
Строительные и дорожные машины. Основы автоматизации
.pdf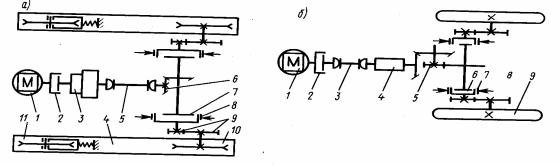
111
Рис. 2.11. Силовые передачи тракторов: а − гусеничного; б − колесного; 1– двигатель; 2–муфта сцепления; 3– карданный вал; 4– коробка передач;
5– главная передача; 6 – фрикционы; 7– ленточный тормоз; 8– бортовой редуктор; 9 – колеса
В состав механической передачи колесного трактора (рис. 2.12, б) с пе редним расположением двигателя 1 входят фрикционная муфта сцепления 2, карданный вал 3, коробка передач 4, главная передача 5, бортовые фрикцио ны 6 с ленточными тормозами 7, бортовые редукторы 8, передающие враще ние пневматическим колесам 9.
В силовых передачах гусеничных и колесных тракторов, одно и двухос ных тягачей, специальных шасси одноковшовых погрузчиков, самоходных кранов автомобильного типа широко применяют гидродинамические переда чи. В таких передачах вместо муфты сцепления устанавливают гидравличе ский трансформатор, а жесткую кинематическую связь между двигателем и ведущими колесами (звездочками гусениц) заменяют жидкостной. Такие си ловые передачи называются гидромеханическими.
При больших сопротивлениях движению (при трогании с места, движении на подъем или в трудных дорожных условиях) используется способность гидротрансформатора увеличивать крутящий момент двигателя с высоким коэффициентом трансформации. По мере снижения сопротивления движе нию постепенно снижается трансформация момента, плавно возрастает ско рость ведущих колес, а работа трансформатора переходит в режим с более высоким КПД. При этом переключение передач осуществляется автоматиче ски, т. е. высшие передачи включаются только тогда, когда вторичный вал достигает определенной частоты вращения. При этом двигатель работает в режиме максимальной мощности, а переключение передач происходит без разрыва крутящего момента. Отсутствие жесткой кинематической связи дви гателя с ведущими звездочками снижает динамические нагрузки на двига тель, повышает долговечность двигателя и силовой передачи.
В гусеничных тракторах с электрической силовой передачей момент ве дущим звездочкам гусениц сообщается тяговым электродвигателем постоян ного тока через бортовые фрикционы и редукторы. Тяговый электродвигатель получает питание от генератора, вращаемого дизелем трактора. Система при
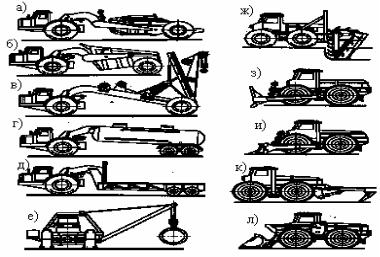
112
вода дизель—генератор—двигатель значительно упрощает кинематическую схему силовой передачи (отсутствуют коробка перемены передач, карданные валы), а главное − обеспечивает в широких пределах бесступенчатое регули рование скорости движения и момента в зависимости от внешней нагрузки. Гидромеханическая и электрическая силовые передачи наиболее полно отве чают режиму работы тракторов с прицепным и навесным рабочим оборудо ванием строительных машин.
Пневмоколесные тягачи. Такие одно и двухосные тягачи предназначены как базовые машины для работы с различного рода прицепным (одноосные) и навесным и прицепным (двухосные) рабочим оборудованием строительных машин (рис. 2.12).
Рис. 2.12. Прицепное и навесное оборудование одно и двухосных тягачей: а – скрепер; б – землевоз; в – кран; г – цистерна для цемента и жидкостей; д – тяжеловоз; е – крантрубоукладчик; ж – траншейный экскаватор;
з – корчеватель; и – бульдозер; к – рыхлитель; л – погрузчик
Пневмоколесные тягачи обладают высокими тяговой характеристикой, транспортными (до 50 км/ч и более) скоростями, большим диапазоном рабо чих скоростей, хорошей маневренностью, что способствует достижению вы сокой производительности строительных машин, создаваемых на их базе.
