преимущества:
–универсальность применения подобных систем на всех типах бензиновых ДВС;
–значительное (в 1,3–1,5 раза) увеличение вторичного напряжения, достигающего 20–30 кВ при всех режимах работы ДВС;
–меньшая чувствительность к шунтирующим нагрузкам Rш и приведенной емкости С2 вторичной цепи;
–большой срок службы контактов прерывателя, достигающий 150–200 тыс. км и более;
–более полное сгорание топлива при малых и больших оборотах работы ДВС, что дает экономию горючего до 3 %;
–увеличение зазора между электродами свечей зажигания с 0,5–0,6 мм до 0,7–0,8 мм;
–облегченный пуск ДВС в зимних условиях при низких температурах;
–значительная экономия времени на профилактические и регулировочные работы при эксплуатации ДВС и всей машины [7, 12].
К недостаткам электронных систем зажигания следует отнести их стоимость; повышенную мощность, потребляемую от источника, и повышенную чувствительность к замасливанию контактов прерывателя. Этот недостаток характерен только для КТСЗ, потому что ток, протекающий через контакты прерывателя, имеет небольшую величину (0,12–0,15 А) [14, 15, 19, 28, 30].
Вопросы для самопроверки
1.Запишите уравнение баланса энергии электромагнитной катушки зажигания КБСЗ.
2.Начертите схему КБСЗ. Объясните принцип работы системы.
3.В чем заключаются недостатки КБСЗ?
4.Назовите преимущества и недостатки КТСЗ.
5.В чем заключаются преимущества и недостатки бесконтактной транзисторной системы зажигания с магнитоэлектрическим датчиком?
6.Назовите величины вторичного напряжения и запасенной энергии КЗ, необходимые для бесперебойного искрообразования на электродах свечи (КБСЗ).
7.Во сколько раз сила тока первичной цепи катушки зажигания в КТСЗ больше по сравнению с КБСЗ?
8.Как влияет температурное состояние ДВС на требуемую энергию искрообразования?
9.Назовите перспективные пути развития систем зажигания для бензиновых ДВС.
10.Назовите различия характеристик катушек зажигания двух систем: КБСЗ и КТСЗ.
11.Каким путем повышается мощность искрообразования в КТСЗ?
12.Преимущества электронных систем зажигания.
13.Назовите недостатки электронных систем зажигания.
14.Начертите принципиальную схему КТСЗ. Объясните принцип работы системы.
15.Особенности устройства КТСЗ.
64
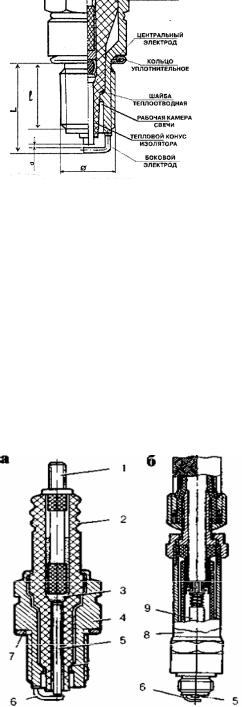
ТЕМА 10. ИСКРОВЫЕ СВЕЧИ ЗАЖИГАНИЯ
Устройство и назначение свечей зажигания. Характеристика. Типы. Маркировка.
