
Строительные и дорожные машины. Основы автоматизации
.pdf121
Необходимое тяговое усилие на приводном элементе конвейера опреде ляют с учетом сопротивления W , возникающего при огибании приводного элемента лентой:
Fo Sнб Sсб W .
Соответствующий этому тяговому окружному усилию момент на валу двигателя привода конвейера
Мд FoD/ 2u ,
где u, передаточное число и КПД привода.
При пуске двигателя имеют место дополнительные сопротивления от инерции вращающихся частей привода и поступательно движущихся частей
конвейера. Для их преодоления на валу двигателя |
|
необходимо создать избы |
|||||||||||||
точный момент Mизб,д,равный: |
|
|
|
|
|
|
|
|
|
|
|
|
|||
|
|
m |
б |
D |
2 |
|
|
|
|
|
|
|
|
||
М |
изб.д |
|
|
|
|
б |
J |
|
0,105n t |
p |
, |
|
|||
|
|
|
2 |
|
|||||||||||
|
|
|
|
|
|
д |
д |
|
|
|
|||||
|
|
5,7u |
|
|
|
|
|
|
|
|
|
||||
где mб, масса вращающихся частей |
барабана; |
|
Dб диаметр |
барабана; |
|||||||||||
коэффициент, учитывающийся вращающихся |
масс двигателя; |
Jд мо |
мент инерции вращающихся частей двигателя; nд частота вращения вала двигателя; tp время разгона двигателя.
Пусковой момент на валу двигателя
Мп Мд Мизб.д.
Двигатель выбирают по мощности для установившегося режима работы конвейера
Р |
F v |
р.о |
/ 1000 |
д |
o |
|
|
и проверяют на перегрузку |
при |
пуске по отношению Мп/Mд < 1,5, где |
vp.o скорость движения рабочего (тягового) органа.
Загрузка транспортируемого материала на ленту производится через спе циальную воронку 3. Съем материала может производиться через приводной барабан или в промежуточных пунктах с помощью специальных сбрасываю щих устройств.
Для предотвращения самопроизвольного обратного хода ленты после оста новки конвейера на валу приводного барабана устанавливается тормоз. Угол наклона конвейера зависит от подвижности транспортируемого материала и коэффициента трения в движении материала о транспортерную ленту. Для таких материалов, как шлак, песок, щебень, он обычно составляет 16...20°.
Для транспортирования строительных материалов применяют тканевые прорезиненные ленты, состоящие из нескольких слоев (прокладок) ткани (бельтинга). Ширина и число прокладок ленты стандартизированы. Растяги вающую нагрузку воспринимают только тканевые прокладки, которые изго

122
товляют из хлопчатобумажных или из более прочных синтетических волокон. Ширина ленты ленточных конвейеров зависит от производительности и ее скорости. У серийно выпускаемых конвейеров она составляет 0,4...1,6 м. Ско рости конвейеров, используемых для транспортирования наиболее распро страненных строительных материалов, находятся в пределах 0,8...2,5 м/с. Конвейеры специального назначения, являющиеся транспортным органом многоковшовых экскаваторов, землеройных комплексов и других машин, имеют ширину ленты до 3,2 м при скорости 8 м/с.
В конвейерах большой длины и производительности прочность прорези ненной ленты с прокладками из синтетических волокон оказывается недоста точной. В этих случаях применяют несколько последовательно расположен ных самостоятельных конвейеров, составляющих общую длину трассы, а для тягового и несущего органов в ряде случаев применяют резинотросовые лен ты, у которых в качестве прокладок использованы тонкие стальные прово лочные канаты при 6...8кратном запасе прочности.
При транспортировании на дальние расстояния применяют также конвейе ры с раздельным тяговым и несущим органами. В качестве тягового органа используют стальные канаты или цепи, а несущего − облегченную прорези ненную ленту специальной формы, опирающуюся на тяговый канат или тяго
вую цепь. |
|
Производительность ленточных конвейеров (т/ч) |
|
П=3600 А р.о , |
(2.9) |
где А — площадь поперечного сечения потока материала, м2; — плотность материала, т/м3.
