
Строительные и дорожные машины. Основы автоматизации
.pdf231
ется от 0,32 (при наклоне в 55°) до 0,74 (при 25°); kр – коэффициент раз-
рыхления грунта (см. табл. 4.1).
Развиваемая двигателем мощность P, кВт, в режиме экскавации грунта траншейным экскаватором определяется суммой четырех ее основных составляющих: на копание Рк, подъем грунта к месту разгрузки Рп, привод отвалообразователя Nотв и ходового механизма Р
Р Рк Рп Ротв Р . |
(4.12) |
Мощность на привод отвалообразователя определяют по формулам, приведенным ранее для транспортирующих машин (см. гл. 3). Остальные со-
ставляющие мощности определяют по формулам: |
|
Рк Птк1 / 3600 ; |
|
Pn Пт gHcpk/ 3600 p ; |
(4.13) |
P Fvx / 3600 x , |
|
где Пт – техническая производительность экскаватора, м3/ч; k1 – удельное сопротивление грунта копанию, кПа (k1 = 100...400 кПа); – плотность грунта в неразрыхленном состоянии, кг/м3; g – ускорение свободного падения, м/с2; Hcр – средняя высота подъема грунта к месту разгрузки, м; k – коэффициент, учитывающий трение грунта о грудь забоя (для ковшовых экскаваторов k =1, для скребковых экскаваторов значение определяют по приведенной ниже зависимости); F – суммарное тяговое усилие с учетом горизонтальной составляющей сопротивления грунта копанию, кН; υх – скорость передвижения экскаватора, м/ч; ηр и ηx – коэффициенты полезного действия передачи и рабочего органа, передачи и движителя соответственно.
Среднюю высоту подъема грунта определяют расстоянием от центра тяжести поперечного сечения траншеи до центра тяжести грунта в ковше (на скребке) в положении его разгрузки. Коэффициент, учитывающий трение грунтов о грудь забоя для скребковых экскаваторов, определяют по формуле
k 1 f1ctg , |
(4.14) |
где f1 – коэффициент внутреннего трения; β – угол наклона груди забоя к горизонту.
На траншейных экскаваторах устанавливают двигатели увеличенной на 20...25 % мощности по сравнению с расчетной, что обеспечивает им устойчивую работу в различных грунтовых условиях.
Карьерные экскаваторы поперечного копания. Применяемые в строи-
тельстве карьерные экскаваторы различают по исполнению рабочего оборудования: соответственно роторные стреловые и цепные. По направлению рабочих движений эти машины относят к экскаваторам поперечного копания.
Роторные стреловые экскаваторы предназначены для разработки грунтов I...III категорий, однородных или с наличием некрупных каменистых
,
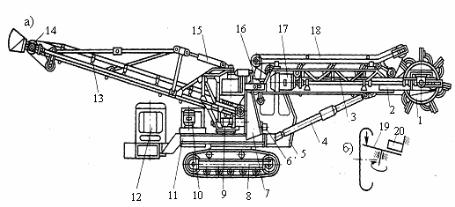
232
включений. Эти машины имеют широкую область применения: на вскрышных работах и карьерной добыче строительных материалов, разработке больших котлованов и других выемок в промышленном, транспортном и мелиоративном строительстве, возведении насыпей, дамб, плотин, на погрузочно-разгрузочных работах на складах насыпных материалов. Отечественной промышленностью выпускаются экскаваторы на базе ди- зель-электрических одноковшовых экскаваторов четвертой и шестой размерных групп для разработки грунта выше уровня стоянки до 7,5 м и ниже этого уровня до 3,5 м при радиусе копания до 11,5 м и технической произ-
водительности в грунтах I категории до 550 м 3/ч. По удельной энергоемкости эти машины находятся на уровне лучших экскаваторов непрерывного действия (0,22...0,24 кВт∙ч/м3), но уступают им по удельной материало-
емкости (100...140 кг/м3/ч).
От базовых одноковшовых экскаваторов в конструкциях роторных стреловых экскаваторов сохраняют ходовые 8 (рис. 4.28, а) и опорноповоротные устройства, частично или полностью платформу 11, на которой располагают силовую дизель-генераторную установку 12 (обычно в хвостовой части платформы с целью ее уравновешивания), насосную станцию 6, механизмы поворота 10, кабину 5 с органами управления и две стойки-пилоны 7.