Пневмоколесные тягачи собирают из узлов и деталей серийного произ водства тракторов и тяжелых автомобилей при широкой степени унифика ции, что делает их конструкцию более долговечной. Мощность дизелей тяга чей достигает 900 кВт при нагрузке на ось 750 кН и более, что обеспечивает реализацию одного из главных направлений развития строительной техники −создания машин большой единичной мощности.
Одноосный тягач (рис. 2.13, а) состоит из шасси, на котором установлены двигатель 6, силовая передача, два ведущих колеса, кабина и опорносцепное устройство. Опорносцепное устройство выполнено в виде стойки 2, которая может качаться вокруг продольной горизонтальной оси, закрепленной в раме
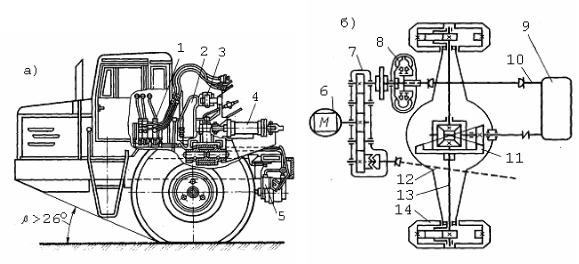
113
тягача, что позволяет полуприцепу перекашиваться относительно тягача в вертикальной плоскости.
Соединяется полуприцеп с тягачом вертикальным шкворнем 3. Поворот тягача относительно оси полуприцепа обеспечивается двумя гидроцилиндра ми 4 на угол до 90 ° в обе стороны. Оба ведущих колеса являются одновре менно и управляемыми. Коробку передач и гидротрансформатор часто мон тируют в одном корпусе, что делает конструкцию более компактной. От раз даточной коробки через вал 12 приводится в действие один или несколько масляных насосов 5, обеспечивающих работу исполнительных органов полу прицепной машины. Управление тягачом и прицепным оборудованием осу ществляется гидрораспределителем.1
Рис. 2.13. Одноосный тягач: а) – общий вид; б) – кинематическая схема: 1–гидрораспределитель; 2– опорносцепное устройство; 3– шкворень; 4– гидроцилиндр; 5– насос; 6 двигатель; 7– раздаточная коробка; 8– гидротрансформатор; 9– коробка пере
дач; 10, 12 – карданные валы; 13 – полуоси; 14– планетарный редуктор
Двухосные тягачи состоят из двух полурам, шарнирно сочлененных между собой. Поворот полурам, так же как и одноосного тягача, осуществляется с помощью двух гидроцилиндров двустороннего действия. Тягачи имеют один или два ведущих моста, одну или две двигательные установки. Силовая пере дача к ведущим колесам аналогична рассмотренной выше.
Коробки передач одно и двухосных тягачей трехступенчатые при одина ковых скоростях движения передним и задним ходом. Последнее особенно важно для машин цикличного действия, требующих особой маневренности при частом реверсировании рабочих движений (одноковшовые фронтальные погрузчики, бульдозеры и др.). В последние годы одно и двухосные тягачи комплектуются моторколесами с шинами до 3 м в диаметре и шириной более
114
1 м с автоматически изменяющимся в зависимости от дорожных условий дав лением воздуха.
Моторколесо представляет собой самостоятельный агрегат с гидравличе ским или электрическим двигателем и планетарным редуктором, встроенным в колесо. Рабочие двигатели питаются от масляных насосов или генератора, приводимых в действие основным двигателем тягача. Система управления двигателями моторколес позволяет каждому из них сообщать различные по величине моменты и частоту вращения, а при разворотах и направление вращения, что особенно важно при работе в сложных дорожных условиях.