Для обеспечения требуемой производительности необходимо, чтобы ши
рина ленты (м) |
/ р.о , |
|
В k |
(2.10) |
где k — коэффициент, учитывающий изменение площади поперечного сече ния материала на желобчатой ленте (для трехроликовой опоры с углом на клона боковых роликов '=20 и 30° соответственно принимают равным 0,05
и 0,04).
При транспортировании крупнокусковых материалов ширина ленты должна исключить их рассыпание и удовлетворять следующему требованию:
В 2амах +0,2 м, |
(2.11) |
где амах − максимальный размер кусков, м.
Таким образом, при известной ширине ленты ее прочность определяется количеством прокладок в ней и допустимой нагрузкой на единицу ширины одной прокладки:
i Sнаб /(ВК), |
(2.12) |
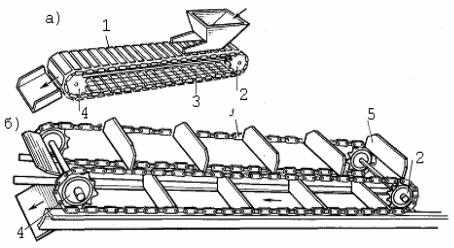
123
где К − допустимое усилие на разрыв 1 см ширины одной прокладки, Н/см. При эксплуатации конвейерная лента вытягивается. Относительное удли
нение ленты при разрыве прокладок доходит до 20...30 %. Поэтому для уст ранения большой вытяжки ленты применяют 10...12кратный запас прочно сти. Допустимое усилие на разрыв принимают 60 Н/см для хлопчатобумаж ных и 300 Н/см − для синтетических бельтингов.
Лента не должна проскальзывать по барабану. Для устранения пробуксов ки ленты увеличивают угол обхвата барабана или коэффициент трения, а при недостаточности этих мер применяют дополнительное натяжение каждой ветви ленты.
Мощность двигателя конвейера должна быть достаточной для возможно сти запуска случайно остановившегося груженого конвейера. Для этого не обходимо, чтобы средний пусковой момент двигателя превышал суммарный момент статических и динамических сопротивлений конвейера, действую щих в период пуска.
Пластинчатые конвейеры. При транспортировании материалов с острыми кромками, например для подачи крупнокускового камня в дробилки, приме няют пластинчатые конвейеры (рис. 2.19, а), у которых тяговым органом яв ляются две бесконечные цепи 3, огибающие приводные 4 и натяжные 2 звез дочки.
Рис. 2.19. Конвейеры с цепным тяговым органом:
а) – пластинчатый; б) – скребковый; 1– цепь; 2,4 – звездочки; 5– скребок
К тяговым цепям прикрепляют металлические пластины, перекрываю щие друг друга и исключающие просыпание материала между ними. Пла стинчатые конвейеры применяют также для перемещения горячих материа лов, деталей и изделий на заводах строительных конструкций.
В цепных конвейерах цепи чаще всего выполняют функции тягового эле мента, а грузонесущими элементами могут быть ковши, пластины или специ альные траверсы, соединенные со звеньями цепи. В отличие от лент и кана

124
тов тяговые цепи при равномерном вращении приводной звездочки с часто той n мин 1перемещаются неравномерно, их движение сопровождается про дольными и вертикальными колебаниями, период которых соответствует времени поворота звездочки на один зуб
t 60/ nz ,
где z число зубьев звездочки.
При этом возникает переменное по знаку продольное ускорение тяговой цепи
j n2 pц/180,
где pц шаг цепи.
Ускорение в свою очередь вызывает динамические нагрузки. Считают, что расчетная динамическая нагрузка Sдин , действующая по ходу цепи, равна ут роенному произведению приведенной массы m движущейся цепи и груза на продольное ускорение
Sдин 3mj.
Сучетом этого тяговое усилие, передаваемое цепи, несколько снижается
Fo Sнаб Sсб Sдин .