В верхней части пилонов шарнирно закрепляют стрелу 2 с ротором 7 на конце и приемным ленточным конвейером 3, расположенным вдоль стрелы. Для работы на уступах различных уровней стрела может поворачиваться относительно шарнира на пилоне в вертикальной плоскости посредством гидроцилиндра 4. Ротор с ковшами и тарельчатым питателем 19 (рис. 4.28, б) приводится во вращение от электродвигателя 17 через систему карданных валов и зубчатых передач, а приемный конвейер — моторбарабаном 16 (рис. 4.28, а). Последний представляет собой барабан со встроенным в него электродвигателем и зубчатым редуктором.
Рис. 4.28. Роторный карьерный экскаватор поперечного копания: а) −общий вид; б) −тарельчатый питатель;1− ротор; 2− стрела; 3− ленточный конвейер; 4, 15− гидроци-
линры; 5− кабина; 6− насосная станция; 7− стойка-пилон; 8,9− ходовое и опорноповоротное устройство; 10 –механизм поворота; 11− платформа; 12− дизель – генератор; 13−отвальный конвейер; 14, 16− мотор-барабан; 17− электродвигатель; 18− прижимной конвейер; 19− тарельчатый питатель; 20− скребок
,
233
Отвальный конвейер 13 опирается на центрально установленный подпятник 9 с индивидуальным электрическим приводом, обеспечивающим конвейеру независимый поворот в плане относительно поворотной платформы. Вертикальное положение отвального конвейера в зависимости от высоты разгрузки регулируют гидроцилиндром 75, шарнирно закрепленным на кронштейнах стоек-пилонов с возможностью соосного вращения с отвальным конвейером. Привод отвального конвейера осуществляется мо- тор-барабаном 14 на его дальнем конце. Для работы верхним копанием (выше уровня стоянки экскаватора) машину располагают перед забоем на расстоянии вылета стрелы. Отвальный конвейер устанавливают по высоте и в плане в положение разгрузки. Вертикальными перемещениями стрелы при вращающемся роторе последний заглубляют в грунт на высоту уступа. Фиксируя в этом вертикальном положении стрелу, одновременным поворотом платформы и вращением ротора при движении ковшей снизу вверх разрабатывают грунт, отделяя его от массива, вынося ковшами вверх и разгружая на тарельчатый питатель, выполненный в виде наклонного вращающегося диска 19 (рис. 4.28, б).
С помощью скребка 20 грунт ссыпается с тарельчатого питателя на приемный ленточный конвейер, транспортируется им и перегружается в центральной части поворотной платформы на отвальный конвейер, которым выносится и разгружается в транспортное средство или в отвал. При разгрузке в транспортные средства положение отвального конвейера в плане неизменно, а при разгрузке в отвал конвейер может находиться в одном положении или поворачиваться для распределения отсыпанного грунта ровным слоем в пределах отведенной полосы. В конце поворотного перемещения платформы, ограниченного шириной захватки забоя, ротор со стрелой опускают до уровня следующего уступа и реверсивным движением поворотной платформы при прежнем направлении вращения ротора повторяют экскавацию грунта. После разработки последнего уступа, чаще всего соответствующего уровню стоянки экскаватора, машину перемещают в направлении к забою на новую стоянку и повторяют землеройный процесс.
Для работы нижним копанием ковши на роторе переставляют, поворачивая их на 180°, для возможности разработки грунта вращением ротора в обратном прежнему направлении. Опустив стрелу, экскавацию грунта осуществляют по описанной выше схеме для верхнего копания. Для надежного транспортирования грунта круто наклоненным приемным конвейером используют прижимной конвейер 18 (см. рис. 4.28, а), который устанавливают над приемным конвейером. Грунт перемещается между лентами двух конвейеров, движущимися в одном направлении. Для добычи полезных ископаемых открытым способом, а также для вскрышных работ применяют мощные роторные комплексы производительностью до 5 000 м3/ч в составе роторного экскаватора и накопительно-перегрузочных устройств с железнодорожными или автомобильными транспортными средствами на карьерно-добычных работах или транспортного отвального обору-
,
234
дования непрерывного действия на вскрышных работах. По своей структуре эти экскаваторы сходны с описанными выше строительными экскаваторами, но отличаются от них размерами и конструктивными решениями отдельных узлов. Фактическая, эксплуатационная производительность этих комплексов в значительной мере зависит от типа транспортных средств, которыми в основном определяются размеры вынужденных простоев экскаватора, меньшие для отвального оборудования непрерывного действия и большие для железнодорожного транспорта, особенно одноколейного.