Диагностика ДВС по состоянию свечи зажигания
10.1. Устройство и назначение свечей зажигания
Свеча зажигания предназначена для воспламенения рабочей смеси в цилиндре двигателя. При подаче высокого напряжения на свечу между электродами возникает искровой разряд, воспламе-
няющий топливовоздушную смесь в цилиндре ДВС [3, 11, 18, 22, 28]. |
|
|
|
|
||||||||||||
Устройство свечи зажигания |
|
|
|
приведено на рис. 10.1. Корпус |
||||||||||||
свечи представляет собой по- |
|
|
|
лую резьбовую конструкцию с |
||||||||||||
головкой |
под |
шестигранный |
|
|
|
ключ. Внутри корпуса распола- |
||||||||||
гается |
керамический |
изолятор, |
|
|
|
выполненный |
из материалов, |
|||||||||
обладающих высокой темпера- |
|
|
|
турной, электрической и меха- |
||||||||||||
нической стойкостью. Изолятор |
|
|
|
должен |
выдерживать |
напряже- |
||||||||||
ние не менее 30 кВ при макси- |
|
|
|
мальной |
температуре. |
|
Внутри |
|||||||||
изолятора |
|
закреплены цен- |
|
|
|
тральный электрод и контакт- |
||||||||||
ный стержень. Изолятор изго- |
|
|
|
тавливается из уралита, синок- |
||||||||||||
саля, |
|
хелумина, |
борокорунда |
|
|
|
или других материалов, которые |
|||||||||
обладают |
высокой |
механиче- |
|
|
|
ской прочностью и изоляцион- |
||||||||||
ной устойчивостью при высо- |
|
|
|
ких температурах. Центральный |
||||||||||||
электрод выполнен из высоко- |
|
|
|
легированных |
материалов: хро- |
|||||||||||
мотитановой стали 13Х25Т или |
|
|
|
хромоникелевого |
|
сплава |
||||||||||
Х20Н80 и др. В свечах с рас- |
|
|
|
ширенным |
температурным |
|||||||||||
диапазоном |
(«термоэластик») |
|
|
|
центральный |
электрод |
выпол- |
|||||||||
няется из меди, серебра или |
|
|
|
платины с термостойким по- |
||||||||||||
крытием |
рабочей |
части. В |
|
|
|
корпус свечи завальцовывается |
||||||||||
и заливается мастикой изоля- |
|
|
|
тор с центральным стержнем. |
||||||||||||
Накатка |
вокруг |
изолятора |
|
|
|
обеспечивает |
прочное |
соеди- |
||||||||
нение керамики и металла. |
|
|
|
|
|
|
|
|
||||||||
Уплотнительное кольцо из- |
Рис. 10.1. Устройство |
готавливается из железа, алю- |
||||||||||||||
миния |
или |
меди. |
Медные |
кольца |
предпочтительнее, так |
|||||||||||
свечи зажигания: |
||||||||||||||||
как улучшают отвод тепла от |
свечи. Уплотнительное кольцо |
|||||||||||||||
L — длина ввертываемой части; |
||||||||||||||||
обеспечивает |
герметизацию |
l — длина резьбы; |
цилиндра ДВС. Экранирован- |
|||||||||||||
ные |
свечи, |
например СН443, |
D — наружный диаметр резьбы; |
имеют |
встроенный |
резистор |
||||||||||
для |
исключения радиопомех |
d — искровый промежуток |
(рис. 10.2, б, поз. 9). |
|
|
|||||||||||
|
|
|
|
|
||||||||||||
|
|
|
|
|
|
|
а) |
|
б) |
|
|
|
|
|
|
|
|
|
|
|
|
|
|
|
|
|
|
|
|
|
|
|
|
|
|
|
|
|
|
|
|
|
|
|
|
|
|
|
|
Рис. 10.2. Конструкция свечи зажигания:
а— неэкранированная; б — экранированная; 1 — контактный стержень; 2 — изолятор; 3 — токопроводящий герметик;
4 — корпус; 5 — центральный электрод; 6 — боковой электрод;
7 — уплотнительное кольцо; 8 — экран; 9 — помехоподавляющий резистор
65
Герметизация центрального электрода и контактного стержня производится специальной токопроводящей стекломассой.
К корпусу свечи приварен боковой электрод из никель-марганцевого или хромоникелевого сплава. Некоторые фирмы, например «Bosch», применяют до четырех боковых электродов в свече. Считается, что увеличение числа боковых электродов способствует снижению колебаний частоты вращения коленчатого вала ДВС за счет более разветвленной и стабильной искры на свече.
Между центральным и боковым электродами устанавливается зазор 0,5–1,2 мм. Чем больше зазор, тем больше воспламеняющая способность искры, но при этом от системы зажигания требуются более высокие напряжение и энергия искрообразования.
Зимой целесообразно использовать минимальный зазор или даже уменьшать его на 0,1–0,2 мм от рекомендуемого минимального значения [3,12,13]. Для КБСЗ рекомендуется устанавливать зазор между электродами свечи зажигания 0,5–0,6 мм, для КТСЗ — 0,7–0,8 мм, для БТСЗ ― 0,8–1,2 мм.