Скребковые конвейеры. Разновидностью конвейеров с цепным тяговым органом являются скребковые конвейеры (рис. 2.19, б). Они отличаются от пластинчатых тем, что на тяговых цепях 3 закреплены скребки 5, а нижняя рабочая ветвь погружена в открытый неподвижный желоб и при своем дви жении перемещает материал.
Ковшовые конвейеры. Такие конвейеры перемещают материал в ков шах в вертикальном или наклонном (под большим углом) направлениях на высоту до 50 м. Ковшовый конвейер (рис. 2.20) представляет собой замкну тый тяговый орган 4 в виде ленты или двух цепей, огибающий приводной 6 и натяжной 1 барабаны (при цепном органе − звездочки), на котором закрепле ны ковши 3 с шагом Т.
Рис.2. 20. Ковшовый конвейер: а)− схема конструкции; б) −мелкий полукруглый ковш;
125
в) − глубокий полукруглый ковш; г) − остроугольный; 1, 6 – ведущий и ведомый бараба ны; 2 – смотровая площадка; 3 – ковш; 4 – тяговый орган; 5 – кожух; 7 – люк
Рабочий орган вместе с ковшами размещен в металлическом кожухе 5. За грузка материала осуществляется через загрузочный 2, а разгрузка − через разгрузочный 7 башмаки. Различают быстроходные со скоростью от 1,25 до 2,0 м/с конвейеры для транспортирования порошкообразных и мелкокуско вых материалов и тихоходные со скоростью 0,4...1,0 м/с для транспортирова ния крупнокусковых материалов. В зависимости от вида транспортируемого материала применяют мелкие и глубокие полукруглые ковши, монтируемые на тяговом органе с шагом 300…600 мм, и остроугольные ковши, распола гаемые вплотную друг к другу.
Заполнение ковшей быстроходных конвейеров происходит при прохожде нии ими загрузочного башмака зачерпыванием, а в тихоходных − путем за сыпания материала в ковш. Разгрузка ковшей быстроходных конвейеров осуществляется при огибании ими приводного барабана под действием цен тробежных сил, а у тихоходных под действием силы тяжести (гравитацион ная разгрузка).
При гравитационной разгрузке остроугольных ковшей материал скатыва ется по передней стенке впереди идущего ковша, в результате чего снижается сила удара его о разгрузочный башмак.
Производительность ковшового конвейера (т/ч) определяется по формуле производительности для машин непрерывного действия с порционной выда чей материала:
П 0,6qkн п, |
(2.17) |
где q – вместимость одного ковша, л; kн |
– коэффициент наполнения ковша, |
принимаемый для мелких 0,6, для глубоких – 0,8 и для остроугольных ковшей
–0,8; –плотность материала, т/м3; п= 60 /T – число разгрузок в минуту;
– скорость ковшей, м/с; T– шаг расстановки ковшей, м.
Ковшовые конвейеры имеют малые габариты, но требуют постоянного кон троля за равномерностью загрузки их материалом.
