
655
.pdf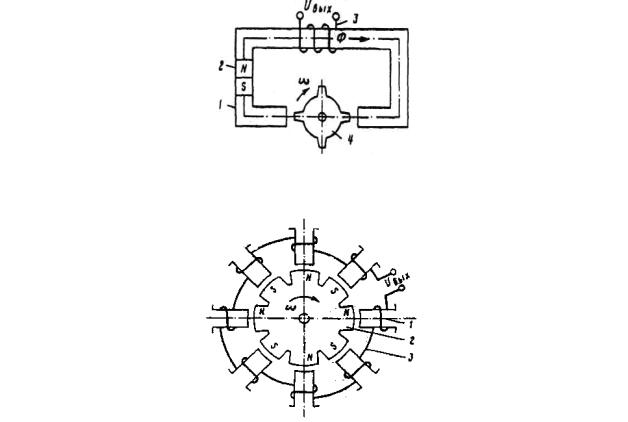
силы света между источником света и фотодатчиком устанавливается непрозрачная цилиндрическая шторка, представляющая собой диск с прорезями, число которых соответствует количеству цилиндров ДВС. Привод шторки или диска осуществляется от вала распределителя (синхронно коленчатому валу) [7, 14, 22, 28].
Внастоящее время на автомобилях отечественного производства наибольшее распространение
вэлектронных системах зажигания получили генераторные датчики Холла и магнитоэлектрические, обеспечивающие высокую точность отслеживания момента искрообразования и обладающие повышенной помехозащищенностью и стойкостью к внешним воздействиям.
Действие магнитоэлектрических датчиков (МЭД) основано на явлении электромагнитной индукции. МЭД представляет собой однофазный генератор переменного тока с возбуждением от постоянных магнитов, в котором механическая энергия преобразуется в электрическую энергию. Различаются МЭД коммутаторного типа с пульсирующим магнитным потоком (рис. 12.1) и МЭД с вращающимися магнитами (со знакопеременным магнитным потоком и симметричной формой сигнала выходного напряжения, рис. 12.2).
Рис. 12.1. Схема магнитоэлектрического датчика коммутаторного типа: 1 — магнитопровод; 2 — постоянный магнит;
3 — обмотка статора датчика; 4 — ротор датчика
Рис. 12.2. Схема магнитоэлектрического датчика с вращающимися магнитами:
1 — полюсный наконечник статора; 2 — зубец ротора (постоянный магнит); 3 — обмотка статора
12.2. Принцип действия магнитоэлектрического датчика
Принцип действия магнитоэлектрического датчика (МЭД) коммутаторного типа основан на изменении магнитного сопротивления магнитной цепи датчика и магнитного потока Ф, пронизывающего обмотку 3 (см. рис. 12.1), при изменении длины воздушного зазора между зубцами вращающегося ро- тора-коммутатора 4 и полюсными наконечниками (неподвижного статора) в магнитопроводе 1, в котором установлен постоянный магнит 2 [15, 16, 19, 22, 28]. Резкое уменьшение сопротивления магнитопроводника приводит к значительному увеличению напряжения на обмотке датчика Uвых.
В соответствии с законом электромагнитной индукции при вращении зубчатого ротора в обмотке статора наводится переменная ЭДС. Когда пара зубцов набегает на полюсные наконечники статора, магнитный поток Ф нарастает, а после достижения максимального значения и удаления зубцов ротора от полюсных наконечников статора — уменьшается (см. рис. 12.2).
81
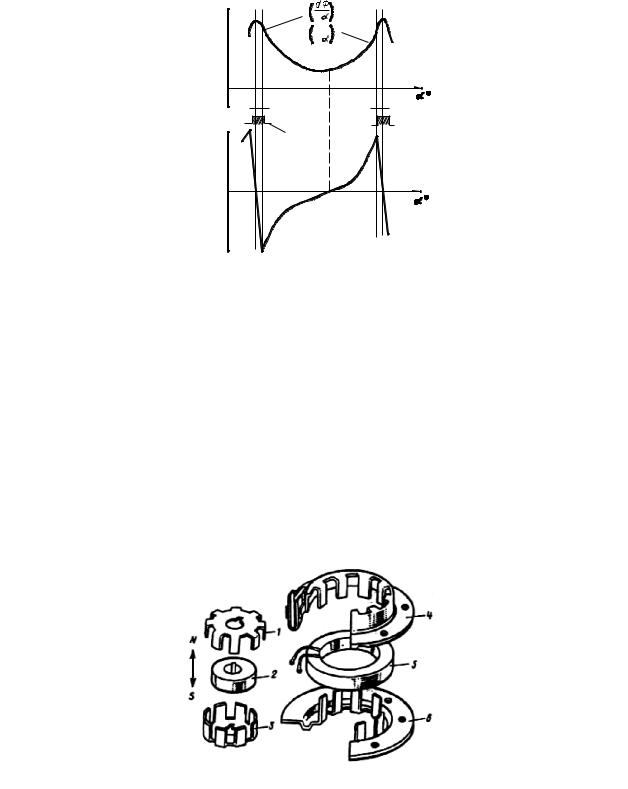
а) |
Ф,Вб |
d |
|
|
max |
||
|
|
||
|
|
dÔ |
|
|
|
d |
min |
|
|
|
, |
|
|
Зубец ротора |
|
б) |
U, |
|
|
|
Полюс статора |
||
|
|
||
|
|
|
, |
Рис. 12.3. Зависимости магнитного потока — а и напряжения — б на выводах обмотки статора датчика от угла поворота валика-распределителя
Таким образом, наибольший магнитный поток (рис. 12.3, а) возникает при совпадении осевых линий зубцов ротора и полюсных наконечников статора (см. рис. 12.1, рис. 12.2). В этот момент выходное напряжение Uвых изменяет знак на противоположный. Напряжение Uвых (рис. 12.3, б) изменяется от положительного максимума до отрицательного значения. Резкий переход выходного напряжения МЭД через нулевое значение используется для выработки сигнала управления моментом зажигания. Максимальные и минимальные значения напряжения Uвых соответствуют максимальным и минимальным скоростям изменения магнитного потока по углу поворота ротора МЭД [16, 19, 22, 28].