10.2. Характеристика. Типы
При работе ДВС свеча подвержена высоким тепловым, электрическим, механическим и химическим нагрузкам. Нижняя часть теплового конуса свечи работает в интервале температур от 400 °С до 950 °С. На саму свечу воздействуют: напряжение до 30 кВ, высокое давление газов до 4 МПа и изменение температуры в диапазоне от –50 °С до +2500 °С. Тепло, подведенное к свече, отводится от нее через различные элементы ее конструкции (корпус, изолятор, центральный электрод) и поступающую в камеру сгорания горючую смесь. Все свечи характеризуются по тепловым качествам, т.е. по их способности выдерживать высокие температуры. Это достигается конструктивно путем использования высокотемпературных электродов и уменьшения внутренней поверхности изоляции, находящейся в прямом контакте с пламенем головки цилиндров.
Нормальная работа свечи происходит при температуре теплового конуса изолятора в диапазоне 400–900 °С [3,18,21,22,25]. После пуска холодного ДВС и до тех пор, пока он не прогреется, на холодном тепловом конусе изолятора свечи появляются отложения из несгоревших углеводородов. По мере прогрева ДВС температура свечи повышается и при достижении 400 °С и выше происходит выгорание нагара ― свеча самоочищается. Если температура свечи превысит 950 °С, возникает калильное зажигание, т.е. топливовоздушная смесь начинает воспламеняться в цилиндре не от искры, а от нагретых частей камеры сгорания (самопроизвольно), в том числе и от самой свечи, через которую отводится часть тепла. Поэтому для каждой конкретной модели ДВС необходимо подбирать свечи с определенной тепловой характеристикой, с определенным калильным числом.
Калильное число характеризует способность свечи к самостоятельной очистке и устойчивости к перегреву с нужным балансом. Калильное число свечи определяют специальным эталонным одноцилиндровым ДВС, степень сжатия которого изменяют до возникновения калильного зажигания. Среднее индикаторное давление при возникновении калильного зажигания соответствует калильному числу. Тепловые характеристики свечей нормируются и устанавливаются через ряд калильных чисел. Ряд калильных чисел свечей стандартизован, и в России он включает: 8; 11; 14; 17; 20; 23; 26.
В некоторых странах под калильным числом понимают время работы эталонного ДВС до начала калильного зажигания. Так нормирует калильное число, например, фирма Bosch (Германия) [18].
По тепловым качествам свечи делятся на «горячие» ― для двигателей с невысокой температурной нагрузкой и «холодные» ― для работы с высокой рабочей температурой в камере сгорания ДВС с большой степенью сжатия.
Теплоотдача свечи определяется целым рядом параметров и зависит от длины теплового конуса изолятора свечи. Длинный тепловой конус затрудняет отвод тепла, и нижняя часть свечи плохо охлаждается. Поэтому такая свеча называется «горячей». Она соответствует малым значениям калильного числа (8, 11) и рекомендуется для низкоскоростных ДВС с малым октановым числом горючего и с малой степенью сжатия. Короткий тепловой конус свечи характерен для «холодной» свечи с большими значениями калильного числа (20, 23, 26). Такие свечи рекомендуются для высокоскоростных, с большой степенью сжатия (форсированных) ДВС с высокооктановым топливом.
Толщина нагара на стенках камеры сгорания ДВС зависит от правильности выбора марки свечи в соответствии с температурным режимом двигателя. В ДВС с высоким температурным режимом нага-
66
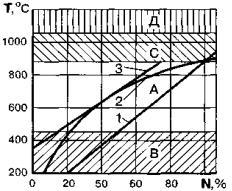
ра отлагается обычно меньше. По этой причине не рекомендуется ДВС долго эксплуатировать без термостата. Это приводит к преждевременному выходу из строя свечей [3, 12, 18, 22, 28].
При работе на этилированных бензинах количество нагара увеличивается в несколько раз по сравнению с работой двигателя на чистом бензине. Это происходит по причине накопления свинцовых соединений, которых в нагаре может содержаться до 40–60 %. Свечи, покрытые таким нагаром, практически коммутируются его сопротивлением, и искрообразование резко ухудшается.
Когда температура свечи менее 400 °С, то на тепловом конусе изолятора происходит усиленное нагарообразование. Свеча начинает работать с перебоями, так как через образовавшийся нагар происходит утечка тока высокого напряжения.
В случае, когда температура изолятора выше 950 °С, возникает калильное зажигание. При этом рабочая смесь воспламеняется от соприкосновения с раскаленным центральным электродом и с другими элементами. Перегретая свеча быстро выходит из строя, вызывая отказ работы ДВС.
На рис. 10.3 приведены зависимости температуры теплового изолятора свечи от нагрузки двигателя для «горячей», «холодной» свечи и свечи «термоэластик». Свеча «термоэластик» — свеча широкого температурного диапазона.