Винтовые конвейеры. Винтовые конвейеры применяются для горизонталь ного или наклонного (под углом до 20°) транспортирования сыпучих, куско вых и тестообразных материалов на расстояние до 30...40 м и имеют произ водительность 20...40 м3/ч. Конвейер (рис. 2.21, а) представляет собой желоб 4 полукруглой формы, внутри которого в подшипниках 5 вращаетсявинт3
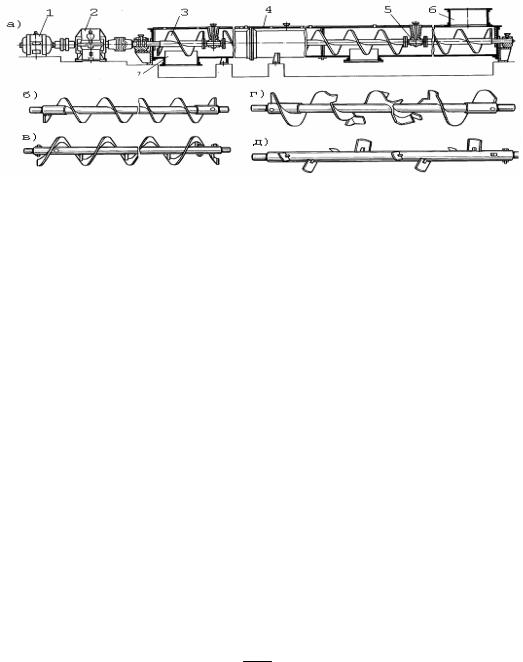
126
Рис.2.21. Винтовые конвейеры: а) –винт полукруглой формы; б) – сплошной; в) – ленточный ; д) –лопастной; г) – фассоный винт; 1– двигатель; 2– редуктор;
3– винт; 4– желоб; 5– подшипник; 6,7 – люки
Вращение винту сообщается электродвигателем 1 через редуктор 2.Загрузка материала производится через загрузочное отверстие 6, а выгрузка − через выходное отверстие 7 с задвижкой. Конструкция винта, частота его враще ния, а также коэффициент заполнения желоба зависят от вида транспорти руемого материала. Сплошной винт (рис. 2.21, б) применяют для хорошо сыпучих материалов (цемента, мела, песка, гипса, шлака, извести в порошке) при коэффициенте заполнения желоба kн =0,25...0,45, частоте вращения вин та 90...120 мин1.
Ленточный и лопастной винты (рис. 2.21, б, д) применяют для транспорти рования кусковых материалов крупного гравия, известняка, негранулирован ного шлака) при kн = 0,25...0,40 и частоте 60...100 мин 1. Для транспортиро вания тестообразных, слежавшихся и в влажных материалов (мокрой гли ны, бетона, цементного раствора) применяют фасонный и лопастной винты
(рис. 2.21, г, д) при частоте вращения 30...60 мин1 и kн =0,15...0,30.
Производительность горизонтального винтового конвейера (м3/ч) зави сит от средней площади сечения потока материала и скорости его движения вдоль оси
П 3600 D2 kн , (2.18)
4
где D – диаметр винта, м; – скорость движения материала вдоль оси конвей ера, м/с.
В случае перемещения материалов при угле наклона конвейера 5° произво дительность его снижается на 10 %, при угле наклона 10° − на 20 %, при угле наклона 20° − на 35 %. Диаметры винтов стандартизированы и составляют 0,15...0,6 м. Шаг винта t D для горизонтальных и t 0,8D для наклонных конвейеров. При частоте вращения двигателя п и шаге винта t D (где Dдиаметр винта) скорость движения материала (м/с) вдоль оси tn/60.
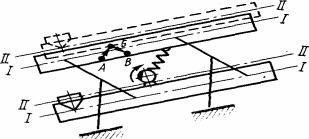
127
Для пропуска через конвейер кускового материала необходимо, чтобы шаг винта был больше максимального размера куска в 4...6 раз для рядового ма териала и в 8...10 раз для сортированного.
Вибрационные конвейеры. Вибрационные конвейеры основаны на принци пе значительного снижения сил внутреннего трения между частицами сыпу чих материалов и вязких смесей, а также внешнего трения об ограждающие поверхности при сообщении материалу колебаний с определенной частотой и амплитудой. Источником колебаний служат электромагнитные возбудители или вибраторы с механическим приводом (эксцентриковые, кривошипно шатунные). Колебания материалу сообщаются через жесткий орган в виде трубы или желоба. Материалы можно перемещать под уклон, по горизонтали, а также под углом вверх. Общий вид конвейера показан на рис. 2.22.
При высоких или среднечастотных колебаниях наклонный желоб при ка ждом колебании переходит из положения I в положение II и вновь возвраща ется в положение I. При этом частица материала, расположенная в точке А, перемещается вместе с желобом в точку 5 и при резком возвращении желоба в исходное положение окажется в точке В, расположенной выше точки A, со вершая за каждое колебание скачкообразное движение по транспортирующе му органу.
