
pdf.php@id=6178
.pdf—интенсивное перемешивание за счет высокой скорости сдвига в зазоре между вращающимися рабочими органами ро тора и неподвижным статором;
—акустическое облучение широкого диапазона частот;
—кавитацию как результат довольно мощных звуковых колебаний с ярко выраженными волнами сжатия и разреже ния.
ЭВС и ГАРТ обеспечивают увеличение на 3—4 порядка энергии смешения в единице объема и скорости сдвига, что представляет практический интерес для получения тонкой эмульсии пластификаторов и смешения компонентов.
Магнитная обработка среды, акустические колебания и ка витация в аппаратах этого типа могут воздействовать на кине тику и глубину процессов капиллярной пропитки и, в ка кой-то степени, диффузии.
Предварительная проверка показала высокую эффектив ность того и другого аппаратов при проведении процесса из готовления пороховой массы.
На рис. 52—55 приведены результаты таких оценок, под тверждающие эффективность того и другого аппаратов.
Существенно улучшается диспергирование, ускоряется ка пиллярная пропитка, повышается однородность топливной массы по химическому составу, по баллистическим и механи ческим характеристикам.
5 10
Рис. 52. Диспергирование капель пластификатора в водной эмульсии в различных аппаратах:
1 — инжектор; 2 — ГАРТ; 3 — ЭВС
1 3 1
Рис. 53. Влияние магнитной обработки воды на процесс капиллярной про питки:
1 — омагниченная вода; 2 — водопроводная вода
Рис. 54. Однородность смеси в зависимости от степени обработки
Разброс, %
Рис. 55. Снижение разбросов основных характеристик в зависимости от степени обработки
132
Расширенные производственные испытания аппаратов типа ГАРТ и ЭВС показали их высокую эффективность и в заво дских условиях. Включение их в типовой промышленный про цесс потребовало широких конструктивных проработок приме нительно к конкретным технологическим операциям.
При этом на стадии промышленных испытаний, несмотря на некоторые преимущества аппарата ЭВС, по соображениям безопасности (унос частиц из индуктора) и большей конструк тивной сложности от него пришлось отказаться в пользу гид родинамического аппарата, который отличался предельной простотой, ибо мог быть изготовлен любым предприятием на базе центробежных насосов. Применительно к специфическим требованиям той или иной операции было разработано не сколько различных конструкций.
Подготовка, дозирование порошкообразных компонентов
иприготовление суспензий
Ввышеописанном первом варианте непрерывной техноло гической схемы «варки» транспортировка сыпучих компонен тов к дозаторам и засыпка их в расходный бункер производи лась вручную. На производствах с относительно малой произ водительностью применялись передвижные бункеры — смесители, что позволяло механизировать операции по транс портировке и загрузке сыпучих компонентов.
Однако использование передвижных контейнеров на заво дах, имеющих более высокие производительности, проблема тично, ибо потребует больших площадей и трудозатрат.
Более оптимальна технологическая схема, представленная на рис. 56.
Сыпучие компоненты из тары 1 вакуумным пневмотранс портом по трубопроводу подаются в стационарный бункер 5. Разделение порошка от воздуха производится в циклонах пер вичной 2 и вторичной 3 очистки. Циклон первичной очистки соединен с бункером через клапан разгрузки 4.
Вакуум создается водокольцевым насосом типа ВВН. Для очистки воздуха в схеме предусмотрен «мокрый» фильтр. Ста ционарный бункер устанавливается над дозатором типа ДН, который дозирует порошок в гидродинамический аппарат АПТС 7 (аппарат приготовления и транспортировки суспен зии).
Аппарат АПТС (рис. 57) совмещает функции гидродинами ческого аппарата и насоса.