Цепные экскаваторы поперечного копания применяют для добычи строительных материалов, в основном в карьерах кирпичных заводов. Базовая часть машины (рис. 4.29, а) состоит из нижней рамы, металлоконструкций надстройки, рельсо-колесного ходового устройства и механизмов привода ковшовой цепи, хода, подъема и опускания ковшовой рамы с питанием от электрической сети. В процессе работы экскаватор перемещается по рельсам вдоль разрабатываемого карьера. Рабочий орган, состоящий из П-образной ковшовой рамы, ковшовой цепи, приводного вала со звездочками, натяжных колес и поддерживающих роликов, установлен так, что его ковшовая цепь перемещается в плоскости, перпендикулярной перемещению экскаватора.
Ковшовую раму подвешивают к стойке через два полиспаста. Перемещаясь вдоль забоя, экскаватор ковшами разрабатывает грунт, которым они заполняются, выносит его из забоя и отсыпает в бункер или отвальный конвейер. Ковшовая рама состоит из четырех шарнирно сочлененных участков: верхней и нижней рам, верхнего и нижнего планирующих звеньев. С помощью полиспастов можно получить различные конфигурации ковшовой рамы, которыми обеспечиваются необходимые схемы копания. Нижнее планирующее звено DЕ (рис. 4.29, б) используют для разработки забоя постоянной глубины параллельным нижним копанием (ниже уровня стоянки экскаватора). С этой целью верхнее планирующее звено ВС жестко соединяют с верхней рамой АВ, а ковшовую раму посредством полиспастов устанавливают в исходное положение АСоDоЕо.
После отработки карьера по всей его длине ковшовую раму опускают на толщину среза h — положение АС1D1Е1, после повторной проходки—до положения АС2D2Е2 и т. д. до предельного положения АВСDЕ, которым исчерпываются кинематические возможности отработки забоя. После этого рельсовый путь отодвигают от забоя на расстояние S, определяемое начальным и конечным положениями ковшовой рамы (0,8...2 м), и повторяют процесс.
При жестком соединении нижнего планирующего звена DЕ (рис. 4.29, в) с нижней рамой СD и изменении положения ковшовой рамы только с помощью нижнего полиспаста получаем веерную схему копания. Последовательные положения ковшовой рамы АСЕо, АСЕ1 и т. д. до предельного АЕ показаны на рис. 4.29, в.
,
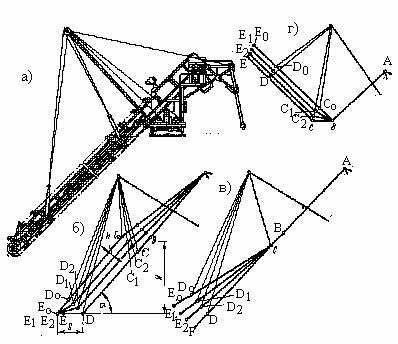
235
Рис.4.29. Карьерный цепной экскаватор поперечного копания: а)−конструктивная схема; схема копания − нижним параллельным (б), нижним
веерным, (в) и верхним параллельным ковшовой рамой (г)
Веерная схема проще в управлении по сравнению со схемой параллельного копания. Для ее реализации не требуется регулировать нижнее планирующее звено, а установка ковшовой рамы в требуемое положение обеспечивается одним полиспастом вместо двух. Ее существенным недостатком является переменная толщина среза по длине разрабатываемого откоса — максимальная внизу и уменьшающаяся практически до нуля в верхней части. Это приводит к неравномерному нагружению ковшей по длине разработки и снижению вследствие этого производительности экскаватора. Эта схема, кроме того, не обеспечивает ровной поверхности подошвы забоя, в связи с чем при переходе на новые уступы требуется проводить дополнительные планировочные работы. Этих недостатков нет в схеме параллельного копания, однако она более сложна конструктивно и в эксплуатации. Верхнее планирующее звено ВС используют для отработки забоя верхним копанием (выше уровня стоянки экскаватора). Схема верхнего копания параллельными срезами показана на рис. 4.29, г.
Отечественной промышленностью выпускаются цепные экскаваторы поперечного копания на глубину (высоту) до 8,5 м производительностью до 45 м3/ч при непрерывной работе. Энергоемкость разработки грунта этими машинами составляет 0,39...1,33 кВт∙ч/м3, а материалоемкость —
260...560 кг/(м3/ч).