Конструктивно МЭД с вращающимися магнитами более сложные. Они состоят из неподвижной статорной обмотки 3 (см. рис. 12.2) статора 1 и постоянного магнита 2, жестко связанного с валиком датчика-распределителя. Число пар полюсов магнита равно числу цилиндров ДВС.
Конструктивно ротор МЭД, устанавливаемый в датчиках-распределителях БТСЗ (рис. 12.4), представляет собой кольцевой постоянный магнит 2, размещенный между двумя частями когтеобразной магнитной системы с полюсными наконечниками 1 и 3. Кольцевая обмотка 5 статора расположена между двумя обоймами 4 и 6 магнитной системы статора с когтеобразными наконечниками, число пар которых равно числу пар полюсных наконечников ротора.
Рис. 12.4. Конструкция магнитоэлектрического датчика: 1, 3 — полюсные наконечники; 2 — постоянный магнит; 4, 6 — обоймы с вращающимися магнитами;
5 — кольцевая обмотка статора датчика
При вращении ротора в магнитной системе статора изменяется магнитный поток, пронизывающий его обмотку, и на выходе датчика появляются импульсы напряжения, близкие синусоидальным. Напряжение МЭД подается на вход транзисторного коммутатора БТСЗ, который коммутирует ток в первичной цепи катушки зажигания, обеспечивая накопление энергии в ней и возникновение высокого вторичного напряжения в момент искрообразования (с соответствующим углом опережения зажигания) [19, 22]. Недостатками подобных МЭД являются: влияние частоты
82
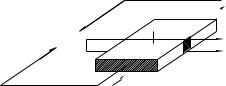
вращения ротора на выходное напряжение, значительная индуктивность самой обмотки датчика и влияние ее на амплитуду и скважность вырабатываемого сигнала.
Изменение величины напряжения МЭД по углу поворота ротора при различных частотах его вращения показано на рис. 12.5. Если уровень напряжения, при котором транзистор коммутатора, управляемый МЭД, переходит в состояние насыщения или отсечки, соответствует значению Uоткр, то при низком значении частоты вращения вала датчика-распределителя — n1 (при остальных одинаковых условиях) искрообразование произойдет позже, чем при более высоких — п2 (п2 › n1). Следовательно, изменение частоты вращения коленчатого вала автоматически приводит к смещению угла θ опережения момента зажигания в сторону его уменьшения (см. рис. 12.5) уже на стадии формирования сигнала МЭД. Это смещение приводит к необходимости дополнительно компенсировать угол опережения механическими автоматами опережения зажигания или применять в коммутаторе корректирующие элементы, что усложняет схему [15, 16, 19].
.
Рис. 12.5. Зависимость выходного напряжения МЭД от угла поворота ротора при разной частоте вращения вала ДВС
При весьма малых пусковых частотах вращения коленчатого вала ДВС напряжение, вырабатываемое МЭД, может быть даже недостаточным для перевода управляемого им входного транзистора коммутатора в открытое состояние, что затрудняет пуск ДВС [22, 28–30].
12.3. Применение датчика Холла в системе зажигания
Эффект Холла открыт относительно давно. Он проявляется в образовании ЭДС в кристаллах ряда материалов, в том числе и полупроводниковых, при прохождении через них электрического тока в момент воздействия магнитного поля. Таким образом, сигналом управления является магнитный поток. Элемент (кристалл) выполняется из полупроводниковых материалов (германий, кремний, арсенид галлия, арсенид индия и др.). Толщина кристалла составляет порядка 10–4 м [19,22, 28–30]. Принцип появления ЭДС в кристалле рассмотрен на рис. 12.6.