2.3. Специализированные транспортные средства
Специализированные транспортные средства применяют в соответствии с их назначением и видом груза: для перевозки грунта, сыпучих грузов, бето нов и растворов, битума, топлива (автомобилисамосвалы, керамзитовозы, ав тобетоносмесители, авторастворовозы, автобитумовозы, топливовозы), по рошкообразных грузов (автоцементовозы, известковозы), строительных кон струкций (панелевозы, фермовозы, плитовозы, сантехкабиновозы), длинно мерных грузов (трубовозы, плетевозы, металловозы), строительных грузов в контейнерах (контейнеровозы), технологического оборудования и строитель ных машин (тяжеловозы).
Специализированные транспортные средства представляют собой прицепы и полуприцепы к базовым автомобилям и седельным тягачам средней и большой грузоподъемности с разрешенной нагрузкой на одиночную ось 60 и 100 кН (автомобили и тягачи с колесной формулой 6Х2 и 6Х4). Конструкция таких транспортных средств учитывает особенности перевозки и физические свойства грузов, сохранение качества грузов, комплексную механизацию по грузки и выгрузки. Главным параметром специализированных транспортных средств принята полная масса транспортного средства с грузом. Использова ние специализированного транспорта способствует дальнейшему развитию индустриальных методов строительства, снижению себестоимости перевозок, росту производительности транспортных средств. Ниже приводятся конст руктивные схемы и технологические возможности отдельных видов специа лизированного транспорта.
Автомобили-самосвалы и автопоезда. Различают автомобилисамосвалы общего назначения и специальные карьерные самосвалы. Автомобили самосвалы общего назначения (рис. 2.14) изготовляют на базе серийных гру зовых автомобилей (иногда с укороченной базой).
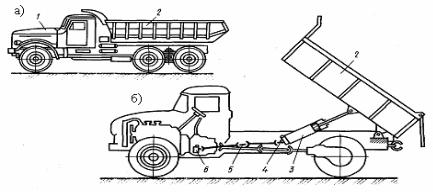
115
Рис. 2.14. Автомобилисамосвалы общего назначения: а) КрАЗ −с кузовом ковшовой формы; б) ЗИЛ− с откидной задней стенкой; 1–двигатель; 2– кузов; 3– гидроподъемник; 4– насос; 5–карданный вал; 6– коробка передач
Их используют для перевозки грунта из котлованов, нерудных строитель ных материалов от карьеров, причалов и железнодорожных станций на пред приятия строительной индустрии и на сооружаемые дороги. Кроме того, ав томобилисамосвалы используют для перевозки асфальтовой массы, строи тельного мусора и других навалочных грузов. Загрузка автомобилей самосвалов производится обычно экскаватором, погрузчиком или из бункера. Кузов 2 самосвалов прямоугольной, трапециевидной или корытообразной формы делается опрокидным с углом наклона до 60°. Различают самосвалы с задней разгрузкой, т. е. опрокидыванием только назад, с боковой разгрузкой на одну или обе стороны и с трехсторонней разгрузкой.
Опрокидывание кузова осуществляется с помощью гидравлического подъ емника, состоящего из одного или двух гидроцилиндров 3 одностороннего действия, питаемых насосной установкой 4, приводимой от двигателя 1 через коробку отбора мощности 6 автомобиля карданными валами 5.
Управление опрокидыванием кузова осуществляется из кабины. При этом положения гидрораспределителя обеспечивают принудительный подъем ку зова, фиксирование его на любом уровне и плавное опускание кузова под действием собственной массы, при котором происходит слив масла в бак че рез клапан с определенным проходным сечением. Грузоподъемность серийно выпускаемых отечественной промышленностью самосвалов составляет 10...12 т при полной массе автомобиля с грузом 19...23 т. Грузоподъемность специальных карьерных самосвалов достигает 300 т, так как они предназна чены для работы вне дорог общей дорожной сети и их осевые нагрузки могут превышать действующие весовые ограничения.
При перевозке массовых грузов применяют автопоезда (рис. 2.15).