Производительность карьерных экскаваторов поперечного копания определяют по формулам (4.10) и (4.11). Для цепных экскаваторов поперечного копания техническая производительность (м3/ч) может быть выражена через глубину (высоту) карьера Н (м), среднюю толщину среза hср
,
236
(м), угол заложения откоса а и рабочую скорость передвижения экскаватора υп (м/ч) по формуле
ПТ Hhсрvnk /sin , |
(4.15) |
где k – коэффициент, учитывающий потери грунта из-за его осыпания на дно карьера.
4.4. Землеройно-транспортные машины (ЗТМ)
Землеройно-транспортными за счет тягового усилия послойно отделяют грунт от массива и транспортируют его к месту укладки (отсыпки) в процессе собственного перемещения. Исключение составляют грейдерэлеваторы, у которых грунт транспортируется и отсыпается в отвал или в транспортные средства специальным транспортирующим органом одновременно с его разработкой.
По режиму работы ЗТМ делят на машины цикличного (бульдозеры, грейдеры, скреперы) и непрерывного (грейдер-элеваторы) действия. По конструкции рабочего оборудования различают отвальные и ковшовые ЗТМ. У первых рабочий орган выполнен в виде отвала, оснащенного в его передней части ножами (бульдозеры, грейдеры) или дискового плуга (грейдер-элеваторы). Ковшами оборудуют скреперы. По признаку подвижности ЗТМ относят к передвижным машинам. В последние годы все большее распространение получают самоходные ЗТМ (бульдозеры, скреперы, автогрейдеры). Реже применяются прицепные машины (скреперы, грейдер-элеваторы).
Рабочий процесс ЗТМ цикличного действия состоит из операций отделения грунта от массива (копания), его транспортирования к месту укладки (отсыпки), разгрузки и возвращения машины на исходную позицию. Грунт отделяют от массива гладкими или оснащенными зубьями ножами за счет тягового усилия тягача. В зависимости от вида рабочего оборудования отделенный грунт накапливается перед отвалом или поступает в ковш, которыми он транспортируется к месту отсыпки. Скорости передвижения ЗТМ выбирают в зависимости от преодолеваемых сопротивлений. При копании скорости машины минимальны, меньше при разработке прочных и больше при разработке слабых грунтов. При транспортировании грунта сопротивления передвижению ЗТМ ниже, чем при копании. Поэтому в транспортном режиме скорости передвижения машины увеличатся. Еще большими они будут при возвращении машины на исходную позицию вследствие снижения сопротивлений передвижению разгруженной машины. При движении по уклонам под гору скорости увеличиваются, а при движении в гору снижаются. При движении по дорогам скорости ограничиваются нормами Госавтоинспекции. Скорости передвижения ЗТМ могут быть также ограничены по технологическим соображениям, например, возможностью оптимального управления грейдером или бульдозером при планировочных работах. В большинстве случаев ЗТМ перемещаются передним ходом. Не-
,
237
которые виды работ в зависимости от местных условий могут выполняться по челночной схеме с возвратом машины на исходную позицию задним ходом, например при засыпке траншей и котлованов бульдозером, при планировочных работах на коротких по длине участках.
Все операции рабочего цикла ЗТМ непрерывного действия (копание, транспортирование и разгрузка грунта) совмещаются во времени. При этом для копания используется землеройный рабочий орган, а для перемещения и отсыпки грунта – специальный транспортирующий орган в виде ленточного конвейера.
ЗТМ особенно эффективны на массовых разработках грунтов. Производительность машины при разработке грунта скреперами с дальностью возки 0,5...1,5 км составляет в среднем 5...40 тыс. м3 грунта в год при стоимости разработки 1 м3 грунта 0,6...0,19 руб. и удельном расходе энергии 6...3,2 кВт∙ч/м3. При работе бульдозеров с дальностью возки 50...100 м соответственно: 6...76 тыс. м3 грунта в год, 0,25...0,085 руб. на 1 м3 грунта и 2,4...1,6 кВт ∙ м3. По этим показателям ЗТМ не уступают самой дешевой экскаваторной разработке грунта с его транспортированием по железной дороге. Для машин очень большой мощности производительность труда повышается в 2...2,5 раза, а стоимость разработки грунта снижается в
1,5...2 раза.