I
B
Ud |
eX |
|
I |
Рис. 12.6. Принцип появления в кристалле полупроводника ЭДС на эффекте Холла:
Ud — напряжение питания кристалла; I — ток в кристалле; В — магнитный поток (входной сигнал);
ex — ЭДС кристалла (выходной сигнал)
К двум выводам кристалла подводится напряжение питания датчика Ud, а с двух выводов снимается ЭДС ex весьма малой величины. Величина ЭДС полупроводникового кристалла зависит от силы тока (от напряжения Ud питания кристалла) и температуры.
В последнее время датчик Холла нашел широкое распространение в системе зажигания ТТМ. Он представляет собой интегральную микросхему, состоящую из последовательного ряда электронных приборов, одним из которых является элемент Холла (рис. 12.7).
83
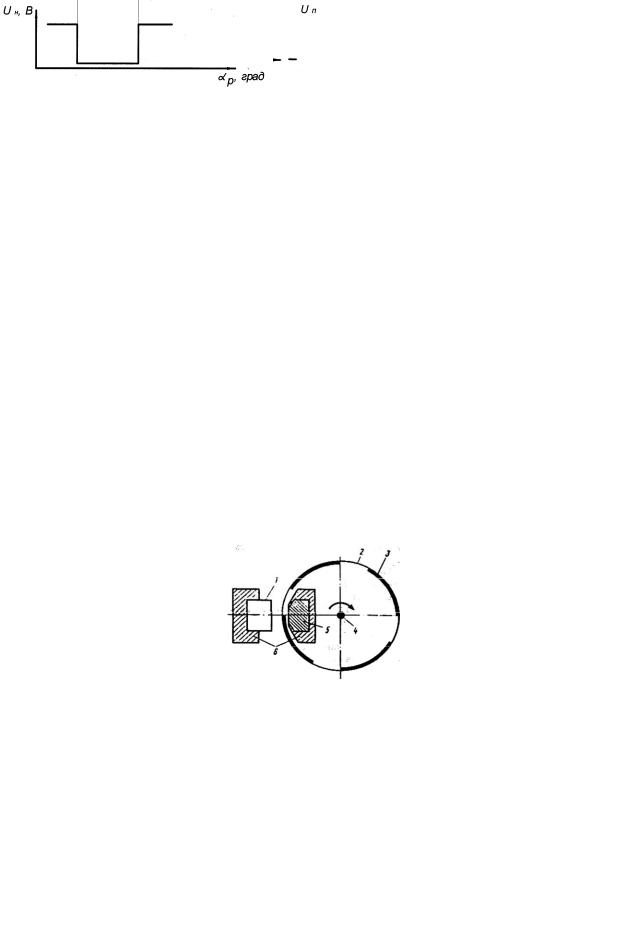
Рис. 12.7. Интегральная микросхема датчика (микропереключателя) на основе эффекта Холла:
В — магнитный поток (входной сигнал — сигнал управления); ЭХ — элемент Холла (полупроводниковый кристалл); ех — ЭДС элемента
Холла; У — усилитель; К — коммутатор (пороговый элемент); VT — транзистор типа «n–p–n»; СТ — стабилизатор напряжения;
Rн — нагрузка; Uн — выходной сигнал микросхемы; Uп — напряжение питания
Конструктивно и технологически датчик Холла выполнен в виде одной микросхемы, которая по существу является магнитоуправляемой интегральной схемой (рис. 12.7, поз 1). Входным сигналом датчика Холла является изменение магнитного потока.
Магнитное поле в датчике Холла создается постоянным магнитом 5 (рис. 12.8). Магнитная система и магнитоуправляемая интегральная схема конструктивно расположены в одном корпусе 6 и образуют в конечном итоге микропереключатель на эффекте Холла. Прерывание магнитного потока осуществляется ротором 2, который имеет шторки с экранами 3 и прорезями и выполнен из магнитомягкой электротехнической стали. Ротор 2 вращается вместе с валиком 4 датчика-распределителя.
Число прорезей экрана 3 равно числу цилиндров ДВС (см. прил. Г). При прохождении прорези ротора около постоянного магнита силовые линии магнитного поля пронизывают поверхность ЭХ и на его выходе появляется ЭДС, равная ех (рис. 12.7, 12,8, 12.9, а). Когда в зазоре между магнитоуправляемой интегральной схемой и магнитом находится экран ротора (см. рис. 12.8), происходит экранирование магнитного потока и значение ех снижается до минимума. При периодическом прерывании магнитного потока на выходе датчика Холла формируется сигнал в виде импульсов прямоугольной формы напряжением Uн (рис. 12.9, б) при определенном угловом положении коленчатого вала ДВС [19, 22, 28–30].