Рис. 2.22. Вибрационный конвейер
В строительстве вибрационные конвейеры используются для транспорти рования материалов равномерным потоком на небольшие расстояния, напри мер при дозировании инертных материалов или при загрузке конвейеров. Вертикальное движение вибрационного желоба описывается дифференци альным уравнением
my Fцsin t G Fст ,
где m масса колеблющихся частей желоба; Fц возмущающая сила, созда ваемая вибратором; угловая частота колебаний вальца; G−сила тяжести вальца; Fст статическая «пригрузка», создаваемая статической силой упру гости подвесок вальца, обычно Fст G.
Разделив обе части дифференциального уравнения на m, запишем в виде
|
Fц |
sin t |
G Fст |
. |
(2.19) |
|
|
||||
y |
m |
m |
|||
|
|
|
|
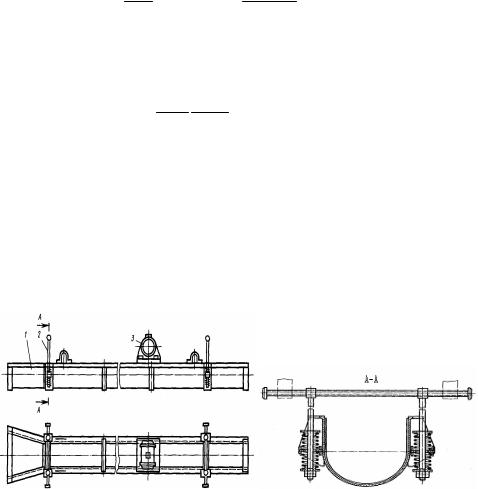
128
Интегрируя уравнение (2.19), находим
|
|
Fц |
|
G F |
|
|
|
|
cos t |
cт |
t c. |
|
|
||||
y ydt |
m |
m |
|||
|
|
|
|
Постоянную интегрирования получим из начальных условий: при t 0 скорость y 0; тогда c Fц/ m и
y Fц (1 cos t) G Fcт gt . m m
Этим уравнением определяется скорость колебательного движения вальца, которое сопровождается его отрывом и ударом об желоб. Динамический ко эффициент удара равен
кд а 2 sin , g cos
где a амплитуда; угол между осью грузонесущего органа и направлением колебаний; угол наклона конвейера к горизонту.
Расчетное значение скорости удара vуд можно найти из условия: при cos t 1; t 2 , откуда t 2 / .
Виброжелобы. При подаче бетонной смеси к месту укладки ее в соору жение применяют виброжелобы (рис. 2.23). Корпус вибрационного желоба 1 с помощью подвески 2 присоединен к несущей конструкции. Колебания кор пусу сообщаются укрепленным на нем вибратором 3.
Рис. 2.23. Вибрационный желоб: 1− корпус; 2− подвеска; 3− вибратор
2.4. Установки для пневматического транспортирования материала
Пневмотранспортными установками перемещают сыпучие материалы по трубам с помощью сжатого или разреженного воздуха. Применение пнев мотранспортных установок для погрузки, разгрузки и перемещения таких строительных материалов, как цемент, песок, известь, опилки и др., позволяет значительно повысить производительность труда, ликвидировать пыление и загрязнение материалов в пути, полностью механизировать процесс загрузки и выгрузки, создать условия для автоматизации транспортных процессов. Ус
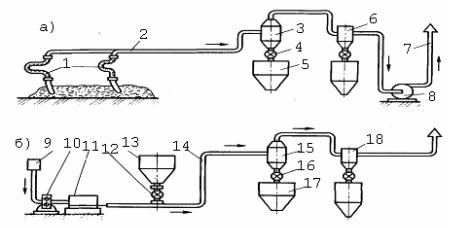
129
тановки пневматического транспортирования выгодно отличаются отсутстви ем движущихся частей, возможностью применения труб небольшого диамет ра, прокладываемых по любой пространственной трассе на значительные рас стояния при высокой производительности.
Недостатками пневматического транспорта являются большой удельный расход воздуха и высокая энергоемкость процесса (1...5 кВт∙ч/т), а также по вышенный износ элементов оборудования при транспортировании абразив ных материалов. Однако повышенная энергоемкость пневмотранспортных установок в значительной степени компенсируется перечисленными преиму ществами.