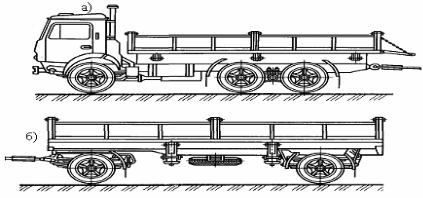
116
Рис.2.15. Общий вид автопоезда КамАЗ5410+ОдАЗ 9370: а)− тягач; б)−прицеп
Использование автопоездов вместо одиночных автомобилейсамосвалов позволяет повысить выработку на среднесписочную машину, снизить расход топлива, уменьшить число водителей. Автопоезда создают на базе автомоби лейсамосвалов и унифицированных автомобильных прицеповсамосвалов и полуприцеповсамосвалов к седельным тягачам, имеющим общие конструк тивные признаки. Гидроцилиндры прицепов действуют от гидравлической системы базового автомобиля. Автомобилисамосвалы, предназначенные для использования в качестве тягачей, оснащаются стандартными буксирными устройствами, а также гидро, пневмо и электровыводами для подключения соответствующих систем прицепов. Разгрузка кузовов самосвала и промежу точных прицепов ведется на две (боковые), а заднего – на три (боковые и зад нюю) стороны. Грузоподъемность автопоезда, выполненного, например, на базе автомобиля с колесной формулой 6Х4 типа КамАЗ, составляет 11 т (пол ная масса 19 т), прицепа полной массой 16 т и полуприцепа −25 т.
Конвейеры. В строительстве используют передвижные и стационарные ленточные конвейеры, перемещающие грузы на сравнительно небольшие расстояния.
Передвижные ленточные конвейеры изготовляют длиной 5, 10 и 15 м. Они оборудуются колесами для перемещения вручную или в прицепе к тягачу. Стационарные ленточные конвейеры для удобства монтажа составляют из отдельных секций длиной 2...3 м и общей протяженностью 40...80 м. Ленточ ные конвейеры широко используются как транспортирующие органы в кон струкциях траншейных и роторных экскаваторов, бетоноукладчиков и дру гих машин, где их параметры определяются параметрами основной машины.
Основным транспортирующим и тяговым органом ленточного конвейера (рис. 2.16, а) является бесконечная прорезиненная лента 4, огибающая два ба рабана — приводной 6 и натяжной 2.
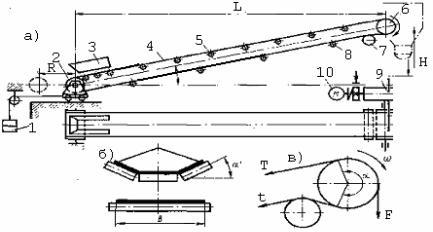
117
Рис. 2.16. Ленточный конвейер: а − схема конструкции; б − роликоопоры; в) − натяжное устройство; 1– натяжное устройство; 3– загружатель; 5,8 – роликоопоры;
9– редуктор; 10– двигатель
Поступательное движение ленты с грузом создается силами трения, дейст вующими в зоне контакта ленты с приводным барабаном. Вращение барабан получает от приводного электродвигателя 10 через редуктор 9. Для увеличе ния тягового усилия рядом с приводным барабаном устанавливают откло няющий. Верхняя рабочая и нижняя холостая ветви поддерживаются верхни ми 5 и нижними 8 роликоопорами. В целях получения наибольшей произво дительности конвейеров их верхние роликоопоры делают желобчатой формы, при прохождении по которым лента той же ширины способна нести больше материала по сравнению с плоской (рис. 2.16, 6).
Для предотвращения провисания ленты между роликоопорами, а также для увеличения тягового усилия лента предварительно натягивается посред ством винтового или грузового натяжного устройства.
В конвейерах ленты выполняют функции тягового и грузонесущего эле мента. Согласно уравнению Эйлера зависимость между натяжением Sнб гибкого тягового органа в точке набегания его на приводной барабан и его натяжением Sсб в точке сбегания с барабана имеет вид
Sнб Sc, e f , |
(2.1) |
где е = 2,718 — основание натурального логарифма; |
f коэффициент трения |
между гибким тяговым элементом и поверхностью барабана; угол обхвата барабана (канатоведущего шкива) гибким тяговым элементом, рад.