Рис. 12.8. Схема датчика Холла:
1 — магнитоуправляемая интегральная схема микропереключателя; 2 — ротор; 3 — экран с прорезями (по числу цилиндров ДВС);
4 — валик датчика-распределителя; 5 — магнит;
6 — корпус микропереключателя
а)
б)
84

Рис. 12.9. Зависимости ЭДС ех чувствительного элемента Холла — а и напряжения Uн — б микросхемы с датчиком Холла
от угла поворота ротора αp
Вмикросхеме обеспечивается гистерезис переключения выходного напряжения, так как уровни в и
гЭДС Холла ех, соответствующие включению и выключению порогового элемента, не совпадают (см. рис. 12.9, а). Частота вращения ротора практически не влияет на фронт и срез импульса ЭДС ех. Поэтому изменение (отклонение) угла опережения зажигания с датчиком Холла значительно меньше, чем с генератором МЭД (см. рис. 12.5).
Датчик Холла, как и все магнитоуправляемые интегральные схемы, чувствителен к воздействию внешних факторов. Исходя из этого, датчик Холла должен удовлетворять требованиям, предъявляемым к электронике, устанавливаемой под капотом машин.
а) |
|
U, |
âûñò óï |
âï àäèí à |
|
|
|
||
|
|
8 |
|
|
|
à) |
6 |
|
|
|
4 |
|
|
|
|
|
|
|
|
|
|
2 |
|
|
б) |
|
|
|
10 |
|
|
|
|
|
|
|
U1, |
|
|
|
|
250 |
|
|
|
á) |
200 |
|
|
|
150 |
|
|
|
|
|
|
|
|
|
|
100 |
|
|
|
|
50 |
 |
|
|
|
12 |
|
|
|
|
|
|
|
в) |
|
|
|
|
|
|
U2,ê |
|
|
|
|
25 |
|
Uï ð |
|
â) |
20 |
|
|
|
15 |
|
|
|
|
|
|
|
|
|
|
10 |
|
|
|
|
5 |
|
|
|
|
|
|
10 |
|
|
|
åì êî ñò í àÿ |
|
|
|
|
ô àçà |
|
âûñò óï |
|
|
âï àäèí à |
|||||
|
|
|
|
|
|
|
|
|
|
|
|
|
|
|
|
|
|
|
|
|
|
|
|
|
|
|
20 |
30 |
t,ì ñ |
|
|
t,ì ñ |
20 |
30 |
t,ì ñ |
|
|
Рис. 12.10. Характеристики процесса искрообразования электронной системы зажигания с датчиком Холла:
а— напряжение сигнала датчика Холла; б — напряжение противо-ЭДС первичной обмотки катушки зажигания;
в— напряжение вторичной обмотки катушки зажигания
Температурный режим нормальной работы датчика Холла обеспечивается при температурах окружающей среды от –40° до +125 °С. Смещение угла момента зажигания (погрешность искрообразования) во всем диапазоне температур не превышает 1° ± 0,5°.
Датчик Холла 40.3706.800 (отечественного производства, см. рис. 12.7) состоит из микросхемы типа К116КПЗ и магнитной системы на феррито-бариевой материальной базе [19, 22, 28–30]. Характеристики процессов искрообразования электронной системы зажигания с датчиком Холла представлены на рис. 12.10 и подобны процессам, изложенным в теме 8 (разд. 8.3).
Вопросы для самопроверки
1.Объясните назначение датчиков в БТСЗ.
2.Назовите типы датчиков, используемые в БТСЗ?
3.В чем особенность действия генераторных датчиков?
4.Назовите принцип работы параметрических датчиков.
5.Начертите схему датчика Холла (микросхему).
6.Объясните принцип работы фото- и пьезоэлектрического датчиков.
7.Перечислите виды магнитоэлектрических датчиков.
85
8.Каков принцип работы магнитоэлектрического датчика?
9.Назовите недостатки работы МЭД при формировании сигнала.
10.Перечислите преимущества и недостатки датчика Холла.
11.Начертите схему формирования импульса высокого напряжения в электронной системе зажигания с датчиком Холла.
12.В каких машинах отечественного производства система зажигания содержит датчик Холла?
13.Назовите температурный режим нормальной работы датчика Холла.
14.Объясните эффект Холла и принцип работы датчика.
15.Какие материалы применяются для изготовления датчика Холла?
ТЕМА 13. ЭЛЕКТРОННОЕ УПРАВЛЕНИЕ ДВИГАТЕЛЕМ ТТМ
Электронные системы автоматического управления топливоподачей бензиновых двигателей.
Экономайзер принудительного холостого хода с электронным управлением.
Электронные системы управления топливоподачей дизелей
13.1. Электронные системы автоматического управления топливоподачей бензиновых двигателей
Применяемые электронные системы автоматического управления (ЭСАУ) топливоподачей бензиновых двигателей подразделяются на системы впрыска (непосредственно в камеру сгорания или во впускной тракт) и карбюраторные системы с электронным управлением. Они могут быть с программным управлением и с автоматической адаптацией. Системы с непосредственным впрыском практически не применяются из-за сложности конструкции. Наибольшее распространение получили системы впрыска во впускной тракт. Они, в свою очередь, подразделяются на системы с впрыском в зону впускных клапанов и с центральным впрыском [11, 16, 19].