133
►к вакуум - насосу
Рис. 56. Схема транспортировки и подготовки сыпучих компонентов:
1 —тара; 2, 3 — циклоны первичной и вторичной очистки; 4 — клапан разгрузки; 5 — стационарный бункер; 6 — дозатор ДН; 7 — АПТС
134
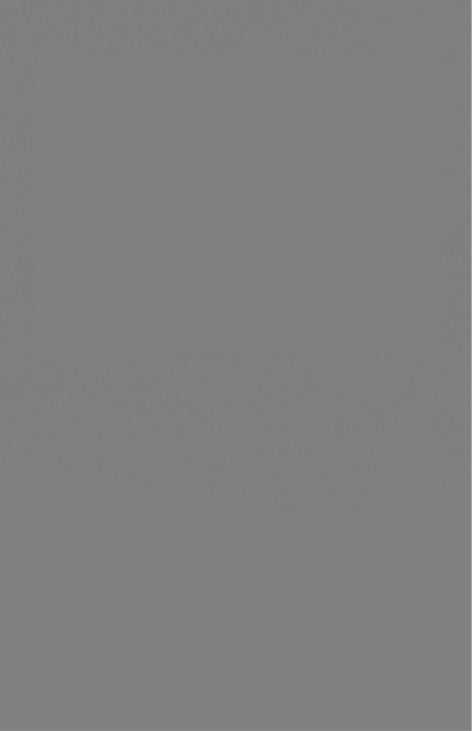
ДБФ и вазелинового масла или в ДНТ. При проведении про цесса в непрерывном режиме ранее гидрофобизация осуществ лялась в двух последовательно связанных емкостях с мешалка ми объемом по 200 л (смеситель и гидрофобизатор). Емкости снабжены паровой рубашкой и загрузочными люками для вво да компонентов и соединены между собой переливной трубой. Габаритные размеры — 1,8х0,9х2 м. Время процесса — 15...20 мин при температуре И0...120°С.
С целью сокращения времени процесса и габаритов обору дования проведена существенная интенсификация гидрофобизации в гидродинамических аппаратах АПТС.
Для определения оптимального времени гидрофобизации обработка Mg(OH)2 проводилась в роторном излучателе АПТС
в дискретном |
режиме |
(проход 0,5, 1, 3. |
10, 15, 20 минут). |
В емкость |
АПТС |
вводились жидкие |
компоненты (ДБФ |
и вазелиновое масло) в заданном соотношении, аппарат вклю чался в режим рециркуляции и при достижении температуры 110...120°С вводился Mg(OH)2. Через определенное время от бирались пробы для оценки степени гидрофобизации методом
определения смачиваемости до |
и после |
обработки (табл. 10). |
|
|
Таблица 10 |
Оценка смачиваемости Mg(OH)2 |
||
Кратность обработки |
|
Смачиваемость, |
(проходов через АПТС) |
1 |
г HzO/2 г Mg(OH)2 |
Негидрофобизированный |
|
0,9 |
1 |
|
0,24 |
2 |
|
0,22 |
3 |
|
0,20 |
4 |
|
0,20 |
Как видно из таблицы, гидрофобизация Mg(OH)2, характе ризуемая смачиваемостью, осуществляется практически за один проход в роторном излучателе. Таким образом, с исполь зованием гидродинамического аппарата АПТС процесс подго товки и ввода Mg(OH)2 осуществляется на малогабаритной не прерывной установке, включающей дозатор типа ДН и ГАРТ типа АПТС.
Непрерывный процесс пассивации и гидрофобизации алюминие во-магниевых порошков
В первом варианте непрерывной технологии «варки» под готовка металлических порошков (пассивация и гидрофобиза-
136
ция) осуществлялась периодически с ручными операциями по транспортировке, загрузке и выгрузке. Далее ввод защищенно го металла осуществлялся непрерывно в виде дозируемой сус пензии. Пассивация производилась в 0,2% растворе хромата калия (КСг04), гидрофобизация — раствором стеарата натрия (в расчете 1,5% от массы алюминиево-магниевого сплава). Данный способ был отработан и применялся в промышленно сти при изготовлении БРТТ, содержащих сплавы типа ПАМ-4.
Создание плазменных топлив, содержащих в составе боль шее количество металлического горючего и, кроме того, се литру, создающую при изготовлении топлива весьма агрессив ную среду, потребовало дополнительных исследований по изы сканию более надежных способов защиты металлического порошка.
В конце 70-х годов был выполнен комплекс исследований по увеличению коррозионной устойчивости сплавов АМД-10
иАМД-5 в двух основных направлениях:
—изыскания более эффективных способов пассивации сплава;
—поиск более эффективных способов гидрофобизации пассивированных порошков.
Эффективность новых технологических приемов по повы шению коррозионной устойчивости сплавов оценивалась ско ростью коррозии последних в агрессивных средах. В качестве агрессивных сред были использованы 0,005% раствор КОН (pH = 10,5) для испытания пассивированных образцов и 0,2% раствор КОН (pH = 12,5) для гидрофобизованных образцов. Скорость коррозии оценивалась по количеству водорода, вы делившегося в течение двух часов.
Кроме коррозионной устойчивости образцов сплава надеж ность способов защиты сплава оценивалась термической ус тойчивостью топлива, содержащего сплав, обработанный раз личными способами.
Для улучшения качества защиты алюминиево-магниевых сплавов были использованы более концентрированные раство ры окислителя и поверхностно-активных гидрофобизующих веществ.