Рис. 10.3. Зависимость температуры теплового изолятора свечи от нагрузки ДВС:
1 — «горячая» свеча; 2 — «холодная» свеча; 3 — свеча «термоэластик»
Зоны температур: А — самоочищения электродов; В — интенсивного нагарообразования; С — перегрева изолятора; Д — калильного зажигания.
10.3. Маркировка
Маркировка свечей зажигания, выпускаемых отечественной промышленностью, включает следующие элементы [3, 11, 18, 22, 28].
1.Обозначение резьбы на корпусе свечи: А–М 14×1,25 или М–М 18×1,5.
2.Калильное число свечи (тепловая характеристика): 8, 11, 14, 17, 20, 23, 26.
3.Обозначение длины резьбовой части корпуса: Н — 11 мм; Д — 19 мм. Если длина резьбовой части корпуса не обозначена, то она равна 12 мм.
4.Обозначение выступания теплового конуса изолятора за торец корпуса: В — тепловой конус выступает за пределы корпуса свечи; отсутствие выступания — не обозначается.
5.Обозначение герметизации в соединении «изолятор — центральный электрод»: Т — герметизация выполнена с использованием термоцемента; герметизация соединения «изолятор — центральный электрод» иным герметиком — не обозначается.
6.Обозначение подавителя радиопомех: Р — наличие в свече резистора – подавителя радиопо-
мех.
Дополнительная запись может быть выполнена последующими обозначениями после дефиса, например: А17ДВР-10. Цифра 10 (после дефиса) указывает на использование специального типа изолятора, на увеличение толщины бокового электрода и введение антикоррозийного покрытия корпуса, которое повышает надежность работы свечи (при высоких напряжениях) и увеличивает ее долговечность. Через дефис может указываться также порядковый номер варианта разработки конструкции свечи и др. [12, 22, 25].
Пример обозначения отечественной свечи для автомобиля ВАЗ (прил. Б, табл. Б2): А17 ДВРМ, где А — резьба М 14×1,25; 17 — калильное число; Д — соответствует длине резьбы на корпусе свечи в 19 мм; В — означает, что тепловой конус изолятора выступает за пределы корпуса свечи; Р —
67
устанавливает наличие помехоподавляющего резистора; М — указывает, что центральный электрод имеет медный сердечник.
Аналогичное обозначение имеют свечи фирмы «Bosch». Первая буква в их обозначении W соответствует отечественной А, D соответствует М, далее может идти буква, обозначающая исполнение свечи (R — со встроенным резистором), последующая цифра характеризует тепловые характеристики (чем меньше цифра, тем свеча «холоднее»). Затем приводится буквенное обозначение длины резьбы свечи (D соответствует 19 мм). Последующее буквенное обозначение ― число боковых электродов, если их больше одного (D — два, Т — три, Q — четыре). Исполнение центрального электрода на свече фирмы «Bosch»: С — медь, Р — платина, S — серебро.
Кроме этого, в маркировке могут быть указаны условия эксплуатации свечей, например, климатические: У — умеренный климат эксплуатации, и другие.
Маркировка свечей зажигания иностранных производителей отличается от отечественных. Между ними существует взаимозаменяемость (материалы по данному разделу темы приведены в прил. Б, табл. Б2) [3, 18, 21, 22, 25].
10.4. Диагностика ДВС по состоянию свечи зажигания
Состояние рабочих свечей зажигания (внешний вид, окраска, напыление, нагар и др.) является «зеркалом» работы самого ДВС и отдельно каждого цилиндра. Опытный специалист по состоянию свечи может дать достаточно полную характеристику технического состояния бензинового ДВС. Ниже приведен ряд примеров, связанных с внешним видом свечи, возможными причинами отказов искрообразования и их устранением [3, 12, 15, 20, 22].
Нормальное состояние свечей зажигания характеризуется, как правило, светло-коричневым легким нагаром. Допускается светло-серый цвет юбки изолятора центрального электрода. Это говорит о том, что такие свечи идеально подходят к данному бензиновому ДВС, и указывает на его хорошее техническое состояние. При настройке карбюратора на слишком бедную смесь цвет изолятора свечи будет коричневым. Интенсивное образование сажи на свече характеризует отклонение в системе питания ДВС от оптимального режима в сторону обогащения топливовоздушной смеси.