Система с впрыском в зону впускных клапанов включает в себя форсунки по числу цилиндров, система с центральным впрыском — одну или две форсунки на весь двигатель. Форсунки в системах с центральным впрыском устанавливаются в специальной смесительной камере, откуда полученная смесь распределяется по цилиндрам.
Принцип действия системы автоматического управления карбюратором заключается в изменении проходного (рабочего) сечения главного топливного жиклера в зависимости от режима работы двигателя.
К электронным системам управления топливоподачей программного типа относятся системы, управляющие форсунками по заранее заданному закону управления (по программе). Необходимым элементом таких систем является постоянное запоминающее устройство (ПЗУ), где хранится программа управления форсунками или карбюратором в соответствии с режимом работы ДВС. Такое ПЗУ получает сигналы от различных датчиков, установленных на ДВС, информацию о режиме работы ДВС (частоте вращения коленчатого вала, угле открытия дроссельной заслонки, крутящего момента), на основании которой форсункам или карбюратору подаются соответствующие команды.
Система с электронным впрыском работает следующим образом. Электрический топливный насос поддерживает постоянное давление топлива, равное примерно 0,2 МПа. Количество поступающего в цилиндры топлива, таким образом, определяется длительностью интервала, в течение которого форсунка находится в открытом состоянии.
Электронная система управления впрыском топлива программного типа (рис. 13.1) выполняет включение – выключение форсунок, т.е. управляет длительностью импульса, в течение которого происходит принудительный впрыск топлива в цилиндры ДВС в зависимости от угла открытия дроссельной заслонки, частоты вращения коленчатого вала, температуры охлаждающей жидкости и абсолютного давления топлива в бензопроводе [16, 19, 22, 24].
86
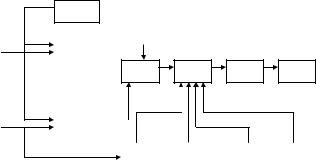
1
2 |
|
3 |
|
|
|
||
|
|
|
|
6 |
7 |
8 |
9 |
4 |
|
5 |
|
|
|
||
|
|
|
|
10 |
|
11 |
|
12 |
|
13 |
|
|
|
|
|
|
|
Рис. 13.1. Структурная схема системы управления впрыском топлива бензинового ДВС:
1 — тактовый генератор; 2 — датчик угла открытия дроссельной заслонки; 3 — АЦП-I; 4 — датчик оборотов коленвала ДВС; 5 — АЦП-II; 6 — ПЗУ; 7 — преобразователь; 8 — усилитель; 9 — электромагнитная форсунка (исполнительный орган); 10 — синхронизатор; 11 — датчик температуры охлаждающей жидкости; 12 — датчик абсолютного давления
(в топливоподаче); 13 — датчик температуры всасываемого воздуха
Информация о необходимом количестве впрыска топлива в виде кодовых комбинаций (в двоичной системе исчисления) хранится в ПЗУ. Каждая кодовая комбинация соответствует определенным частоте вращения коленчатого вала и углу открытого состояния дроссельной заслонки. Выбирая из ПЗУ нужную кодовую комбинацию, система впрыскивает в зону впускного клапана двигателя соответствующее количество топлива. Выбор кодовой комбинации из ПЗУ осуществляется системой управления на основании информации от датчиков частоты вращения коленчатого вала и угла открытия дроссельной заслонки. Синхронизация работы системы на этапе «впрыск топлива — искрообразование» обеспечивается с помощью датчика положения коленчатого вала ДВС. На датчике-распределителе 4 (рис. 13.1) установлены дополнительные контакты, которые формируют информацию о частоте вращения коленчатого вала двигателя в виде импульсного сигнала. Этот сигнал поступает на вход анало- гово-цифрового преобразователя (АЦП) 5, с помощью которого преобразуется в двоичный код для обращения к ПЗУ 6. Для преобразования аналогового напряжения, снимаемого с датчика угла открытия дроссельной заслонки 2, используется другой АЦП 3. Тактовый генератор 1 предназначен для формирования импульсов постоянной частоты, необходимых для работы обоих АЦП. Преобразованные сигналы, представленные в двоичном коде, один из которых характеризует угол открытия дроссельной заслонки, а второй — частоту вращения коленчатого вала, подаются на адресные входы ПЗУ [24, 28–30].
С выхода ПЗУ снимается сигнал в виде двоичного кода, характеризующий время открытия электромагнитной форсунки в зависимости от частоты вращения коленчатого вала и угла открытия дроссельной заслонки. Этот двоичный код преобразуется в устройстве 7 в интервал времени, пропорциональный требуемому количеству топлива. Устройство синхронизации 10, выходы которого связаны с распределителем 4, обеспечивает своевременный впрыск топлива в соответствующей точке рабочего цикла ДВС, что позволяет уменьшить оседание частиц топлива на стенках впускного топливопровода.
На входы преобразователя 7 дополнительно подается информация от датчиков: температуры охлаждающей жидкости 11, абсолютного давления топливоподачи 12, температуры всасываемого воздуха 13 для коррекции интервала времени, формируемого преобразователем 7. Далее этот сигнал усиливается в усилителе мощности 8 и подается на электромагнитные форсунки 9 [11, 24, 28– 30].