При установившемся движении гибкого тягового элемента тяговое (окруж ное) усилие на приводном элементе определяется по разности натяжений Sнб и
Sсб. |
|
|
|
|
|
|
ef |
1 . |
|
F |
S |
нб |
S |
сб |
S |
сб |
(2.2) |
||
o |
|
|
|
|
|
|
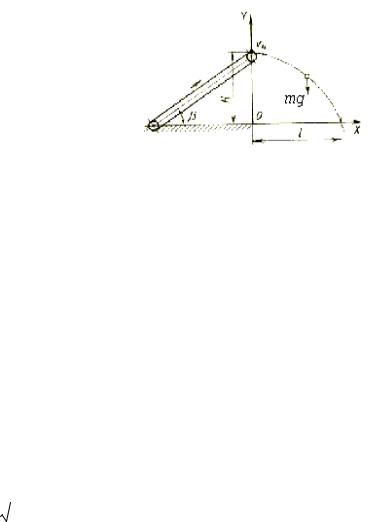
118
Из этого уравнения следует, что тяговое усилие, сообщаемое гибкому тя говому органу, может быть повышено путем увеличения начального натяже ния тягового элемента, равного Sсб, угла обхвата или коэффициента трения f между гибким тяговым и приводным элементами.
На ленточных отвальных конвейерах часто применяется инерционная раз грузка, при которой материал разгружается в основном за счет сообщаемой ему кинетической энергии и отбрасывается в сторону от машины на значительное расстояние. Это расстояние, так же как и характер траектории движения частиц материала или груза при сходе с конвейера, можно заранее определить. Для системы, изображенной на рис.2.17, соста
вим |
дифференциальные уравнения движения гру |
||
за: |
|
|
|
|
|
|
|
|
|
mx 0; |
my mg |
или |
x 0; |
y g, где m масса перемещае |
мого груза.
Интегрируя эти уравнения при начальных
условиях |
– при t 0, x vн,y 0 |
|
(здесь |
|
vн начальная скорость груза), находим |
Рис.2.17. Расчетная схема |
|||
|
|
|
|
конвейера |
|
x |
vн; y gt . |
||
Последние уравнения интегрируем при t 0, |
||||
x 0, y H |
(здесь Н максимальная высота падения груза): |
|||
|
|
|
2 |
/2 |
|
x vнt; y Н gt |
|
Для составления уравнения троектории движения груза после схода с конвейера исключим из первого выражения время t x/vн и подставим его во второе; тогда получим
y H |
g |
|
x |
2 |
2v |
н2 |
|
||
|
|
|
Эта зависимость представляет собой уравнение параболы. Как видно из схе
мы, при x l, |
y 0; если эти условия подставим в уравнение параболы, то |
|||
найдем максимальную дальность l отбрасывания груза |
|
|||
|
l vн |
|
. |
(2.3) |
|
2H/g |
Из выражения (2.3) следует, что дальность отбрасывания груза тем боль ше, чем выше его начальная скорость в момент схода его с конвейера и чем больше высота Н или наклон конвейера к горизонту.
При перемещении насыпных грузов на ленточных конвейерах распреде ленную массу q грузонесущего элемента находят
q A ,
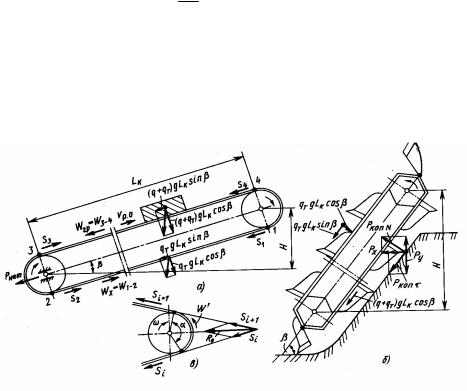
119
где A площадь поперечного сечения материала, расположенного на длине
1 м.