По принципу работы пневмотранспортные установки делятся на установки всасывающего и нагнетательного действий (рис. 2.24).
Установки всасывающего действия (рис. 2.24, а). В таких установках за грузка и транспортирование материала производятся в результате разрежения воздуха в транспортном трубопроводе 2, создаваемого вакуумнасосом 8. Ма териал в транспортный трубопровод поступает через сопла. При этом воз можны загрузка материала из нескольких мест и транспортировка его в одно место.
Рис. 2.24. Принципиальные схемы пневмотранспортных установок:
а) – всасывающего действия; 1− сопла; 2− трубопровод; 3− осадительная камера; 4− за твор; 5− бункер; 6− фильтр; 7− труба; 8− насос; б) − нагнетательного действия; 9−воздухоприемник; 10− компрессор; 11− воздухосборник; 12− затвор; 13− загружатель; 14− трубопровод; 15−осадительная камера; 16− шлюзовой затвор;
17− бункер; 18− фильтр
Из транспортного трубопровода материал поступает в осадительную камеру 3, где частицы материала выпадают из потока воздуха в результате резкого снижения скорости воздуха при расширении выходного сечения и через шлюзовой затвор 4 высыпаются в бункер 5. Воздух проходит дальнейшую очистку в фильтрах 6 и в очищенном от материала виде поступает в вакуум насос 8 и далее в атмосферу через трубу 7. Разряжение воздуха в трубопрово де уменьшается по направлению движения материала. Соответственно изме
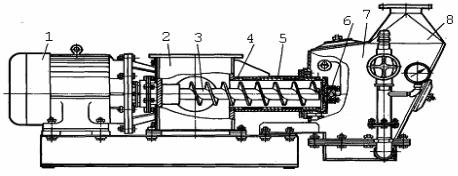
130
няется и скорость воздуха. В установках всасывающего типа она минимальна у сопла и максимальна у вакуумнасоса. Перепад давлений во всасывающих установках составляет 0,03...0,04 МПа, в результате его транспортирование возможно на небольшие расстояния.
Установки нагнетательного действия (рис. 2.24,6). В таких установках перемещение материала происходит под действием избыточного давления, создаваемого компрессором 10. Материал из бункера подается в загружатель 13, откуда он через затвор 12 под давлением сжатого воздуха по транспорт ному трубопроводу 14 поступает в осадительную камеру 15 и через шлюзо вой затвор 16 в бункер 17. Воздух, пройдя фильтры 18, выбрасывается в ат мосферу. Для сжатия и нагнетания воздуха применяются компрессоры с давлением до 0,8 МПа и производительностью воздуха до 100 м3 / мин. Заса сываемый компрессором из атмосферы воздух через воздухоприемник 9 очищается от пыли и далее поступает в воздухосборник 11, который пред назначен для определенного запаса сжатого воздуха и равномерного переме щения материала по трубам.
В установках нагнетательного действия наибольшее применение получи ли загружатели, выполненные в виде пневмовинтового насоса (рис. 2.25).
Рис.2.25 Пневмовинтовой насос: 1−двигатель; 2−воронка; 3−винт; 5−корпус; 6− клапан; 7−камера; 8− транспортный трубопровод
Он состоит из цилиндрического корпуса 5, винта 3 с переменным шагом, вращаемого двигателем 1,и смесительной камеры 7. Вследствие уменьшения шага винта материал по мере его прохождения к смесительной камере по степенно уплотняется, препятствуя просачиванию сжатого воздуха в загру зочную воронку 2. Степень уплотнения материала регулируется клапаном 6. В смесительную камеру по трубопроводу поступает сжатый воздух от ком прессора. Материал, попадая в струю сжатого воздуха, смешивается с ним и далее поступает в транспортный трубопровод 8 (см. на рис. 2.24, б поз. 14). Недостатком пневмовинтовых насосов является быстрый износ винта и корпуса насоса. Для повышения надежности корпус насоса футеруют сменными гильзами 4. Скорость воздуха, поступающего в загружатель,