Электронные системы впрыска топлива обеспечивают высокую стабильность параметров. За счет этого они имеют преимущества перед обычными карбюраторами. К недостаткам таких систем относятся: низкая по сравнению с карбюраторами надежность, более сложное обслуживание и ремонт. Кроме того, данные системы, несмотря на сложность устройств, не учитывают индивидуальных особенностей ДВС: изменения его характеристик в процессе эксплуатации.
В настоящее время в системах управления впрыском топлива находит применение принцип оптимального управления. Он заключается в том, что в процессе регулирования подачи топлива учитывается влияние управляющего воздействия системы на эксплуатационные характеристики ДВС. На основании этой оценки формируется управляющий сигнал, который обеспечивает оптимальное значение регулируемых характеристик.
87

В качестве оптимизируемых показателей чаще используются: расход топлива, токсичность отработавших газов и мощность ДВС. Однако добиться одновременной оптимизации этих трех характеристик весьма сложно. Получение максимальной мощности ДВС достигается путем обогащения горючей смеси, а топливная экономичность — путем ее обеднения. Наилучшая очистка отработавших газов от токсичных элементов обеспечивается при составе смеси, близком к стехиометрическому. Стехиометрический состав ― качественное соотношение между компонентами, в данном случае — количеством топлива и воздуха, для полного сгорания в камере цилиндра ДВС. Поэтому применяемые на практике электронные карбюраторные системы являются программно-адаптивными с обратной связью. Параметром обратной связи служит химический состав отработавших газов (рис. 13.2) [15, 16, 19, 22, 28].
Для определения состава отработавших газов используется так называемый датчик кислорода (λ- зонд). Он устанавливается в выпускной системе двигателя и реагирует на процентное содержание кислорода в отработавших газах, пропорциональное коэффициенту избытка воздуха. λ-зонд фиксирует момент прохождения состава воздушно-топливной смеси через состояние, соответствующее стехиометрическому. Упрощенная схема управления, используемая в качестве «стабилизатора» стехиометрического состава смеси, представлена на рис. 13.2 [19, 22, 24, 28–30].
Рис. 13.2. Структурная схема стабилизации стехиометрического состава смеси в электронной карбюраторной системе управления:
1 — ДВС; 2 — λ-зонд; 3 — каталитический нейтрализатор; 4 — блок сравнения (напряжение рассогласования); 5 — дозирующее
устройство топливовоздушной смеси; 6 — блок опорного сигнала (задатчик сигнала); ОГ — отработавшие газы
Система работает следующим образом. Если дозирующее устройство 5 выдает для ДВС стехиометрический состав смеси, то с λ-зонда 2, установленного в выпускном тракте ДВС 1, снимается напряжение, которое поступает в блок сравнения 4. На вход блока 4 с блока-задатчика 6 подается опорное напряжение Uоп, равное напряжению λ-зонда при стехиометрическом составе горючей смеси. Пока на оба входа схемы поступают одинаковые напряжения, то напряжение на ее выходе, называемое напряжением рассогласования (ошибки), Uош равно нулю. Дозирующее устройство продолжает вырабатывать стехиометрический состав горючей смеси. Установленный в выпускной системе ДВС каталитический нейтрализатор 3 при этом обеспечивает качественную очистку отработавших газов (ОГ) от токсичных компонентов СО, СН, NO. Если состав горючей смеси отклонится от стехиометрического, напряжение на выходе λ-зонда 2 изменится. В результате на выходе схемы сравнения 4 появится напряжение рассогласования Uош. Сигнал со схемы сравнения поступает в дозирующее устройство 5, и происходит «поправка». Это вновь приводит к образованию стехиометрического состава топливовоздушной смеси.
Электронные карбюраторные системы на основных режимах работы ДВС являются замкнутыми системами регулирования, а некоторые системы производят поиск оптимального значения (экстремума) выходного параметра. Как правило, регулирующим органом, управляющим составом смеси, служит линейный соленоид с конусными измерительными иглами.
Ниже приведен ряд систем впрыска бензиновых ДВС, получивших широкое распространение [19, 22, 28].
Система К-Jetronic. Система устанавливается на автомобилях Audi-80, -100; BMW-320i, -520i; Mercedes-Benz-450 и др. Она имеет гидромеханическое управление. Топливо дозируется в зависимости от расхода воздуха и непрерывно впрыскивается в зону впускных клапанов. Управление
88
частотой вращения коленчатого вала происходит с помощью дроссельной заслонки, расположенной во впускном коллекторе.
Система КЕ-Jetronic. Система устанавливается на автомобилях Audi-80, -100; Ford Escort; Mer- cedes-Benz-190 и др. и предсталяет собой усовершенствованную систему К-Jetronic. Она оснащена электронным блоком управления (ЭБУ), корректирующим состав рабочей смеси в зависимости от температуры охлаждающей жидкости (от теплового режима ДВС).