Совершенствование конструкции скреперов происходит в следующих направлениях: повышение комфортности условий труда оператора путем создания шумоизолируемых кабин с установкой кондиционеров, систем защиты оператора от падающих предметов и опрокидования, введение в
конструкцию амортизирующих подвесок; создание трансмиссий с регулируемым гидротрансформатором для скреперов с механизированной загрузкой; создание высокоэффективных гидрозамедлителей; создание систем микропроцессорного управления машиной, контроль за работой всех основных узлов; повышение надежности и долговечности скреперов; развитие модульного метода создания машин, позволяющего успешно применять агрегатный ремонт, упрощающего уход и обслуживание.
Бульдозеры. Бульдозеры предназначены для послойной разработки грунтов с их последующим перемещением перед рабочим органом (отвалом) по поверхности земли на небольшие расстояния. Установка на бульдозерах заднего рыхлительного оборудования позволяет эффективно разрабатывать прочные разборно-скальные грунты, в том числе в условиях зон холодного климата. Экономически выгодная дальность перемещения грунта бульдозером составляет 15…70 м в зависимости от мощности трактора, достигая 180 м при работе наиболее тяжелых машин в горнодобывающей промышленности.
Бульдозеры принято классифицировать номинальному тяговому усилию, ходовым системам базовых тракторов, назначению, конструктивным особенностям навесного оборудования. Основным классификационным параметром, связанным с массой трактора и непосредственно определяющим остальные технико-экономические показатели бульдозеров и бульдо-
,
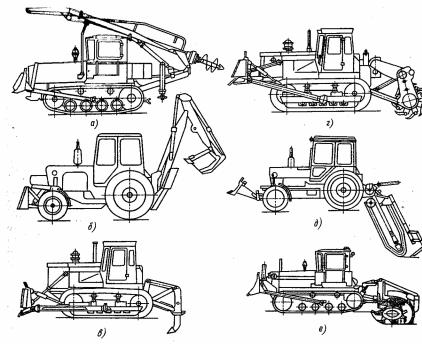
238
зеров с рыхлителями, является номинальное тяговое усилие, по которому различают: бульдозеры очень легкие (малогабаритные) − номинальное тяговое усилие до 25 кН, легкие − 25…135 кН, средние − 135… 200 кН, тяжелые − 200…350 кН и сверхтяжелые − свыше 350 кН.
Соответственно модели гусеничных бульдозеров определены по тяговым классам тракторов типоразмерным рядом: 3, 4, 6, 10, 15, 25, 35, 50, 75
и 100, охватывающим бульдозеры с номинальным тяговым усилием трактора 30… 1000 кН и бульдозеры с рыхлителями − 100… 1000 кН.
По типу ходовой системы (типу движителя) различают бульдозеры и бульдозеры с рыхлителями гусеничные и пневмоколесные, которые в свою очередь подразделяются на несколько видов.
По назначению различают бульдозеры общего, специального и многоцелевого. Бульдозеры общего назначения приспособлены для выполнения землеройно-транспортных и планировочных работ. Бульдозеры специального назначения обеспечивают выполнение узкоспециализированных работ определенного вида: чистку снега, сгребание торфа и т. д. Разновидности бульдозеров многоцелевого назначения показаны на рис. 4.30.
Рис. 4.30. Бульдозеры многоцелевого назначения с задним оборудованием:
а − бурильно-крановым; б − экскаваторным; в − рыхлительным; г − землеройнофрезерным; д − траншеекапателя; е − каналокапателя
Например, бульдозер ДЗ-1091 на базе гусеничного трактора Т-130М, рис.4.30 (дорожно-землеройный, типоразмерный ряд −10, ходовая система (тип движителя) − 9, назначение −1).
,
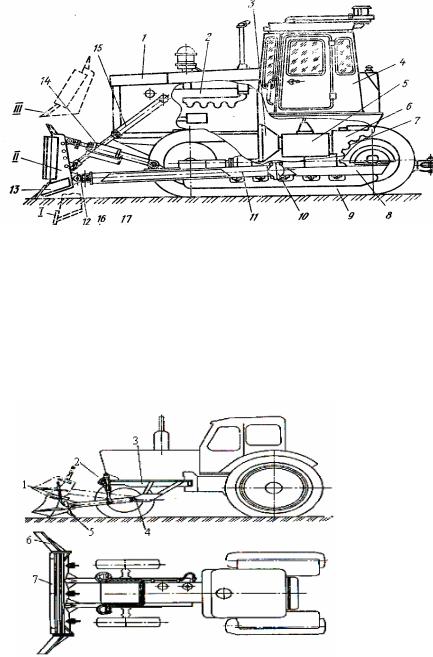
239
Рис.4.30. Бульдозер-толкач ДЗ-1091 1 – трактор; 2 – двигатель; 3 – муфта сцепления; 4 – кабина; 5 – коробка передач; 6 –
задний мост; 7 – звездочка; 8 – гусеничная тележка; 9 –гусеница; 10, 12 – шарниры; 11
– толкающий брус; 13 – отвал; 14 – гидрораскос; 15 – гидроцилиндр подъема и опускания; 16 – механизм компенсации перекоса; 17 – раскос
Бульдозер на пневмоколесном ходу является более маневренной машиной. Такие бульдозеры на базе серийного трактора «Беларусь» и К-702 приведены на рис.4.31 и 4.32.