На рис.2.18 показана схема сил, действующих на верхнюю (груженую) и нижнюю (холостую) ветви тягового элемента, опирающиеся при своем дви жении на опоры качения. На прямолинейных участках сопротивления (Н) движению гибкого тягового элемента равны:
для верхней ветви
Wгр q qт gL o cos q qт gL sin ;
для нижней (холостой) ветви
W |
q |
т |
gL cos q |
т |
gL sin , |
x |
|
o |
|
где q, qт распределение массы перемещаемого груза и тягового органа; Lk длина конвейера; o, o суммарные коэффициенты сопротивления движе нию для верхней и нижней ветвей тягового элемента; угол наклона кон вейера к горизонту.
Сопротивление движению при огибании гибким тяговым элементом при водных и направляющих барабанов определяется по формуле, в которой пер вым членом определяются сопротивления трения в опорах барабанов, а во втором – сопротивления перегиба гибкого тягового элемента, зависящие от жесткости лент и от сопротивления трения в сочленениях
W Ro dц cж Si 1 Si ,
D
где Ro Si 1 Si sin /2 реакция в опорах барабана, огибаемого гибким тяговым элементом; угол обхвата барабана гибким тяговым элементом; Si 1,Si натяжения в набегающей и сбегающей ветвях гибкого тягового эле мента; D,dц диаметр барабана и его цапфы; коэффициент трения в цап фах; сж коэффициент жесткости гибкого тягового элемента.
Рис.2.18.Схема для определения сопротивлений движения конвейера: а) − схема сил; б) – схема сил в рабочем положении; в) – угол обхвата шкива
120
Принимая для упрощения о о , получаем
W q 2qт gL o qgH .
Натяжение в отдельных точках гибкого тягового элемента определяют пу тем последовательного обхода его замкнутого контура, считая, что натяже ние Si 1 в каждой последующей по ходу точке контура равно натяжению Si в предыдущей точке плюс сопротивление Wi i 1 междуэтими точками
Si 1 Si Wi i 1 .
Перед расчетом замкнутый контур тягового элемента разбивается на после довательные участки, границы которых отмечаны цифра ми 1, 2 (см. рис.2.19). Отсчет натяжений начинаем от точки 1 сбегания тягового элемента с приводного барабана; в этой точке натяжение задаем, ис ходя из экспериментальных данных, или определяем по формуле, зная допускае мое провисание f гибкого тягового элемента между роликами а холостой вет ви для ленточных конвейеров
S |
сб |
S |
S |
min |
|
qтglo2 |
, |
(2.4) |
|
8 f |
|||||||||
|
1 |
|
|
|
|
||||
гдеlo расстояние между |
роликами, м; |
Si натяжение в точке 1. |
|||||||
В соответствии с указанным правилом натяжения в остальных точках тя |
|||||||||
гового элемента будут равны: |
|
|
|
|
S2 S1 W1 2; S3 S2 W2 3; S4 Sнб S3 W3 4.
Необходимое начальное натяжение гибкого тягового элемента обеспечи вается натяжным устройством конвейера, с помощью которого регулируется осевое расстояние между приводным и отклоняющим барабанами. Как вид
но из схемы на рис. 2.18, а |
натяжное устройство должно обеспечить уси |
|||
лие |
|
|
|
|
Fнат S2 S3 |
|
|
||
или, с учетом выражений, |
полученных для S2 и, |
S3, |
||
Fнат S2 S3 W2 3 2S2 W2 3 2S1 2W1 2 |
W2 3, |
|||
Заменяя в этом уравнении S1 |
по формуле (2.4), находим |
|
||
Fнат |
qтglo2 |
2W12 W2 3. |
|
|
8 f |
f |
0,01...0,03 lo . Как |
||
При расчете усилия натяжения принимаем |
||||
видим, максимальное натяжение гибкого тягового |
элемента имеет место в |
|||
точке его набегания на приводной |
барабан. |
|
|