Системы L-Jetronic и LE-Jetronic. Система L-Jetronic устанавливается на автомобилях BMW-528i, Opel Rekord, Volkswagen Polo и др. Система LE-Jetronic устанавливается на автомобилях BMW-520i, Opel Senator, Volvo-360 и др. Они осуществляют прерывистый впрыск топлива (одну или две порции за весь цикл) во впускной коллектор в зону впускных клапанов. Состав смеси определяется длительностью впрыска. Все управление осуществляется ЭБУ на основе информации о расходе воздуха через впускной коллектор, положении дроссельной заслонки, температуре воздуха и охлаждающей жидкости и частоте вращения коленчатого вала. Впрыск топлива осуществляется с помощью электромагнитных форсунок, управляемых ЭБУ, к которым под постоянным давлением подается топливо.
Системы LЕ2-Jetronic, L3-Jetronic и LН-Jetronic. Система LЕ2-Jetronic устанавливается на автомобилях BMW-520i, Opel Senator, Peugeot-309 и др., L3-Jetronic — на автомобилях BMW-520i и др., LНJetronic — Mercedes-Benz-600, Volvo-940 и др. Эти системы являются усовершенствованными системами L-Jetronic [19].
Системы LЕ2-Jetronic отличаются отсутствием пускового топливного клапана. Обогащение смеси достигается только за счет удлинения цикла подачи топлива через основные форсунки.
Блок управления системы L3-Jetronic представляет собой цифровую микро-ЭВМ, в памяти которой содержится оптимальная программа управления составом смеси для конкретного ДВС. Он способен отделить заведомо ложные сигналы от датчиков и компенсировать скачки напряжений бортовой сети автомобиля.
Система LН-Jetronic отличается от системы L3-Jetronic отсутствием паруса, тормозящего воздушный поток. Для измерения расхода воздуха используется платиновая нить с электроподогревом, обдуваемая потоком поступающего в цилиндры двигателя воздуха. После каждой остановки двигателя платиновая нить нагревается для выжигания образующегося на ней нагара [11, 19].
Система Mono-Jetronic. Устанавливается на автомобилях Audi-100, на многих автомобилях фирмы Fiat и др. Эта система имеет всего одну топливную форсунку, расположенную перед дроссельной заслонкой. Качество смеси определяется длительностью импульса открытия форсунки. Топливо в системе Mono-Jetronic подается под более низким давлением, нежели в описанных выше системах, — около 0,1 МПа.
Система Motronic. Широко распространена на большинстве современных автомобилей. Объединяет в себе электронную систему зажигания и систему топливоподачи, например КЕ-Jetronic, L- Jetronic, Mono-Jetronic.
Система Motronic имеет единый ЭБУ, обеспечивающий оптимальные характеристики зажигания и подачи топлива в зависимости от режима работы ДВС, температуры воздуха и охлаждающей жидкости и состава отработавших газов [16, 19, 22, 24, 29, 30].
13.2.Экономайзер принудительного холостого хода
сэлектронным управлением
При движении машины значительное время занимает режим принудительного холостого хода, когда коленчатый вал двигателя вращается за счет кинетической энергии машины. Этот режим наблюдается, например, при движении объекта с высокой скоростью при включенной передаче и опущенной педали управления подачей топлива, т.е. когда ДВС работает в тормозном режиме. Экономайзер принудительного холостого хода (ЭПХХ) предназначен для быстрого прекращения подачи топлива в ДВС в режиме холостого хода. В этом случае происходит снижение расхода топлива на 2–3 % и выброса токсичных веществ на 15–30 %.
Режим принудительного холостого хода в ЭПХХ определяется исходя из двух условий: частота вращения коленчатого вала ДВС должна быть больше частоты холостого хода, а дроссельная заслонка — закрыта [11, 19, 24, 29, 30].
Прекращение подачи топлива обеспечивается электромагнитными клапанами, установленными в каналах холостого хода карбюратора, например, в ЭПХХ автомобиля ЗИЛ-130. На легковых автомобилях для прекращения подачи топлива используется два клапана. Один из них, вакуумный, устанавливается в канале холостого хода, а другой, электромагнитный, ― в магистрали, соединяющей впуск-
89
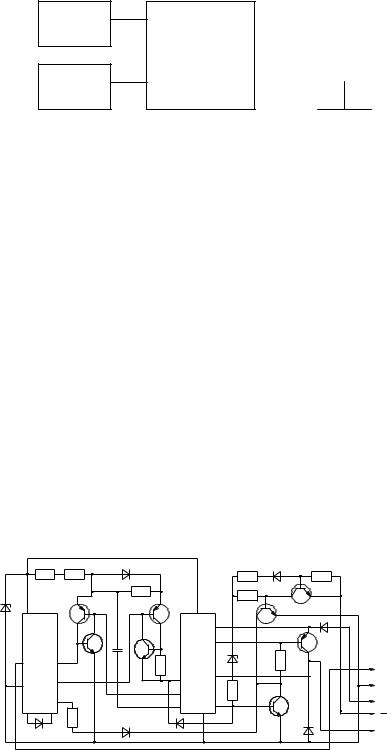
ной коллектор с диафрагменной камерой вакуумного клапана [19, 22, 28–30]. На рис. 13.3 приведена функциональная схема ЭПХХ легкового автомобиля ВАЗ-2108.