Рис.4.31. Рабочее оборудование бульдозера ДЗ-3711:
1–отвал с жесткими толкающими брусьями; 2–гидроцилиндр; 3–подрамник; 4– шарнир; 5– рыхлительные зубья; 6–уширители; 7- козырек
Бульдозер на базе трактора К-702 состоит из отвала 2 с ножами 1, двух толкающих брусьев 8, двух кронштейнов 7 крепления бульдозерного оборудования, гидроцилиндров 9 для изменения угла поперечного отвала, двух гидроцилиндров 4 подъема и опускания отвала, двух кронштейнов 3 крепления гидроцилиндров, баласта 5, трубопроводов гидросистемы.
,
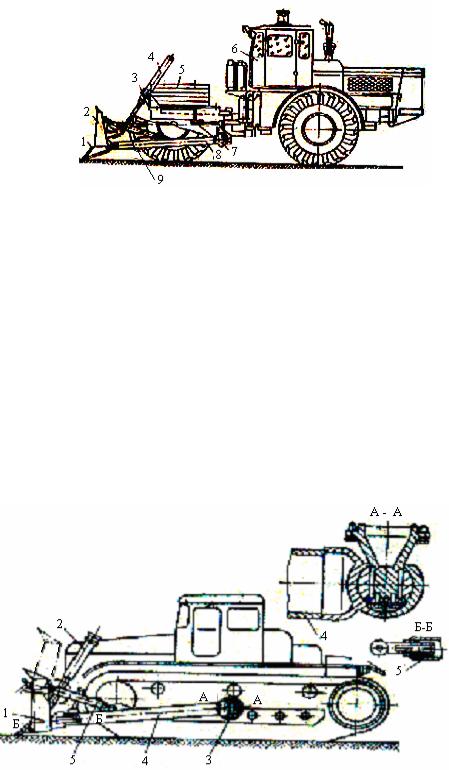
240
Рис.4.32. Бульдозер на базе трактора К-702: 1−нож;2− отвал; 3−кронштейн; 4, 9−гидроцилиндры; 5− балласт; 6− кабина; 7− кронштейн; 8−толкающий брус
На гусеничных тракторах выпускают бульдозеры с неповоротным отвалом: ДЗ-421Г на тракторе ДТ-75; ДЗ-101А на тракторе Т-4АП2; ДЗ-109; ДЗ-110В и ДЗ-110А-1 (с автоматическим управлением) на тракторе Т- 130М; ДЗ-351С на тракторе Т-180Г; ДЗ-118 на тракторе ДЭТ-250М; с поворотным отвалом ДЗ-109Б на тракторе Т-130М. Мощный бульдозер ДЗ118 (рис.4.33) с гидравлическим управлением на гусеничным тракторе ДЭТ-250 имеет поворотный и неповоротный отвалы.
Оборудование бульдозера состоит из отвала 1 с ножами, толкающих брусьев 4 с шаровой опорой 3, гидравлических цилиндров управления 2, 5. Отвал бульдозера управляется двумя гидроцилиндрами, установленными на цапфах в передней части трактора.
Рис.4.33. Бульдозер ДЗ-1181 с гидравлическим управлением: 1− отвал; 2, 5− гидроцилиндр; 3− шаровая опора; 4, 6− толкающие брусья и раскосы
Бульдозеры выполняют как навесное оборудование на пневмоколесных так и гусеничных тракторах, рис.4.34. Рабочее оборудование в виде отвала 5 с ножами 4 в его нижней части навешивают на трактор через два толкающих бруса 2 или универсальную раму 3, которые имеют шарнирные соединения 1 с боковыми балками ходовых тележек трактора или с кронштейнами его нижней рамы (при пневмоколесном тракторе).
,