Если свечи покрыты сухим черным налетом матового оттенка, то основной причиной этого может быть неправильная регулировка или неисправность карбюратора, дозирующего слишком богатую смесь.
Работа ДВС на холостых оборотах сопровождается черным выхлопом и неустойчивостью. В общем случае это может быть вызвано следующими причинами:
–неправильной регулировкой угла зажигания;
–низкой компрессией в цилиндре ДВС из-за отсутствия герметичности клапана или всех клапанов;
–износом цилиндро-поршневой группы;
–загрязнением воздушного фильтра;
–трещиной в изоляторе свечи;
–калильное число свечи больше, чем необходимое для данного ДВС.
Блестящий черный налет свидетельствует о попадании масла в камеру сгорания по причине износа маслосъемных колпачков штанг клапанов или колец поршней.
Толстый слой рыхлых отложений углеводородов на свече говорит о низком качестве используемых бензина и (или) масла.
Отложения красного цвета возникают из-за превышения допустимых норм концентрации железосодержащих присадок в топливе (качество топлива).
Радужный налет на свече характеризует обеднение топливовоздушной смеси в цилиндре ДВС, чаще из-за неисправности карбюратора или приборов впрыска.
Огнеупорный изолятор центрального электрода имеет бело-желто-зеленый оттенок. Свеча без нагара. Возможными причинами могут быть:
–неисправность карбюратора, результатом чего является слишком бедная смесь;
–резкая смена длительности холостого хода ДВС на избыточную акселерацию;
–обеднение смеси из-за подсоса воздуха со стороны впускного коллектора;
–нарушение крепления карбюратора или герметичности отводов на системы принудительного холостого хода и пневматического усилителя тормозов;
–испарение охлаждающей жидкости, попадающей в цилиндр из-под прокладок головки блока двигателя и впускного коллектора. При этом возможен белый выхлоп.
68
Электроды свечи блестят «как новые». Причиной этого является перегрев свечи, характеризующийся перегревом самого ДВС по разным причинам.
Вид изолятора центрального электрода кристально-белый, без всяких отложений. Эта свеча работала в режиме перегрева, возможно, из-за несоответствия ее калильного числа данному ДВС.
Для устранения перегрева ДВС и соответственно свечи зажигания нужно проверить систему охлаждения: термостат и радиатор. При необходимости следует внешнюю поверхность радиатора продуть сжатым воздухом и промыть его внутренние полости, проверить действительную температуру охлаждающей жидкости (с использованием ртутного термометра). Надо также проверить включение температурного датчика электрического вентилятора охлаждения (при его наличии) в рабочем режиме ДВС, поменять свечи на более «холодные» (с большим калильным числом), проверить работу карбюратора, так как бедная смесь повышает температуры сгорания и соответственно тепловой режим. Следует использовать бензин с более высоким октановым числом, с помощью корректора октанового числа топлива установить (в сторону его увеличения) соответствующий угол опережения зажигания, проверить момент искрообразования и при необходимости правильно установить.
Повреждение электродов характеризуется «неправильным» процессом горения топливовоздушной смеси в цилиндре ДВС. При этом электроды свечи выгорают, наконечник обгорает и приобретает блеск. На юбке изолятора центрального электрода образуются блестящие металлические шарики, выгорает сам изолятор. Это характерно для ДВС, работающего длительное время с аномальным сгоранием топлива в камере (детонация, калильное зажигание). Причиной возникновения таких процессов могут быть:
–низкое качество бензина;
–раннее зажигание;
–плохое техническое состояние ДВС;
–перегрев ДВС при длительных режимах под перегрузкой.
Разрушение изолятора центрального электрода свечи является следствием детонации. Образование на ней трещины, сколов и других механических повреждений происходит также из-за детонации в камере сгорания ДВС.
Для устранения причин детонации в цилиндре ДВС необходимо:
–проверить соответствие бензина данному двигателю (степени сжатия);
–проверить соответствие калильного числа свечи данному ДВС;
–установить правильный угол опережения момента зажигания;
–отрегулировать топливную систему;
–обогатить рабочую смесь;
–проверить систему охлаждения.
Существуют и другие характерные причинно-следственные признаки работы ДВС и свечей зажигания, например, их разгерметизация. В этом случае на изоляторе свечи (в месте соединения изолятора с корпусом) по всему периметру соединения образуется желтый налет. Во всех вышерассмотренных случаях отказов проверка свечи на соответствие калильному числу и качества используемого бензина является первостепенной операцией [3,18, 21–25].