На рис. 58 показаны результаты оценки коррозионной ус тойчивости сплава АМД-10 (10% Mg), пассивированного рас творами К2Сг20 7 различной концентрации, а на рис. 59 — коррозионная устойчивость тех же образцов, гидрофобизован ных 1,5% стеарата натрия.
137
Рис. 58. Коррозионная устойчивость АМД-10, пассивированного раствора
ми |
К2Сг20 7 |
различной |
концентрации: |
1 - исх. образец; 2 - |
0,2%; |
3 - 0,3%; |
4 - 0,5%; 5 - 1,0%; 6 - 1,5%; |
|
7 - |
1,2%; 8 - |
2,0% |
Рис. 59. Зависимость коррозионной устойчивости гидрофобизованного АМД-10 от концентрации раствора К2Сг20 7 при пассивации сплава:
1 - 0,2%; 2 - 0,3%; 3 - 0,5%; 4 - 2,0%; 5 - 1,0%; 6 - 1,2%; 7 - 1,5%
138
Как видно из графиков, существенное улучшение коррози онной устойчивости сплавов достигается при повышении кон центрации К2Сг20 7 с 0,2...0,3% до 0,5... 1,0%. Дальнейшее уве личение концентрации раствора до 2% оказывает менее суще ственное влияние, и использование в производстве такой концентрации нецелесообразно.
Внастоящее время в зависимости от оборудования и орга низации технологических процессов «варки» существуют и пе риодический, и непрерывный способы подготовки и ввода ме таллического горючего.
Вкачестве пассивирующих реагентов применяют растворы КСЮ4 (для топлив типа РАМ-10К) и К2Сг20 7 для плазменных топлив.
Технология непрерывной подготовки и ввода металличе ского горючего показана на рис. 60.
Вскрытие барабанов производится дистанционно на стан ке, установленном в отдельной кабине отделения гидрофобизации. Из барабанов с использованием кантователя сплав пе ресыпается в расходный контейнер 2. Автоматически открыва ется нижний разгрузочный люк контейнера и сплав самотеком поступает по рукаву в бункер дозатора ДН 5, которым дозиру-
Рис. 60. Технологическая схема непрерывной подготовки и ввода металли ческого горючего:
1 —■барабан с алюминиево-магниевым сплавом; 2 — расходный контей нер; 3 — дозатор ДН; 4 — насос-дозатор НД; 5 — пассиватор; 6 — гидро динамический аппарат; 7 — гидрофобизатор; 8 — винтовой насос; 9 — емкость раствора бихромата калия; 10 — емкость раствора стеарата натрия
139
ется в пассиватор 5. Одновременно в пассиватор из бачка — растворителя 9 дозатором НД 4 через теплообменник дозиру ется раствор хромата (бихромата) калия. Из пассиватора сус пензия сплава самотеком по переливной трубе поступает в гидрофобизатор 7. С целью интенсификации пассивации до момента перелива суспензия многократно прокачивается через гидродинамический аппарат типа СН, АПТС 6.
Из гидрофобизатора суспензия сплава самотеком поступает по переливной трубе в винтовой насос 8, которым транспор тируется через теплообменник в форсмеситель.
Подготовка и ввод ВВ
Взрывчатые вещества, вводимые в состав БРТТ (гексоген,
дазнн, |
октоген), |
поставляются |
заводами-изготовителями |
в мешках в сухом виде. |
|
||
Производственные операции по растариванию, дозирова |
|||
нию ВВ |
и т. д., |
учитывая их способность к электризации |
и чувствительность к трению и удару, представляют серьезную опасность и требуют разработки специальных мероприятий.
Применительно к непрерывному процессу изготовления топливной массы ввод ВВ потребовал решения двух вопросов:
—снижения чувствительности к электризации и механи ческим воздействиям;
—разработки способа непрерывного дозирования ВВ.
Что касается решения |
первой задачи, то наиболее легкий |
|
и известный |
путь просматривался за счет флегматизации, |
|
в том числе и |
водой. |
|
Поскольку |
достаточно |
полных сведений в литературе |
о влиянии влажности на взрывчатые характеристики ВВ в ши роком температурном диапазоне не имелось, были проведены целенаправленные исследования взрывчатых характеристик ув лажненных гексогена и дазина в широком температурном диа пазоне (20...—40°С).
На рис. 61, 62 приведены данные по влиянию влажности на чувствительность гексогена и дазина к удару и трению. Из графиков видно, что чувствительность к механическим воздей ствиям при увлажнении уменьшается как при положительных, так и отрицательных температурах. Чувствительность к удару гексогена при содержании влаги 20% падает более чем в 10 раз.
Увлажнение ВВ существенно снижает и их взрывчатые ха рактеристики. В табл. 11, 12 приведены данные по влиянию
140