СЗ
Электронный |
|
|
блок |
ЭМК |
|
управления |
|
|
|
|
|
|
|
|
Д
Рис. 13.3. Упрощенная функциональная схема экономайзера принудительного холостого хода (ЭПХХ) с электронным управлением
На основе информации о частоте вращения коленчатого вала, получаемой от первичной цепи системы зажигания СЗ (см. рис. 13.3), и информации о положении дроссельной заслонки, получаемой от датчика положения дроссельной заслонки Д, электронный блок управления (ЭБУ) вырабатывает сигнал, управляющий электромагнитным клапаном (ЭМК). ЭМК открывает и закрывает подачу топлива в канал холостого хода карбюратора. Датчик положения дроссельной заслонки представляет собой микровыключатель с замыкающимися контактами при полностью отпущенной педали управления подачей топлива (в режиме холостого хода).
Принципиальная схема электронного блока управления ЭПХХ 50Д.3761 отечественного производства приведена на рис. 13.4. Структурно он состоит из двух компараторов напряжения, цепи обратной связи и несимметричного триггера. Блок управления работает следующим образом. Входной сигнал с прерывателя системы зажигания (клемма 1) подается на вывод 4 микросхемы А1. На выходе микросхемы А1 (вывод 3) формируются импульсы постоянной длительности, частота повторения которых соответствует частоте входных сигналов. На транзисторах VT1 и VT2 построен ключ, который во время действия импульса на выходе микросхемы А1 разряжает времязадающий конденсатор С1. В паузе между импульсами конденсатор С1 заряжается через резисторы R1 и R2. Максимальное напряжение, до которого заряжается конденсатор С1, увеличивается с уменьшением частоты входного сигнала.
На транзисторах VT3 и VT4 построен пороговый элемент. Когда напряжение на конденсаторе С1 превысит опорное значение, равное примерно 8 В, эти транзисторы открываются. Таким образом, при уменьшении частоты входного сигнала до величины ниже порога включения конденсатор С1 успевает зарядиться до напряжения, превышающего опорное значение порогового элемента. При этом транзисторы VT3 и VT4 открываются и через микросхему А2 на базу транзистора VT6 подается сигнал, который открывает этот транзистор и, следовательно, транзистор VT8, в результате чего на нагрузку (клемма 6) подается напряжение питания.
R1 |
R2 |
|
VD3 |
|
R7 |
VD7 |
R10 |
|
|
|
|
|
|||
|
|
|
R4 |
|
|
|
|
|
|
|
|
|
R8 |
|
VT7 |
|
|
|
|
|
|
|
|
VD1 |
VT1 |
|
VT4 |
|
|
|
|
|
|
|
|
|
VT5 |
|
|
8 |
|
|
|
5 |
|
|
|
|
|
|
|
|
7 |
|
|
|
|
|
VT3 |
|
8 |
VT8 |
VD9 |
|
|
|
|
|
|
||
|
|
|
C1 |
|
|
|
|
|
|
|
R5 |
|
VD6 |
|
|
4 |
3 |
VT2 |
|
A2 |
|
R9 |
|
A1 |
|
|
|
|
|
1 |
|
|
|
|
|
|
|
||
|
|
|
3 |
|
9 |
|
|
|
1 |
|
|
|
|
2 |
|
2 |
|
|
|
|
|
||
|
|
|
|
|
|
||
|
|
|
|
|
|
|
|
|
|
|
1 |
|
R6 |
VT6 |
4 |
|
|
|
|
|
|
||
|
9 |
|
|
|
|
|
|
|
|
2 |
|
4 |
|
|
|
|
|
|
|
|
|
||
|
|
|
|
|
|
|
|
|
|
|
|
|
|
|
5 |
6 |
5 |
R3 |
VD4 |
VD5 |
6 |
VD8 |
|
|
|
|
|
|
6 |
||
|
|
|
|
|
|
||
|
|
|
|
|
|
|
|
VD2 |
|
|
|
|
|
|
|
Рис. 13.4. Принципиальная схема электронного блока управления ЭПХХ 50Д.3761 отечественного производства. Клеммы подключения:
1 — входной электрический сигнал с прерывателя системы зажигания СЗ; 2, 4 — напряжение питания блока управления; 5 — входной электрический сигнал от потенциометрического датчика положения дроссельной заслонки карбюратора ДВС; 6 — выходной сигнал
управления электромагнитным клапаном (ЭМК) холостого хода в карбюраторе
При соединении штекера 5 с «массой» (через контакты датчика положения дроссельной заслонки) выходное напряжение на электромагнитном клапане изменяется в зависимости от вход-
90