Вопросы для самопроверки
1.Конструкция современной свечи зажигания.
2.Как осуществляется герметизация элементов конструкции свечи?
3.Какие нагрузки воспринимает свеча зажигания?
4.Какие материалы используются для изготовления изоляторов свечи?
5.Что называется калильным числом свечи зажигания?
6.Какими способами можно предохранить свечи от коррозии?
7.Какие условия требуются для бесперебойной работы свечи?
8.Какие свечи называют «горячими» и « холодными»?
9.Что характеризует тепловые качества свечей?
10.Какие элементы обозначаются в маркировке отечественной свечи?
11.Примеры маркировки разных свечей зажигания.
12.Объясните необходимость экранирования свечей зажигания.
13.Перечислите ряд калильных чисел отечественных искровых свечей.
14.Диагностика работы ДВС по состоянию свечи зажигания. Примеры.
15.Каков внешний вид свечи при нормальной работе ДВС?
16.Когда появляется нагар на свече зажигания и каковы способы его устранения?
69
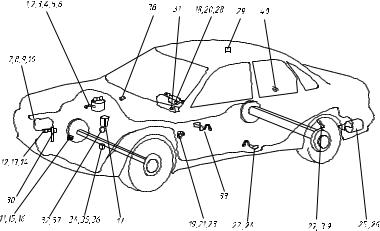
17.Назовите причины разрушения электродов свечей зажигания.
18.Чем объясняется «замасливание» свечей зажигания?
19.Каким образом происходит самоочищение свечей зажигания?
20.Назовите диапазон температур оптимальной работы свечей зажигания.
ТЕМА 11. ДАТЧИКИ БОРТОВЫХ ЭЛЕКТРОННЫХ СИСТЕМ
Электронные системы управления современными транспортными средствами. Датчики давления.
Датчики температуры. Датчики расхода жидкостей и газов. Датчики состава выхлопных газов.
Радарные и другие специальные датчики
11.1. Электронные системы управления современными транспортными средствами
Современные электронные системы автоматического управления (ЭСАУ) узлами и агрегатами машин имеют различные датчики, которые преобразуют информацию о значениях контролируемых неэлектрических параметров в электрический сигнал: напряжение, ток, частоту и т.д. (рис. 11.1) [19]. Сигнал преобразуется в цифровой код, который поступает в микроконтроллер. Микроконтроллер на основании этого кода и в соответствии с его программным обеспечением принимает решения и тем самым управляет объектом через исполнительные механизмы (реле, соленоиды, электродвигатели и др.). В современных ТТМ датчики устанавливаются практически во всех системах. Их общее количество достигает 40 ед.
Рис. 11.1. Расположение датчиков на автомобиле:
1 — конфигурации впускного коллектора с управляемой геометрией;
2 — тахометра; 3 — положения распределительного вала;
4 — нагрузки двигателя; 5 — положения коленчатого вала;
6 — крутящего момента двигателя; 7 — количества масла;
8 — температуры охлаждающей жидкости; 9 — скорости автомобиля;
10 — давления масла; 11 — уровня охлаждающей жидкости;
12 — радарный системы торможения; 13 — атмосферного давления;
14 — радарный системы предотвращения столкновений;
15 — скорости вращения ведущего вала коробки передач; 16 — выбранной передачи в коробке передач; 17 — давления топлива
в рампе форсунок; 18 — скорости вращения руля; 19 — положения педали; 20 — скорости вращения автомобиля относительно вертикальной оси;
21 — противоугонной системы; 22 — положения сидения; 23 — ускорения при фронтальном столкновении; 24 — ускорения при боковом столкновении; 25 — давления топлива в баке; 26 — уровня топлива в баке; 27 — высоты кузова по отношению к шасси; 28 — угла поворота руля; 29 — уровня влажности атмосферного воздуха (дождь, туман); 30 — температуры забортного воздуха; 31 — веса пассажира; 32 — кислорода;
33 — фиксирующий посадку пассажира; 34 — положения дроссельной заслонки; 35 — пропусков воспламенения; 36 — положения клапана рециркуляции выхлопных газов; 37 — абсолютного давления во впускном коллекторе; 38 — азимута; 39 — скорости вращения колес; 40 — давления в шинах [4, 9, 11, 16, 19, 24, 29, 30]
70